ТЕМА 3. Закалка и отпуск углеродистых сталей.
Цель работы: исследование фазовых превращений в углеродистых сталях при нагреве и охлаждении при закалке, при отпуске закаленных сталей. Изучение неравновесных структур после закалки и отпуска. Свойства мартенсита. Закаливаемость сталей.
Теоретическая часть: Способы термической обработки сталей: - Закалкастали ( этот процесс повышает твердость, прочность и износостойкость металла – деталь нагревается до определенной температуры, далее выдерживается некоторое время для прогрева всего объема и только потом уже охлаждается в масле или воде в зависимости от того какая сталь: конструкционная, инструментальная или углеродистая); - Отпуск (при отпуске повышается пластичность материала и уменьшается хрупкость мартенситной структуры, при этом уровень прочности сохраняется - отпуск применяется при изготовлении подшипников, пружин, режущих инструментов и других деталей); - Отжиг (уменьшение твердости металла для улучшения обрабатываемости, снятия внутреннего напряжения, достижения максимальной однородности металла, при этом происходит медленное нагревание до 740-850С, потом происходит выдержка и медленное охлаждение); - Нормализацию (при этом процессе повышается прочность металла, твердость и ударная вязкость, а также низкая пластичность, металл нагревается до критической температуры, далее происходит выдержка и охлаждение на открытом воздухе); - Цементацию - (в твердом карбюризаторе) (поверхностное насыщение углеродом для повышения прочности и износостойкости поверхностного слоя изделий при пластичной сердцевине); - Искусственное старение (процесс происходит при различных температурах и занимает несколько часов, используется в основном для стабилизации геометрических размеров изделий).
|
|
Цель закалки стали – улучшение свойств стали. Процесс закалки необходим очень многим деталям, изделиям. Эта термообработка основана на перекристаллизации стали, нагретой до температуры выше критической; после достаточной выдержки - следует быстрое охлаждение. Таким путем предотвращают превращение аустенита до перлита. Закаленная сталь имеет неравновесную структуру мартенсита, троостита или сорбита. Чаще всего, при закалке, сталь резко охлаждают на мартенсит. Смягчают действие закалки процессом отпуска. Отпуск - нагрев стали до температуры ниже точки А1. При отпуске структура стали из мартенсита закалки переходит в мартенсит отпуска, троостит отпуска или сорбит отпуска. Стали, подвергающиеся закалке, характеризуются закаливаемостью и прокаливаемостью. Закаливаемость - способность стали повышать твердость в результате закалки. Прокаливаемость - способность стали образовывать закаленный слой со структурой мартенсита и высокой твердостью. Прокаливаемость образца характеризуется максимально получаемой твердостью по сечению изделия (образца). При неполной прокаливаемости ее конкретная величина определяет возможность получения при закалке материала с установленным значением твердости на определенной глубине. Полная прокаливаемость, то есть наличие мартенситной структуры по всему сечению изделия, называется сквозной. Стали с малым содержанием углерода закалить на мартенсит очень трудно, так как начало и конец процесса образования мартенсита происходит в области высоких температур, соответствующих образованию других, более устойчивых структур (троостит, сорбит). Прокаливаемость обыкновенной углеродистой стали распространяется на 5...7 мм. Микроструктура закаленной стали зависит от ее химического состава и условий закалки (температуры нагрева и режима охлаждения). Закалка стали с содержанием углерода до 0,025...0,03% задерживает выделение третичного цементита по границам зерен и не меняет структуру феррита. Такая закалка повышает пластичность и почти не изменяет прочностных характеристик. Микроструктура стали с 0,08...0,15% С (с нагревом выше верхних критических точек и охлаждением в воде) представляет собой низкоуглеродистый мартенсит с выделениями феррита. Дальнейшее увеличение содержания углерода (0,15...0,25%) при тех же условиях закалки приводит к повышению твердости с 110...130 НВ до 140...180 НВ, а предел текучести возрастает на 30...50%. Наиболее значительное изменение свойств происходит при содержании углерода более 0,30...0,35%. Микроструктура доэвтектоидных сталей представляет собой мартенсит, кристаллы которого имеют характерную форму пластин (игл). При содержании углерода более 0,5...0,6% в микроструктуре сталей наблюдается незначительное (2...3%) количество аустенита. Микроструктура заэвтектоидных сталей состоит из мартенсита, зерен вторичного цементита (не растворившегося при нагреве) и остаточного аустенита. Кристаллы (иглы) мартенсита очень небольших размеров. Повышение температуры закалки вызывает растворение вторичного цементита и способствует росту зерна. В тех случаях, когда требуются высокая твердость и повышенная износостойкость поверхности при сохранении вязкой и достаточно прочной сердцевины изделия, применяется поверхностная закалка, то есть закалка не на полную глубину. Поверхностной закалке подвергаются стали с содержанием углерода более 0,3%. Выбор оптимальной толщины упрочняемого слоя определяется условиями работы детали и составляет от 1,5 до 15 мм (и выше). Площадь сечения закаленного слоя не должна превышать 20% площади всего сечения. В практике наиболее часто используют поверхностную закалку с индукционным нагревом током высокой частоты (ТВЧ).
|
|
|
|
|
|
Закалка. Охлаждение деталей. Закалённая сталь отличается большой хрупкостью, поэтому после Закалка её обычно подвергают отпуску. При одной и той же твёрдости сталь, подвергнутая Закалка с последующим отпуском, более пластична (следовательно, более работоспособна), чем сталь, подвергнутая медленному охлаждению, при котором происходит распад аустенита на феррит и цементит. Это определяет чрезвычайно широкое использование закаленной стали в технике: применение её не только для получения стали с высокой твёрдостью, но и для получения (после соответствующего отпуска) стали со средней и низкой твёрдостью, но обладающей хорошими конструкционными свойствами. Процесс закалки заканчивается охлаждением деталей. Скорость охлаждения деталей должна быть такой, чтобы деталь получилась заданной структуры. Скорость V 2, обеспечивающая мартенситную структуру (с остаточным аустенитом, не без троостита), называется критической скоростью закалки. Так как С-образные кривые доэвтектоидной, заэвтектоидной сталей смещены влево по сравнению с кривыми эвтектоидной стали, критическая скорость закалки их выше, следовательно, получение структуры мартенсита достигается труднее, а для некоторых марок структура мартенсита даже недостижима. Легирующие компоненты стали облегчают закалку, так как при этом С-образные кривые смещаются вправо, следовательно, критическая скорость понижается. Если скорость охлаждения меньше критической, то в структуре закаленной стали, наряду с мартенситом, будет троостит, а если скорость уменьшается дальше, то получаются структуры троостита или сорбита без мартенсита. Резкость закалки (получение мартенсита без троостита) зависит от природы температуры охлаждающей среды. Охлаждение струей воздуха или холодными металлическими плитами дает закалку на сорбит. Наиболее распространено охлаждение деталей погружением в воду, щелочные, кислые растворы, масло, расплавленный свинец и др. При этом получается резкая или умеренная закалка (на мартенсит или троостит). Охлаждающая способность воды резко изменяется в зависимости от температуры воды; если эту способность при 18 ° принять за единицу, то при 74 ° охлаждающая способность будет иметь коэффициент 0,05. К наиболее резким охладителям относится 10%-ный раствор NaOH в воде. Если температура 18 ° его коэффициент – 2,0. К умеренным охладителям относятся минеральные масла с коэффициентом 0,2-0,25. Для закалки применяют различные приемы охлаждения в зависимости от марки стали, формы, размеров детали, технических требований к ним. Простая закалка в одном охладителе (чаще всего в воде, в водных растворах) выполняется путем погружения детали до полного охлаждения. При охлаждении необходимо освобождать деталь от слоя пара хороший теплоизолятор. Такой способ закалки самый распространенный. Для получения высокой твердости, наибольшей глубины закаленного слоя, для углеродистой стали применяют охлаждение деталей при интенсивном обрызгивании. Прерывистая закалка - процесс охлаждения последовательно в двух средах: первая среда – охлаждающая жидкость (обычно вода); вторая – воздух или масло. Резкость такой закалки меньше, чем предыдущей. Ступенчатая закалка - в процесс охлаждения деталь быстро погружают в соляной расплав и охлаждают до температуры несколько выше Мн (см. рис. 3), короткое время выдерживают, затем охлаждают на воздухе. Выдержка обеспечивает выравнивание температуры от поверхности к сердцевине детали, что уменьшает напряжения, возникающие при мартенситном превращении. Способ погружения деталей в закалочную ванну должен быть таким, чтобы при закалке они как можно меньше коробились. Детали с большим отношением длины к диаметру или ширине (напильники, сверла и др.) следует погружать в охладитель вертикально.
Дата добавления: 2021-07-19; просмотров: 117; Мы поможем в написании вашей работы! |
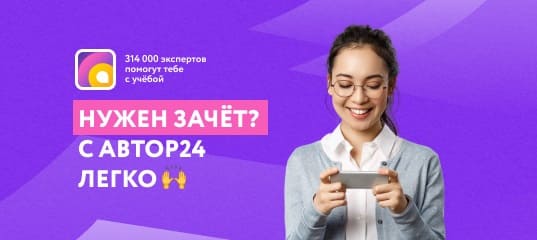
Мы поможем в написании ваших работ!