Заместителю директора по персоналу подчиняются:
- Группа по нормированию труда и заработной плате: занимается контролем отработанного времени, разрабатывает сметы и калькуляции, производит проверку использования рабочего времени.
- Группа по работе с персоналом: ведет работу по движению персонала, следит за своевременным обучением, издает приказы и распоряжения по приему и переводу персонала, занимается подбором и расстановкой кадров.
- Канцелярия: занимается делопроизводством.
Главному экономисту подчиняется:
- Планово-экономический отдел: занимается разработкой бюджетов для подразделений, контролирует и рассчитывает выполнение планов производственного задания, определяет рентабельность производства, занимается планированием затрат.
1. 3. Эффективность использования автотранспорта
Транспортные предприятия имеют большой парк грузовых автомобилей с помощью которого перевозится основная часть грузов. От того, насколько эффективно он используется, зависит себестоимость перевозок, а следовательно, и финансовые результаты деятельности. Поэтому поиск резервов более эффективного использования грузовых машин в каждом хозяйстве имеет большое значение.
Для оценки работы грузового автотранспорта применяется целая система частных и обобщающих показателей. Частные технико-эксплуатационные показатели позволяют оценить отдельные стороны работы машин с точки зрения использования времени их работы, скорости движения, пробега, грузоподъемности и т.д., что является частью таких обобщающих показателей, как производительность работы машин и себестоимость перевозок, с помощью которых оцениваются окончательные результаты работы автотранспорта.
|
|
Для оценки степени использования машин на протяжении года рассчитывается коэффициент использования машин в работе Км:
Км = количество отработанных дней автопарком/количество машин – дней нахождения на предприятии.
Коэффициент технической готовности машин Кт.г.:
Кт.г. = автомобиле-дни нахождения в хозяйстве – автомобиле-дни в ремонте/автомобиле-дни нахождения в хозяйстве
Для характеристики степени использования автомашин на протяжении рабочего дня рассчитывается коэффициент использования их рабочего времени Кр:
Кр = время нахождения машин в пробеге/время нахождения машин в наряде
Коэффициент использования пробега Кп:
Кп = пробег с грузом на общий пробег
Коэффициент использования грузоподъемности машин Кгр:
Кгр = средняя загруженность 1 машины/средняя техническая грузоподъемность 1 машины.
Ниже в таблице приведены данные показатели транспортного предприятия.
Таблица 1 – Показатели использования грузового автотранспорта
|
|
№ п/п | Показатели | 2005 | 2006 | 2007 | 2007 г. в % к 2005 г. |
1. | Среднегодовое число машин, шт. | 16 | 16 | 18 | 112,5 |
2. | Общий тоннаж, т. | 115,8 | 115,8 | 124,6 | 107,6 |
3. | Средняя грузоподъемность машин, т. | 7,2 | 7,2 | 6,9 | 95,8 |
4. | Автомобиле - дни всего, тыс. дней в т. ч.: а) в работе б) в ремонте и его ожидании | 5840 729 120 | 5840 1124,5 144 | 6570 1156 162 | 112,5 158,6 135 |
5. | Общий пробег автомобилей, тыс. км. в т.ч. с грузом, тыс. км | 183,8 128,7 | 162,4 113,7 | 172,2 120,5 | 93,7 93,6 |
6. | Время пребывания в наряде, тыс.ч. в т.ч. в движении, тыс.ч. | 13500 12150 | 11100 9990 | 10700 9690 | 79,3 79,8 |
7. | Объем перевезенных грузов, тыс. т. | 52,6 | 53,3 | 35,3 | 67,1 |
8. | Объем грузооборота, тыс. т-км. | 726,3 | 735,1 | 534,1 | 73,5 |
9. | Средняя загруженность машины, т. | 5,6 | 6,5 | 4,4 | 78,6 |
10. | Общие затраты эксплуатации парка, тыс. руб. | 4201,4 | 4505,4 | 3053,9 | 72,7 |
11. | Коэффициент технической готовности | 0,98 | 0,98 | 0,98 | 100,0 |
12. | Коэффициент использования автопарка | 0,12 | 0,19 | 0,18 | 150 |
13. | Коэффициент использования пробега | 0,7 | 0,7 | 0,69 | 98,6 |
14. | Коэффициент использования грузоподъемности машин | 0,78 | 0,90 | 0,64 | 82,1 |
15. | Коэффициент использования рабочего времени машин | 0,9 | 0,9 | 0,91 | 101,1 |
16. | Средняя техническая скорость, км/ч | 15,1 | 16,3 | 17,8 | 117,9 |
17. | Средняя эксплуатационная скорость, км/ч | 13,6 | 14,6 | 16,1 | 118,4 |
18. | Среднее расстояние перевозки, км | 13,8 | 13,8 | 15,1 | 109,4 |
19. | Выработка на 1 автомобиле-тонно-день нахождения в хозяйстве, ткм | 17,3 | 17,5 | 11,8 | 68,2 |
20. | Себестоимость 1т-км, руб. | 5,78 | 6,13 | 5,72 | 99,0 |
|
|
Анализируя таблицу видно, что коэффициент использования автопарка очень низкий, это говорит о больших простоях автомобилей. В хозяйствах часто считают, что производительность автомобильного парка определяется общим количеством сделанных тонно-километров. При такой оценке использования машин объем грузоперевозок в ряде случаев увеличивают не за счет улучшения использования грузовых машин, а за счет увеличения их количества. Следовательно, чтобы исключить необъективность в оценке использования автопарка необходимо детально проанализировать один из качественных важнейших показателей работы автопарка – себестоимость одного тонно-километра перевезенного груза. В 2009 году себестоимость 1 т-км уменьшилась по отношению к 2007 году на 0,06 рублей или на 1% благодаря резкому сокращению грузооборота. Улучшить использование грузового автотранспорта также можно за счет снижения числа холостых пробегов, своевременного проведения технического обслуживания и обновления автопарка.
|
|
Готовя анализ по затратам на ремонт машин во время прохождения столкнулись с проблемой, что администрация предприятий, связанных с ремонтом не предоставляет такие данные и эта часть отчета осталась не выполненной. Поставлена задача во время прохождения преддипломной практики получить такие данные и использовать их в последующем отчете.
Таблица 2 – Анализ затрат на ремонт машин в мастерской хозяйства, тыс. руб.
Показатели | Легковые автомобили | Грузовые автомобили |
Стоимость фактических ремонтов по дефектным ведомостям | ||
Фактические затраты на ремонт | ||
Изменение за счет работы мастерской (+,-) | ||
Стоимость фактических ремонтов по нормативным затратам | ||
Отклонение за счет изношенности машин (+,-) |
Таблица 3 - Анализ затрат на ремонт машин в мастерской хозяйства, тыс. руб.
Показатели | Легковые автомобили | |
Российское производство | Иномарки | |
Стоимость фактических ремонтов по дефектным ведомостям | ||
Фактические затраты на ремонт | ||
Изменение за счет работы мастерской (+,-) | ||
Стоимость фактических ремонтов по нормативным затратам | ||
Отклонение за счет изношенности машин (+,-) |
2. ПРОИЗВОДСТВЕННАЯ ХАРАКТЕРИСТИКА ЦЕХА «БАЗА ПРОИЗВОДСТВЕННОГО ОБСЛУЖИВАНИЯ» «БПО»
БПО включает в себя: токарный, сварочный, цех по ремонту ДВС,
цех по ремонту ТО, механический цех.
Цех по ремонту ДВС.
В этом цехе делаются следующие работы:
· ремонт КПП автомобилей;
· ремонт мостов и редукторов;
· ремонт головок блока;
· ремонт гидросистем автомобиля;
· ремонт электроаккумуляторов и тормозных камер.
Работа в цехе БПО направлена на выполнение всех видов технического обслуживания и ремонта автомобильного транспорта.
2.1 Кадровый состав-
1.4 слесаря по двигателям внутреннего сгорания
2.1 человек по ремонту топливного насоса высокого давления
3.2 человека по ремонту коробок передач
4.2 человека по ремонту мостов и агрегатов
5.1 токарь
6.1 вулканизатор
7.1 кузнец
8.4 слесаря по ремонту автомобилей 4 разряда
оператор заправочных станций,
слесари – электрика
медик
электрогазосварщик
2.2. План-схема
Таблица 4 – Ведомость оборудования и оргоснастки
Номер на плане | Наименование | Тип, модель | Количество | Габариты | Год выпуска |
1 | Компрессор | BM-12 | 2 | 2007 | |
2 | Склад | - | 1 | 1990 | |
3 | Шкаф с инструментами | - | 5 | 2005 | |
4 | Инструменты для шиномонтажа | - | 6 | 2005 | |
5 | песок | - | 3тонны | J | 189.д.н.э |
6 | гидравлический подъём | MOD | 2005 | ||
7 | смотровая яма | - | 3 | 1990 | |
8 | место для козелков, лежаков, | - | 2 | 2000 | |
9 | моторный и агрегатный цех | - | 1 | 1990 | |
10 | моторный и агрегатный цех | - | 1 | 1990 | |
11 | пожарный гидрант | - | 1 | 1990 | |
12 | кран-балка | - | 1 | ||
13 | место для курения | - | 4 | 1990 |
2.3Технологическое оборудование цеха БПО.
1. Сварка Хиларг 450 , Кемпомиг 550.
2. Аппарат электровулканизирующий модель 6134.
3. Балансировочная установка microtec 520.
4. Универсальный станок для притирки клапанов модель ОПР – 1841А.
5. Гидравлический верстачный пресс модель Р – 324.
6. Установка для сверления модель Р – 175.
7. Кран – балка модель НКМ – 301.
8. Грузоподъмный кран модель 423М.
9. Гайковерт модель Н – 319.
10. Наканавный гидравлический подъемник модель П- 112.
3.ОХРАНА ТРУДА И ТЕХНИКА БЕЗОПАСНОСТИ В ЦЕХЕ БПО
3.1 Охрана труда
1. К самостоятельной работе по ремонту и техническому обслуживанию автомобилей допускаются лица, имеющие соответствующую квалификацию, получившие вводный инструктаж и первичный инструктаж на рабочем месте по охране труда, прошедшие проверку знаний по управлению грузоподъемными механизмами.
2. Слесарь, не прошедший своевременно повторный инструктаж по охране труда (не реже одного раза в 3 месяца), не должен приступать к работе.
3. Слесарь обязан соблюдать правила внутреннего трудового распорядка, утвержденные на предприятии.
4. Продолжительность рабочего времени слесаря не должна превышать 40 ч в неделю.
Продолжительность ежедневной работы (смены) определяется правилами внутреннего трудового распорядка или графиками сменности, утверждаемыми работодателем по согласованию с профсоюзным комитетом.
5. Слесарь должен знать, что наиболее опасными и вредными производственными факторами, действующими на него при проведении технического обслуживания и ремонта транспортных средств, являются:
автомобиль, его узлы и детали;
оборудование, инструмент и приспособления;
электрический ток;
этилированный бензин;
освещенность рабочего места.
6. Слесарь должен работать в специальной одежде и в случае необходимости использовать другие средства индивидуальной защиты.
7. В соответствии с Типовыми отраслевыми нормами бесплатной выдачи рабочим и служащим специальной одежды, специальной обуви и других средств индивидуальной защиты слесарю выдаются:
8. Слесарь должен соблюдать правила пожарной безопасности, уметь пользоваться средствами пожаротушения.
Курить разрешается только в специально отведенных местах.
9. Слесарь во время работы должен быть внимательным, не отвлекаться на посторонние дела и разговоры.
10. О замеченных нарушениях требований безопасности на своем рабочем месте, а также о неисправностях приспособлений, инструмента и средств индивидуальной защиты слесарь должен сообщить своему непосредственному руководителю и не приступать к работе до устранения замеченных нарушений и неисправностей.
11. Слесарь должен соблюдать правила личной гигиены. Перед приемом пищи или курением необходимо мыть руки с мылом, а при работе с деталями автомобиля, работавшего на этилированном бензине, предварительно обмыть руки керосином.
Для питья пользоваться водой из специально предназначенных для этой цели устройств (сатураторы, питьевые баки, фонтанчики и т.п.).
12. За невыполнение требований инструкции, разработанной на основе данной и указанных в п. 1.2, слесарь несет ответственность согласно действующему законодательству.
3.2 Требования безопасности перед началом работ.
1. Получить задание.
2. Одеть специальную одежду и застегнуть манжеты рукавов.
3. Осмотреть и подготовить свое рабочее место, убрать все лишние предметы, не загромождая проходы.
4. Проверить наличие и исправность инструмента, приспособлений:
-гаечные ключи не должны иметь трещин и забоин, губки ключей должны быть параллельны и не закатаны;
-раздвижные ключи не должны быть ослаблены в подвижных частях;
-слесарные молотки и кувалды должны иметь слегка выпуклую, не косую и не сбитую, без трещин и наклепа поверхность бойка, должны быть надежно укреплены на рукоятках путем расклинивания завершенными клиньями;
-рукоятки молотков и кувалд должны иметь гладкую поверхность;
-ударные инструменты (зубила, крейцмейсели, бородки, керны и пр.) не должны иметь трещин, заусенцев и наклепа. Зубила должны иметь длину не менее 150 мм;
-напильники, стамески и прочие инструменты не должны иметь заостренную нерабочую поверхность, должны быть надежно закреплены на деревянной ручке с металлическим кольцом на ней;
-электроинструмент должен иметь исправную изоляцию токоведущих частей и надежное заземление.
5.Проверить состояние пола на рабочем месте. Пол должен быть сухим и чистым. Если пол мокрый или скользкий, потребовать, чтобы его вытерли или посыпали опилками, или сделать это самому.
3.3 Требования безопасности во время работы
1. Во время работы слесарь должен, все виды технического обслуживания и ремонта автомобилей на территории предприятия выполнять только на специально предназначенных для этой цели местах (постах).
2. После постановки автомобиля на пост технического обслуживания или ремонта обязательно проверить, заторможен ли он стояночным тормозом, выключено ли зажигание (перекрыта ли подача топлива в автомобиле с дизельным двигателем), установлен ли рычаг переключения передач (контроллера) в нейтральное положение, перекрыты ли расходные и магистральный вентили на газобаллонных автомобилях, подложены ли специальные противооткатные упоры (башмаки) (не менее двух) под колеса. В случае невыполнения указанных мер безопасности сделать это самому.
На рулевое колесо повесить табличку «Двигатель не пускать - работают люди!». На автомобиле, имеющем дублирующее устройство для пуска двигателя, повесить аналогичную табличку у этого устройства.
3. После подъема автомобиля подъемником на пульте управления подъемником повесить табличку «Не трогать - под автомобилем работают люди!», а при подъеме гидравлическим подъемником после его поднятия зафиксировать подъемник упором от самопроизвольного опускания.
4. Ремонт автомобиля снизу вне осмотровой канавы, эстакады или подъемника производить только на лежаке.
5. Для пуска двигателя и передвижения автомобиля обратиться к водителю, перегонщику, бригадиру или слесарю, назначенным приказом по предприятию для выполнения этой работы.
6. Перед пуском двигателя убедиться, что рычаг переключения передач (контроллера) находится в нейтральном положении и что под автомобилем и вблизи вращающихся частей двигателя нет людей.
7. Перед проворачиванием карданного вала проверить, выключено ли зажигание, а для дизельного двигателя - отсутствие подачи топлива. Рычаг переключения передач установить в нейтральное положение, а стояночный тормоз освободить. После выполнения необходимых работ снова затянуть стояночный тормоз.
Слесарю запрещается:
-выполнять работы под автомобилем или агрегатом, вывешенным только на подъемном механизме (кроме стационарных электроподъемников) без подставки козелков или других страхующих устройств;
-поднимать агрегаты при косом натяжении троса или цепи подъемного механизма, а также зачаливать агрегаты стропом, проволокой и т.п.;
-работать под поднятым кузовом автомобиля-самосвала, самосвального прицепа без специального инвентарного фиксирующего приспособления;
-работать с поврежденными или неправильно установленными упорами;
сдувать пыль и стружку сжатым воздухом, направлять струю воздуха на стоящих рядом людей или на себя;
-хранить на рабочем месте промасленные обтирочные материалы и хранить чистые обтирочные материалы вместе с использованными;
-применять этилированный бензин для мытья деталей, рук и т.д.;
-загромождать проходы между стеллажами и выходы из помещений материалами, оборудованием, тарой, снятыми агрегатами и т.п.;
-хранить отработанное масло, порожнюю тару из-под топлива и смазочных материалов;
-применять приставные лестницы;
-использовать для крепления шлангов проволоку или иные предметы.
3.4 Требования безопасности в аварийных ситуациях
· О каждом несчастном случае, очевидцем которого он был, слесарь должен немедленно сообщить работодателю, а пострадавшему оказать доврачебную помощь, вызвать врача или помочь доставить пострадавшего в здравпункт или ближайшее медицинское учреждение.
Если несчастный случай произошел с самим слесарем, он должен по возможности обратиться в здравпункт, сообщить о случившемся работодателю или попросить сделать это кого-либо из окружающих.
· В случае возникновения пожара немедленно сообщить в пожарную охрану, работодателю и приступить к тушению пожара имеющимися средствами пожаротушения.
4. ОПИСАНИЕ ТЕХНОЛОГИЧЕСКОГО ПРОЦЕССА «Установка передней рессоры автомобиля КАМАЗ»
Для снятия передней рессоры:
- разгрузить домкратом колесо на стороне снимаемой рессоры и установить подставку под лонжерон рамы;
- снять колесо, отсоединить и снять амортизатор (для передней подвески);
- отвернуть гайки 15 (смотреть рисунок 1) стремянок 16 крепления рессоры, подложить под барабан подкладки и, опуская домкрат, освободить балку
- от рессоры до посадки барабана на подкладку;
- снять клин крепления пальца 2 рессоры, выбить палец, вывести ушко 3 из переднего кронштейна 1 и снять рессору.
Установка передней рессоры:
1. подъемным приспособлением опустить рессору на переднюю ось, предварительно установив кронштейн амортизатора под рессору
2. установить накладку рессоры и совместил их центрирующие элементы
3. вставить стремянки рессоры в отверстия площадки передней оси и затянул гайки стремянки
4. подвести передний конец рессоры к кронштейну, совместил отверстие ушка рессоры с отверстиями в кронштейне
5. вставить палец и стяжные болты
6. надеть на болты шайбы и затянул гайки
7. поднять за раму переднюю часть автомобиля
8. убрать подставку и опустил автомобиль
9. присоединить амортизатор к передней оси
10. вставил распорную втулку и стяжной болт в задний кронштейн рессоры и закрепил его.
По окончанию работы смазал палец ушка рессоры до появления свежей смазки из втулки ушка и прибрал рабочее место.
ЗАКЛЮЧЕНИЕ
В ходе производственной практики на базе производственного обслуживания предприятия ООО «АРГОС – ЧУРС» в ремонтной мастерской были освоены навыки организации рабочего места и самостоятельной работы, получен большой опыт практической работы по выбранной специальности, приобретены необходимые умения и навыки.
Выполненны поставленные задачи такие как :
1.Выполнено индивидуальное задание предусмотренного программной «Балансировка колеса автомобиля».
2.Ознокомление с новым оборудованием на предприятии «АГРОС-ЧУРС»
3.Разработан отчет по производственной практике.
В целом можно считать, что практика пройдена успешно, поставленные цели и задачи достигнуты.
Дата добавления: 2023-01-08; просмотров: 64; Мы поможем в написании вашей работы! |
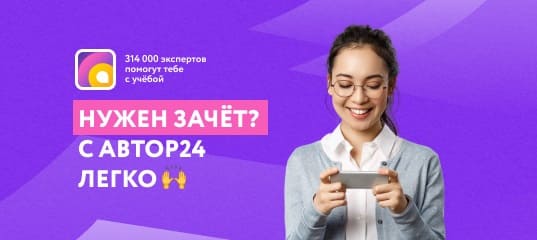
Мы поможем в написании ваших работ!