Машина для внесения твердых минеральных удобрений МРД-8
Распределитель удобрений предназначен для транспортирования и поверхностного внесения твердых минеральных удобрений, известковых материалов и химических мелиорантов а также внесения песчано-солевых смесей поверхностным способом.
Машина комплектуется сменными дисками и туконаправителями в зависимости от вида вносимого продукта.
Регулировка доз внесения производится изменением высоты подъема заслонки дозатора.
АГРОТЕХНИЧЕСКИЕ ТРЕБОВАНИЯ
Заправщики жидкого аммиака большой грузоподъемности (5,2 ...6 т) используют для транспортировки аммиака от базовых (заводских и прирельсовых) до глубинных складов, полевых станций раздачи и полевых емкостей. Заправщики меньшей грузоподъемности (2,6 ...3,2 т) используют для доставки жидкого аммиака от складов, полевых станций раздачи и полевых емостей в поле и заправки аммиаком резервуаров агрегатов. Емкости этих заправщиков также могут быть использованы в качестве полевых промежуточных заправщиков.
Транспортные машины на заводских, прирельсовых и глубинных складах, раздаточных станциях заправляют жидким аммиаком как перекачивающими устройствами хранилищ, так и автономным перекачивающим устройством самих машин. С помощью этих устройств транспортные машины заправляют аммиаком из любых других транспортных машин, непосредственно из железнодорожных цистерн, а также сливают жидкий аммиак в складские и полевые емкости и емкости заправщиков и агрегатов для внесения.
|
|
Транспортируют жидкий аммиак от базовых до глубинных складов, полевых станций раздачи и полевых емкостей в течение всего года по дорогам всех категорий.
Заправляют жидким аммиаком цистерны транспортных машин и сливают его только паровозвратным способом.
Потери аммиака при заправке, транспортировке и сливе не допускаются.
Эксплуатация заправщиков должна осуществляться при температуре окружающей среды в пределах от —40 до +40°С.
Допустимое давление емкости заправщика — 2,0 МПа.
Технологическая арматура и контрольно-измерительные приборы транспортных машин закрывают общим кожухом и запирают.
Соединительные муфты жидкостной и газовой коммуникаций должны быть унифицированы с муфтами жидкостных и газовых коммуникаций заводских, прирельсовых и глубинных складов, раздаточных станций и полевых емкостей.
Вносят жидкий аммиак внутрипочвенно, лентами после предпосевной и основной обработки почвы, одновременно со вспашкой, при подкормке пропашных культур, а также на сенокосах и пастбищах.
Вносят жидкий аммиак при температуре воздуха не ниже 3°С и влажности почвы 20 ...40%.
Внесение жидкого аммиака можно проводить на всех типах почв с ровным рельефом и на склонах до 7°.
|
|
Глубина внесения жидкого аммиака зависит от механического состава, влажности и качества обработки почвы. На легких почвах аммиак вносят на глубину 14... 16 см, на средних и тяжелых—10... 12 см. На недостаточно разработанных участках, несколько переувлажненных или сухих почвах, а также после известкования глубину внесения увеличивают на 3...5 см.
Глубина заделки аммиака при внесении его на сенокосах и пастбищах на средне- и тяжелосуглинистых почвах должна составлять 8... 10 см, на песчаных и супесчаных— 10... 12 см.
Внесение аммиака при вспашке проводят на глубину пахотного слоя. Отклонение от заданной глубины хода рабочих органов не должно превышать 15%.
Вносят жидкий аммиак культиваторами, приспособленными для внесения в почву жидких минеральных удобрений, плугами, оборудованными специальными рабочими органами для внесения и заделки аммиака в почву.
Потери аммиака в процессе внесения его культиватором в подготовленную для посева почву (при глубине заделки 14 см) и плугом (при глубине заделки 20 см) не должно превышать 0,8% от вносимой дозы, а из почвы в течение 2 ч после внесения — 0,2%. Потери аммиака при заправке машины не допускаются.
|
|
Выход аммиака из питательных трубок рабочих органов при их выглублении не допускается.
Показатель неравномерности внесения удобрений по ширине захвата и в направлении движения агрегата (коэффициент вариации) не должен превышать 10%.
Дозирующее устройство машины должно обеспечивать заданную дозу внесения аммиака независимо от изменения скорости движения и величины давления в резервуаре и иметь шкалу настройки. Регулируют машину на дозу внесения непрерывно при максимальном рабочем захвате 50 ...250 кг/га. Допустимое отклонение фактической дозы от установленной по шкале или таблице не должно превышать 10%.
Расстояние между рабочими органами для внесения и заделки аммиака при сплошном внесении не должно превышать 350 мм. При подкормке пропашных культур рабочие органы расставляют на ширину междурядий.
Не допускается нарушения технологического процесса работы машины вследствие намерзания почвы на рабочие органы.
Забивание рабочих органов растительными остатками в процессе работы не допускается.
Агрегат для внесения заправляют от транспортных или заправочных емкостей или на складе жидкого аммиака с помощью перекачивающих средств заправщиков или складов.
|
|
СПОСОБЫ ПОГРУЗКИ
Автомобиль-разбрасыватель и тракторный разбрасыватель загружают одним из трех способов: самотеком из силосов и бункеров через верхний загрузочный люк; самозагрузкой из амбарных складов и крытых железнодорожных вагонов; пневматически из других машин-минераловозов или железнодорожных вагонов-минераловозов с пневматической выгрузкой.
Применение пневмотранспорта позволяет избежать загрязнения окружающей среды, улучшить условия труда обслуживающего персонала. Потери удобрений при этом приближаются к нормам естественной убыли.
Из средств доставки широкое распространение получили автомобиль-разбрасыватель АРУП-8, автоцементовозы ТЦ-б, ТЦ-10, ТЦ-11 и другие, а также тракторный разбрасыватель РУП-8.
Комплектование агрегата.
4.1 Подготовка агрегатов к работе.
Перед началом работ по внесению удобрений разбрасыватель собирают. При сборке разбрасывающего устройства необходимо следить за тем, чтобы оси шнеков были параллельны поверхности планчатого транспортера и между собой, так как в противном случае трудно обеспечить равномерность разбрасывания удобрений. После сцепки с трактором соединяют вал отбора мощности трактора с карданным валом.
Перед пуском разбрасывателя в работу необходимо его тщательно осмотреть, исправить или заменить все изношенные детали, подтянуть крепления, смазать согласно инструкции трущиеся поверхности. Затем следует отрегулировать разбрасывающее устройство, причем зазор между внутренними стенками боковин и шнеками не должен превышать 10 мм, лопасти нижнего шнека должны быть повернуты на 45° относительно лопастей верхнего шнека, приводная втулочно-роликовая цепь при нажатии на середину ее верхней ветви должна отклоняться не более чем на 3-4 см, цепи транспортера при нажатии не должны отклоняться более чем на 2-3 см, давление в шинах должно быть в пределах 2-2,5 кг/см2, для шин размером 12X16".
После этого приступают к регулировке рабочих органов машины иа определенную норму высева удобрений. Для этого загружают разбрасыватель взвешенным количеством удобрений Р (т) и определяют длину пути L (м), на котором эти удобрения будут ' рассеяны ,при ширине захвата В (м) и принятой норме Н (т/га). Таким образом:
h = P / 10 000 HB
Если заправленного количества удобрений хватит для работы на заранее рассчитанное расстояние, то регулировка проведена правильно.
В противном случае регулировку проводят вновь увеличивая или уменьшая скорость движения транспортера до тех пор, пока фактическая длина рабочего. пути агрегата не совпадает с расчетной ±(5-8)%.
4.2 Техническое обслуживание разбрасывателей удобрений
Система технического обслуживания включает очистку, мойку, контроль состояния узлов и деталей машин, заправку, смазку, крепление, регулировку узлов и механизмов машин.
Задача системы технического обслуживания - предупредить повышенный износ. Профилактические мероприятия позволяют резко сократить количество поломок, уменьшить вредное влияние регулировок и износа на показатели работы машин. Техническое обслуживание машин проводится через определенные интервалы. Система технического обслуживания и ремонта тракторов и сельскохозяйственных машин включает обкатку, техническое обслуживание, периодический технический осмотр, ремонт и хранение.
Важным условием и надежной работой машин является своевременное и качественное выполнение всех элементов системы технического обслуживания. Работа по каждому элементу технического обслуживания проводится в соответствии с требованиями инструкции изготовителей машин, правилами технического обслуживания, диагностики и хранения машин.
Первой частью технического обслуживания является эксплуатационная обкатка: приработка трущихся поверхностей деталей новых или отремонтированных машин, проверка работы узлов и механизмов, выявление случайных дефектов (недостаточная затяжка резьбовых соединений, подтекание смазки, топлива, воды).
На заводе и в ремонтной мастерской не проводится полной приработки трущихся поверхностей, поэтому у поверхностей новых деталей наблюдаются микронеровности, которые при больших нагрузках входят в зацепления, выламываются и вместе со смазкой попадают между трущимися поверхностями, резко увеличивая износ и сокращая срок службы машин. Если новую машину загрузить полностью, то могут произойти заедания трущихся поверхностей, ослабление креплений, повышенный износ, нарушение регулировок, поломки деталей. Обкатка с постепенным увеличением нагрузок осуществляется в соответствии с требованиями заводских инструкций.
Обкатка трактора класса до 25 л.с продолжается в течение 50—60 ч: 15 мин — двигатель на холостом ходу; 4—5 ч — на холостом ходу на III—IX передачах; 25 ч — на легких транспортных работах с тяговой нагрузкой до 40% от номинальной, 28 ч — на легких полевых работах с использованием раздельно-агрегатной системы с тяговой нагрузкой 9 кН.
Периодическое техническое обслуживание включает ежесменное техническое обслуживание (ЕТО), техническое обслуживание 1 (ТО-1), техническое обслуживание 3 (ТО-3) и сезонное техническое обслуживание (СТО). ЕТО проводят в начале, в период работы и по окончании смены (через 8...10 ч). ЕТО включает очистку трактора от пыли и грязи, проверку комплектности, течи и при необходимости доливку охлаждающей жидкости, масла топлива, электролита, работоспособности рулевого управления, систем освещения, сигнализации и тормозов; слив конденсата из воздушных баллонов.
ТО-1 включает все операции ЕТО и, кроме того, мойку трактора, очистку фильтров, проверку и регулировку механизмов трактора.
ТО-2 включает все операции ТО-1, а также смену масла в системе смазки; промывку, регулировку и смазку узлов и механизмов трактора.
ТО-3 включает все операции ТО-2 и регулировку топливной аппаратуры, гидросистемы, электрооборудования. СТО включает все операции очередного планового технического обслуживания, а также ряд работ по подготовке тракторов к работе в условиях осенне-зимнего периода (при температуре окружающего воздуха 5°С и ниже) или весенне-летнего периода эксплуатации (при температуре воздуха выше 5°С). СТО включает замену масел, например летних сортов на зимнее или наоборот, очистку радиатора от накипи, установку плотности электролита в соответствии с рекомендуемой. Для всех тракторов проводится: ТО-1 через 60 моточасов; ТО-2 через 240; ТО-3 через 960 моточасов.
При этом рекомендуется ТО-1 проводить по истечении 30 дней после последнего планового обслуживания.
Для навесного оборудования (бороны, плуги, культиваторы, катки, сеялки и др.) устанавливается единый вид обслуживания — ежесменный.
Для более сложного навесного оборудования (роторные снегоуборщики, газонокосилки, сенокосилки) выполняется два вида обслуживания: ежесменное и плановое. Допускается колебание интервалов технического обслуживания + 10% нормативных. Затраты времени на техническое обслуживание следует рассматривать как необходимые и обеспечивающие продолжительную эффективную и качественную работу агрегата.
Важной частью планово-предупредительной системы технического обслуживания является периодический технический осмотр, который проводится для оценки технического состояния машины и принятия решения о необходимости ремонта. В последнее время применяется проверка технического состояния машин без разработки при помощи специального диагностического оборудования. Периодический технический осмотр, проводимый при выполнении ТО-1, ТО-2, ТО-З, позволяет установить содержание необходимого ремонта минитракторов.
Результаты исследований показали, что треть минитракторов, направляемых на капитальный ремонт, не нуждается в ремонте и для восстановления их работоспособности достаточно выполнить ТО-З.
Перед длительным хранением машины моют и смазывают, сшивают детали и узлы, которые следует хранить в специально оборудованных помещениях, закрывают заглушками отверстие, ремонтируют и красят поврежденные места, наносят защитный антикоррозийный слой на поверхности деталей.
4.3 Установка разбрасывателя на заданную норму внесения удобрений.
В зависимости от используемой техники и расстояния перевозки применяются следующие технологические схемы внесения минеральных удобрений: прямоточная, с перегрузкой и перевалочная.
Основной схемой внесения минеральных удобрений является схема с перегрузкой: погрузка удобрений погрузчиком со склада в автосамосвалы-перегрузчики САЗ-3502 или загрузчики сеялок ЗСА-40, АС-2УМ, транспортировка их на поле, перегрузка в сеялки или разбрасыватели и внесение их в почву последними.
Прямоточная схема работы (транспортировка и внесение осуществляются одним агрегатом) может быть рекомендована для внесения минеральных удобрений прицепами-разбрасывателями, если места хранения удобрений расположены вблизи полей.
При внесении удобрений разбрасывателем КСА-3 применение прямоточной схемы выгоднее (по сравнению с перевалочной схемой) даже с увеличением расстояния транспортировки до 20-30 км.
Если в хозяйствах отсутствуют машины ЗСА-40.САЗ-3502 или КСА-3 и расстояние транспортировки превышает 5 км, применяют перевалочную схему работы.
Подготовка поля к работе.
1. Поле освобождают от препятствий, мешающих нормальной работе агрегатов. Неустранимые и малозаметные препятствия (глубокие ямы, канавы, овраги) ограждают или отмечают предупредительными знаками и об этом заранее сообщают трактористу.
2. Перед началом работ выбирают целесообразную схему работы машин и устанавливают наиболее выгодное направление рабочих ходов агрегатов, учитывая состояние поверхности почвы. Движение агрегата должно совпадать с направлением предшествующей вспашки или движением уборочных машин.
3. При выбранном направлении движения агрегата на поле отмечают поворотные полосы и провешивают линию первого прохода. Ширину поворотной полосы выбирают в зависимости от состава агрегатов и способа движения пределами поля, поворотные полосы не отбивают.
4. При выборе длины гона учитывают, что машины для внесения минеральных удобрений относятся к группе машин с ограниченным запасом рабочего хода, так как их емкости требуют периодической загрузки. Наилучшие условия для работы агрегатов создаются, когда запас рабочего хода (длина пути, проходимого агрегатом в рабочем положении между двумя очередными загрузками) достаточен на движение агрегата до конца гона и обратно.
Длину гона выбирают кратной запасу рабочего хода. В практике, однако, наблюдаются различные соотношения между ними: длина гона в несколько раз меньше запаса рабочего хода; длина гона примерно равна запасу рабочего хода; длина гона в несколько раз больше запаса рабочего хода.
5. Для каждого из указанных случаев в зависимости от технологической схемы работы машин существуют свои наиболее целесообразные варианты разбивки поля.
6. При подготовке поля для работы по прямоточной технологии руководствуются общими требованиями. Кроме того, при разметке поля, у которого длина гона примерно равна запасу рабочего хода, учитывают состояние подъездных путей и расположение поля относительно места заправки. Если место заправки находится в направлении движения агрегата, то поле разбивают на два участка и обрабатывают сначала один участок, а затем — другой. При этом длина участка должна составлять половину запаса рабочего хода. Если место заправки расположено в направлении, перпендикулярном движению агрегатов, и имеются подъездные пути к обоим концам поля, то его на участки не разбивают, а агрегат заезжает на поле с одного из его концов, движется до противоположного конца поля, затем подъезжает к месту заправки, и процесс повторяется. В этом случае длина обрабатываемого участка должна быть равной запасу рабочего хода агрегата.
7. При работе разбрасывателей по перегрузочной схеме с использованием перегрузчиков типа САЗ-3502 подготовка поля и выбор способов движения агрегатов зависят не только от соотношения длины гона и пути разбрасывания, но и от способности перегрузчиков передвигаться по полю.
Если перегрузчики могут свободно проходить по полю, его размечают, руководствуясь общими требованиями к разметке полей, а агрегаты заправляют в различных местах.
Если движение перегрузчиков по полю затруднено, то агрегаты заправляют на границах поля, а само поле размечают в соответствии с требованиями по подготовке полей для прямоточного способа работы, исходя из соотношения длины гона к запасу рабочего хода агрегата.
8. При работе машин по перевалочной технологической схеме руководствуются общими требованиями к разметке полей, учитывая соотношение длины гона к запасу рабочего хода и место расположения заправки, как и по прямоточной схеме.
9. Дополнительно определяют места разгрузки удобрений. Места расположения куч (штабелей) отмечают вешками с указанием количества удобрений, которое необходимо сгрузить в данном месте.
10. Количество удобрений в куче (штабеле) определяют по формуле.
11. При подготовке группы полей примерно равной площади, расположенных на расстоянии друг от друга не более 1...2 км, удобрения размещают в одной куче (штабеле) на расстоянии, одинаковом от этих полей. Если поля значительно отличаются по размерам, то выгоднее расположить кучу (штабель) удобрений у поля, имеющего большую площадь.
Подготовка полей зависит от используемых агрегатов, предполагаемых способов их движения и схемы организации работы.
При работе на поле нескольких агрегатов его разбивают на отдельные участки с учетом сменной выработки машин. На поле отмечают поворотные полосы, линию первого прохода агрегата и места заправки сеялок или разбрасывателей (при перевалочной схеме работы).
Основным способом движения агрегатов на внесении минеральных удобрений является челночный.
В случаях, когда повороты агрегата можно делать за пределами поля, поворотные полосы не отбивают.
На полях с малой длиной гона (до 250 м), а также при работе с широкозахватными агрегатами (3-5-сеялочными) применяется способ движения с перекрытием. Такой способ работы наиболее целесообразен, когда отсутствует возможность выезда за пределы поля, так как в этом случае ширина поворотной полосы сокращается примерно на Vs по сравнению с челночным способом.
При движении агрегатов способом с перекрытием поле разбивают на отдельные загоны. Ширина загона зависит от состава агрегата.
6. Правила личной гигиены при работе с удобрениями.
Меры безопасности: Коллекция предназначена для ознакомления с внешним видом удобрений, открывать емкости с удобрениями запрещается! При работе соблюдайте общие требования безопасности и правила личной гигиены.
Меры первой доврачебной помощи в случае контакта с удобрениями: При попадании на кожу - смыть водой с мылом. При попадании в глаза - промыть большим количеством воды и при необходимости обратиться к врачу для консультации. При попадании в желудок - дать выпить несколько стаканов воды, прополоскать рот, вызвать рвоту. При необходимости вызвать врача или доставить пострадавшего в медицинское учреждение.
7. Техника безопасности при работе разбрасывателей удобрений
Общие положения. При ремонте сельскохозяйственных машин рабочие должны знать и выполнять правила безопасности, производственной санитарии и противопожарные мероприятия.
Для предупреждения несчастных случаев на производстве действующим законодательством предусмотрено обязательное обучение всех работников правилам техники безопасности.
Вводный инструктаж - это начальный этап обучения рабочего технике безопасности. Рабочего знакомят с правилами безопасности на территории ремонтного предприятия, рассказывают о правилах, которые следует соблюдать при организации и содержании рабочих мест, и разъясняют влияние правильной организации рабочего места (размещение инструментов, приспособлений, материалов и т. д.) на повышение производительности труда. Кроме того, рассматривают правила безопасности труда при обслуживании станочного оборудования, разъясняют правила ношения рабочей одежды и защитных средств, общие правила электробезопасности.
При проведении вводного инструктажа на рабочем месте заведующий мастерской или бригадир рассказывает об обязанностях рабочих, об устройстве и обслуживании оборудования и механизмов, о значении и правилах пользования предохранительными устройствами, о правилах техники безопасности при использовании транспортных средств и грузоподъемных механизмов.
Проведение инструктажа на рабочем месте фиксируют в журнале регистрации. Карточка с указанием вводного инструктажа и журнал регистрации являются документами, которыми руководствуются при разрешении трудовых споров, возникающих в процессе работы.
Разборочно-сборочные работы. Съемники и приспособления для сборки и разборки должны быть исправны. При сборке сборочных единиц и механизмов, оснащенных пружинами, используют приспособления, обеспечивающие невозможность внезапного действия пружины.
Зевы гаечных ключей должны соответствовать размерам гаек и головок болтов. Запрещается подкладывать металлические пластины между головкой болта (гайкой) и зевом ключа. Не допускается удлинять гаечные ключи присоединением другого ключа или трубы, ударять молотком по ключу, а также отвертывать гайки и болты при помощи зубила и молотка.
При вывертывании или,ввертывании шлицевых винтов рекомендуется пользоваться отверткой с длиной рабочей части, равной диаметру головки винта.
При работе раздвижным ключом необходимо прижимать губки ключа вплотную к граням гайки и поворачивать его в сторону подвижной части ключа.
Нельзя размечать тяжелые детали на краю верстака или полки стеллажа.
Совпадение отверстий проверяют только специальными оправками и ломиками.
При снятии или установке тяжелых грузов необходимо пользоваться подъемно-транспортными средствами. При этом не следует поднимать груз, масса которого превышает грузоподъемность механизма. Следует надежно и без перекоса крепить груз на крюке и не оставлять груз в поднятом состоянии.
Для мойки деталей, требующих промывки на рабочем месте, нужно пользоваться передвижными моечными ваннами с крышками.
При обкатке машины на стенде следует предварительно убедиться, что в опасной зоне нет людей, и перед пуском стенда дать предупредительный сигнал.
Слесарные, сверлильные и токарные работы. Рабочее место рабочего оборудуют исправными приспособлениями и инструментом. Тиски должны быть прочно укреплены на верстаке. Запрещается пользоваться тисками с изношенной насечкой губок. Бойки молотков и кувалд должны быть слегка выпуклыми и гладкими, ручки молотков и кувалд закрепляют заершенным клином из мягкой стали. Поверхность ручек должна быть овальной, гладкой, без трещин, заусенцев и сучков. Напильники, шаберы и другой инструмент с заостренными нерабочими концами должны быть надсажены на рукоятки с бандажными кольцами. На ударной поверхности зубил, крейцмейселей, бородков и других инструментов не должно быть заусенцев, выбоин и трещин, затылки инструментов не должны быть скошены или сбиты.
Напильники очищают от стружки металлической щеткой. Не разрешается выбивать стружку ударами по напильнику.
При рубке твердых и хрупких металлов зубилом или крейцмейселем следует пользоваться защитными очками. Резать металл ручными и приводными ножовками следует только после того, как ножовочные полотна натянуты и прочно закреплены.
Выполняя работы на сверлильном станке, необходимо устанавливать сверло и патрон только при остановке шпинделя. Сверло должно быть надежно закреплено в патроне, который сцентрирован с осью шпинделя станка. Запрещается останавливать патрон руками. Деталь укрепляют на столе станка в машинных тисках. Перед выходом сверла из отверстия нужно, выключить автоматическую подачу и перейти на ручную, уменьшив нажим на сверло. Стружку необходимо удалять железным крючком или щеткой при остановленном станке. Запрещается охлаждать сверло мокрой тряпкой.
При выполнении токарных работ устанавливать и снимать патрон, инструмент, детали, а также переключать скорости можно только при полной остановке станка.
Длина устанавливаемых под резец подкладок должна быть равна длине всей опорной поверхности резца. При работе на токарном станке следует использовать защитный экран, а при его отсутствии специальные очки. Работать без защитных ограждений запрещается.
Работая пневматическим инструментом, необходимо соблюдать следующие меры предосторожности: присоединять и отъединять шланги только после прекращения подачи воздуха; перед присоединением к пневматическому инструменту продувать шланги; перед началом работы инструмент опробовать вхолостую; переносить пневматический инструмент, соединенный с воздушным шлангом, взявшись рукой только за рабочую часть инструмента или шланг. При обрыве шланга, перерывах в работе и неисправности перекрывают воздушный вентиль и выключают воздух только тогда, когда инструмент установлен в рабочее положение.
Для безопасности работы с электроинструментом следует проверить состояние выключателя, заземляющего провода и надежность изоляции питающих проводов. При работе электроинструментом пользуются резиновыми перчатками, галошами и резиновыми ковриками. При необходимости переноса электроинструмента его следует отключить от силовой линии и держать за корпус. Заменять сверла или шлифовальные круги необходимо только после отключения электроинструмента от силовой линии. Электроинструмент подключают к силовой линии только при помощи штепсельного разъема. В случае сильного нагрева электроинструмента нужно делать перерывы в работе и включать его на некоторое время вхолостую. Во избежание несчастного случая нельзя присоединять электроинструмент к оголенным концам проводов, контактам рубильников или пускателей.
Сварочные работы. Необходимо защищать глаза, лицо и тело от излучений сварочной дуги масками, шлемами и щитками. К сварке допускают только рабочих, сдавших экзамены по соответствующей программе и получивших право на выполнение сварочных работ.
Спецодеждой сварщика должны служить брезентовая куртка, брюки навыпуск, кожаные ботинки и брезентовые рукавицы, а электросварщика - диэлектрические перчатки или рукавицы. Одежда сварщика должна быть сухой, без следов масла.
При выполнении газосварочных и электросварочных работ необходимо следить за тем, чтобы всегда действовала вентиляция. Это особенно важно при сварке металлов с примесью цинка, меди, свинца или бронзы.
Учитывая взрывоопасность ацетилена даже при малых его количествах в окружающем воздухе, газосварщик должен следить за исправностью газосварочной аппаратуры и не допускать утечки ацетилена из шлангов и генераторов. Ацетиленовые генераторы устанавливают в специальных помещениях.
Тару, в которой упакован карбид кальция, во время перевозок необходимо защищать от толчков и не допускать нарушения герметичности упаковки. Вскрывая барабаны с карбидом, нужно предохраняться от появления ацетилена. При вскрытии барабанов не следует применять стальные зубила, которые могут вызвать появление искры. Для этого используют латунные зубила и молотки.
При сборке газосварочной аппаратуры шланги необходимо плотно надевать на ниппеля водяных затворов, но не закреплять их проволокой.
Кислородные баллоны и аппаратуру, соприкасающуюся с кислородом, нужно оберегать от попадания масел или жира. При транспортировке кислородных баллонов следует соблюдать особую осторожность и переносить баллоны при помощи носилок и ручных тележек.
Запорный вентиль кислородного баллона нужно открывать плавно и медленно, находясь при этом в стороне от струи газа. Не допускается открытие вентиля гаечным ключом, зубилом и молотком. При необходимости применяют специальный ключ.
Дата добавления: 2021-06-02; просмотров: 92; Мы поможем в написании вашей работы! |
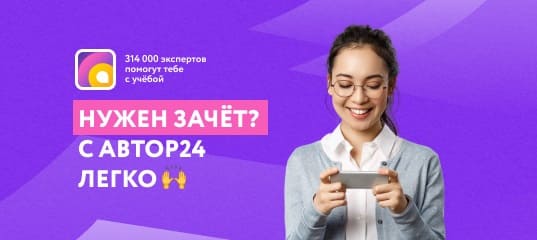
Мы поможем в написании ваших работ!