Сплавы с заданным коэффициентом теплового расширения
Методы определения твердости
Твердость – способность материалов сопротивляться пластической или упругой деформации при внедрении в него более твердого тела, которое называется индентором .
Существует разные методы определения твердости.
Твердость по Бринеллю определяется как отношение нагрузки при вдавливании стального шарика в испытуемый материал к площади поверхности полученного сферического отпечатка (рис. 4.7а).
HB = 2P / pD [D - Ö D2 – d2],
где Р – нагрузка, кгс;
D – диаметр шарика, мм;
d – диаметр лунки, мм
Рис. 4.7. Схемы испытания на твердость: а – по Бринеллю; б – по Роквеллу; в – по Виккерсу
Твердость по Роквеллу определяется глубиной проникновения в испытуемый материал алмазного конуса с углом при вершине 120о или закаленного шарика диаметром 1,588 мм (рис. 4.7.б).
Конус или шарик вдавливают двумя последовательными нагрузками:
- предварительной Ро = 10 н;
- общей Р = Ро + Р1, где Р1 – основная нагрузка.
Твердость обозначается в условных единицах:
- для шкал А и С HR = 100 – (h – ho) / 0,002
- для шкалы В HR = 130 – (h – hо) / 0,002
Для определения твердости используется алмазный конус при нагрузке 60 Н (HRA), алмазный конус при нагрузке 150 Н (HRC) или стальной шарик диаметром 1,588 мм (HRB).
Твердость по Виккерсу измеряют для деталей малой толщины и тонких поверхностных слоев, полученных химико-термической обработкой.
Эта твердость определяется как отношение нагрузки при вдавливании в испытуемый материал алмазной четырехгранной пирамиды с углом между гранями 136о к площади поверхности полученного пирамидального отпечатка (рис. 4.7.в):
|
|
HV = 2P * sin a/2 / d2 = 1,854 P/d2,
где P – нагрузка, кгс;
a = 136о – угол между гранями;
d – среднее арифметическое длин обеих диагоналей, мм.
Величину HV находят по известному d согласно формуле или по расчетным таблицам согласно ГОСТ 2999-75.
Микротвердость , учитывая структурную неоднородность металла, применяют для измерения малых площадей образца. При этом вдавливают пирамиду как при определении твердости по Виккерсу, при нагрузке Р = 5-500 Н, а среднее арифметическое длин обеих диагоналей (d) измеряется в мкм. Для измерения микротвердости используется металлографический микроскоп.
Основные превращения в сталях
В сталях основными являются три структуры: аустенит – твердый раствор углерода в γ – Fe [Fe γ(С)]; мартенсит – пересыщенный, частично упорядоченный твердый раствор углерода в α – Fe [Fe γ(С)]; перлит – эвтектоидная смесь феррита и цементита [Feα + Fe3 С]. Переход из одной структуры в другую характеризует основные превращения при термической обработке:
|
|
- первое превращение – это превращение перлита в аустенит, которое происходит при нагреве: П→А (рис. 8.1).
Рис. 8.1. Изменение энергии фаз в зависимости от температуры
- второе превращение – это превращение аустенита в феррито-цементитные смеси разной дисперсности в зависимости от скорости охлаждения: А→Ф+Ц;
- третье превращение заключается в превращении аустенита в мартенсит А→М при быстром охлаждении (при закалке);
- четвертое превращение заключается в разложении мартенсита при отпуске закаленной стали (М → продукты распада).
Любой технологический процесс термической обработки состоит из определенных комбинаций этих четырех превращений.
Цементация стали
При цементации происходит поверхностное насыщение стали углеродом, в результате чего получается высокоуглеродистый поверхностный слой, а сердцевина стали остается мягкой и вязкой, несмотря на то, что сталь после цементации подвергается закалке.
Цементация выгодно распределяет углерод от поверхности, а термическая обработка (закалка) упрочняет деталь, поверхность и сердцевину.
Поверхность стали после такой обработки имеет высокую твердость и износостойкость при вязкой сердцевине.
|
|
Цементации подвергают низкоуглеродистые и легированные стали с содержанием углерода меньше 0,3 %, которые должны обладать:
- закаливаемостью на 29-43 HRC (углеродистые 08, 10, 15, 20; легированные 20ХГТ, 12ХН2);
- прокаливаемостью, обеспечивающей требуемую структуру сердцевины;
- наследственно-мелкозернистостью;
- хорошей технологичностью при насыщении углеродом и последующей термической обработке и обработке резанием.
Различают два вида цементации: твердую и газовую.
Долговечность и надежность цементированных деталей и допустимый уровень их нагружения при эксплуатации определяются следующими параметрами:
- составом стали;
- толщиной и структурой цементированного слоя (рис.12.1);
- наличием дефектов в слое;
- твердостью поверхностных слоев и сердцевины.
На цементацию детали поступают с припуском на шлифование 0,05- 0,1мм; температура цементации выше Ас3 (930-950 оС). В твердом карбюризаторе 1 мм слоя образуется в течение 8-10 ч, в газовом - 1 мм образуется за 6 - 7 ч.
Твердый карбюризатор - древесный активированный уголь, каменноугольный полукокс и торфяной кокс с добавками активизаторов (BаCО3 и Na2СО3) в количестве 10 - 40 % от веса угля.
Газовый карбюризатор - природный газ и жидкие углеводороды.
|
|
Для неответственных деталей закалка их может производиться сразу с температур цементации (рис. 12.2,а) или после повторного нагрева до температуры выше Ас1 на 30 оС и охлаждении в воде (рис. 12.2, б).
Для ответственных деталей после цементации делают двойную закалку с нагревом выше Ас1 + 30 оС и охлаждением в воде (рис. 12.2, в).
После любого режима термической обработки делается низкий отпуск (160-180 оС).
Глубина цементированного слоя составляет 0,5 - 2,0 мм (иногда до 4 мм) с концентрацией углерода 0,8 - 1,2 % ( рис. 12.1).
За глубину цементированного слоя принимают глубину слоя со структурой заэвтектоидной, эвтектоидной и доэвтектоидной стали с содержанием углерода более 0,4 % (рис.12.1).
При цементации получаем твердость поверхностного цементированного слоя углеродистой стали 60-64 HRC (900HV), для легированной 58-61HRC (снижение твердости происходит за счет наличия в структуре остаточного аустенита); твердость сердцевины составляет 20-35HRC.
Азотирование стали
Азотирование – это процесс насыщения поверхностного слоя азотом.
Цель такой обработки изделия: получение высокой твердости, износостойкости, повышенной усталостной прочности, сопротивления коррозии. Карбюризатором является аммиак (NH3 → 3H + N).
Азотированию при температуре 500 - 600 оС с выдержкой до 60 часов подвергают готовые изделия, прошедшие механическую и окончательную термическую обработку (закалку и высокий отпуск).
К азотируемым сталям относятся среднеуглеродистые стали, легированные хромом, молибденом, алюминием (38Х2МЮА, 35ХМА, 38Х2Ю).
Глубина азотированного слоя составляет 0,3 - 0,6 мм, скорость азотирования – 0,01 мм/ч и менее.
Твердость азотированного слоя по Виккерсу составляет ~ 1200HV.
Азотированию подвергают мерительный инструмент, гильзы, цилиндры, зубчатые колеса, шестерни, втулки, коленчатые валы.
Сплавы с заданным коэффициентом теплового расширения
К сплавам с заданным коэффициентом теплового расширения относятся железо-никелевые сплавы:
- сплав ИНВАР - 36Н (≤ 0,05 % С и 35-37 % Ni). Он почти не расширяется при температуре от -60 до +100 °С и применяется в специальных приборах (альтиметрах, барографах) высокой точности, работающих при переменных нагрузках и климатических изменениях температуры;
- сплав КОВАР - 29НК (0,03 % С, 29 % Ni, 17-18 % Со). Он имеет низкий коэффициент теплового расширения в интервале температур от -70 до + 420 оС и применяется для деталей, впаиваемых в стекло при создании вакуумноплотных спаев.
- сплав платинит - H42 (42-48 % Ni, остальное Fe). Он имеет коэффициент теплового расширения, равный коэффициенту теплового расширения платины и стекла.
Магниевые сплавы
Магний - щелочноземельный металл серебристо-белого цвета. Аллотропических превращений не имеет. Температура плавления 650°. Плотность - 1,74 г/см³ — он самый легкий из всех применяемых в технике металлов.
Кристаллическая решетка магния гексагональная.
В литом состоянии предел прочности магния на разрыв составляет 10—13 кг/мм2 при относительном удлинении 3—6%.
Магний обладает большой активностью при взаимодействии с кислородом и в виде порошка и тонкой ленты сгорает на воздухе при ослепительно белом пламени.
В чистом виде магний применяют в пиротехнике, при фотографии — для осветительных эффектов; наиболее широкое применение он получил для изготовления сверхлегких сплавов (электрон).
Металлический магний получается главным образом путем электролиза при температуре 750—770° безводного хлористого магния (MgCl2). Одновременно с магнием при этом получается и газообразный хлор.
Магниевые сплавы
Магниевые сплавы характеризуются небольшим удельным весом (около 2,0 г/см3, т.е. они в 1½ раза легче алюминиевых сплавов).
Магниевые сплавы обладают отличной механической обрабатываемостью, допускающей высокие скорости резания, и сравнительно большой прочностью (δ до 27 кг/мм2).
Недостатки магниевых сплавов
Недостатками магниевых сплавов являются:
- их легкая окисляемость и самовозгораемость при плавке, что вызывает необходимость плавки и разливки этих сплавов под слоем флюсов или в вакууме;
- меньшая коррозионная стойкость и более низкие литейные свойства, чем у алюминиевых сплавов.
Эти недостатки устраняются добавкой в сплавы небольших количеств бериллия, нанесением защитных покрытий и улучшением технологии производства отливок.
В качестве легирующих добавок в магниевых сплавах используют алюминий, цинк и марганец, растворяющиеся в магнии. Растворимость падает с уменьшением температуры, что позволяет применять для этих сплавов термическую обработку, заключающуюся в закалке с последующим старением.
Магниевые сплавы делятся на деформируемые (МА) и литейные (МЛ). Эти сплавы очень легкие и используются для изготовления деталей в авиастроении.
Маркировка: Мг90 – 99,9% Mg, Мг95, Мг96; сплавы – МЛ10, МЛ3, МА5, МА2-2.
Титан и его сплавы
Титан – это серебристо-белый металл с малой плотностью (4,5 г/см3) и высокой температурой плавления (1672 оС), имеющий две аллотропические модификации: α – низкотемпературную с плотноупакованной гексагональной решёткой и β – высокотемпературную с кубической объёмноцентрированной решёткой. Температура перехода α ↔ β равна 882 оС.
Для улучшения прочностных и пластических свойств титан легируется различными элементами, содержание которых, в общей сложности, не превышает 10 –15 %. Легирующие элементы смещают температуру аллотропического превращения титана. Алюминий, кислород, азот, углерод стабилизируют α –фазу ; железо, молибден, тантал, вольфрам, хром, марганец, никель стабилизируют β –фазу;
Титан имеет высокую коррозионную стойкость в большом количестве агрессивных сред, превосходя в этом отношении нержавеющую сталь. При нагреве до 500 оС титан становится активным и поглощает из атмосферы газы (кислород, азот, водород), что сильно влияет на его механические свойства.
Технический титан маркируется в зависимости от содержания примесей: BT1-00 (сумма примесей менее 0,398 %), ВТ1-0 (сумма примесей менее 0,55 %).
Титановые сплавы классифицируются:
- по технологии изготовления на деформируемые, литейные и изготовленные методами порошковой металлургии. Для маркировки деформируемых титановых сплавов используется буквенно-цифровой код:
- ОТ4-0, ОТ4-1, ОТ4 - сплавы, в которых основными легирующими добавками являются алюминий и марганец; буква О в начале означает «опытный» - совместное производство ВИАМ и Свердловского завода;
- ВТ5, ВТ5-1, ВТ3-1, ВТ6, ВТ9 и т.д. – сплавы, легированные алюминием или алюминием и вольфрамом; буква В означает производителя – Всероссийский институт авиационных материалов (ВИАМ); если стоит буква П – ЦНИИ конструкционных материалов «Прометей» (С – Петербург);
Стоящие за буквами цифры являются условным порядковым номером.
Особенности маркировки литейных титановых сплавов – наличие буквы Л в конце обозначения марки: ВТ5Л, ВТ3-1Л и др. Буква И в конце – специального назначения, В – преобладание ванадия (ПТ3В).
Для изготовления деталей методом порошковой металлургии используют сплавы ВТ5, ВТ5-1, ОТ4 и др. Порошковые сплавы маркируются так же, как и деформируемые. Иногда титан маркируется просто буквой Т и цифрами, показывающими содержание титана.
Литейные сплавы титана обладают более низкими механическими свойствами, чем соответствующие деформируемые;
- по способу упрочнения на термически упрочняемые и не упрочняемые термической обработкой;
- по структуре на однофазные α – сплавы (не содержат b-стабилизаторов); псевдо –а - сплавы (коэффициент b- стабилизации не более 0,25); (a + b)-сплавы (коэффициент b-стабилизации от 0,3 до 0,9); псевдо-b-сплавы (коэффициент b-стабилизации от 1,4 до 4,4) и b-сплавы (коэффициент b-стабилизации > 2,5).
Преимуществом титановых сплавов, по сравнению с техническим титаном, являются следующие свойства:
- сочетание высокой прочности (σв = 800-1500 МПа) с хорошей пластичностью (δ = 18-25 %);
- малая плотность и высокая удельная прочность (σв/γ до 40);
- хорошая жаропрочность (до 600-700 оС);
- высокая коррозионная стойкость;
- низкая пластичность при комнатной температуре;
- высокая чувствительность к поверхностным дефектам.
Все титановые сплавы подвергаются термообработке, ХТО и ТМО и для повышения их износостойкости возможно применение цементации и азотирования.
Основными недостатками титана и его сплавов являются:
- высокая способность при повышенных температурах к взаимодействию со всеми газами, а также с материалами плавильных печей;
- невысокие антифрикционные свойства;
- плохая обрабатываемость резанием;
- невысокая жесткость конструкции из-за низкого значения модуля упругости.
Титановые сплавы используют в авиа- и ракетостроении (корпуса двигателей, баллоны для газов, сопла, диски, детали крепежа, фюзеляжа), в химической промышленности (компрессоры, клапаны, вентили), в изготовлении криогенной техники.
Цинк и его сплавы
Цинк - голубовато-серебристый блестящий металл; на воздухе быстро окисляется, покрываясь тонкой защитной пленкой, уменьшающей его блеск; имеет низкую температуру плавления. Объем металла при плавлении увеличивается в соответствии со снижением плотности. С повышением температуры уменьшается кинетическая вязкость и электропроводность цинка и возрастает его удельное электрическое сопротивление.
Цинк — твердый металл, но становится пластичным при 100–150 °C. При температуре выше 210 °С может деформироваться. Температура плавления — очень низкая для металлов. Несмотря на это, цинк имеет хорошую электропроводность. Наиболее общие и важные физические характеристики цинка представлены ниже:
- Плотность — 7,133 г/см³.
- Теплопроводность — 116 Вт/(м·К).
- Температура плавления цинка — 419,6 °C.
- Температура кипения — 906,2 °C.
- Удельная теплота испарения — 114,8 кДж/моль.
- Удельная теплота плавления — 7,28 кДж/моль.
- Удельная магнитная восприимчивость — 0,175·10-6.
- Предел прочности при растяжении — 200–250 Мн/м2.
Маркировка: Ц0, Ц1С, ЦВ00, ЦАМ10-5 (Al-10%, Cu-5%).
Сплавы на основе хрома
Хром — блестящий металл серебристо-белого цвета. Его плотность равна 7,16 г/см3, температура плавления 1903° С, температура кипения 2567° С. Железо и хром в полной мере взаимно растворимы в твердом и жидком состояниях.
Маркировка: Х99Н1 – 99% Cr + 0,01% N; Х99Н4; Х99; Х97,5
Сплавы на основе марганца
Марганец — металл серебристого цвета, плотность его равна 7,3 кг/см3, температура плавления 1244° С, температура кипения 2095° С, теплота плавления 14,6 МДж/кг-атом (3500 кал/г-атом) теплота испарения 224,8 МДж/г-атом (53 700 кал/г-атом). В жидком состоянии железо и марганец полностью взаимно растворимы, химических соединений они не образуют. Сплавы марганца, содержащие 75—85% Mn, с железом легкоплавки, температура плавления железа и Mn составляет около 1380° С.
Маркировка: металлический Мн998 – 99,8% Mn; Мн997, Мн965, Мн95; азотированный Мн92Н6 – 92% Mn + 6% N; Мн87Н6, Мн89Н4, Мн91Н2.
Ферросплавы
Ферросплавы — сплавы железа с другими элементами (Cr, Si, Mn, Ti и др.), применяемые главным образом для раскисления и легирования стали (напр., феррохром, ферросилиций). К ферросплавам условно относят также некоторые сплавы, содержащие железо лишь в виде примесей (силикокальций, силикомарганец и др.), и некоторые металлы и неметаллы (Mn, Cr, Si) с минимальным содержанием примесей. Получают из руд или концентратов в электропечах или плавильных шахтах (горнах). Как правило, стоимость металла в виде ферросплава ниже, чем стоимость его в чистом виде.
Ферросилиций – кремниево-железный сплав, отличающийся отменными прочностными показателями. Используют его в качестве раскислителя, восстановителя и укрепителя. Он широко применяется в выплавке рессорно-пружинных, коррозийно- и жаростойких, электротехнических сталей, термитных смесей.
Маркировка: ФС90 – 90% Si + 10% Fe; ФС75, ФС70, ФС50, ФС20.
Ферромарганец представляет собой легирующий ферросплав с содержанием марганца в нем от 70% до 90%, серы не более 6%, фосфора до 0.5%. В зависимости от химического состава ГОСТом 4755-91 предусмотрено производство ферромарганца трех основных видов: низкоуглеродистый, среднеуглеродистый и углеродистый. Низкоуглеродистый ферромарганец содержит не менее 85% марганца и менее 0,5 углерода.
Среднеуглеродистый сплав данного рода состоит из более 85% марганца и от 1 до 2% углерода. Углеродистый ферромарганец содержит в своем составе более 70% марганца и до 7% углерода.
Данный продукт применяют в металлургии для улучшения коррозионной устойчивости и стойкости на разрыв стали, улучшения ее твердости и увеличения плотности. Используют также этот ферросплав в черной металлургии для очищения металлов путем их раскисления и для обработки электродов в процессе сварочных работ. Оправдано также применение ферромарганца для выплавки сталей с низким содержанием углерода.
Маркировка: ФМн90 – 90% Mn + 10% Fe; ФМн88, ФМн78, ФМн70.
Ферросиликомарганец - ферросплав, в котором содержится большое количество марганца. Значительную часть занимает кремний. Все остальное - это железо со всевозможными примесями. Это легирующая добавка, которая позволяет получить определенные марки стали. Раскислительность материала значительно выше, чем в случае с простым марганцем либо же кремнием. При добавлении материала в жидкую сталь получается более износостойкий материал с повышенными характеристиками, который гораздо лучше переносит внешние воздействия. В частности, ему не страшна влага. Плотность уменьшается. Кроме того, ферросиликомарганец способствует устойчивости при изгибе.
Маркировка: МнС17Р35 – 17% Si + 0,35% P + 60-65% Mn; МнС25, МнС17, МнС22, МнС12.
Ферромолибден - легирующий компонент стали, в сплав входит молибден, занимающий чуть больше половины объема и железо. При применении устраняется хрупкость, повышается прокаливаемость стали и, как показывает практика, увеличивается температурный интервал закалки.
Маркировка: ФМо60 – 60% Mo + 40% Fe; ФМо58, ФМо55, ФМо50.
Ферротитан представляет собой сплав, созданный сплавлением железа и других металлов (кремния, марганца, хрома, алюминия и так далее). Процентное количество титана или 60 % или до 35 %. Его применяют в производстве нержавеющей стали разного вида, быстрорежущих, инструментальных и штамповых сталей, сварочных электродов. Имеет отличную свариваемость (адгезия) и лучшие жароупорные качества.
Маркировка: ФТи70С05 – 70% Ti + 0,5% Si + 5% Al; ФТи35С7, ФТи30.
Силикокальций – это сплав нескольких химических элементов между собой – железа, кремния и кальция. В результате этого соединения проявляются свойства эффективного дисульфатора, литейного чугуна, дегазатора стали и комплексного раскислителя. Используется во время раскисления стали и различных сплавов, а также модифицированного чугуна.
Маркировка: СК10 – 10% Ca + 45% Si + 1% Al; СК15, СК20, СК25, СК30
Ферросиликохром - ферросплав, применяемый для легирования и раскисления стали и сплавов, модифицирования чугуна, а также для использования в качестве восстановителя при выплавке феррохрома.
Маркировка: ФХС20 – 20% Si + 48% Cr + 4,5% C + 0,04% P; ФХС33, ФХС40; если повышено содержание фосфора, то в конце добавляется буква Р (ФХС48Р).
Ферробор – сплав железа и бора, применяемый для легирования и модифицирования стали, чугуна и сплавов цветных металлов. Содержит 6-20% бора, до 15% кремния, до 12% алюминия, примеси углерода, серы, фосфора, меди.
Маркировка: ФБ20 – 20% B; ФБ17, ФБ12, ФБ6.
Феррониобий является химическим ферросплавом с большим содержанием ниобия (около 60%). Так же в состав материала входит алюминий, кремний, железо, титан и прочие примеси. Это наиболее дорогостоящее металлургическое сырье с высокой температурой плавления (1700 градусов по Цельсию), так как растворение феррониобия происходит в металле крайне медленно. Применяется: в виде добавки к более низколегированной стали (для нефтяной и газовой проводки, мостов, строительных сооружений, ЖД путей, корпусов легкового и грузового автотранспорта); в сталелитейной промышленности для легирования стальных сплавов некоторых марок, а также при производстве электродных покрытий; в составе хромоникелевой стали для предотвращения межкристаллитной коррозии и улучшения технических характеристик исходного материала.
Маркировка: ФНб60 – 60% Nb; ФНб58; если повышено содержание Si (до 20%), то в конце ставится буква С (ФНб50С, ФНб55С).
Ферровольфрам - это ферросплав вольфрама и железа, который массово применяется в черной металлургии во время легирования стали и других сплавов. Массовая доля вольфрама составляет 60-85%, до 7% молибдена и других примесей. Ферровольфрам очень тяжело плавится, в нормальных условиях обладает химической стойкостью. Он улучшает свойства стали при высоких температурах, придает ей стойкость против отпуска, улучшает теплостойкость. Ферровольфрам придает сплавам твердости и износостойкости. Он повышает интенсивность намагничивания для магнитных сталей. Повышает сопротивляемость разрыву, позволяет создать мелкозернистую структуру стали.
Маркировка: ФВ80(а) – 80% W, (а) – повышенное содержание Al (3-6%); ФВ75(а), ФВ70(а), ФВ70, ФВ72, ФВ65.
Феррованадий представляет собой особый вид ферросплава, с четко регламентированным содержанием ванадия. В качественном продукте, произведенном в четком соответствии с положениями ГОСТа 27130-94, содержание ванадия должно составлять от 35 до 85 процентов. Используют феррованадий в качестве легирующей добавки при производстве инструментальных и конструкционных сталей, а также жаропрочных сплавов. Благодаря этому стали и сплавы получают более крепкую микрокристаллическую структуру с улучшенными характеристиками устойчивости к коррозии, механическим нагрузкам и повреждениям. Также феррованадий вводится в состав многих сталей для улучшения такой их характеристики как прокаливаемость.
Маркировка: ФВо50У0,4 – 50% V + 0,4%; ФВо50У0,5; ФВо40У0,75
Феррохром входит в группу ферросплавов, основные компоненты – железо и хром. Классификация зависит от того, сколько в составе различных элементов (хром, кремний, углерод, примеси). В целом по процентному содержанию выделяют 10 марок. Однако главного компонента – самого хрома, может быть только 65 или 68 процентов. Феррохром необходим для производства нержавеющей стали.
Маркировка: FeCr…C50 - 5% C
Алюминиевые сплавы
АМц – Al+Mn
АМ – Al+Cu
Al+Si – силумины
Al+Zn+Mg – алькусины (В95)
Al+Mg – магналии
АВ – авиаль, АК – ковочный, АЛ – литейный, ВАД – деформируемый, изготовляемый ВИАМ (ВАД1, ВАД23), Д – дюралюминий, В – высокопрочный, САП – спеченные алюминиевые порошки (САП-1), САС – спеченные алюминиевые сплавы; цифры означают номер сплава.
Буквы в конце: М – мягкий (после отжига), Т – после закалки и естественного старения, А – плакированный (нанесен чистый слой алюминия), Н – нагартованный (3 – на ¾, 2 – на ½, 1 – на ¼), П – полунагартованный (полуфабрикат); ч – чистый, пч – повышенной чистоты, оч – особой чистоты, с – селективный.
Примеры: АК12М2 – 12% Si + 2% Cu; АМг4К – 4% Mg + 1% Si; А6П; АДоч; АК7М2; АК21М2; АК4МЦ6.
Особые виды чугунов
АЧС-1 - антифрикционный чугун серый 1-й марки
АЧВ-1 – антифрикционный чугун высокопрочный 1-й марки
АЧК-2 – антифрикционный чугун ковкий 2-й марки
Передельный чугун: П1, П2; для литейного производства – ПЛ1, ПЛ2; фосфористый – ПФ1, ПФ2, ПФ3; высококачественный – ПВК1, ПВК2, ПВК3.
Литейный чугун: Л1-6, ЛР1-7 (литейный, рафинированный магнием)
ЧВГ30 – чугун с вермикулярным (червеобразным) графитом
Минералокерамика
Минералокерамическим называют материал, полученный путем обработки порошкообразных минералов или их смесей с другими веществами и последующего обжига отформованного полуфабриката. Минералокерамические режущие пластины изготавливаются методами порошковой металлургии из исходного сырья дисперсностью 1...2 мкм.
Инструментальная промышленность выпускает минералокерамический инструмент, оснащенный многогранными (трех -, четырех -, пяти -, и шестигранными) неперетачиваемыми пластинами.
Современная минералокерамика подразделяется на четыре группы:
- оксидная;
- оксидно-карбидная;
- оксидно-нитридная;
- нитридно-кремниевая.
1.1. Оксидная минералокерамика
1.1. Оксидная минералокерамика изготавливается из технического глинозема (А12О3) - полупродукта алюминиевой промышленности, получаемого химическим путем из естественных глиноземных пород (бокситов). Имеет твердость HRA 92...95, микротвердость до 32000 МПа, теплостойкость 12OO°C, предел прочности на сжатие 5000 МПа.
Недостатком оксидной минералокерамики является ее низкая изгибная прочность, предел прочности на изгиб 450 МПа.
Основными марками оксидной минералокерамики является традиционная марка ЦМ-332 (цементный материал, литер 332), новые марки ВО-13, ВО-14, ВШ-75 и др.
Особенно эффективно применение минералокерамики при точении термически необработанных сталей при скорости резании V=100 м/мин и выше. При этом обеспечивается шероховатость обработанной поверхности до Ra=0,63… 0.40 мкм.
1.2. Минералокерамика оксидно-карбидная
Научный поиск, направленный на совершенствование дешевого минералокерамического режущего материала, привел к созданию оксидно- карбидной минералокерамики (марки ВЗ, ВОК-60. ВОК-63 и др.), имеющий предел прочности на изгиб до 700 МПа. При этом оксидно-карбидная минералокерамика сохраняет высокую твердость, теплостойкость, износостойкость и прочность на сжатие, присущие оксидной минералокерамике.
В состав оксидно-карбидной минералокерамики входят окись алюминия и карбиды тугоплавких металлов (минералокерамика ВОК-60 содержит 60% окиси алюминия AI2O3 и 40% карбида титана TiC).
Отличительной чертой оксидно-карбидной минералокерамики является её способность работать в условиях прерывистого резания с ударными нагрузками например, при обработке плоских поверхностей торцевыми фрезами. Стойкость торцовых фрез, оснащенных оксидно-карбидной минералокерамикой значительно выше стойкости фрез, оснащенных твердым сплавом.
1.3 Нитридно-кремниевая минералокерамика (НКК)
Представлена маркой силинит-Р. НКК (как инструментальный материал) обладает следующими отличительными свойствами по сравнению с другими видами режущей керамики:
- высокая плотность;
- высокое значение вязкости;
- высокая термопрочность;
- малый коэффициент линейного расширения.
Эти характеристики дают хорошие предпосылки данного инструментального материала для использования его как альтернативного твердому сплаву. Плотность НКК (силинит-Р) находится в пределах 3,2...3,4 г/см3, прочность на изгиб 500...700 МПа, прочность на сжатие 2500 МПа, микротвердость-32000 МПа.
Основу силинита Р составляет нитрид кремния Si3N4 с небольшим количеством добавок карбидов и окислов.
Опыт применения НКК Кіоn-2000 показывает, что инструмент, оснащенный данной керамикой, способен работать при точении чугуна (НВ147) на скоростях резания до V=500 м/мин при t =2,5 мм и подачах, превышающих значения S>1,3 мм/об.
По предельным значениям используемых подач при резании пластинами Kion-2000 вполне сопоставим с твердосплавным инструментом при возможности повышения скорости резания в 2...3 раза.
Инструмент, оснащенный мииералокерамикой, позволяет заменить операции шлифования токарной обработкой, причем качество обработанной поверхности не снижается и в большинстве случаев повышает эксплуатационные свойства деталей. Применение минералокерамики позволяет, наряду со значительным снижением трудоемкости, технологическим методом повысить долговечность работы деталей.
Минералокерамическим режущий инструмент получил значительное применение в машиностроительных отраслях промышленности. Данный инструмент также можно широко использовать в практике лезвийной обработки восстановленных напеканием автоматической наплавкой поверхностей деталей машин при выполнении чистовых операций взамен операции шлифования.
Увеличение номенклатуры деталей, обработанных инструментом, оснащенным минералокерамикой, является одной из важных задач при решении вопроса повышения качества и снижения трудоемкости обработки
2. Сверхтвердые материалы (СТМ) на основе нитрида бора
Рассмотрены физико-технические свойства разновидностей кубического нитрида бора (эльбор-Р, белбор-Р, гексанит-Р и др.)
Одним из наиболее эффективных направлений совершенствования технологии в современной металлообработке является внедрение и широкое применение инструмента из СТМ на основе нитрида бора. Эффективное применение СТМ достигается в том случае, когда четко соблюдаются рекомендуемые режимы резания и правила по использованию СОЖ, что связано с физико-механическими характеристиками данного режущего материала. Одной их важных характеристик композитов является возможность работы с ударом и без удара, на что необходимо обращать особое внимание.
СТМ выпускаемые в странах СНГ и в дальнем зарубежье, в зависимости от основного процесса, протекающего при получении и определяющего свойства СТМ на основе нитрида бора, можно разделить на три вида:
1. СТМ, синтез, которого основан на фазовом превращении графитоподобного нитрида бора в кубический нитрид бора BN. Из материалов этой группы в странах СНГ производят: - композит 01 - эльбор РМ, - композит 02- белбор.
2. СТМ, получение которых основано на частичном или полном превращении вюрцитного нитрида бора в кубический. В СНГ из материалов этой группы производят: - однослойный композит 10 и двухслойный композит 10Д (гексанит P), - модификация композита 09 (НТНБ, ПТНБ-ИК).
3. СТМ поручение которых основано на методах порошковой металлургии, спеканием частиц кубического нитрида бора BN. По этой технологии получают следующие модификации: композит 05, киборит, ниборит.
2.1 Эльбор-Р
Микротвердость эльбора, определяющая его режущую способность, близка к микротвердости алмаза и составляет 70000...90000 МПа, что обеспечивает высокую размерную стойкость инструмента. Теплостойкость эльбора1400…1500 0С - наивысшая среди всех известных режущих материалов для лезвийных инструментов. Важнейшим свойством эльбора является его способность противостоять циклическому воздействию высоких температур. При нагревании до температуры 1000°С на поверхности его кристаллов образуется тонкая защитная пленка, предохраняющая его от дальнейшего окисления.
Химическая стойкость эльбора-Р, определяющая в известной степени его износ при резании, также весьма высока. Эльбор нерастворим в концентрированных и разбавленных кислотах и щелочах, не разлагается в растворах щелочных металлов.
Эльбор-Р в отличие от алмаза инертен к железу, что способствует снижению его диффузивного и адгезионного износа. Этим он выгодно отличается от алмаза.
Предел прочности на изгиб эльбора - 700 МПа, что выше предела прочности на изгиб алмаза. Масса эльбора измеряется, как и масса алмаза, в каратах. Плотность эльбора 3,44…3,49 г/см3.
Точение закаленных сталей резцами из эльбора обеспечивает шероховатость обработанной поверхности Ra=0,63…0,1 мкм и точность до 6…4 квалитетов.
При обработке чугуна можно получить при такой же высокой точности шероховатость обработанной поверхности Ra=1,25…0,4 мкм
По режущим свойствам и износостойкости резцы из эльбора-Р в 5 6 раз превосходят резцы из твердого сплава при обработке закаленных сталей (HRC3 58…65) и чугунов (НВ 200). В связи с этим лезвийный инструмент из эльбора, несомненно, перспективен и находит все большее применение при окончательной обработке деталей из закаленных сталей и высокопрочных чугунов вместо шлифования.
Основной торговой маркой эльбора, используемого для оснащения резцов, фрез и другого лезвийного инструмента, является композит 01 (эльбор -Р) и композит 05.
Композит 01 (эльбор-Р) предназначен для чистовой обработки (без удара) закаленных сталей с наибольшей твердостью HRC3 67 и высокопрочных чугунов.
Резцы из эльбора-Р рекомендуются применять на следующих операциях:
1) обтачивание валиков из закаленной стали и высокотвердых чугунов взамен шлифования;
2) растачивание отверстий в деталях из закаленной стали и высокотвердых чугунов взамен шлифования,
3) прецизионная обработка деталей из незакаленных сталей взамен точения твердосплавными резцами и шлифования;
4) обработка деталей из труднообрабатываемых материалов
Композит 05 применяется для получистовой и чистовой обработки (без удара) чугунов (заготовки композита 05 выпускаются в виде цилиндров диаметром 8 мм, что позволяет снимать большие припуски) и не рекомендуется для обработки сталей.
2.2. Гексанит
Институтом проблем материаловедения АН УССР были созданы поликристаллические сверхтвердые материалы на основе вюрцитного нитрида бора, получившие наименование гексанит-Р и гексанит-А и используемые соответственно для лезвийного и шлифовального инструмента.
Использование ударных волн для осуществления фазового превращении в графитоподобном нитриде бора приводит к сильному измельчению получаемого материала (размер частиц основной фракции менее 1 мкм) и вносит большие искажения в структуру кристаллической решетки. Эти особенности вюрцитного нитрида бора обеспечивают возможность спекания его в поликристалический СТМ при более низких давлениях, чем применяемые для получения эльбора-Р, имеющего структуру кубического нитрида бора. Последнее обстоятельство позволило получать в серийном производстве поликристаллы гексанита—Р диаметром до 6…8 мм на стандартном прессовом оборудовании. Поликристаллы гексанита-Р и гексанита-А отличаются высокой микротвердостью 40000...70000 МПа, и сравнительно высокой теплостойкостью - до 9000С, а также сильно выраженными пластическими свойствами. Они имеют предел прочности на изгиб 1300 МПа. Основной отличительный признак поликристаллов гексанита-Р - способность работать при сильных ударных нагрузках за счет двухслойности. Гексанит-Р (торговая марка композит 10Д) применяется для получистовой и чистовой обработки прерывистых поверхностей деталей из закаленных сталей твердостью до HRC3 60 и чугунов.
Гексанит-Р можно применять и при чистовой обработке деталей высокой твердости и разнотвердости, восстанавливаемых напеканием или наплавкой при ремонте сельскохозяйственной техники.
Сравнительные характеристики СТМ на основе нитрида бора
Марка | Первоначальное название | Твердость HV, ГПа | Теплостойкость, oС |
Композит 01 | Эльбор-Р | 60...80 | 1100...1300 |
Композит 02 | Белбор | 60...90 | 900...1000 |
Композит 03 | Исмит | 60 | 1000 |
Композит 05 | Композит | 70 | 1000 |
Композит 09 | ПКНБ | 60...90 | 1500 |
Композит 10 | Гексанит-Р | 50...60 | 750...850 |
Эффективность применения лезвийных инструментов из различных марок композитов связана с совершенствованием конструкции инструментов и технологии их изготовления и с определением рациональной области их использования:
композиты 01 (эльбор-Р) и 02 (белбор) используют для тонкого и чистового точения и фрезерования без ударов деталей из закаленных сталей твердостью 55...70 НRС, чугунов и твердых сплавов ВК15, ВК20 и ВК25 с подачами до 0,20 мм/об и глубиной резания до 0,8
композит 05 применяют для чистового и получистового точения без ударов деталей из закаленных сталей твердостью 40...58 HRC, чугунов твердостью до 300 НВ с подачами до 0,25 мм/об и глубиной до 2,5 мм
композит 10 (гексанит-Р) используют для тонкого, чистового и получистового точения и фрезерования с ударами деталей из закаленных сталей твердостью не выше 58 HRC, чугунов любой твердости.
Абразивные зерна
Наибольшее распространение для производства абразивных инструментов на гибкой основе получили такие типы абразивного зерна:
Дата добавления: 2021-04-24; просмотров: 280; Мы поможем в написании вашей работы! |
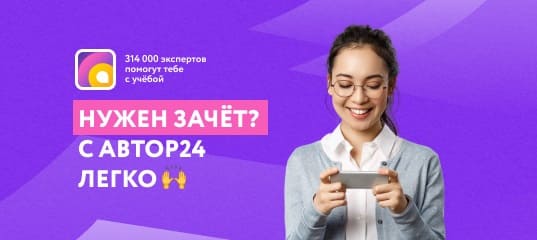
Мы поможем в написании ваших работ!