СУЩНОСТЬ ПРОЦЕССА РЕКТИФИКАЦИИ
Лекция 8
ВЫДЕЛЕНИЕ СПИРТА ИЗ БРАЖКИ И ЕГО ОЧИСТКА
СОСТАВ БРАЖКИ, ВИДЫ СПИРТА
Бражка — сложная многокомпонентная система состоящая из воды (82—90 мас.%), сухих веществ (4—10 мас.%) и этилового спирта с сопутствующими летучими примесями. (5—8 мас.%, или 6-10 об. %). Бражка всегда содержит некоторое количество диоксида углерода. В 1 л ее, взятом непосредственно из бродильного аппарата, находится 1—1,5 г СО,2. При перекачке бражки в ректификационное отделение-35—45% его теряется. Кислотность бражки — около 0,5°, рН 4,9—5,2. Состав бражки в значительной мере изменяется в зависимости от вида исходного сырья и принятых технологических режимов ее приготовления.
Сухие вещества бражки представлены как взвешенными частицами (дрожжевые клетки, шелуха, дробина), так и растворенными в водно-спиртовой смеси органическими и неорганическими веществами, (несброженные сахара, декстрины, белки, минеральные вещества и др.). Зерно-картофельная бражка содержит значительное-количество взвешенных частиц и обладает большей вязкостью, чем мелассная, однако общее содержание сухих веществ в мелассной бражке обычно больше (8—10 мас.%), чем в зерновой (5—7%) и особенно в картофельной (3—4%).
Летучие примеси, сопутствующие спирту, отличаются, большим разнообразием. В настоящее время их идентифицировано более 70, но общее содержание невелико и обычно не превышает 0,5% от содержания этилового спирта.
|
|
Все летучие примеси можно в основном разделить на четыре группы: спирты, альдегиды, кислоты и эфиры. Кроме того, выделяют группу азотистых соединений (аммиак, амины, аминокислоты), серосодержащих соединений (сероводород, сернистый ангидрид, сульфокислоты, меркаптаны) и некоторые другие вещества.
Состав и содержание летучих примесей зависят от вида и качества сырья, от принятых технологических режимов его переработки. Примеси частично переходят из сырья, воды, вспомогательных материалов, частично образуются в процессе приготовления сусла, однако большая часть их появляется в процессе брожения.
Наибольшее количество примесей (0,35—0,45% к количеству этилового спирта) приходится на долю спиртов — метилового, пропилового, изобутилового, изоамилового. Последние три спирта составляют основу сивушного масла (обычно 0,3—0,35% к количеству этилового спирта в бражке). Метиловый спирт содержится в зерно-картофельной и свекловичной бражке — не более 0,2% к количеству этилового спирта.
Содержание летучих кислот (уксусная, масляная; пропионовая, валериановая и др.) невелико — около 0,005—0,1% к количеству этилового спирта.
Основное количество альдегидов приходится на долю уксусного. Содержание альдегидов в мелассной бражке значительно (около 0,05% количеству этилового спирта) и в 10—50 раз превышает их содержание в зерно-картофельной бражке. Содержание альдегидов в бражке резко возрастает при усиленной аэрации сусла в процессе дрожжегенерирования. В бражке содержится около 0,05% эфиров к количеству этилового спирта. Группа эфиров в основном представлена уксусноэтиловым, муравьиноэтиловым, уксуснометиловым, изомасляноэтиловым.
|
|
Спирт из бражки выделяют с помощью ректификации на сырцовых ректификационных установках. При этом вместе с ним отгоняется и значительная часть сопутствующих летучих примесей. Получаемый продукт называется спиртом-сырцом (ГОСТ 131—67).
Ректификованный спирт получают путем очистки спирта-сырца от указанных примесей, ректификацией на брагоректификационных установках. Различают три вида ректификованного спирта (ГОСТ 5962—67): экстра, высшей очистки, I сорта.
Помимо спирта-сырца и ректификованного спирта спиртовой промышленностью вырабатывается в небольших количествах абсолютный спирт. Не следует смешивать понятия: безводный (100%-ный) и абсолютный спирт. В последнем допускается содержание воды до 0,2 об.%. Безводный спирт промышленностью не вырабатывается.
|
|
ПОЛУЧЕНИЕ СПИРТА-СЫРЦА
ФАЗОВОЕ РАВНОВЕСИЕ В СИСТЕМЕ ЭТАНОЛ — ВОДА
Летучесть отдельных компонентов смеси характеризуют коэффициентом испарения (К= Y / X ) —отношением концентрации данного вещества в паровой фазе Y к концентрации его в жидкой фазе X при равновесном состоянии фаз.
Летучая часть бражки состоит в основном, из воды и этилового спирта, поэтому в процессе выделения спирта бражку рассматривают как бинарную смесь этилового спирта и воды. Зависимость между составом паровой и жидкой фазы летучих веществ определяется законами Д. П. Коновалова и М. С. Вревского.
В верхней части рис. 1 линия /изображает зависимость равновесного состава пара У от состава жидкости X при атмосферном давлении и температуре кипения для смеси этиловый спирт — вода. Она представляет собой геометрическое место точек значений коэффициентов испарения этилового спирта Kэ.c = Y/X из водно-спиртовой смеси. При малых концентрациях спирта в смеси значения Kэ.c максимальны (около 13), при больших — минимальны (около 1).
Рис. 1 Зависимость равновесного содержания пара. Температуры кипения и упругости пара от концентрации водно-спиртового раствора при давлении:
|
|
1 – атмосферное; 2 – ниже атмосферного; 3 – выше атмосферного.
Линия равновесного состава в точке А пересекает диагональ, следовательно, в этой точке состав паровой и жидкой фазы одинаковый. Эта точка получила название азеотропной точки, или точки нераздельного кипения. Для нее Y = X , или Kэ.c = 1. При нормальном давлении нераздельнокипящая смесь системы этиловый спирт - вода содержит 97,2 об.% (95,57 мас.%) этилового спирта при температуре кипения 78,15°С; при том же давлении температура кипения этилового спирта равна 78,3°С, а воды 100°С.
В соответствии с законом Вревского при повышении давления растворы с низкой концентрацией спирта, примерно до 30— 40 мас.%, образуют пары с большим содержанием спирта, а растворы с высокой концентрацией спирта — пары с меньшим содержанием спирта, что наглядно показано в верхней части рис. 1 пунктирной линией. Из рисунка также видно, что с изменением давления сдвигается и положение азеотропной точки. Так, при давлении 93 кПа (температура кипения 27°С) нераздельнокипящая точка смещается вправо вплоть до Х= 100, т. е. при этом давлении пар всегда будет иметь большую концентрацию спирта, чем исходная жидкость (вплоть до 100%).
Анализируя положение кривой фазового равновесия, легко установить, что при атмосферном давлении пары над жидкостью будут обогащаться этиловым спиртом только до азеотропной тонки. Следовательно, путем ректификации (многократного испарения и конденсации) при атмосферном давлении можно достигнуть максимальной крепости спирта 97,2 об. %. Чтобы получить спирт большей крепости, необходимо уменьшить давление; тогда азеотропная точка сдвинется вправо, т. е. в область требующейся крепости. Этим приемом иногда пользуются на практике при получении абсолютного спирта.
Фазовое равновесие в бинарной смеси, этиловый спирт — вода при атмосферном давлении изучено В. Н. Стабниковым и О. Г. Мудравской. По их данным строят график фазового равновесия, который широко применяют для расчета процесса ректификации и анализа работы ректификационных колонн. В ряде случаев возникает необходимость иметь аналитическую зависимость указанного равновесия, которая по тем же данным установлена П. С. Цыганковым (табл.1).
Таблица 1.
Интервалы концентраций,мол. % | Уравнения для Y, мол. % | |
0—23 | Х/(0,014595 + 0,0773) | |
23—55 | 0,395 Х + 45,52 | |
55-66,5 | 0,5087Х + 39,27 | |
66,5—82 | 0,6548X +29,56 | |
82—89,4- . | 0,8113Х + 15,08 |
Наличие сухих веществ в водно-спиртовых растворах, как показано работами С. Е. Харина и В. М. Перелыгина, немного увеличивает концентрацию спирта в парах, однако в практических расчетах обычно пользуются кривой фазового равновесия для чистых водно-спиртовых растворов.
СУЩНОСТЬ ПРОЦЕССА РЕКТИФИКАЦИИ
Ректификация применяется для разделения жидких смесей на компоненты или фракции, различающиеся летучестью, (фугитивностью), и осуществляется путем многократного двустороннего массо-и теплообмена между противоточно движущимися паровым и жидкостным потоками — флегмой.
Взаимодействие фаз при ректификации представляет собой диффузию легколетучего компонента (л.л.к.) из жидкости в пар и труднолетучего компонента (т.л.к.) из пара в жидкость. Способ контактирования потоков может быть ступенчатый (в тарельчатых колоннах) или непрерывный (в насадочных колоннах).
Назначение контактных устройств (тарелок, насадки) состоит в создании условий, способствующих максимальному приближению парового и жидкостного потоков. Чтобы эти потоки могли обмениваться веществом и энергией, они должны быть неравновесны друг к другу. При контактировании парового и жидкостного потоков в результате массо- и теплообмена величина неравновесности уменьшается затем потоки отделяются один от другого, и процесс продолжается путем нового контактирования этих фаз уже на другой смежной ступени, с другими жидкими и паровыми потоками. В результате многократно повторяющегося на последовательных тарелках (ступенях), контактирования движущихся в противотоке по высоте колонны жидкости и пара состав взаимодействующих фаз существенно изменяется: паровой поток при движении вверх обогащается л.л.к., а жидкостный, стекая вниз, обедняется им, т. е. обогащается т.л.к. При достаточно большом пути контактирования противоположно движущихся потоков можно получить пар, выходящий из верхней части колонны, представляющий собой более или менее чистый л.л.к., конденсация которого дает дистиллят, а из нижней части колонны — сравнительно чистый т.л.к., так называемый кубовый остаток.
Флегма образуется в результате частичной конденсации паров, выходящих из верхней части колонны, в специальных теплообменных: аппаратах — дефлегматорах — или вводится в колонну в виде питания. Для создания парового потока в колонне в ее нижнюю часть вводят определенное количество тепла непосредственным впуском греющего пара (случай открытого обогрева колонны) или подачей его в специальный теплообменник, через поверхность теплопередачи которого тепло передается кипящему кубовому остатку (случай закрытого обогрева).
Чаще разделяемую смесь (питание) в жидком, парообразном или смешанном виде подают в середину колонны (рис. 2) между
Рис. 2 Схемы ректификационных колон
1 – дефлегматор; 2 – колонна; А – разделяемая смесь; в – вода; Д – дистиллят; П – пар; О – остаток.
концентрационной, или укрепляющей и отгонной, или исчерпывающей частью колонны. Верхнюю тарелку отгонной части колонны называют питающей тарелкой. Колонна, имеющая концентрационную и отгонную части, называется полной ректификационной колонной (рис. 2а). В такой колонне создаются наиболее благоприятные условия для получения в практически чистом виде обоих компонентов бинарной смеси, однако возможно и самостоятельное действие отгонной и концентрационной колонны. Такие колонны именуют неполными. Из нижней части неполной отгонной колонны (рис. 2б) в жидком виде отводится практически чистый т.л.к., над верхней тарелкой получается пар, несколько обогащенный л.л.к. В неполную концентрационную колонну, (рис. 2в) разделяемую смесь вводят в парообразном виде под ее нижнюю тарелку. Из верхней части концентрационной колонны отводят в парообразном, виде практически чистый л.л.к., а с нижней тарелки получается флегма, несколько обогащенная т.л.к. В отличие от полной ректификационной колонны в неполных колоннах для дальнейшего обогащения дистиллята отгонной колонны л.л.к. или остатка концентрационной колонны т.л.к. нужна их дополнительная ректификация.
Орошение флегмой, необходимое для осуществления процесса ректификации, в отгонных колоннах достигается подачей питания в жидком виде на верхнюю тарелку. В полных и укрепляющих колоннах орошение проводят за счет части конденсата пара, выходящего из верхней части колонны. Остальной пар образует дистиллят — верхний продукт колонны, поэтому орошение и отбор дистиллята количественно связаны между собой.
Отношение количества горячего (при температуре конденсации) орошения или флегмы ( L ) к количеству дистиллята ( D ) называется флегмовым числом ( R ):
R = L / D = ( G — D )/ D ,
где G — количество пара, выходящего из колонны.
Флегмовое число может изменяться от 0 до ∞. При R=0 не будет массообмена и обогащения пара л.л.к. При R =∞ весь конденсат паров, выходящий из колонны, полностью поступает на орошение; в этом случае отбор дистиллята равен нулю, колонна работает «на себя» (при установившемся процессе нижний продукт колонны будет иметь тот же состав, что и исходное питание). Практически колонна должна работать при 0<R<∞.
Отбирать дистиллят можно после частичной или полной конденсации пара (рис. 3)г. В 1 варианте обеспечивается дополнительное обогащение дистиллята л.л.к. вследствие частичной конденсации пара и массообмена между флегмой и паром при противоточном движении их в дефлегматоре. Во 2варианте пар, выходящий из колонны, дистиллят и флегма имеют одинаковый состав, и дефлегматор не дает никакого укрепляющего эффекта. В спиртовой промышленности обычно используют первый вариант.
Рис. 3. Способы орошения колонн: 1 — дефлегматор; 2 — колонна; 3 — конденсатор.
Тепло конденсации пара обычно отводят водой, продуктами, подлежащими нагреванию, или воздухом в специальных воздушных дефлегматорах.
Открытый обогрев колонн применим в том случае, когда греющий пар не оказывает отрицательного влияния на качество конечных продуктов, не взаимодействует с продуктами ректификации и не образует новых, трудноразделимых систем в колонне. При открытом обогреве конденсат греющего пара смешивается с конечным продуктом разделения (остатком). Закрытый обогрев требует наличия пара более высоких параметров.
Процесс массообмена между паровым и жидкостным потоками на контактных устройствах определяется величиной поверхности контакта фаз (Fm2), средней разностью концентраций, или средней движущей силой процесса (∆Скг/кг), и коэффициентом массопередачи, отнесенным к 1 м2 поверхности фазового контакта [Ккг/(м2*ч)]. Коэффициент массопередачи зависит от природы вещества и гидродинамического режима контакта фаз. Количество вещества, перешедшего из одной фазы в другую (в кг/ч), определяется равенством
М=К*F*∆C
Конструкция контактного устройства должна обеспечивать возможно большую величину массообмена на нем. Это достигается в первую очередь созданием развитой поверхности контакта фаз. Тарелки ректификационных колонн могут быть колпачковые, решетчатые, чешуйчатые, клапанные и др. (рис. 4). Насадочная колонна представляет собой цилиндр, наполненный насадкой — телами с развитой поверхностью (кольца, шары, седла, сетки, блоки, пакеты, рейки и т. д.). Пар и жидкость контактируют на поверхности насадки при противоточном движении.
Работа контактных устройств оценивается пропускной способностью по пару и жидкости, способностью разделять рабочую смесь, диапазоном устойчивой работы, гидравлическим сопротивлением и др.
Пропускная способность по пару и жидкости определяет производительность колонн, или удельный съем конечного продукта с единицы поперечного сечения колонн.
Способность разделять перегоняемую смесь называют эффективностью контактного устройства или колонны в целом и обычно оценивают числом теоретических тарелок (ступеней изменения концентраций), или числом единиц переноса. Эффективность тарельчатых колонн, как правило, оценивают числом теоретических тарелок (т.т.).
Рис. 4. Типы тарелок:
a — ситчатые (чешуйчатые): 1 — сосливными стаканами; 2 —без стаканов (решетчатые); б— колпачковые: 1 — одноколпачковые,;. 2 — многоколпачковые и клапаны клапановых тарелок; в: 1 —- круглые; 2 — прямоугольные.
Допустим, поступающая на тарелку жидкость (рис. 5, а) содержит Xi+1л.л.к., а покидающая ее — X*i; проходящий через тарелку пар соответственно содержит Yi и у*i+1 того же компонента. Если тарелка обеспечивает контакт пара и жидкости, в результате которого покидающие тарелку пар Y*.i+1 и жидкость Х*i будут равновесны, то такая тарелка имеет эффективность, равную одной теоретической тарелке.
Рис. 5. теоретическая тарелка в диаграмме Х-Y
Практически такое равновесие почти никогда не достигается. Теоретическая тарелка является идеальной тарелкой и служит эталоном для оценки эффективности реальных тарелок.
Мерой эффективности реальной, или действительной, тарелки является коэффициент полезного действия (КПД) ее. В практике определяют КПД не отдельной тарелки, а средний КПД тарелок всей колонны или значительного ее участка, который равен отношению числа тарелок (п),. необходимых для осуществления заданного разделения смеси, к числу реальных (N), необходимых для той же цели:
Величина КПД тарелок зависит от их конструкции, диаметра колонны, межтарелочного расстояния, скорости пара, загрузки колонны, физических свойств разделяемой смеси и многих других факторов, поэтому обычно КПД определяют опытным путем.
Эффективность работы насадочных колонн оценивают, числомединиц переноса, предъявляющим собой изменение концентрации в колонне, отнесенное к единице движущей силы. Чаще пользуются высотой насадки, эквивалентной одной единице переноса (ВЭЕП). Она изменяется в широких пределах в зависимости от конструкции и размера насадки, а также гидродинамического режима работы; колонны. Для мелкой насадки ВЭЕП может составлять несколько миллиметров, для крупной (обладающей высокой пропускной способностью по пару и жидкости) — 1—1,5 м.
В спиртовом производстве наибольшее распространение получили колпачковые (капсульные) тарелки. Многоколпачковые тарелки применяют в колоннах для разделения жидкостей, не содержащих взвешенных частиц, одноколпачковые— для разделения жидкостей со взвешенными частицами. Реже применяют ситчатые тарелки, которые имеют отверстия 2,5—3,5 мм (для разгонки первых из упомянутых жидкостей) и 8—12 мм (для вторых). В последние годы в спиртовой промышленности начали применять тарелки новых типов: решетчатые провальные (без сливных устройств), чешуйчатые и клапанные. Они обладают большей пропускной способностью по пару и жидкости.
При выборе типа тарелки учитывают ее удельную производительность, эффективность, экономичность конструкции, а также способность обеспечивать оптимальные условия работы колонны для заданного технологического режима.
Устойчивая работа тарелок должна соответствовать каким нагрузкам по пару и жидкости, при которых достигаются наиболее интенсивный их контакт и высокая эффективность. При больших нагрузках по пару может происходить большой унос жидкости с тарелки на тарелку, на тарелке может накапливаться жидкость сверх допустимого количества. Верхний предел нагрузки по пару характеризуется «захлебыванием» тарелок. Внешний признак захлебывания — резкое повышение давления в нижней части колонны и понижение давления в верхней. При нагрузках по пару, приближающихся к минимально допустимым, часть жидкости (флегмы) переходит с тарелки на тарелку, не вступая в контакт с паром. Большая нагрузка по жидкости также может привести к захлебыванию колонны. Максимально допустимая нагрузка по жидкости определяется количеством ее, необходимым для создания активной зоны контакта обменивающихся сред.
На работу тарелок большое влияние оказывает межтарелочное расстояние. Оно определяется в. первую очередь необходимостью создания условий для контакта пара и жидкости, происходящего в зонах барботажа, пены и брызг. Эти зоны расположены последовательно над тарелкой и должны вмещаться между смежными тарелками. Высота каждой зоны определяется физическими свойствами разделяемой жидкости, конструкцией тарелки, нагрузкой по пару и обычно находится опытным путем. При работе с жидкостями, дающими рыхлую пену, унос жидкости в основном происходит за счет хлопьев пены, обладающих высокой парусностью, Для колонн, перерабатывающих жидкости, не пенящиеся и не содержащие взвешенных частиц, обычно принимаемое межтарелочное расстояние 178—230 мм; для колонн, перерабатывающих жидкости со взвешенными частицами, — 280—500 мм.
Коэффициент полезного действия тарелок в силу различных условий эксплуатации колонн может изменяться в пределах 0,35— 0,65.
Дата добавления: 2021-05-18; просмотров: 114; Мы поможем в написании вашей работы! |
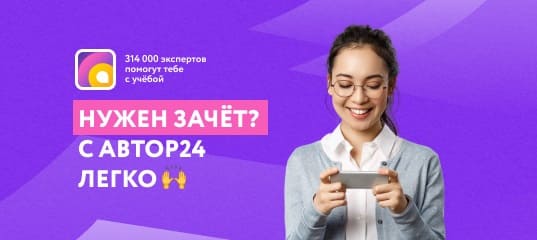
Мы поможем в написании ваших работ!