Опишите процесс азотирования стали. Укажите его достоинства и область применения
выплавка сталь азотирование кристаллический
Азотирование стали впервые предложено акад. Н.П. Чижевским. Процесс азотирования стальных деталей заключается в поверхностном насыщении азотом в среде аммиака (NH3) при температурах нагрева 500-700° С в течение 20-90 ч. Глубина азотированного слоя допускается в пределах 0,2-0,8 мм.
Азотирование применяется для повышения твердости, износостойкости, предела усталости, сопротивления коррозии и жаропрочности.
Азотированию могут подвергаться детали из углеродистой низко-легированной и легированной сталей, а также чугун.
Детали из углеродистой и низколегированной стали азотируют для увеличения сопротивления коррозии. Твердость азотированной. поверхности у них не превышает HV 250-300.
Азотирование может быть низкотемпературным (500-600˚С) или высокотемпературным (600-1200˚С). Термическая диссоциация аммиака представляет собой ионизационный процесс, сопровождающийся образованием ионов в рабочем пространстве печи. Азотированию подвергаются стали перлитного, ферритного и аустенитного классов, а также чугуны и другие сплавы. В результате азотирования сталь приобретает высокую твердость на поверхности, не изменяющуюся при нагреве до 400-450˚С; высокую износостойкость и низкую склонность к задирам; высокий предел выносливости; высокую кавитационную стойкость; хорошую сопротивляемость коррозии в атмосфере, пресной воде и паре
|
|
Технологический процесс изготовления деталей при применении азотирования состоит из следующих этапов:
) предварительная термическая обработка заготовки;
) механическая обработка детали, включая шлифование;
) защита мест, не подлежащих азотированию (покрытие тонким слоем олова гальваническим способом);
) азотирование;
) окончательное шлифование или доводка в соответствии с заданными допусками.
Легированные стали с содержанием хрома, никеля, алюминия и молибдена после азотирования имеют поверхностную твердость HV 850-1200 (рис. 37). Это достигается за счет образования мелкодисперсных нитридов на поверхности детали (химических соединений азота с элементами AlN, GrN, Cr2N, MoN).
Достоинство азотированного слоя - сохранение высокой твердости при нагреве до высоких температур.
Эта особенность азотированного слоя расширяет область применения азотирования и дает хорошие результаты в борьбе с износом деталей, работающих при повышенных температурах.
Снижение хрупкости азотированного слоя позволяет применять азотирование при изготовлении деталей, имеющих острые кромки и вырезы, а также нешлифуемых деталей. Так, например, в станкостроении для шпинделей, опор качения и ходовых винтов используют стали 40Х, 40ХФА, 18ХГТ, а для гильз, накладных направляющих планок, ходовых винтов пар качения - стали 40ХФА, 20ХЗВА, 20ХЗМВФ.
|
|
Опишите сущность модифицирования чугунов. Укажите свойства модифицированных чугунов, их маркировку и область применения
Применяемые способы сфероидизирующей обработки условно можно разделить на четыре группы: модифицирование в форме, модифицирование в специальной реакционной камере, модифицирование в ковше и обработка чугуна модифицирующей проволокой.
Чугуны - это наиболее широко применяемый материал для литых деталей, используемых при относительно невысоких напряжениях и малых динамических нагрузках. Температура плавления чугунов значительно ниже, чем у стали на 300-400°С, что облегчает процесс литья.
Чугун с графитом как мягкой и хрупкой составляющей, хорошо обрабатывается резанием (образованием ломкой стружки) и получают более чистую поверхность, чем сталь (кроме автоматных). Чугуны имеют повышенное содержание углерода (2,2 - 4%) и кремния (0,8 - 2%) - элементов соответствующих графитизации. Однако в марках чугуна химический состав не указывается. Структура и свойства чугунов зависят главным образом от условий получения отливки (температура жидкого металла, введение модификаторов, и особенно значительно, от условий охлаждения при литье). Поэтому, при одинаковом химическом составе, чугун может иметь сильно отличающуюся структуру и свойства (например, белый или серый чугун).
|
|
Ферритно-перлитные СЧ18; СМ20 - станины станков и механизмов, поршни, цилиндры.
Перлитные СЧ25, СЧ30, СЧ35 - детали, работающие на износ (тормозные барабаны, цилиндры, шестерни).
Серый чугун - в структуре серых чугунов присутствует графит пластической формы. Отливки из этого чугуна получают в земляных и металлических формах, кокилях. С увеличением толщины отливки и, следовательно, с замедлением охлаждения и при повышенном содержании кремния образуется больше графита и его пластины крупнее, а в металлической основе возрастает количество феррита. Однако их механические свойства (особенно пластичность) ниже, чем у других чугунов с графитом. Серый чугун используют для менее ответственного назначения и при отсутствии ударных нагрузок.
Ферритные: СЧ10, СЧ15 - используют детали неответственного назначения (крышки, шкивы и т.п.).
Ковкий чугун - имеет в структуре графит хлоповидной формы и в связи с этим более высокие механические свойства, прежде всего пластичность. Все ковкие чугуны содержат меньше кремния. Ковкие чугуны используются более целесообразно использовать для тонкостенных деталей.
|
|
Ферритные КЧ 35-10; КЧ 37-2 - фланцы, муфты.
Ферритно-перлитные КЧ 45-7 - задний мост, картер автомобиля, ступицы.
Высокопрочный чугун - имеет графит шаровидной формы, что в меньшей степени нарушает сплошность металлической основы. Прочные свойства этих чугунов наиболее высокие, отступают в прочности углеродистым конструкционным стилям, подверженным термической обработке, но пластичность высокопрочных чугунов ниже, чем у стали и у ковкого чугуна. Использование в промышленности высокопрочных чугунов, главным образом для массивных отливок из-за повышенных механических свойств возрастает за счет серых чугунов.
Ферритный: ВЧ 50-70 - траверсы прессов, фланцы, цилиндры, шестерни.
Перлитный: ВЧ 80-2 - цилиндры, поршни.
Отбельный чугун - имеет в сердцевине структуру серого или высокопрочного чугуна, а в поверхностном слое повышенной твёрдости (HB 450-500) ледебурит и персит. Отбельный чугун используют в ограниченных пределах для деталей простой формы, получающих твёрдую поверхность при литье.
Используют прокатные балки, рабочие части различного оборудования, колёса неответственного назначения.
Белый чугун - имеет структуру персита и цементита по всему сечению и, как правило, доэвтектический. При высокой износостойкости и твёрдости, но плохой обрабатываемости резанием белые чугуны имеют сильно сниженные механические свойства и почти не применяются.
Дата добавления: 2021-04-24; просмотров: 90; Мы поможем в написании вашей работы! |
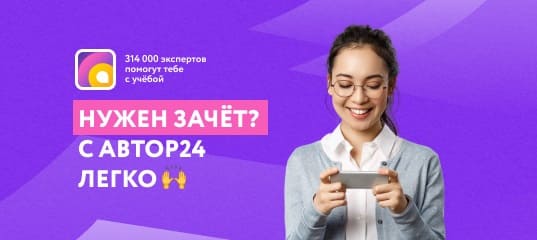
Мы поможем в написании ваших работ!