Задача 1 ОБОЗНАЧЕНИЕ, АНАЛИЗ И РАСЧЕТ ЭЛЕМЕНТОВ СОЕДИНЕНИЙ. Министерство образования и науки Российской Федерации
Министерство образования и науки Российской Федерации
Федеральное государственное бюджетное образовательное учреждение высшего профессионального образования
«Магнитогорский государственный технический университет
им. Г.И. Носова»
И.Д.Кадошникова
М.В.Аксенова
В.И.Кадошников
Е.В.Куликова
О.А.Филатова
А.П.Батрашкин
О.А.Белан
ПРИКЛАДНАЯ МЕХАНИКА.
ВЗАИМОЗАМЕНЯЕМОСТЬ ДЕТАЛЕЙ МАШИН
Учебное пособие к курсовой работе по метрологии стандартизации и сертификации, к контрольной работе по нормированию точности, к курсовому проекту по деталям машин и основам конструирования и к курсовому проекту по прикладной механике для студентов обучающихся по направлению 150400 «Технологические машины и оборудование», специальности 150401 «Проектирование технических и технологических комплексов» и других специальностей.
Магнитогорск
2011
УДК 621.86
Рецензенты:
Заведующий кафедрой «Теоретической механики и сопротивления материалов» Магнитогорского государственного технического университета им. Г.И. Носова,
Кандидат технических наук А.С.Савинов
Заведующий кафедрой «Машиноведение» Магнитогорского государственного университета,
Директор ООО ˝Протей˝ Р.Р.Дема
Прикладаная механика. Взаимозаменяемость деталей машин.
|
|
Кадошникова И.Д., Аксенова М.В., Кадошников В.И., Куликова Е.В., Батрашкин А.П., Филатова О.А.,Белан О.А.: Учеб.пособие. - Магнитогорск: МГТУ, 2012.- 221 с.
ISBN
Учебно-методическое пособие к курсовой работе по метрологии стандартизации и сертификации, к контрольной работе по нормированию точности, к курсовому проекту по деталям машин и основам конструирования и к курсовому проекту по прикладной механике для студентов обучающихся по направлению 150400 «Технологические машины и оборудование», специальности 150401 «Проектирование технических и технологических комплексов» и других специальностей.
УДК 621.86
ISBN
© МГТУ им. Г.И.Носова, 2011
© Кадошникова И.Д.,
Аксенова М.В.,
Кадошников В.И.,
Куликова Е.В.,
Филатова О.А.,
Батрашкин А.П.,
Белан О.А..
Оглавление
ВВЕДЕНИЕ.. 4
ТРЕБОВАНИЯ К ОФОРМЛЕНИЮ... 5
|
|
Задача 1 ОБОЗНАЧЕНИЕ, АНАЛИЗ И РАСЧЕТ ЭЛЕМЕНТОВ СОЕДИНЕНИЙ.. 6
Задача 2ВЫБОР ПОСАДОК ДЛЯ СОЕДИНЕНИЙ С ПОДШИПНИКАМИ КАЧЕНИЯ.. 14
Задача 3 ДОПУСКИ И ПОСАДКИ ШПОНОЧНЫХ СОЕДИНЕНИЙ ГОСТ 23360 (СТСЭВ183) СТСЭВ57-75 22
Задача 4 ПОСАДКИ ШЛИЦЕВЫХ СОЕДИНЕНИЙ.. 30
Задача 5. ВЫБОР УНИВЕРСАЛЬНЫХ СРЕДСТВ ИЗМЕРЕНИЯ.. 38
Задача 6 РАСЧЕТ И ВЫБОР ПОСАДОК С НАТЯГОМ... 99
Задача 7.ПРЕДЕЛЬНЫЕ ГЛАДКИЕ КАЛИБРЫ... 107
Задача 8.РАСЧЕТ ПОСАДКИ С ЗАЗОРОМ ДЛЯ ПОДШИПНИКА СКОЛЬЖЕНИЯ.. 115
Задача 9 НАЗНАЧЕНИЕ КОМПЛЕКСА НЕОБХОДИМЫХ ПАРАМЕТРОВ ДЛЯ КОНТРОЛЯ КАЧЕСТВА ИЗГОТОВЛЕНИЯ ЗУБЧАТОГО КОЛЕСА.. 122
Задача 10 РАССЧИТАТЬ ЗАДАНУЮ В УЗЛЕ РАЗМЕРНУЮ ЦЕПЬ, ОБОСНОВАВ ВЫБОР МЕТОДА РАСЧЕТА . 129
Задание 11. РАСЧЕТ ПАРАМЕТРОВ МЕТРИЧЕСКОЙ РЕЗЬБЫ... 152
ПРИЛОЖЕНИЕ А.. 156
ПРИЛОЖЕНИЕ Б.. 172
ПРИЛОЖЕНИЕ В.. 181
ПРИЛОЖЕНИЕ С.. 187
ПРИЛОЖЕНИЕ Д.. 192
ПРИЛОЖЕНИЕ Е.. 196
ПРИЛОЖЕНИЕ Ж... 209
БИБЛИОГРАФИЧЕСКИЙ СПИСОК ……………………………………………………………….………217
ВВЕДЕНИЕ
Динамичное развитие экономики России невозможно без повышения конкурентоспособности отечественных товаров и услуг как на внутреннем, так и на внешнем рынке. Определяющим для потребителей во всех странах мира стало качество. Производители должны знать требования предъявляемые к качеству выпускаемых ими товаров, изучать их. Требования отличаются в зависимости от покупательной способности населения, уровня конкуренции, климатических условий, культурных традиций и многих других факторов. А это означает, что качеством продукции и услуг необходимо управлять, уметь количественно оценивать и анализировать их показатели.
|
|
Метрология - это наука об измерениях, а измерение – один из важнейших путей познания.
Основная задача метрологии - обеспечение единства измерений состояния измерений, при котором их результаты выражены в узаконенных единицах, а погрешности известны с заданной вероятностью и не выходят за установленные пределы.
Большое значение для регулирования механизмов рыночной экономики приобрела сертификация.
Сертификация - это деятельность третьей независимой стороны, которая дает нам уверенность в том, что данное изделие, процесс, услуга соответствуют определенному нормативному документу. Сертификация считается основным достоверным способом доказательства соответствия продукции (процесса, услуги) заданным требованиям.
Стандартизация - это деятельность, направленная на разработку и установление требований, норм, правил, характеристик как обязательных для выполнения, так и рекомендуемых, обеспечивающая право потребителя на приобретение товаров надлежащего качества за приемлемую цену, а также право на безопасность и комфортность труда. Основными результатами деятельности по стандартизации должны быть повышение степени соответствия продукта (услуги), процессов их функциональному назначению, устранение технических барьеров в международном товарообмене, содействие научно - техническому прогрессу и сотрудничеству в различных областях.
|
|
Основой стандартизации является ЕСДП - единая система допусков и посадок. Основой ЕСДП является взаимозаменяемость - способность одного изделия, процесса или услуги быть использованным вместо другого изделия, процесса, услуги и при этом выполнять те же функции.
ТРЕБОВАНИЯ К ОФОРМЛЕНИЮ
В курсовой работе следует применять термины и обозначения, принятые вметодических указаниях (табл. 1).
Оформлять курсовую работу необходимо в соответствии с требованиями стандарта предприятия СМК-О-С-МГТУ-32-06, СМК-О-СЗ6-07. Проекты (работы) курсовые и дипломные. Общие требования к оформлению.
Курсовая работа включает:титульный лист, содержание (оглавление), введение, текст пояснительной записки с расчетами, схемами, сборочными и рабочими чертежами деталей, список использованной литературы.
Таблица 1 - Принятые термины и обозначения
Обозначения | Наименование обозначений (термины) |
D
Dmax, Dmin
(dmax, dmin)
Dc (dc)
ES (es)
EI (ei)
Smax, Smin, Sс
Nmax, Nmin
TD, Td
TS, TN,TSN
IT
A∆. A∆...
A1,A2…,Б1,Б2…
∆S, ∆I
![]() ![]() | Номинальный размер предельные размеры отверстия (вала): наибольший или максимальный, наименьший или минимальный действительный размер отверстия (вала) верхнее предельное отклонение отверстия (вала) нижнее предельное отклонение отверстия (вала) зазор максимальный, зазор минимальный, зазор средний натяг максимальный, натяг минимальный допуск отверстия, допуск вала допуск посадки с зазорами, с натягами, переходной; допуск размера по соответствующему квалитету, например IT5, IТ14; номинальный размер замыкающего звена номинальный размер составляющего звена размерной цепи верхнее предельное отклонение замыкающего звена, нижнее предельное отклонение замыкающего звена звенья увеличивающие звенья уменьшающие единица допуска,число единиц допуска (коэффициент точности) координата середины поля допуска система отверстия, система вала относительная геометрическая точность погрешность формы поправка, учитывающая реальные условия работы запас прочности технологический, запас прочности эксплуатационный натяг максимальный функциональный, натяг минимальный функциональный зазор максимальный функциональный, зазор минимальный функциональный |
Задача 1 ОБОЗНАЧЕНИЕ, АНАЛИЗ И РАСЧЕТ ЭЛЕМЕНТОВ СОЕДИНЕНИЙ
1.1 Выписать (таблица 1.1) в соответствии с вариантом исходные данные к задаче. По таблицам ГОСТ 25347-82, СТСЭВ 144-75 (приложение А5-А6) определить предельные отклонения отверстий и валов. Выделить поля допусков предпочтительного применения (Приложение А3-А4). Исходные данные оформить по таблице 1.2.
Таблица1.1
Последняя цифра шифра зачетной книжки | 1-й индекс шифра | 2-й индекс шифра | 3-й индекс шифра | ||||
номинальный диаметр, мм | поля допусков отверстий | поля допусков вала | |||||
1 2 3 4 5 6 7 8 9 0 | 14 24 30 18 40 65 10 120 80 50 | Н9 Н7 Н9 Н7 Н7 Н9 Н8 Н9 Н7 Н8 | Js9 G6 K8 Js8 E8 T7 F6 U8 R7 D9 | F9 N7 U8 G7 P7 JS9 M6 D9 F7 F8 | h9 h5 h8 h7 h6 h7 h5 h8 h6 h7 | f9 n6 s5 m6 m6 ϳs7 u7 u8 js7 js7 | x8 u7 c8 p6 r7 z8 n7 js6 t6 s7 |
Таблица 1.2 - Исходные данные
D, мм | Поля допусков | ||||||
Отверстия | вала | ||||||
Предельные отклонения, мкм | |||||||
| ES(es) | ||||||
EI(ei) | |||||||
Примечание. Поля допусков: * - предпочтительные. |
1.2 Составить возможные посадки из полей допусков валов и отверстий, вошедших в таблицу 1.2. Выделить предпочтительные посадки. Результаты записать в таблицу 1.3.
Таблица 1.3- Возможные сочетания полей допусков
Примечание. Посадки* - предпочтительные. |
1.3 Разделить посадки из таблицы 1.3 по системам и группам. Результаты записать таблицу 1.4.
Таблица 1.4 - Посадки по системам и группам
Система | Посадки | ||
с зазором | с натягом | переходные | |
СН, отверстия Ch, вала Комбинированная | |||
Примечание. В обозначение посадки включить предельные отклонения (например: |
1.4. Выписать одно из сопряжений и определить для него элементы присоединительных размеров.
1.4.1. Определить предельные размеры для отверстия и вала, допуски отверстия и вала.
1.4.2. Определить для выписанной посадки предельные зазоры (натяги), допуск посадки.
1.4.3. Дать графическое изображение посадки со всеми элементами.
Пример оформления смотрите на рисунке 1.1.
Предельные отклонения в мкм
Рисунок 1.1- Схема полей допусков посадки
1.5 Рассчитать погрешность формы для деталей соединения, приняв относительную геометрическую точность 60 %. Принять допуск формы ГОСТ 24643-81 (СТ СЭВ 636—77). (Таблица 1.5).
1.6 Установить величину шероховатости поверхности вала и отверстия в зависимости от номинального размера и квалитета. (Таблица 1.7; 1.8).
1.7 Обозначить точность размеров на чертежах. (Рисунок 1.2).
Таблица1.5 Допуски формы поверхностей (по ГОСТ 24643-81) | ||||||||||||||||||
Длина большей стороны или нормируемого участка, мм
| Допуски плоскостности TFE ( | |||||||||||||||||
Степени точности | ||||||||||||||||||
3 | 4 | 5 | 6 | 7 | 8 | 9 | 10 | 11 | 12 | |||||||||
До 10 | 0,6 | 1 | 1,6 | 2,5 | 4 | 6 | 10 | 16 | 25 | 40 | ||||||||
Св. 10 до 16 | 0,8 | 1,2 | 2 | 3 | 5 | 8 | 12 | 20 | 30 | 50 | ||||||||
Св.16 до 25 | 1 | 1,6 | 2,5 | 4 | 6 | 10 | 16 | 25 | 40 | 60 | ||||||||
Св. 25 до 40 | 1,2 | 2 | 3 | 5 | 8 | 12 | 20 | 30 | 50 | 80 | ||||||||
Св. 40 до 63 | 1,6 | 2,5 | 4 | 6 | 10 | 16 | 25 | 40 | 60 | 100 | ||||||||
Св. 63 до 100 | 2 | 3 | 5 | 8 | 12 | 20 | 30 | 50 | 80 | 120 | ||||||||
Св. 100 до 160 | 2,5 | 4 | 6 | 10 | 16 | 25 | 40 | 60 | 100 | 160 | ||||||||
Св. 160 до 250 | 3 | 5 | 8 | 12 | 20 | 30 | 50 | 80 | 120 | 200 | ||||||||
Св. 250 до 400 | 4 | 6 | 10 | 16 | 25 | 40 | 60 | 100 | 160 | 250 | ||||||||
Св. 400 до 630 | 5 | 8 | 12 | 20 | 30 | 50 | 80 | 120 | 200 | 300 | ||||||||
Возможные способы обработки | Доводка, шлифование и шабрение повышенной точности | Шлифование, шабрение, точение повышенной точности | Грубое шлифование, точение, протягивание, фрезерование, строгание
| Фрезерование, точение, строгание, долбление | Грубая механическая обработка всех видов | |||||||||||||
Примечания: 1.Значения допусков 1; 2; 13-16-й степеней точности приведены в ГОСТ 24643-81. 2.Допуски TFE и TFL рекомендуется принимать при нормальной (А) относительной геометрической точности поверхности равными 60 % от допуска Г размера, при повышенной (В) точности — 40 % от Т, при высокой (С) — 25 % от Т. Полученные значения округляют до стандартных значений по таблице. 3.Отклонение от плоскостности — наибольшее расстояние от точек реальной поверхности до прилегающей плоскости в пределах нормируемого участка. Отклонение от прямолинейности - наибольшее расстояние от точек реального профиля до прилегающей прямой в пределах нормируемого участка (длины). | ||||||||||||||||||
Номинальный диаметр, мм | Допуски цилиндричности TFZ ( | |||||||||||||||||
Степени точности | ||||||||||||||||||
3 | 4 | 5 | 6 | 7 | 8 | 9 | 10 | 11 | 12 | |||||||||
ДоЗ | 0,8 | 1,2 | 2 | 3 | 5 | 8 | 12 | 20 | 30 | 50 | ||||||||
Св. 3 до 10 | 1 | 1,6 | 2,5 | 4 | 6 | 10 | 16 | 25 | 40 | 60 | ||||||||
Св. 10 до18 | 1,2 | 2 | 3 | 5 | 8 | 12 | 20 | 30 | 50 | 80 | ||||||||
Св. 18 до 30 | 1,6 | 2,5 | 4 | 6 | 10 | 16 | 25 | 40 | 60 | 100 | ||||||||
Св. 30 до 50 | 2 | 3 | 5 | 8 | 12 | 20 | 30 | 50 | 80 | 120 | ||||||||
Св. 50 до 120 | 2,5 | 4 | 6 | 10 | 16 | 25 | 40 | 60 | 100 | 160 | ||||||||
Св. 120 до 250 | 3 | 5 | 8 | 12 | 20 | 30 | 50 | 80 | 120 | 200 | ||||||||
Св. 250 до 400 | 4 | 6 | 10 | 16 | 25 | 40 | 60 | 100 | 160 | 250 | ||||||||
Св. 400 до 630 | 5 | 8 | 12 | 20 | 30 | 50 | 80 | 220 | 200 | 300 | ||||||||
Возможные | Доводка, хонингование, тонкое шлифование, алмазное растачивание, тонкое точение, растачивание повышенной точности | Шлифование, хонингование, Чистовое точение и растачивание, тонкое развертывание, протягивание | Чистовое | Точение и растачивание, сверление, литье под давлением | Механичес-кая обработка | |||||||||||||
способы | точение и | |||||||||||||||||
обработки | растачивание, | |||||||||||||||||
развертывание | ||||||||||||||||||
протягивание, зенкерование |
|
| ||||||||||||||||
|
|
| ||||||||||||||||
|
|
| ||||||||||||||||
|
|
|
| |||||||||||||||
|
|
|
| |||||||||||||||
|
|
|
| |||||||||||||||
|
|
|
| |||||||||||||||
|
|
|
|
| ||||||||||||||
Примечания: 1.Значения допусков 1; 2; 13-16-й степеней точности приведены в ГОСТ 24643-81. 2. Допуски TFZ, TFK и TFP рекомендуется принимать при нормальной (А) относительной геометрической точности поверхности равными 30% (при погрешностях типа изогнутости 60 %) от допуска Т размера, при повышенной (В) точности — 20 % (40% ) от Т, при высокой (С) — 12,5 % (25 %) от Т. Полученные значения округляют до стандартных значений по таблице. 3. Отклонение от цилиндричности наибольшее расстояние от точек реальной поверхности до прилегающего цилиндра в пределах нормируемого участка. Отклонение от круглости — наибольшее расстояние от точек реального профиля до прилегающей окружности. Отклонение профиля продольного сечения — наибольшее расстояние от точек образующих реальной поверхности, которые лежат в плоскости, проходящей через ее ось, до соответствующей стороны прилегающего профиля. Пример пользования таблицей. Вал
| ||||||||||||||||||
Таблица 1.6 Допуски расположения поверхностей (по ГОСТ 24643-81)
| |||||||||||||||||
Интервалы размеров, мм | Допуски параллельности ТРА (//), перпендикулярности TPR ( | ||||||||||||||||
|
| Степени точности | |||||||||||||||
| 3 | 4 | 5 | 6 | 7 | 8 | 9 | 10 | 11 | ||||||||
До 10 | 1 | 1,6 | 2,5 | 4 | 6 | 10 | 16 | 25 | 40 | ||||||||
Св. 10 до 16 | 1,2 | 2 | 3 | 5 | 8 | 12 | 20 | 30 | 50 | ||||||||
Св. 16 до 25 | 1,6 | 2,5 | 4 | 6 | 10 | 16 | 25 | 40 | 60 | ||||||||
Св. 25 до 40 | 2 | 3 | 5 | 8 | 12 | 20 | 30 | 50 | 80 | ||||||||
Св. 40 до 63 | 2,5 | 4 | 6 | 10 | 16 | 25 | 40 | 60 | 100 | ||||||||
Св. 63 до 100 | 3 | 5 | 8 | 12 | 20 | 30 | 50 | 80 | 120 | ||||||||
Св. 100 до 160 | 4 | 6 | 10 | 16 | 25 | 40 | 60 | 100 | 160 | ||||||||
Св. 160 до 250 | 5 | 8 | 12 | 20 | 30 | 50 | 80 | 120 | 200 | ||||||||
Св. 250 до 400 | 6 | 10 | 16 | 25 | 40 | 60 | 100 | 160 | 250 | ||||||||
Св. 400 до 630 | 8 | 12 | 20 | 30 | 50 | 80 | 120 | 200 | 300 | ||||||||
Возможные способы обработки | Доводка, шлифование, шабрение, хонингование, тонкое точение | Шлифование, шабрение, хонингование, фрезерование, строгание, растачивание повышенной точности | Шлифование, фрезерование, строгание, протягивание, долбление, растачивание | Точение, фрезерование, строгание, растачивание, сверление и развертывание по кондуктору | Грубая механическая обработка | ||||||||||||
П р и меч а ни я: 1.Значения допусков 1; 2; 13-16-й степеней точности приведены в ГОСТ 24643-81. 2.Допуск для данной степени точности выбирают подлине нормируемой поверхности или длине нормируемого участка. Допуски торцового или полного торцового биения определяют по наибольшему диаметру торцовой поверхности или диаметру, на котором задан допуск торцового биения. 3.Отклонение от параллельности плоскостей (прямых) разность наибольшего и наименьшего расстояний между плоскостями (прямыми) в пределах нормируемого участка Отклонение от перпендикулярности плоскости (или оси) относительно оси – отклонение угла между плоскостью (осью) и осью от прямого угла, выраженное в линейных единицах на длине нормируемого участка. Торцовое (полное торцовое) биение разность наибольшего и наименьшего расстояний от точек реального профиля до плоскости, перпендикулярной к базовой оси. Определяют на заданном диаметре (на всей торцевой поверхности). Отклонение наклона - отклонение угла между прилегающей плоскостью (осью поверхности ) и базой от номинального значения угла, выраженное в линейных единицах на длине нормируемого участка. | |||||||||||||||||
Интервалы размеров, мм | Допуски соосности ТРС ( | ||||||||||||||||
Степени точности | |||||||||||||||||
3 | 4 | 5 | 6 | 7 | 8 | 9 | 10 | 11 | 12 | ||||||||
До 3 | 2 | 3 | 5 | 8 | 12 | 20 | 30 | 50 | 80 | 120 | |||||||
Св. 3 до 10 | 2,5 | 4 | 6 | 10 | 16 | 25 | 40 | 60 | 100 | 160 | |||||||
Св. 10 до 18 | 3 | 5 | 8 | 12 | 20 | 30 | 50 | 80 | 120 | 200 | |||||||
Св. 18 до 30 | 4 | 6 | 10 | 16 | 25 | 40 | 60 | 100 | 160 | 250 | |||||||
Св. 30 до 50 | 5 | 8 | 12 | 20 | 30 | 50 | 80 | 120 | 200 | 300 | |||||||
Св. 50 до 120 | 6 | 10 | 16 | 25 | 40 | 60 | 100 | 160 | 250 | 400 | |||||||
Св. 120 до 250 | 8 | 12 | 20 | 30 | 50 | 80 | 120 | 200 | 300 | 500 | |||||||
Св. 250 до 400 | 10 | 16 | 25 | 40 | 60 | 100 | 160 | 250 | 400 | 600 | |||||||
Св. 400 до 630 | 12 | 20 | 30 | 50 | 80 | 120 | 200 | 300 | 500 | 700 | |||||||
Возможные способы обработки | Тонкое шлифование и точение, внутреннее шлифование с одной установки, хонингование | Шлифование, точение повышенной точности, внутреннее шлифование и растачивание с одной установки | Грубое шлифование, точение и растачивание нормальной точности, протягивание, развертывание | Точение, растачивание, сверление | Грубая механи-ческая обработка | ||||||||||||
Примечания: 1.Значения допусков 1; 2; 13-16-й степеней точности приведены в ГОСТ 24643-81. 2.Допуски соосности ТРС, симметричности TPS и пересечения осей TPX даны в таблице 3.Отклонение от соосности - наибольшее расстояние между осью поверхности и осью Пример пользования таблицей. Вал | |||||||||||||||||
Таблица 1.7 Значения параметров шероховатости (по ГОСТ 2789-73) | ||||||||||||||||||||||||
Среднее арифметическое отклонение профиля Ra, мкм | ||||||||||||||||||||||||
100 | 80 | 63 | 50 | 40 | 320 32 | 250 25 | 200 20 | 160 16 | 125 12,5 | |||||||||||||||
10 1 | 8 0,8 | 6,3 0,63 | 5 0,5 | 4 0,4 | 3,2 0,32 | 2,5 0,25 | 2 0,2 | 1,6 0,16 | 1,25 0,125 | |||||||||||||||
0,1 0,01 | 0,08 0,008 | 0,063 | 0,05 | 0,04 | 0,035 | 0,025 | 0,02 | 0,016 | 0,012 | |||||||||||||||
Высота неровностей профиля по десяти точкам Rz,наибольшая высота неровностей профиля Rmах, мкм | ||||||||||||||||||||||||
1000 | 800 | 630 | 500 | 400 | 320 | 250 | 200 | 1600 160 | 1250 125 | |||||||||||||||
100 10 | 80 8 | 63 6,3 | 50 5 | 40 4 | 32 3,2 | 25 2,5 | 20 2 | 16 1,6 | 12,5 1,25 | |||||||||||||||
1 0,1 | 0,8 0,08 | 0,63 0,063 | 0,5 0,05 | 0,4 0,04 | 0,32 0,032 | 0,25 0,025 | 0,2 | 0,16 | 0,125 | |||||||||||||||
Средний шаг неровностей профиля Sm,средний шаг неровностей профиля по вершинам S,мм | ||||||||||||||||||||||||
10 | 8 | 6,3 | 5 | 4 | 3,2 | 2,5 | 2 | 1,6 | 12,5 1,25 | |||||||||||||||
1 0,1 | 0,8 0,08 | 0,63 0,063 | 0,5 0,05 | 0,4 0,04 | 0,32 0,032 | 0,25 0,025 | 0,2 0,02 | 0,16 0,016 | 0,125 0,0125 | |||||||||||||||
0,01 | 0,008 | 0,006 | 0,005 | 0,004 | 0,003 | 0,002 |
|
|
| |||||||||||||||
Относительная опорная длина профиля tp,%,уровень сечения р,% от Rmах | ||||||||||||||||||||||||
tp | 90 | 80 | 70 | 60 | 50 | 40 | 30 | 25 | 20 | 15 | 10 | |||||||||||||
p | 90 | 80 | 70 | 60 | 50 | 40 | 30 | 25 | 20 | 15 | 10 | 5 | ||||||||||||
Базовая длина l, мм | ||||||||||||||||||||||||
|
| 0,01; 0,03; 0,08; 0,25; 0,8; 2,5; 8;25 |
| |||||||||||||||||||||
II р и м е ч а н и я: 1.Предпочтительные значения параметров подчеркнуты. 2.Ra — среднее арифметическое абсолютных значений отклонений профиля от средней линии профиля. Rz — среднее расстояние между находящимися в пределах базовой длины высшими точками пяти наибольших выступов и низшими точками пяти наиболее глубоких впадин. Rmах — расстояние между линиями выступов и впадин в пределах базовой длины. | ||||||||||||||||||||||||
Рисунок 1.2 - Примеры обозначения точности на чертежах.
Примечание: 1.2.1-обозначение на сборочных чертежах; 1.2.2, 1.2.3 - обозначение точности на чертежах деталей
Таблица 1.8 - Минимальные требования к величине шероховатости в зависимости от допусков размеров и относительной геометрической точности. Руководящие материалы Бюро взаимозаменяемости БВ-РТМ-62-71/НИИмаш. М, 1973)
Допуск размера по квалитетам | Относительная геометрическая точность, α% | Номинальные размеры, мм | |||
до 18 | свыше 18 до 50 | свыше 50 до 120 | свыше 120 до 500 | ||
значение Ra мкм, не более | |||||
IT4 | 100 | 0,4 | 0,8 | 0,8 | 1,6 |
60 | 0,2 | 0,4 | 0,4 | 0,8 | |
40 | 0,1 | 0,2 | 0,2 | 0,4 | |
IT5 | 100 | 0,4 | 0,8 | 1,6 | 1,6 |
60 | 0,2 | 0,4 | 0,8 | 0,8 | |
40 | 0,1 | 0,2 | 0,4 | 0,4 | |
IT6 | 100 | 0,8 | 1,6 | 1,6 | 3,2 |
60 | 0,4 | 0,8 | 0,8 | 1,6 | |
40 | 0,2 | 0,4 | 0,4 | 0,8 | |
IT7 | 100 | 1,6 | 3,2 | 3,2 | 3,2 |
60 | 0,8 | 1,6 | 1,6 | 3,2 | |
40 | 0,4 | 0,8 | 0,8 | 0,8 | |
IT8 | 100 | 1,6 | 3,2 | 3,2 | 3,2 |
60 | 0,8 | 1,6 | 1,6 | 3,2 | |
40 | 0,4 | 0,8 | 0,8 | 1,6 | |
IT9 | 100 и 60 | 3,2 | 3,2 | 6,3 | 6,3 |
40 | 1,6 | 3,2 | 3,2 | 6,3 | |
25 | 0,8 | 1,6 | 1,6 | 3,2 | |
IT10 | 100 и 60 | 3,2 | 6,3 | 6,3 | 6,3 |
40 | 1,6 | 3,2 | 3,2 | 6,3 | |
25 | 0,8 | 1,6 | 1,6 | 3,2 | |
IT11 | 100 и 60 | 6,3 | 6,3 | 12,5 | 12,5 |
40 | 3,2 | 3,2 | 6,3 | 6,3 | |
25 | 1,6 | 1,6 | 3,2 | 3,2 | |
IT12 | 100 и 60 | 12,5 | 12,5 | 25 | 25 |
40 | 6,3 | 6,3 | 12,5 | 12,5 |
КОНТРОЛЬНЫЕ ВОПРОСЫ И ЗАДАНИЯ
1. Что называется взаимозаменяемостью? Виды взаимозаменяемости.
2. Дать определения размеров: номинального, предельного, действительного.
3. Допуск размера, допуск посадки и их расчет. Определение
характера посадки, расчет зазора, натяга.
4. Понятия основного отклонения.
5. Признаки ЕСДП: поле допуска, единица допуска, число единиц допуска, допуск, квалитет.
6. Точность обработки при изготовлении и ремонте деталей
машин: виды ошибок, отклонение формы, шероховатость.
7. Посадки в системе отверстия, посадки в системе вала.
8. Допуски формы и расположения поверхностей.
9. Суммарные допуски формы и расположения.
Задача 2ВЫБОР ПОСАДОК ДЛЯ СОЕДИНЕНИЙ С ПОДШИПНИКАМИ КАЧЕНИЯ
Подшипники качения - это опоры вращающихся или качающихся деталей. Их устанавливают между вращающимися и не вращающимися деталями конструкции. Подбор подшипников качения производят по динамической грузоподъемности, долговечности подшипника, частоте вращения вращающегося кольца.
Одним из важнейших условий хорошей работы подшипников является обеспечение в них оптимальных зазоров. Увеличение радиальных зазоров понижает точность вращения, увеличивает вибрации. Уменьшение зазоров ухудшает способность шарикоподшипников воспринимать осевую нагрузку, приводит к повышению температуры и снижает максимально допустимые частоты вращения.
Рабочий зазор в подшипнике - это
Sнач - начальный геометрический зазор в подшипниках, установленный соответствующими нормативами; ut - температурное изменение зазора; uнагр - контактные деформации от радиальной нагрузки.
Для обеспечения максимальной несущей способности подшипника очень важно правильно подобрать посадки подшипников на вал и в корпус. При выборе посадок для подшипников качения учитывают вращение вала или корпуса, нагрузку и число оборотов, тип и конструкцию подшипника, температуру при установившемся режиме работы, условия монтажа и вид нагружения колец. При вращающемся вале соединение внутреннего кольца подшипника должно быть неподвижным (с натягом), а по наружному диаметру подшипника возможен и небольшой зазор. Если вал не подвижен, а вращается корпус с наружным кольцом подшипника ( например в колесе автомобиля), то неподвижная посадка (прессовая) должна быть по наружному диаметру подшипника, а по внутреннему диаметру подшипника с валом может быть и небольшой зазор. При таком назначении посадок обеспечивается медленное провертывание невращающегося кольца в работающем подшипнике. Провертывание кольца содействует равномерному износу его дорожки качения, что ведет к увеличению срока службы подшипника.
Посадку кольца подшипника определяет вид нагружения кольца (циркуляционно, местно или колебательно нагруженное).
Для циркуляционно нагруженных колец подшипников посадка определяется в зависимости от интенсивности радиальной нагрузки, для местно нагруженных колец - по характеру распределения нагрузки (с умеренными толчками, спокойная, с ударами, вибрацией).
2.1 Выписать исходные данные в соответствии с вариантом из таблицы 2.1 и оформить их по форме таблицы 2.2.
Таблица 2.1 - Варианты задания
Исходные данные | Предпоследняя цифра шифра студента в зачетной книге | |||||||||
0 | 1 | 2 | 3 | 4 | 5 | 6 | 7 | 8 | 9 | |
Номер подшипника | 316 | 220 | 218 | 214 | 317 | 305 | 205 | 213 | 309 | 217 |
Класс точности | 0 | 6 | 6 | 0 | 6 | 5 | 0 | 6 | 0 | 6 |
Вращается вал | да | да | нет | да | да | нет | да | нет | да | нет |
Вращается корпус | нет | нет | да | нет | нет | да | нет | да | нет | да |
| Последняя цифра шифра студента в зачетной книге | |||||||||
0 | 1 | 2 | 3 | 4 | 5 | 6 | 7 | 8 | 9 | |
Нагрузка |
| |||||||||
R, кН | 1,3 | 2,5 | 3,5 | 3,8 | 1,8 | 2,0 | 3,0 | 6,0 | 8,0 | 4,5 |
Характер нагрузки | 1 | 3 | 4 | 4 | 2 | 5 | 1 | 3 | 2 | 5 |
Примечание | 1-спокойная нагрузка, толчки отсутствуют;2-легкие толчки, кратковременные перегрузки до 150% от расчетной нагрузки; 3- умеренные толчки, вибрации, кратковременные перегрузки до 150% от расчетной нагрузки;4- значительные толчки, вибрации, кратковременные перегрузки до 200% от расчетной нагрузки;5-сильные удары, кратковременные перегрузки до 300% от расчетной нагрузки. |
Таблица 2.2 - Исходные данные
Условие обозначения подшипника | R, kH | K1 | K2 | Вид нагружения колец подшипника | |
внутреннего | наружного | ||||
2.2 Записать в таблицу 2.3 основные габаритные размеры подшипника по ГОСТ 8338—75 (СТ СЭВ 402—76). (Таблица 2.4)
Таблица 2.3 - Основные габаритные размеры подшипника
d, мм | D, мм | В, мм | r, мм |
2.3 Определить интенсивность радиальной нагрузки |
где R - радиальная нагрузка или реакция опоры на подшипник, кН; В - ширина кольца, м; r-радиус скругления фаски, м; К1 - коэффициент, зависящий от характера нагрузки (при перегрузке до 150 % с умеренными толчками и вибрацией К1= 1, при перегрузке до 300 %, сильных ударах и вибрации К1 = 1,8); К2- коэффициент неравномерности распределения радиальной нагрузки между рядами роликов в двухрядных конических роликоподшипниках или между сдвоенными шарикоподшипниками при наличии осевой нагрузки на опору; К3- коэффициент, учитывающий степень ослабления посадочного натяга при полом вале или тонкостенном корпусе (при сплошном вале (К3=1).
2.4 Выбрать поле допуска поверхности детали, сопрягаемой с циркуляционно нагруженным кольцом подшипника. (Таблица 2.5)
2.5 Выбрать поле допуска поверхности детали, сопрягаемой с местно нагруженным кольцом подшипника. (Таблица 2.6)
2.6 Определить предельные отклонения присоединительных диаметров подшипников качения по ГОСТ 520—71 (СТСЭВ 774— 77), таблице 2.7.
2.7 Построить схемы полей допусков сопряжений:
а) внутреннее кольцо подшипника - вал;
б) корпус — наружноекольцо подшипника.
2.8 Вычертить сборочный и рабочие эскизы деталей. Указать на эскизах точность размера, допуск формы, допуск радиального биения торца, шероховатость, таблица 1.5, 1.6, 1.7, 1.8. Пример обозначения точности в соединениях с подшипниками качения представлен на рисунке 2.2.
2.9 Определить вероятностные допуски и вероятностные предельныне натяги и зазоры выбранных посадок.
Таблица 2.4 - Нормальные габаритные размеры подшипников (ГОСТ 8338-75, СТ СЭВ 402-76)
Условное обо- значение подшипников | Габаритные размеры | |||
внутренний диаметр, d, мм | наружный диаметр, D,мм | ширина, B, мм | радиус закругления фаски, r, мм. | |
Легкая серия | ||||
204 205 206 207 208 209 210 211 212 213 214 215 216 217 218 220 | 20 25 30 35 40 45 50 55 60 65 70 75 80 85 90 100 | 47 52 62 72 80 85 90 100 110 120 125 130 140 150 160 180 | 14 15 16 17 18 19 20 21 22 23 24 25 26 28 30 34 | 1,5 1,5 1,5 2,0 2,0 2,0 2,0 2,5 2,5 2,5 2,5 2,5 3,0 3,0 3,0 3,5 |
Средняя серия | ||||
305 306 307 308 309 310 311 312 313 314 315 316 317 318 | 25 30 35 40 45 50 55 60 35 70 75 80 85 90 | 62 72 80 90 100 110 120 130 140 150 160 170 180 190 | 17 19 21 23 25 27 29 31 33 35 37 39 41 43 | 2,0 2,0 2,5 2,5 2,5 3,0 3,0 3,5 3,5 3,5 3,5 3,5 4,0 4,0 |
Тяжелая серия | ||||
406 407 408 409 410 411 412 413 414 415 | 30 35 40 45 50 55 60 65 70 75 | 90 100 110 120 130 140 150 160 180 190 | 23 25 27 29 31 33 35 37 42 45 | 2,5 2,5 3,0 3,0 3,5 3,5 3,5 3,5 4,0 4,0 |
Таблица 2.5 -Допускаемые интенсивности нагрузок на посадочной поверхности вала и корпуса по ГОСТ 3325-85
Диаметр отверстия внутреннего кольца подшипника, мм | Допускаемые значения PR, kH/м | ||||
поля допусков для вала | |||||
свыше | до | js6 | k6 | m6 | n6 |
18 80 180 360 | 80 180 360 630 | 300 550 700 900 | 300-1350 550-2000 700-3000 900-3400 | 1350-1600 2000-2500 3000-3500 3400-4500 | 1600-3000 2500-4000 3500-6000 4500-8000 |
Диаметр отверстия внутреннего кольца подшипника, мм | поля допусков для вала | ||||
свыше | до | K7 | M7 | N7 | P7 |
50 180 360 630 | 180 360 630 1600 | 800 1000 1200 1600 | 800-1000 1000-1500 1200-2000 1600-2500 | 1000-1300 1500-2000 2000-2600 2500-3500 | 1300-2500 2000-3300 2600-4000 3500-5500 |
Таблица 2.6 - Посадки для местно нагруженных колец подшипников по ГОСТ 3325—85
Диаметр, мм | Посадки | Типы подшипников | |||
свыше | до | на вал | В корпус стальной или чугунный | ||
неразъемный | разъемный | ||||
Нагрузка спокойная с умеренными толчками и вибрацией К1=1 | |||||
80 | H6 | H7 | H7, H8 | Все типы, кроме штампованных игольчатых | |
80 260 | 260 500 | g6, f7 f7 | G7 | ||
Нагрузка с ударами и вибрацией К1>1 | |||||
80 | 80 260 | h6 | JS7 | JS7 | Все типы, кроме штампованных игольчатых, роликовых двухрядных |
260 | 500 | g6 | H7 |
При колебательном нагружении для радиальных шарико и ролико подшипников класса точности 0 и 6, поля допусков валов принимают по js6, поля допусков отверстия JS7.
Таблица 2.7 - Отклонения присоединительных диаметров подшипников качения по ГОСТ 520—71 (СТ СЭВ 774—77)
Номинальные размеры среднего диаметра, мм | Отклонения диаметра отверстия подшипника, мкм | Номинальные размеры среднего диаметра | Отклонения наружного диаметра подшипника, мкм | ||||
свыше | до | вернее | нижнее | свыше | до | верхнее | нижнее |
10 18 30 50 80 120 180 250 | 18 30 50 80 120 180 250 315 | 0 0 0 0 0 0 0 0 | -8 -10 -12 -15 -20 -25 -30 -35 | - 18 30 50 80 120 150 180 250 315 400 | 18 30 50 80 120 150 180 250 315 400 500 | 0 0 0 0 0 0 0 0 0 0 0 | -8 -9 -11 -13 -15 -18 -25 -30 -35 -40 -45 |
Таблица 2.8 - Шероховатость и отклонения формы посадочных и опорных торцовых поверхностей подшипников по ГОСТ 3325-85 класс точности подшипников 0,6 (выборка)
Посадочные поверхности | Шероховатость Ra, мкм не более | Допуск круглости, допуск профиля продольного сечения, мкм, не более | ||||||
до 80 | св.80 до500 | св.18 до30 | св.30 до50 | св.50 до80 | св.80 до120 | св.120 до180 | св.180 до250 | |
Валов | 1,25 | 2,5 | 3,5 | 4,0 | 5,0 | 6,0 | 6,0 | 7,0 |
Отверстий корпусов | 1,25 | 2,5 | 5,0 | 6,0 | 7,5 | 9,0 | 10,0 | 11,5 |
Опорных торцов заплечиков валов и корпусов | 2,5 | 2,5 | Допуски торцевого биения заплечиков валов, заплечиков отверстий корпусов, мкм, не более | |||||
21/33 | 25/39 | 30/46 | 35/54 | 40/63 | 46/72 | |||
Примечание: * - числитель для валов, заменитель для корпусов |
Пример:
Рассчитать и подобрать посадки для соединения внутреннего кольца подшипника с валом и наружного кольца с корпусом редуктора.
Исходные данные Т = 600 Н∙м; [τ] = 20 Н/мм2; R = 9 кН; К1, К2, К3 = 1.
Решение.
1 Определяем диаметр поверхности вала под подшипник:
мм.
2 По СТ СЭВ 514 (приложение А.1) принимаем d = 55 мм. Этому диаметру соответствует подшипник шариковый № 311 с размерами d = 55 мм; D = 120 мм; B = 29 мм; r = 3 мм (таблица 2.4).
3 Определяем интенсивность нагрузки на посадочной поверхности:
,
,
Н/мм.
4 При интенсивности нагрузки Н/мм подбираем (таблица 2.5) посадку для внутреннего кольца с валом Ø55 k6, (таблица 2.6), посадку для наружного кольца с корпусом Ø120 G7.
5 Результаты расчета и подбора посадок заносим в таблицу 2.9.
Таблица 2.9 – Результаты расчета и подбора посадок
Параметры | ![]() | ![]() |
Класс точности по СТ СЭВ 774-77 Размер, посадка Охватывающая поверхность: верхнее отклонение, мкм нижнее отклонение, мкм допуск, мкм Охватываемая поверхность: верхнее отклонение, мкм нижнее отклонение, мкм допуск, мкм Зазор, мкм наибольший наименьший Натяг, мкм наибольший наименьший Допуск посадки, мкм | 0 Ø55 k6 Внутреннее кольцо 0 –15 (таблица 2.7) 15 Вал +21 +2 (таблицы 2.7) 19 – – 36 2 34 | 0 Ø120 G7 Отверстие в корпусе +47 +12 (таблица 2.7) 35 Наружное кольцо 0 –15 (таблица 2.7) 15 62 12 – – 50 |
Таблица 2.10 Точность размеров ширины колец шариковых и роликовых радиальных и шариковых радиально-упорных подшипников.
Интервалы номинальных диаметров d, мм | Допускаемые отклонения, мкм ГОСТ520-71 ширины колец В, выборка | ||||||
0,6 | 0 | 6 | 5,4,2 | 5 | 4 | 2 | |
верхние | нижние | нижние | верхние | нижние | нижние | нижние | |
Св.2,5 до 10 | 0 | -120 | -120 | 0 | -40 | -40 | -40 |
Св.10 до 18 | 0 | -120 | -120 | 0 | -80 | -80 | -80 |
Св. 18 до 30 | 0 | -120 | -120 | 0 | -120 | -120 | -120 |
Св.30 до 50 | 0 | -120 | -120 | 0 | -120 | -120 | -120 |
Св.50 до 80 | 0 | -150 | -150 | 0 | -150 | -150 | -125 |
Св.80 до 120 | 0 | -200 | -200 | 0 | -200 | -200 | -125 |
Св.120 до 180 | 0 | -250 | -250 | 0 | -250 | -250 | -125 |
Св.180 до 250 | 0 | -300 | -300 | 0 | -250 | -250 | -125 |
Св.250 до 315 | 0 | -350 | -350 | 0 | -300 | -300 | -150 |
Св.315 до 400 | 0 | -400 | -400 | 0 | -350 | - | - |
Св.400 до 500 | 0 | -450 | -450 | 0 | -400 | - | - |
Ширина подшипника В = 29 мм.
Допуск мкм, нижнее отклонение ei = –120 мкм (таблица 2.10).
6 Определяем вероятностные допуски выбранных посадок:
мкм;
мкм.
7 Находим вероятностные предельные натяги в соединении внутреннего кольца с валом и зазоры в соединении наружного кольца с корпусом:
мкм;
мкм;
мкм;
мкм;
мкм;
мкм.
8 Строим схемы расположения полей допуска выбранных посадок.
Рисунок 2.1 – Схемы расположения полей допусков в соединении внутреннего кольца подшипника с валом и наружного кольца с корпусом редуктора.
Рисунок 2.2 - Обозначение точности подшипников качения на чертежах
КОНТРОЛЬНЫЕ ВОПРОСЫ И ЗАДАНИЯ
1. Классы точности подшипников качения.
2. Материалы, применяемые .для изготовления подшипников качения.
3. Значение рабочего зазора для обеспечения несущей способности подшипника.
4. Виды нагружения колец подшипников качения.
5. Как выбрать поле допуска для деталей, сопрягаемых с подшипником?
6. Что влияет на интенсивность радиальной нагрузки?
7. Какие поля допусков валов образуют посадки с натягами при
сопряжении с внутренним кольцом подшипника?
8. Расскажите о расположении полей допусков внутреннего и
наружного колец подшипника относительно линии номинального размера.
Дата добавления: 2018-02-18; просмотров: 1041; Мы поможем в написании вашей работы! |
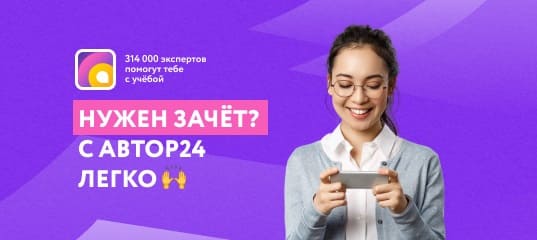
Мы поможем в написании ваших работ!