Конструирование деталей из пластмасс
Конструкция пластмассовой детали должна отвечать требованиям, определяемым свойствами применяемого материала, особенностями процесса изготовления, условиями сборки и эксплуатации. Следует стремиться к упрощению конструкции детали как по технологическим, эксплуатационным, так и экономическим соображениям. Чем проще деталь, тем дешевле оснастка, выше производительность труда, лучше качество и ниже ее стоимость. Детали простой конфигурации изготавливают с более высокой точностью, чем сложные. К простым относят монолитные детали типа плит простой геометрической формы, габаритными размерами до 80 мм с отношением высоты к длине не более 1 : 10 и разностенностью не более 2 : 1 при прессовании и 2,5 : 1 - при литьевом прессовании и литье под давлением, а также детали, имеющие форму тела вращения, монолитные, с отношением диаметра к высоте не более 1 : 2 и с габаритными размерами до 50 мм. Детали, конфигурация которых не отвечает приведенной характеристике, относят к категории сложных.
Требования к конструкции пластмассовой детали следующие:
- деталь должна иметь технологические (съемные) уклоны,
- допуски должны быть технически обоснованными; при назначении их следует руководствоваться особенностями эксплуатации детали, величинами колебаний усадки пресс-материала, а также высотой детали. от которой зависит величина уклона,
- в деталях недопустимы поднутрения,
|
|
- деталь должна иметь закругления, необходимые для увеличения механической прочности, облегчения процесса формообразования и улучшения внешнего вида,
- стенки должны быть равной толщины,
- прессованные детали не должны иметь консольных участков, т.е. выступов или приливов значительной длины,
- при выборе материала детали следует учитывать среду, которая будет воздействовать на нее в процессе эксплуатации.
Наиболее часто встречающимися видами брака являются коробление и трещины, которые появляются в процессе эксплуатации. Трещины возникают от неправильного сочетания пластмассы с металлической арматурой, вследствие усадочных напряжений, особенно при наличии значительной разницы в толщинах стенок детали. при отсутствии или неправильном назначении радиусов закруглений, при неправильном назначении уклона.
Внешняя форма детали должна обеспечивать возможность применения неразъемных матриц и пуансонов. Изготовление деталей в пресс-формах с разъемными элементами повышает стоимость и увеличивает трудоемкость процесса изготовления. Конфигурация детали не должна препятствовать свободному течению массы при заполнении пресс-формы. Внешний вид и точность готового изделия определяется точностью изготовления и согласованностью размеров сопрягаемых деталей. Сопрягаемые элементы детали ограничивают жесткими допусками. Величину и направление уклонов необходимо увязывать между собой. На форму детали влияет величина текучести пресс-материала. Детали из пластмасс с пониженной текучестью должны быть невысокие, без тонких стенок, ребер и сквозной арматуры. Наиболее технологическими формами плоских деталей из пластмасс являются круглая. овальная или любая другая, но с плавными очертаниями. Для этого острые прямые и тупые углы на наружном контуре, а также в отверстиях следует выполнять скругленными. Это важно для изделий из гетинакса, слюды, органического стекла. Следует стремиться к тому, чтобы наиболее ответственные или сопрягаемые впоследствии элементы детали не попадали в плоскость разъема формы, т.к. на точность размеров детали сильно влияет погрешность, зависящая от величины облоя. В пресс-формах прямого прессования вследствие отжима пресс-массы по кромке пуансона облой располагается по всему контуру изделия. В пресс-формах литьего прессования облой находится в местах перехода впускного литника в тело изделия. Удаление облоя требует применения дополнительных механических операций, приводит к ухудшению внешнего вида, а часто и к порче детали. Поэтому на пластмассовых деталях необходимо допускать минимальный слой облоя толщиной не более 0,3 мм, расположенный так. чтобы его удобно было удалять. Можно избежать образования облоя применением метода безоблойного прессования, т.е. облой отделяется в процессе прессования или при разъеме пресс-формы. Способ прямого безоблойного прессования применяют для изделий, имеющих в сечении простую фигуру (окружность, овал, прямоугольник). Этот способ не применяют для деталей с толщиной стенок менее 2 мм и армированных, за исключением изделий с вертикальной штифтовой или втулочной арматурой.
|
|
|
|
Технологические уклоны назначают при получении деталей из пластмасс методом прессования или литьем под давлением. Технологические уклоны назначают на вертикальных внешних и внутренних поверхностях, параллельных усилию замыкания пресс-формы или совпадающих с направлением извлечения из детали подвижных формующих элементов сложных пресс-форм. Технологические уклоны не назначают на элементах деталей, которые могут быть выполнены без уклонов, например, на плоских монолитных деталях толщиной 5 - 6 мм и менее, на тонкостенных деталях высотой 10 - 15 мм, на наружных поверхностях полых деталей высотой до 30 мм, на конусных деталях и деталях, имеющих сферическую форму. Технологический уклон внутренних поверхностей и отверстий деталей должен быть больше уклона наружных поверхностей, этим учитывают различный характер усадки поверхностей. Рекомендуются следующие углы уклона:
|
|
Наружные поверхности - 15¢, 30¢, 1°.
Внутренние поверхности - 30¢, 1°, 2°.
Отверстия глубиной до 1,5 d - 15¢, 30¢, 45¢.
Ребра жесткости, выступы - 2°, 3°, 5°, 10°, 15°.
Толщина стенок оказывает влияние на возникновение внутренних напряжений, являющихся причиной образования вздутий, трещин, коробления во время выдержки детали в матрице или пресс-форме. Толщина стенки детали зависит от длины (высоты) стенки, текучести пластмассы, механической прочности материала, конфигурации элементов детали. Из пластмасс, обладающих низкой текучестью, можно получить изделия небольшой высоты с толстыми стенками, а из пластмасс, имеющих большую текучесть, высокие тонкостенные конструкции. При большей механической прочности пластмасс возможно получение более высоких тонкостенных деталей, при низкой прочности подобные изделия получить недопустимо. Толщину сплошных сечений не рекомендуется назначать свыше 10 - 12 мм. Толщину стенок можно уменьшить применением ребер жесткости или приданием стенкам рациональных профилей. При конструировании деталей необходимо учитывать, что прочность пресс-материалов при сжатии значительно превосходит прочность при их растяжении. При конструировании деталей из пластмасс необходимо соблюдать условие равностенности. При разностенности может быть нарушена норма времени выдержки при прессовании, величина которой определяется наибольшей толщиной стенки изделия. Различная скорость охлаждения приводит к ухудшению свойств, при литье термопластов наличие утолщенных мест приводит к браку из-за образования в них газовых пузырей или поверхностных утяжин. В случае, когда по конструктивным соображениям невозможно обеспечить равностенность, допускаемая разность в толщинах стенок при прессовании должна составлять не более 2 : 1, при литье под давлением деталей простой конфигурации, плоскостных монолитных с габаритными размерами до 80 мм и отношением высоты к длине не более 1 : 5 или деталей типа втулок монолитных и сквозных с теми же габаритами разностенность должна быть не более 2,5 : 1. Условие равностенности рекомендуется соблюдать при конструировании приливов под шпильку, зубчатых колес, шкивов, маховиков, роликов и др. В ряде случаев утолщения необходимы, поэтому правильно сконструированной деталью можно считать такую, у которой величина разностенности не превышает 30% от наименьшей толщины стенки и отсутствуют резкие переходы. Переходы от большого сечения стенки к меньшему рекомендуется выполнять при помощи радиусов закруглений или уклонов, а в цилиндрических элементах при помощи конусности в соответствии с ГОСТ 8593. По конструктивным соображениям стенки утолщают в следующих случаях:
- при наличии отверстий,
- при конструировании деталей с резьбой,
- для увеличения прочности элементов деталей, работающих в абразивной среде,
- при проектировании ступиц шкивов и зубчатых колес необходимо предусматривать прилив над местом расположения шпоночной канавки для компенсации местного ослабления детали,
- для увеличения сопрягаемых поверхностей,
- при конструировании деталей с рифлением,
- при конструировании армированных деталей, для создания вокруг арматуры стенок соответствующей толщины.
Торцы деталей для упрочнения выполняют в виде буртиков разнообразных конструкций. Торцы предохраняют края изделия от поломки, предотвращают коробление, облегчают формообразование и извлечение детали из формы. Толщина буртиков не должна превышать 1,5 - 2 толщин стенки. Буртики необходимо делать непрерывными по всему контуру детали, т.к. в местах разрыва возникают напряжения, приводящие к трещинам.
Для увеличения жесткости и прочности пластмассовых деталей, усиления особо нагруженных мест или выступающих частей рекомендуется предусматривать в конструкции детали ребра жесткости. В зависимости от назначения ребра жесткости подразделяют на следующие виды:
- усиливающие, они служат для увеличения прочности детали в определенных сечениях, уменьшения напряжений, особенно в тонкостенных деталях,
- разводящие, эти ребра воспринимают сосредоточенные нагрузки и переносят их рассредоточено на большую площадь стенки детали,
- обеспечивающие равностенность детали,
- конструктивные, имеющие целевое назначение,
- технологические, применяемые в зависимости от технологического процесса изготовления пластмассовой детали, к ним относят ребра, применяемые для устранения коробления детали, облегчения извлечения детали из формы, уменьшения времени выдержки детали в форме.
При конструировании пластмассовых деталей с ребрами жесткости необходимо принимать во внимание во внимание следующие рекомендации. Ребра жесткости не должны быть толще стенки или ее элемента, к которому примыкают. Оптимальная толщина ребер жесткости не должна превышать 0,6 - 0,8 толщины сопрягаемой стенки. Ребра жесткости не должны доходить до опорной поверхности или до края примыкающего к нему элемента на 0,5 - 1,0 мм. Ребра жесткости рекомендуется располагать на прямых участках элементов детали. Необходимо стремиться к диагональному или диаметральному расположению ребер жесткости. При сопряжении ребристых деталей типа плит рекомендуется располагать ребра в шахматном порядке, избегая крестообразных сопряжений, дающих значительные местные скопления массы. Ребра жесткости, которые служат для укрепления элементов деталей, рекомендуется размещать симметрично оси детали во избежание ее коробления. В ребристых деталях следует избегать замкнутых контуров или стремиться к уменьшению периметра таких контуров. Для уменьшения опасности возникновения напряжений в самом ребре жесткости форму его сечения сохраняют постоянной по всей длине. Ребрам жесткости придают наибольший допустимый технологический уклон и располагают их в плоскости разъема пресс-формы или перпендикулярно к ней. Ребра жесткости, если позволяет их конструкция, желательно располагать так, чтобы они работали на сжатие, а не на растяжение.
На изделиях из пластмасс с наружной и с внутренней стороны предусматривают закругления. Наличие закруглений способствует:
- увеличению механической прочности детали в целом или отдельных ее элементов,
- устранению или уменьшению внутренних напряжений, следствием которых являются коробление и другие виды отклонений от правильной геометрической формы,
- уменьшению величины и колебаний усадки детали, следовательно повышению точности.
Кроме того облегчается течение массы в пресс-форме во время процесса формообразования, упрощается изготовление пресс-формы и уменьшается его износ, упрощается процесс извлечения детали из пресс-формы, улучшается внешний вид изделия. Без закруглений можно выполнять поверхности, находящиеся в плоскости разъема форм, т.к. на них закругления величиной 0,2 - 0,3 мм образуются после снятия облоя механической обработкой, и наружные кромки деталей или кромки отверстий, образующиеся в местах соединения оформляющих элементов пресс-формы. Острые кромки на детали также должны быть закруглены, радиус закругления в этом случае берут минимальным (0,5 мм). Радиусы закруглений и фаски для деталей из пластмасс и металла регламентированы ГОСТ 10948. Минимальный радиус наружного закругления для деталей из термореактивных пластмасс должен составлять 0,8 мм, а для термопластов типа полистерола и полиметилметакрила 1 - 1,5 мм, для реактопластов 0,8 мм. При выполнении радиусов закруглений на деталях рекомендуется: величину их по всей длине закругления сохранять одинаковой, на одном изделии принимать наименьшее количество значений радиусов закруглений, не принимать максимальных значений.
При конструировании пластмассовых деталей с отверстиями конфигурацию и расположение последних выбирают в соответствии с определенными правилами и нормами. Оформление отверстий в деталях может быть полное (при прессовании) и частичное (с последующим досверливанием), часто отверстия сверлят в опрессованной детали. В деталях из пластмасс следует применять отверстия наиболее простых форм. Цилиндрические отверстия наиболее просты изготовлении, овальные отверстия - наиболее трудоемки. Отверстия простых форм могут быть сквозными и глухими. Сквозные отверстия по характеру оформления могут быть односторонние, односторонние с протаскиванием формующей шпильки, двусторонние. Направление осей отверстий, не совпадающее с направлением прессования или съема изделия нежелательно. При выборе положения отверстий в детали можно руководствоваться следующими рекомендациями:
- Расстояние между соседними отверстиями или отверстием и краем изделия должно быть не менее диаметра отверстия.
- При расположении отверстия близко от края изделия желательно, чтобы край изделия соответствовал форме примыкающего к нему отверстия.
- Боковые отверстия, сконструированные в виде открытых с одного края пазов, упрощают изготовление детали.
- На деталях с большим количеством мелких отверстий (d = 1,5 - 2,0 мм) перемычки должны быть максимальных размеров.
- Если при прессовании необходимо получить два и большее число смежных отверстий, то минимальное расстояние между ними должно равняться величине b1 = S / a + 1.
b1
S
a b2
Рисунок 5 - Оформление смежных отверстий, получаемых прессованием
Диаметры отверстий выбирают по ГОСТ 6636, диаметры сквозных отверстий для болтов, винтов, шпилек и заклепок, устанавливаемых с зазорами в соединяемые детали, регламентированны ГОСТ 11284.
При конструировании пластмассовых деталей с углублениями и технологическими отверстиями необходимо стремиться к такой конфигурации, при которой поверхность углубления (или отверстия) отстояла бы от поверхности изделия на расстояние, равное толщине изделия. Внутренние углы и кромки этих элементов обязательно должны быть закруглены. Конструкция пластмассового изделия не должна иметь выступов и приливов значительной длины. Если этого избежать невозможно, то для придания им необходимой прочности и жесткости следует вводить ребра жесткости или проектировать сборную конструкцию.
Для устранения влияния коробления, усадки и неровностей больших площадей, повышения жесткости и точности сопрягаемых элементов деталей применяют выступающие над поверхностями опорные плоскости в виде выступов, бобышек, буртиков. При конструировании этих элементов следует придерживаться следующих рекомендаций:
- Опорные поверхности (крышек, плит и т.д.) ограничивать до минимума.
- Высота бобышек должна быть минимальной.
- При необходимости выполнять бобышку высотой, превышающей 1 / 3 высоты основной стенки, необходимо предусматривать в основной стенке выемку.
- Бобышки сопрягают с основной стенкой детали плавно, без резких углов и переходов.
- Крепежные проушины для большей жесткости и прочности укрепляют ребрами жесткости, избегая при этом резких углов и переходов.
Накатку и рифление осуществляют в процессе формообразования и обычно на наружных поверхностях деталей. Для обеспечения простоты извлечения детали из формы накатку и рифление выполняют прямыми ребрами, параллельными направлению выталкивания детали из формы. Ширина ребер должна быть не менее 0,3 - 0,5 мм, а высота возвышения над базовой поверхностью не должна превышать их ширины.
Резьбы в пластмассовых изделиях получают тремя способами:
- непосредственно при прессовании или литье изделия,
- механической обработкой отдельных элементов изделия,
- вставкой металлических частей, имеющих резьбы, в прессованные изделия.
Наиболее экономичным и производительным способом получения резьбы является прямое или литьевое прессование. Наименьший диаметр резьбы, получаемой прессованием, в зависимости от типа пресс-материала и его технологических свойств:
- Порошковые композиционные пластики - 3 мм.
- Волокнистые материалы - 4 мм.
Не рекомендуется изготавливать прессованием резьбы, шаг которых менее 0,7 мм. Преимущество резьб, получаемых механической обработкой, заключается в большей их точности по сравнению с прессованием. Такие резьбы рекомендуется применять:
- при повышенных требованиях к точности диаметральных или координатных размеров (при наличии нескольких резьбовых сопрягающихся элементов),
- при низкой механической прочности форм формующего резьбу элемента пресс-формы (например, если резьбовые знаки имеют диаметр менее 2,5 - 3,0 мм),
- при получении наружной резьбы диаметром менее 10 - 12 мм и внутренней диаметром менее 4 мм,
- при получении мелких резьб с шагом 0,5 мм и менее.
Для прессуемых резьб всех видов обязательно наличие фаски или кольцевой вытачки на конце резьбы. Величина фаски зависит от шага резьбы и регламентирована ГОСТ 10549.
Надписи на деталях получают в процессе прессования. В некоторых случаях надписи наносят после изготовления детали гравировкой, печатанием или другими способами. При изготовлении пресс-формы резанием надписи на деталях следует делать выпуклыми, а в формах, получаемых холодным выдавливанием, - углубленными. При оформлении надписей следует:
- наименьшую их высоту над поверхностью изделия устанавливать в пределах 0,3 - 0,5 мм,
- буквы высотой 0,75 мм выполняют шире у основания, чем у вершины,
- для защиты выпуклого шрифта от повреждений надписи помещают в незначительные углубления на поверхности изделия.
Дата добавления: 2018-02-18; просмотров: 2144; Мы поможем в написании вашей работы! |
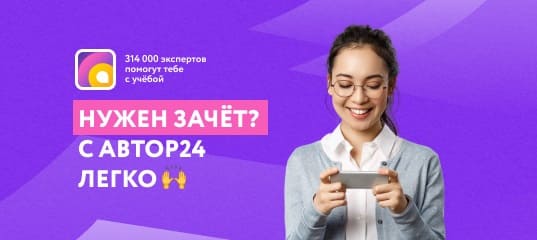
Мы поможем в написании ваших работ!