Превращения при отпуске стали.
Тема 8. Термическая обработка сталей и сплавов
Закалка и отпуск. Структурные превращения при закалке и отпуске. Режимы закалки и отпуска, охлаждающие среды. Влияние на свойства сталей. Способы упрочнения поверхности деталей.
Лекция 10. Закалка стали. Структурные превращения при закалке. Виды и способы закалки.
При больших степенях переохлаждения возрастает термодинамическая неустойчивость аустенита, скорость диффузии углерода резко падает. При переохлаждении аустенита в эвтектоидной стали до 240 ºC подвижность атомов углерода близка к нулю, и происходит бездиффузионное превращение аустенита. При этом меняется лишь тип решетки γ→α, а весь углерод, ранее растворенный в решетке аустенита, остается в решетке феррита, несмотря на то, что равновесная концентрация углерода в феррите при комнатной температуре не превышает 0,006 %. В результате образуется пересыщенный твердый раствор внедрения углерода в α-железе, который называется мартенситом. Из-за пересыщенности углеродом решетка мартенсита сильно искажена и вместо кубической приобретает тетрагональную форму, при которой отношение параметров решетки существенно отличается от единицы, т.е. с/а≠1. Чем больше углерода, тем выше степень тетрагональности мартенсита (рис. 10.1). Такая структура при рассмотрении под микроскопом имеет игольчатый вид.
Рис.10.1. Тетрагональная кристаллическая ячейка мартенсита
|
|
Мартенсит имеет высокую твердость (до 65 НRC) и прочность, значения которых возрастают с увеличением содержания углерода в мартенсите. Временное сопротивление низкоуглеродистого мартенсита (0,25 %С) составляет 1000 МПа, а мартенсит с содержанием 0,6-0,7 % С имеет временное сопротивление 2600-2700 МПа. Однако с повышением содержания углерода в мартенсите возрастает и его склонность к хрупкому разрушению. Высокая твердость мартенсита обусловлена искажениями кристаллической решетки и соответственно большими внутренними напряжениями, определяемыми растворенным углеродом, а также возникновением фазового наклепа за счет увеличения объема при превращении аустенита в мартенсит. В результате этого плотность дислокаций в мартенсите достигает уровня холоднодеформируемой стали и равняется 1010-1012 см -2.
Скорость образования кристаллов мартенсита очень велика. Пластины мартенсита растут до границы аустенитного зерна либо до имеющего в стали дефекта. Последующие пластины мартенсита, расположенные под углом к первым, ограничены размерами первичных пластин мартенсита и границами аустенитных зерен. Кристаллическая решетка новой фазы мартенсита закономерно ориентирована относительно исходной фазы – аустенита. При практически мгновенном γ→α переходе атомы смещаются упорядоченно, строго ориентированно на расстояния, меньшие межатомных. При этом сохраняется общая сопрягающая плоскость решеток γ- и α-Fe – так называемая когерентная связь. Из- за когерентности сопряжения решеток и различия удельных объемов фаз (аустенита и мартенсита) мартенситное превращение приводит к возникновению больших внутренних напряжений.
|
|
Мартенситное превращение проходит в интервале температур начала Мн и конца превращения Мк (рис.10.2).
Рис.10.2. Диаграмма изотермического превращения переохлажденного аустенита эвтектоидной стали.
Положение точек Мн и Мк не зависит от скорости охлаждения, но зависит от содержания углерода в стали. Для эвтектоидной стали оно начинается при 240 и заканчивается при –50 ºC. Однако при этой температуре в стали сохраняется еще некоторое количество не превращенного, так называемого остаточного аустенита. Охлаждение ниже температуры Мк не приводит к его окончательному распаду. Наличие остаточного аустенита нежелательно, так как приводит к неоднородности свойств по сечению и и изменению размеров деталей. Последнее обстоятельство объясняется тем, что мартенсит имеет наибольший удельный объем по сравнению с другими структурами, а аустенит – наименьший. Поэтому при переходе аустенитной структуры в мартенситную объем и размеры деталей увеличиваются. Увеличение удельного объема при образовании мартенсита является одной из основных причин возникновения при закалке больших внутренних напряжений, вызывающих деформацию и коробление изделий, а также появление закалочных трещин.
|
|
Закалка стали состоит в нагреве ее выше температур фазовых превращений, выдержке для завершения всех превращений и охлаждения с высокой скоростью с целью получения при комнатной температуре неравновесных структур, обеспечивающих более высокую прочность и твердость стали.
В зависимости от температуры нагрева различают полную и неполную закалку. При полной закалке нагрев осуществляют на 30-50 ºC выше Ас3 или Ас m . После закалки получается мартенситная структура с некоторым количеством остаточного аустенита.
При неполной закалке сталь нагревают на 30-50 ºC выше АС1, но ниже Ас3 или Ас m . В этом случае в нагретом состоянии структура доэвтектоидных сталей состоит из аустенита и феррита, а заэвтектоидных – из аустенита и вторичного цементита. При быстром охлаждении аустенит превращается в мартенсит, твердость которого зависит от содержания углерода в стали.
|
|
После неполной закалки в доэвтектоидных сталях структура состоит из мартенсита и включений зерен феррита. Наличие феррита в структуре закаленной стали снижает твердость, поэтому неполная закалка доэвтектоидных сталей нежелательна.
Заэвтектоидные стали обычно используют для изготовления инструмента. Важнейшим требованием, предъявляемым к инструментальным сталям, является твердость. Твердость заэвтектоидных сталей после полной закалки снижается за счет значительного увеличения количества остаточного аустенита в мартенситной структуре этих сталей.
Остаточного аустенита тем больше, чем большее количество углерода переходит в твердый раствор при нагреве стали. После неполной закалки в заэвтектоидных сталях структура состоит из мартенсита и округлых включений цементита вторичного, которые не только не уменьшают ,но даже увеличивают твердость, а следовательно и износостойкость стали. Кроме того, поскольку нагрев ведется при температурах ниже Ас m , уменьшается рост зерна, снижаются термические напряжения при закалке и менее интенсивно обезуглероживается поверхность металлов.
Наиболее благоприятная структура заэвтектоидных сталей достигается тогда, когда включения вторичного цементита имеют форму сфероидов – зернистую форму (рис.10.3).
Рис. 10.3. Микроструктура заэвтектоидной стали с 1,2% С:
а – избыточной цементит в виде сетки; б – зарнистый цементит
Цементитная сетка по границам зерен недопустима, так как увеличивается хрупкость стали. Поэтому закалке заэвтектоидных сталей должен предшествовать отжиг – сфероидезация.
Таким образом, для доэвтектоидных сталей рационально применять полную закалку, для заэвтектоидных – неполную (рис.10.4).
Рис. 10.4. Оптимальные температуры нагрева под закалку углеродистых сталей.
При закалке для достижения максимальной твердости стремятся получить мартенситную структуру. Минимальная скорость охлаждения, необходимая для переохлаждения аустенита до мартенситного превращения, называется критической скоростью закалки.
Скорость охлаждения определяется видом охлаждающей среды. Критическая скорость закалки определяется по диаграмме изотермического распада аустенита (рис.10.5), из которого следует, что быстрое охлаждение необходимо в области наименьшей устойчивости аустенита (500-650 ºC) с тем, чтобы предотвратить его превращение в феррито-цементитную смесь.
Рис. 10.5. Наложение кривых охлаждения на диаграмму изотермического распада аустенита.
Ниже 300 ºC, наоборот, целесообразно медленное охлаждение для предотвращения коробления и растрескивания деталей.
Значения скорости охлаждения сталей в различных средах приведены в табл.9.1.
Таблица 10.1.
Интенсивности Н закалки в различных средах
Движение | Воздух | Масло | Вода | Соленая вода |
Отсутствует | 0,02 | 0,25 | 1,0 | 2,0 |
Среднее | 0,05 | 0,4 | 1,3 | 2,5 |
Сильное | 0,08 | 0,9 | 2,0 | 4,0 |
Интенсивность охлаждения закалочной среды количественно оценивается параметром Н. Условно принято, что для спокойной воды Н = 1.
Данные табл.10.1 показывают, что нет идеальной закалочной среды, удовлетворяющей условию достижения оптимальной скорости охлаждения при закалке от разных температур. Растворы солей и щелочей при образовании могут вызвать коробление и трещины, а масло, имеющее хорошие свойства при этих температурах, менее выгодно при температурах 650-550 ºC.
Выбор способа охлаждения нагретой под закалку стальной детали зависит от формы, размеров и химического состава стали.
Чем сложнее форма и больше сечение детали, тем выше напряжения, возникающие при закалке, и больше опасность образования трещин. Чем больше содержание углерода в стали, тем большие объемные изменения протекают при превращении, тем больше опасность деформации и образования трещин, тем тщательнее должен быть выбор способа охлаждения при закалке.
Идеальная кривая охлаждения должна характеризоваться максимальной скоростью в начале охлаждения при прохождении интервала наименьшей устойчивости аустенита и минимальной скоростью в конце охлаждения при мартенситном превращении (рис 10.6).
Рис. 10.6. Схема режимов при разных способах закалки:1 – закалка в одном охладителе; 2 – закалка в двух средах; 3 – ступенчатая закалка; 4 – изотермическая закалка; 5 – идеальный режим охлаждения
Наиболее простой способ закалки – это закалка в одном охладителе, при котором нагретая деталь погружается в охладлающую жидкость и остается там до полного охлаждения. Недостатком этого способа является возникновение значительных внутренних напряжений. Для деталей из углеродистых сталей сечением более 5 мм наиболее широко применяемой закалочной средой является вода, для деталей меньших размеров и легированных сталей – масло.
Для уменьшения внутренних напряжений применяется закалка в двух средах, при которой деталь сначала охлаждают в воде до 300-400 ºC, а затем для окончательного охлаждения переносят в масло. Недостатком этого способа является трудность регулирования выдержки деталей в первой охлаждающей жидкости.
Точное регулирование времени выдержки деталей в первой охлаждающей жидкости достигается при ступенчатой закалке (рис.10.6, кривая 3). При этом способе деталь быстро охлаждается погружением в соляную ванну с температурой, немного превышающей (на 30-50 ºC) температуру мартенситного превращения данной стали Мн, выдерживаемой при этой температуре до достижения одинаковой температуры по всему сечению, после чего охлаждается на воздухе.
Мартенситное превращение происходит при медленном охлаждении на воздухе, что резко снижает внутренние напряжения и возможность коробления.
Недостатком этого способа является ограничение размеров деталей, Из-за низкой скорости охлаждения в сравнительно нагретой среде при закалке крупных деталей в их центральных зонах скорость охлаждения может оказаться ниже критической. Максимальный диаметр деталей из углеродистых сталей, закаливаемых этим способом, составляет 10 мм, легированных –20-30 мм.
При изотермической закалке, в отличие от ступенчатой, сталь выдерживается в ваннах до окончания изотермического превращения аустенита. Температура соляной ванны обычно составляет 250-350 ºC. В результате изотермической закалки получается структура бейнита с твердостью 45-55НRC при сохранении повышенной пластичности и вязкости.
Закалка с самоотпуском применяется в случае термообработки инструмента типа зубил, молотков, в которых должны сочетаться высокие твердость и вязкость. В этом случае изделия выдерживают в закалочной ванне не до полного охлаждения. За счет тепла внутренних участков происходит нагрев поверхностных слоев до нужной температуры, т.е. самоотпуск.
В структуре стали, закаленной при комнатной температуре, присутствует некоторое количество остаточного аустенита. Остаточный аустенит снижает твердость и износостойкость деталей и может приводить к изменению их размеров при эксплуатации в условиях низких температур из-за самопроивольного образования мартенсита из аустенита. Для уменьшения остаточного аустенита в структуре применяют обработку холодом.
Обработка холодом состоит в охлаждении стали ниже 0 ºC до температур конца мартенситного превращения Мк (обычно не ниже –75 ºC), получаемых в смесях сухого льда со спиртом. Обработка холодом должна проводиться сразу после закалки во избежание
Важной характеристикой стали является прокаливаемость. Прокаливаемостью называется глубина проникновения закаленной зоны. Несквозная прокаливаемость обусловлена тем, что при закалке детали аустенит охлаждается быстрее с поверхности и медленнее в сердцевине. Распределение скорости охлаждения по сечению детали показывает, что у поверхности скорость охлаждения максимальна, а в центре – минимальна (рис.10.7).
Рис. 10.7. Влияние скорости охлаждения на прокаливаемость стали
Прокаливаемость, как и критическая скорость охлаждения связана со скоростью превращения аустенита и, следовательно, с положением кривых на диаграмме изотермического превращения. За глубину прокаливаемости принимается слой с полумартенситной зоной: 50% мартенсита и 50% троостита.
Критический диаметр Dкр- максимальный диаметр сечения изделия, прокаливающегося в данном охладителе насквозь (50% мартенсита и 50% троостита)
Наиболее простой метод определения критического диаметра – метод торцевой закалки (рис.10.8).
Рис. 10.8. Схема испытания на прокаливаемость методом торцевой закалки.
После закалки измеряют твердость на боковой поверхности по высоте образца.
При сквозной прокаливаемости по сечению изделия механические свойства одинаковы, при несквозной прокаливаемости в сердцевине наблюдается снижение прочности, пластичности и вязкости металла.
Превращения при отпуске стали.
Сталь после закалки находится в метастабильном( неравновесном) состоянии. Исходной структурой закаленной стали является сильно пересыщенный углеродом раствор α - железа – мартенсит и некоторое количество остаточного аустенита. Закаленная сталь обладает высокой твердостью и прочностью, но вляется ,как правило, хрупкой.
Отпуск состоит в нагреве закаленной стали до температуры ниже точки Ас1 с целью перехода стали в более устойчивое состояние и получения при достаточно высокой прочности удовлетворительного уровня пластичности и вязкости.
Характер структурных изменений, происходящих при отпуске сталей, зависит, во-первых, от состава стали, во-вторых, - от конкретной температуры и продолжительности отпуска. Рассмотрим процессы, происходящие при отпуске углеродистых сталей.
Распад мартенсита с выделением карбидов – главный процесс при отпуске сталей. Распад мартенсита в зависимости от температуры и продолжительности отпуска проходит через стадии предвыделения, выделения промежуточных метастабильных карбидов (типа Fe3C), выделения цементита и его коагуляции.
Кроме того, структурные изменения при отпуске стали дополняются распадом остаточного аустенита.
Первая стадия отпуска углеродистой закаленной стали проходит при нагреве до 200 ºC (первое превращение при отпуске). Из мартенсита выделяются мельчайшие частицы карбидной фазы (типа Fe2.4C – ε-карбид). Одновременно тетрагональность решетки уменьшается. Образуется структура отпущенного мартенсита.
При нагреве до температур 200-300 ºC происходит распад остаточного аустенита (второе превращение при отпуске). Остаточный аустенит превращается в смесь пересыщенного α - твердого раствора и еще не обособившихся частиц карбидов, т.е. образуется отпущенный мартенсит.
Когда температура отпуска достигает 300-400 ºC, углерод полностью выделяется из α - твердого раствора с образованием Fe3C (третье превращение при отпуске). При нагреве до 400 ºC сталь состоит из относительно мелких включений феррита и цементита, образующих структуру троостита.
При нагреве до 600 ºC происходит коагуляция карбидов и полная перекристаллизация мартенсита. В результате сталь приобретает структуру сорбита (четвертое превращение при отпуске).
Ферритно-цементитные смеси, получаемые при распаде аустенита (сорбит, троостит), отличаются от ферритно-цементитных смесей, образующихся при распаде мартенсита. В первом случае сорбит и троостит имеют пластинчатую форму цементита, а во втором – зернистую форму. Разная форма цементита обусловливает различия в уровнях механических свойств. Зернистые структуры после отпуска стали обеспечивают у нее более высокие механические свойства, в первую очередь, характеризующиеся большой пластичностью и вязкостью при близкой твердости и прочности. Поскольку сталь после отпуска приобретает структуру сорбита и троостита, по внешним признакам схожую с такой же структурой, получаемой при распаде аустенита, но имеющей принципиальные различия внутреннего строения, принято сорбит и троостит, получаемые в процессе отпуска, называть сорбитом отпуска и трооститом отпуска.
Отпуск стали оказывает существенное влияние на ее механические и служебные свойства. При низких температурах отпуска (до 250 ºC) уменьшается склонность стали к хрупкому разрушению. Пластичность и вязкость стали при низкотемпературном отпуске несколько возрастает из-за уменьшения внутренних напряжений и изменений структуры стали.
С повышением температуры отпуска до 500-600 ºC в структуре стали происходят существенные изменения, сопровождающиеся заметным снижением твердости, временного сопротивления и предела текучести и повышением относительного удлинения, ударной вязкости и трещиностойкости.
Отпуск является заключительной операцией термической обработки, состоящей из нагрева стали ниже его критической точки Ас1 с последующим охлаждением, при котором формируется окончательная структура стали. Отпуск проводится после операции закалки. Изменения в структуре при нагреве закаленной стали приводят к изменению ее свойств.
Различают низкий, средний и высокий отпуск.
Низкий отпуск проводят при 150-200 ºC. Целью низкого отпуска является снижение внутренних напряжений и некоторое уменьшение хрупкости мартенсита при сохранении высокой твердости и износостойкости деталей. Структура стали после низкого отпуска представляет собой мартенсит отпуска. Основная область применения низкого отпуска – режущий и мерительный инструмент, а также машиностроительные детали, которые должны обладать высокой твердостью и износостойкостью.
Средний отпуск проводят при температуре 350-450 ºC. Цель среднего отпуска состоит в некотором снижении твердости при значительном увеличении предела упругости. Структура стали представляет собой троостит отпуска, обеспечивающий высокие пределы прочности, упругости и выносливости, а также улучшение сопротивляемости действию ударных нагрузок.
Высокий отпуск проводят при 550-650 ºC. Цель высокого отпуска – достижение оптимального сочетания прочностных и вязких свойств. Структура стали представляет собой однородный сорбит отпуска с зернистым цементитом. Область применения высокого отпуска – конструкционные стали, детали из которых подвергаются воздействию высоких напряжений и ударным нагрузкам.
Термическая обработка, состоящая из закалки с высоким отпуском, улучшающая общий комплекс механических свойств, является основным видом термической обработки конструкционных сталей. Она называется термическим улучшением.
Температуру отпуска обычно выбирают в зависимости от заданной твердости. В этом случае изделие закаливают на максимальную твердость, а затем отпуском твердость снижают до заданной.
Вязкость сталей, особенно легированных, зависит от режима отпуска: температуры, времени выдержки и скорости охлаждения после отпуска (рис.9.9). При определенных температурах и медленном охлаждении в сталях появляется отпускная хрупкость.
Принято различать отпускную хрупкость 1 и 11 рода.
Отпускная хрупкость 1 рода (необратимая) наблюдается при отпуске как легированных, так и углеродистых сталей при температуре около 300 ºC ( в интервале температур 250-400 ºC).
Рис.10.9 Зависимость ударной вязкости от температуры отпуска
Причина отпускной хрупкости 1 рода – неравномерность распада мартенсита по границам зерен и внутри зерна при отпуске. Вблизи границ карбиды выделяются интенсивнее, там создается концентрация напряжений, что делает границы зерен более хрупкими. При повышении температуры отпуска или при увеличении продолжительности нагрева структура по сечению зерна выравнивается и отпускная хрупкость 1 рода устраняется. Повторный отпуск при температуре 250-400 ºC не приводит к отпускной хрупкости.
Отпускная хрупкость 11 рода (обратимая) наблюдается при медленном охлаждении после отпуска при температурах 450-550 ºC. Этот вид отпускной хрупкости обратим, так как при повторном нагреве, но быстром охлаждении при этой же температуре он исчезает. При медленном охлаждении по границам зерен успевают выделиться мелкие карбиды, фосфиды и нитриды, которые приводят к их охрупчиванию. При быстром охлаждении эти частицы не выделяются. Этот вид хрупкости характерен для легированных сталей с повышенным содержанием хрома и марганца. Введение в сталь даже небольших количеств молибдена (0,2-0,3% Mo) или вольфрама (0,6-1,0% W) резко снижает склонность к отпускной хрупкости 11 рода.
Мерами борьбы с отпускной хрупкостью 11 рода являются охлаждение после отпуска не на воздухе, а в масле, а для крупных деталей – даже в воде, а также дополнительное легирование стали молибденом и вольфрамом.
Контрольные вопросы
1. Какая структура называется мартенситом?
2. При каких температурах начинается и заканчивается мартенситное превращение?
3. От каких факторов зависит температура начала и конца мартенситного превращения?
4. Как влияет наличие остаточного аустенита на свойства стали?
5. Чем объяснить коробление деталей и увеличение их размеров после закалки?
6. Что представляет собой технологический процесс закалки стали?
7. Какие виды закалки вам известны?
8. Какую скорость охлаждения называют критической?
9. От каких факторов зависит выбор способа охлаждения нагретой под закалку стальной детали?
10. Что называют прокаливаемостью? Что принимают за глубину прокаливаемости?
11. В чем заключается отпуск стали? Какова его цель?
12. Какие различают виды отпуска?
13. Что называют отпускной хрупкостью?
Дата добавления: 2021-07-19; просмотров: 634; Мы поможем в написании вашей работы! |
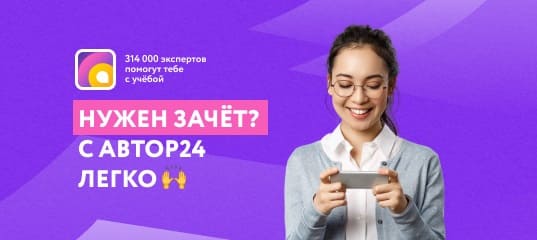
Мы поможем в написании ваших работ!