Опишите технологию с теоретическим обоснованием
Обеспечение необходимой дисперсности и заданных физико-механических свойств материала при использовании различных типов машин
Для производства лекарственных препаратов использует много способов и в этом процессе могут быть задействованы несколько производственных машин одновременно. Дисперсность материала имеет большое значение при выборе способа сушки и конструкции сушильного аппарата; она определяет физические и другие свойства материала.
О дисперсности материала достаточно полно можно судить по его удельной поверхности. Чем выше дисперсность материала, тем больше контактов между кристаллами.
Если степень дисперсности материала невелика, то лишь малая доля его вещества находится в состоянии поверхностных слоев, и она мало влияет на объемные свойства материала - весовой и молекулярный состав, теплоемкость, скорость объемных реакций. Но даже малое количество вещества в поверхностных слоях может сильно влиять на поверхностные свойства материала - внешнее трение, скорость гетерогенных реакций, прилипание, связность элементов структуры, и вообще на изменение дисперсной структуры материала.
Увеличение относительного объема поверхностных слоев с уменьшением величины частиц. Если степень дисперсности материала невелика, то объем вещества, находящегося в поверхностных слоях и обладающего своеобразными свойствами, мал по сравнению с объемом фазы. Поэтому свойства такого материала обусловлены объемными свойствами его фаз, и границы между ними можно считать геометрическими поверхностями, не имеющими толщины.
|
|
С увеличением диспергирования или естественной дисперсности материала подвижность частиц возрастает.
Существует оптимальная вязкость, зависящая от дисперсности материала и вязкости раствора, при которой достигается максимальная прочность.
Этапы приготовления препаратов из водной суспензии. Если имеют в виду статистическое определение дисперсности материала, то описанный способ удаления избытка суспензии при помощи фильтровальной бумаги непригоден, так как возможно, что частицы некоторого размера будут предпочтительно удерживаться на пленке. В этом случае необходимо дать возможность капле полностью испариться на пленке. Однако в процессе испарения капли в ней возникают микропотоки (в особенности, когда наиболее крупные частицы или их агрегаты возвышаются над уровнем жидкости и происходит испарение с их поверхности, смачиваемой за счет капиллярных сил), что приводит к взаимному притяжению частиц и образованию агрегатов.
Процесс спекания портландцементного клинкера происходит при постоянном изменении дисперсности материала.
|
|
Технологические режимы плазменного напыления определяются: видом и дисперсностью материала, током плазменной струи и его напряжением, видом и расходом плазмообразующего газа, диаметром сопла плазменной горелки и расстоянием от сопла до напыляемой поверхности.
Оптимальная влажность компостируемой массы варьирует и зависит от природы и дисперсности материала. Различные материалы могут иметь разную влажность до тех пор, пока поддерживается соответствующий объем свободного газового пространства.
Таким образом, для увеличения поверхности соприкосновения необходимо, во-первых, повысить дисперсность материала или пористость его кусков. Второй задачей является создание в аппарате таких условий, при которых вся или большая часть поверхности твердых частичек омывается потоком газа или жидкости.
Измельчение исходных компонентов является необходимой операцией, поскольку она обеспечивает достижение той дисперсности материала, которая соответствует особенностям принятого способа получения катализатора и отвечает требованиям к его свойствам. Измельчение производят в дробилках и помольных машинах.
|
|
Химическая устойчивость минералов зависит от состава, строения (конституции) и степени дисперсности материала, а также от характера среды и времени пребывания минералов в этой среде.
Экстраполяция к (нулевому значению константы скорости деструкции правомерна, поскольку в случае, когда дисперсность материала (возрастает и поверхность интенсивно обновляется, константа деструкции становится а несколько порядков выше, чем при усталостном режиме.
Неправильная, нитеобразная форма целлюлозных частиц не позволяет дать точную оценку размеров частиц, характеризовать дисперсность материала. Максимум кривых распределения приходится на интервал 50 - 100 мкм, диаметр частиц составляет 15 - 20 мкм.
Основными характеристиками дисперсности материалов следует считать удельную поверхность частиц порошка (в расчете на 1 г) и гранулометрический состав, который задается обычно в виде функции распределения частиц по фракциям.
Природа материала (гидрофильность), степень дисперсности, условия изготовления и продолжительность хранения влияют на содержание влаги и летучих. Чем выше степень дисперсности материала, тем более развитой поверхностью он обладает и, следовательно, тем выше его сорбционная способность. Этим объясняется повышенная склонность тонкодисперсных порошков к увлажнению и наличие в них большего количества адсорбированного газа и примесей других веществ, поглощенных из окружающей среды в процессе их изготовления или хранения. Содержание летучих в полимерах зависит от наличия в сырье остаточного мономера и низкокипящих пластификаторов, которые при температуре переработки переходят в газообразное состояние.
|
|
При низких температурах преобладает второй фактор, а при высоких - первый. Очевидно, что чем выше дисперсность материала и, следовательно, чем больше контактов между кристаллами, тем сильнее проявляется второй фактор.
В результате механохимической активации повышается не только дисперсность материала, но и реакционная способность, выражаемая в приросте гидравлической активности на 30 - 40 МПа.
Для повышения пластичности глин их подвергают вылеживанию во влажном состоянии в помещениях (влажных подвалах), на воздухе (вымораживанию), а также пропариванию. Вылеживание и пропаривание способствуют разрыхлению и увеличению дисперсности материала. Практикуется также добавка к тощим глинам более пластичных глин или же различных коллоидальных веществ (декстрин, крахмал и пр.)
Столь широкие диапазоны колебаний величин, определяющих качественно однозначные понятия, свидетельствуют лишь о том, что классификация измельчителей по дисперсности не учитывает прочности измельчаемого материала. Это является следствием отсутствия физико-механического обоснования классификации измельчителей по дисперсности материала. Аналогичные феноменологические классификации по тому или иному внешнему признаку, не связанному органически с энергетикой, конструкцией и областью применения измельчителя, являются произвольными И могут быть построены в различных вариантах.
Столь широкие диапазоны колебаний величин, определяющих качественно однозначные понятия, свидетельствуют лишь о том, что классификация измельчителей по дисперсности не учитывает прочности измельчаемого материала. Это является следствием отсутствия физико-механического обоснования классификации измельчителей по дисперсности материала. Аналогичные феноменологические классификации по тому или ному внешнему признаку, не связанному органически с энергетикой, конструкцией и областью применения измельчителя, являются произвольными и могут быть построены в различных вариантах.
Опишите технологию с теоретическим обоснованием
Возьми: Кодеина 0.01
Натрия гидрокарбоната
Терпина гидрата поровну по 0.25
Смешай, получи порошок.
Дай таких доз числом 12.
Обозначь: по 1 порошку 2 раза в день.
Процесс изготовления порошков состоит из следующих основных стадий: измельчения и просеивания, смешивания (при изготовлении сложных порошков), дозирования и упаковки. Необходимость выполнения тех или иных технологических стадий или операций зависит от рецептурной прописи, медицинского назначения и вида исходных препаратов. В соответствии с этими факторами к порошкам предъявляются различные требования в отношении степени размельчения, способа приготовления, упаковки и отпуска.
Помимо своего состава и способа назначения, порошки отличаются друг от друга также агрегатным состоянием (кристаллические и аморфные), плотностью, твердостью, цветом, запахом и другими свойствами.
Порошки животного и растительного происхождения, как правило, являются аморфными и отличаются от порошков минерального происхождения меньшей плотностью.
Некоторые вещества, прописываемые в порошках, изменяются под воздействием света, кислорода, углекислоты и влаги воздуха (аминазин, апоморфина гидрохлорид, ртути окись желтая, кортизона ацетат и др.), гигроскопичны (адреналина гидрохлорид, натрия хлорид, мочевина, гексаметилентетрамин и др.), достаточно легко теряют кристаллизационную воду (натрия сульфат, магния сульфат), летучи (камфора, ментол, хлоралгидрат, фенил салицилат и др.).
Иногда в результате смешивания нескольких порошкообразных веществ могут иметь место химическое взаимодействие между ними, изменение ряда вышеперечисленных физических свойств состава, в некоторых случаях образование взрывоопасных смесей и т.д.
Основной целью стадии измельчения является достижение более быстрого и полного терапевтического эффекта за счет уменьшения размера частиц и увеличения их количества. Кроме того, тонкоизмельченные вещества лучше смешиваются, меньше расслаиваются при дозировании, а при рассматривании невооруженным глазом в смеси таких веществ не обнаруживаются отдельные частицы ингредиентов, наличие которых в соответствии с указаниями ГФ недопустимо. Скорость и полнота всасывания лекарственного вещества, его концентрация и время пребывания в организме в значительной мере зависят от размера частиц.
Если порошки содержат частицы разного размера, то являются полидисперсными, если частицы имеют одинаковый размер - монодисперсными. Монодисперсных порошков практически не существует, имеются лишь некоторые препараты, по составу приближающиеся к таковым (например, ликоподий (споры плауна)).
Основной задачей просеивания является получение продукта с как можно более сходным размером частиц. В аптечной практике эта технологическая стадия используется крайне редко. В большинстве случаев просеивают лишь измельченное лекарственное растительное сырье. Для этих целей чаще всего используют сита №61 (0,1 мм) и №38 (0,16 мм). Первое применяют в основном при просеивании материала для глазных порошков, присыпок и порошков для вдуваний, второе - для большинства остальных порошков. До 0,16 мм (сито №38) измельчают вещества, для которых не указана степень дисперсности. Для просеивания используют стандартные наборы сит с ободками диаметром 150-200 мм. Сита могут закрываються крышками, что особенно важно при работе с ядовитыми и легко распыляющимися веществами. Крышку рекомендуется открывать не сразу после просеивания, а спустя 20-30 с, так как за это время пыль внутри сита успевает осесть.
Смешивание осуществляют для получения однородной порошковой смеси.
Его, как правило, производят одновременно с измельчением в ступке, аппарате М.X. Исламгулова или других аппаратах, используемых для этой цели.
При смешивании измельченных лекарственных веществ (т.е. при производстве сложных порошков) вращение пестика должно осуществляться с меньшим давлением на дно и стенки ступки, чем при порошковании. Процесс следует производить при частом собирании порошка со стенок ступки и пестика пластмассовой пластинкой до получения однородной смеси. Однородность проверяется следующим образом: при надавливании пестиком на смесь не должно обнаруживаться отдельных частиц. Если ингредиенты сложного порошка выписаны в равных или приблизительно равных количествах, в зависимости от свойств лекарственных веществ возможны несколько вариантов порядка их смешивания. В случае, когда составные части порошковой смеси имеют приблизительно одинаковые физические свойства (плотность, кристаллическую структуру и др.) при их смешивании следует учитывать, какое из веществ больше втирается в поры ступки.
Дозирование порошковых смесей осуществляют либо по массе, либо по объему.
Наиболее распространено дозирование по массе. Этот метод более точен, чем дозирование по объему. Необходимы ручные аптечные весы, чашки которых до начала работы протирают ватой, смоченной этанолом или смесью этанола с эфиром. Процесс дозирования заключается в следующем: порошок из ступки насыпают на чашку весов с помощью ложечки из пластмассы. После развешивания его высыпают из чашки в капсулу. По завершении работы чашки весов вытирают стерильными марлевыми салфетками или ватными тампонами.
Дозирование по объему менее точно, однако отличается большей производительностью. Используют специальные дозаторы, предназначенные для объемного дозирования сыпучих лекарственных веществ в дозах от 0,1 до 2,0 г.
Возьми: Кодеина 0.01
Натрия гидрокарбоната
Терпина гидрата поровну по 0.25
Смешай, получи порошок.
Дай таких доз числом 12.
Обозначь: по 1 порошку 2 раза в день..: Codeini 0,01hydrocarbonas 0,25Hydrate 0,25. f. pulvisin partes aequales №12. По 1 порошку 2 раза в день.
Потери кодеина в незатертых ступках №2 или №3 составляют 0,14 мг (приблизительно 8%). В максимальном количестве в данном рецепте выписан натрия гидрокарбонат, потери которого составляют около 3,5%.
Поэтому вначале в ступке №2 или №3 измельчают 1,8 г натрия гидрокарбонат, высыпают его в капсулу, оставив столько, сколько примерно равно массе ингредиента, выписанного в рецепте в наименьшем количестве, т.е. кодеина. В ступку помещают 0,01 г. кодеина, перемешивают, добавляют 0,25 г. терпина гидрата и дробно 0,25 г. натрия гидрокарбоната. Перемешивают, дозируют по 0,1 г в вощеные капсулы.
Дата добавления: 2021-04-24; просмотров: 70; Мы поможем в написании вашей работы! |
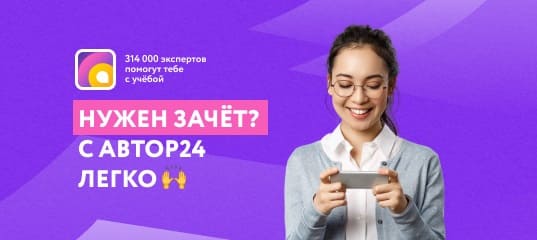
Мы поможем в написании ваших работ!