Преимущества и недостатки термической обработки
РЕФЕРАТ
По учебной дисциплине «Технология производства ЭС»
По направлению 211000.62 - Конструирование и технология электронных средств
ХИМИЧЕСКАЯ И ТЕРМИЧЕСКАЯ ОБРАБОТКА ДЕТАЛЕЙ
Преподаватель О.Н. Петрова
Студент гр. 1021 Воронцов А.М.
Содержание
Введение
. Термическая обработка
Классификация видов термической обработки
Преимущества и недостатки термической обработки
Историческая справка
Оборудование
Обозначение на чертеже
Пример технологического процесса с использованием термической обработки
. Химическая обработка
Классификация химической обработки
Преимущества и недостатки
Историческая справка
Оборудование
Система обозначений
Заключение
Список литературы
Введение
Целью данного реферата является изучение термической и химической обработки деталей. Данные способы обработки широко используются на сегодняшний момент.
Будут рассмотрены вопросы классификаций термической и химической обработки, а так же достоинства и недостатки обоих способов обработки. Так же будут задеты вопросы исторической справки термической обработки и химии в целом, оборудование, на котором происходят эти виды обработки, обозначение на чертежах. И в заключении будет представлен пример технологического процесса термической обработки детали (часть маршрутной карты).
Термическая обработка
|
|
Классификация видов термической обработки
Любой процесс термической обработки можно описать графиком, показывающим изменение температуры во времени. По такому графику можно определить температуру нагревания, время нагревания и охлаждения, средние и истинные скорости нагревания и охлаждения, время выдержки при температуре нагревания и общую продолжительность производственного цикла. Но по форме этого графика ничего нельзя сказать о том, с каким видом термообработки мы имеем дело. Вид термообработки определяется не характером изменения температуры во времени, а типом фазовых и структурных изменений в металле.
Основываясь на последнем признаке, А. А. Бочвар разработал классификацию, охватывающую многочисленные разновидности термической обработки черных и цветных металлов и сплавов. На основе классификации А. А. Бочвара Комиссией по стандартизации Совета Экономической Взаимопомощи были разработаны классификация видов и разновидностей термической обработки сталей и цветных металлов и сплавов, а также соответствующая терминология. На рисунке приведена схема классификации основных видов термической обработки металлов и сплавов.
|
|
Рис. 1 Классификация видов термической обработки
Термическая обработка подразделяется на собственно термическую, химико-термическую и термомеханическую (или деформационно-термическую). Собственно термическая обработка заключается только в термическом воздействии на металл или сплав, химико-термическая - в сочетании термического и химического воздействия, термомеханическая - в сочетании термического воздействия и пластической деформации. Собственно термическая обработка включает следующие основные виды: отжиг 1-го рода, отжиг 2-го рода, закалку с полиморфным превращением, закалку без полиморфного превращений, отпуск и старение. Эти виды термической обработки относятся и к сталям, и к цветным металлам и сплавам.
Собственно термическая обработка
Отжигом называют термообработку, направленную на получение в металлах равновесной структуры. Любой отжиг включает в себя нагрев до определенной температуры, выдержку при этой температуре и последующее медленное охлаждение. Цель отжига - уменьшить внутренние напряжения в металле, уменьшить прочностные свойства и увеличить пластичность. Отжиг делят на отжиг 1 рода и 2 рода.
Отжиг 1 рода - это такой вид отжига, при котором не происходит структурных изменений, связанных с фазовыми превращениями.
|
|
Отжиг 2 рода - термообработка, направленная на получение равновесной структуры в металлах и сплавах, испытывающих фазовые превращения.
Закалка с полиморфным превращением в принципе применима к любым металлам и сплавам, в которых при охлаждении перестраивается кристаллическая решетка. Во время ускоренного охлаждения при такой закалке протекает мартенситное превращение и образуется фаза, называемая мартенситом. Поэтому закалку с полиморфным превращением обычно называют закалкой на мартенсит.
Закалка без полиморфного превращения применима к любым сплавам, в которых одна фаза полностью или частично растворяется в другой. Например, в сплаве С0 на рисунке при нагревании до Тзакβ-фаза растворяется в матричной α-фазе. При обратном медленном охлаждении β-фаза выделяется из α-фазы, в которой концентрация компонента В уменьшается в соответствии с ходом сольву саnb.
Рис. 2 Схема к объяснению закалки без полиморфного превращения
Так как составы α- и β-фаз различны, то выделение β-фазы связано с диффузионным перераспределением компонентов. При достаточно быстром охлаждении диффузионное перераспределение, необходимое для зарождения и роста кристаллов β-фазы, не успевает пройти и β-фаза не выделяется из α-раствора. После такой термообработки (закалки) сплав при комнатной температуре состоит из одной α-фазы, как и при температуре нагрева под закалку.
|
|
Следовательно, закалка без полиморфного превращения состоит в фиксации при более низкой температуре состояния, свойственного более высокой температуре. При температуре нагрева под закалку Тзак в сплаве С0 твердый раствор ненасыщенный. После закалки α-раствор при комнатной температуре имеет такой же состав, как и при температуре закалки, но он уже пересыщенный, так как состав насыщенного раствора соответствует точке b. Таким образом, при закалке без полиморфного превращения образуется пересыщенный твердый раствор. Такая закалка к чистым металлам принципиально неприменима.
Рассмотренную на примере сплава С0 закалку без полиморфного превращения широко применяют к алюминиевым, магниевым, никелевым, медным и другим сплавам, а также к некоторым легированным сталям. Закалкой далеко не всегда фиксируют однофазное состояние. Например, в сплаве С2 при любых температурах, вплоть до эвтектической, содержится β-фаза. При температуре закалки Тзак в этом сплаве находятся насыщенный твердый раствор состава точки m и нерастворенный избыток β-фазы. При достаточно медленном охлаждении из-за выделения β-фазы из α-раствора его состав должен изменяться по линии mb.
Отпуск и старение - это разновидности термической обработки, в результате которой происходит изменение свойств закаленных сплавов.
Термин отпуск принято применять только к тем сплавам, которые были подвергнуты закалке с полиморфным превращением, а термин старение - в случае закалки без полиморфного превращения (после такой закалки фиксируется пересыщенный твердый раствор).
Цель отпуска стали - улучшение ее свойств. Отпуск стали смягчает действие закалки, уменьшает или снимает остаточные напряжения, повышает вязкость, уменьшает твердость и хрупкость стали. Отпуск производится путем нагрева деталей, закаленных на мартенсит до температуры ниже критической.
В отличие от отпуска после старения увеличиваются прочность, твердость, уменьшается пластичность.
Главный процесс при старении - это распад пересыщенного твердого раствора, который получается в результате закалки.
Таким образом, старение сплавов связано с переменной растворимостью избыточной фазы, а упрочнение при старении происходит в результате дисперсных выделений при распаде пересыщенного твердого раствора и возникающих при этом внутренних напряжений.
В стареющих сплавах выделения из пересыщенных твердых растворов встречаются в следующих основных формах: тонкопластинчатой (дискообразной), равноосной (обычно сферической или кубической) и игольчатой. Энергия упругих искажений минимальна для выделений в форме тонких пластин - линз. Основное назначение старения - повышение прочности и стабилизация свойств.
Различают старение естественное, искусственное и после пластической деформации.
Естественное старение - это самопроизвольное повышение прочности (и уменьшение пластичности) закаленного сплава, которое происходит в процессе его выдержки при нормальной температуре. Нагрев сплава увеличивает подвижность атомов, что ускоряет процесс.
Твердые растворы при низких температурах чаще всего распадаются до стадии образования зон. Данные зоны являются дисперсными областями, которые обогащены избыточным компонентом. Они сохраняют ту кристаллическую структуру, которую имел первоначальный раствор. Зоны носят название в честь Гинье и Престона. При использовании электронной микроскопии данные зоны можно наблюдать в сплавах Al - Ag, которые имеют вид сферических частиц диаметром ~10А. СпалавыAl - Cu имеют зоны-пластины, которые имеют толщину <10А.
Искусственное старение - это повышение прочности, происходящее в процессе выдержки при повышенных температурах. Если закаленный сплав, имеющий структуру пересыщенного твердого раствора, подвергнуть пластической деформации, то это ускоряет протекающие при старении процессы. Этот вид старения носит название деформационного. Термическая обработка алюминиевых сплавов состоит из двух циклов - закалки и старения. Старение охватывает все процессы, происходящие в пересыщенном твердом растворе, - процессы, подготавливающие выделение, и процессы выделения. Превращение, при котором происходят только процессы выделения, называется дисперсионным твердением.
Для практики большое значение имеет инкубационный период - время, в течение которого в закаленном сплаве совершаются подготовительные процессы, время, в течение которого закаленный сплав сохраняет высокую пластичность. Это позволяет проводить холодную деформацию непосредственно после закалки.
Если при старении происходят только процессы выделения, без сложных подготовительных процессов, то такое явление называют дисперсионным твердением.
Практическое значение явления старения сплавов очень велико. Так, после старения увеличивается прочность и уменьшается пластичность низкоуглеродистой стали в результате дисперсных выделений в феррите цементита третичного и нитридов.
Старение является основным способом упрочнения алюминиевых сплавов, некоторых сплавов меди, а также многих жаропрочных и других сплавов. В настоящее время все более широко используют мартенситностареющие сплавы.
Сегодня достаточно часто вместо термина «естественное старение» используют термин - «низкотемпературное старение», а вместо «искусственного старения» - «высокотемпературное старение». Самыми первыми металлами, которые были упрочнены при помощи старения, были алюминиевые сплавы. Упрочнение проводилось при температурах выше 100 °C.
В разных температурных интервалах наблюдаются различия в процессе распада. Поэтому для получения оптимального комплекса свойств в сплавах применяется сложное старение, проходящее в определенной последовательности, при низких и более высоких температурах.
Старение сплавов, вызванное процессом распада пресыщенного твердого раствора, является наиболее важным. После охлаждения сплавов появляется состояние пресыщения твердого раствора. Это вызвано тем, что при высокой температуре увеличивается растворимость примесей и легирующих компонентов.
Преимущества и недостатки термической обработки
термическая химическая обработка закалка
Отжиг
Преимущества:
отсутствие ограничений на вид детали;
поиск глобального минимума;
эффективность при решении задач различных классов, требующих оптимизации.
Недостатки:
требование бесконечно медленного охлаждения, на практике означающее медленную работу алгоритма;
сложность настройки.
Закалка
Преимущества: высокая производительность, отсутствие обезуглероживания и окисления поверхности детали, возможность регулирования и контроля режима термической обработки, возможность применения автоматизации технологического процесса, высокая культура производства. Закалочные агрегатывозможно устанавливать в поточную линию механического цеха при массовом производстве.
Недостатки: высокая стоимость индукционных установок и индукторов (для каждой детали свой индуктор). Поэтому этот метод экономически целесообразно использовать только при массовом производстве однотипных деталей простой формы.
Историческая справка
Железо, судя по данным раскопок в Египте и в бассейне рек Тигра и Евфрата, стало известно не позднее 4500 лет до н. э. Первые изделия из метеоритного железа получали ковкой. Греки приписывали изобретение ковки Гефесту - богу огня и покровителю кузнецов. Следующим по времени освоения процессом обработки металлов давлением было волочение. В III-IV тысячелетии до н. э. в Вавилоне при изготовлении украшений из благородных металлов золота и серебра применяли волочение. Первые волоки были получены из камня. Протягивание проволоки производили вручную. В последующем основным волочильным инструментом была доска с просверленными в ней отверстиями различного диаметра. Последовательно протаскивая заготовку через несколько отверстий с уменьшающимся диаметром, получали проволоку нужного размера. На территории нашей Родины в ХIII в. до н. э. были известны орудия и оружие из железа. Железо получали прямым восстановлением руд в сыродутных печах в форме губчатых криц, из которых ковали всевозможные изделия. Основное оборудование кузнеца Древней Руси составляли: кузнечный горн, меха, наковальня, а инструментом служили кувалды, зубила, клещи.
Металлографическое и рентгенографическое изучение железных изделий археологических памятников показало, что в Х-ХIII в. н. э. техника обработки железа на Руси достигла большого совершенства. В то время широко применяли наряду со свободной ковкой кузнечную сварку, пайку медью, полировку, цементацию, термическую обработку (закалка, отпуск).
Оборудование
Оборудование для проведения термической обработки делится на основное, дополнительное и вспомогательное. К основному относятся печи, ванны, агрегаты, установки ТВЧ, закалочные баки и т. п. Дополнительное оборудование используется после термической обработки - это моечные машины, дробеструйные агрегаты, травильные установки и линии, правильные пресса. К вспомогательному оборудованию относятся установки для получения контролируемой атмосферы, подъемно-транспортное (контейнеры, толкатели, подъемники и др.), маслоохладительные системы, воздуходувы, вентиляторы и др.
Основное термическое оборудование включает нагревательные печи и устройства, а также установки, обеспечивающие режимы охлаждения. Печи и нагревательные устройства группируются по технологическому назначению в зависимости от вида операций, для которых они предназначены: закалочные, отпускные, нормализационные, цементационные и другие. Печи могут работать на газообразном и жидком топливе, а также на электроэнергии. По конструкции печи бывают периодического (камерные, шахтные, колпаковые и другие) и непрерывного действия (конвейерные, карусельные, барабанные).
По признаку использования различных сред в рабочем пространстве печи могут быть с насыщающей, окислительной или нейтральной атмосферой, вакуумные, печи-ванны с расплавленными солями и металлами. К основным характеристикам печей относятся тип, максимальная температура, расход топлива или номинальная мощность, размеры рабочего пространства, число тепловых зон, производительность, средства перемещения изделий внутри печи. Каждая печь или нагревательное устройство снабжены приборами для измерения и регулирования температуры (или ее записи), давления газа, подачи воздуха или состава контролируемой атмосферы. Современные термические печи чаще всего включают в себя автоматические загрузочные и разгрузочные устройства. Выбор оборудования для термической обработки металлических заготовок прежде всего определяется видом металлопродукции (прокат, поковки, слитки, трубы, рельсы, проволока, лента).
Так, для термической обработки ленты, полосы или проволоки чаще всего используют колпаковые и проходные печи с роликовым подом. Для обработки сортового металла мелких и средних размеров обычно применяют проходные печи с шагающими балками или цепной конвейерной системой. Для термической обработки труб используют специальные виды печей. Обработку особо крупных поковок, слитков больших размеров и других массивных изделий проводят в печах с выкатным подом.
Для обработки полуфабрикатов и изделий, полученных методами порошковой металлургии, изделий тонкого сечения, а также листов или лент с предварительно нанесенными покрытиями применяют проходные печи с конвейерной лентой. В последнее время на металлургических заводах часто применяют термическую обработку различных видов проката с использованием тепла прокатного нагрева. В этом случае специфика термических операций (нормализация, закалка, охлаждение с регулируемой скоростью) определяется созданием специальных установок и устройств, которые располагают непосредственно за прокатным оборудованием.
Обозначение на чертеже
На чертежах изделий, подвергаемых термической и другим видам обработки, указывают показатели свойств материалов, полученных в результате обработки, например: твердость (HRCэ, HRB, HRA, HB, HV), предел прочности (σв), предел упругости (σу), ударная вязкость (ак) и т. п.
Глубину обработки обозначают буквой h.
Величины глубины обработки и твердости материалов на чертежах указывают предельными значениями: «от…до», например: h0,7…0,9; 40…46 HRCэ
В технически обоснованных случаях допускается указывать номинальные значения этих величин с предельными отклонениям, например, h 0,8±0,1; (43±3) HRCэ.
Допускается указывать значения показателей свойств материалов со знаками ≥ или ≤, например σв≥1500 кгс/см2, твердость ≥780 HVт.п.
Обозначение твердости HRCэ следует указывать только во вновь разрабатываемой документации. При использовании ранее разработанной документации для перевода значения твердости HRCв HRCэ следует руководствоваться ГОСТ 8. 064 - 79
Допускается на чертежах указывать виды обработки, результаты которых не подвергаются контролю, например, отжиг, а также виды обработки, если они являются единственными гарантирующими требуемые свойства материала и долговечность изделия. В этих случаях наименование обработки указывают словами или условными сокращениями, принятыми в научно-технической литературе (рис.1, 2).
![]() | ![]() |
Рисунок 1. Указание на чертежах вида обработки | Рисунок 2. Указание на чертежах вида обработки |
Дата добавления: 2021-04-24; просмотров: 400; Мы поможем в написании вашей работы! |
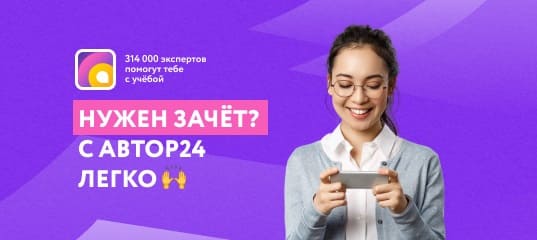
Мы поможем в написании ваших работ!