Основные операции на металлорежущих станках
Департамент образования и науки города Москвы
Государственное бюджетное профессиональное образовательное учреждение города Москвы
«Колледж железнодорожного и городского транспорта»
Отчёт по практике
УП.01 Учебная практика.
ППКРС: 23.01.09 Машинист локомотива по программе базовой подготовки на базе среднего общего образования.
Допуск к защите: Отчёт составил:
__________________ __________ /В.Д.Чарыков
__________________ Группа: 3М-285
(оценка)
проверил руководитель практики:
_______________И.А. Грибков
Москва 2019 год.
СОДЕРЖАНИЕ
Введение………………………………………………………………………..….3
Основные операции на металлорежущих станках……………………...………6
Токарная обработка………………………………….…………………….……..7
Сверление………………………………………………………………….……...8
Фрезерование……………………………………………………………….…….9
Полирование……………………………………………………………..………11
Виды металлорежущих станков…………………………...……….........……...12
|
|
Заточные станки…………………………………………………………..……..13
Фрезерные станки………………………………………………………...……...14
Сверлийные станки………………………………………………………..…….15
Полировальные станки…………………………………………………...……...16
Безопасность труда…………………………………………………….....……...17
Заключение…………………………………………………………….....………18
Список использованных ресурсов………............................................................19
ВВЕДЕНИЕ
Учебную практику УП.01 я проходил в мастерской №5 с 07.06.2019 по 28.06.2019 и с 02.09.2019 по 04.10.2019 года.
В процессе слесарной учебной практики, я узнал множество новой информации, связанной с слесарным делом. Познакомился с большим количеством оборудования, приспособлений, инструментов, а также научился применять их на практике. Узнал, какие бывают слесарные операции, как они правильно выполняются и что при их выполнении применяется (оборудование, приспособления, инструменты), а именно такие операции, как: разметка, рубка, правка и рихтовка, гибка, резка, опиливание металла, а также сверление, зенкерование, зенкование, развертывание, нарезание резьбы, клепка, шабрение и др. Познакомился с такими станками как: сверлильный, сверлильно-фрезерный, заточный. Узнал из каких основных частей они состоят, принцип их работы, а также охрану труда и технику безопасности при работе на них. На этих станках я научился выполнять такие операции как: сверление, фрезерование, зенкование металлических деталей, а также заточку различного инструмента для выполнения работы. Научился работать с мерительным (ШЦ-1) и разметочным (ШЦ-2) инструментами, а так же узнал, какие существуют шкалы твердости.
|
|
Еще я научился организовывать свое рабочее место (слесарный верстак), узнал, как правильно располагать инструменты и приспособления на своем рабочем месте, познакомился с режимом труда, санитарно-гигиеническими условиями труда, противопожарными мероприятиями, безопасными условиями труда.
Так как моей основной темой отчета по практике является работа на металлорежущих станках, то далее пойдет речь именно об этой теме. Но для начала я бы хотел рассказать, как появилась профессия слесарь.
Искусство добывать и обрабатывать металл вручную известно с древних времен. Человек на заре своего развития был в полной зависимости от стихийных сил природы, но на протяжении долгих веков он постепенно освобождался от этой зависимости, подчиняя себе природу. Борясь за свое существование, первобытный человек на первых порах изготовлял и приспосабливал для себя различные орудия из дерева, камня, а затем из бронзы и железа. Сначала эти орудия напоминали собой органы человеческого тела, например каменный молоток напоминал кулак, нож - форму когтей или зубов, грабли и лопаты - форму кисти и пальцев руки и т. п.
|
|
Люди научились добывать и обрабатывать металлы в давние времена. Из металла изготовлялись орудия труда, например топоры, косы, серпы, средства защиты - щиты, мечи и др., предметы домашнего обихода - посуда для варки пищи (котлы, чашки, тазы), украшения и другие изделия.
На протяжении многих лет металлические изделия изготовлялись ремесленниками-кузнецами. Первоначально эта группа ремесленников изготовляла вручную разнообразные металлические изделия, в дальнейшем развитие кузнечного ремесла, появление различных приспособлений, совершенствование орудий производства, применение бронзы и железа привели к разносторонности кузнечных работ. Это вызвало разделение труда между кузнецами-ремесленниками. Одни кузнецы выполняли более грубые и крупные работы, например орудия труда, предметы домашнего обихода и др., а другие - более мелкие и тонкие работы. Кузнецами-ремесленниками того времени вручную изготовлялись разнообразные изделия.
|
|
Появляется новая отрасль кузнечного производства - холодная ковка металла, т. е. окончательная обработка без нагрева металла. Наиболее типичными представителями этой отрасли были замочники - мастера по изготовлению замков. В начале 18 в. замочников называли "шлоссерами" (по-немецки Schloss- замок). Со временем иностранное слово приобрело иной смысл. Так возникло название "слесарь".
Образцы оружия, орудий труда, различных механизмов (замков, часов, машин) и других изделий поражают несложностью обработки, тщательностью отделки и говорят о том, что холодная обработка металла, искусство резать металл вручную были широко развиты среди народа несколько столетий назад. Развитие техники многим обязано талантливым русским людям, которых во все времена в России было много. Эти "умельцы", как их тогда называл народ, были разносторонне развитыми людьми, которые самостоятельно решали сложные технологические задачи. Особенно своим мастерством славились московские, тульские и уральские мастера.
Изготовление огнестрельного и холодного оружия, а также доспехов требовало выполнения слесарной работы. Благодаря этому развилось искусство чеканить украшения и выковывать сложнейшей формы шлемы. При изготовлении ружейного замка, сверлении пушек применялись различные инструменты и приспособления. Таким образом, в 14-15 вв. возникла самостоятельная отрасль кузнечного ремесла - холодная ковка, а вместе с ней и слесарное ремесло.
Особое развитие слесарное ремесло получило после Великой Октябрьской социалистической революции. Наши ученые, инженеры и техники, рабочие многое сделали, чтобы заменить тяжелый, малопроизводительный ручной труд работой механизмов и машин.
С появлением металлорежущих станков и их совершенствованием постепенно сокращалась роль и доля ручного труда, который стал заменяться трудом строгальщиков, токарей, фрезеровщиков, шлифовщиков и др. Но одной из ведущих остается профессия слесаря. По-прежнему ценится труд слесаря-мастера, от которого требуется умение выполнять все виды ручной обработки металлов.
Сегодня профессия «Слесарь» широко распространенная профессия с большим разнообразием объектов, материалов, условий, средств и приемов труда.Разборка, ремонт, сборка и испытания узлов и механизмов. Ремонт, монтаж, демонтаж, испытания, регулирование, наладка оборудования, агрегатов и машин и сдача после ремонта. Слесарная обработка деталей и узлов. Изготовление приспособлений для ремонта и монтажа. А теперь поговорим непосредственно о работе на металлорежущих станках.
Основные операции на металлорежущих станках
Токарная обработка
![]() |
Рис.1 Заточка зубила на заточном станке.
Токарная обработка металла осуществляется на специальных станках с применением различного режущего инструмента (резцов, сверл, разверток и др.), необходимого для того, чтобы придавать заготовке определенный вид. Металл по данной технологии обрабатывается благодаря сочетанию главного движения (вращения закрепленной в патроне/планшайбе заготовки) и движения подачи (совершается резцом до тех пор, пока заготовка не достигнет заданного размера, формы и качества поверхности).
Благодаря различным вариантам совместного использования этих движений, токарной обработке можно подвергать изделия из металла различной формы, кроме того, токарные станки необходимы для:
- нарезки резьбы;
- сверления отверстий, а также их растачивания, обработки разверткой и зенкером;
- резки деталей;
- вытачивания на изделиях канавок различных форм.
В результате токарной обработки металла можно получить деталь, удовлетворяющую всем требованиям к качеству, а именно токарная обработка металла подразумевает выполнение изделия с соответствующими требованиям размерами, формами, степени гладкости поверхностей и точности их расположения.
При токарной обработке металла проверку качества осуществляют предельными калибрами (на крупносерийном производстве), а также штангенциркулями, микрометрами, нутромерами и т. д. (на единичных и мелкосерийных производствах).
Сверление
Рис.2 Просверливание отверстия в заготовке на сверлильном станке
Рассверливание металла — это одна из многочисленных операций, которая часто выполняется при слесарных работах. Сверление производится для различных разборных/неразборных соединений, когда требуются определенного диаметра отверстия для заклепочных, болтовых либо шпилечных креплений.
Сам по себе металл — высокопрочный материал, поэтому при работе с ним независимо от того, требуется его рассверлить или прорезать, используются режущие инструменты, которые намного прочнее его.
Фрезерование
Рис.3 Фрезерование отверстий в заготовке на фрезерном станке.
Фрезерная обработка в последнее время набирает большую популярность, поэтому столь же востребована, как сверление деталей и токарная обработка. Суть её заключается в срезании слоя металла при помощи вращающейся, зубчатой фрезы. Фрезерование можно выполнять на заготовках из разных материалов, причем проделывается это как на специальных станках, так и вручную.
Полирование
Рис.4 Полировка шахматной пешки на полировальном станке.
Полирование металлических листов используется для придания поверхности листа ровной и гладкой поверхности, с зеркальным блеском. В результате полировки исчезают мелкие царапины, потертости, неровности, а также следы окисления за счет снятия тонкого слоя металла. Латунные листы со временем приобретают темный цвет за счет оксидов меди. Вернуть зеркальный блеск и цвет латунным листам можно при помощи полирования.
Полирование листов различается на:
механическое( с использованием абразивных кругов),
химическое (с использованием паст и порошков),
электролитическое,
ионное,
гидроабразивное,
магнитоабразивное,
ультразвуковое.
Механическое полирование подразумевает использование абразивных кругов или лент, а также пасту ГОИ.
При химическом полировании на поверхность листа наносят химически агрессивный реагент и используют гальванические пары. В результате на поверхности листа образуется пассивирующая оксидная пленка, которая выравнивает неровности и шероховатости.
Электромеханический метод полировки заключается в погружении листа в раствор электролита под напряжением и образованию пассивирующей пленки.
Также полирование листов осуществляется при помощи ультразвука или ионно-плазменной обработки.
Полирование металла осуществляется ручным или автоматическим (полуавтоматическим) способом. Автоматическое полирование стальных, нержавеющих и цветных листов осуществляется при помощи специализированного оборудования - бормашин, шлифовальных машин и электроточил. Основным элементом полировальных машин являются абразивные круги. Для процессов полировки используются абразивы с очень мелким зерном (алмазная крошка, титановая крошка, карбиды твердых металлов, корунды и пр.).
Полирование металлических листов осуществляется на высоких скоростях. Также используются вспомогательные материалы (паста ГОИ, алмазная паста и пр.).
Полировка металлических поверхностей различается по классам ( в зависимости от глубины шероховатостей – высоте неровности в микронах). Классы чистоты поверхности при полировке включают в себя с 10 по 14 классы по ГОСТ 2789-59. Высота неровностей при полировке составляет от 0.8 до 0.05 микрон.
Виды металлорежущих станков
Заточные станки
Рис.5 Заточной станок Makita GB 801
Спектр заточных станков варьируется от крупных промышленных станков для твердосплавного инструмента до маленьких, используемых в домашних мастерских. Примеры затачиваемого инструмента: зенкеры, развёртки, метчики, плашки, фрезы, фрезерные головки, фасонные резцы.
Станки подразделяются на универсальные, предназначенные для затачивания режущих инструментов различных видов вручную, и специализированные — для затачивания инструментов одного вида.Специализированные заточные станки обычно комплектуются специальными приспособлениями, служащими для установки и закрепления режущего инструмента неподвижно.
Фрезерные станки
Фре́зерные станки́ — группа металлорежущих и деревообрабатывающих станков в классификации по виду обработки. Фрезерные станки предназначены для обработки с помощью фрезы плоских и фасонных поверхностей, зубчатых колёс и т. п. металлических и других заготовок.
Рис.6 Фрезерный станок
При этом фреза, закрепленная в шпинделе фрезерного станка, совершает вращательное (главное) движение, а заготовка, закреплённая на столе, совершает движение подачи прямолинейное или криволинейное (иногда осуществляется одновременно вращающимся инструментом). Управление может быть ручным, автоматизированным или осуществляться с помощью системы ЧПУ.
Сверлильные станки
Рис.7 Напольный сверлильный станок
Сверлильные станки предназначены для сверления глухих и сквозных отверстий в сплошном материале, рассверливания, зенкерования, развертывания, нарезания внутренних резьб, вырезания дисков из листового материала. Для выполнения подобных операций используют сверла, зенкеры, развертки, метчики и другие инструменты. Формообразующими движениями при обработке отверстий на сверлильных станках являются главное вращательное движение инструмента и поступательное движение подачи инструмента по его оси.
Основной параметр станка — наибольший условный диаметр сверления отверстия (по стали). Кроме того, станок характеризуется вылетом и наибольшим ходом шпинделя, скоростными и другими показателями.
Полировальные станки
Рис.8 Полировальный станок.
Полировально-шлифовальное оборудование используется для выполнения разных видов обработки поверхностей металлических деталей. К ним относятся:
Основные этапы обработки:
Черновая обработка поверхностей.
Снятие фасок, заусенцев, удаление зазубрин, выравнивание поверхностей.
Исправление геометрии режущих кромок, заточка или придание им нужного угла атаки.
Шлифовка деталей (требуется соответствующая оснастка).
Полировка.
Конструкция агрегата состоит из электродвигателя, на сквозном валу которого по обе стороны установлены рабочие круги. На передней части кожуха, непосредственно под двигателем, располагается панель управления, основными элементами которой являются кнопки «пуск» и «стоп». В зависимости от вида или марки оборудования, рабочие инструменты могут иметь защитные кожухи, опорные площадки — подручники.
Дата добавления: 2021-04-24; просмотров: 493; Мы поможем в написании вашей работы! |
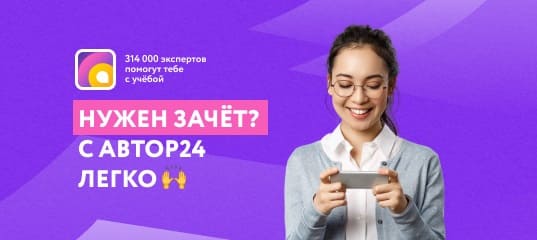
Мы поможем в написании ваших работ!