Использование аддитивных технологий при изготовлении сопел сварочных горелок
Современные информационные технологии
(курс лекций)
Аддитивные технологии
Основные методы и материалы
Аддитивные технологии в настоящее время являются одними из самых передовых и востребованных в мире.
Аддитивные технологии (Additive Manufacturing – от слова аддитивность – прибавляемый) – это послойное наращивание и синтез объекта с помощью компьютерных 3D технологий. Изобретение принадлежит Чарльзу Халлу, который в 1986 г. сконструировал первый стереолитографический трехмерный принтер.
Существует множество технологий, которые можно назвать аддитивными, их объединяет одно: построение модели происходит путем добавления материала (от английского аdd– добавлять) в отличие от традиционных технологий, где создание детали происходит путем удаления «лишнего» материала.
Классической и наиболее точной технологией является SLA-технология (от Stereolithography Apparatus), или стереолитография – послойное отвердение жидкого фотополимера лазером (рис.1).
Рис. 1. Пример изготовления формы для отливки: слева– литейная SLA-модель; справа–Al-отливка
Существует много видов фотополимерных композиций, поэтому спектр применения прототипов, полученных по SLA-технологии, очень широк: макеты и масштабные модели для аэро- и гидродинамических испытаний, литейные и мастер-модели, дизайн-модели и прототипы, функциональные модели и т. д.
Селективное лазерное спекание – SLS-технология (Selective Laser Sintering, Selective Laser Melting) – еще одно важное направление аддитивных технологий (рис.2). Здесь строительным (модельным) материалом являются сыпучие, порошкообразные материалы, а лазер является не источником света, как в SLA-машинах, а источником тепла, посредством которого производится сплавление частичек порошка. В качестве модельных материалов используется большое количество как полимерных, так и металлических порошков.
|
|
Рис.2. Пример деталей, изготовленных по SLS технологии (слева направо): функциональная полиамидная модель; полистирольная модель; инфильтрованная воском литейная модель
Порошкообразный полиамид применяется в основном для функционального моделирования, макетирования и изготовления контрольных сборок. Полистирол используется для изготовления литейных выжигаемых моделей.
Отдельным направлением является послойное лазерное спекание (сплавление) металлопорошковых композиций. Развитие этого направления AF-технологий стимулировало и развитие технологий получения металлических порошков. На сегодняшний день номенклатура металлических композиций имеет широкий спектр материалов на основе Ni и Co (CoCrMO, Inconel, NiCrMo), на основе Fe (инструментальные стали 18Ni300, H13; нержавеющая сталь 316L), на основе Ti (Ti6-4, CpTigr1), на основе Al (AlSi10Mg, AlSi12). Производятся порошки бронз, специальных сплавов, а также драгметаллов – главным образом для нужд дентальной медицины.
|
|
Из металлических порошков «выращивают» заготовки пресс-форм, специальные инструменты, оригинальные детали сложной конфигурации, которые трудно или невозможно получить литьем или механической обработкой – импланты, эндопротезы и пр. При штучном и мелкосерийном производстве зачастую становится экономически выгодным «вырастить» небольшую партию деталей на SLS-машине, чем изготавливать литейную или штамповую оснастку.
В сочетании с HIP (Hot Isostatic Pressing – горячее изостатическое прессование) и соответствующей термообработкой такие детали не только не уступают литым или кованым изделиям, но и превосходят их по прочности на 20–30%.
Большие перспективы открываются для еще одной аддитивной технологии – технологии струйной печати – InkJet- или PolyJet-технологии. Эта технология предполагает нанесение модельного материала или связующего состава с помощью струйных головок. Особый интерес InkJet-технологии представляют для литейного производства. Они позволяют «выращивать» непосредственно литейные формы, т. е. «негатив» детали, и исключить стадии изготовления формовочной оснастки – мастер-модели и литейной модели. Компания ExOne (и ее дочернее предприятие ProMetal GmbH) выпускает машины типа S-Max, которые позиционируются не как «прототипирующие машины», а как вполне рядовое индустриальное оборудование, устанавливаемое в общей технологической цепи производства выпуска не только опытной, но и серийной продукции. Практически все автомобильные компании мира обзавелись такими машинами. С их помощью стало возможным не в разы, а на порядок сократить время прохождения НИОКР по важным позициям – литейным деталям: блоки и головки цилиндров двигателей, мосты и коробки передач, деталям, на изготовление которых в традиционном опытном производстве тратились месяцы, а с учетом экспериментальной доводки и подготовки производства – многие месяцы. Теперь конструктор может увидеть свой новый двигатель на испытательном стенде не через полгода, а через две недели после завершения технического проекта.
|
|
Сегодня в России существует множество компаний, оказывающих услуги по прототипированию, однако в основном это небольшие предприятия, обладающие одним-двумя недорогими 3D-принтерами, способными выращивать несложные детали. Связано это с тем, что высокотехнологичное оборудование, способное обеспечить высокое качество изделий, стоит дорого и требует для работы и обслуживания квалифицированного, специально обученного персонала. Далеко не каждая компания может себе это позволить, ведь для покупки необходимо четко понимать, каким образом и насколько эффективно это оборудование будет использоваться, будет ли оно загружено работой. Слабостью таких компаний является отсутствие комплексности решения задач. В лучшем случае дело ограничивается оказанием достаточно простой услуги – изготовлением прототипа или модели тем или иным способом. Тогда как AF-технологии – это не только и не столько 3D-принтер, но важная часть 3D-среды, в которой происходит рождение нового продукта – от замысла конструктора до материализации его идей в серийном производстве. Среда, в которой новый продукт создается, «живет», эксплуатируется, ремонтируется вплоть до завершения «жизненного цикла» этого продукта.
|
|
Поэтому для полноценного использования AF-технологий нужно создать эту среду: освоить 3D-проектирование и моделирование, CAE- и САМ-технологии, технологии оцифровки и реинжениринга, сопутствующие технологии, включая и вполне традиционные, но переформатированные под 3D-среду. Причем осваивать аддитивные технологии следует не в отдельно взятом учреждении или фирме а в целой отрасли, например, авиационной или автомобильной. Тогда и AF-технологии будут выглядеть не экзотическими изысками, а вполне естественным и эффективным звеном общей 3D-среды создания, производства и жизненного цикла изделия.
На рынке существуют крупные компании, обладающие оборудованием высокого уровня, которые, как правило, решают достаточно сложные производственные задачи и оказывают широкий спектр полезных услуг, сопутствующих прототипированию, способных от начала до конца провести НИОКР и проконтролировать качество работ на каждом этапе. К таким предприятиям можно отнести ФГУП «НАМИ», АБ «Универсал», НПО «Салют», ОАО «НИАТ» (Москва), УМПО (Уфа), НИИ «Машиностроительные Технологии», СПбПУ, ОАО «Тушинский машиностроительный завод» и ряд других. Однако такой комплексный подход по силам далеко не каждому предприятию.
Рынок аддитивных технологий в России развивается, но происходит это очень медленно, поскольку, чтобы вывести эти технологии на должный уровень, необходима поддержка государства. При должном внимании к внедрению AF-технологий они могут значительно повысить скорость реагирования на потребности рынка и экономическую эффективность многих отраслей промышленности.
В настоящее время доступен широкий выбор методов аддитивного производства. Основные различия заключаются в методе нанесения слоев и используемых расходных материалах. Некоторые методы основываются на плавке или размягчении материалов для создания слоев: сюда входит выборочное лазерное спекание (SLS), выборочная лазерная плавка (SLM) (рис. 3), прямое лазерное спекание металлов (DMLS), печать методом послойного наплавления (FDM или FFF). Другим направлением стало производство твердых моделей за счет полимеризации жидких материалов, известное как стереолитография (SLA). В случае с ламинированием листовых материалов (LOM), тонкие слои материала подвергаются резке до необходимого контура, с последующим соединением в единое целое. В качестве материалов для LOM могут использоваться бумага, полимеры и металлы. Каждый из перечисленных методов имеет свои преимущества и недостатки, в связи с чем некоторые компании предлагают выбор расходного материала для построения модели – полимера или порошка. Принтеры, работающие по технологии LOM, зачастую используют обычную офисную бумагу для постройки прочных прототипов. Ключевыми моментами при выборе подходящего устройства являются скорость печати, цена 3D-принтера, себестоимость печатаемых прототипов, а также стоимость и ассортимент совместимых расходных материалов.
Рис. 3. Пример деталей, изготовленных по SLM технологии
Принтеры, изготавливающие полноценные металлические модели, имеют достаточно высокую стоимость, однако возможно использование менее дорогих устройств для производства литейных форм с последующей отливкой металлических деталей.
В качестве расходных материалов используются всевозможные полимеры, включая акрилонитрилбутадиенстирол (ABS), поликарбонат (PC), полилактид (PLA), полиэтилен высокого давления (HDPE), смеси поликарбоната и ABS-пластика, полифениленсульфон (PPSU) и др.
Как правило, полимер поставляется в форме наполнителя, изготовленного из чистого пластика.
В сообществе энтузиастов 3D-печати существует несколько проектов, направленных на переработку использованного пластика в материалы для 3D-печати. Проекты основаны на выработке расходных материалов с помощью шредеров и переплавляющих устройств.
Основные методы аддитивного производства представлены в табл. 1.
Технология FDM/FFF имеет определенные ограничения по сложности создаваемых геометрических форм. Например, создание навесных конструкций (таких, как сталактиты) невозможно само по себе, ввиду отсутствия необходимой поддержки.
Таблица 1
Основные методы аддитивного производства
Метод | Используемые материалы | Технология |
Экструзионный | Термопластики (такие как полилактид (PLA), акрилонитрилбутадиенстирол (ABS) и др.) | Моделирование методом послойного наплавления (FDM или FFF) |
Проволочный | Практически любые металлические сплавы | Производство произвольных форм электронно-лучевой плавкой (EBFȝ) |
Порошковый | Практически любые металлические сплавы | Прямое лазерное спекание металлов (DMLS) |
Титановые сплавы | Электронно-лучевая плавка (EBM) | |
Титановые сплавы, кобальт-хромовые сплавы, нержавеющая сталь, алюминий | Выборочная лазерная плавка (SLM) | |
Порошковые термопластики | Выборочное тепловое спекание (SHS) | |
Термопластики, металлические порошки, керамические порошки | Выборочное лазерное спекание (SLS) | |
Струйный | Гипс, пластики, металлические порошки, песчаные смеси | Струйная трехмерная печать(3DP) |
Ламинирование | Бумага, металлическая фольга, пластиковая пленка | Изготовление объектов методом ламинирования (LOM) |
Полимеризация | Фотополимеры | Стереолитография (SLA) |
Фотополимеры | Цифровая светодиодная проекция (DLP) |
Потенциал современных устройств для 3D печати достаточно огромен. Сейчас даже весьма простенький домашний настольный принтер может выполнить модель из пластика, точность воспроизведения которой составляет 100 микрон (рис. 4). Другими словами, это будет полная копия оригинала, которую человек будет не способен отличить от прототипа.
Технология «струйной печати», с использованием порошковых материалов разработана в Массачусетском Технологическом Институте. Первым и основным производителем оборудования такой технологии стала компания Z Corporation.
Рис.4. Домашние FDM принтеры
Суть технологии такова - специальная струйная головка, адаптированная из струйных принтеров Hewlett-Packard набрызгивает на порошковый материал клеящее вещество. В качестве порошка используется обычный гипс или крахмал. В забрызганных местах порошок склеивается и формирует модель. Печать, как и в предыдущих случаях, идет послойно, а лишний порошок в конце стряхивается. Однако есть и существенная разница - этот принтер может использовать клеящую жидкость с добавлением пигментных красителей - а значит, печатать цветные модели. В цветном принтере от Z Corporation установлены 4 струйные головки с клеящимися чернилами основных цветов, так что полученная модель может воспроизводить не только форму, но и окраску (то есть, текстуру) своего виртуального прототипа (рис. 5).
Рис. 5. Пример производственного аддитивного производства
Интересный вариант вышеописанной порошковой струйной печати разрабатывает компания ProMetal (рис.6). Ее фирменный производственный процесс под названием Direct Metal Process работает абсолютно аналогично. Только вместо гипсового порошка применятся порошок металлический. Далее сформованное изделие обжигается в печи, так что порошок либо сплавляется сам, либо связывается более легкоплавким металлом (как и при лазерном спекании металлических порошков). Это еще один метод непосредственного производства при помощи трехмерной печати.
Рис. 6. Деталь, изготовленная из металла по технологии ProMetal
Таким образом, перспективы перед 3D- печатью открываются самые оптимистичные. Эта технология позволяет экономить массу времени и сил дизайнерам и инженерам. Большие возможности аддитивных технологий откроются, когда она станет доступна на бытовом уровне или в виде недорогой услуги, т.к. можно будет изготовить любой придуманный и нарисованный на компьютере предмет.
Использование аддитивных технологий при изготовлении сопел сварочных горелок
Аддитивные технологии находят применение в различных отраслях промышленности, в том числе, сварочном производстве.
Изготовление сопелсварочных горелок со сложной формой внутренней поверхности можно выполнять по технологии лазерного запекания металлического порошка (SLS)илис использованием полимеров. Для изготовления сопла и других деталей выбрали метод струйной трехмерной печати (3DP). Этот метод прототипирования позволил на основе математической модели при помощи 3D-принтера получить послойно созданный прототип сопла горелки, обеспечивающее устойчивую защиту сварочной зоны при ветровых нагрузках. В качестве материала использовали термостойкий полибензоимидазол (PBI) и полиэфирэфиркетон (РЕЕК). С помощью такой технологии возможно производство литейных форм с последующей отливкой металлических сопел. Этот пластик обладает высокой температурной стойкостью (+310 °С постоянно и до +500 °С кратковременно), прочностью, низким коэффициентом теплового расширения. Для прототипирования сопла на кафедре «Теория и технология сварки материалов» СПбПУ разработали и собрали 3D принтер из готовых модулей на основе микроконтроллера, работающего по определенной компьютерной программе (Repetier-Host) (рис. 7).
Рис. 7. Модули для принтера: экструдер, микроконтроллер, плата
в сборе, драйвер, двигатель
Экструдер установлен на каретке, скользящей на двух цилиндрических валах, приводится в движение с помощью шаговых двигателей с ременной передачей. Горячий стол установлен на платформе с винтовым приводом и приводится в движение так же с помощью шагового двигателя (рис. 8).
Рис. 8. Вид 3D-принтера
Производственный цикл начинается с обработки трехмерной цифровой модели. Вначале вводятся исходные данные по разрабатываемому изделию. Расчёты и необходимая корректировка детали производятся без лишних финансовых затрат на эксперименты. Например, при производстве сопел из полимеров, по расчетам, произведенным с помощью программы, становиться известен вес, объём и время изготовления, а так же станет видно, в каком месте не соблюдается конфигурация образующей сопла (рис. 9).
Рис. 9. Программный анализ 3D-модели
Далее по информационным данным модели создаётся специальный код, который задаёт команды на движения и количество выдавливаемого из экструдера пластика, руководствуясь алгоритмом работы микропроцессора. После чего выдается полная информация о предстоящей работе и наглядный пример послойного формирования модели сопла (рис. 10).
Рис. 10. Программная визуализация изготовления модели сопла
Применение аддитивных технологий позволяет изготавливать сопла сварочных горелок сложной формы, например конфузорных, высокого качества при минимальной трудоёмкости.
Контрольные вопросы к разделу 1
1. Сущность аддитивных технологий.
2. Разновидности аддитивных технологий.
3. Назовите источники нагрева в аддитивных технологиях.
4. Что такое SLA-технологии?
5. Материалы, применяемые в аддитивных технологиях.
6. От чего зависит спектр применения прототипов, полученных по SLA-технологии?
7. Что представляет собой селективное лазерное спекание?
8. Какие существуют виды лазерного спекания?
9. Что представляют собой металлопорошковые композиции?
10. Сущность послойного лазерного спекания (сплавления) металлопорошковых композиций.
11. Представте пример деталей, изготовленных по SLS технологии
12. Преимущества и недостатки послойного лазерного спекания.
13. Какие достоинства технологии струйной печати – InkJet- или PolyJet-технологии?
14. Какие сдерживающие факторы препятствуют внедрению аддитивных технологий в России?
15. Какие расходные материалы используются в аддитивных технологиях?
16. Охарактеризуйте основные виды аддитивного производства.
17. Какие составные элементы аддитивного производства?
18. Назовите основные этапы аддитивных технологий.
19. Назовите основные узлы и элементы при использовании аддитивных технологий.
20. Альтернативой каких сварочных технологий могут быть аддитивные технологии.
21. Покажите возможность применения аддитивных технологий при изготовлении сварочного оборудования.
22. Покажите возможность применения аддитивных технологий при производстве сварочной оснастки.
23. Какие сложности получение композиционных покрытий при использовании аддитивных технологий?
24. В каких случаях целесообразно применять композиционные покрытия?
25. Назовите возможные сочетания наплавочных материалов при использовании композиционных покрытий.
Дата добавления: 2021-05-18; просмотров: 109; Мы поможем в написании вашей работы! |
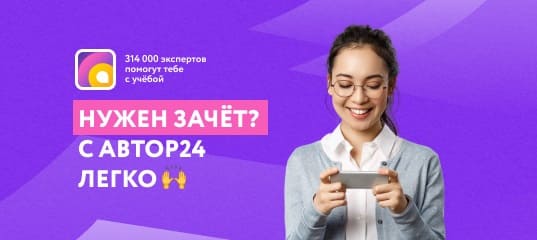
Мы поможем в написании ваших работ!