Определение критических частот роторной системы.
При определении критических частот вращения роторной системы были приняты следующие условия моделирования:
- глобальный контакт – «связанные»;
- набор соприкасаний элементов сборки – «связанные»;
- сетка криволинейная, высокого качества;
- диск турбины моделируется как абсолютно жесткое тело;
- в качестве опор моделируются подшипники качения с условием «самовыравнивания» (двухрядный, сферический шарикоподшипник).
В связи со сложностью построения сетки на натурном диске турбины, как абсолютно жесткое тело, (наличие радиусов, фасок на теле лопаток, при количестве 100 лопатки), натурный диск турбины был заменен упрощенным элементом (без лопаток) с аналогичной массой, полярным и диаметральным моментом инерции.
Результаты вычислений собственных частот не вращающейся роторной системы приведены на рис. 8.20 и 8.21.
Рис. 8.20. Колебания ротора турбины
Рис. 8.21. Колебания ротора турбины
Как видно из результатов вычислений собственных частот не вращающейся роторной системы собственная частота первой формы колебаний равняется 628 Гц. Эта величина в 12 раз больше рабочей частоты. В связи с этим нет необходимости определять критические частоты прямой и обратной синхронной прецессии первой формы колебаний и обратной синхронной прецессии второй формы колебаний.
Расчет диска турбины на прочность.
На этапе эскизного проектирования определялась геометрия диска турбины. Допущением при расчете эквивалентных напряжений в диске турбины являлось следующее условие:
|
|
- в процессе численного моделирования отсутствуют призонные болты, гайки и элементы контровки;
- в системе «диск – вал» применялось условие «непроникновение». В сборке вал использовался для фиксации роторной системы в пространстве. Для фиксации применились подшипники качения. Такое допущение, при численном моделировании, не существенно влияет на результаты вычислений эквивалентных напряжений в диске турбины. Моделирование роторной системы с призонными болтами показывает увеличение эквивалентных напряжений на 1.3% (появляются напряжения в зоне затяжки гаек призонных болтов) при значительном увеличении времени вычислений и сложного процесса сборки роторной системы (результаты вычислений сборки роторной системы в данном разделе не приводятся). Необходимо добавит что, использование виртуальных болтов так – же увеличивает время вычислений эквивалентных напряжений в элементах роторной системы.
Основные условия численного моделирования;
- частота вращения роторной системы увеличена по сравнению с расчетной и принята равной – 350 рад./сек. (3340 об/мин). Такое условие частично компенсирует моделирование сборки без призонных болтов. Расчетное значение частоты вращения роторной системы – 314 рад./сек. (3000 об/мин);
|
|
- градиент температуры в объеме диска турбины отсутствует (равен нулю);
- температура материала диска турбины принята постоянной и равна – 300 К.;
- при моделировании упрощенного варианта сборки, выбрана сетка криволинейная, высокого качества;
- предел текучести материала диска турбины – 75 МПа (минимальное значение для алюминиевых сплавов).
Необходимо отметить, что выбор материал, для изготовления диска турбины, в первую очередь будут зависеть не от прочностных характеристик материала а от качества литейных свойств выбранного материала. Вследствие этого прочностные характеристики материала, для изготовления, диска турбины будут естественно зависеть от применяемого материала. Диск турбины должен изготавливаться методом прецизионного литья, вследствие этого предел текучести материала диска турбины может возрасти до значения порядка 160 - 200 МПа.
Результаты численного моделирования эквивалентных напряжений в диске турбины представлены на рис. 8.22 и 8.23.
|
|
Рис.22. Напряжения в диске турбины
На рис. 8.22 показано распределение максимальных и минимальных эквивалентных напряжений, вычисленных для моделируемой роторной системы.
Рис. 8.23. Распределение запаса прочности
На рис. 8.23 показано распределение максимальных и минимальных значений запаса прочности. Минимальное значение запаса прочности (для материала с пределом текучести 75 МПа – 2.73).
По результатам расчетов можно сделать следующие выводы.
Для материала диска турбины, обладающего минимальным пределом текучести запас прочности более чем достаточный. На рис. 8.23 наглядно видно, что запас прочности (2,73) находится в области центрального отверстия диска турбины и отверстий для призонных болтов. Максимальное напряжение, в роторной системе, находится в области соединения вала с диском (рис. 8.22). Предел текучести материала вала - 530 МПа. Запас прочности вала в этом месте составляет значение - 17.6.
Расчет призонных болтов.
Исходные данные для расчета призонных болтов.
Эффективная мощность турбины - 720000 Вт
Рабочая частота вращения - 314 рад/с
Крутящий момент на валу отбора мощности - 2293 Н*м
Осевое усилие затяжки каждого болта - 3000 Н
|
|
Материал | Предел текучести | Предел прочности при растяжении | Используемые детали |
Алюминий 3003-Н18 | 185 МПа | 200 МПа | Диск турбины |
Сталь AISI 1045 | 530 МПа | 625 МПа | Вал и призонные болты |
Условия моделирования.
1. Вращающий момент приложен к нижнему бандажу турбины (рис.8.25).
2. Диск турбины не имеет лопаток (уменьшается количество конечных элементов и соответственно время вычисления).
В расчётной модели (рис. 8.24) были приняты следующие допущения:
1. В качестве болтового соединения используется упрощённая модель без резьбы (рис.26) (уменьшается время вычисления, затяжка болтового соединения регламентируется удлинением призонного болта).
2. Не учитывается крутящий момент при затяжке болтового соединения (не известны достоверные значения коэффициентов рения покоя и движения). Вследствие такого условия моделирования, призонный болт не воспринимает крутящий момент во время процесса затяжки. Такое допущение, на первом этапе моделирования справедливо только в том случае, если в дальнейшем будет проведено исследование на предмет несущей способности, отдельно взятого болтового соединения, с условием наличия при моделировании всех нагрузочных факторов. Такие исследования были проведены для различного ряда коэффициентов трения покоя и движения (в данном разделе не описаны). Результат исследований показал правомерность вышеуказанного допущения в связи с полученным высоким (n>5) запасом прочности болтового соединения.
На рис. 8.24 показана расчетная модель болтового соединения диска турбины и вала.
|
|

|
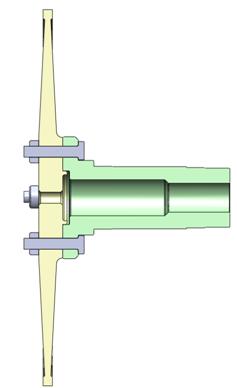
На рис. 8.25 и 8.26 показана схема нагружения основных элементов турбопривода
|

|
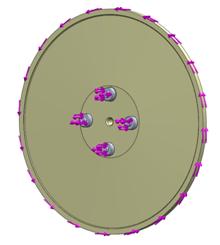
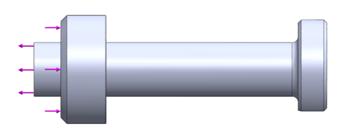
Рис. 8.25. Схема нагружения Рис. 8.26. Схема нагружения
При моделировании рассматривались два случая жесткой фиксации вала отбора мощности.
1. Место закрепления в области опоры со стороны диска турбины (жесткая заделка) на валу (место закрепления выделено, синим цветом) (рис. 8.27).
2. Место закрепления в области опоры на валу со стороны компенсирующей муфты (жесткая заделка) (место закрепления выделено, синим цветом).
На рис. 8.27 и 8.28 показано место фиксации и сетка для расчёта модели.
Сетка уменьшена на отверстиях в диске, валу, а так же на поверхности болта и поверхности соприкосновения гайки и диска. Это сделано для проверки сходимости результатов.
Рис. 8.27. Место фиксации Рис. 8.28. Расчетная модель
Результаты расчётов представлены на рис. 8.29 – 8.31
Рис. 8.29. Распределение напряжений
Максимальны, эквивалентные напряжения располагаются в болтовом соединении, у головки призонного болта и составляют 32 МПа.
Минимальное значение запаса прочности (рис. 30): n>5 расположено в местах скругления болта у головки. Вычисления производились в среде Solid Works Simulation 2010 [6,7]. В этой среде, при импорте в формат JPEG, данный формат не распознает указатели максимальных и минимальных напряжений, запаса прочности и деформации.
Рис. 8.30. Распределение запаса прочности
На рис. 8.30. представлено распределение запаса прочности в сборочной единице. Минимальное значение запаса прочности n=5.24.
На рис. 8.31. показано удлинение призонного болта при заданных исходных данных.
Рис. 8.31. Деформации узла
Максимальное удлинение призонного болта - 0.002 мм.
Для второго случая полученные параметры отличаются от первого на 5%. В связи с этим нет необходимости приводить эти данные.
По результатам расчетов можно сделать следующие выводы.
Болтовое соединение диска турбины и вала имеет запас прочности n>5 при наличии четырех призонных болтов. Но желание иметь более равномерное распределения удельного напряжения в зоне контакта «диск – вал» привело к решению применить не четыре, а восемь призонных болтов при эквивалентной поперечной площади сечения призонных болтов. Осевое усилие затяжки может изменяться исходя из условия обеспечения жесткого соединения и прочностных характеристик применяемых материалов.
Заключение
1. Проведены расчетные и конструкторские работы по созданию турбодетандерной установки для понижения давления магистрального природного газа с одновременной вырвботкой электроэнергии.
2. Разработана технологическая схема универсальной турбодетандерной установки без подогрева природного газа.
3. Проведено расчетное исследование по обоснованию применения осевой активной турбины в качестве силового агрегата для вращения электрогенератора переменного тока.
4. Приведена методика испытаний активной турбины на модельном рабочем теле – воздухе.
5. Проведен расчет параметров активной турбины на воздухе.
6. Определены параметры и предварительная схема стенда испытаний активной турбины на воздухе.
7. Разработана конструктивная схема универсальной турбодетандерной установки с активной турбиной эффективной мощности от 50 до 600 кВт.
8. Разработана конструкторская документация на турбопривод для УТДУ-1-Э с мощностью 720 кВт.
9. Для некоторых основных деталей турбопривода рассмотрены варианты изготовления различными методами и из различных материалов. Для экспериментальной модели диск активной турбины рекомендуется изготавливать из алюминиевого сплава методом механической обработки.
10. Проведены расчеты на прочность и колебания основных элементов турбопривода.
Дата добавления: 2018-02-18; просмотров: 785; Мы поможем в написании вашей работы! |
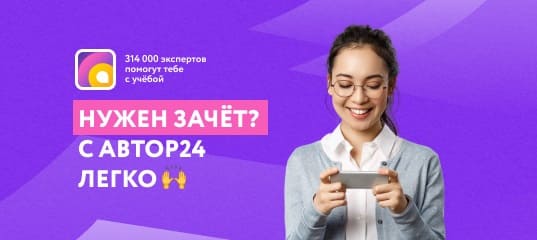
Мы поможем в написании ваших работ!