Правила внутреннего распорядка
Ознакомление с предприятием
История предприятия
ООО «БелАгроВет» - одно из ведущих преприятий по производству медицинской одежды в Беларуси. Основано предприятие в г Солигорске в 1996году. 11 июля 1998 года коллектив предприятия вместе с трудящимися праздновал открытие швейного предприятия в городе Могилеве. В строй действующих швейных предприятий вступила с численностью 35 человек. Основными нашеми сотрудниками являются Россия, Украина. За период деятельности был выпущен широкий ассортимент медицинской одежды, наиболее полно удовлетворяющий любым запросам наших клиентов
Ассортимент: Всегда в широком ассортименте оригинальная модная медицинская одежда(медицинские халаты, хирургические костюмы, костюмы для скорой помощи) и форма для персонала (одежда для сотрудников торговой сети, одежда для официантов и обслуживающего персонала фартуки для официантов и персонала ресторана, униформа для гостиниц, униформа для поворов). Изделие имеют всю группу размеров и ростов, а так же насыщены различной цветовой гаммой. Вся продукция изготавливается с учетом профессиональных требований в области медицины
Качество: Хорошо отлаженное швейное производство, контроль качества на каждом этапе, привлечение высокопрофессиональных специалистов и консультантов для независимой экспертной оценки качества выпускаемой продукции.
Оборудование: Современное швейное оборудование для пошива и производства медицинской одежды, постоянная модернизация технического оснащения.
|
|
Ткань: Используется современные ткани с корово и водоотталкивающей пропиткой, а так же с разными процентными содержанием хлопкового волокни от 35% до 80%. Все материалы сертифицированы.
Сроки исполнения заказов от14 до 30 дней( в зависимости от сложности и объема заказа).
С каждым годом проводится большая работа по внедрению нового ассортимента, а также создаются и осваиваются новые виды изделий.
Сегодня на предприятии работает 50 человек. Предприятие работает в одну смену: с 8.00 до 17.00. обеденный перерыв в соответствии с графиком.
На предприятии может изготавливаться до 100 моделей в месяц, это зависит от величины заказа или партии. Сроки выполнения заказов устанавливаются фирмами, но также зависят от времени на транспортировку сырья и готовых изделий, что связано с большой удалённостью фирм заказчиков и сложностью оформления документов для перевозки через границу.
Структура предприятия
Структура предприятия представлена на Схеме 1.
Организация внутрифабричного и внутрицехового транспорта
При проектировании потока необходимо выбрать такие транспортные средства, которые реализуют главное требование планировки - непрерывность передачи полуфабрикатов. Это означает, что рабочие места и транспортные средства должны быть взаимоувязаны таким образом, чтобы каждый исполнитель имел возможность взять полуфабрикат для обработки с предыдущей операции и передать на последующую, не меняя своей основной рабочей позы.
|
|
Кроме того, для удобства обслуживания следует выбирать минимально необходимое количество видов транспортных средств для одного потока, цеха и предприятия в целом.
Бесприводные транспортные средства являются самыми простыми и экономичными в изготовлении и эксплуатации. Они применяются для транспортировки полуфабрикатов от одного рабочего места к другому, а также для временного хранения полуфабрикатов при изготовлении различных швейных изделии. На предприятии проходившем преддепломную практику использовалось междустолье ,тележки и кронштейны. Выбор вида перемещения полуфабрикатов зависит от организационных и технологических условий работ.
Среди передвижных транспортных средств наибольшее распространение получили тележки, на которых пачки полуфабрикатов укладываются или навешиваются. Напольные тележки применяются для транспортировки и хранения пачек деталей, полуфабрикатов и готовых изделий при изготовлении изделий на любой стадии технологического процесса (заготовка, монтаж, отделка). На предприятии проходившем преддепломную практику использовалось междустолье ,тележки и кронштейны.
|
|
Правила внутреннего распорядка
Внутренний трудовой распорядок - это регламент (порядок) выполнения работниками работы у нанимателя под его руководством и контролем. Настоящие правила имеют целью обеспечение труда, укрепление его дисциплины, рациональное использование рабочего времени, улучшение качества работ, содействие росту производительности труда. Наниматель может требовать, а работники обязаны выполнять работу, обусловленную трудовым договором, с подчинением внутреннему трудовому распорядку. Настоящие правила внутреннего трудового распорядка обязательны как для работников, так и для нанимателей. Правила внутреннего трудового распорядка должны быть вывешены нанимателем на видном месте. И работники должны беспрекословно их соблюдать, и подчиняться им.
Ознакомление с работой цехов
Экспериментальный цех
|
|
Основной задачей экспериментального цеха ООО « БелАгроВет» является своевременная и качественная подготовка моделей к запуску в производство, к которой относится:
• разработка перспективного и текущего ассортимента изделий с учетом изучения спроса, конъюнктур рынка и направлений моды;
• моделирование;
• конструкторско-технологическая проработка новых моделей;
• разработка оптимальных режимов технологического процесса;
• изготовление лекал;
• нормирование расхода всех материалов;
• подготовка технической документации на модель.
В соответствии с задачами экспериментального цеха в нем выделяются следующие группы: 1-моделирования; 2- конструирования; 3-технологическая; 4- лекальная; 5- нормирования.
При разработке моделей на предприятии, модельер выполняет серию эскизов моделей, которые рассматривает и утверждает художественно-технический совет. После того как некоторые эскизы утверждены, начинается работа по созданию конструкции. Конструкторскую проработку новых моделей выполняет инженер-конструктор, она состоит в разработке всех видов лекал в необходимом количестве. Сначала разрабатываются лекала на базовый размеро-рост, а затем выполняется градация лекал, с помощью Инвестроника и Лектра. Проверка систем размножения деталей выполняется в натуральную величину. Для этого конструктор заказывает для зарисовки на плоттере схему размножения каждой детали по размерам и ростам, он проверяет сопряжение деталей, совпадение надсечек, составляет табель мер. После того, как лекала получены, конструктор по лекалам-эталонам вручную изготавливает вспомогательные лекала.
Совместно с конструкторской проработкой идет технологическая, которую выполняет инженер-технолог. Она заключается в разработке технологии изготовления новой модели, с учетом конструкции деталей, свойств материалов и существующих на предприятии условий производства. Совместно с технологом сотрудничают лаборанты-портные, которые выполняют раскрой опытного образца, и его изготовление. В процессе проработки выявляются недостатки конструкции, технологии и вносятся изменения для их устранения. С целью проверки пригодности модели к изготовлению в условиях массового производства, прошивается опытная партия моделей. Для производственных целей в экспериментальном цехе изготавливается несколько образцов-эталонов. Если модель разрабатывается на внутренний рынок, то технолог составляет техническое описание внешнего вида модели и особенности обработки, если на фирму, то только особенности обработки. После того, как прошит образец и лекала утверждены, их передают лекальной группе. Также лекальная группа может изготавливать 1-2 экземпляра для выполнения экспериментальных раскладок в группе нормирования, это обычно выполняют для тканей в клетку или полоску.
Нормирование расхода материалов является одной из наиболее трудоемких работ ЭП. От ее правильного проведения во многом зависит экономное расходование материалов.
Производственный отдел даст инженеру нормировщику шкалу размеров и ростов соответствующих удельных весов, по которой нормировщик составляет сочетания. Из опыта работы данного предприятия замечено, что обычные способы составления сочетаний не всегда приемлемы, поэтому здесь в одно сочетание ставят самый большой и самый маленький размер. Затем для раскладчика выписывается отдельный бланк задания, в котором указывается: % межлекальных отходов, ширина ткани, поверхность, вид раскладки, а конструктор дает раскладчику папку с кодами деталей данной модели. После того, как раскладка выполнена, раскладчик выполняет ее проверку, следит, не превышает ли процент межлекальных выпадов допустимых норм, и проверяет соответствие предварительным нормам на раскладку. Если все правильно, то раскладка сдается в базу данных главного компьютера на хранение. Если же какая-то из полученных норм не устраивает, то вызывают представителя фирмы и согласовывают с ним увеличение норм на данную модель.
Подготовительный цех
В подготовительном цехе осуществляют приемку материалов, их хранение, промер длины и ширины, определение координат текстильных пороков, расчет кусков материалов для использования их с минимальными остатками, своевременный подбор и передача их в раскройный цех.
На фабрику материалы доставляют автотранспортом в рулонах, запакованных в полиэтиленовую пленку. Принимаются материалы путем проверки количества товарных мест и их номеров с записью в сопроводительном документе отправителя. На принятую ткань заполняется приходной ордер в 2-х экземплярах. Претензии о недостаче материала по количеству, или о несоответствии его качеству направляют поставщику не позднее, чем в 14-дневный срок.
Разгрузка рулонов с автотранспорта осуществляется вручную. Нераспакованные рулоны хранятся в специально отведенных для этого местах.
Распаковка осуществляется в зоне разбраковки и промера, при этом начинается заполнение промерочной ведомости на каждый артикул ткани отдельно. В ней записывают номер куска, присвоенный ему на текстильном предприятии, порядковый номер куска, присвоенный ему на швейном предприятии, наименование и артикул материала, количество погонных метров и ширину, указанную в ярлыке предприятия-поставщика. Распаковку осуществляют вручную, при этом используют нож, ножницы, материалы размещают отдельно, в соответствии с назначением и видом.
Разбраковку и промер материалов выполняют с целью проверки сорта материала, точного измерения длины и ширины кусков, отметки определения координат текстильных пороков. Проверке надлежит вся партия поступившего материала, за исключением прокладки, которую не разбраковывают и не промеряют в целях сохранения клеевого покрытия, в этом случае принимают данные текстильного предприятия. Ткани промеряют на 3-х метровых промерочных столах, оснащенных концевыми линейками. Промеренную ткань разбраковывают на браковочно-промерочных машинах БМ-180.
Результаты разбраковки и промера каждого куска заносят в его паспорт, заполняемый в 2-ух экземплярах: 1-ый используется для расчета кусков, 2-ой прикрепляется к куску и содержит: артикул ткани, номер модели, длину и ширину куска, условные и фактические отрезы. Если в куске имеются фактические разрезы, то отрезы проверяют на разнооттеночность, в случае ее обнаружения на отрезы оформляются паспорта на отдельные куски. Данные измерения длинны и ширины также заносятся в промерочную ведомость. По ней проверяют недостачу материала по площади в кусках, которые имеют отклонения фактической ширины от указанной в ярлыке.
Сроки хранения ткани, а также величина запаса на участке составляет около 20 дней, но в связи с нестабильностью сегодняшнего времени может меняется в зависимости от сроков поставки, дальности расположения поставщика, величины партии. Условия хранения материалов: влажность воздуха 65%, температура 18-21°С. Подготовка материалов для подачи в раскройный цех осуществляется на основании карты расчета и в соответствии с графикам раскроя.
Рулоны материалов выбираются из зоны хранения в порядке их записи в раcчетно-планировочной карте. На каждую расчетно-планировочную карту выписывается карта раскроя, в ней представляется опись рулонов материалов в той же последовательности, что и в карте расчета, с указанием количества погонных метров и ширины ткани в каждом куске. Отпускают ткани в раскройный цех по данным фактического промера ткани, при этом оформляется "накладная на отпуск ткани в раскройный цех ".
Сущность расчета кусков состоит в условии расчленения его на полотна, длины которых равны длине настилов, таким образом, чтобы сумма длин полотен равнялась длине куска. Такой расчет редко удается получить, поэтому расчет куска условно принято считать безостатковым, если остаток от него не превышает допускаемой величины (на данном предприятии он составляет 0,5-2 см.) и зависит от длины куска, способа раскладки, структуры ткани. Задача расчета кусков является многовариантной трудновыполнимой, поэтому для облегчения работы используется автоматизированный способ расчета, выполняемый на ЭВМ. Основной целью данного расчета является:
• расчет одного куска на минимальное количество настилов;
• обеспечение минимальной величины концевых неучитываемых остатков от кусков;
• минимальное количество нерациональных остатков;
• высота настилов достигает максимальной, технически возможной или приближается к ней;
• выполняется требования графика раскроя.
Сочетание размеров и ростов, включенных в карту расчета, и количество изделий по каждому из них определяется графиком раскроя. Норма на раскладку поступает из экспериментального цеха отдела нормирования.
Каждая расчетная карта анализируется по следующим показателям:
• средняя высота настила;
• процент нерациональных отходов;
• процент одиночек;
• наличие рациональных остатков (весовой лоскут, угары, брак);
Раскройный цех
Основными функциями раскройного цеха являются:
• Постоянное повышение технического уровня производства.
• Внедрение новых методов организации производства.
• Максимальное использование производственных мощностей.
• Строгое соблюдение техники безопасности.
Основные технические операции:
• прием основного, подкладочного, прокладочного и отделочного материала;
• Прием обмеловок, выполненных на графопостроителе;
• Настилание материалов;
• Выделение в индивидуальный раскрой полотен с дефектами;
• Контроль качества настилания;
• Рассекание настилов на части;
• Точное вырезание деталей;
• Дублирование отдельных деталей, контроль качества кроя;
• Нумерация деталей кроя;
• Комплектование кроя в пачки;
• Заполнение сопровождающих крой документов, талонов, ярлыков;
• Упаковка кроя;
• Отправление на хранение.
Рулоны ткани из подготовительного цеха поступают в раскройный цех. Приемка материалов, поступающих из подготовительного цеха, производится мастером цеха, путем проверки соответствия данных о количестве кусков ткани, их длины, ширины и артикула напаспортах кусков, данным карты расчета. После чего укладываются на поддоны или на многоярусные накопители, где хранятся некоторое время. Затем в соответствии с производственной программой, рулоны доставляют на рабочее место для настилания. Настилание материалов выполняется на машине PIONER SUPER или па машине PIONER PROFESSIONAL, для настилания различными способами.
Настилание тканей выполняют универсальные бригады. Высота настилания зависят от толщины материала. Ткани в клетку и полоску настилают вручную на настилочных столах. Для настилания вручную применяют настилочные столы с прижимными концевыми линейками, обрезными линейками, устройствами для размотки рулона.
Контроль качества готового настила предусматривает проверку соблюдений основных технологических требовании, предъявляемых к настилу и выполняется самими рабочими, а также мастером в течении всей смены.
После настилания на верхнем полотне записывается размер, рост, указывается направление ворса стрелкой. Зарисовка раскладки, выполненная на бумаге, накладывается на верхнее полотно и закрепляется.
Документальное оформление настила представляет учет расхода материала на настил и является заключительной операцией по подготовке настила к раскрою. Оно включает:
• проверку общего количества полотен в настиле и количество полотен по артикулам;
• уточнение фактической длины настила;
• подсчет количества и общей длины остатков от кусков по артикулам;
• запись в карте раскроя результатов использования ткани, высоты настила, длины раскладки, количества стыков и концов в настиле, данных о количестве изделий.
Информация о настиле вводится в компьютер или передается для выписки маршрутных листов, после этого настилподается на раскрой. Дальнейшими операциями являются: разрезание настила на частии вырезание крупных деталей на передвижном раскройном оборудовании; транспортирование частей настила к стационарным ленточным настилам; вырезание деталей на стационарных ленточных машинах.
Для рассекания настила на части на фабрике используется ручная раскройная машина с вертикальным ножом КУ-1602. Применяют такие ручные раскройные передвижные машины, CS 529 A, CS 529 B, CS 529 C и стационарные ЯВ5 300.
Сборка и комплектовка пачек предусматривает комплектование пачек всех деталей, принадлежащих одному изделию определенного размера, роста и модели, при комплектовки используется перечень деталей кроя для каждой модели.
Дублирование деталей выполняется в раскройном цеху на дублирующих установках. Режимы и параметры дублирования зависят от свойств материала и устанавливается в экспериментальной лаборатории. После дублирования проверяют соответствие контуров деталей лекал, т. к. некоторые ткани могут дать усадку или наоборот растянуться. В этом случае предусматривается осноровка деталей. Окончательно детали кроя комплектуются и укладываются в тележки в размерах, определяемых количеством полотен в настиле. Крупные детали укладываются вниз, мелкие наверх.
Маршрутные листы печатаются на ЭВМ. Маршрутные листы сопровождают весь маршрут следования кроя, полуфабриката и готовых изделий, полученных из него. В маршрутных листах указываются следующие данные:
• номер цеха, бригады, смены, для которой предназначен крой:
• номер карты раскроя и номер раскладки (выкладки), по которой был выполнен раскрой материала;
• наименование изделия;
• номер модели;
• размер, рост;
• артикул основного и подкладочного материала.
Швейный цех
В швейном цехе на технологических потоках, оснащённых стачивающими и специальными машинами, а также оборудованием для ВТО, шьют изделия. При этом потоки могут быть однофасонные, многофасонные и много ассортиментные.
Основными задачами пошивочного цеха являются:
- обеспечение своевременного и ритмичного выполнения производственного плана по всем технико-экономическим показателям;
- постоянное повышение производительности труда, выпуск продукции высокого качества;
- постоянное повышение технического уровня производства;
Функции швейного цеха:
- проверка качества кроя (организует своевременное обеспечение процессов комплектов и качественным кроем, фурнитурой и другими материалами);
- организация качественного изготовления швейных изделий, соответствующим техническим условиям;
- обеспечение ритмичной передаче изделий в процессе производства;
- соблюдение технологической дисциплины, своевременно устранять выявленные дефекты пошива;
- обеспечение своевременного выпуска изделия и производства в соответствии с графиком запуска.
Готовые изделия передаются на отделку. В цехе отделки производят ВТО, в результате которой готовым изделиям придают товарный вид. Также в цехе отделки изделия чистят, обметывают петли, пришивают пуговицы и комплектуют. После готовые изделия поступают на склад готовой продукции.
3 Работа в качестве мастера участка(дублера мастера участка)
Мастер является непосредственным руководителем трудового коллектива, организатором труда и производства. Он подчиняется начальнику смены и начальнику цеха, а также мастеру потока с более высоким квалификационным разрядом.
Основные задачи мастера:
- обеспечение выполнения плановых заданий;
- снижение затрат на единицу продукции;
- изготовление продукции высокого качества;
- повышение производительности труда;
- строгое соблюдение дисциплины, правил техники безопасности и охраны труда.
Мастер осуществляет руководство возглавляемым им участком, обеспечивает запуск и выпуск модели, своевременно подготавливает производство, обеспечивает расстановку рабочих, контролирует соблюдение технологических процессов, проверяет качество выпускаемой продукции, осуществляет производственный инструктаж рабочих. Также мастер участвует в присвоении рабочим тарифных разрядов, премирует рабочих из специального фонда мастера, представляет их к другим видам премирования и поощрения. Мастер с разрешения начальника цеха имеет право отстранять от работы лиц, систематически нарушающих производственную и трудовую дисциплину, прекращать работы на неисправном оборудовании, запрещать обработку недоброкачественного сырья, материалов, полуфабрикатов.
Дата добавления: 2018-02-18; просмотров: 1160; Мы поможем в написании вашей работы! |
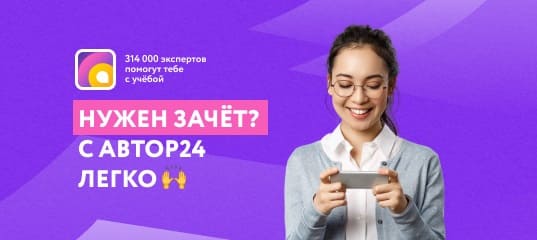
Мы поможем в написании ваших работ!