Основные схемы пылеприготовления.
Пылеприготовление производится в системе специальных устройств, в которых последовательно осувществляеются первоначальное грубое дробление (в валковых и молотковых дробилках) до кусков в несколько см, сушка и окончательный размол до пылевидного состояния с размером частиц в несколько десятков мкм. Часто размол и сушку совмещают. Принципиальные схемы систем пылеприготовления приведены на рис. 3.1.
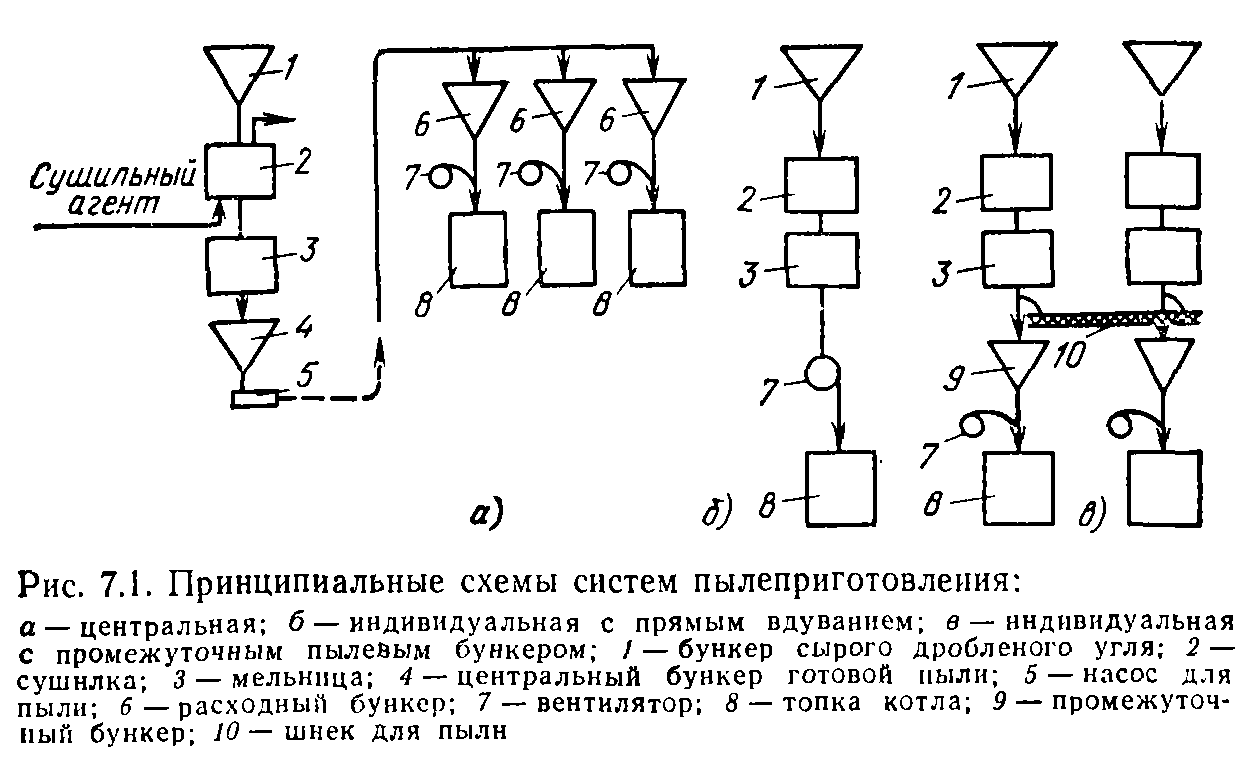
Рис. 3.1. Принципиальные схемы систем пылеприготовления: а – центральная; б – индивидуальная с прямым вдуванием; в – индивидуальная с промежуточным пылевым бункером; 1 – бункер сырого дроблённого угля; 2 – сушилка; 3 – мельница; 4 – центральный бункер готовой пыли; 5 – насос для пыли; 6 – расходный бункер; 7 – вентилятор; 8 – топка котла; 9 – промежуточный бункер; 10 – шнек для пыли.
Положительной особенностью схемы «а» является независимость размольных установок от работы котла, мельница может работать с полной нагрузкой периодически. У неё потери тепла при сушке. Она применяется для блоков 500-800МВт.
Система «б» имеет жёсткую связь мпельничного оборудования с котлом. Её применяют при сжигании высокореактивных бурых и каменных углей, допускающих грубый помол.
Система «в» с пылевым бункером повышает надёжность установки и её применяют для мощных котлов при работе на тощих и малореакционныхуглях, требующих тонкого помола.
Сушку топлива различат по замкнутой (сушильный агент с пылью сбрасывается в топку) и разомкнутой (сушильный агент сбрасывается в атмосферу) схеме (см. рис. 3.2).
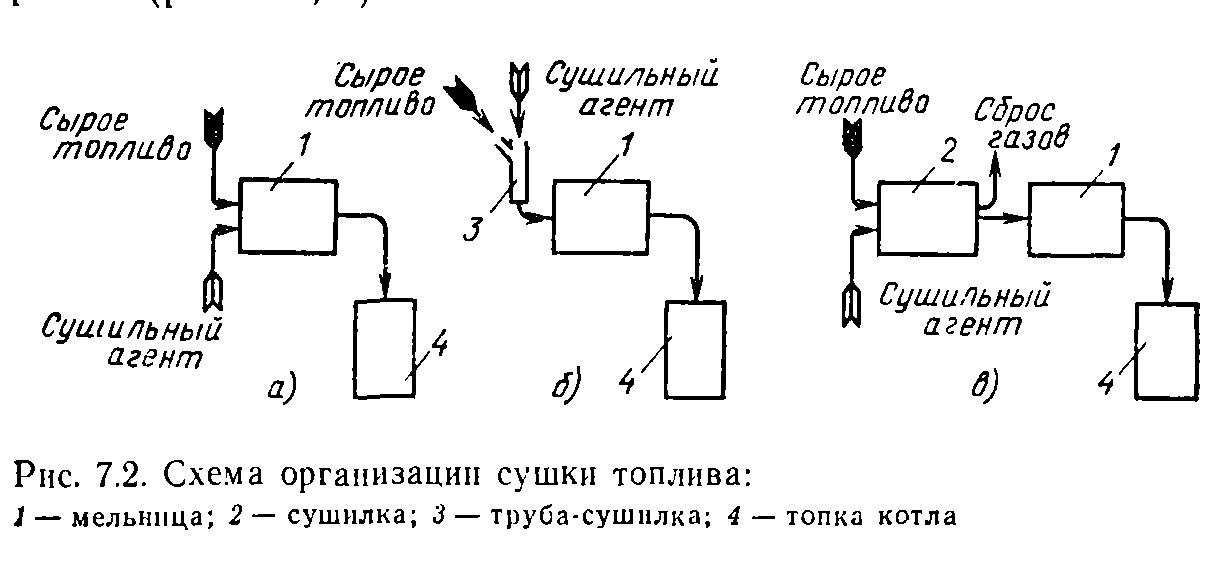
Рис. 3.2. Схемы организации сушки топлива: 1 – мельница; 2 – сушилка; 3 – труба-сушилка; 4 – топеа котла.
Схева «а» применяется для относительно сухих углей (внешней влажности до 10%) и происходит одновременно с размолом.
Схема «б» с сушильными трубами применяется для топлив с внешней влажности до 20%.
Для высоковлажных топлив (внешней влажности более 20%) применяется схема «в».
Для предварительной подсушки топлива перед мельницей применяют следующие типы сушилок:
Газовые барабанные;
Паровые трубчатые;
Пневматические (трубы-сушилки);
С кипящим слоем.
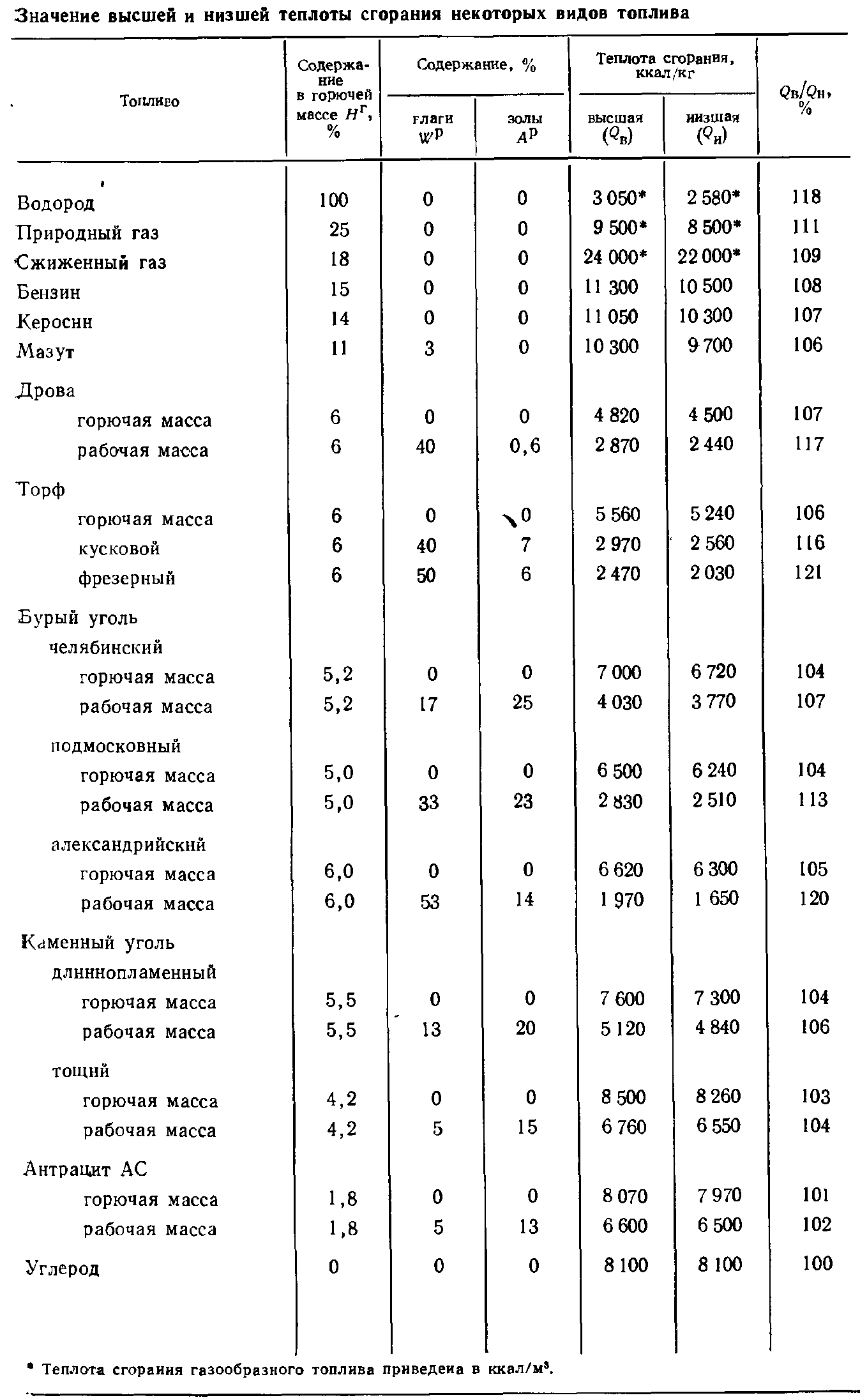
Паровые котельные установки
Котельная установка – это комплекс устройств, предназначенных для получения пара или горячей воды. Котельная установка может быть одной из составляющих тепловой электростанции или выполнять самостоятельные функции (отопление и горячее водоснабжение, технологическое водо- и пароснабжение.В зависимости от назначения котельная установка состоит из парового или водогрейного котла и вспомогательного оборудования, обеспечивающего его работу. Последовательно включенные элементы котельной установки образуют тракты.
Топливный тракт – комплекс оборудования для подготовки топлива к сжиганию и подачи в топку. При использовании твердого топлива в него могут входить бункера, питатели сырого топлива и пыли, углеразмольные мельницы, мельничные вентиляторы, сепараторы, транспортеры, пылепроводы и т.п. При сжигании газа и мазута - газопроводы и мазутопроводы, расходомеры, запорная и регулирующая арматура.
Пароводяной тракт – представляет собой систему последовательно включенных элементов оборудования, в которых движется обогреваемый теплоноситель (поверхности нагрева котла, трубопроводы, барабаны, сепараторы, пароохладители и теплообменники в пределах котла, запорная и регулирующая арматура).
Газовоздушный тракт состоит из последовательно расположенных воздушного и газового трактов. Первый из них включает в себя совокупность оборудования для забора воздуха из атмосферы, нагрева и подачи его в топку котла (дутьевые вентиляторы, воздушные короба, воздухоподогреватели и горелочные устройства), второй – комплекс элементов котельной установки, по которым осуществляется движение продуктов сгорания (топка и другие газоходы котла, устройства для очистки дымовых газов, дымососы).
Паровой (водогрейный) котел – это устройство, в котором для получения пара (горячей воды) требуемых параметров используют теплоту, выделяющуюся при сгорании органического топлива. Основные элементы котла – топка и теплообменные поверхности. Если в котле используют теплоту уходящих газов других технических устройств (ГТУ, технологических установок), его называют котлом-утилизатором. Котел-утилизатор в некоторых случаях не имеет топки и воздухоподогревателя, а его основные элементы – поверхности нагрева.
Классификация котлов. По виду вырабатываемого теплоносителя котельные установки делятся на
паровые и водогрейные. В зависимости от назначения они разделяются на
энергетические,
производственные, производственно-отопительные и отопительные. Энергетические котельные установки вырабатывают пар для паровых турбин на тепловых электростанциях. Такие котельные оборудуют, как правило, котлоагрегатами большой и средней мощности, которые вырабатывают пар повышенных параметров. Производственные и производственно-отопительные котельные установки (обычно паровые) вырабатывают насыщенный или слабо перегретый пар (до 4 МПа и 450 ºC), который используется в технологических процессах различных отраслей (сушка, варка, ректификация, концентрирование растворов и др.), а также для обеспечения теплотой систем отопления, вентиляции и горячего водоснабжения. Отопительные котельные установки (в основном водогрейные, но они могут быть и паровыми) предназначены для обслуживания систем отопления, горячего водоснабжения и вентиляции производственных и жилых помещений.По характеру движения воды, пароводяной смеси и пара паровые котлы подразделяются на барабанные с естественной циркуляцией, барабанные с многократной принудительной циркуляцией и прямоточные (рис. 4.1). В барабанных котлах с естественной циркуляцией движение пароводяной смеси в подъемных (обогреваемых) трубах и жидкости в опускных (необогреваемых) трубах происходит вследствие разности их плотностей. В котлах с многократной принудительной циркуляцией движение воды и пароводяной смеси осуществляется с помощью циркуляционного насоса. В прямоточных котлах нет циркуляционного контура, нет многократной циркуляции воды, отсутствует барабан, вода прокачивается питательным насосом через экономайзер, испарительные поверхности и пароперегреватель, включенные последовательно.По перемещению продуктов сгорания и воды котлы подразделяют на газотрубные (жаротрубные и с дымогарными трубами), в которых газы движутся внутри труб, водотрубные, в которых вода или пароводяная смесь движутся внутри труб и водотрубно-газотрубные.По конструктивным особенностям различают котлы цилиндрические, горизонтально-водотрубные, вертикально-водотрубные.В зависимости от паропроизводительности различают котлы малой (до 20 – 25 т/ч), средней (от 35 – 50 до 160 – 220 т/ч) и большой паропроизводительности (от 220 – 250 т/ч и выше). По уровню давления перегретого пара различают котлы с низким (ниже 4 МПа), средним ( от 4 до 11 МПа), высоким (более 11 МПа) и сверхкритическим давлением (выше 25 МПа).По уровню давления в газовом тракте различают котлы с естественной, уравновешенной тягой и под наддувом.Возможна также классификация по виду сжигаемого топлива, способу шлакоудаления и т.п.
|
|
Рис. 4.1. Схемы движения воды, пароводяной смеси и пара в котлах: а – барабанном с естественной циркуляцией; б – барабанном с многократной принудительной циркуляцией; в – прямоточном; 1 – барабан; 2 – пароперегреватель; 3 – водяной экономайзер; 4 – питательный насос; 5 – обогреваемые трубы; 6 – опускные трубы; 7 – циркуляционный насос.
Технологическая схема котельной установки, работающей на твёрдом топливе, представлена на рис. 1.12. Топливо, прошедшее дробидьный блок 3, мельницу 5, где мелко дробится, направляется в вентилятор - мельницу (эксгаустер) 6. Мельничный вентилятор служит для пневматического транспорта пыли в системе пылеприготовления и для обеспечения необходимых скоростей смеси воздуха и пылевидного топлива в горелках. Топливная пыль в горелке смешивается с закрученным потоком воздуха, подаваемым котельным вентилятором 11. Воздух, забирается венилятором с самого верха помещения или из межкожухового пространства котла, образованного стенками его внутреннего и наружного кожухов, подогревается и направляется в воздухоохладитель 10. Горячий воздух, выходящий из воздухоподогревателя, подходит к воздухонаправляющему устройству. Температура подогрева воздуха достигает 130—200ºС, это позволяет увеличить температурный напор в топке, улучшить протекание процессов смесеобразования и сгорания и повысить экономичность котла. Горячие газы, образовавшиеся в результате горения топлива, омывают поверхности нагрева, отдавая им свое тепло. Отработавшие газы с температурой 170—400ºС через золоуловитель 14 дымососом 15 отводятся через дымовую трубу 16 в атмосферу.
Рис. 1.12. Технологическая схема котельной установки, работающей на твёрдом топливе. 1 – вагон с топливом; 2 – бункер разгрузочного устройства; 3 – дробильный блок; 4 – бункер котла для сырого топлива; 5 – мельница для размола топлива; 6 – эксгаустер; 7 – барабан котла; 8 – пароперегреватель; 9 – экономайзер; 10 – воздухоподогреватель; 11 – вентилятор; 12 – деаэратор; 13 – питательный насос; 14 – золоуловитель; 15 – дымосос; 16 – дымовая труба; 17 – ленточный транспортёр; 18 – штабель угля; 19 – багерная насосная система золоудаления; а – питательная вода; б – перегретый пар; в – продукты сгорания; г – шлак и зола.Питательная вода, поступающая из деаэратора 12 в пароводяной барабан 7 и поддерживающая в нём постоянный уровень, предварительно подогревается в экономайзере 9. Температура воды на выходе из экономайзеров на 30—50ºС ниже температуры насыщения. В испарительной поверхности нагрева, образованной конвективным и экранным пучками, вода доводится до кипения. Отделение влажного насыщенного пара происходит в пароводяном коллекторе. Образовавшийся пар поступает в пароперегреватель 8, перегретый — к потребителям. Котлы небольшой производительности, как правило, не имеют пароперегревателей и производят влажный насыщенный пар.
Топочные устройства котлов.Топка – устройство котла, предназначенное для сжигания органического топлива, частичного охлаждения продуктов сгорания и выделения золы.Топки подразделяются на слоевые, камерные и вихревые. При слоевом процессе сжигания топлива (рис. 4.2, а) поток воздуха проходит через неподвижный или движущийся в поперечном направлении слой топлива. Чтобы частицы топлива, лежащие на решетке, не уносились потоком, их вес должен быть больше подъемной силы воздуха, действующей на каждую частицу. Характерной особенностью слоевого сжигания топлива является наличие значительного количества горящего топлива в топке. Это обеспечивает устойчивость работы топки и позволяет при изменении нагрузки котла регулировать работу топки первоначально только изменением количества подаваемого воздуха.
Рис. 4.2. Схемы топочных процессов сжигания топлива. Если крупнозернистое топливо находится во взвешенном состоянии и не перемещается с потоком газов, то образуется «кипящий слой» (рис. 4.2, б).При факельном топочном процессе (рис. 4.2, в) частицы топлива движутся вместе с газовоздушным потоком через топку, находясь во взвешенном состоянии. При этом время пребывания частиц топлива в топке незначительно, скорость обтекания частиц воздухом и количество горящего топлива также незначительные. Факельный процесс чувствителен к изменению режимов работы, поэтому необходимо тщательно регулировать подачу топлива и воздуха в топку. При вихревом топочном процессе частицы топлива организованно циркулируют по определенным траекториям до полного выгорания, поэтому в топках можно сжигать более крупные частицы (3–5 мм). Более совершенным вихревым топочным процессом является циклонный процесс (рис. 4.2, г).Работа топочных устройств характеризуется теплопроизводительностью (в МВт)
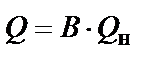
(B – секундный расход топлива, кг/с или м
3/с; Q
н – низшая теплота сгорания топлива, МДж/кг или МДж/м
3); объемной тепловой нагрузкой (в МВт/м
3) топки объемом V
т (qυ= B·Q
н / Vт); тепловой нагрузкой (в МВт/м
2) зеркала горения решетки площадью A
т (
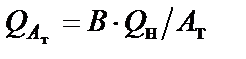
).Камерные топки позволяют сжигать любое топливо – жидкое, газообразное и твердое в виде пыли. Камерная топка состоит из горелок и топочной камеры.
Горелка – устройство, предназначенное для подачи топлива к месту смешения его с воздухом и сжигания, обеспечения стабильного сжигания и регулирования горения. По способу подачи в топочную камеру газа и воздуха и условий их смешения все газовые горелки разделяются на горелки без предварительного смешения (диффузионные), горелки с полным предварительным смешением (кинетические), горелки с неполным предварительным смешением (диффузионно-кинетические). Широко распространена классификация газовых горелок по способу подачи воздуха. По этому признаку горелки подразделяются на бездутьевые (воздух поступает в топку за счет разряжения в ней), инжекционные (воздух засасывается за счет энергии газовой струи), с принудительной подачей воздуха (воздух подается в горелку или в топку с помощью дутьевого вентилятора).В диффузионных горелках газ смешивается с воздухом в топке вследствие взаимной диффузии газа и воздуха на границах вытекающего потока. Диффузионные горелки дают более длинный светящийся факел.В инжекционных горелках воздух подсасывается за счет инжекции газовой струей, выходящей из сопла с большой скоростью. Такие горелки могут быть как с полным предварительным смешением газа с воздухом (инжекционные горелки среднего давления), так и с неполной инжекцией воздуха (инжекционные горелки низкого давления).В горелках с принудительной подачей воздуха процесс образования газовоздушной смеси начинается в самой горелке и завершается в топке. Такие горелки называются двухпроводными и смесительными (газ и воздух подаются по двум трубам и смешиваются в горелке). Газ для лучшего перемешивания выходит через многочисленные отверстия, направленные под углом к потоку воздуха. В зависимости от направления газового потока различают горелки с центральной подачей газа, если поток направлен от центра к периферии, и горелки с периферийной подачей газа, если поток газа направлен от периферии к центру горелки. В большинстве таких горелок воздуху придается вращательное движение с помощью завихрителей, либо придавая горелке улиткообразную форму или вводя воздух в цилиндрическую горелку тангенциально. Эффективное и экономичное сжигание мазута достигается в результате его тонкого и однородного распыления, хорошего смешивания с воздухом и создания условий для стабилизации фронта загорания и стойкого факела необходимой формы и направления.Мазутные горелки состоят из форсунки, воздухонаправляющего устройства и амбразуры. Форсунки предназначены для распыления жидкого топлива и регулирования его подачи, а воздухонаправляющие устройства и амбразуры – для создания однородной воздушно-мазутной смеси и ее распределения в топочном пространстве.Чаще всего форсунки классифицируются по способу распыления топлива. Форсунки, в которых распыление топлива происходит за счет потенциальной энергии мазута, находящегося под высоким давлением, называются механическими. Форсунки, в которых для распыления мазута используется кинетическая энергия распыляющего агента (пар, воздух), называются пневматическими. Форсунки, в которых для распыления мазута используется механическая энергия вращательного распылителя (диск или стакан), называются ротационными.В механических форсунках подогретое топливо под давлением пропускается через мелкие отверстия распыливающей головки. Механические форсунки компактны, но чувствительны к отклонениям от расчетных режимов работы и загрязнениям топлива. Паровые форсунки характеризуются высоким качеством распыления, но расходуют большое количество пара. Комбинированные паромеханические форсунки обеспечивают удовлетворительное распыление мазута в широком диапазоне изменения мощности форсунки (от 20 до 100 %) при существенно меньшем расходе пара.
Рис. 4.4 Схема газомазутной горелки ГМГМ: 1 – газовый канал; 2 – завихритель вторичного воздуха; 3 – монтажная плита; 4 – завихритель первичного воздуха; 5 – газовыходные отверстия; 6 – паромеханическая форсунка.
Широкое применение находят комбинированные газомазутные горелки, предназначенные для раздельного и совместного сжигания газа и мазута. За основу создания таких горелок принимают обычно газовые горелки, в центральную часть которых устанавливают мазутную форсунку (рис. 4.4).Для камерного сжигания пылевидного твердого топлива применяют вихревые и прямоточные щелевые горелки. Принципиальные схемы вихревых горелок приведены на рис. 4.5. Наименование горелки отражает способ ввода первичного (с пылью) и вторичного воздуха.
Рис. 4.5. Схемы пылеугольных горелок: а – прямоточно-улиточная; б – прямоточно-лопаточная; в – двухулиточная; I – первичный воздух с угольной пылью; II – вторичный воздух.
Принцип работы парового барабанного котла с естественной циркуляцией.В общем случае технологический процесс получения пара в барабанном паровом котле осуществляется в следующей последовательности (рис. 4.6). Топливо при помощи горелочных устройств 1 вводится в топку, где и сгорает. Воздух, необходимый для сгорания топлива, подается в топку дутьевым вентилятором или подсасывается через колосниковую решетку – при естественной тяге.Для улучшения процесса сгорания топлива и повышения экономичности работы котла воздух перед подачей в топку предварительно подогревается дымовыми газами в воздухоподогревателе 8.Дымовые газы, отдав часть своего тепла радиационным поверхностям нагрева, размещенным в топочной камере, поступают в конвективную поверхность нагрева, охлаждаются и дымососом удаляются через дымовую трубу в атмосферу.Сырая водопроводная вода проходит через катионитовые фильтры, умягчается и далее поступает в деаэратор, где из нее удаляются коррозионно-активные газы (O2 и CO2) и стекает в бак деаэрированной воды. Из бака питательная вода забирается питательными насосами и подается в экономайзер 7 парового котла. Нагретая теплом дымовых газов вода из экономайзера поступает в верхний барабан 4 котла, откуда по опускным трубам 3 направляется в коллектора экранов 10–12 или в нижний барабан. Возвращаясь по подъемным трубам 2 в верхний барабан, часть воды испаряется. В верхнем барабане происходит отделение пара от воды. Пар направляется в пароперегреватель 5 (если это необходимо), где он перегревается до требуемой температуры. Затем перегретый пар поступает в общий паровой коллектор, откуда подается потребителям.
Рис. 4.6. Принципиальная схема парового котла: 1 – газомазутная горелка; 2 – подъемные (экранные) трубы; 3 – опускные трубы; 4 – барабан; 5 – пароперегреватель; 6 – поверхностный пароохладитель; 7 – водяной экономайзер; 8 – трубчатый воздухоподогреватель; 9 – линия рециркуляции воды; 10 – коллектор заднего экрана; 11 – коллектор бокового экрана; 12 – коллектор фронтового экрана; 13 – фестон; п.в – питательная вода; н.п – насыщенный пар; п.п – перегретый пар; х.в – холодный воздух; г.в – горячий воздух; т – топливо; у.г – уходящие газы.
Удаление шлака и золыТопочная камера может работать
с удалением шлаков в твердом состоянии (топка с твердым шлакоудалением) либо выводом шлаков из топки в жидком состоянии (топка с жидким шлакоудалением). В любом случае золовые фракции уносятся с потоком газов из топки в отвердевшем состоянии.
Рис. 4.7 Схема образования шлака и золы в котле.
Рис. 2.1. Топка с твердым шлакоудалением: 1 - холодная воронка; 2 - шлаковая ванна с водой; 3 - канал гидрозолоудаления; 4 - горелка; 5 - настенные экраны; 6 - ядро факела; 7 - шнековый шлакоудаляющий механизм; в – электродвигатель
Рис. 2.2. Топочная камера с жидким шлакоудалением: а - общий вид топки; б - вид футерованного экрана; 1 - камера сгорания; 2 - под топки; 3 - шлаковая летка; 4 - камера охлаждения; 5 - труба; 6 - шипы до их покрытия обмазкой; 7 - огнеупорная обмазка труб (футеровка) по шипам. Выпавшие в топке и газоходах котельного агрегата в результате сгорания топлива шлак и золу, а также летучую золу, улавливаемую в золоуловителе, удаляют из котельного агрегата, а затем из помещения котельной.Основными способами шлакозолоудаления являются:- вагонеточный – для котельных с котлами старой конструкции;- механический – скреперный, скребковый и др., как правило, следует предусматривать в котельных с котлами, оборудованными топками для слоевого сжигания топлива;- гидравлический – в котельных с котлами для камерного сжигания твердого топлива и при выходе очаговых остатков 12 т/ч и более;- пневматический – может применяться независимо от способа сжигания топлива при выходе шлака и золы от 4 до 12 т/ч;- пневмогидравлический – применяется в котельных с котлами малой и средней производительности при расположении золоотвала на небольшом расстоянии от котельной. Такой способ золошлакоудаления применяется при реконструкции существующих котельных, в которых шлаковые и золовые бункера котлов находятся ниже отметки каналов гидрозолоудаления.При вагонеточном способе золошлакоудаления золу и шлак выгружают несколько раз в смену из бункеров под котлами в вагонетки с опрокидывающимся кузовом. Перед выгрузкой в вагонетки шлак в бункере охлаждается и обильно увлажняется водой из специально установленных для разбрызгивания воды сопл. Для предохранения персонала от ожогов и вредных газов шлак спускают в вагонетки в закрытых вентилируемых камерах.Большое применение в котельных имеет схема скреперного мокрого или сухого золоудаления. Шлак, образующийся в результате сгорания топлива, попадает в скреперный канал.При мокром способе золошлакоудаления канал, в котором движется скрепер, заполнен водой, являющейся гидравлическим затвором для воронок шлаковых бункеров котлов. Скрепер перемещают в канале при помощи электролебедки и троса в направляющих роликах.При сухом способе скреперного золоудаления шлак обливают водой в шлаковом бункере и сбрасывают в скреперный канал. Скрепер подхватывает выгруженный из топки шлак и подает его по горизонтальному и наклонному каналу в бункер, откуда он выгружается в автосамосвал и вывозится из котельной. Скребковое золоудаление принципиально не отличается от мокрого скреперного золоудаления.Гидравлическое удаление золы и шлаков широко распространено в котельных большой мощности. Система обладает высокой производительностью и надежностью. Гидравлическое золоудаление включает в себя операции: удаление шлака и золы в пределах котельной; перекачивание с помощью багерных насосов или гидроаппаратов смеси воды, золы и шлака в золоотстойник.Зола и шлак смываются из бункеров котлов с помощью специальных смывных устройств в самотечный канал, по которому шлакозоловая смесь перемещается к устройствам для ее внешней транспортировки. Смыв золы осуществляется, как правило, непрерывно, а шлака периодически – 1–2 раза в смену. Самотечные каналы облицовывают базальтовыми плитками и выполняют с уклоном 2–3º. Для предотвращения образования заторов гидросмеси в самотечные каналы через побудительные сопла подается вода.При пневматической системе шлакозолоудаления транспортировка шлака и золы осуществляется в трубах потоком воздуха. Побудителями движения воздуха могут быть паровые эжекторы или вакуумные насосы. Пневматическую систему шлакозолоудаления рекомендуется применять в котельных для слоевого сжигания твердого топлива, а также в случаях, когда зола и шлак используются в качестве сырья побочных производств – изготовление строительных конструкций, производство цемента. Зола от сжигания древесных отходов может быть использована для удобрения полей в сельском хозяйстве. Пневматическая система применяется в случаях, когда район строительства котельной трудно обеспечивается водой или значительно удалены места для золоотвалов.
Тепловые схемы котельных с паровыми котлами.Отпуск пара технологическим потребителям часто производится от производственных котельных, в которых вырабатывается насыщенный или слабо перегретый пар с давлением до 1,4 или 2,4 МПа. Пар используется технологическими потребителями и в небольшом количестве – на приготовление горячей воды, направляемой в систему теплоснабжения. Приготовление горячей воды производится в сетевых подогревателях, устанавливаемых в котельной.Принципиальная тепловая схема производственной котельной с отпуском небольшого количества теплоты на нужды отопления, вентиляции и горячего водоснабжения в закрытую систему теплоснабжения показана на рис. 3.3.
Рис. 3.3. Тепловая схема производственной котельной: 1 – паровой котел; 2 – расширитель непрерывной продувки; 3 – насос сырой воды; 4 – барботер; 5 – охладитель непрерывной продувки; 6 – подогреватель сырой воды; 7 – химводоочистка; 8 – питательный насос; 9 – подпиточный насос; 10 – охладитель подпиточной воды; 11 – сетевой насос; 12 – охладитель конденсата; 13 – сетевой подогреватель; 14 – подогреватель химически очищенной воды; 15 – охладитель выпара; 16 – атмосферный деаэратор; 17 – редукционно-охладительная установкаНасос сырой воды подает воду в охладитель продувочной воды, где она нагревается за счет теплоты продувочной воды. Затем сырая вода подогревается до 20–30 °C в пароводяном подогревателе сырой воды и направляется на химводоочистку. Химически очищенная вода направляется в охладитель деаэрированной воды и подогревается до определенной температуры. Дальнейший подогрев химически очищенной воды осуществляется в подогревателе паром. Перед поступлением в головку деаэратора часть химически очищенной воды проходит через охладитель выпара деаэратора.Подогрев сетевой воды производится паром в последовательно включенных двух сетевых подогревателях. Конденсат от всех подогревателей направляется в головку деаэратора, в которую также поступает конденсат, возвращаемый внешними потребителями пара.Подогрев воды в атмосферном деаэраторе производится паром от котлов и паром из расширителя непрерывной продувки, в котором котловая вода частично испаряется вследствие снижения давления. Продувочная вода после использования в охладителе непрерывной продувки сбрасывается в продувочный колодец (барботер).Деаэрированная вода с температурой около 104 °С питательным насосом подается в паровые котлы. Подпиточная вода для системы теплоснабжения забирается из того же деаэратора, охлаждаясь в охладителе подпиточной воды до 70 °С перед поступлением к подпиточному насосу. Использование общего деаэратора для приготовления питательной и подпиточной воды возможно только для закрытых систем теплоснабжения ввиду малого расхода подпиточной воды в них. В открытых системах теплоснабжения расход подпиточной воды значителен, поэтому в котельной следует устанавливать два деаэратора: один для приготовления питательной воды, другой – подпиточной воды. В котельных с паровыми котлами, как правило, устанавливаются деаэраторы атмосферного типа.Для технологических потребителей, использующих пар более низкого давления по сравнению с вырабатываемым котлоагрегатами, и для подогревателей собственных нужд в тепловых схемах котельных предусматривается редукционная установка для снижения давления пара (РУ) или редукционно-охладительная установка для снижения давления и температуры пара (РОУ).
Экономичность работы котельного агрегата оценивается коэффициентом полезного действия (КПД). КПД котлоагрегата «брутто» (валовый) называется отношение количества тепла, полезно использованного в агрегате к количеству затраченного тепла в один промежуток времени:
ηбрка=100 Q1/ Qрр,%
или ηбрка=100-(q2+ q3+ q4+ q5+ q6), %.
Дата добавления: 2018-02-18; просмотров: 2088; | Поделиться с друзьями:
|
Мы поможем в написании ваших работ!