Выбор стали для изготовления валов двигателей
Механические свойства стали определяются не только её составом, но зависят и от её строения (структуры). Поэтому целью термической обработки является получение необходимой структуры, обеспечивающей требуемый комплекс свойств стали. Различают предварительную и окончательную термическую обработки. Предварительной термической обработке подвергают отливки, поковки, штамповки, сортовой прокат и другие полуфабрикаты. Она проводится для снятия остаточных напряжений, улучшения обрабатываемости резанием, исправления крупнозернистой структуры, подготовки структуры стали к окончательной термической обработке и т.п. Если предварительная термическая обработка обеспечивает требуемый уровень механических свойств, то окончательная термическая обработка может и не проводиться.
Получение структуры сорбит для данной стали можно достичь и просто отжигом ее при тех же температурах, при которых материал нагревается под закалку, с последующем охлаждением на воздухе. Такой технологический процесс называется нормализацией. Однако улучшение этих сталей в отличии от нормализации обеспечивает повышенный предел текучести в сочетании с хорошей пластичностью и вязкостью, высоким сопротивлением развитию трещины, снижает порог хладноломкости.
Выбор режима термической обработки стали
Для стали 40ХФА выбрана термическая обработка, состоящая из закалки с последующим высоким отпуском. Температура и продолжительность закалки: доэвтектойдные стали нагревают под закалку до температуры на 30..50 °С выше температуры АС3. Для данной стали температура нагрева под закалку составляет 830..850 °С. Исходная структура стали феррита+перлит при нагреве стали до температуры закалки (выше А3) и выдержки при этой температуры превращается в аустенит. Продолжительность выдержки при температуре аустенизации должна обеспечить прогрев детали по сечению и завершение фазовых превращений, но не более. Иначе будет происходить нежелательный рост зерна, что в последующем приведет к охрупчиванию материала.
|
|
Исходя из сказанного, продолжительность прогрева детали из данного материала выбирают следующим образом: на 1мм поперечного сечения детали -- 45-75 сек в электропечах и 15-25 сек в соляной ванне (это чтобы прогреть деталь) + 15..20 % от продолжительности прогрева детали. Выбранный режим нагрева должен обеспечить полное превращение исходной феррито-перлитной структуры в аустенит. Последующее охлаждение материала произведем в масле, чтобы обеспечить скорость охлаждения больше, чем vкр (наименьшая скорость охлаждения, при которой аустенит превращается в мартенсит, т.е. в структуру закаленной стали). При скоростях охлаждения меньше vкр в углеродистой стали протекает только диффузионные процессы распада аустенита с образованием феррито-перлитной структуры различной степени дисперсности (перлит, сорбит, тростит). При высоких скоростях охлаждения (выше vкр) диффузионный распад аустенита подавляется -- аустенит претерпевает только мартенситное превращение. Мартенсит представляет собой пересыщенный твердый раствор внедрения углерода в Fea. Как правило, при закалке не весь аустенит превращается в мартенсит, и структура закаленной стали представляет собой мартенсит и остаточный аустенит.
|
|
Образование в результате закалки мартенсита приведет к большим остаточным напряжениям, повышению твердости, прочности, однако резко возрастает склонность материала к хрупкому разрушению, особенно при динамических нагрузках. В связи с этим проводится окончательная операция термической обработки -- высокотемпературный отпуск, при котором снимаются остаточные напряжения и обеспечиваются необходимые механические свойства материала.
Отпуск заключается в нагреве до температуры ниже АС1 , выдержке при заданной температуре и последующем охлаждении с определенной скоростью. Режим отпуска Т=650 °С в течение 1-6 часов в зависимости от габаритов изделия. Охлаждающая среда -- масло. Структура стали после высокого отпуска -- сорбит отпуска. Высокий отпуск следует наилучшее соотношение прочности и вязкости.
|
|
Для изготовления валов 35мм, 50мм и 120мм, имея предел прочности не ниже 75 МПа, может подойти стали 40ХФА.
Таким образом, эти свойства обеспечивают требования, формулированные в задаче.
Заключение
Как было отмечено выше, нет чётких единых принципов выбора марок сталей для изготовления деталей машин, т.е. немаловажную роль в этом процессе играет субъективный фактор.
Это во многом связано ещё и с тем, что изложенные выше требования к материалу нередко противоречивы. Так, например, более прочные стали менее технологичны, т.е. труднее поддаются обработке резанием, холодной объёмной штамповке, сварке и т.д. Решение обычно компромиссно между указанными требованиями. Например, в массовом машиностроении предпочитают упрощение технологии и снижение трудоёмкости изготовления детали некоторой потере свойств. В специальных же отраслях машиностроения, где проблема прочности (или удельной прочности) играет решающую роль, выбор стали и последующая технология её термической обработки должны рассматриваться только из условия достижения максимальных эксплуатационных свойств. При этом не следует стремиться к излишне высокой долговечности данной детали по отношению к долговечности самой машины. Выбор материала обычно осуществляется на основании сравнительного анализа 2…3 марок сталей, из которых изготавливаются аналогичные детали других моделей машин.
|
|
У многих деталей машин (валов, шестерён и т.д.) поверхность в процессе эксплуатации подвергается истиранию и в то же время на них воздействуют динамические (чаще всего ударные) нагрузки. Для успешной работы в таких условиях поверхность детали должна иметь высокую твёрдость, а сердцевина быть вязкой. Такое сочетание свойств достигается правильным выбором марки стали и последующим упрочнением её поверхностных слоёв. Для изготовления подобных деталей можно применять различные группы сталей и способы их поверхностного упрочнения.
Список используемой литературы
1. Геллер, Ю.А., Рахштадт, А.Г. Материаловедение: Учебное пособие для высш. учеб. завед. 6-е изд. перераб. и доп. М.: Металлургия, 1989.
2. Термическая обработка в машиностроении: Справочник / Под ред. Ю.М. Лахтина и А.Г. Рахштадта - М.: Машиностроение, 1980.
3. Лахтин Ю.М., Леонтьева В.П. Материаловедение: Учебник для высш. техн. учеб. завед. 3-е изд., перераб. и доп. М.: Машиностроение, 1990.
4. С. И. Алаи, П.М. Григорьев, А.Н. Ростовцев Технология конструкционных материалов: Учебник для студентов пед. ин-тов - М.: Просвещение, 1986.
5. Гуляев А.П., Металловедение: Учебник для вузов. 6-е изд., перераб. и доп. М.: Металлургия, 1986.
6. Журавлев В.Н., Николаева О.И. Машиностроительные стали: Справочник. 4-е изд., перераб. и доп. М.: Машиностроение, 1992.
7. Ушаков В.Г., Филатов В.И., Ибрагимов Х.М. Выбор марки стали и режима термической обработки деталей машин: Учебное пособие для студентов: Издательство ЮУрГУ, 2001.
8. А.Н Ростовцева, А.П. Надточий, Ф.А. Фурманов Справочник по техническому труду: - М.: Просвещение, 1996.
Дата добавления: 2018-02-15; просмотров: 1661; Мы поможем в написании вашей работы! |
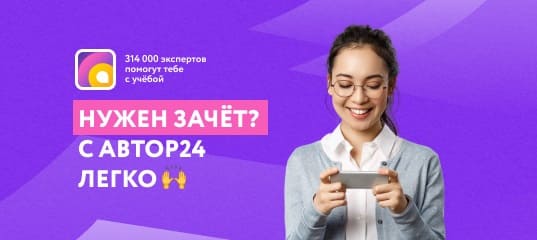
Мы поможем в написании ваших работ!