Агломерация Окомкование Брикетирование
Министерство науки и высшего образования Российской Федерации
Технический институт (филиал) федерального государственного
автономного образовательного учреждения высшего образования
«Северо-Восточный федеральный институт имени М.К. Аммосова»
в г. Нерюнгри
Учебно-методическое пособие
Самостоятельная работа студентов
по дисциплине «Обогащение полезных ископаемых»
для студентов по специальности 21.05.04 «Горное дело»
Часть 1
Нерюнгри 2019
Утверждено научно-методическим советом Технического института (филиала) «СВФУ им. М.К. Аммосова».
Составители:
Э.Ф. Редлих – старший преподаватель кафедры «Горное дело» ТИ (ф) СВФУ
В.Ф. Рочев - к.т.н., доцент кафедры Горное дело» ТИ (ф) СВФУ
Рецензенты:
В учебно-методическом пособии по дисциплине «Обогащение полезных ископаемых» представлены: теоретическая подготовка студентов, вопросы по темам для студентов очного и заочного обучения по специальности: 21.05.04 «Горное дело», специализации: «Открытые горные работы», «Подземная разработка пластовых месторождений», «Маркшейдерское дело», «Электрификация и автоматизация горного производства».
© Технический институт (ф) СВФУ, 2019
ОГЛАВЛЕНИЕ
|
|
Введение | 4 | |
Раздел 1. Подготовительные процессы 1.1Грохочение 1.2Дробление 1.3Измельчение 1.4Классификация | 5 19 30 36 | |
Раздел 2 Основные обогатительные процессы 2.1 Гравитационные методы обогащения 2.2.Флотационные методы обогащения | 51 81 | |
Раздел 3. Вспомогательные процессы 3.1Обезвоживание продуктов обогащения 3.2 Дренирование 3.3 Центрифугирование 3.4 Сгущение 3.5 Фильтрование 3.6 Окускование 3.7Сушка | 94 94 95 96 97 98 101 106 | |
Раздел 4. Опробование и контроль процессов обогащения | 110 | |
Раздел 5. Технология обогащения полезных ископаемых 5.1 Обогащение руд цветных металлов 5.2 Обогащение руд черных металлов 5.3 Обогащение угля Список литературы | 112 115 117 119 | |
ВВЕДЕНИЕ
Обогащением полезных ископаемых называют совокупность процессов первичной обработки минерального сырья, добытого из недр, в результате которых происходит отделение полезных минералов, а при необходимости и их взаимное разделение, от пустой породы.
В результате обогащения получают один или несколько продуктов, называемых концентратами. Так как большая часть ценного компонента переходит в один продукт ,т.е. концентрат, то другой продукт получаемый в процессе обогащения называется отходами (хвостами), обедняется. Это не значит, что хвост – это пустая порода, иногда идет обогащение хвостов, для выделения из них полезных продуктов.
|
|
Полезным или ценным компонентом называют тот элемент или природный минерал, с целью получения которого добывается данное полезное ископаемое.
Например: медь - в медных рудах; железо- в железных рудах и т.п.
Кроме основных компонентов в полезном ископаемом могут содержаться примеси, они могут быть полезными и вредными. Полезные примеси, это примеси которые могут быть извлечены в процессе обогащении, и вредные- ухудшающие качество полезного ископаемого.
Основные группы твердых полезных ископаемых:
-металлические: руды, служащие сырьем для получения черных, цветных, редких, драгоценных и других металлов;
- неметаллические: сырье для получения неметаллических элементов и соединений, строительных материалов, керамических изделий, абразивных и других материалов.
- горючие полезные ископаемые: уголь, сланцы, торф, используемые как топливо или химическое сырье.
|
|
Технология обогащения ПИ состоит из ряда последовательных операций, осуществляемых на ОФ. Обогатительными фабриками наз. промышленные предприятия, на которых методами обогащения обрабатывают полезные ископаемые и выделяют один или несколько товарных продуктов с повышенным содержанием ценных компонентов и пониженным содержанием вредных примесей.
I. ПОДГОТОВИТЕЛЬНЫЕ ПРОЦЕССЫ
1.1 ГРОХОЧЕНИЕ
Теоретическая подготовка
1.Назначение операций грохочения.
Процесс разделения материала на два или несколько классов крупности носит общее название - классификация по крупности. Такое разделение осуществляется двумя основными способами:
- грохочением;
- классификацией в водной или воздушной среде.
Грохочение - это процесс разделения кусковых и зернистых материалов на продукты различной крупности, называемые классами, с помощью просеивающих поверхностей с калиброванными отверстиями.
В результате грохочения исходный материал разделяется на надрешетный (верхний) продукт, зерна (куски) которого больше размера отверстий просеивающей поверхности. Надрешетный продукт называют классом +d (крупнее d ), а подрешетный продукт -d ( мельче d) ,
|
|
где d – размер отверстия сита.
При последовательном просеивании материала на n –ситах получаeтся
n +1 классов крупности:
+d1 ;
________
-d1 + d2
________
-d2 + d3 и т.д.
(например классы +25; -25+13;-13+6 и -3)
Последовательный ряд абсолютных размеров отверстий сит (от больших к меньшим), применяемых при грохочении, называют шкалой сит или шкалой грохочения. Постоянное отношение размера отверстий предыдущего сита к размеру отверстий последующего называется модулем шкалы сит. Чаще всего применяют модуль «2» (100,50,25) и √ 2 (1,41) , в основании которого принято сито с отверстием размером 0,074 мм.
Грохочение производится на грохотах, который имеет одну или несколько просеивающих поверхностей, установленных в одном или нескольких коробах.
Основные виды операций грохочения:
- подготовительное грохочение применяется для разделения материала на несколько классов, предназначенных для последующей раздельной обработки;
- вспомогательное грохочение применяется при дроблении для выделения готового класса из продукта перед его дроблением, для контроля крупности дробленного продукта;
- самостоятельное грохочение применяется для разделения на классы, представляющие собой готовые продукты (ж.р., стрит.материалы);
- избирательное грохочение применяется для обогащения полезных ископаемых, при различии в твердости, крепости или форме кусков ценного продукта и пустой породы;
- обезвоживающее грохочение применяется для удаления основной массы воды или пульпы от зернистых материалов.
По размерам кусков различают грохочение:
- крупное (от 300 до 100мм);
- среднее (от 60 до 25 мм);
- мелкое (от 25 до 6 мм);
- тонкое (от 6 до 0,5 мм);
- особо тонкое (до 0,045 мм).
2.Гранулометрический состав.
Распределение зерен минерального сырья по классам крупности характеризует гранулометрический состав исходного сырья продуктов обогащения.
Для определения гранулометрического состава используют следующие способы:
- измерение крупных кусков по трем взаимно перпендикулярным направлениям;
- ситовый анализ – рассев на наборе сит на классы различной крупности.
Ситовый анализ крупных материалов(продуктов дробления) производится вручную на наборе сит или с помощью автоматического вибрационного гранулометра, мелких материалов(продуктов измельчения) производится на механическом анализаторе (встряхивателе);
- седиментационный анализ - разделение материала по скорости падения частиц различной крупности в водной среде для материала крупностью от 40 до 5 мкм;
- микроскопический анализ- измерение частиц под микроскопом и классификация их на группы в узких границах определенных размеров(от 50 мкм до десятых долей микрометра).
Такой анализ позволяет определять выходы различных классов, производительность дробильных и измельчительных аппаратов, осуществлять контроль процессов грохочения, дробления, измельчения и т.д.
3. Ситовый анализ
Заключается в рассеве пробы материала на нескольких ситах с различными стандартными размерами отверстий заданного модуля. Ситовый анализ материала крупнее 25 мм производится вручную на наборе сит или качающихся горизонтальных грохотах. Материал менее 25 мм рассеивается на лабораторных ситах. В зависимости от крупности материала и необходимой точности ситового анализа пробы рассеиваются сухим или мокрым способом.
Например:
Если позволяет крупность материала и он не подвержен слипанию применяется сухой способ рассева на механическом встряхивателе:
- сита устанавливают друг над другом сверху вниз от крупных размеров до мелких;
- пробу засыпают на верхнее сито, закрывают крышкой и встряхивают в течение 10-30 мин;
- после рассева каждый класс крупности взвешивают на технических весах;
- выход каждого класса определяется делением массы класса на общую массу пробы.
Для тонкоизмельченного материала применяют мокрое просеивание. Для этого пробу засыпают на сито с мелкими отверстиями и производят отмывку мельчайших частиц многократным погружением сита в бачок с водой или промывкой материала на сите слабой струей воды. Отмывку производят до тех пор , пока промывочная вода не станет прозрачной. Оставшийся на сите материал высушивают и взвешивают. По разности определяют массу отмытого шлама. Высушенный материал повторно рассеивают сухим способом на ситах, включая и самое мелкое, на котором производилась отмывка шлама. Определив массу подрешетного продукта последнего сита, ее прибавляют в полученной ранее массе отмытого шлама.
Результаты ситового анализа приводятся в виде таблиц или графиков.
Таблица 1- Ситовый анализ
Класс | Выход | |||
Частный | Суммарный,% | |||
кг | % | По «+» | По «-« | |
-25+13 | 8 | 10 | 10 | 100 |
-13+6 | 11,2 | 14 | 24 | 90 |
-6+3 | 12,8 | 16 | 40 | 76 |
-3+1 | 14,4 | 18 | 58 | 60 |
-1+0,5 | 16 | 20 | 78 | 42 |
-0,5+0 | 17,6 | 22 | 100 | 22 |
По данным ситового анализа строятся характеристики крупности.
На оси ординат откладывают суммарный выход классов в процентах, на оси абсцисс - размеры отверстий сит в мм. На основании суммарных выходов материала крупнее диаметра отверстий сита строится кривая по «плюсу» мельче «по минусу». Сумма выходов по обеим кривым должна всегда равняться 100%. Поэтому обе кривые характеристик являются зеркальным отражением одна другой. Они всегда пересекаются в точке соответствующей суммарному выходу 50%. Точка пересечения кривой с осью абсцисс показывает максимальный размер куска материала в данной пробе.
Суммарные характеристики «по плюсу» бывают вогнутыми, выпуклыми и прямолинейными.
Вогнутые указывают на преобладание мелких зерен в пробе (хрупкие полезные ископаемые, уголь), выпуклые – для крепких руд. По суммарной характеристике крупности можно определить выход любого класса, для этого на оси абсцисс находят размер нужного класса и перпендикулярно к оси ординат проводят линию до пересечения с осью. Точка пересечения определяет суммарный выход искомого класса.
При построении суммарных характеристик в широком диапазоне размеров отверстий сит графики получаются сильно растянутыми. Чтобы избежать этого, графики строят в системе координат с полулогарифмическими (по оси ординат откладывают логарифмы размеров сит) или логарифмическими (по оси ординат также откладывают логарифмы суммарных выходов классов) шкалами.
4. Конструкции грохотов
4.1.Общие сведения
Все грохоты можно подразделить на две основные группы:
- с неподвижной просеивающей поверхностью (колосниковые, прямоугольные, конические, цилиндрические, дуговые);
- с подвижной просеивающей поверхностью (барабанные, валковые, плоскокачающиеся и вибрационные).
4.2.Неподвижные грохоты.
А. Неподвижные колосниковые грохоты представляют собой наклонные решета, собранные из колосников, образующих между собой продольные щели. Размер щели между колосниками составляет не менее 50 мм, угол наклона при грохочении руд 40-50о , углей 30-35о . При грохочении влажного материала угол наклона увеличивают на 5-10о. Решета по бокам обычно имеют борта. Исходный материал загружается на верхнюю часть решетки и движется по ней самотеком под действие силы тяжести. Во время движения более мелкий материал проваливается через щели между колосниками, а надрешетный продукт разгружается в конце решета.
Площадь решетки колосникового грохота F(м2) определяется по эмпирической формуле
где Q – производительность грохота по исходному материалу, т/ч ;
а – ширина щели между колосниками, мм
Ширина грохота В во избежание заклинивания крупных кусков должна быть не менее тройного размера d max наибольшего куска (В≥3d max) , а длина L=2В или больше. Чаще всего L/B =2/3 . Практически длина составляет
3-5 м. Эффективность грохочения неподвижных колосниковых грохотов низкая и обычно изменяется в пределах 50-60%. Применяют их чаще для крупного и реже для среднего грохочения, когда допустима пониженная эффективность грохочения.
Б. Прямоугольные грохоты применяют для предварительного отсева мелких классов (0-6 или 0-13) угля при пониженных требованиях к засорению надрешетного продукта подрешетным. Эти грохоты применяют как для сухого ,так и для мокрого грохочения углей. Грохот представляет собой неподвижный наклонный (40-50о к горизонту) короб, на дне которого расположена просеивающая поверхность (колосниковое сито). Грохоты снабжают очистительными устройствами. При мокром грохочении вода, подаваемая из сопел, интенсивно отмывает подрешетный продукт и удаляется вместе с ним.
В. Дуговой грохот (сито) представляет собой полукруглую колосниковообразную щелевидную (шпальтовую) решетку с поперечно расположенными по отношению к потоку колосниками 6. Исходное питание поступает в приемную коробку 5, откуда через кромку стенки 4 кармана 3 попадает на колосниковую решетку. Подрешетный продукт с водой проходит через отверстия сита и удаляется через разгрузочный патрубок 1, а надрешетный продукт сходит в конце сита. Колосниковая решетка в нижней части крепится к раме 2 с помощью деревянных клиньев 7, уголков 8 и упора для решетки 9. Колосниковая решетка собирается из колосников трапецеидального сечения, изготовленных из износостойкой нержавеющей стали. Размер отверстий сит S= 0,3-3 мм.
Дуговые грохоты применяют для мокрого грохочения мелкого и тонкого материала (12-0,071 мм). Исходный материал в виде пульпы подается на решетку самотеком или насосом. Центробежная сила, возникающая при круговом движении пульпы по ситу, способствует эффективному выделению воды и мелкого материала через щелевые отверстия сита. Эффективность грохота- 30-75%. Применяют на углеобогатительных фабриках для обесшламливания, предварительного обезвоживания, а также на рудообогатительных фабриках.
Г. Конические циклонные грохоты сходны по принципу действия с дуговыми грохотами и состоят из усеченного конуса в верхней части и пирамиды в нижней части, соединенных кольцом и расположенных в корпусе. Стенки этих частей выполнены из стержней или колосниковой решетки.
Грохоты с неподвижной рабочей поверхностью высоко-производительны, отличаются простотой конструкции , эксплуатационной надежностью, отсутствием динамических нагрузок на здание, низким уровнем шума.
Недостаток- пониженная эффективность грохочения.
4.3 Подвижные(механические) грохоты.
А. Барабанные грохоты в зависимости от формы барабана бывают цилиндрическими и коническими. Просеивающей поверхностью в них являются боковые перфорированные или сетчатые стенки барабана 1, наклоненные к горизонту под углом от 1 до 14о (чаще 4-7о ). Барабан от привода вращается на опорных роликах 2. Исходный материал загружается внутрь барабана на верхнем его конце и за счет вращения и наклона барабана перемещается в продольном направлении. Во время движения мелкий материал просеивается через отверстии сита, а крупный (надрешетный продукт) удаляется из барабана в нижнем его конце.
Барабанные грохоты изготавливают также для грохочения материала на несколько классов. В этом случае сито собирается по длине из нескольких секций, имеющих разные размеры отверстий, меньшие у места загрузки и наибольшие у разгрузочного конца или сита изготавливают концентрическими, в этом случае сито с более крупными отверстиями входит в сито с более мелкими отверстиями. Применяют также грохоты с барабаном призматической формы (шестигранной), которые называются бутарами.
Диаметр барабанных грохотов изменяется от 500 до 3000 мм, длина от 2000 до 9000 мм, производительность 200-25- т/ч. Эффективность грохочения составляет 60-70 %.
Частота вращения грохота n (мин-1 ) устанавливается в пределах
R – радиус барабана, м.
Барабанные грохоты отличаются спокойной работой, их легко герметизировать пыленепроницаемым кожухом. Однако они громоздки, имеют малую удельную производительность( на 1 м2 просеивающей поверхности). Применяются для промывки глинистых руд (скрубберы), промывки и сортировки щебня, гравия и песка и т.д.
Б. Инерционные грохоты ГИЛ,ГИС,ГИТ относят к вибрационным грохотам с круговыми колебаниями(вибрациями). Они просты по конструкции и состоят из трех основных деталей: короба с ситом, вибровозбудителя и пружинных опор или подвесок.
Он состоит из короба 3 с ситом 4, установленным на пружинах(рессорах) 2 под углом 15-30о к горизонту и закрепленных на раме 1. По бокам короба укреплены два подшипника 8, через которые проходит вал 5 вибровозбудителя с закрепленными на нем шкивами 6, имеющими неуравновешанные грузы - дебалансы 7. Вал вибровозбудителя приводится во вращение от электродвигателя с помощью клиноременной передачи. При вращении шкивов с дебалансами возникают центробежные силы инерции, вызывающие круговые или эллиптические вибрации грохота. Исходный материал подается в верхнюю часть грохота и за счет вибраций короба и наклона сита продвигается к разгрузочному концу. Во время этого движения происходит просеивание мелкого материала. ГИТ-руды, ГИЛ-угли.
В. Вибрационные грохоты
К ним относят самобалансные грохоты ГСЛ, ГСС, ГСТ или ГИСЛ, ГИСС и ГИСТ.
Отличительная особенность – простота установки и универсальность.
Грохот имеет горизонтальный или наклонный короб 1 с одним или несколькими ситами 3, подвешенный на пружинах 2. Колебания коробу придает самобалансный вибровозбудитель 4, закрепленный на коробе, который состоит из корпуса, в котором на двух параллельных валах размещены два цилиндрических зубчатых колеса с равным числом зубьев и одинаковые дебалансы.
Исходное питание
Ро
Благодаря этому валы вращаются с одинаковой частотой в противоположном направлении. Дебалансы расположены по отношению друг к другу так, что при вращении валов составляющие центробежные силы Ро, то взаимно погашаются (I,III) как силы противоположно направленные и равные по величине, то взаимно складываются (II,IV). По этой причине вибровозбудитель совершает колебания по оси х-х в горизонтальном направлении. ВВ монтируется на коробе под углом 35-55о , за счет чего коробу сообщаются наклонные прямолинейные колебания.(вибрации) Материал, находящийся на сите грохотов подбрасывается и просеивается. Площадь сит от 7,5 до 21 м2 , материал крупностью до 600мм. Эффективность грохочения-80-90%.
Самобалансные грохоты легкого типа применяют для грохочения углей, антрацитов и горючих сланцев, а также обезвоживания продуктов обогащения. Самобалансные грохоты тяжелого типа с несколькими вибровозбудителями применяют для грохочения руд и горячего агломерата.
Производительность Q(т/ч) вибрационных грохотов определяется по эмпирической формуле
F – рабочая площадь сита, м2 ;
q – удельная производительность на 1 м2 поверхности сита,м 3/(ч·м2);
δ - насыпная плотность грохотимого материала,т/м3;
l - поправочный коэффициент (содержания исходного материала зерен размером меньше половины размера отверстия,%);
k – поправочный коэффициент (содержания в исходном материале зерен размером больше размера отверстий сита,%);
m – поправочный коэффициент эффективности грохочения, %;
n – поправочный коэффициент формы зерен ;
o – поправочный коэффициент состояния материала;
p – поправочный коэффициент зависящий от способа грохочения.
4.4 Просеивающие поверхности грохотов и эффективность грохочения.
Конструкции просеивающих поверхностей зависят от технологического назначения грохота и условий его работы. В качестве просеивающей(рабочей) поверхности грохотов применяют колосниковые решетки, листовые сита(решета) и проволочные сетки.
1. Колосниковые решетки.
Применяют преимущественно для крупного и среднего грохочения как в неподвижных, так и в подвижных грохотах. Решетки собирают из стержней и колосников различной формы параллельными рядами. Часто решетки собирают на месте из рельсов, сварных металлических балок и т.п. На вибрационных грохотах колосниковые решетки изготовляют сборными, состоящими из отдельных секций.
2.Листовые решета
Применяют для среднего грохочения. Они представляют собойстальные листы с просверленными или проштампованными отверстиями различной формы.
Во избежание забивания отверстий сит, их делают в колосниковых и листовых решетах расширяющимися книзу. Толщина листа равна 4-6 мм при размере отверстий менее 10мм и 8-10мм для отверстий 30-60мм. В последнее время начали применять резиновые листовые решета с квадратными и прямоугольными отверстиями. Они износоустойчивы, меньше забиваются, снижают уровень шума, применяют для мелкого грохочения.
3.Проволочные сетки
Их изготавливают из стальной (легированная или нержавеющая сталь), латунной, медной, бронзовой, никелевой и другой проволоки с прямоугольными или квадратными отверстиями.
Начато изготовление сеток с капроновыми нитями, которые более износоустойчивы по сравнению с металлическими.
Коэффициент живого сечения.
Просеивающая поверхность грохота характеризуется коэффициентом живого сечения. Этот коэффициент определяется как отношение площади отверстий сита в свету к общей его площади и выражается в процентах.
Для сеток с квадратными отверстиями:
Для сеток с прямоугольными отверстиями:
a – диаметр проволоки в мм;
b – ширина отверстия, мм;
l - длина отверстия в мм.
На практике стремятся использовать решета с наибольшим коэффициентом живого сечения, т.к. они повышают эффективность грохочения. При грохочении влажных и особенно глинистых материалов отверстия сит быстро замазываются и живое сечение уменьшается. Для предотвращения этого применяют струнные сита или подогрев сит.
4. Эффективность грохочения - количественная оценка полноты отделения мелкого материала от крупного.
Эффективность грохочения Е определяется отношением массы фактически полученного подрешетного продукта к массе его в исходном материале(%,1).
С- масса подрешетного продукта,т;
Q- масса исходного материала;
а – содержание нижнего класса в исходном материале, %.
Так как в производственных условиях непосредственное определение массы полученного подрешетного продукта затруднено, на практике используют другую формулу для Е или ή (кпд грохочения):
η – кпд грохочения, % ;
b – содержание нижнего класса в надрешетном продукте, %.
Значения а и b определяют на основании тщательного рассева проб исходного материала и надрешетного продукта.
Основными показателями работы грохота являются его производительность и эффективность. Эти показатели всегда взаимосвязаны. Производительность различных грохотов можно сравнивать при условии, что они обуславливают одинаковую эффективность грохочения. Считается, что от ширины грохота зависит его производительность, а от длины- эффективность грохочения.
5. Факторы, влияющие на процесс грохочения
А. Влажность материала;
Повышенная влажность вызывает слипание частиц между собой и залипание отверстий. Обычно это наступает при влажности материала более 10-12%.Эффективность грохочения резко снижается. В этом случае производят мокрое грохочение.
Б. Геометрическая форма зерен;
Наиболее благоприятной является круглая форма.
Наиболее трудными для просеивания являются зерна, диаметр которых близок к размеру отверстия сита
«Трудные» - 0,75 диаметра сита и выше.
«Затрудненные»- размер которых больше отверстия сита, но меньше их полуторной величины.
В. Угол наклона сита;
Увеличение угла – уменьшает размер отверстия и увеличивает скорость движения зерен по ситу и соответственно проскакивание мимо отверстий. Оптимальный угол наклона сита устанавливают экспериментально.
Г. Плотность исходного материала.
Для материала большей плотности – производительность выше.
Вопросы для самопроверки
1. Основные понятия и назначение операции грохочения. Класс. Шкала грохочения. Модуль шкалы классификации.
2. Понятие о крупности.
3. Средний диаметр куска сыпучего материала и его определение. Стандартные шкалы сит.
4. Гранулометрический состав. Общее понятие о седиментационном и микроскопическом анализах. Ситовый анализ. Обработка данных ситового анализа.
5. Частная и суммарная характеристики крупности.
6. Уравнения характеристик крупности (Область применения каждого уравнения).
7. Порядок выделения классов при грохочении.
8. Просеивающая поверхность грохотов: колосниковые решетки, листовые сита (решета), шпальтовые решета, струнные сита, резиновые сита, проволочные сетки, коэффициент живого сечения просеивающей поверхности, способы плетения сеток.
9. Эффективность процесса грохочения. Определение эффективности грохочения, вывод формулы.
10. Легкие, трудные и затрудняющие зерна.
11. Влияние различных факторов на эффективность процесса грохочения.
12. Классификация грохотов.
13. Неподвижные колосниковые грохоты.
14. Валковые грохоты.
16. Барабанные грохоты: призматические, цилиндрические, ГЦЛ.
17. Вибрационные грохоты
18. Дуговые грохоты.
1.2 ДРОБЛЕНИЕ
Теоретическая подготовка
1.Назначение операций дробления.
Дробление и измельчение- процессы разрушения полезных ископаемых под действием внешних сил до заданной крупности, требуемого гранулометрического состава или необходимой степени раскрытия минералов При дроблении и измельчении не следует допускать переизмельчения материала, т.к. это ухудшает результаты обогащения и удорожает процесс.(Частицы размером менее 20-10 мкм обогащаются неудовлетворительно).
Процессы дробления и измельчения могут быть подготовительными операциями или иметь самостоятельное значение. Эти процессы принципиально не различаются между собой.
Дробление- крупность более 5мм (разрушение – в дробилках).
Измельчение – менее 5 мм.(разрушение в мельницах).
При дроблении и измельчении применяют следующие способы разрушения:
Степень дробления (или измельчения) показывает степень сокращения крупности в процессе разрушения кускового материала. Она характеризуется отношением размеров максимальных кусков в дробимом и дробленном материале.
i – степень дробления;
Dmax и D ср - соответственно максимальный и средний размеры дробимого материала;
d max и d ср - соответственно максимальный и средний размеры дробленного материала.
На практике степень дробления может быть очень высокой, которую в один прием дробления получить невозможно. Дробилки работают эффективно только при ограниченных степенях дробления – обычно 3-8. Исключение составляют дробилки ударного действия, применяемые для дробления хрупких полезных ископаемых, тогда степень дробления может достигать - 30.
1.Раздавливание
4.Срезывание
Поэтому дробление крупного материала до требуемого размера производится в несколько приемов, называемых стадиями дробления.
Дробление …………………………крупное среднее мелкое
Максимальная крупность
материала, мм
до дробления 500-1500 100-350 40-100
после дробления 100-350 40-100 10(5)-30
Степень дробления, достигаемая в каждой отдельной стадии, называется частной.
Пример:
Руда – стадий дробления: 2 или 3.
Калийная соль – 1 стадия дробления.
Магнетитовые руды- четырехстадиальное дробление.
Как правило , крупное, среднее и мелкое дробление производится сухим способом. Мокрое дробление применяется для материалов со значительным содержанием глинистых материалов.
2. Законы дробления.
Законы дробления(измельчения) характерихуют зависимость работы, затрачиваемой на дробление (измельчение), от результатов дробления(измельчения), т.е. крупности продукта.
Работа А (Дж), затрачиваемая на дробление(измельчение), пропорциональна вновь образованной поверхности кусков(частиц) дробленного продукта
где
σ – временное сопротивление сжатию, Н·м/ м2 ;
Δ S – площадь вновь образованной поверхности, м 2 ;
KR – коэффициент пропорциональности , Н·м/ м2 ;
D – характерный размер куска , м.
Уравнение соответствует гипотезе Риттингера(1867г)
Если при разрушении куска кубической формы энергия затрачивается в основном на деформацию объема, то в этом случае производимая работа прямо пропорциональна изменению его первоначального объема и определяется по формуле Кирпичева-Кика
где К и Кк –коэффициенты пропорциональности, Н·м/ м2 ;
Δ V – деформированный объем, м3 ;
П.А.Ребиндер(1941г.) объединил обе гипотезы и в этом случае полная работа дробления
По гипотезе Бонда (1950г.) полная работа дробления пропорциональна среднему геометрическому между объемом и площадью поверхности куска:
Все формулы различаются коэффициентом пропорциональности и показателями степени диаметра дробимого куска. По обобщающей гипотезе
Работу дробления можно представить в виде
где К – коэффициент пропорциональности в общем виде; m =2÷3.
При m =2 формула совпадает с формулой Риттингера, при m=3- с формулой Кирпичева-Кика, при m=2,5 – с формулой Бонда.
Когда степень дробления велика можно пренебречь работой деформации объема и в этом случае применяют закон Риттингера. Когда степень дробления мала (крупное дробление), можно пренебречь работой образования новых поверхностей и тогда подходит закон Кирпичева-Кика. Формула П.А.Ребиндера имеет универсальное значение. Закон Бонда занимает промежуточное положение.
3.Конструкции дробилок
А. Щековые дробилки
В щековых дробилках (ЩД) материал раздавливается между двумя плитами, одна из которых неподвижная, а вторая подвижная (качающаяся). Щековые дробилки бывают с простым (ЩДП) и сложным (ЩДС) движением подвижной щеки.
С простым движением щеки (ЩДП)
Рабочая камера образуется неподвижной 1 и подвижной 2 щеками и двумя боковыми стенками. Подвижная щека 2 шарнирно подвешена на оси 10. Боковые стенки рабочей камеры, а также щеки футеруются съемными плитами из марганцовистой износоустойчивой стали или закаленного чугуна. Поверхность боковых стенок делается гладкой, а щек рифленой. На эксцентрик 3 вала надета головка массивного шатуна 8, получающего при вращении возвратно-поступательное движение. Нижний конец шатуна имеет гнезда, в которые свободно вставлены одним концом две распорные плиты 7. Другими концами распорные плиты вставлены:
левая - в гнездо на подвижной щеке;
правая – в гнездо регулировочного устройства , закрепленного на задней стенке станины. Удержание свободно вставленных в гнезда распорных плит происходит как за счет давления самой подвижной щеки, так и за счет тяги 9 с пружиной 6 , оттягивающей щеку вправо. При движении шатуна вверх угол между распорными плитами увеличивается и подвижная щека приближается к неподвижной, раздавливая материал. При движении шатуна вниз подвижная щека отходит от неподвижной и дробленый материал выпадает из разгрузочного отверстия дробилки. Исходный материал загружается в рабочую камеру дробилки сверху и постепенно в процессе раздавливания опускается вниз. Нагрузки на приводной двигатель крайне неравномерны. Для аккумуляции энергии во время холостого хода и передачи ее во время рабочего хода щеки, на вал шатуна надевают два массивных маховика 4.
Для предохранения дробилки от поломок в случае попадания в рабочую камеру недробимых предметов, правую распорную плиту делают ослабленного сечения(просверливания отверстий в плите, составления плиты из двух частей с клепкой внахлест). Такая плита при повышенных нагрузках ломается и ее заменяют новой, при этом все остальные рабочие механизмы остаются в исправном состоянии. Ширину выпускной щели можно изменять с помощью прокладок и регулировочных клиньев 5. Габаритные размеры загрузочного отверстия дробилок должны быть на 10-15% больше размера наибольших кусков в питании.
Угол захвата не должен превышать 25о , т.к. в противном случае не все куски будут захватываться и будут выбрасываться вверх.
Со сложным движением щеки: (ЩДС)
Отличается тем, что у них подвижная щека 2 подвешена непосредственно на эксцентрик 3 вала, а внизу опирается на одну распорную плиту 7. Благодаря такой подвеске, каждая точка поверхности подвижной щеки движется не по прямой, как у ЩДП, а по эллипсоидной линии. При приближении к неподвижной щеке подвижная щека одновременно движется несколько вверх, а при обратном ходе- вниз. За счет этого в процессе дробления наблюдается не только раздавливание, но и истирание дробимого материала.
Для увеличения степени дробления щековые дробилки изготавливают с увеличенной высотой камеры дробления в 2 2,5 раза больше ширины приемного отверстия. В нижней части неподвижной щеки футеровку скашивают для образования параллельной зоны в месте разгрузки.
В настоящее время введен трехступенчатый запуск дробилок:
1 ступень- приведение во вращение маховика;
2 ступень- передача вращения валу дробилки, благодаря тому , что маховик входит в сцепление с валом дробилки с помощью фрикционной муфты;
3 ступень- приведение во вращение второго маховика.
4. Производительность дробилок
где:
Q- объемная производительность,м3/ч;
KB и C – поправочные коэффициенты( С=1÷0,84);
S ср- ход щеки в средней точке,м;
L и b –соответственно длина и ширина выпускной щели,м;
n – частота качаний щеки,мин-1 ;
B- ширина приемного отверстия,м;
D ср – средневзвешанный размер куска в питании,м;
ά – угол захвата в градусах.
4. Применение, достоинства и недостатки.
Щековые дробилки чаще всего применяют для крупного дробления твердых и средней твердости полезных ископаемых.
Степень дробления в щековых дробилках i=3÷ 5 (до 8).
Достоинства: просты в конструктивном отношении, не требуют большой высоты для установки, пригодны для дробления вязких и глинистых руд.
Недостатки: требуют равномерной подачи питания, нем могут работать под «завалом» и поэтому нуждаются в питателе. Они малопригодны для дробления плитнякового материала. Сменные части дробилок изнашиваются быстро. Поэтому если нет явных технико-экономических показателей их применения, следует искать альтернативные конструкции дробилок.
Б..Конусные дробилки
Принцип действия всех конусных дробилок одинаков. Дробящим рабочим органом у них является подвижный конус, помещенный эксцентрично внутри неподвижного конуса(чаши). Процесс дробления происходит за счет эксцентричного движения внутреннего конуса. Во время приближения дробящего конуса происходит раздавливание , раскалывание, излом находящихся в рабочем пространстве кусков материала, а во время удаления- разгрузка дробленого материала. Процесс дробления происходит непрерывно при последовательном перемещении зоны дробления по окружности конусов.
Марки: ККД, КСД, КМД.
Для крупного дробления руд твердого и средней твердости применяют конусные дробилки с подвесным валом и разгрузкой дробленого продукта под дробилку. Дробление материала происходит в кольцевом рабочем пространстве между наружным неподвижным конусом 1 и подвижным дробящим конусом 2, жестко закрепленным на валу 3. Верхний конец вала шарнирно подвешен в точке О, а нижний – свободно вставлен в эксцентриковый стакан 4. ось О-О’ вала 3 наклонена к оси симметрии О-О дробилки. Эксцентриковый стакан вращается в центральном вертикальном подшипнике 5 корпуса дробилки и поддерживается подпятником 6. При вращении эксцентрикового стакана 4 вокруг оси дробилки О-О ось вала 3описывает коническую поверхность с вершиной в точке О. При этом подвижный дробящий конус совершает круговые движения внутри неподвижного конуса, последовательно максимально приближаясь к стенкам неподвижного конуса и удаляясь от противоположной стороны. Через пол-оборота эксцентрикового станка положение дробящего конуса изменяется на противоположное. Приближение дробящего конуса к неподвижному сопровождается дроблением материала, а удаление разгрузкой продукта под дробилку. При дроблении возникают большие силы трения между кусками материала и поверхностью дробящего конуса, вызывающие вращение вала 3 вокруг своей оси в направлении, обратном вращению эксцентрикового вала. Размер конусных дробилок для крупного дробления характеризуется размером загрузочного отверстия В, а также шириной кольцевой выходной щели е. Производительность
где:
Q – объемная производительность,м3/ч;
К1 - коэффициент (0,6-0,7);
Кк - поправочный коэффициент на крупность;
Кт - поправочный коэффициент на твердость;
Кв - поправочный коэффициент на влажность;
D – диаметр конуса дробления, м;
r - эксцентриситет конуса в плоскости выходной щели, м;
n 0 – частота качаний дробящего конуса, мин-1;
b – размер выпускной щели, м.
Cтепень дробления: 3-6. Для них требуется большая высота, а также они отличаются сложностью конструкции.
Конусные дробилки КСД и КМД имеют сходные конструкции. Они отличаются лишь размерами приемных отверстий, выпускных щелей и профилем дробящей зоны. От дробилок для крупного дробления их отличает характер расположения неподвижного конуса(чаши), который повернут большим основанием вниз, и более пологая форма подвижного конуса.
Производительность
где:
К0 – коэффициент пропорциональности;
Степень дробления: 4-6.
В. Валковые дробилки
В валковых дробилках материал дробится двумя параллельно расположенными валками, вращающимися навстречу друг другу. Исходный материал подается сверху в пространство между валками, захватывается ими и дробится. Валковые дробилки не переизмельчают материал. Валки дробилок бывают гладкими, рифлеными и зубчатыми.
Валковая дробилка с гладкими валками ВДГ состоит из двух валков 1 и 5, вращающихся с одинаковой частотой навстречу друг другу и раздавливающих дробимый материал 3 при ограниченном истирании. Валок 1 насажен на вал, вращающийся в двух подшипниках 4, имеющих возможность перемещаться по направляющим рамы 7. Подвижные подшипники прижимаются до упора пружинами 6, которые играют роль защитного устройства.
При попадании в дробилку недробимых предметов пружины сжимаются, подшипники с валком 5 отодвигаются и пропускают недробимый предмет. После этого за счет пружин валок занимает первоначальное положение. Зазор между дробящими валками регулируется прокладками, располагающимися между неподвижными и подвижными подшипниками. В зависимости от угла захвата диаметр валка дробилки должен быть в 18-20 раз больше диаметра максимального куска в питании. Дробилка закрывается кожухом. Поверхность валков футеруется марганцовистой сталью. Дробленый материал разгружается вниз под дробилку. Исходный материал загружается через верхнюю приемную воронку питателем в рабочее пространство дробилки равномерно по всей длине валков. Применяют для среднего и мелкого дробления твердых полезных ископаемых, когда недопустимо переизмельчение, а также для дробления влажных и глинистых руд. Степень дробления: 3-4.
Валковые дробилки с зубчатыми валками имеют на поверхности валков зубья или рифли, выстапающие на 40-60мм над их поверхностью. Эти дробилки применяют для крупного и среднего дробления углей, антрацитов, кокса и других хрупких и мягких полезных ископаемых. Степень дробления: 4-6. Диаметр валков дробилок должен быть в 3-6 раз больше максимального размера куска в питании.
Достоинства; простота конструкции, надежность в работе, удобство обслуживания и ремонта.
Недостатки: низкая производительность, быстрый и неравномерный износ футеровки, большой удельный расход электроэнергии.
Производительность
где:
n - частота вращения валков, мин-1;
D - диаметр валков,м;
L- длина валков,м;
S- ширина щели между валками,м;
K- коэффициент разрыхления дробленого материала в момент выхода из дробилки;
δ- плотность дробимого материала, т/м3.
Г. Дробилки ударного действия.
В дробилках ударного действия разрушение дробимого материала происходит за счет кинетической энергии движущихся тел. К ним относятся три типа дробилок: молотковые, роторные и стержневые(дезинтеграторы).
Дробилки ударного действия применяют для среднего и мелкого дробления мягких и средней крупности неабразивных материалов( углей, известняков, гипса, мела, асбестовых руд, каменной соли). Основными преимуществами этих дробилок являются простота конструкции, большая производительность, низкая металлоемкость, высокая степень дробления (до 30) и удобство обслуживания. Выпускают одно- и двухроторными с нереверсивным и реверсивным роторами. По расположению молотков: одно- и двухрядными.
Однороторная молотковая дробилка
Состоит из корпуса 1, вращающегося на валу ротора 2, с шарнирно закрепленными на нем молотками 4. Внутри корпус дробилки футеруется и имеет отбойные плиты 3.Внизу корпуса имеется полукруглая колосниковая решетка 5. Ротор собирается из двух концевых и нескольких промежуточных дисков, жестко закрепленных на валу. Через отверстия в дисках пропускают стержни, на которых свободно подвешивают дробящие молотки различной конфигурации. Исходный материал питателем через зев поступает в дробилку и разбивается ударами молотков, ударами кусков об отбойные плиты и истиранием кусков молотками на колосниковой решетке. Дробленый материал проходит через отверстия колосниковой решетки и уходит под дробилку. Крупность материала регулируется отверстиями в колосниковой решетке.
Роторные дробилки
Отличаются тем, что дробление в них осуществляется жестко закрепленными на роторе билами.
K – коэффициент учитывающий твердость материала и конструктивные особенности дробилки(0,12-0,23);
L – длина ротора,м;
d – диаметр окружности вращения молотков (бил), м;
n 2 – частота вращения ротора, мин-1.
Стержневые дробилки (дезинтеграторы)
Состоят из двух цилиндрических роторов (корзины) разного диаметра, входящих один в другой, таким образом, что концентрическая окружность одного ротора размещается внутри концентрической окружности другого ротора. Цилиндрические поверхности роторов набираются из жестко закрепленных бичей(прутьев) диаметром 30-40 мм и шагом бил примерно 200мм. Роторы вращаются в разные стороны от различных приводов. Исходный материал загружается внутрь меньшего ротора, и дробление осуществляется ударами бичей, дробленый материал просыпается между билами под дезинтегратор. Роторы закрываются кожухом.
Вопросы для самопроверки
1. Сущность процесса дробления.
2. Законы дробления (Риттенгера, Кирпичева-Кика, Ребиндера, Бонда) и их взаимная связь.
3. Способы и стадии дробления.
4. Степень дробления (частная и общая).
5. Схемы дробления.
6. Классификация машин для дробления. Эффективность дробления.
7. Классификация щековых дробилок.
8. Щековая дробилка с простым движением подвижной щеки. Щековая дробилка со сложным движением щеки. Схема. Принцип действия. Достоинства и недостатки, обозначение. Футеровка щековых дро-билок.
9. Предохранительные устройства в щековых дробилках против поломки при попадании недробимых предметов.
10. Классификация конусных дробилок. Схема устройства. Особенности конструкции рабочего пространства конусных дробилок.
11. Конусная дробилка для крупного дробления с механической регули-ровкой разгрузочной щели.
12. Конструкция конусных дробилок для среднего и мелкого дробления.
13. Классификация и область применения валковых дробилок.
14. Валковая дробилка с гладкими валками.
15. Двухвалковая дробилка с зубчатыми валками.
16. Предохранение дробилок от поломок при попадании недробимого предмета.
17. Дробилки ударного действия: молотковые, роторные дробилки, дез-интеграторы. Конструкция. Принцип действия. Классификация. Об-ласть применения. Достоинства и недостатки.
1.3 ИЗМЕЛЬЧЕНИЕ
Теоретическая подготовка
1. Назначение операций измельчения
Процесс измельчения полезных ископаемых в зависимости от требуемой крупности осуществляется в одну или нескольких стадий в открытом или закрытом циклах.
Открытым наз. процесс измельчения при котором продукт, выдаваемый мельницей, является готовым. Замкнутым наз. процесс измельчения, при котором продукт, выдаваемый мельницой, подвергается классификации с получением продукта требуемой крупности, возвращаемого на доизмельчение в туже мельницу.
2. Классификация
- крупное – 50-60% класса – 0,074мм;
- среднее - 60-85% класса - 0,074мм;
- тонкое - более 85% класса – 0,074мм.
Для крупного измельчения используют одностадиальные схемы, которые просты в регулировании и обслуживании, легко автоматизируются, требуют меньших затрат.
измельченный продукт
Двухстадиальные схемы измельчений могут быть в 1 стадии с открытым и замкнутым циклами измельчения. Такие схемы более сложны и дорогостоящи, но позволяют получать тонкоизмельченный продукт с содержанием класса -0,074мм до 85%.
Измельченный продукт пески
Применение замкнутого цикла измельчения обеспечивает наиболее эффективную работу мельниц и позволяет получать более равномерный по крупности измельченный продукт с минимальным содержание тонких частиц, по сравнению с открытых циклом. Эффективность работы мельниц существенно зависит от циркулирующей нагрузки (возвращаемая на доизмельчение масса материала). Циркулирующая нагрузка С вырается в долях единицы или процентах. Наиболее интенсивно производительность мельниц возрастает при циркулирующей нагрузке, равной 50-200%. При дальнейшем ее повышении до 500% производительность увеличивается незначительно. Оптимальный вариант 150-300%.
Циркулирующую нагрузку можно определять по данным ситового анализа продуктов измельчения и классификации. Для замкнутого цикла
β 3 ,β4, β5 –содержание расчетного класса (-0,074мм) соответственно в питании, сливе и песках.
Измельчение полезных ископаемых производят в аппаратах, называется мельницами.
3.Конструкции мельниц.
Мельницы подразделяются на механические(с мелющими телами), чашевые (бегунные) и аэродинамические. По конструкции различают мельницы: барабанные, ролико - кольцевые, чашевые и дисковые. Барабанные в сою очередь, классифицируются на мельницы с вращающимся барабаном, вибрационные и центробежные. Измельчение полезных ископаемых, как правило, производится с водой. Оно более производительно, происходит без пылеобразования и позволяет осуществлять самотечное транспортирование измельченного продукта.
А. Барабанные мельницы: цилиндрические и конические.
Короткие: длина барабана меньше или равна его диаметру.
Длинные: длина барабана в 1,5-3 раза больше его диметра.
Трубные: дина барабана больше трех его диаметров.
Барабанная мельница представляет собой цилиндрический барабан 1 с торцевыми крышками 2 и 3 и пустотелыми цапфами 4 и 5. исходный материал загружается через одну цапфу, а измельченный продукт разгружается через другую. При вращении барабана измельчающая среда
(шары, стержни, куски руды) и исходный продукт благодаря трению поднимаются на некоторую высоту, а затем сползают, скатываются или падают вниз. Измельчение происходит за счет удара падающей среды, раздавливания и трения между перекатывающимися слоями. Движение материала вдоль оси барабана происходит за счет перепада уровней загрузки и разгрузки и напора в результате непрерывной загрузки исходного материала. При мокром измельчении материал транспортируется водой, а при сухом воздушным потоком.
При увеличении частоты вращения барабана мельницы может наступить момент, когда дробящие тела начнут прижиматься центробежной силой к поверхности барабана и , не отрываясь от нее, будут вращаться вместе с барабаном. Такая частота вращения называется критической и определяется по формуле:
n кр – критическая частота вращения мельницы, мин-1;
Действительная частота вращения барабанных мельниц принимается 0,7-0,85 критической.
В зависимости от способа разгрузки различают мельницы:
- с центральной разгрузкой (стержневые и шаровые – свободный слив через цапфу, с высоким уровнем пульпы);
- разгрузкой через решетку (шаровые – прохождение через отверстия в торцевой решетке, а затем лифтом принудительно удаляется из мельницы, с низким уровнем пульпы).
Производительность барабанных мельниц определяется по содержанию вновь образованного класса крупностью – 0,074 мм
где
Q – производительность по исходной руде, т/ч;
q – удельная производительность по вновь образуемому классу, т/(м3· ч);
V- объем барабана мельницы,м3;
β к , β и – содержание расчетного класса соответственно в конечном и исходном продукте, доли единиц.
На действующих ОФ удельная производительность мельниц в первой стадии измельчения по вновь образованному классу крупностью менее 0,074 мм составляет 0,9 -1,5т/ч на 1 м3 объема барабана мельницы. Максимальная крупность материала поступающего в стержневые мельницы не должна превышать 20-25мм, а в шаровые 10-15 мм.
Б.Мельницы самоизмельчения
Используются когда в измельченном материале нежелательно присутствие железа, образующегося за счет истирания шаров и стержней.
Различают следующие виды самоизмельчения:
- рудное, когда руда крупностью 350-0мм (или 600-0) поступает в мельницы, глее крупные куски руды, измельчаясь сами, измельчают более мелкие куски;
- рудногалечное, когда мелкая руда измельчается в мельницах телами в виде рудной гали (крупностью 30-80мм), отбираемые или после II стадии дробления руды, или при рудном самоизмельчении;
- аэродинамическое, когда руда, движущаяся с повышенной скоростью (100м/с и более) в потоках газа, самоизмельчается за счет соударений частиц измельчаемого материала.
Преимущества:
-при рудном самоизмельчении можно измельчить руду крупностью 350-0, т.е. после I стадии дробления, исключив при этом среднее и мелкое дробление;
-достигается экономия в расходе на самоизмельчающие тела(стержни, шары);
-уменьшается переизмельчение руды, т.е. улучшается процесс обогащения.
Недостатки:
- повышенный расход электроэнергии;
- малая удельная производительность;
- высокий расход футеровки.
Конструкции:
Мельница мокрого самоизмельчения. (Каскад)
Состоит из цилиндрического барабана , к торцовым стенкам которого крепятся литые полые цапфы, помещенные в подшипники. Барабан изготавливают большого диаметра (9-11м) и небольшой длины(Д:L=3:1)
Футеровочные плиты барабана имеют скосы, предназначенные для крепления полок(ребер), которые предназначены для подъема крупных кусков руды на большую высоту и вследствие этого увеличения силы удара при их падении. Загрузка материал осуществляется через загрузочную воронку и спираль цапфы. Разгрузка производится через решетку и разгрузочную цапфу, к которой крепится съемная бутара для классификации пульпы. Применяют для I стадии измельчения.
Сухового самоизмельчения - мельницы «Аэрофол», сходны с мокрым самоизмельчением. Мельницы работают с воздушным классификатором. Для отсоса измельченного материала используется система , состоящая из вентилятора, циклона и аппаратов для очистки воздуха.
Вопросы для самопроверки
1. Сущность процесса измельчения и его место в процессах рудоподготовки.
2. Общие сведения о мельницах, их классификация.
3. Принцип действия и область применения.
4. Шаровые мельницы с центральной разгрузкой и разгрузкой через решетку.
5. Стержневые мельницы.
6. 57. Футеровка шаровых и стержневых мельниц.
7. Галечные мельницы.
8. Мельницы самоизмельчения и полусамоизмельчения (типа «Каскад» и «Аэрофол»).
9. Футеровка для мельниц самоизмельчения. схема устройства, принцип действия, область применения, конструкция и технические характеристики.
10. Мелющие тела (дробящая среда).
11. Коэффициент заполнения мельницы измельчающими телами.
12. Циркуляционная нагрузка.
13. Пульпа: содержание твердого в пульпе по массе, разжижение, плотность пульпы.
14. Производительность барабанных мельниц. Единицы измерения производительности мельниц.
15. Факторы, влияющие на производительность барабанных мельниц.
1.4 КЛАССИФИКАЦИЯ
1.Закономерности падения минеральных зерен в воде и воздухе.
Характер падения тел в жидкой и газообразной среде определяется взаимодействием трех сил:
- силы тяжести, направлена вниз и зависит от плотности и объема твердого тела;
- подъемной (архимедовой силой), направлена вверх и зависит от объема тела и плотности среды;
- силой сопротивления, направлена вверх и зависит от режима движения( турбулентного или ламинарного) и слагается из так называемого сопротивления сил инерции(динамического) и сопротивления сил трения (вязкостного), они действуют одновременно, но с неодинаковой силой. Преобладание динамического сопротивления наблюдается при турбулентном движении и характерно для больших размеров движущихся частиц(2мм и выше) и больших скоростях движения. Преобладание вязкостного сопротивления наблюдается при ламинарном движении (характерно для вяжущихся частиц небольшого размера 0,1 и ниже) и небольших скоростях движения, а также при высоких значениях вязкости среды. Для частиц промежуточного размера (0,1-2мм) характерен переходный режим, при котором наблюдается действие обоих видов сопротивления.
Параметр, характеризующий режим течения жидкости, называется параметром Рейнольдса (Re). При значениях Re ≥ 1000 течение жидкости турбулентное, Re ≤1000 – ламинарное и при Re =1000÷1 режим течения жидкости промежуточный.
Начальный момент движения тела в среде характеризуется нулевым значением скорости его движения и максимальным значением ускорения. По мере возрастания скорости падения тела, увеличивается сила сопротивления среды, ускорение уменьшается и за короткий промежуток времени эта сила достигает величины движущей силы. В это момент падающее тело достигает своей предельной (максимальной) скорости. Скорость становится постоянной, ускорение равно нулю. Конечная или постоянная скорость обозначается ύ0.
Разница в конечных скоростях падения различных минеральных частиц определяет процессии их разделения при классификации и гравитационном обогащении.
Установлены следующие закономерности падения минеральных частиц в среде:
- более крупные и плотные частицы имеют наиболее высокие скорости падения;
- с увеличение плотности и вязкости среды скорость падения в ней зерен снижается.
- форма и характер поверхности зерен значительно изменяют скорость их падения. При одинаковой массе частиц наименьшее сопротивление испытывают шарообразные частицы, большее- угловатые, затем продолговатые и максимальное- пластинчатые. Шероховатые частицы испытывают большие сопротивления, чем частицы с гладкой поверхностью.
- температура среды сказывается на изменение скорости падения частиц следующим образом: при Re≥ 200 изменение температуры среды не влияет на скорость движения частиц; при Re от 1,74 до 200 влияние температуры на изменение скорости движения частиц ничтожно мало и при значениях Re≤1,74 температура среды является одним из основных факторов, влияющих на их скорость.
Для определения скорости свободного ( движение отдельных, единичных частиц в неограниченном пространстве) падения ύ0 (м/с) частиц различной крупности и плотности можно пользоваться следующими уравнениями:
- для частиц крупностью 2 мм и выше (формула Риттингера):
для воды
для воздуха
- для частиц крупностью 0,1мм и ниже (формула Стокса)
для воды
для воздуха
- для частиц крупностью 0,1-2мм (формула Алена)
для воды
для воздуха
где
d- диаметр частиц,м;
δ- плотность частиц,кг/м3;
μ- коэффициент вязкости,Н·с/м2 (для воды μ=0,001, для воздуха μ=0,000018).
Можно также пользоваться универсальным методом П.В.Лященко, который приемлем для определения конечных скоростей движущихся частиц любой крупности и плотности в различной среде.
Определение конечной скорости производится исходя из параметра Лященко Re2ψ , где ψ – коэффициент сопротивления среды. Метод Лященко заключается в следующем:
А. Зная размер частицы, ее плотность, а также характеристику среды, определяем силу тяжести G0 этой частицы в среде
d- размер частицы,м;
δ – плотность частицы, кг/м3;
Δ- плотность среды,кг/м3;
g – ускорение свободного падения,с/с2.
Б. Определяем значение параметра Лященко по формуле
Зная значение параметра Re2 ψ по диаграмме Лященко Re2 ψ – Re определяем значение Re.
В. Исходя из значения Re определяем конечную скорость падания частицы по формуле
В процессе разделения частицы различной крупности и плотности может наблюдаться явление равнопадаемости. Равнопадающими называются такие минеральные зерна, которые при различных плотностях и диаметрах имеют одинаковую конечную скорость падения в одной и той же среде. Отношение диаметров зерен (соответственно d1 и d2) двух минералов различной плотности, падающих с одинаковой скоростью, называется коэффициентом равнопадаемости и обозначается буквой «е». Пренебрегая коэффициентом, учитывающим различие в форме частиц:
для крупности 2мм и более
для частиц крупностью 0,1-2мм
для частиц крупностью 0,1 мм и меньше
где
δ 1 и δ 2 – плотность соответственно тяжелого и легкого зерен, кг/м3 ;
Δ – плотность среды, кг/м3.
Коэффициент равнопадаемости показывает во сколько раз диаметр частицы легкого минерала больше диаметра частицы тяжелого минерала, имеющих одну и туже конечную скорость падения. Коэффициент равнопадаемости величина переменная и зависит от изменения размера зерен. Для того, чтобы избежать смеси различных зерен, необходимо крупность разделяемого материала иметь в пределах равнопадаемости.
В реальных условиях возникает дополнительное сопротивление, вызываемое трением частиц друг о друга и о стенки камеры. Среда разделения при этом испытывает влияние динамического воздействия как отдельных зерен, так и всей движущейся массы. Движение частиц в таких условиях наз. стесненным движением. Конечные скорости стесненного падения частиц всегда ниже скоростей их свободного падения.
Ричардсон (1908-1909г.г.) установил, что скорости стесненного падения в 2,76 раза для кварца и в 3,47 раза для свинцового блеска меньше соответствующих скоростей свободного падения. Величина обратная полученным цифрам наз. коэффициентам снижения скорости и обозначается К.
К=0,362 – кварц
К=0,288-свинцовый блеск
Исходя из этого конечную скорость стесненного падания υст (м/с) можно определить
где
υ0 – конечная скорость свободного падения частиц, м/с.
Р.Ричардсон предложил формулу для определения скорости стесненного падения
где
К- коэффициент формулы Риттингера;
d – диаметр частицы в м;
δ – плотность частицы, кг/м3;
σ - плотность гидросмеси, средняя между плотностью среды и частиц, кг/м3;
Очевидно, что скорость стесненного падения зависит от коэффициента разрыхления движущейся массы зерен. Чем больше разрыхление, тем ближе условия их движения приближаются к условиям свободного падения. На основании этого П.В.Лященко предложил следующую формулу для определения конечной скорости стесненного падения:
где
θn – коэффициент разрыхления, в долях единицы, представляет собой отношение объема промежутков между взвешенными зернами к полному объему V1 , занимаемой взвесью. Определяется по формуле
где
V 2 – объем , занимаемый твердыми частицами в объеме взвеси;
n – показатель степени, n=5÷7,5
При среднем значении n=6 формула принимает вид:
Вследствие снижения скоростей падения частиц в стесненных условиях, по сравнению со свободным падением, происходит соответственно изменение значения коэффициента равнопадаемости. В стесненных условиях значение коэффициента равнопадаемости выше, чем при свободном падении. По одной из версий стесненное падение рассматривается как падение зерен в тяжелой среде.
Коэффициент равнопадаемости ест при стесненном падении по аналогии с формулой для крупных зерен:
где
Δ + x – плотность среды ( для угольных и сланцевых частиц х =110÷300 кг/м3, для рудных – 400 кг/м3 и более).
Коэффициент равнопадаемости в стесненных условиях всегда выше, чем при свободном падении зерен. Вследствие этого разделение смеси минеральных зерен в стесненных условиях можно производить при бо'льших значениях максимальных и минимальных размеров.
2. Процесс классификации
Классификация- процесс разделения смеси минеральных зерен на классы различной крупности по скоростям их осаждения в водной или воздушной средах. Осуществляется в специальных аппаратах наз. классификаторами.
Используется два основных способа разделения частиц:
А. разделение в потоке, направление которого перпендикулярно или направлено под углом по отношению к действующим силам ( в горизонтальной или наклонной струе воды или воздуха).
Траектория движения в горизонтальных потоках воды (воздуха) зависит от V р, которая определяется сложением скорости вертикального перемещения (V в) их под действием силы тяжести и скорости горизонтального движения в направлении движения потока. Исходная пульпа подается слева, а слив удаляется справа. Глубина потока равна h , путь горизонтального потока l. Если частица во время своего горизонтального движения с потоком успевает опуститься на глубину потока, она выпадает вниз, если не успевает, то потоком выносится в слив.
Б. Разделение в потоке, направление которого совпадает (или противоположно) с направлением основных действующих на частицы сил(в вертикальной струе воды или воздуха).
Восходящий поток воды движется со скоростью V ж ,смесь разделяется на продукта, скорость которых больше или меньше скорости восходящего потока. Так как скорость падения крупных частиц выше, чем мелких, в процессе классификации в осадок будут выпадать крупные частицы, а в слив уходить мелкие.
Процессы классификации нашли широкое применение на ОФ. Верхний предел крупности материала, подвергаемого классификации, не превышает 5-6мм для руд и 13 мм – для углей.
Классификация может являться:
- самостоятельной операцией;
- подготовительной операцией;
КОНСТРУКЦИИ КЛАССИФИКАТОРОВ
1. Механические классификаторы
А. Спиральный классификатор
Представляет собой полуцилиндрическую наклонную ванну 6 прямоугольной в плане формы с гребковым механизмом 5 в виде шнека или спирали. В нижнем конце ванны имеется емкость 4 для пульпы. Исходная пульпа подается в среднюю часть классификатора. Зона I характеризуется интенсивным перемешиванием; зона II –восходящими потоками, выносящими мелкие зерна в слив; зона III – малой интенсивностью перемешивания.
В классификаторе образуется:
- слой неподвижного , осевшего , слежавшегося материала 1, предохраняющего дно 7 классификатора от износа при движении шнека;
- слой осевшего крупного материала (песков) 2, непрерывно транспортируемого вращающимся шнеком 5 к верхнему разгрузочному концу классификатора. Когда пески спиралью поднимаются выше уровня пульпы, происходит их частичное обезвоживание;
- слой пульпы, расположенный в верхней части емкости 4, в которой концентрируются мелкие зерна, транспортируемые потоком к сливному порогу 3.
Классификаторы изготавливают односпиральными и двухспиральными с погруженной и непогруженной спиралью. У классификаторов с погруженной спиралью парвый виток спирали у сливного порога целиком погружен в пульпу, а с непогруженной - вся верхняя половина первого витка спирали у сливного порога выступает над зеркалом пульпы.
Спиральные калссификаторы с непогруженной спиралью применяются для получения крупного слива, а с погруженной для получения тонкого слива. Спирали имеют диаметр до 3м и длиной корыта до 15,5м. Применяют спиральные классификаторы в основном при замкнутом цикле измельчения руд в стержневых, шаровых мельницах и мельницах самоизмельчения.
Достоинства:
- простота конструкции;
- возможность остановки и пуска классификатора без выпуска песков и осуществления самотечного замыкания мельницы с классификатором при больших размерах оборудования;
- наличием спокойной зоны классификации, обеспечивающей получение более равномерного слива.
Недостаток – получение песков со значительным содержанием шламов.
Производительность спиральных классификаторов:
По сливу для классификаторов с непогруженной спиралью
по пескам
где
m – число спиралей;
n - частота вращения спирали, мин-1 ;
KβKδKcKα – поправочные коэффициенты соответственно на крупность слива, плотность классифицируемого материала, угол наклона днища классификатора и заданную плотность слива;
D – диаметр спирали, м.
Б. Спирально-лопастной или гидросепаратор – по конструкции аналогичен сгустителю небольшого размера.
Состоит из цилиндрического чана 1 с конусным днищем 4, по которому вращаются плоские спиральные гребки 3 для транспортирования оседающего материала к центральному разгрузочному отверстию 6 и дальше по трубе 5. Разгрузка слива производится в кольцевой желоб 2. пульпа, подлежащая классификации, подается по трубе в центр чана. Применяют на ОФ при получении особо тонкого слива, а также для обесшламливания пульп. Изготавливают их диаметром 12-16 м. Спирально - лопастные классификаторы , используемые для обесшламливания магнетитовых пульп, оборудуют намагничивающими катушками для образования магнетитовых флокул( хлопьев), ускоряющих осаждение мелкого материала.
В. Классификатор элеваторный
Относится к аппаратам, в которых разделение исходного продукта на два продукта разной крупности происходит в горизонтально движущихся потоках пульпы. Классификатор представляет собой железобетонную или металлическую емкость(зумпф) 2, из которой осевший крупный материал выгружается с помощью элеватора 1 с перфорированными ковшами. Для лучшего стока воды элеватор устанавливают под углом 65-700. Высота элеватора в зоне обезвоживания должна быть не менее 4 м Площадь в плане обычно (6х6) м. Исходная пульпа подается в специальное приемное устройство, из которого равномерно распределяется по всей ширине.. Мелкие частицы уходят вместе со сливом со стороны, противоположной загрузке. Элеваторные классификаторы применяют на углеобогатительных фабриках. Их использование позволяет совмещать операции предварительного обезвоживания мелкого концентрата и его классификацию по размеру зерна 0,5 мм и исключает из технологической схемы фабрики обезвоживающие грохоты мелкого концентрата и шлама. Удельная производительность не выше 25-30 м3 /ч пульпы на 1 м2 площади классификатора и концентрации твердого в оборотной воде не более 120-150 г/л.
Г. Гидравлические классификаторы.
Наиболее распространенными являются конусные классификаторы, отстойники и многокамерные классификаторы. Общим для всех конструкций является наличие горизонтального потока пульпы. Классификаторы применяют для разделения материала по крупности на два продукта и более без дополнительной подачи воды или с добавлением ее в небольших количествах.
Автоматические конусы являются простейшими аппаратами для гидравлической классификации и представляют собой металлический корпус в виде перевернутого усеченного конуса. Применяются для отделения песков от шламов или для обезвоживания обесшламленного мелкозернистого материала.
Четырехкамерный гидравлический классификатор КГ-4 представляет собой открытый расширяющийся корпус 1, состоящий из верхней части в виде желоба, и нижней, заканчивающейся пирамидальными камерами, размеры которых увеличиваются в направлении от загрузочного конца корпуса к разгрузочному. В нижней части каждой камеры (спиготы) крепятся специальные классифицирующие устройства 5. Они состоят из верхней камеры с перемешивающим устройством 4 (лопастные мешалки) для разрыхления взвеси песков, камеры для тангенциального подвода воды (вортекса) и разгрузочного устройства. Лопастные мешалки 4, медленно (1-2мин-1) вращаясь с помощью полых вертикальных валов, осуществляют перемешивание материала в зоне его наиболее быстрого сгущения. Через полые валы проходят стержни –штоки, на нижних концах которых имеются клапаны. При помощи кулачкового механизма, расположенного в каждом редукторе 2, приводимых в движение приводом 3, осуществляется подъем и опускание штоков. При подъеме выпускные клапаны открываются и происходит разгрузка пескового материала , при опускании клапаны закрываются и выгрузка прекращается. Частота открытия клапанов в первых камерах больше, чем в последних.
Исходная пульпа подается в классификатор со стороны его узкой части, где скорость максимальна. По мере расширения классификатора скорость потока уменьшается. По этой причине в начале классификатора осаждаются наиболее крупные зерна, затем мелкие. В слив уходит самая тонкая часть материала. Вода тангенциально подается снизу, что создает устойчивость и более равномерное распределение скоростей восходящего потока.
Применяют гидравлические классификаторы для разделения материала на узкие классы перед их обогащением на концентрационных столах.
Производительность – 15-25 т/ч, крупность исходного материала не более 2мм.
Д. Центробежные классификаторы
К центробежным классификаторам относятся гидроциклоны, осадительные центрифуги, а также воздушные сепараторы (классификаторы).
Наибольшее распространение получили конические гидроциклоны.
Гидроциклон представляет собой металлический (чугунный) или сварной стальной цилиндро-конический 2,1 корпус, закрытый сверху крышкой с отверстием и трубой 3 в центре. Внутренняя поверхность футеруется износостойкими материалами , такими как резина, каменное литье, керамика, легированные чугуны, твердые сплавы. Исходная пульпа подается в гидроциклон под давлением через питающую насадку 4, установленную касательно( тангенциально) к цилиндрической части циклона. Благодаря такому подводу исходной пульпы создается ее интенсивное вращательное движение. На частицы находящиеся в пульпе, действуют силы тяжести, силы сопротивления среды, силы трения. Главной из которых является центробежная сила инерции, в несколько раз превышающая силу тяжести. Под ее действием более крупные и тяжелые частицы отбрасываются к стенкам гидроциклона, постепенно продвигаются по ним вниз и непрерывно разгружаются через песковое отверстие (насадку).
5. Слив , содержащий основную массу жидкости и уносящий с собой мелкие зерна, уходит через верхний сливной патрубок 3. Таким образом в гидроциклоне наблюдается внешний (нисходящий) поток I и внутренний вращающийся(восходящий) поток II. Разделение происходит в основном в нисходящем потоке.
Применение: в схемах измельчения руд в замкнутых циклах при использовании шаровых мельниц, а также для обесшламливания и сгущения пульпы.
Производительность по исходной пульпе:
где
Q – производительность ,м3/ч;
Kα и KD- эмпирические коэффициенты , учитывающие диаметр гидроциклона.
и угол конусности
где
D – диаметр гидроциклона;
α – угол конусности, градус; при α=200 Kα=1
dn и d – диаметры питающего и сливного отверстий, см;
p 0 – давление на входе в гидроциклон, МПа.
Е. Воздушные классификаторы(сепараторы)
Воздушные сепараторы изготовляют диаметром цилиндрической части корпуса до 4,9м. Их широко используют в циклах сухого измельчения при приготовлении пылевидного топлива, обогащения асбестовых руд, а также обеспыливания угля перед его обогащением.
Классификатор состоит из вертикальной шахты 6 с наклонными пересыпными полками 7. Исходный материал из бункера с затворами 3 поступает в шахту, куда подается движущийся навстречу материалу поток воздуха. Крупный продукт, пересыпаясь с полки на полку, проходит вниз и выгружается через затворы1, а мелкий продукт, захватываемый воздухом, выходит через патрубок 4 и улавливается затем в циклоне. Регулирование производится путем изменения расхода воздуха дроссельным клапаном 2, связанным с рукояткой 5. Дополнительное регулирование производится изменением угла наклона полок 7, которые попарно связаны тягами 8.
Вопросы для самопроверки
1. Определить характер падения тел в жидкой и газообразной средах.
2. Как определить коэффициенты равнопадаемости в водной и воздушной средах.
3. Технология процесса классификации.
4. Параметры Лященко и Рейнольдса.
5. Конструкции и принцип работы механических классификаторов.
6. Конструкции и принцип работы гидравлических классификаторов.
7. Конструкции и принцип работы центробежных классификаторов.
8. Конструкции и принцип работы воздушых классификаторов.
9. Дайте определение коэффициента сопротивления среды. В чем он выражается?
10. Какова область применения формул Риттингера, Аллена и Стокса
по определению конечной скорости падения?
11. В чем заключается метод определения конечной скорости падения (по Лященко)?
12. Как влияют форма зерен и температура среды на скорость их падения?
II. ОСНОВНЫЕ ОБОГАТИТЕЛЬНЫЕ ПРОЦЕССЫ
2.1. ГРАВИТАЦИОННЫЕ МЕТОДЫ ОБОГАЩЕНИЯ
1.Общие положения. Фракционный анализ.
Гравитационными процессами обогащения называются процессы, в которых разделение минеральных частиц, отличающихся плотностью, размером или формой, обусловлено различием в характере и скорости их движения в среде под действие силы тяжести и сил сопротивления.
В качестве среды, в которой осуществляется гравитационное обогащение, используется при мокром обогащении – вода, тяжелая суспензия или растворы; при пневматическом – воздух.
К гравитационным процессам относятся отсадка, обогащение в тяжелых средах, концентрация на столах, обогащение в шлюзах, струйных концентраторах, сепараторах, пневматическое обогащение. Гравитационные процессы обогащения могут применяться как самостоятельно, так и в различных сочетаниях с другими процессами обогащения.
Достоинства: высокая производительность, простота производственного комплекса, относительная дешевизна, высокая эффективность разделения минеральных смесей.
Фракционный анализ полезных ископаемых производится с целью определения их обогатимости, т.е. количественного и качественного определения соотношения фракций различной плотности.
Разделение на фракции различной плотности может быть произведено следующими методами:
- разделением в тяжелых жидкостях;
- разделением в тяжелых суспензиях;
- магнитогидростатической или магнитодинамической сепарации.
В качестве среды разделения применяют следующие растворы и тяжелые жидкости:
- хлористый кальций CaCl2 (плотность 2000 кг/м3);
- хлористый цинк ZnCl2 (плотность 2900 кг/м3);
- четыреххлористый углерод CCl4 (плотность 1600 кг/м3);
- бромоформ CHBr3 (плотность 2890 кг/м3);
- тетрабромэтан C2H2Br4 (плотность 2960 кг/м3);
- жидкость Туле (HgI2 + KI) –плотность 3170 кг/м3;
- жидкость Рорбаха (BaI2 + HgI2) – плотность 3500 кг/м3;
- жидкость Клеричи [CH2( COOTe)2 HCOOTe] – плотность 4250 кг/м3.
Фракционный анализ углей крупностью более 0,5 мм и руд крупностью более 0,2 мм производится в статических условиях, а более мелкого материала в лабораторных центрифугах. Перед расслоением проба обесшламливается путем промывки в воде на сите с отверстиями 0,5мм и 0,2мм. Определение фракционного состава углей производят согласно ГОСТ 1790-77.
Масса пробы угля зависит от размера максимального куска в пробе:
Размер наибольшего куска, мм | 100 | 50 | 25 | 6 | 3 | 1 | 0,5 |
Масса, кг, не менее | 100 | 50 | 25 | 6 | 3 | 1 | 1 |
Расслоение пробы производится в наборе последовательно расположенных металлических бачков 1, наполненных растворами хлористого цинка плотностью 1300;1400;1500;1600 и 1800 кг/м3 . Кроме бачков с растворами, имеются бачки для обесшламливания угля, отмывки раствора от угольных и породных фракций, аккумуляция запаса раствора. Фракционный анализ заключается в последовательном погружении в сетчатом бачке 2 пробы порциями не более 6-8кг в приготовленные растворы (от менее плотных к более плотным или наоборот) и съеме с поверхности раствора всплывающих фракций. Общее число фракций превышает на единицу число бачков с тяжелыми растворами.
Легкие (всплывшие) фракции и последнюю тяжелую(потонувшую) тщательно промывают водой, подсушивают и взвешивают.
После разделки пробы направляют на химический анализ с целью определения их влажности. Зольности, а в некоторых случаях сернистости, теплоты сгорания и т.д. Данные фракционного анализа записывают в таблицу.
Таблица 1 - Результаты фракционного анализа угля
Плотность фракций кг/м3 |
Выход | Зольность % | Суммарные легкие фракции | Суммарные тяжелые фракции | |||
кг | % | Выход % | Зольность % | Выход % | Зольность % | ||
<1300 | 60 | 54,5 | 6 | 54,5 | 6 | 100 | 23,1 |
1300-1400 | 15 | 13,6 | 9 | 68,1 | 6,6 | 45,5 | 43,4 |
1400-1500 | 6 | 5,5 | 12 | 73,6 | 7 | 31,9 | 58,3 |
1500-1600 | 3 | 2,7 | 25 | 76,3 | 7,6 | 26,4 | 67,9 |
1600-1800 | 2 | 1,8 | 46 | 78,1 | 8,5 | 23,7 | 72,8 |
>1800 | 24 | 21,9 | 75 | 100 | 23,1 | 21,9 | 75 |
итого | 100 | 100 |
Выход фракций определяют делением частного значения на суммарную сумму всех фракций и умножением результата на 100 %. Суммарный выход легких фракций вычисляется путем суммирования частных выходов сверху вниз. Суммарный выход тяжелых фракций вычисляется суммированием частных выходов снизу вверх. Средневзвешанная зольность легких фракций подсчитывается путем деления суммы произведений выходов и зольности на суммарный выход легких фракций.
Например
Средневзвешанная зольность двух легких фракций будет:
Аd1+2 = (54,5·6 + 13,6·9)/ (54,5+13,6)=6,6%
Средневзвешанная зольность двух тяжелых фракций будет:
Аd6+5= (21,9·75+1,8·46)/ (1,8+21,9)=72,8%
По результатам фракционного анализа строят кривые обогатимости. Кривые обогатимости строят в прямоугольной системе координат на миллиметровой бумаге.
где
δ – кривая плотностей , показывает зависимость суммарного выхода легких фракций от плотности разделения;
θ –кривая средних золностей отходов, показывает зависимость между суммарным выходом тяжелых фракций и их зольностью;
λ – кривая элементарных зольностей, показывает зависимость между выходом и зольностью элементарных слоев;
β – кривая средних зольностей концентрата, показывает зависимость между суммарным выходом легких фракций и их зольностью.
Для построения кривой λ используют следующий метод:
для каждой фракции на графике строят прямоугольник, нижняя горизонтальная сторона которого представляет значение зольности данной фракции, а правая вертикальная сторона- выход данной фракции. Число таких прямоугольников должно быть равным числу фракций, и располагаться они должны последовательно один за другим сверху вниз. Каждую правую сторону прямоугольников делят пополам и через точки, соответствующие серединам прямоугольников, проводят плавную кривую.
При проведении кривой «срезают» и «наращивают» треугольные части прямоугольников. Необходимо, чтобы при этом площади наращиваемых и срезаемых треугольников были равновеликими.
Начальные точки кривых λ и β и конечные точки кривых λ и θ должны совпадать. Они отражают зольность в верхнем и нижнем элементарных слоях фракций, соответствующие минимальной и максимальной зольности самого «чистого» угля и самой зольной породы.
Чем более пологий вид имеет кривая λ , тем легче обогатимость угля.
Так как при гравитационных процессах обогащения разделение происходит преимущественно по различию в плотностях отдельных компонентов, технологические результаты обогащения характеризуются взаимозасорением продуктов обогащения «посторонними фракциями», т.е. фракциями, плотность которых для легкого продукта выше плотности разделения, а для тяжелых- ниже. Чем меньше взаимозасорение, тем качественнее продукты обогащения, тем выше извлечение и ниже потери полезных компонентов.
2. ОТСАДКА
Отсадка является одним из наиболее распространенных методов гравитационного обогащения полезных ископаемых. Область применения отсадки охватывает полезные ископаемые по плотности извлекаемых компонентов от 1200 до 15600 кг/м3 и по крупности обогащаемого материала
От 0,2 до 50 мм для руд и 0,5 до 120 мм –для углей.
Отсадкой называют процесс разделения смеси минеральных зерен по плотности в водной или воздушной среде, пульсирующей относительно разделяемой смеси в вертикальном направлении. Исходный материал вместе с водой непрерывно подается на отсадочное решето, через отверстия которого попеременно проходят восходящие и нисходящие вертикальные потоки воды. В период восходящего потока материал поднимается и разрыхляется, а в период нисходящего- опускается и уплотняется. В результате действия чередующихся восходящих и нисходящих потоков воды исходный материал через определенный промежуток времени разделяется на слои таким образом, что на отсадочном решете( внизу) располагаются зерна наибольшей плотности, а в верхних слоях- наименьшей. Такое идеальное распределение возможно только в том случае, если они обладают одинаковыми размерами и формой. В реальных условиях происходит «взаимозасоряемость» классов.
Слой материала, находящийся на решете называют постелью. Постель образуется при отсадке крупного материла, состоит из зерен самого материала и называется естественной. Через принудительно пульсирующую толщу материала тяжелые зерна проникают в нижние слои постели, а легкие в верхние. При обогащении мелкого материала ( для руд <3-5мм; для углей <6-10мм) на решето укладывается в специально сделанные гнезда искусственная постель. Она состоит из тяжелых естественных и искусственных минералов (полевой шпат, резиновые шарики, свинцовая дробь, галенит и т.п.), крупность которых приблизительно в два раза больше отверстий решета, а плотность близка к плотности тяжелых фракций обогащаемой минеральной смеси. В этом случае искусственная постель является как бы фильтрующим слоем, пропускающим зерна тяжелого минерала и задерживающим зерна легкого. В конце машины имеется сливной порог, установленный на несколько сантиметров выше отсадочного решета, через который удаляются легкие фракции.
1. Разделение зерен в отсадочной машине
В процессе отсадки на решете 2, расположенном в корпусе 1 отсадочной машины, образуется толща разделяемого материала, продвигающаяся вместе с водой к разгрузочному концу( слева направо). В конце машины материал обычно бывает полностью расслоен на легкие и тяжелые фракции. Легкие фракции потоком воды выносятся через сливной порог 3, а тяжелые фракции при работе машин на крупном материале сползают в щелевое отверстие между решетом и сливным порогом и разгружаются с помощью секторных, роторных и других устройств. При отсадке мелкого материла тяжелая фракция проходит через слой искусственной постели и удаляется под решето. Размер отверстий решета должен быть больше максимального размера зерен обогащаемого материала. Легкие фракции удаляются через сливной порог 3.
Уровень тяжелых фракций на решете отсадочной машины регулируется специальным поплавковым устройством. При увеличении или уменьшении толщины слоя тяжелого материала автоматически увеличивается или уменьшается интенсивность разгрузки тяжелых фракций.
Кроме воды в машину вместе с исходным материалом (наз транспортной), под решето подается подрешетная вода. Она предназначена для поддержания оптимальной разрыхленности постели и уменьшения вредного действия нисходящих струй воды. Из общего расхода воды(2-5м3/т исходного материала) на долю транспортной приходится 30-40%, а на долю подрешетной 70-60%.
2.Конструкции отсадочных машин
Представляет собой устройство для гравитационного обогащения, в котором исходный материал разделяется на отсадочном решете под влиянием вертикальных колебаний жидкости.
Все отсадочные машины состоят из металлического корпуса 1 прямоугольной формы (в плане) в котором располагается отсадочное решето 2. Подрешетная часть корпуса (нижняя его часть) имеет пирамидальную, полуцилиндрическую или параболическую форму. В поршневых, беспоршневых и диафрагмовых машинах решето установлено неподвижно. Продольная вертикальная не доходящая до дна перегородка делит поршневые и беспоршневые машины на два отделения: первое –рабочее, на решете 2 которого происходит разделение минеральных зерен, и второепоршневое (или воздушное). Колебания воды в поршневой машине вызывается перемещением вверх и вниз поршня 4, связанного штоком с эксцентриковым приводом. В беспоршневой воздушно-золотниковой машине колебания воды происходят за счет использования энергии сжатого воздуха, поступающего через пульсатор 5. Так же пульсатором происходит
периодический выпуск воздуха. При впуске воздуха уровень воды в отсадочном отделении повышается(восходящий поток), при выпуске воздуха в атмосферу –понижается (нисходящий поток). Машина работает при давлении 15-40 КПа.
В диафрагмовых отсадочных машинах вертикальные пульсации воды создаются за счет движения расположенной между смежными секциями эластичной диафрагмы 6, связанной штоком 7 с эксцентриковым приводом. В отсадочной машине с подвижным решетом пульсация воды создается за счет вертикальных движений самого решета 2 с находящимся на нем разделяемым материалом.
Каждый тип машин предназначен для обогащения определенных полезных ископаемых. Поршневые отсадочные машины (ОМ) применяют для обогащения марганцевых, оловянных и вольфрамовых руд. Диафрагмовые отсадочные машины (МОД-1,2,3,6) применяют для обогащения руд: железных ,марганцевых, оловянных, вольфрамовых, золотосодержащих россыпей, руд редких металлов). Беспоршневые отсадочные машины( ОМК,ОМШ,МОБ,ОМР) применяют для обогащения углей и руд черных металлов. Отсадочные машины с подвижным решетом (МОП) применяют для обогащения марганцевых и реже железных и вольфрамовых руд.
Производительность может быть определена исходя из удельной производительности на 1м2 площади отсадочного отделения или по эмпирической формуле
где
Q – производительность, т/ч;
H - высота слоя материала в камере машины, расположенного выше сливного порога в период взвешанного состояния материала, м;
B - ширина машины, м;
υ - продольная скорость движения зерен материала в отсадочной камере,м/с;
δ - плотность исходного материала, кг/м3;
θ - степень разрыхления материала в период его взвешанного состояния, доли ед.
Вопросы для самопроверки
1. В чем заключается скоростная, тяжелосредная, статистическая и энерге-тическая гипотезы отсадки?
2. По каким признакам производится классификация отсадочных машин?
3. Каково устройство поршневых отсадочных машин и машин с подвижным решетом?
4. Каково устройство диафрагмовых отсадочных машин и какие факторы влияют на эффективность их работы?
5. Каков принцип действия беспоршневых отсадочных машин и по каким признакам они классифицируются?
6. Какова конструкция пульсаторов?
7. Каковы различия в циклах отсадки?
3. ОБОГАЩЕНИЕ В ТЯЖЕЛЫХ СРЕДАХ
1. Основные положения
Процесс обогащения в тяжелых средах основан на разделении смеси зерен по плотности в гравитационном или центробежном полях в среде, плотность которой- промежуточная между плотностями разделяемых частиц. Минералы меньшей плотности , чем среда всплывают, а более тяжелые- тонут. Чаще всего применяют тяжелые суспензии, в качестве утяжелителей суспензии применяют естественные сыпучие тонкоизмельченные вещества- кварцевый песок, лесс, глина; тяжелые минералы- пирит, барий, магнетит, галенит; ферросплавы. Наибольшее распространение получили следующие утяжелители:
кварцевый песок- 2650 кг/м3
магнетит - 5000кг/м3
ферросилиций -6400-7000кг/м3
галенит -7500 кг/м3.
Основными свойствами тяжелых суспензий являются их плотность, вязкость и устойчивость. Плотность является основным технологическим свойством, характеризующим граничную плотность разделения. Характеризуется она отношением массы суспензии к ее объему. Плотность суспензии увеличивается с увеличением объемной концентрации и плотности утяжелителя.
Δс - плотность суспензии , кг/м3
где
С - объемная концентрация утяжелителя, доли ед.;
δ – плотность утяжелителя, кг/м3.
Пример:
1.Определить плотность суспензии при плотности утяжелителя(магнетита)
δ = 5000кг/м3 и объемной концентрации утяжелителя с=25%(0,25).
Δс =0,25(5000-1000) +1000 =2000кг/м3
2.Определить необходимую плотность утяжелителя для приготовления теля(магнетита) δ = 5000кг/м3 и объемной концентрации утяжелителя С=0,1
Δс = С(δ – 1000) +1000,
Δс=1400кг/м3
δ = 1000+( Δс -1000)/С = 1000+(1400-1000)/0,1= 5000кг/м3
Устойчивость суспензии является одним из важнейших свойств, влияющих на точность разделения минеральных зерен в процессе обогащения. Под устойчивостью суспензии понимается ее способность сохранять постоянную плотность во времени в различных по высоте слоях. Устойчивость суспензии определяется скоростью осаждения твердой фазы и зависит от крупности частиц утяжелителя, их плотности, объемного содержания утяжелителя, ее температуры. Повышение устойчивости суспензии достигается подбором утяжелителей определенного состава, созданием восходящих или горизонтальных потоков суспензии, механическим перемешиванием, добавлением веществ-стабилизаторов, которые препятствуют осаждению частиц утяжелителя.
Вязкость суспензии или внутреннее трение характеризует сопротивление относительному движению ее элементарных слоев. Существенное влияние на вязкость оказывает крупность частиц утяжелителя(гранулометрический состав) и объемная его концентрация в суспензии. Чем крупнее частицы утяжелителя , тем меньше вязкость суспензии и выше ее подвижность при одной и той же плотности, однако при этом ухудшается устойчивость суспензии( наблюдается быстрое осаждение частиц утяжелителя). Чем меньше крупность частиц утяжелителя, тем выше устойчивость суспензии, но тем выше ее вязкость и ниже текучесть. Поэтому крупность частиц подбирается с учетом всех показателей. Максимальная крупность частиц утяжелителя редко превышает 0,5мм и в большинстве случаев составляет 0,15-0,05мм. Объемное содержание утяжелителя не должно превышать 30%.
Приготовление суспензии: дробление, измельчение, классификация утяжелителя, смешивание в специальном смесителе с водой в заданной пропорции.
Суспензия в процессе работы засоряется мелкими частицами обогащаемого материала. Для восстановления суспензии ее подвергают регенерации.
Регенерация - восстановление первоначальных свойств суспензии с последующим возвращением в технологический процесс.
Применение обогащения в тяжелых средах:
- для удаления пустой породы перед тонким измельчением руд;
- удаление пустой породы из энергетических углей;
- обогащение труднообогатимых углей для целей коксования.
Достоинства:
- высокая эффективность процесса;
- простота конструкций машин;
- высокая производительность;
- нечувствительность процесса к изменениям производительности и качества материала.
Недостатки: дороговизна.
2. Тяжелосредные сепараторы.
Служат для обогащения средне- и крупнокускового материла.
А. Конусные сепараторы.
Представляют собой металлическую емкость (ванну) 1, в верхней части цилиндрической, а в нижней- конической формы, заполненной тяжелой суспензией.
Конусный сепаратор с аэролифтной разгрузкой тяжелой фракции имеет эролифтный подъемник 2. Руда подается в ванну сепаратора сверху. Разгрузка легкой (всплывшей) фракции осуществляется самотеком в желоб 3. тяжелая(потонувшая) фракция опускается вниз, попадает в загрузочную часть аэролифта и поднимается по трубе вверх к месту разгрузки, расположенному выше уровня суспензии. Суспензия подается в сепаратор или с исходной рудой или отдельно по трубам. Эти сепараторы предназначены для обогащения руд и неметаллических полезных ископаемых крупностью от 100 до мм. Производительность их по исходной руде составляет до 35т/ч на 1м2 площади зеркала суспензии в сепараторе.
Б. Конусный сепаратор ОК(обогатительный конус) имеет размещенную в центре ванны 1 мешалку 4, вращение которой препятствует расслоению водно-песчаной суспензии. Легкая фракция круговым движением суспензии увлекается к разгрузочному желобу 3, расположенному тангенциально. Тяжелая фракция попадает в разгрузочную камеру 6, снабженную шиберными задвижками 5 и 7. Во время наполнения тяжелого продукта в разгрузочной камере 6 верхняя шиберная задвижка 5 открыта, а нижняя 7 –закрыта. После наполнения разгрузочной камеры тяжелым продуктом, верхняя задвижка перекрывается и одновременно открывается нижняя задвижка. После освобождения камеры цикл повторяется. Суспензия подается сверху и сбоку.
Диаметр камер от 2200 до 5600мм, и предназначены для обогащения углей крупностью от 200(100) до 13(6) мм. Производительность по исходному углю составляет 10-16 т/ч на 1 м2 площади зеркала суспензии в сепараторе.
В. Сепаратор барабанный со спиральной разгрузкой(СБС)
Применяют для обогащения руд цветных и черных металлов и неметаллических полезных ископаемых крупностью от 150 до 4мм.
Производительность по исходному сырью- до 14т/ч на 1 м2 площади зеркала суспензии. Размеры: диаметр от 1800 до 3000мм и длиной от 3600 до 6000мм.
Г. Колесный сепаратор(СКВ) .
В - вертикальное колесо.
Сепаратор двухпродуктовый.
Для обогащения угля крупностью от 300 до 13(6) мм . Производительность их по исходному углю составляет 95-120 т/ч на 1м ширины ванн сепаратора.
Д. Сепаратор СТТ –трехпродуктовый.
Вопросы для самопроверки
1. Как готовят тяжелые среды – жидкости и суспензии? На чем основано разделение полезных ископаемых в тяжелых средах?
2. От чего зависит плотность тяжелых суспензий и как она устанавливается?
3. Каково значение вязкости и устойчивости суспензий?
4. По каким признакам классифицируются суспензионные сепа-
раторы?
5. Как устроены конусные, колесные и барабанные суспензионные сепараторы? Какова область их применения?
6. Каковы методы и схемы регенерации минеральных суспензии?
4. Гидроциклоны.
Тяжелосредные гидроциклоны бывают двухпродуктовыми (КГ) и трехпродуктовыми(ГТ).
А. Двухпродуктовый гидроциклон
Представляет собой разновидность обычных гидроциклонов. Суспензия подается в цилиндрическую часть гидроциклона 2 совместно с обогащаемым материалом через загрузочный патрубок. Тангенциальный ввод исходного материала под давлением приводит к возникновению центробежных сил, которые перемещают тяжелый продукт к стенкам конической части корпуса 4, по которым он скользит и удаляется с частью суспензии через песковую насадку 1. Легкий продукт с основной частью суспензии удаляется через сливную трубу 3. Гидроциклон чаще всего устанавливают под углом примерно 200 к горизонту.
Б. Трехпродуктовый тяжелосредный гидроциклон.
Состоит из двух секций, содиненных в один агрегат. В первой цилиндрической секции 5, в которую исходный материал подается вместе с суспензией подается тангенциально через патрубок 6, происходит одновременно разделение материала по плотности на две фракции и уплотнение(сгущение) части суспензии, которая проходит во вторую цилиндроконическую секцию 4 со смесью промежуточной и тяжелой фракцией.
Из цилиндрической секции выделяется через сливную трубу 7 легкая фракция. Тангенциальный разгрузочный патрубок 1 цилиндрической секции является соединительным звеном 2 и служит входным патрубком 3 для цилиндроконической секции. В цилиндрической секции, конструкция которой полностью аналогична двухпродуктовому гидроциклону, через трубу 8 выделяется промпродуктовая, а через песковый насадок 10 тяжелая фракция. Вся конструкция крепится на раме 9.
Преимущество центробежных гидроциклонов заключается в наличии центробежного поля, в десятки раз увеличивающего скорость разделения материала по плотности. Кроме того, турбулентный вращающийся поток разрушает структуру суспензии, вследствие чего уменьшается ее вязкость, что позволяет эффективно обогащать материал крупностью до 0,2мм.
Такие циклоны применяют для обогащения углей крупностью от 25(40) до 0,5(0,2)мм. Производительность тяжелосредных гидроциклонов диаметром 500мм по исходному питанию составляют: для двухпродуктовых 50т/ч; трехпродуктовых-65-80т/ч.
Вопросы для самопроверки
1. Принцип работы годроциклонов.
2. Достоинства и недостатки двухпродуктовых гидроциклонов.
3. Достоинства и недостатки треъпродуктовых гидроциклонов.
4. Преимущества центробежных гидроциклонов.
4. ОБОГАЩЕНИЕ В ПОТОКЕ ВОДЫ, ТЕКУЩЕЙ ПО НАКЛОННОЙ
ПЛОСКОСТИ
1.Общие сведения.
Этот метод обогащения осуществляется в наклонных водных потоках малой глубины(толщины). Исходный материал вместе с водой движется по наклонной плоскости, и минеральная частица, находящаяся в потоке воды, имеющей скорость υ испытывает действие следующих сил:
- силы тяжести G0 , направленной вертикально вниз;
- силы динамического воздействия потока воды Рд , направленной в сторону его движения;
- силы от воздействия вертикальной составляющей скорости потока Рв направленной вверх;
- силы трения Рт , направленной в сторону, противоположную движению зерна.
Разделение минеральных частиц по плотности и крупности происходит за счет различия в характере их движения. При малых скоростях потока зерна оседают на дне, при больших – взвешиваются в потоке. Для гравитационного расслоения зерен по плотности в текущем потоке воды создается такой режим движения, который исключает перенос во взвешенное состояние тяжелых зерен. Поэтому в верхних слоях потока находятся наиболее легкие частицы, а тяжелые медленно скользят по дну. Выносу легких частиц в верхние слои потока способствуют образующиеся во время движения пульпы придонные вихри.
Скорость движения отдельных слоев жидкости по глубине потока неодинакова: она максимальная на поверхности потока и минимальная у его дна. Поэтому легкие зерна минералов, находящиеся в верхних слоях потока, сносятся потоком быстрее и легче, чем зерна тяжелых минералов.
Такой принцип используется в шлюзах, моечных и струнных желобах, струнных концентраторах, винтовых и конусных сепараторах, концентрационных столах.
2. Шлюзы, моечные желоба, струнные концентраторы.
Шлюзы бывают неподвижными и подвижными. Неподвижный шлюз представляет собой слабонаклонный прямоугольный желоб, длина которого значительно больше ширины. На дно шлюза укладывается специальное покрытие( шероховатый покров и трафареты) для создания шероховатости и удержания осевших на дно тяжелых зерен. Пульпа( при Ж:Т не менее 5:1) подается в верхнюю часть шлюза. В потоке воды , стекающем по шлюзу, происходит разделение частиц. Тяжелые зерна оседают на дно, а более легкие катятся по дну или движутся с потоком воды во взвешенном состоянии. На дне шлюза образуется движущаяся постель, в которой происходит расслаивание материала по плотности. Тяжелые частицы концентрируются и накапливаются в гнездах трафаретов, осадок уплотняется, а легкие смываются потоком воды и уносятся вместе с водой из шлюза.
Трафареты представляют собой уложенные на дне шлюза поперечные брусья или панцирные сетки с крупными отверстиями или полочки лестничного типа, наклоненные по ходу потока. Исходный материал на шлюз подают до тех пор, пока не заполнятся ячейки трафаретов. После этого загрузку прекращают, производят удаление осевшего тяжелого материала путем сполоска, и шлюз вновь включают в работу. Поэтому шлюзы относят к аппаратом периодического действия. Операция сполоска осуществляется вручную или с помощью водяных эжекторных насосов, которые засасывают тяжелую фракцию из трафаретов и транспортируют на дальнейшую обработку.
Применение: для обогащения руд с низким содержанием тяжелых минералов, а именно оловянных, вольфрамовых, золото- и платиносодержащих руд.
Для эффективного обогащения на шлюзах разность плотностей полезных минералов и пустой породы должна быть значительной.
Основное условие обогащения:
Полное предварительное отделение (раскрытие) полезных зерен из сростков с породой(для руд) и из глинистых агломератов (для песков). Для этой цели перед обогащением на шлюзах устанавливают дезинтегрирующие аппараты. Обычно в результате обогащения на шлюзах получается черновой концентрат, требующий последующего дообогащения.
Для обогащения крупнозернистого материала крупностью -100+13мм применяют шлюзы глубокого наполнения со скоростью потока до 3м/с. Для обогащения мелкозернистого материла крупностью -13+0мм применяют шлюзы малого наполнения, называемые подшлюзками, со скоростью потока 1-1,5м/с.
Аппарат | шлюз | подшлюзок |
Длина,м | 20-30 | 6-10 |
Ширина,м | 0,7-1 | 0,7-1 |
Угол наклона, градус | 3-5 | 2-3 |
Высота трафаретов,мм | 50 | 25-30 |
Расстояние между планками трафаретов,мм | 90-150 | 25-30 |
Высоа стенок шлюза,мм | 750-800 | 450-500 |
Глубина наполнения шлюза,мм | 80 | 50 |
Интервал между съемом(сполоском) тяжелого материала (шлихов) на шлюзах с неподвижной рабочей поверхностью изменяется в пределах от (4-8ч) до 10-15суток в зависимости от характера обогащаемого материала, его крупности и содержания тяжелой фракции.
Кроме неподвижных шлюзов, имеются подвижные механизированные шлюзы ШМС( шлюз металлический секционный) и НРП (шлюз подвижный с резиновым покрытием). Основной особенностью этих шлюзов является возможность сполоска тяжелой фракции без снятия улавливающего покрытия. Сполоск производят автоматическим поворачиванием шлюза и смыва тяжелой фракции сильной струей воды.
Моечный желоб – сходен по конструкции со шлюзами и представляет собой неподвижный, слабонаклонный, прямоугольный металлический желоб с гладким дном. Тяжелая фракция оседает на дно и движутся по нему, а легкие перемещаются верхними слоями потока. Тяжелая фракция через специальные разгрузочные камеры непрерывно удаляется.
Струйный концентратор (желоб) представляет собой неподвижный короткий наклонный суживающийся желоб 1 с гладким днищем.
Узкой частью желоб устанавливается вниз. Исходная пульпа подается с малой начальной скоростью на верхнюю широкую часть аппарата. Во время стекания происходит постепенное сужение потока, что приводит к увеличение его глубины и изменению характера движения от ламинарного в начале желоба к турбулентному в его конце. Происходит перегруппировка частиц и на выходе из желоба в нижнем придонном слое располагаются зерна большей плотности, а в верхних слоях меньшей. Так как тяжелые частицы движутся с меньшей скоростью, чем легкие, на выходе из желоба образуется веер минералов различной плотности, разделяемых с помощью перегородок - отсекателей 2.
Применяются эти аппараты при обогащении песков россыпных месторождений.
Преимущества: высокая производительность, низкие капитальные затраты.
Но на них получают черновые концентраты, требующие дальнейшего обогащения.
3. Концентрационные столы
КС бывают подвижными и неподвижными. Неподвижные концентрационные столы (вашгерды, автоматические шлюзы) используются в основном для обогащения золотосодержащих песков и тонкоизмельченных руд редких металлов и минералов. Недостаток: малая производительность и неэффективное извлечение зерен тяжелых минералов.
Подвижные концентрационные столы имеют несколько разновидностей: ленточные, круглые и качающиеся. Наиболее широкое применение имеют качающиеся концентрационные столы(сотрясательные). Обогащение на подвижных КС является процессом разделения полезных ископаемых по плотности в тонком слое воды, текущем по слабонаклонной плоской поверхности стола( дека), совершающей ассиметричные возвратно-поступательные движения в горизонтальной плоскости перпендикулярно к направлению движения потока воды.
Качающийся(сотрясательный) концентрационный стол СКМ-1
состоит из деревянной деки 2 трапецеидальной формы, опирающейся на шесть роликов 7 опор скольжения 6, установленных на рычагах, закрепленных в кронштейнах рамы. Поверхность деки стола покрыта линолеумом, на котором крепятся деревянные планки- рифли 1, расположенные параллельно движению стола. Применяют также деки из алюминиевых сплавов. В продольном направлении рифли скашивают по высоте и у разгрузочного конца они имеет минимальную высоту. В поперечном сечении рифли имеют прямоугольную форму. Скашивание рифлей способствует расхождению продуктов веером по поверхности деки. Длина рифлей также переменная: у загрузочного устройства вверху она самая короткая, самая длинная – в нижней части деки. Высота рифлей меньше в верхней части деки и наибольшая в нижней. Нижняя рифля в два раза больше самой верхней. Для регулирования поперечного наклона деки имеется креновый механизм, при вращении маховика 8 которого дека за счет винта 9 поворачивается на одинаковый угол. Поперечный угол наклона деки зависит от крупности и плотности обогащаемого полезного ископаемого и составляет 2-30 для мелкого и 5-90 для крупного материала.
Дека стола совершает возвратно-поступательные движения за счет приводного механизма, с которым она соединяется тягой. Приводной механизм состоит из эксцентрикового вала с роликом и коленчатого рычага или коромысла .При вращении эксцентрикового вала ролик нажимает на горизонтальное плечо коромысла, вследствие чего вертикальное плечо движется вправо, и будучи связанным с декой стола через тягу , заставляет ее двигаться назад. В это время пружина, которая находится под декой сжимается. В это период дека имеет минимальную скорость в начале движения и максимальную в его конце. При дальнейшем вращении эксц. вала вертикальное плечо коромысла отклоняется влево, а пружина, разжимаясь, толкает деку вперед. В этот период дека стола имеет максимальную скорость в начале хода и минимальную в конце хода. Ход деки можно изменять с помощью винта , частоту качаний стола- сменой шкивов на валу электродвигателя. Такое движение деки, когда она как бы выдергивается в горизонтальном направлении из-под материала, находящегося на его поверхности, за счет чего материал продвигается вперед деки.
Процесс разделения на КС происходит следующим образом:
Исходный материал в виде пульпы подается на деку стола по лотку 5. Вода подается в водяной желоб 4 и через регулируемые отверстия 3 распределяется по всей длине деки. В межрифельном пространстве стола за счет рифлей образуются желобки, в которых минеральные частицы, под действием комплекса механических и гидродинамических сил, разделяются по плотности и крупности. В самом нижнем слое наиболее мелкие зерна тяжелого минерала, над ними более крупные зерна той же плотности в смеси с мелкими зернами меньшей плотности. Легкие зерна распределяются в верхних слоях в той же последовательности. Во время пребывания на деке происходит его разрыхление. При возвратно-поступательном движении деки частицы перемещаются вдоль оси стола(желобков) и одновременно подвергаются смывному действию воды, текущей поперек стола.
Смывное действие воды оказывается более сильным в верхних слоях материала, и частицы меньшей плотности будут сноситься водой со скоростью u2 , которая больше скорости u1 частиц большей плотности. В нижних слоях материала под действием сотрясательных движений деки, направленных перпендикулярно ее наклону , перемещение тяжелых зерен совершается со скоростью υ1 , которая больше, чем скорость υ2 перемещения вышележащих легких зерен. Равнодействующие скоростей ω1 и ω2 частиц различной плотности направлены под разными углами к направлению движения стола, что и определяет различные траектории их движения по поверхности деки стола. Частицы большей плотности 1, находящиеся вблизи поверхности деки, интенсивно перемешиваются в продольном направлении; частицы меньшей плотности 2, расположенные в верхних частях слоя, интенсивнее сносятся потоками смывной воды в поперечном направлении. При движении материала вдоль межрифельных каналов происходит уменьшение толщины слоя и легкие частицы последовательно смываются вниз. В результате материал на деке стола образует так называемый веер из частиц различной плотности и размера.
Достоинства: обеспечение высокого извлечения тяжелых минералов и высокую степень концентрации.
Применение: для обогащения оловянных и вольфрамовых руд, руд редких и благородных металлов крупностью от 3-0,04мм, и углей крупностью менее 13 мм.
Недостатки: при обогащении неклассифицированного материала ухудшаются качественные показатели и снижается производительность столов.
Содержание твердого в питании составляет 15-40%, расход смывной воды 1-2м3/т.
Современные КС - СКО (стол концентрационный опорный двухъярусный с дебалансным приводом) и СК-22 (опорно-подвесной трехдечный).
Производительность
где
q- удельная производительность, т/(ч·м2);
F- площадь деки ,м2.
dmax – максимальный размер зерен обогащаемого материала, мм.
Вопросы для самопроверки
1. Какие силы действуют на минеральное зерно в потоке, текущем по наклонной плоскости?
2. Как найти скорость движения частиц в таком потоке?
3. По каким признакам производится классификация машин и аппаратов для обогащения в потоке воды, текущем по наклонной плоскости?
4. Каковы конструкции и принцип действия неподвижных и ленточных столов?
5. Каковы устройства и принцип действия однодечных и многодечных сотрясательных столов?
5.ПРОТИВОТОЧНАЯ СЕПАРАЦИЯ
Противоточные сепараторы представляют собой аппараты, в которых гравитационное разделение материала происходит под действием системы силовых полей, направленных под углом друг к другу. Различают шнековые сепараторы СШ и СВШ и крутонаклонные сепараторы КНС.
Применение:
для обогащения энергетических углей, антрацитов и механизированного удаления породы из угля крупностью от 6 до 100(150) мм.
1. Во всех противоточных сепараторах исходный уголь делится на два продукта: концентрат (легкая фракция) и отходы (тяжелая фракция).
Исходный уголь подается в центральную часть цилинд-рического корпуса, снаб-женного шнеком .
Вода поступает в сепаратор навстречу движения шнека и транспортирует легкие фракции к месту их выгрузки. Движение тяжелых частиц навстречу потоку осуществляется шнеком.
Исходный уголь подается сверху в центральную часть цилиндрического корпуса через полый вал. Транспортирование легких фракций осуществляется спиральным восходящим потоком воды в пространстве между шнеком и корпусом сепаратора, а тяжелых- по наклонной спирали шнека вниз.
Крутонаклонный сепаратор
Тяжелая фракция
Исходный уголь подается в центральную часть прямоугольного корпуса, наклоненного к горизонту под углом 46-540. Внутри корпуса находится специальная дека, снабженная зигзагообразными перегородками, которые создают на деке переменное поле скоростей потока по длине и ширине канала, позволяющее раздельно регулировать режимы обогащения в концентратном и породном отделениях. В нижнюю часть сепаратора подается с заданной скоростью вода. Тяжелые фракции выпадают в придонный слой, движущийся навстречу потоку воды и преодолевающий его. Легкие фракции выносятся потоком воды вверх через сливной порого сепаратора. Таким образом по всей длине рабочей зоны сепаратора осуществляется разделительный процесс противоточного типа.
Достоинства: простота конструкции, надежность в работе, имеют малый абразивный износ.
2. Промывка и протирка
Процесс разделения материала с помощью разрыхления и удаление зернистой части с помощью механизмов, а глины с помощью воды наз.промывкой. В результате получают мытый материал и глинистую суспензию(шламы). Промывке подвергаются россыпи цветных, редких и благородных металлов, неметаллическое сырье, кварцевые пески, фосфориты, флюсовые известняки и другие полезные ископаемые с высоким содержанием глины. Промывка может быть самостоятельным процессом или подготовительным.
Для промывки легкопромывистых руд крупностью до 150-200мм применяют промывочные грохоты. Для промывки средне- и легкопромывистых руд крупностью до 200мм применяют бутары, скрубберы, скруббер-бутары; труднопромывистых руд крупностью до 75-100мм –корытные мойки, бичевые промывочные машины; крупностью до 25мм – промывочные башни.
Скруббер-бутара СБ-1,3
Представляет собой комбинацию жестко соединенных между собой скруббера 1(барабан снабженный внутри дезинтегрирующими и перемешивающими устройствами 2) и конической (или цилиндрической) перфорированной бутары (барабанный грохот) 3. Скруббер-бутару устанавливают наклонно (до70) или горизонтально на приводных 4 и опорных 7 роликах, вращение которых осуществляется от электродвигателя6 через редуктор 7. Исходный материал подается в загрузочное отверстие в торцовой крышке барабана скруббера. Вследствие вращения скруббера и воздействия подаваемой в скруббер воды материал интенсивно перемешивается и разрыхляется. Поступающий в бутару материал разделяется на мытую руду (крупный продукт) и глинистую пульпу- шламы(мелкий продукт).
Размеры барабана в мм:
Диаметр……………….. 1300-3350
Длина…………………...5200-10770
Частота вращения……...15-20мин-1
Расход воды…………….206 м3/т
Производительность……30-250м3/ч
3. Наклонная корытная мойка
Состоит из наклонного (6-120) корыта с полукруглым днищем. В корыте установлены два вращающихся навстречу друг другу вала с насаженными на них лопастями. Корыто на 2/3 заполнено водой. Исходный материал загружается в мойку на расстояние около 1/3 длины корыта от нижнего его конца; вода подается из брызгал(форсунок) сверху в верхнюю часть корыта(иногда снизу). Вращающиеся от привода валы своими лопастями перетирают руду и перемещают ее вверх к разгрузочным люкам. Глинистые частицы и мелкие зерна крупностью до 2мм удаляются со сливом через отверстие в боковой стенке в нижней части корыта. Крупность слива можно регулировать расходом воды.
4. Промывочная башня
Представляет собой железобетонный цилиндрический резервуар 7 с коническим днищем. В центре башни установлена труба 4, опирающаяся на колпак 2, внутри которой расположен аэролифт 8 для транспортировки мытой руды. Воду и сжатый воздух подают в башню через сопла 3. Исходный материал загружают в заполненную водой башню сверху. Промывка происходит за счет интенсивного движения воды, производимого сжатым воздухом, подаваемым снизу через сопла. Мытая руда аэролифтом подается в сепаратор-распределитель 5, с помощью которого руда распределяется на потоки- циркулирующий, возвращаемый опять в башню, и поток, выводимый из цикла промывки или направляемый в другую башню.
Обычно производится двух- и трехстадиальная промывка руды. Слив, состоящий в основном из глинистых материалов, удаляется в сливной желоб 6. Внизу конического днища имеется шлюз 1 для улавливания посторонних предметов, удаление которых осуществляется с помощью секторного затвора шлюза 9. При промывке в башне истирание зерен минимальное.
Размеры башни в м:
диаметр………………………………….5,5-10
высота цилиндрической части…………6,1-12
высота башни……………………………до 20
Расход, м3/т :
воздуха…………………………………..18-24
воды……………………………………...2,8-3,0
Продолжительность промывки,ч………10-14
Производительность, т/ч……………….120-600
5. Пневматическое обогащение
Осуществляется в соответствии с законами гравитационного разделения частиц различной плотности в вертикальном восходящем или пульсирующем потоке воздуха. Принцип действия воздушного потока на разделяемые минералы практически аналогичен действию водного потока. Поэтому, если пренебречь сжимаемостью воздуха, можно считать ,что законы, действующие при падении минеральных зерен в воде, применимы и к воздушной среде, но с учетом разницы между плотностью воды и воздуха, а также коэффициента их вязкости.
Сущность обогащения:
На слой разделяемого материала, находящегося на наклонном решете, воздействует непрерывный или пульсирующий поток воздуха, нагнетаемые под решето вентилятором. Под действие воздушного потока происходит разрыхление всей толщи обогащаемого материала(постели) и перемещение более тяжелых частиц вниз, а более легких –вверх. При этом материал разделяется на слои различной плотности. Минералы большей плотности находятся внизу постели, а меньшей вверху постели. Дальнейшее разделение материала на продукты осуществляется путем перемещения образующихся слоев различной плотности по рабочей поверхности аппарата в одном или нескольких направлениях. Для обеспечения подвижности слоя материала скорость воздушного потока должна быть значительной, т.е. давление воздушного потока должно быть таким, чтобы преодолеть сопротивление воздухопровода, перфорированной рабочей поверхности(сита) и слоя обогащаемого материала.
Применение:
Для обогащения полезных ископаемых обладающих незначительной плотностью, т.е. каменных и бурых углей, асбеста и некоторых других ПИ.
Целесообразно в районах с суровым климатом или в районах с недостатком воды.
Достоинства:
Низкая себестоимость процесса обогащения, меньшая энергоемкость, отсутствие потребности в воде, получение сухих продуктов обогащения.
Недостатки:
Снижение результатов при обогащении исходного материала повышенной влажности, более низкая технологическая эффективность обогащения.
Вопросы для самопроверки
1.Для каких полезных ископаемых применяются процессы промывки и протирки?
2. Как классифицируются руды по степени промывистости?
3. Что такое пластичность и число пластичности?
4. Каковы принцип действия, устройство и область применения корытных моек, скруббера-бутары, скрубберов и промывочных барабанных грохотов?
5. В чем заключается разница между способами разделения минеральных зерен в водной и воздушной средах?
ПНЕВМАТИЧЕСКОЕ ОБОГАЩЕНИЕ
Осуществляется в соответствии с законами гравитационного разделения частиц различной плотности в вертикальном восходящем или пульсирующем потоке воздуха. Принцип действия воздушного потока на разделяемые минералы практически аналогичен действию водного потока. Поэтому, если пренебречь сжимаемостью воздуха, можно считать ,что законы, действующие при падении минеральных зерен в воде, применимы и к воздушной среде, но с учетом разницы между плотностью воды и воздуха, а также коэффициента их вязкости.
Сущность обогащения:
На слой разделяемого материала, находящегося на наклонном решете, воздействует непрерывный или пульсирующий поток воздуха, нагнетаемые под решето вентилятором. Под действие воздушного потока происходит разрыхление всей толщи обогащаемого материала(постели) и перемещение более тяжелых частиц вниз, а более легких –вверх. При этом материал разделяется на слои различной плотности. Минералы большей плотности находятся внизу постели, а меньшей вверху постели. Дальнейшее разделение материала на продукты осуществляется путем перемещения образующихся слоев различной плотности по рабочей поверхности аппарата в одном или нескольких направлениях. Для обеспечения подвижности слоя материала скорость воздушного потока должна быть значительной, т.е. давление воздушного потока должно быть таким, чтобы преодолеть сопротивление воздухопровода, перфорированной рабочей поверхности(сита) и слоя обогащаемого материала.
Применение:
Для обогащения полезных ископаемых обладающих незначительной плотностью, т.е. каменных и бурых углей, асбеста и некоторых других ПИ.
Целесообразно в районах с суровым климатом или в районах с недостатком воды.
Достоинства:
Низкая себестоимость процесса обогащения, меньшая энергоемкость, отсутствие потребности в воде, получение сухих продуктов обогащения.
Недостатки:
Снижение результатов при обогащении исходного материала повышенной влажности, более низкая технологическая эффективность обогащения.
А. Пневматический сепаратор
По принципу работы напоминает концентрационный стол. Представляет собой короб 4 с односкатной декой 14. Короб устанавливается на раме 10 с помощью ножевых опор 8. Дека получает возвратно-поступательные движения от эксцентрико-шатунного механизма 9, установленного на раме. Дека покрыта резиновым или металлическим ситом 3 с отверстиями 6-8мм. На деке поверх сита крепятся рифли 13, расположенные под углом 10-110 к оси сепаратора. Рифли имеют наибольшую высоту в нижнем углу загрузочного торца деки. Высота рифлей постепенно уменьшается к концу деки.
Дека разделена на четыре поля с самостоятельным подводом воздуха снизу через рукава 12 к диффузорам 2 от общего воздухопровода 11. Подача воздуха осуществляется вентилятором 1.
Дека имеет поперечный и продольный наклоны: угол наклона деки к горизонту составляет в продольном направлении 4-110 и в поперечном 4-110
и может регулироваться.
Исходный уголь через питающий лоток 7 подается на деку, под действием воздушного потока материал разрыхляется и под действием встряхивания деки расслаивается по плотности и крупности. Частицы угля как более легкие, занимают верхние слои постели, скатываются через рифли в поперечном направлении деки и разгружаются вдоль бортов. Частицы породы как более тяжелые, осаждаются в межрифлевом пространстве и перемещаются под действием качательных движений деки в ее конец к приемному желобу. Сепараторы работают в замкнутом воздушном режиме. Дека сепаратора сверху закрыта зонтом 6. Для очистки воздуха от основной массы пыли устанавливается циклон 5.
СП12,СП6,ОСП-100 и СПБ-100М
Техническая характеристика:
Рабочая площадь деки,м2 …………………………….6,5-17
Частота качаний,мин-1 ………………………………..200-400
Удельный расход воздуха,тыс.м3/ (ч·м2)…………….6,5-15,5
Производительность, т/ч………………………………40-100
Б. Применяют также для обогащения углей пневматические отсадочные машины ПОМ-1,ПОМ-1М,ПОМ-2М,ПОМ-2А.
Вопросы для самопроверки
1.Сущность метода пневматического обогащения.
2.Достоинства и недостатки пневматического обогащения.
3.Принцип работы пневматической отсадочной машины.
2.2 ФЛОТАЦИОННЫЕ МЕТОДЫ ОБОГАЩЕНИЯ
Флотацией называется процесс разделения тонкоизмельченных полезных ископаемых, осуществляемый в водной среде и основанный на различии их способности, естественной или искусственно создаваемой, смачиваться водой, что определяет избирательное прилипание частиц минералов к поверхности раздела двух фаз.
Флотационный процесс осуществляется в трехфазной системе, включающей твердую(Т), жидкую (Ж) и газообразную (Г) фазы. Наибольшее распространение получила пенная флотация, которая основана на способности несмачиваемых (гидрофобных) минералов прилипать к пузырькам воздуха, которые образуются в результате аэрации пульпы, и всплывать вместе с ними на поверхность пульпы, образуя пенный продукт, а смачиваемых (гидрофильных) минералов оставаться взвешанными в пульпе, образуя камерный продукт. Минеральные частицы, закрепившиеся на поверхности воздушных пузырьков, наз. флотирующими, а незакрепившимися - нефлотирующимися.
Крупность флотируемых частиц в процессе пенной флотации обычно 0,15мм для руд, и 0,5мм для углей.
Для увеличения естественного различия в смачиваемости поверхности минералов или для искусственного создания такого различия минеральную поверхность обрабатывают особыми веществами, называемые флотационными реагентами.
Обычно в пенный продукт флотации извлекают полезный минерал, а в камерный- минералы пустой породы. Такой процесс носит название прямой флотации. В отдельных случаях наоборот и такой процесс называется обратной флотацией.
Если в процессе флотации получают концентрат, содержащий два или более компонента, такую флотацию называется коллективной. Если в процессе флотации последовательно получают несколько концентратов при содержании в каждом только одного ценного компонента, то такую флотацию называется селективной.
1. Разновидности флотационного процесса.
Масляная флотация - процесс, при котором в пульпу вводится минеральное масло(нефтепродукт) , плотность которого меньше плотности воды. Гидрофобные частицы прилипают к капелькам масла, а гидрофильные остаются взвешанными в пульпе.
Пленочная флотация - процесс, при котором на поверхность движущегося потока воды ссыпается слой мелких минеральных частиц. Гидрофобные смачиваются водой и удерживаются в виде пленки на поверхности воды за счет сил поверхностного натяжения. Гидрофильные минералы смачиваются водой и тонут.
Флотация твердой стенкой - процесс, при котором минеральные частицы разделяются при помощи гидрофобной твердой поверхности(стенки). К таким поверхностям прилипают гидрофобные частицы( обогащение алмазов).
Электрофлотация - основана на использовании в качестве газовых пузырьков водорода и кислорода, образующихся при электролизе воды.
Кроме этих способов существуют : ионная, флотоотсадка, флотогравитация и другие способы.
2. Физические и физико-химические основы флотационного процесса.
Флотационный процесс осуществляется в гетерогенной системе, состоящей из твердой (минеральная частица), жидкой (вода) и газообразной(воздух) фаз, физико-химические свойства соприкасающихся фаз и поверхностные явления, происходящие на границах их разделов, имеют очень важное значение. Каждая из поверхностей раздела фаз резко отличается по своим свойствам от объемных свойств фаз тем, что на поверхности их раздела имеется избыток свободной поверхностной энергии, образующийся вследствие некомпенсированных сил, действующих в этом слое.
При соприкосновении двух фаз, жидкой и газообразной, на молекулу 1, находящуюся внутри объема жидкости, действуют силы взаимного притяжения других молекул, расположенных вокруг нее, и поэтому силы взаимного притяжения молекул уравновешены. Молекула 2 , находящаяся на поверхности жидкости, испытывает значительное притяжение со стороны нижележащих молекул объема жидкости, так как силы взаимного притяжения молекул газообразной фазы из-за их значительного удаления друг от друга несущественны. В результате этого на поверхности раздела возникают неуравновешенные силы, стремящиеся втянуть молекулу внутрь жидкости. Под действием этих сил жидкая фаза стремится к сокращению свободного поверхностного слоя. Для создания новой поверхности раздела необходимо затратить работу, которая называется поверхностным натяжением или удельной свободной поверхностной энергией и обозначается σ (Н/м).
Поверхность минеральных частиц также имеет избыток свободной энергии. При дроблении и измельчении минералов их кристаллическая решетка разрушается и на поверхности раскола происходит разрыв связей между атомами и молекулами, которые в этом случае взаимодействуют по аналогии с предыдущим явлением, главным образом лишь с нижележащими атомами и молекулами, находящимися в объеме тела. Чем больше связей разрушено и чем они были сильнее, тем выше свободная поверхностная энергия. Так как зона действия молекулярных сил небольшая, предполагается, что свободная поверхностная энергия концентрируется в тонком поверхностном слое толщиной в несколько молекул.
Вода является полярной жидкостью и благодаря значительному дипольному моменту своих молекул вступает в связь с поверхностью минералов, образуя на ней упорядоченные пограничные слои, называемые гидратными. Толщина и структура гидратных слоев зависят от смачиваемости поверхности. Гидрофильные поверхности характеризуются преобладанием на них нескомпенсированных связей; они активно взаимодействуют с молекулами воды, благодаря чему происходит смачивание поверхности минерала водой(гидратация). Гидрофобные поверхности характеризуются незначительной поверхностной энергией; они слабо взаимодействуют с молекулами воды и не смачиваются ею.
Возможность гидротации твердой поверхности определяется по работе адгезии (взаимное притяжение молекул двух разнородных фаз на границе ихразделов) WA , т.е. по затратам энергии на разрыв жидкой и твердой фаз
где
ж.г. – жидкость – газ
т.г. – твердое-газ
ж.т. – жидкость – твердое
На практике пользоваться этой формулой затруднительно из-за невозможности экспериментально определить эти значения, поэтому используют оценку гидратированности поверхности по краевому углу смачивания. Краевой угол смачивания θ – это угол , образованный касательными к поверхности минерала и поверхности пузырька на границе трех фаз(жидкость- газ- твердое).
Теоретически краевой угол смачивания может поменяться в широких пределах от 00 (абсолютная смачиваемость, полная гидрофильность, капля полностью растекается по поверхности минерала) до 1800 (абсолютное несмачивание, предельная гидрофобность, капля воды совершенно не растекается по поверхности минерала; полная несмачиваемость никогда не наблюдается).
Краевые углы можно измерить двумя способами: при нанесении на минеральную поверхность капли воды в окружении воздуха и при подведении пузырька газа под минерал в окружении воды. Равновесное значение краевого угла смачивания θ определяется по уравнению
Откуда
Подставляя значение σт.г. - σж.т. в уравнение работы адгезии , получаем:
Чем больше значение краевого угла смачивания, тем хуже минерал смачивается водой, и тем легче пузырек воздуха вытесняет воду с поверхности минерала и закрепляется на минерале. Флотация наблюдается уже при краевых углах смачивания менее 900. Краевой угол смачивания может служить мерой флотируемости минералов.
Основным актом пенной флотации является закрепление отдельной минеральной частицы на поверхности воздушного пузырька и образование комплекса минерал – воздушный пузырек. Минерализация воздушных пузырьков происходит при столкновении их с частицами или в результате образования на минеральных поверхностях мельчайших пузырьков газа, выделяющегося из раствора. Частицы минерала, покрытые мельчайшими пузырьками, легче закрепляются на крупных пузырьках. Работа вытеснения воды воздухом с поверхности минерала может совершаться только за счет уменьшения потенциальной энергии системы. Следовательно при вытеснении воды воздухом сумма всей поверхностной энергии системы должна стать меньше первоначальной.
При сближении частицы с пузырьком воздуха необходимо преодолеть сопротивление прослойки воды между ними. Прилипание частицы к воздушному пузырьку (по Н.Н.Фрумкину) происходит следующим образом:
При сближении пузырька и частицы до расстояния от h 1 до h 2 свободная поверхностная энергия остается неизменной. При утончении прослойки воды от h 2 до h 3 свободная энергия возрастает и для преодоления этого барьера приходится затрачивать дополнительную энергию. При достижении некоторого критического расстояния h3 прослойка воды становится тонкой и неустойчивой, свободная поверхностная энергия резко снижается, и частица на участке h 3 – h 4 с очень большой скоростью, скачкообразно, сближается с пузырьком и прилипает к нему. Продолжительность прилипания лежит в пределах 0,0001-0,015 с. На твердой поверхности обычно остается тончайшая пленка воды толщиной h 4 , которая меньше при большей степени гидрофобности поверхности частицы и больше- при меньшей ее гидрофобности. Удаление этой остаточной водяной пленки затруднительно, так как связано с возрастанием свободной поверхностной энергии.
В практике флотации, в результате слипания в пульпе пузырьков и минеральных частиц, образуются разнообразные агрегаты (один пузырек и прилипшая к нему единичная частица, единичная частица с группой прилипших пузырьков, пузырек с несколькими прилипшими к нему частицами и т.д.).
В пульпе флотационных машин минерализованные пузырьки испытывают действие различных сил (силы тяжести, механических струй пульпы, взаимных столкновений), стремящихся оторвать частицы от пузырьков.
Чтобы этого не случилось, силы прилипания должны быть больше сил отрыва. Равновесное условие действия силы прилипания( левая часть уравнения) и силы отрыва (правая часть уравнения) имеет вид
где
d – диаметр окружности, по которой воздушный пузырек прикрепляется к твердой поверхности,м;
σж.г – поверхностная энергия на разделе фаз жидкость-газ, Н/м;
V – объем пузырька,м3;
Δ – плотность жидкости,кг/м;
R – радиус пузырька,м;
h – высота пузырька,м;
θ – краевой угол в градус.
Из уравнения следует, что прочность прилипания тем выше, чем больше краевой угол смачивания и чем меньше гидратирована поверхность минеральных частиц.
3.Флотационные реагенты
Химические вещества, вводимые во флотационную пульпу для управления флотационным процессом, обеспечения высокой избирательности флотации различных минералов(т.е. эффективности отделения полезных минералов от пустой породы или их отделения друг от друга) ,повышения прочности воздушных пузырьков и стабилизации процесса флотации, наз. флотационными реагентами.
Реагенты делятся на группы:
- собиратели (или коллекторы);
- пенообразователи;
- активаторы;
- депрессоры(подавители);
- регуляторы среды.
В большинстве случаев закрепление реагентов на поверхности твердого и газообразного вещества происходит за счет адсорбции (физической или химической). Адсорбция является самопроизвольным процессом, сопровождающимся уменьшением свободной энергии системы. Физическая адсорбция между кристаллической решеткой адсорбента и адсорбируемым веществом осуществляется силами молекулярного притяжения. При хемосорбции закрепление адсорбируемого реагента осуществляется путем образования поверхностных химических соединений мономолекулярного характера. Эти соединения существуют только в комплексе с твердой фазой. Хемосорбция дает более прочную связь адсорбированного вещества с адсорбентом, чем физическая адсорбция.
Адсорбцию (Г) реагента на поверхности раздела жидкой и газообразной фаз можно определить из уравнения Гиббса
где
С - концентрация растворенного вещества;
R - газовая постоянная;
Т - абсолютная температура;
dσ / dC – частная производная поверхностной энергии по концентрации, называемая поверхностной активностью.
При отрицательном значении dσ / dC адсорбция положительная, концентрация растворенного вещества на разделе фаз больше, чем в объеме раствора. В этом случае растворенное вещество понижает поверхностное натяжение и называется поверхностно-активным. При положительном значении наблюдается обратный процесс, поверхностное натяжение повышается. Скорость адсорбции зависит от концентрации реагента в растворе, его химической природы и структуры, температуры и диффузии молекул.
Реагенты-собиратели – органические вещества, избирательно концентрирующиеся на поверхности извлекаемых минеральных частиц, гидрофобизирующие их поверхность и способствующие прилипанию их к воздушным пузырькам. Это гетерополярные и аполярные вещества.
Молекулы гетерополярных собирателей имеют сложную ассиметричную структуру, состоящую из двух частей: полярной 1 и аполярной2 . Действие реагентов-собирателей сводится к тому, что их молекулы своей полярной частью закрепляются на поверхности минерала в точке 3, а их аполярная (гидрофобная ) часть обращена в водную среду. Такая структура слоя реагента-собирателя обуславливает несмачиваемость поверхности минерала. Большинство гетерополярных реагентов растворимы в воде, а аполярные собиратели плохо растворимы в воде.
Реагенты-пенообразователи – поверхностно-активные вещества, самопроизвольно концентрирующиеся на поверхности раздела вода-воздух и понижающие на этой границе поверхностное натяжение. Молекулы пенообразователя адсорбируются на границе раздела вода-воздух таким образом, что полярная часть молекулы пенообразователя, вступая во взаимодействие с диполями воды, обращена в одную фазу, а аполярная в воздушную фазу.
Реагенты Э-1 иЭ-1А представляют собой смесь монобутиловых спиртов низших полиэтиленгликолей. Применяются при коллективной флотации, не обладают собирательным действие.
Пенообразователь ИМ-68 – представляет собой смесь высокомолекулярных спиртов, содержащих 6-8 атомов углерода в радикале. В состав входят: гексиловый спирт, гептиловый спирт, октиловый спирт. Применяется при флотации железных руд и углей, не обладает собирательным действием.
Кубовые остатки - производства бутиловых спиртов представляют собой смесь октиловых спиртов и спиртов, содержащих более восьми атомов углерода в радикале. Применяется при флотации углей.
Пенообразователь Т-80, представляет собой смесь диоксановых и пирановых спиртов. Применяется при флотации руд и углей.
Пенообразователь ОП СБ представляет собой смесь монобутиловых эфиров полипропиленгликолей. Применяется при флотации медно-молибденовых руд.
Сосновое масло – представляет собой смесь ароматических спиртов терпенового ряда с ароматическими углеводородами. Дорог, поэтому применяется редко.
Реагенты-регуляторы. Применение реагентов-регуляторов дает возможность проводить селективную флотацию. Они делятся на: активаторы, подавители и регуляторы концентрации водородных ионов в пульпе.
Реагенты-активаторы. Основное назначение- улучшение закрепления реагентов-собирателей на поверхности извлекаемого материала с целью интенсификации его флотации. Медный купорос(CuSO4 ·5H2O), сернистый натрий(Na2S), серная кислота(H2SO4).
Реагенты-подавители(депрессоры). Понижают флотируемость тех минералов, извлечение которых в данном процессе не нужно.В качестве подавителей применяют щелочные реагенты(известь, едкий натр)
Реагенты-регуляторы среды. Эти реагенты, изменяющие концентрацию гидроксильных и водородных ионов (рН среды) флотационной пульпы, применяют для создания оптимальных условий действия других реагентов при флотации. В качестве реагентов применяют известь- Са(ОН)2.
4.Флотационные машины
Машины для флотационного обогащения полезных ископаемых, в камерах которых исходный материал разделяется в аэрированной пульпе на пенный и камерный продукты.
Классификация: способа аэрации пульпы .
Механические – перемешивание пульпы, засасывание и диспергирование воздуха осуществляется импеллером(мешалкой) различной конструкции.
Пневматические- - перемешивание и аэрация пульпы осуществляется подачей через патрубки или пористые перегородки сжатого воздуха.
Пневмомеханические- воздух подается от воздуходувки, а перемешивание пульпы и диспергирование воздуха осуществляется импеллером.
Пневмогидравлические с самоаэрацией – использование для диспергирование принудительно подаваемого воздуха, различных гидравлических устройств.
Машины с изменяемым давлением – аэрация в которых обеспечивается выделением растворенных газов из пульпы.
Комбинированные- пульпа аэрируется несколькими способами.
Формы камеры.
По форме камеры разделяют флотационные машины корытного типа, общего уровня и камерного типа.
Корытного типа – одна вытянутая в длину камера.
Общего уровня – одна вытянутая в длину камера с перегородками , не доходящими до днища.
Камерного типа- состоит из несколько соединенных между собой камер
Съем минерализованной пены с поверхности пульпы может осуществляться самотеком, с помощью гребковых устройств и адгезионного барабана.
В. Камерного типа
Механические флотационные машины
ФМ
Состоит из ряда сдвоенных камер квадратного сечения, первая из которых всасывающая, а вторая прямоточная. В каждой камере установлен блок аэратора, стоящий из вертикального вала 6 , на котором жестко закреплен импеллер, представляющий собой вогнутый диск 7 с шестью радиальными лопатками. Вал вращается внутри вертикальной трубы 1 , верхний конец которой герметически соединяется с корпусом подшипника, а нижняя часть расширяется в виде надимпеллерного стакана, к которому крепится диск 4 с направляющими пластинами 5, расположенными под углом 600 к радиусу. В боковых стенках надимпеллерного стакана имеются три отверстия, одно из которых предназначено для присоединения патрубка 8 (в прямоточной камере это отверстие закрыто пробкой), а два других расположенных друг против друга- для подвода промпродуктов. Если промпродукты не подводятся, одно отверстие закрывается пробкой, а другое перекрывается шибером. Степень открытия этого отверстия регулируется тягой. Исходная пульпа поступает в камеру через приемный канал 10, откуда по трубе 8 направляется в аэратор, расположенный в центре камеры. При вращении импеллера пульпа лопатками отбрасывается от центра к периферии, в результате чего в центральной зоне импеллера создается небольшое разряжение. За счет этого воздух из атмосферы по трубе 9 и центральной трубе 1 засасывается в машину, диспергируется импеллером и смешивается с пульпой. Всасывющая и прямоточная камеры разделены перегородкой 2 , имеющей в нижней части нерегулируемое отверстие, через которое насфлотированная пульпа (камерный продукт) из левой камеры попадает в правую. Уровень пульпы в камерах одинаков. Пески из прямоточной камеры удаляются через специальное отверстие. Всплывший пенный продукт из машины удаляется в желоб гребками через продольный борт машины. Общее число камер может быть 22-24.
Имеются ФМ с кипящим слоем, в которых над аэратором по всему сечению камеры установлено решето для создания кипящего слоя из крупнозернистой фракции пульпы. В таких машинах флотируются частицы большей крупности и с большой скоростью.
Применяют для обогащения руд и углей.
Пневматические флотационные машины
В машинах этого типа аэрирование и перемешивание пульпы осуществляется подачей в нее сжатого воздуха от воздуходувок (давление до 25-35 кПа).
Достоинства: проще по конструкции, затрачивают меньше энергии, занимают меньшую площадь.
Применяют для флотации полезных ископаемых простого состава.
Аэролифтные патрубочные машины
Изготавливают с мелкими и глубокими камерами. По всей длине камера машины разделяется на аэрационное и флотационное отделения. Воздух подается по вертикальным патрубкам, снабженным на концах резиновыми наконечниками, предотвращающими попадание в патрубки пульпы. Диспергирование воздуха происходит за счет воздействия вихревого движения пульпы, которое создается за счет перегородок. Для взаимодействия воздуха с пульпой используется принцип аэролифта, когда один из сообщающихся сосудов насыщается пузырьками воздуха, а другой малоаэрирован. Возникает разность гидростатического давления, за счет чего пульпа движется в вертикальном направлении с большой скорость и разгружается в конце ее через разгрузочное устройство. Пена стекает с двух сторон ванны в специальные желоба. Применяют для обогащения монометаллических руд крупностью до 0,3 мм и углей.
Кроме рассмотренных ранее флотационных машин применяют пневматические машины колонного типа, пенной сепарации, пневмомеханические флотационные машины.
5. Производительность флотационных машин.
Зависит от объема камер и времени флотации. Необходимое число камер механических и пневмомеханических машин определяется по формуле:
где
n - необходимое число камер;
V - объем флотируемой пульпы, м3/сут;
t - продолжительность флотации,мин;
Vk – объем флотационной камеры,м3;
K - коэффициент использования камеры( К=0,65-0,8);
Q - производительность по твердому, т/сут;
R - отношение Ж:Т (весовое) в исходной пульпе;
δ –плотность твердой фазы пульпы, т/м3.
Необходимая длина ФМ пневматических корытного типа L(м)
S- площадь поперечного сечения ванны, м2 (не более 10м).
Вопросы для самопроверки
1. На каком принципе основано разделение угольных и породных частиц при флотации?
2. Почему не флотируются угольные частицы крупностью более 1мм?
3. Как влияет гранулометрический состав на результаты флотации?
4. Назовите реагенты для флотации угля, способы подачи их в пульпу и расход.
5. Какие требования предъявляются к машинам для флотации угля?
6. Укажите преимущества механических флотомашин.
7. Какое вспомогательное оборудование необходимо использовать при флотации угля?
8. Чем обусловлена возможность применения прямых схем флотации?
9. Каким образом автоматизирован процесс флотации
10.Какие методы применяются для обезвоживания крупных, мелких
классов углей, угольных шламов?
11.В чем заключается механизм действия флокулянтов?
12. Какие флокулянты применяют на углеобогатительных фабриках?
13. Как влияет на процесс флокуляции гранулометрический и вещественный состав твердой фазы?
14. Нарисуйте схемы обработки и складирования отходов флотации.
15. Какой процесс называется обогащением угля?
16. Дать определения продуктам обогащения.
17. Перечислить методы определения гранулометрического состава сыпучих материалов.
18.Определение гранулометрического состава руды методом ситового
анализа.
19. Перечислить методы определения гранулометрического состава сыпучих материалов.
20. Изложить методику проведения ситового анализа.
21. Дать определение непрерывному, разовому, мокрому рассевам.
22. Перечислить и охарактеризовать виды влаги.
III. Вспомогательные процессы
1.1Обезвоживание продуктов обогащения
Процесс удаления избыточной влаги из продуктов обогащения называется обезвоживанием. Отделяемая от продуктов обогащения вода используется для оборотного водоснабжения или сбрасывается за пределы предприятия. Содержание влаги (или влажность) определяется отношением массы воды в продукте к общей массе сырого продукта и выражается в процентах. Содержание влаги регламентируется ГОСТами и должно быть в пределах:
- для угольных концентратов -1,5-2%;
- для цветных металлов -5-12%;
- для магнетитовых концентратов-2-4% и т.д.
Различают следующие виды влаги:
- химически связанная влага - представляет собой молекулы воды, химически связанные с веществом минерала и непосредственно входящие в его кристаллическую решетку(может быть выделена нагреванием минерала до 3000 и выше);
- адсорбированная влага - представляет собой гидратные пленки, удерживаемые на поверхности минерала за счет сил адсорбции;
- капиллярная влага - представляет собой молекулы воды, удерживаемые в порах минералов силами капиллярного давления;
- гравитационная (свободная) влага - представляет собой воду, заполняемую промежутки между частицами.
В зависимости от влажности продуктов обогащения различают:
- обводненные продукты, представляющие собой смеси твердого и воды и содержащие все виды влаги (40%);
- мокрые продукты-содержащие часть гравитационной влаги, капиллярную, адсорбированную и химически связанную влагу (от 15-25% до 40%);
- влажные продукты - содержащие только некоторую часть капиллярной влаги, адсорбированную и химически связанную влагу (от 5-6 до 15-25%);
- воздушно-сухие продукты - содержащие только адсорбированную и химически связанную влагу(4-6%);
- сухие продукты - содержащие только гигроскопическую и химически связанную влагу(0,5-4%).
В зависимости от крупности обезвоживаемых материалов различают следующие основные методы обезвоживания;
1.Дренирование- для углей крупностью более 10мм и руд более 3-5мм.
2.Центрифугирование- для углей крупностью 0,5-10мм.
3.Сгущение-для углей крупностью менее 0,5мм и для руд менее 0,1мм.
4.Фильтрование- для углей крупностью менее 1-0,5мм и руд менее 0,1мм.
5.Сушка- для углей крупностью менее 10мм и руд менее 0,5-1мм.
3.2 Дренирование
Дренирование - процесс удаления воды из зернистых продуктов за счет естественной фильтрации жидкости через промежутки между частицами под действием силы тяжести. Дренирование производится на обезвоживающих грохотах, в элеваторах, горизонтальных ковшовых конвейерах, механических спиральных классификаторах, бункерах и штабелях.
Грохоты имеют щелевидные сита из нержавеющей стальной или латунной проволоки трапецеидального сечения, расположенные широкой стороной трапеции вверх. Ширина щелей сита составляет 0,25;0,5;0,75 и 1мм.
Обезвоживающие элеваторы и горизонтальные ковшовые конвейеры.
Элеваторы устанавливают на отсадочных машинах, моечных желобах и в зумпфах-классификаторах. Обезвоживание происходит в дырчатых ковшах элеваторов в период подъема материала.
Ковшовые конвейеры устроены подобно элеваторам.
Обезвоживающие бункера и штабели.
Бункер представляет собой железобетонные прямоугольные ячейки с пирамидальной нижней частью имеющей перфорированный затвор для стока воды. Выпуск воды производится открытием затвора.
Штабели - представляют собой влажный материал, уложенный в конусообразные штабели, размещенные в закрытых складах. Исходный материал предварительно обезвоживается в прямоугольных отстойниках, имеющих по всей ширине сливные пороги для отвода основной массы воды.
Пол наклонный, вода сливается через боковые отверстия-окна, а затем перемещается в конусные штабели вторичного обезвоживания.
3.3 Центрифугирование.
Операция обезвоживания мелких мокрых и тонких обводненных продуктов под действием центробежных сил. Центрифугирование осуществляется в центробежных аппаратах, называемых центрифугами.
Фильтрующая центрифуга.
Состоит из корпуса 2, в котором на вертикальном валу закреплен конический ротор 3. Поверхность ротора представляет собой фильтрующее сито со щелевидными отверстиями размером 0,25-0,5мм. Частота вращения ротора составляет 400-600 мин-1. Обезвоживаемый продукт через питающую трубу попадает на вращающийся вместе с ротором распределительный диск 1, с которого он центробежной силой равномерно разбрасывается на внутреннюю фильтрующую поверхность ротора. Под действием центробежной силы происходит принудительная фильтрация воды через осадок твердых частиц и сетчатую поверхность ротора. Прошедшая через сито ротора жидкая фаза называется фугатом, а движущийся по ситу обезвоженный продукт осадком. Осадок удаляется с ротора самотеком за счет центробежных сил.
В центрифугах с вибрационной выгрузкой осадка, перемещение и разгрузка происходит за счет вибраций ротора. В шнековых центрифугах разгрузка осадка производится принудительно, с помощью шнека, вращающегося с частотой несколько меньшей, чем частота вращения ротора. Для обезвоживания тонких обводненных продуктов применяют осадительные центрифуги.
3.4 Сгущение
Процесс осаждения твердых частиц из мелкозернистых (размером менее 0,5мм) пульп с получением уплотненного сгущенного продукта и осветленного слива. Для сгущения применяют устройства и аппараты, в которых осаждение частиц происходит под действием силы тяжести - цилиндрические и конические сгустители, шламовые отстойники и т.п.
Цилиндрические сгустители делятся на :
- с центральным расположением привода (одно- и многоярусные);
- с периферическим расположением привода.
Одноярусный цилиндрический сгуститель
с центральным приводом состоит из цилиндрического чана 1 со слабонаклонным днищем и кольцевым сливным желобом 2, загрузочной трубы 8 и разгрузочной воронки 10 для выгрузки сгущенного осадка. На центральном валу 9 крепится гребковая рама с граблинами 7. Вал проходит через ферму 3, на которой располагается электропривод 6 для вращения граблин. В случае зашламливания гребковой рамы и ее остановки вал вместе с рамой автоматически поднимается вверх при помощи механизма 5, имеющего указатель для перегрузки сгустителя. Чан сгустителя изготовлен из бетона. Чан заполняется пульпой. Вверху располагается слой осветленной жидкости (зона А), ниже слой пульпы исходной плотности (зона Б), еще ниже промежуточный слой (зона В), и наконец в самом низу находится уплотненный сжатый слой (зона Г). Сгущенный продукт ,осевший на дне сгустителя, гребками перемещается к центру в разгрузочную воронку, откуда удаляется шламовыми насосами. Осветленный слив переливается через порог и удаляется в кольцевой сливной желоб.
3.5 Фильтрование
Процесс разделения жидкой и твердой фаз пульпы с помощью пористой перегородки под действием разности давлений, создаваемой разряжением или избыточным давлением воздуха. Жидкая фаза пульпы проходит через отверстия в перегородке и собирается в виде фильтрата, а твердая задерживается на поверхности перегородки в виде обезвоженного осадка, а потом удаляется.
Различают фильтрование под вакуумом (вакуум-фильтры) и под давлением(пресс-фильтры). В качестве пористых перегородок применяют различные фильтрующие ткани:
- хопчатобумажные - фильтрбельтинг, фильтродиагональ;
- синтетические - нейлон, лавсан, капрон;
- металлические - сетки из стальной и латунной проволоки.
На ОФ применяют в основном дисковые, барабанные и ленточные вакуум - фильтры.
Шестидисковый вакуум-фильтр
Состоит из фильтрующих дисков 2, расположенных на пустотелом валу 1. Диски своей нижней половиной помещены в ванну 5. Диски набираются из 12 пустотелых секторов7 с перфорированной или рифленой поверхностью. Каждый из секторов обтягивается фильтровальной тканью или сеткой. Секторы крепятся к валу длинными шпильками(спицами) 6 и накладками. Секторы дисков соединены с каналами вала, из которых через распределительные головки отсасывают воздух, и в секторах образуется вакуум. Вал с дисками приводится во вращение с помощью привода. Фильтр снабжен ножами 3 для снятия осадка с поверхности секторов, мешалкой 4 для перемешивания пульпы и желобом для сбора перелива.
Принцип работы фильтра:
Исходная пульпа поступает в ванну и в период нахождения дисков в ванне за счет вакуума происходит накопление осадка на их боковых поверхностях. При выходе диска из ванны просушивают осадок воздухом. Время накопления и просушки осадка зависит от частоты вращения вала. Съем обезвоженного осадка производится в емкость в конце фазы подсушки Расчет сгустителей сводится к определению общей площади сгущения и диаметра сгустителя по удельной производительности на 1 м2.
Пластинчатый сгуститель
Представляет собой камеру, в которой исходное питание подается через окно. В камере установлены параллельные пластины, расположенные на расстоянии 50-7-мм друг от друга под углом 40-600 к горизонту. Пластины позволяют разделить поток на струи с ламинарным движением пульпы и уменьшить путь оседания твердых частиц. Общая площадь сгущения равна площади всех пластин. Сгустители изготавливают с площадью сгущения 50,100,200 и 1000м2.
Шламовые отстойники
Для выделения твердой фазы из пульп очень малой плотности. Они представляют собой большие прямоугольные бассейны. Устанавливают их в основном на углеобогащении для осветления шламовых вод.
резкой подачей сжатого воздуха (отдувкой). После отдувки фильтрующая ткань промывается. Полный цикл производится за один оборот вала.
Применение: для обезвоживания рудных и угольных пульп, флотоконцентратов, содержащих тонкие частицы твердого.
Достоинства: большая поверхность фильтрования, занимают небольшую площадь, просты в обслуживании.
Барабанные вакуум - фильтры
Применяют реже, чем дисковые. Поверхность барабана обтянута фильтрующей тканью. При вращении барабана, нижняя часть которого погружена в ванну, происходит накопление и подсушка осадка.
Недостатки: громоздки и дороги.
Применение: при обезвоживании зернистого тяжелого материала, который не удерживается на дисковых фильтрах.
В последнее время применяют ленточные вакуум-фильтры (конструктивно напоминают конвейер).
Фильтр-пресс
Состоит из ряда фильтрующих плит, расположенных горизонтально между стяжками двух плит, верхней упорной и нижней нажимной. Фильтрующие плиты состоят из верхней и нижней рам. Верхняя фильтрующая рама покрыта перфорированной листовой поверхностью и тканью и является камерой для отвода фильтрата. Нижняя рама при сжатии плит служит камерой фильтрования. Под днищем рамы закреплена эластичная диафрагма, которая при подаче на нее воды (давление 1,5 МПа) служит для отжатия влаги из осадка. К плитам приварены патрубки, которые образуют коллекторы, первый служит для отвода фильтратной воды и воздуха, а второй - для подачи исходной пульпы.
Фильтрующая ткань сшита в виде бесконечной ленты и натянута между плитами посредством роликов, натяжного устройства и приводного барабана. После каждого цикла ткань перемещается на один или два марша, осадок снимается ножами и сбрасывается на конвейер.
Принцип работы:
При помощи зажима плиты сжимаются и через коллектор в камеру фильтрования подается исходное питание. Фильтрат проходит через ткань в камеру фильтрата и отводится по коллектору. Отложившийся на ткани осадок отжимается диафрагмой и при необходимости промывается водой и высушивается воздухом. После этого давление снимается, плиты раздвигаются и осадок лентой удаляется из камер на конвейер.
Применение: для обезвоживания угля и руды.
3.6 Окускование полезных ископаемых.
Получаемые в результате обогащения полезные ископаемые часто бывают непригодны из-за своей крупности для дальнейшей переработки или прямого использования. Поэтому для повышения эффективности использования полезных ископаемых применяют операции окускования.
Окускованное полезное ископаемое обладает более высокими показателями, большей устойчивостью при транспортировке и хранении.
Способы окускования
Агломерация Окомкование Брикетирование
для мелких руд тонкоизмельченных мелких и тонких руд
и концентратов руд и концентратов и концентратов,
менее 8(6) мм 80-90% содержания торфа и угля
класса -0,06мм
Агломерация
Является термохимическим способом обработки мелких руд и концентратов с целью их окускования, получаемого за счет спекания.
Технология:
- подготовка смеси (шихты) к агломерации;
- процесс агломерации;
- обработка спекшегося продукта с целью получения агломерата требуемой крупности.
Крупность входящих в состав агломерационной шихты компонентов не должна превышать, мм:
- окисленных железных руд-8(смесь концентрата и руды);
- магнетитовых руд-6;
- возврата -6(мелкого агломерата, оставшегося от предыдущего спекания);
- флюсов-3(известняк, доломит);
- топлива-3(мелкий кокс, антрацит, каменный уголь).
Процесс агломерации производится в агломерационных машинах, состоящих из последовательного ряда спекательных тележек (паллет), вытянутых в длину. Тележки имеют невысокие борта, колосниковое дно и шарнирно соединены между собой. За счет приводного барабана осуществляется медленное движение тележек от места загрузки шихты до выгрузки агломерата. Загрузка производится специальных устройством- укладчиком, обеспечивающим постоянство высоты (250-300мм) слоя материала. Зажигание верхнего слоя шихты производится в зажигательном горне (или горелке) , установленном сразу за укладчиком. Продукты горения от сжигания в горне газообразного или жидкого топлива просасываются через слой шихты и воспламеняют твердое топливо. Шихта разогревается до температуры 1150-13500. Для поддержания горения топлива через слой шихты просасывается воздух. Просос воздуха происходит за счет создания эксгаустером (вентилятором) вакуума в подколосниковом пространстве агломерационной машины.
В процессе агломерации в слое материала образуются следующие зоны:
1- исходная шихта;
2- конденсация;
3- переувлажнение;
4- сушка;
5- интенсивный нагрев;
6- плавление или формирование агломерата;
7- готовый охлаждающийся агломерат.
Процесс протекает таким образом, что в каждый момент горение происходит только в небольшом (не более 40мм) по толщине слоя шихты, так как более глубокие слои не могут гореть из-за низкой для воспламенения температуры и недостаточного содержания кислорода. Выше этого слоя находится готовый спек. По мере перемещения материала вдолб машины горящий слой шихты продвигается все ниже и ниже и при достижении постели (или колосников) процесс спекания заканчивается.
По времени процесс агломерации длится 10-15 мин и подразделяется на три периода:
tH - начальный когда формируются отдельные зоны агломерируемого материала;
t0 - основной, когда газодинамический и тепловой режимы стабилизировались;
tз - когда происходит «выклинивание» отдельных зон.
В процессе спекания происходит также окисление серы, мышьяка, сурьмы и других примесей, а также окислительно-восстановительные процессы в руде. После спекания конечный продукт поступает на дробление, грохочение и охлаждение. После повторного грохочения получается готовый агломерат (надрешетный продукт крупностью более 5-8мм) и мелочь (подрешетный продукт) который используется для создания постели в агломерационной машин. Площадь агломерации в машине до 600м2.
Окомкование
Процесс окускования тонкоизмельченных (85-95% класса 0,06мм) влажных материалов (главным образом железных концентратов) за счет их способности образовывать при перекатывании агрегаты круглой формы- окатыши. Полученные в процессе окатывания сырые окатыши подвергаются упрочению обжиговым или безобжиговым методами. Упрочненные окатыши обладают однородностью по химическому составу и крупности, хорошей восстановимостью и прочностью.
Технология получения обожженных окатышей:
- подготовка шихты для окомкования;
- процесс получения сырых окатышей;
- обжиг окатышей.
1. Подготовка шихты: заключается в усреднении сырья, измельчении добавок до требуемой крупности, дозирования компонентов шихты и смешивания сырья в шнековых, роторных и барабанных смесителях. В шихту добавляют упрочняющие добавки, наиболее распространенным является бентонит( особый вид глины).
2. Окомкование производится во вращающихся барабанных и тарельчатых окомкователях.
Представляет собой наклонную чашу 1, внутрь которой загружается шихта. Чаша имеет очистное устройство 2 и привод 3. Чаша вращается вокруг своей оси, угол наклона чаши можно изменять с помощью специальных рычаговых механизмов. Во время вращения чаши материал, двигаясь по поверхности образует комочки, которые при перекатывании, за счет захватывания близлежащих частиц, превращаются в окатыши сферической формы размером 10-20мм.
3. Для обжига окатышей применяют конвейерные обжиговые машины, комбинированные установки и шахтные печи. При обжиге окатыши проходят последовательно стадии: сушки, подогрева, обжига и охлаждения. В результате получают прочные окатыши, которые после грохочения, отправляют на плавку. Некондиционную мелочь отправляют в качестве оборотного продукта.
Метод безобжигового упрочения окатышей предусматривает введение в шихту специальных вяжущих веществ, затвердевающих при естественных или умеренно повышенных температурах.
Брикетирование
Процесс окускования мелкозернистых материалов за счет прессования под давлением с целью получения из них брикетов - кусков геометрически правильной формы и одинаковых размеров.
Брикетирование руд
Основными видами сырья являются пылеватые руды (бурые железняки), мелкие железные руды, отходы черной металлургии (стружка, окалина), марганцевые руды, медистые колчеданы, окисленные никелевые руды, цинковые концентраты.
Технология:
- подготовка сырья;
- прессование;
- упрочнение брикетов.
Вальцовый пресс состоит из одной или двух пар вращающихся навстречу друг другу вальцов. На цилиндрической поверхности вальцов крепятся бандажи из твердой износо - и термостойкой стали с углублениями в виде различных симметричных полуформ.
Исходная шихта из распределительной чаши 1, снабженной мешалкой 2 поступает через отверстие в дне по течке 3 в пространство между вальцами 1, заполняя углубления в бандажах. При вращении вальцов навстречу друг другу углубления в бандажах совпадают и сжимают находящуюся в них шихту. Ниже линии центров вальцы расходятся и брикеты под действием собственной тяжести выпадают из ячеек. Вальцы приводятся в движение от электропривода через ременную и зубчатую передачи 8. Давление в прессе составляет около 80 МПа.
В качестве связующих веществ используют растворимое стекло, известь, щелоки. В настоящее время в практике получила распространение технология брикетирования при высоких температурах (800-10500) без связующих веществ.
Брикетирование бурых и каменных углей.
Технология брикетирования бурых углей:
- дробление угля до крупности -6+0мм;
- сушка в сушилках до влажности 18-20%;
- охлаждение;
- брикетирование в штемпельных или кольцевых прессах высокого давления.
Штемпельный пресс:
Основной деталью является пресс-форма, размещенная в прессовой головке 1, состоящей из верхней 2 и нижней 3 частей, соединенных между собой стяжными болтами. Прессование происходит в пресс - форме за счет возвратно-поступательного движения штемпеля 5 от шатуна. При движении штемпеля вправо порция угля питателем подается по вертикальному каналу 4 в пресс-форму, при ходе шатуна влево штемпель проталкивает уголь в формовочный канал и спрессовывает его в брикет. Одновременно поворачивая нажимную плиту, которая прижимается к матрицам. Форма и размеры брикета зависят от конфигурации и формы матрицы. Находящиеся в канале брикеты перемещаются за один цикл на расстояние ширины брикета. И самый крайний выпадает из канала.
Технология брикетирования каменных углей и антрацитов (крупность 6-10мм):
- сушка;
- смешивание со связующим материалом в паровом смесителе;
- охлаждение;
Прессование в вальцовых прессах.
Каменные угли и антрациты характеризуются более плотной структурой по сравнению с бурыми углями, меньшей пластичностью и более низким содержанием битума, поэтому их прессуют с добавлением связующих веществ. В качестве связующих веществ применяют нефтяные битумы, иногда каменноугольный пек.
3.7 Сушка
Сушка - процесс обезвоживания влажного материала, основанный на испарении содержащейся в нем воды при нагревании.
Среда, воспринимающая испаряемую из материала влагу, называется сушильным агентом. Таким агентом могут быть горячие дымовые газы или нагретый воздух. Сушка производится в аппаратах, называемых сушилками.
Необходимый объем V(м3) газовых сушилок определяется по формуле:
где
W - расход испаренной влаги, кг/ч;
A - напряжение объема установки по испаренной влаге, кг/(м3·ч).
Значение А получают опытным путем. Величина W зависит от массы высушиваемого материала и от исходной и конечной его влажности.
Барабанная прямоточная сушилка.
Представляет собой сварной, наклонный (под углом 1-50 в сторону разгрузки) барабан 2 с насаженными на него двумя бандажами 1. Посредством бандажей барабан опирается на опорные ролики 6 и вращается вокруг своей оси при помощи укрепленного на барабане зубчатого обода 3, находящегося в зацеплении с шестерней 5 привода 4. С одной стороны барабана происходит загрузка материала и подача вентилятором (дымососом) горячего газа из топки, а с другой разгрузка высушенного материала. Внутри барабана устанавливают насадки 7 для лучшего его заполнения и более интенсивного перемешивания. Сушка происходит при непосредственном контакте горячих газов с материалом, который при вращении барабана пересыпается и медленно перемещается из сушилки вместе с отработанными газами. Газы перед их выбросом в атмосферу обязательно подвергается очистке. Барабанные сушилки предназначены для сушки любого материала независимо от их крупности и начальной влажности. Барабан имеет диаметр 0,5-3,5м и длиной от 2,5 до 27м.
Сушильная установка с трубой сушилкой
Включает в себя вертикальную трубу 3, в которую из бункера питателем - забрасывателем 2 подается исходный материал. Нижняя часть трубы присоединяется к топке 9, а верхняя через газопровод- к циклону 4, батарейному пылеуловителю 5, вентилятору-дымососу 8 и скруберру 6. В трубу-сушилку дымовые газы из топки засасываются при помощи вентилятора - дымососа и движутся по трубе вверх. Материал питателем -забрасывателем подается в нижнюю часть трубы и потоком горячих газов выносится по трубе вверх. В период движения по трубе материал высушивается и, попадая затем в циклон, отделяется от газов, затем выгружается через устройство 7. Скорость движения газов в трубе должна быть достаточной для подъема наиболее крупных частиц. Провалившийся
(не высушенный газами) материал собирается внизу и через затвор 1 выводится из трубы. Трубы-сушилки применяют для сушки продуктов небольшой плотности, крупностью не более 10-15мм. Наибольшее применение нашли для сушки угольных концентратов.
Диаметры: 0,8;0,9;1,0;1,1;1,2;1,5м.
Длина трубы: 15-25м.
Сушилка кипящего слоя
Работает на принципе псевдоожижения сыпучего материала потоками горячих газов. Горючие газы из топки 12, где они образуют за счет сжигания газообразного или жидкого топлива, при помощи нагнетательного вентилятора 8 поступают под газораспределительную решетку 10. Материал из бункера 13 питателем 14 подается в сушильную камеру 9 на решетку 10. Горячие газы, проходя через решетку и слой сушимого материала, поддерживают его вследствие повышенного давления во взвешенном состоянии (кипящий слой). Сушка материала происходит во время его движения по решетке. Отработанные газы подвергаются очистке в сухих пылеуловителях 6, скрубберах 5, имеющих затворы 7 и предохранительные клапаны 4. В период растопки воздух подается вентилятором 1, дымовые газы выбрасываются через растопочную печь 2 с заслонкой 3.
Сушилки кипящего слоя используют в основном для сушки угольных концентратов и отличаются высокой интенсивностью сушки. Площадь решеток составляет от 2,5 до 10 м2. Производительность по высушиваемому углю 100-250т/ч.
Вопросы для самопроверки
Сущность процессов, машины, технология:
1.Окускование ПИ?
2.Брикетирование?
3. Агломерация и окомкование?
4.Дренирование?
5. Центрифугирование?
6. Сгущение?
7. Фильтрование?
8. Сушка?
9. Очистка сточных вод ОФ?
10. Обеспыливание и пылеулавливание?
IV. Опробование и контроль процессов обогащения.
Назначение операций опробования и контроля.
Совокупное управление всеми фазами производства в режиме оптимизации определяет качество конечной продукции предприятия. Под управлением понимается определенная совокупность воздействий, направленных на стабилизацию или улучшение работы управляемого объекта в соответствии с выбранной целью управления.
Управление технологическим производственным процессом можно разделить на три этапа:
- измерение значения контролируемого параметра;
- принятие управляющего решения;
- реализация решения.
Опробование сопутствует любому процессу обогащения, так как только соответствующими измерениями возможно определение качества исходных и полученных продуктов и расчет технологических показателей. На основании опробования составляется технологический и товарный балансы исходного сырья и продуктов обогащения.
Технологический баланс
Составляется аналитическим (расчетным) методом без учета механических потерь. Он подсчитывается за смену, за сутки, декаду и т.п. по уравнениям баланса на основе расчета. Оформляется технологический баланс в виде таблицы, которая включает массовый (весовой) и процентный выход продуктов обогащения, содержание в них и в исходном сырье полезного компонента (компонентов), его извлечение в отдельные продукты. Технологический баланс позволяет контролировать общий ход технологического процесса, сравнивать работу отдельных смен, бригад.
Товарный баланс
Составляется как с использованием данных химического анализа, так и результатов взвешивания и определения влаги всех входных и выходных продуктов обогащения. В товарном балансе учитываются все механические потери.
Опробование
Опробование - совокупность операций по отбору проб исходной руды и продуктов ее обогащения и подготовке их к анализу. Пробой называется взятая по определенным правилам от общей массы с требуемой точностью порция материала, которая должна сохранять определенные свойства исходной массы. Отобранная за один прием проба называется частной(точечной), а составленная из суммы частных проб – называется общей (объединенной) пробой.
В практике опробования, для определения числа частных проб n пользуются математико-статистической формулой:
где
σ - среднее квадратическое отклонение содержания полезного компонента в опробуемом продукте (%);
t - отклонение, выраженное в долях от σ, характеризующее вероятность наступления события (при t=2 погрешность в 95 случаях из 100 не превышает заданную);
Δ – абсолютная погрешность отбора проб в % (0,2-0,8).
Пробы:
Минералогическая проба - позволяет с помощью микроскопического анализа выяснить качественный состав полезного ископаемого , структурные (размер и форма минеральных включений) и текстурные (пространственное распределение минеральных компонентов) его особенности, характер прорастания минералов.
Химическая проба - предназначается для определения содержания различных компонентов в опробуемом материале.
Минимальная проба определяется по формуле:
где
Q - минимальная масса пробы, кг;
К – коэффициент пропорциональности, зависящий от свойств полезного ископаемого (0,6-0,06);
d - диаметр максимальных кусков опробуемого материала, мм;
α- показатель степени, равный 1,5-2,7 (чаще принимается равным -2).
Технологическая проба - предназначается для всестороннего детального исследования полезного ископаемого с целью выбора рациональных методов его обработки и рациональной технологической схемой обогащения. Эти пробы характеризуют средний состав полезного ископаемого во всем месторождении.
Пробы ситового и седиментационного анализов - предназначаются для определения гранулометрического состава опробуемых материалов и должны быть представительными в отношении содержания в них отдельных классов крупности.
для руды
для угля
где
d - максимальный размер кусков, мм.
Методы автоматизированного опробования материала.
Метод продольных сечений - заключается в том, что опробуемый поток материала делится на ряд непрерывных продольных полос, из которых одна или несколько чередующихся отбираются в пробу. Применяется для однородных материалов малой мощности.
Метод поперечных сечений - предусматривает периодическое отсекание в пробу одинаковых поперечных полос материала от потока. На точность опробования этим методом не влияет неоднородность материала.
Вопросы для самопроверки
1. Основы опробования и контроля технологических процессов обогащения.
2. Опробование технологических процессов обогащения.
3. Классификация проб.
4. Статистические характеристики параметров опробования и контроля.
5. Определение минимальной массы пробы.
6. Методика определения значений К и α.
7. Масса пробы для различных видов исследований.
V. Технология обогащения полезных ископаемых
5.1. Обогащение руд цветных металлов
Руды цветных металлов отличаются большим разнообразием по химическому и минеральному составу, характеру вкрапленности, степени окисленности, физическим свойствам и другим признакам. Руды, содержащие в своем составе один ценный металлический компонент, называются монометаллическими, а два и более -полиметаллическими. Как правило, большинство руд являются полиметаллическими, но не все металлические компоненты в них имеют промышленное значение. Основная масса (80—85%) цветных металлов в рудах сосредоточена в сульфидных минералах, представляющих собой соединения металлов с серой. Различают руды:
- сульфидные, в которых содержание ценного компонента в виде несульфидных минералов не превышает 10% общей массы в руде;
- смешанные, в которых 80—90% цветных металлов сосредоточены в сульфидных оруденениях, а содержание окисленных форм металла составляет от 10 до 20%;
- окисленные, в которых содержание окисленных форм металла свыше 20%.
По содержанию металлов руды делятся на богатые, бедные и забалансовые (непромышленные). Такое деление является условным и изменяется в зависимости от уровня развития техники и технологии обогащения, потребностей в производстве металлов и др. Основным процессом обогащения руд цветных металлов является пенная флотация. Большинство мелко - и тонковкрапленных руд обогащают по флотационным схемам, отличающимся большим разнообразием. На флотационное обогащение руда поступает измельченной. Крупность измельчения определяется минеральным составом руды и характером вкрапленности минералов.
Схемы флотационного обогащения монометаллических руд сводятся к следующим вариантам: руда крупновкрaпленная, полезные минералы не склонны к ошламованию. Грубоизмельченная руда флотируется в одну стадию и один прием с получением кондиционного концентрата и отвальных хвостов; руда мелковкрапленная, полезные минералы не склонны к ошламованию. Мелкоизмельченная руда флотируется по простой схеме, после основной флотации некондиционные концентрат и хвосты подвергаются перечистной и контрольной флотации. Чем выше содержание полезного компонента в руде, тем меньше требуется перечистных операций для концентрата, и тем больше контрольных — для хвостов. Чем выше требования к качеству концентрата, тем большему числу перечистных операций Промпродукты, полученные в процессах перечистной и контрольной флотации, если они содержат свободные зерна полезного минерала и пустой породы, подвергают повторной флотации или совместно с исходной рудой, или в отдельном цикле. Если промпродукты состоят из сростков минералов, то они флотируются после доизмельчения или с исходной рудой, или в отдельном цикле;
- руда имеет агрегати вную вкрапленность. Грубоизмельченная руда флотируется с получением отвальных хвостов и бедного концентрата, который после доизмельчения флотируется во второй стадии с получением кондиционного концентрата и хвостов (или промпродукта);
- руда имеет неравномерную вкрапленность. Грубоиз-мельченная руда флотируется с получением кондиционного концентрата и богатых хвостов, которые после измельчения направляют во вторую стадию обогащения, после которой получают кондиционные концентраты (промпродукт) и отвальные хвосты. Для руд с неравномерной вкрапленностью применяют также трехстадиальные схемы.
При обогащении полиметаллических руд применяют одно-, двух- и трехстадиальные схемы с получением двух, трех и более концентратов и отвальных хвостов. В зависимости от последовательности выделения полезных компонентов различают коллективные, селективные и коллективно - селективные схемы обогащения.
Коллективная схема флотационного обогащения предусматривает получение коллективного концентрата, содержащего одновременно несколько полезных компонентов.
Прямая селективная (или последовательно селективная) схема флотационного обогащения предусматривает последовательное выделение отдельных полезных компонентов с получением нескольких концентратов.
Коллективно-селективнаясхема флотационного обогащения предусматривает получение вначале коллективного руда крупновкрaпленная, полезные минералы не склонны к ошламованию. Грубоизмельченная руда флотируется в одну стадию и один прием с получением кондиционного концентрата и отвальных хвостов.
Технологическая схема обогащения руды на флотационной фабрике.
Схемы коллективной флотации в практике обогащения полезных ископаемых применяются сравнительно редко (флотация золотосодержащих руд, когда в концентрат переходят золото и сульфидные минералы; медно-пиритных руд, при малом содержании в них пирита, с получением медно-пиритного концентрата и др.). Наибольшее распространение в практике флотационного обогащения полиметаллических руд получили последовательно селективные и коллективно-селективные схемы.
Самостоятельная работа
1. Составить схему прямой селективной флотации медно-пиритной руды.
2. Составить схему коллективно-селективной флотации медно-пиритной руды.
5.2 Обогащение руд черных металлов
Железные руды по минеральному составу рудной части подразделяются на магнетитовые (60% запасов); гематитовые (мартитовые и окисленные - 15%); бурожелезняковые (20%) и сидеритовые (5%).
В промышленности в первую очередь используются богатые магнетитовые, гематитовые и бедные магнетитовые руды после их обогащения. Бедные гематитовые, гематито-мартитовые, окисленные и сидеритовые руды обогащаются в незначительном объеме.
Качество концентратов, используемых для выплавки металла, регламентируется по содержанию железа, шлакообразующих элементов и рудных примесей.
Доменные руды, поступающие в передел без обогащения, должны иметь крупность: магнетитовые 50(40) - 10 мм; гемахитовые 50(80) -10 мм; бурожелезняковые 80(120) - 5мм, Содержание железа в магнетито-гематитовых рудах составляет 46-56, бурожелезняковых - не менее 44, сидеритовых 32,5-36%.
Магнетитовые руды представлены обычно магнетитом (Fe304) с примесями гематита, мартита и др.
Ярко выраженные магнитные свойства магнетита предопределяют выбор наиболее экономичного метода обогащения - магнитной сепарации в слабом магнитном поле. По магнитным схемам обогащения (с применением как мокрой, так; в отдельных случаях и сухой магнитной сепарации) перерабатываются большинство магнетитовых кварцитов. Технология переработки магнетитовых руд предусматривает стадиальное обогащение с последовательным выводом нерудной части в хвосты. Схемы бывают двух-, трех- и многостадиальные с I-III стадиями измельчения и II-V стадиями обогащения. Применение стадиальных схем обогащения позволяет без переизмельчения выводить из процесса пустую породу по мере раскрытия минералов. Все разновидности схем обогащения обеспечивают получение железных концентратов с содержанием в них железа 63% и выше.
К разновидностям данной схемы относят схемы с включением в I стадию измельчения мокрого рудного самоизмельчения (в этом случае применяется одностадиальное дробление), а во II и III — рудногалечное измельчение.
Исходную дробленую руду крупностью более 12 (6) мм иногда перерабатывают по схеме с сухой магнитной сепарацией с получением отвальных хвостов и с последующим измельчением концентрата сухой магнитной сепарации и обогащением его по магнитообогатительной схеме.
Для обогащения магнетито-гематитовых или магнетито-мартитовых руд с преобладанием магнетита применяют комбинированные магнито-флотационные и магнито-гравитационные схемы. Флотация железных руд производится с применением анионных (прямая и обратная флотация) и катионных (обратная флотация) реагентов-собирателей.
Самостоятельная работа
Составить схему стадиального обогащения руды (по выбору).
5.3. Обогащение углей
Обогащению подвергаются рядовые угли, которые по своей зольности (иногда и сернистости) не удовлетворяют требованиям. Предъявляемым потребителями. При обогащении угля удаляются содержащиеся в нем минеральные примеси. Зольность является основным показателем качества при обогащении и переработке углей. В зависимости от своих физико-механических свойств и возможности использования для технологических целей или энергетических целей угли делятся на различные марки и группы. В качестве основных классифицирующих параметров приняты: выход летучих веществ Vdaf , %, толщина пластического слоя y , мм и влага общая Wrt ,%.
Различают марки углей: Д (длиннопламенный), Г (газовый), ГЖ (газовый жирный), Ж (жирный), К (коксовый), ОС (отощенный спекающийся), Т (тощий) и А (антрацит). Указанный ряд марок углей характеризуется уменьшением выхода летучих веществ (от марки Д до марки А) и увелическием показателей толщины пластического слоя (от марки Д до марки К) с дальнейшим уменьшением у марок ОС, Т и А.
Для коксования используют угли наиболее ценных марок (К, ГЖ,Ж), для обогащения применяют более совершенные технологические схемы, более глубокое обогащение (обычно до 0 мм). Энергетические угли обогащаются в том случае, когда это экономически выгодно.
Обогатимость углей (их способность к разделению на соответствующие продукты) характеризуется показателем обогатимости Т, предствляющим собой отношение суммарного выхода промежуточных фракций (для каменных углей плотностью 1400-1800кг/м3и для антрацитов 1800-2000 кг/м3) к выходу беспородной массы:
где
γпп и γп – содержание соответственно промежуточной и породной (плотностью более 1800 кг/м3 для каменных углей и более 2000 кг/м3 для антрацитов) фракций.
В зависимости от значения Т различают следующие категории обогатимости углей и антрацитов.
Степень обогатимости | Легкая | Средняя | Трудная | Очень трудная |
Категория обогатимости Т | 1 | 2 | 3 | 4 |
Т, % | До 4 вкл. | Свыше 4 до 10 вкл. | Свыше 10 до 17 вкл. | Свыше 17 |
В зависимости от степени обогатимости углей и их назначения разработаны типовые схемы обогащения.
Степень обогатимости | 1-2 | 2-3 | 4 |
Обогащение | 1.Мокрая классифика-ция на классы круп-ностью 13(10)мм 200(300) мм <13(10)мм 2.Обесшламливание класса <13(10). 3.Обогащение угля крупностью 13(10)-200(300)мм в тяжелых суспензиях (можно отсадкой). 4.Обогащение угля крупностью 0,5-13(10)мм– отсадкой. 5.Шламов крупностью <0,5 мм – 0,5-13(10)мм- флотацией. | 1.Класификация ря-дового угля с дешла-мацией мелкого класса. 2.Обогащение крупного класса 13(10)-200(300) мм в тяжелых суспензиях. 3.Мелкого 0,5-13(10)мм в тяжелосуспензинных гидроциклонах с после-дующим переобогаще-нием микста вместе с дробленным промпро-дуктом в тяжелосуспен-зионных гидроцикло-нах. 4.Шлама крупностью <0,5мм – флотацией. | 1.Классификация рядового угля. 2. Обогащение угля крупностью >6мм в магнетитовой сус-пензии плотностью 1800-2000 кг/м3 и рссортировку обога-щенного угля на товарные сорта по крупности. 3.Отсев (<6мм) рядо-вого угля используется без обогащения. |
Все технологические схемы предусматривают обезвоживание продуктов обогащения. Сгущение шлама и регенерацию суспензии.
В результате обогащения коксующихся углей получают низкозольные концентраты, используемые для коксования, высокозольный промпродукт, используемый как низкосортное топливо, и отходы (хвосты), сбрасываемые в отвал.
Список литературы
1. Авдохин, В. М. Обогащение углей. Т. 1. Процессы и машины: учебник для вузов. –М.: Изд-во «Горная книга», 2012. 424 с.
2. Абрамов, А. А. Переработка, обогащение и комплексное использование твердых полезных ископаемых. Т. 1. Обогатительные процессы и аппараты: учебник для вузов. – М.: Изд-во Моск. гос. горного унта, 2004. - 470 с.
3. Абрамов, А. А. Переработка, обогащение и комплексное использование твердых полезных ископаемых. Т. 1. Обогатительные процессы и аппараты: учебник для вузов. – М.: Изд-во Моск. гос. горного унта, 2001. - 411 с.
4. Авдохин В. М. Основы обогащения полезных ископаемых [Электронный ресурс]: Учебник для вузов. В двух томах. Т. 1. - М.: Горная книга, 2008. – 423 с. – Режим доступа: www.knigafund.ru
3. Авдохин В. М. Основы обогащения полезных ископаемых [Электронный ресурс]: Учебник для вузов. В двух томах. Т. 2. - М.: Горная книга, 2008. – 315 с. – Режим доступа: www.knigafund.ru
Интернет-ресурсы
1. Дробильное оборудование http://www.dromash.ru/hogging-machine.
2. Каталог оборудования для подготовительных процессов обогащения полезных ископаемых http://www.dromash.ru.
3. Каталог оборудования для вспомогательных процессов обогащения полезных ископаемых http://www.andritz.com/ep.
|
|
|
Дата добавления: 2021-06-02; просмотров: 710; Мы поможем в написании вашей работы! |
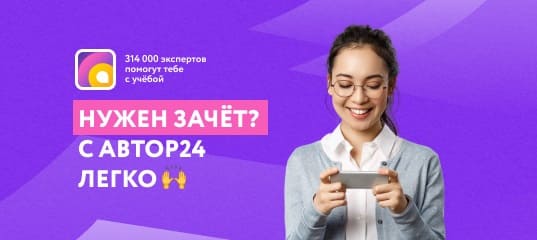
Мы поможем в написании ваших работ!