Классификация и их характеристика
К высоколегированным сталям относят сплавы, содержащие более 45% железа, суммарное количество легирующих элементов в которых составляет не менее 10% при содержании одного из элементов не менее 8%.
В зависимости от основных свойств и назначения высоколегированные стали подразделяют на следующие группы: коррозионно-стойкие, обладающие стойкостью против электрохимической коррозии (влажной атмосферной, почвенной, щелочной, кислотной, солевой, морской и др.), в том числе против межкристаллитной коррозии под напряжением, питтинговой (точечной) коррозии и др.; жаростойкие (окалиностойкие), обладающие стойкостью против химического разрушения (коррозии) их поверхности в газовых средах (в том числе в сухой воздушной атмосфере) при температурах выше 550 °С, работающие в ненагруженном или слабонагруженном состоянии; жаропрочные, работающие в нагруженном состоянии при высоких температурах в течение определенного гарантированного времени и обладающие при этом достаточной окалиностойкостью.
Все эти стали, как правило, коррозионностойки в атмосферных условиях, поэтому их часто называют общим названием - нержавеющие.
Самостоятельную группу, хотя и не предусмотренную стандартом, составляют хладостойкие высоколегированные стали и сплавы, сохраняющие на протяжении ограниченно или неограниченно длительного времени под напряжением достаточную пластичность и вязкость при температурах ниже 100 °С* (* по ГОСТ 9867-61 единица измерения температуры 1К)
|
|
вплоть до - 269 °С.
B зависимости от структуры, определяемой химическим составом, получаемой при охлаждении на воздухе после высокотемпературного нагрева, высоколегированные стали подразделяют на следующие классы: мартенситный - стали с основной структурой мартенсита;
мартенситно-ферритный - стали, содержащие в структуре, кроме мартенсита, не менее 5% феррита; ферритный - стали, имеющие структуру феррита, не претерпевающие α(δ) γ-превращений;
аустенитно-мартенситный - стали, имеющие смешанную структуру аустенита и мартенсита, количество которых можно изменять в широких пределах; аустенитно-ферритный (или ферритно-аустенитный) - стали, имеющие смешанную структуру аустенита и феррита, количество последнего в которых составляет более 10%; аустенитный - стали, имеющие преимущественно однофазную аустенитную структуру.
Группу собственно нержавеющих в атмосферных условиях составляют стали, содержащие свыше 10% хрома. К коррозионностойким в различных агрессивных средах относятся стали, содержащие 15% и более хрома.
Жаростойкими до температуры 900 °С являются нержавеющие стали марок 12X17, 08Х17Т, 15Х18СЮ; до температуры 1100 °С - 15Х25Т, 15X28, 20Х25Н20С2 и другие; до температуры 1300°С - 15Х25Ю5 и др.
|
|
Жаропрочными при температурах до 565-610 °С являются стали с содержанием 11-12,5% хрома, легированные молибденом, вольфрамом, ванадием; при температурах до 650 °С -хромоникелевые стали типа 18-9 и 18-10, стабилизированные титаном; до 800 °С - хромоникельмолибденовые аустенитные стали, сталь 15Х14Н14В2М и др.
Весьма перспективными коррозионностойкими и хладостойкими являются стали с низким содержанием углерода и дополнительно легированные азотом. Последний целесообразно использовать как для частичной замены никеля, так и для повышения прочностных характеристик стали. Перспективность сталей с низким содержанием углерода и наличием азота основана на лучшей свариваемости и более высокой коррозионной стойкости.
По составу различают стали хромистые, хромоникелевые, хромомарганцевые, хромоникельмарганцевые и стали, дополнительно легированные азотом, а также с добавками специальных легирующих элементов (молибдена, вольфрама и др.) и карбидообразующих (титана, ниобия, тантала), играющих роль стабилизаторов структуры и свойств.
Технология сварки
|
|
Высоколегированные стали и сплавы, как правило, обладают увеличенным до 1,5 раза коэффициентом линейного расширения при нагревании и пониженным в 1,5-2 раза коэффициентом теплопроводности по сравнению с низкоуглеродистыми сталями.
Большинство этих сталей склонно к образованию горячих или холодных трещин при сварке, что усложняет процесс обеспечения качества сварных соединений с требуемыми свойствами. При дуговой сварке высоколегированных сталей следует предохранять поверхности металла от попадания на него брызг металла и шлака, так как они, повреждая поверхность, могут быть причиной коррозии или концентрации напряжений, ослабляющих конструкцию. Для предохранения от приваривания брызг на поверхность металла, прилегающую к шву, наносят защитное покрытие (кремнийорганический лак, грунт ВЛ-02, ВЛ-023 и др.).
Высокохромистые мартенситные стали (20X13, 14Х17Н2 и др.), мартенситно-ферритные (12X13, 14Х12Н2МФ и др.)- это закаливающиеся стали, склонные к образованию холодных трещин. В меньшей степени к ним относятся стали ферритного класса (12X17, 08Х17Т, 08Х18Т1 и др.). Для предотвращения трещинообразования применяют предварительный или сопутствующий подогрев, особенно необходимый с увеличением содержания в стали углерода и ее толщины. После сварки мартенситные, мартенситно-ферритные, а иногда и ферритные стали подвергают высокому отпуску при температуре 680-720 °С, а жаропрочные (20X13, 12X13 и др.) - при температуре 730-750 °С. Отпуск улучшает структуру, механические свойства и коррозионную стойкость.
|
|
Следует учитывать, что коррозионная стойкость сталей, не содержащих титана или ниобия, при нагревании более 500 °С постепенно падает, поэтому в сталь вводят эти элементы и дополнительно легируют молибденом, ванадием и другими добавками, например мартенситная сталь 18X1ШНФБ; мартенситно-ферритная 18Х12ВМБФР; ферритная 15Х25Т и др. Для сварки мартенситных, мартенситно-ферритных и ферритных сталей применяют электроды, стержни и покрытия которых обеспечивают получение наплавленного металла, близкого по химическому составу к основному металлу, например мартенситную сталь марки 15X11 ВМФ сваривают электродами Э12Х11НВМФ марки КТИ-10; мартенситно-ферритную сталь марки 12X13 -электродами Э12Х13 марки УОНИИ-13/ШЗ и т.д. Если конструкции из стали этого класса работают на статическую нагрузку и к швам не предъявляются требования высокой прочности, сварку можно выполнить аустенитными или аустенитно-ферритными электродами, например ферритную сталь 15Х25Т сваривают электродами Э02Х20Н14Г2М2 марки ОЗЛ-20, при этом отпуск после сварки можно не проводить.
Для сварки используют режим с малой погонной энергией для предотвращения роста зерна и охрупчивания зоны термического влияния.
В покрытии электродов, применяемых для сварки высокохромистых сталей, не должно быть газообразующих органических соединений, а газовая защита должна осуществляться за счет диссоциации карбонатов и выделяемой при этом СО (окиси углерода). Как и при сварке среднелегированных сталей, требования к качеству сборки и очистки металла перед сваркой остаются такими же и еще более ужесточаются.
Высокохромистые стали рассмотренных классов свариваются также в среде аргона вольфрамовым электродом. Этим способом рекомендуется соединять детали толщиной до 5-6 мм с подогревом, последующая термообработка не требуется. Целесообразно сваривать вольфрамовым электродом корневые швы более толстой стали, что обеспечивает хорошее формирование обратного валика, остальные слои шва выполняют электродуговой ручной сваркой или другим способом.
К высоколегированным хромоникелевым сталям относятся стали аустенитного, аустенитно-мартенситового и аустенитно-ферритного классов. Высоколегированные аустенитные сплавы на железоникелевой или никелевой основе являются устойчиво аустенитными и не меняют структуры при нагревании и охлаждении на воздухе. Эти стали и сплавы широко применяются в различных конструкциях, работающих в тяжелых условиях высоких и низких температур. Жаропрочные стали, легированные элементами-упрочнителями - вольфрамом и молибденом, способны длительно выдерживать большие нагрузки в условиях высоких температур. Жаростойкие стали устойчивы против химического разрушения поверхности в газовых агрессивных средах при температурах 1100-1150 °С. Эти стали и сплавы содержат мало вредных примесей, поэтому основными задачами при сварке являются хорошая защита расплавленного металла от воздуха и применение электродов со стержнем аустенитной структуры и покрытием основного типа.
Аустенитные хромоникелевые стали особенно чувствительны к увеличению углерода и серы, а также других элементов, образующих легкоплавкие эвтектики.
Для борьбы с горячими трещинами стремятся уменьшить содержание в стали и наплавленном металле С, S, и других элементов или подавить их другими добавками, связывающими S, как, например, Мn, а также уменьшить влияние термических напряжений путем применения благоприятных режимов сварки и предварительного и сопутствующего подогрева. Хромомарганцевые стали 15Х17АГ14 и хромоникельмарганцевые стали 12Х17Г2АН4 менее склонны к образованию горячих трещин, чем хромоникелевые.
В хромоникелевых сталях может развиваться межкристаллитная коррозия при замедленном охлаждении в интервале 500-800 °С в связи с тем, что по границам зерен происходит выделение карбидов хрома за счет обеднения хромом участков, прилегающих к границам зерен. В результате этого содержание Сr в приграничных участках падает ниже 12%, что под действием агрессивных сред приводит к коррозии. Так как аустенит представляет собой твердый раствор Cr, Ni, Мn, С и других элементов в железе, а растворимость С в Fe не превышает 0,02-0,03 %, то в интервале указанных температур лишний углерод выделяется из твердого раствора и образует карбид хрома. Чем больше в стали углерода, тем больше ее склонность к межкристаллитной коррозии. Увеличение процента хрома тормозит этот процесс.
Ферритная составляющая в аустенитно-ферритной стали должна быть в пределах 3-5 % феррита. Для предупреждения межкристаллитной коррозии необходимо применять сварку на низких режимах (на уменьшенных токах, малой погонной энергии и электродами диаметром не более 4-5 мм), особенно для многослойных швов.
Одним из дефектов аустенитно-мартенситных и аустенитно-ферритных сталей является склонность их при сварке к перегреву и охрупчиванию зоны влияния. Это вызывается ростом зерна в связи с перегревом ферритной фазы, образующейся вблизи зоны сплавления. Охрупчиванию способствует также превращение обогащенного углеродом аустенита (при высокой температуре аустенит переобогащается углеродом) в мартенсит с охлаждением шва. Снижение аустенитной фазы ниже 20 % повышает склонность их к межкристаллитной коррозии. Для предупреждения этого дефекта стремятся снизить содержание углерода в швах. Иногда назначают полную термообработку для восстановления коррозионных свойств.
Сварка аустенитных сталей не вызывает особых затруднений. Надо иметь в виду, что в сварных соединениях аустенитно-ферритных и аустенитно-мартенситных сталей возможно выделение водорода по границам зерен. Для предупреждения этого сварное соединение подвергают отпуску в течение 1-2 ч при температуре 150 °С.
Высокоуглеродистые аустенитные стали хорошо свариваются в атмосфере аргона с применением присадочной проволоки того же состава, что и основной металл, но с меньшим содержанием углерода; сварка рекомендуется для стали толщиной до 5-7 мм.
В целях экономии высоколегированной стали для изготовления сосудов, аппаратов и трубопроводов, работающих под давлением в агрессивных средах, применяют двухслойную сталь, основной слой которой состоит из низкоуглеродистой или низколегированной стали толщиной 4-60 мм, а плакирующий (облицовочный) - из высоколегированной стали или сплава толщиной 0,7-6 мм. При ручной дуговой сварке такой стали делают двухстороннюю разделку и сперва заваривают основной слой электродами УОНИИ-13/45 или УОНИИ-13/55, при этом стараются не задеть плакирующий слой. После зачистки корня шва со стороны плакирующего слоя заваривают первый слой электродами с повышенным запасом аустенитности, например марки К-ЗМ, а затем заваривают плакирующий слой электродами НЖ-13, СЛ-28 или им аналогичными.
Некоторые данные о режимах и выборе электродов для ручной дуговой сварке приведены в табл.1.
Таблица 1. Некоторые марки электродов для сварки высоколегированных сталей и сплавов.
Марка стали | Марка электродов | Тип электродов по ГОСТ 10052-75 | Структура наплавленного металла |
Коррозионно-стойкие стали | |||
08Н18Н10,08Х18Н10Т, 12Х18Н10Т, 08Х18Н12Т, 08Х18Н12Б, 08Х22Н6Т и подобные, работающие в агрессивных средах: к металлу шва предъявляются требования по стойкости к МКК к металлу шва предъявляются жесткие требования по стойкости к МКК | ЦЛ-11, ОЗЛ-7, ОЗЛ-8, ОЗЛ-22, ОЗЛ-36 | Э-04Х20Н9 Э-07Х20Н9 Э-08Х19Н10Г2Б | Аустенитно-ферритная с 2,5... 7% α-фазы |
ОЗЛ-7, АНВ-13 | Э-08Х20Н9Г2Б | Аустенитно-ферритная с 5,0... 10% α-фазы | |
Те же стали, работающие при температурах до 600 °С в жидких агрессивных средах; к металлу шва предъявляются требования по стойкости к МКК | Л-38М | Э-02Х19Н9Б | Аустенитно-ферритная с 3,0... 5,0% α-фазы |
10Х17Н13М2Т, 10Х17Н13МЗТ, 08Х18Н12Б, 08X2IH6M2T и подобные, работающие при температурах до 700 °С: к металлу шва предъявляются требования по стойкости к МКК к металлу шва предъявляются жесткие требования по стойкости к МКК | СЛ-28, ОЗЛ-20, ОЗЛ-41 | Э-8Х19Н10Г2МБ, Э-09Х19Н10Г2М2Б | Аустенитно-ферритная с 4,0... 5,0% α-фазы |
НЖ-13 | Э-09Х19Н10Г2М2Б | Аустенитно-ферритная с 4,0... 8,0% α-фазы | |
Жаропрочные стали | |||
12Х18Н9,12Х18Н10Т, 08Х18Н12Т, работающие при температурах до 800 °С | ЦТ-15, ЦТ-26 | ЭА-1М2 Э-08Х16Н8М2 Э-08Н17Н8М2 | Аустенитно-ферритная с 2,0... 4,0% феррита |
10Х23Н18 и подобные, работающие при температурах выше 850 °С | ОЗЛ-4 ОЗЛ-6 | Э-10Х25Н13Г2 | Аустенитно-ферритная с содержанием феррита не менее 2,5 % |
Жаростойкие стали | |||
Х20Н14С2,20Х20Н14С2, 20Х25Н20С2, работающие при температурах 900 ... 1100°С | ОЗЛ-6 ОЗЛ-31М | Э-12Х24Н14С2 | Аустенитно-ферритная с 3 ... 10% α-фазы |
20Х25Н20С2, 4Х18Н25С2, работающие при температурах до 1050 °С; к металлу шва предъявляются требования жаростойкости и жаропрочности | ОЗЛ-5 ОЗЛ-9-1 | Э-28Х24Н16Г6 | Аустенитно-карбидная |
Сварка под флюсом
Этот один из основных способов сварки высоколегированных сталей толщиной 3 ... 50 мм имеет большое преимущество перед ручной дуговой сваркой покрытыми электродами ввиду стабильности состава и свойств металла по всей длине шва при сварке с разделкой и без разделки кромок. Это достигается отсутствием частых кратеров, образующихся при смене электродов, равномерностью плавления электродной проволоки и основного металла по длине шва (при ручной сварке меньшая скорость плавления электрода вначале его использования и большая в конце изменяет долю основного металла в шве, а значит, и его состав), более надежной защитой зоны сварки от окисления легирующих компонентов кислородом воздуха и др. Хорошее формирование поверхности швов с мелкой чешуйчатостью и плавным переходом к основному металлу, отсутствие брызг на поверхности изделия заметно повышают коррозионную стойкость сварных соединений. При этом способе уменьшается трудоемкость подготовительных работ, так как разделку кромок выполняют на металле толщиной свыше 12 мм (при ручной сварке свыше 3 ... 5 мм). Возможна сварка с повышенным зазором и без разделки кромок стали толщиной до 30 ... 40 мм. Уменьшение потерь на угар, разбрызгивание и огарки электродов на 10 ... 20 % снижает расход дорогостоящей сварочной проволоки. Однако при сварке под флюсом некоторых марок жаропрочных сталей требование обеспечения в металле шва регламентированного количества ферритной фазы не всегда может быть достигнуто. Это объясняется трудностью получения необходимого состава металла шва за счет выбора только сварочных флюсов и проволок (последние имеют значительные колебания химического состава в пределах стали одной марки) при сварке металла различной толщины (различная форма разделки и, значит, доля участия основного металла в формировании шва).
При сварке используют безокислительные низкокремнистые фторидные и высокоосновные флюсы, создающие в зоне сварки безокислительные или малоокислительные среды, способствующие минимальному угару легирующих элементов. Остатки шлака и флюса на поверхности швов, которые могут служить очагами коррозии сварных соединений на коррозионно- и жаростойких сталях, необходимо тщательно удалять. Тип флюсов предопределяет преимущественное использование для сварки постоянного тока обратной полярности. При этом достигается и повышенная глубина проплавления.
Сварка в защитных газах
В качестве защитных используют инертные (аргон, гелий) и активные (углекислый) газы, а также различные смеси инертных или активных газов и инертных с активными. Этот способ сварки имеет ряд существенных преимуществ. Его можно использовать для соединения металлов широкого диапазона толщин - от десятых долей до десятков миллиметров.
Применение инертных газов существенно повышает стабильность дуги. Значительное различие теплофизических свойств защитных газов и применение их смесей, изменяя тепловую эффективность дуги и условия ввода теплоты в свариваемые кромки, значительно расширяют технологические возможности дуги. При сварке в инертных газах наблюдается минимальный угар легирующих элементов, что важно при сварке высоколегированных сталей. При сварке в защитных газах возможности изменения химического состава металла шва более ограничены по сравнению с другими способами сварки и возможны за счет изменения состава сварочной (присадочной) проволоки или изменения доли участия основного металла в образовании металла шва (режим сварки), когда составы основного и электродного металлов значительно различаются.
Сварку в защитных газах можно выполнять неплавящимся вольфрамовым или плавящимся электродом.
Для сварки высоколегированных сталей используют аргон высшего или 1-го сортов по ГОСТ 10157-79. Сварку ведут на постоянном токе прямой полярности. Исключение составляют стали и сплавы с повышенным содержанием алюминия, когда для разрушения поверхностной пленки окислов, богатой алюминием, следует применять переменный ток.
Сварку можно выполнять непрерывно горящей или импульсной дугой. Импульсная дуга благодаря особенностям ее теплового воздействия позволяет уменьшить протяженность околошовной зоны и коробление свариваемых кромок, а также сваривать металл малой толщины при хорошем формировании шва. Особенности кристаллизации металла сварочной ванны при этом способе сварки способствуют дезориентации структуры, уменьшая вероятность образования горячих трещин. Однако эта же особенность может способствовать образованию околошовных надрывов при сварке высоколегированных сталей. Для улучшения формирования корня шва используют поддув газа, а при сварке корневых швов на металле повышенных толщин - специальные расплавляющиеся вставки.
Электродуговая сварка
Современные высоколегированные стали, даже не подвергнутые специальному металлургическому улучшению-вакуумному, электрошлаковому, плазменно-дуговому переплавам,- отличаются хорошей раскисленностью и высокой чистотой по кислороду и вредным примесям.
Практически все защитные среды, применяемые для наиболее распространенных методов электродуговой сварки сталей, не являются абсолютно нейтральными по отношению к жидкому металлу. Не только активные или защитные газы - двуокись углерода, смеси аргона и гелия с кислородом или углекислым газом - либо активные флюсы - шлаки, но и обычно поставляемые промышленностью газы - аргон и гелий, а также фторидные (так называемые бескислородные) флюсы или основные покрытия электродов содержат: защитные газы - небольшое количество кислорода, водорода, азота, а флюсы - активные окислы, примеси серы, фосфора и водород.
Естественно, что при использовании этих защитных сред, особенно аргона, гелия и фторидных флюсов, насыщение жидкого металла кислородом и азотом несравнимо меньше, чем при сварке незащищенной дугой или с защитой активными газами и шлаками. Однако, за исключением сварки в вакууме, при электродуговой сварке различных сталей происходят в большей или в меньшей степени активные металлургические процессы взаимодействия жидкого металла с защитной средой.
В зависимости от вида и режима электродуговой сварки, качества и состава защитной среды, химического состава основного и присадочного металлов в сварочной зоне могут происходить реакции прямого окисления элементов металла и его раскисления, окислительно-восстановительные реакции и связанные с ними выгорание некоторых элементов и соответственное снижение количества их в шве по сравнению с содержанием в свариваемом (основном) и присадочном (электродном) металлах либо переход их из флюса (шлака) или расплавленного электродного покрытия в шов. При этом может происходить увеличение или, наоборот, уменьшение количества в шве кислорода, азота, водорода, серы и фосфора, а также рафинирование металла при введении элементов, связывающих вредные примеси в нерастворимые в жидком металле соединения или измельчающих структуру последнего при его затвердевании.
Процессы взаимодействия жидкого металла с газовой фазой и шлаком при электродуговой сварке происходят как на стадии образования капель электродного металла и перехода их через дуговой промежуток в сварочную ванну, так и на стадии существования жидкого металла в ванне до его затвердевания, причем наиболее интенсивно эти реакции протекают на первой стадии.
Для обеспечения требуемого состава металла шва, а следовательно, хотя бы ориентировочного учета степени окисления (выгорания) элементов присадочного и свариваемого (основного) металлов или, наоборот, легирования ими металла шва за счет флюса, покрытия электродов или защитного газа, а также возможного рафинирования жидкого металла и требуемого в связи со всем этим состава электрода необходимо знать направление и примерную степень развития окислительно-восстановительных реакций в сварочной зоне. Это, как известно, зависит от концентрации, температуры, удельной поверхности и продолжительности контактирования реагирующих веществ, а также от химического сродства к кислороду различных элементов, содержащихся в металле электродных капель и сварочной ванны. Чем больше концентрация, удельная поверхность и продолжительность контактирования жидкого металла с газовой фазой и компонентами шлака в зоне сварки, тем полнее протекают реакции их взаимодействия.
Температура капель в зоне дуги составляет 2150-2350 °С,
а газа - 2900 °С, в то время как температура металла в сварочной ванне равна в среднем 1750° С, а газа в месте соприкосновения с ванной - 2300 °С.
Естественно, что температура металла в ванне под дугой значительно выше, чем в средней ее части, а по мере удаления от дуги снижается до температуры кристаллизации металла.
Из данных некоторых опытов следует, что температура капель электродного металла может изменяться в зависимости от защитной среды (наличия и количества в зоне дуги ионизирующих веществ и деионизаторов), рода сварочного тока и его полярности, а также от режима сварки.
Полнота завершения химических реакций при взаимодействии металла с защитной средой в дуге в значительной степени зависит также от величины поверхности контактирования взаимодействующих веществ (металла капель с газом или шлаком) и продолжительности их контактирования, т. е. от размера капель, количества их образования в единицу времени и скорости перехода с электрода через дуговой промежуток в ванну, Это в свою очередь зависит от режима сварки - силы сварочного тока и напряжения дуги.
Многочисленными опытами установлено, что с повышением сварочного тока средний размер капель электродного металла уменьшается, количество же расплавляемого металла в единицу времени (коэффициент расплавления) и удельная поверхность (отношение поверхности капли к ее объему ) возрастают. Следовательно, общая продолжительность образования капли на конце электрода и ее перелета через дуговой промежуток в сварочную ванну с увеличением тока значительно уменьшается. С повышением же напряжения дуги, наоборот, размер капель увеличивается, количество их в единицу времени уменьшается, средняя удельная поверхность капли также уменьшается, а продолжительность образования и перелета капли с электрода в ванну возрастает.
Другие способы сварки
Сварку угольным электродом применяют очень редко - при изготовлении тонкостенных неответственных конструкций. Это объясняется опасностью науглероживания шва и повышенным короблением изделий ввиду малой концентрированности угольной дуги как источника теплоты.
Перспективно для сварки высоколегированных сталей использование электронного луча. Возможность за один проход сварить без разделки кромок металл большой толщины с минимальной протяженностью околошовной зоны - важное технологическое преимущество этого способа. Однако и при этом способе возможно образование в шве и околошовной зоне горячих трещин и локальных разрушений. Наличие вакуума, способствуя удалению вредных примесей и газов, увеличивает испарение и полезных легирующих элементов. При глубоком и узком проваре часть газов может задержаться растущими кристаллами в шве и образовать поры. Сварка металла большой толщины затруднена из-за непостоянства глубины проплавления. Сложность и дороговизна аппаратуры и процесса определяют возможность применения электронно-лучевой сварки только при изготовлении ответственных конструкций.
Список литературы
1. Фролов В.В. «Теория сварочных процессов». Москва. Высшая школа. 1988г.
2. Лившиц Л.С. «Металловедение для сварщиков (сварка сталей)». Москва. Машиностроение. 1979г.
. Петров Г.Л., Тумарев А.С. «Теория сварочных процессов (с основами физической химии)». Москва. Высшая школа. 1977г.
. Геворгян Г.В. «Основы сварочного дела». Москва. Высшая школа. 1991г.
. Соколов И.И. «Газовая сварка и резка металлов». Москва. Высшая школа. 1978г.
Дата добавления: 2021-04-24; просмотров: 60; Мы поможем в написании вашей работы! |
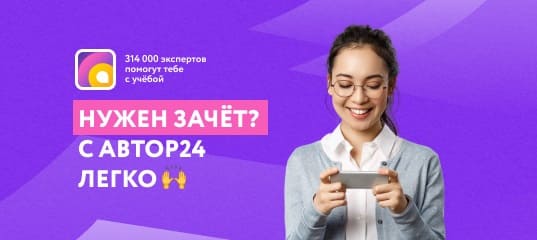
Мы поможем в написании ваших работ!