ВЫБОР И РАСЧЕТ МАТЕРИАЛЬНОГО БАЛАНСА И ОБОРУДОВАНИЯ
Расчет материального баланса
Цель расчета - оптимизировать расходы сырья для производства облицовочной керамической плитки. В качестве расчетной единицы взяли партию из 1000 плиток, которая должна быть представлена потребителю.
Для того чтобы представить потребителю партию из 1000 плиток, учитывали потери исходного материала по операциям. Потери считали по формуле:
,
где Аn — количество вещества (ингредиента), перерабатываемого на операции «n»;
M— количество вещества, передаваемого c предыдущей операции;
Вi - процент технологического отсева на операции «n» (потери или отбор проб на испытания).
Масса партии готовых плиток 250 кг. Единичная готовая плитка весит 0,25кг. Масса глазури – 30 кг.
1) Расчет массы сырья для шликера, поступившего на стадию выходного контроля:
кг.
2) Расчет массы смеси, поступившей на стадию обжига:
кг.
3) Расчет массы смеси, поступившей на стадию прессования:
г.
4) Расчет массы смеси, поступившей на стадию получения пресс-порошка:
г.
5) Расчет массы смеси, поступившей на стадию массоприготовления:
г.
6) Рассчитываем массу каждого компонента в смеси, поступившей на стадию смешения:
1. Глина – 99000 г;
2. Кварцевый песок – 33000 г;
3. Мел, шлак – 22000 г;
4. Сода – 440 г;
5. Жидкое стекло – 1100 г.
7) Расчет массы глины, поступившей на стадию помола:
г.
8) Расчет массы песка, поступившего на стадию отсева крупных камней:
г.
9) Расчет массы сырья для глазури, поступившей на стадию выходного контроля:
|
|
г.
10) Расчет массы глазури, поступившей на стадию обжига:
г.
11) Расчет массы глазури, поступившей на стадию глазурования:
г.
12) Расчет массы глазури, поступившей на стадию слива и перекачки:
г.
13) Расчет массы глазури, поступившей на стадию массоприготовления:
г.
На стадии входного контроля не существуют безвозвратных потерь.
Данные, полученные в результате расчетов, занесены в таблицу 3.1.
Таблица 3.1. – Материальный баланс для производства партии настенной керамической плитки
Наименование операции | Количество, г. | Потери | Готовое изделие, г. | ||||
% | На партию, г. | ||||||
Помол глинистого сырья | 101020 | 2 | 2020 | 98999 | |||
Отсев крупных камней песка | 33673 | 2 | 673 | 32999 | |||
Массоприготовление шликера | 259485 | 3 | 7785 | 251700 | |||
Получение пресс-порошка | 251700 | 1 | 2517 | 249183 | |||
Прессование | 249183 | 2 | 4984 | 244200 | |||
Обжиг | 244200 | 9 | 21978 | 222222 | |||
Выходной контроль | 222222 | 1 | 2222 | 219999 | |||
Итого для шликера | 259485 | 16 | 39486 | 251700 | |||
Массоприготовление глазури | 37667 | 2 | 753 | 36914 | |||
Слив и перекачка массы глазури | 36914 | 3 | 1107 | 35806 | |||
Глазурование | 35806 | 7 | 2506 | 33300 | |||
Вторичный обжиг | 33300 | 9 | 2997 | 30303 | |||
Выходной контроль глазури | 30303
| 1 | 303 | 29999 | |||
Итого для глазури | 37667 | 22 | 7666 | 29999 | |||
Режим работы цеха
Годовой календарный фонд времени, или полное годовое время, в течение которого предприятие должно работать без каких-либо потерь, определяется режимом работы производства:
Треж = (Тк-Тпр)*С*Dрн
где Тк — календарный фонд времени, 365 дней;
Тпр — число праздничных дней в году;
Dpн — продолжительность рабочей недели в часах;
С — число смен работы производства в сутки.
Эффективный фонд времени — это годовое время, в течение которого фактически работают рабочие и производится работа на оборудование при установленном в цехе режиме работ:
Т эф=Т реж -Трем -Ттех –Тост,
где Трем — продолжительность простоя ведущего (или групп) оборудования во всех видах планово-предупредительного ремонта (ППР), проводимого в рабочее время в часах за год. Простои оборудования в ремонтах, проводимых в перерыве между сменами и в выходные дни, в Трем не учитывается;
Ттех — время остановок ведущего оборудования для переключения с производства одного продукта на другой, чистки и т.д. в часах за год.
Тост — время остановки цеха в часах для ремонта межцеховых коммуникаций (электроэнергия, пар, вода, канализация и т.д.).
|
|
Расчет полного годового времени:
Треж=(365-8)*8*2=5712
Расчет эффективного фонда времени:
Тэф=5712-150-213-100=5249
Расчетный фонд рабочего времени головного агрегата (гидравлического пресса) по различным техническим и организационным причинам полностью не используется, и для корректирования этого времени вводят коэффициент использования оборудования Кио, который равен 0,7. Отсюда эффективный фонд рабочего времени равен:
Тэф=5249*0,7=3674 часа
Коэффициент полезного действия смесителя:
Определение производительности головного агрегата
Головным агрегатом в производстве керамической плитки является гидравлический пресс, который осуществляет формование.
В общем виде годовая производственная мощность определяется по формуле:
М=Пч*Тэф,
Где Пч – производительность головного агрегата в час, Тэф – эффективный фонд времени.
Годовая производственная мощность головного агрегата равна:
М=3674*1080=3967,92 т/год
Производительность пресса в данных условиях равна 3967,92 тонны в год.
Дата добавления: 2018-02-18; просмотров: 945; Мы поможем в написании вашей работы! |
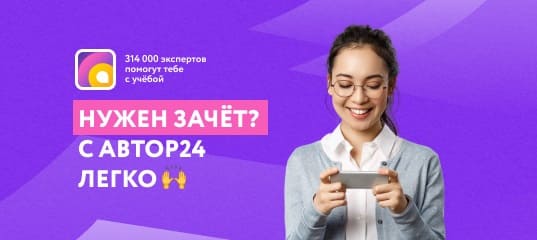
Мы поможем в написании ваших работ!