Динамический метод (по Шору )
Метод Бринелля (ГОСТ 9012)
Для определения твердости по Бринеллю в качестве твердого тела, вдавливаемого в испытуемый материал (индентор), используют стальной шарик диаметром D 2,5; 5; 10 мм, в зависимости от толщины изделия.
Испытание проводится на специальном приборе-прессе твердомере Бринелля (рис.1).
|
где P – нагрузка, кгс; F – поверхность отпечатка, мм2.
,
где D – диаметр вдавливаемого шарика, мм; d – диаметр отпечатка, мм
Рисунок 2 Схема определения
твердости по Бринеллю
Диаметр шарика и нагрузку выбирают так, чтобы соблюдалось соотношение: .
Нагрузка Р, в зависимости от диаметра шарика и измеряемой твердости: для термически обработанной стали и чугуна – , литой бронзы и латуни –
, алюминия и других очень мягких металлов –
.
Продолжительность выдержки : для стали и чугуна – 10 с, для латуни и бронзы – 30 с.
Твердость НВ выражается в кгс/мм2 (без указания размерности). Стандартными условиями являются D = 10 мм; Р = 3000 кгс; = 10 с. В этом случае твердость по Бринеллю обозначается НВ 250. При изменении условий испытаний помимо значений твердости указывается D шарика, усилие и выдержка. Например, 185 НВ /5/750/20, где 5 – D шарика, 750 – нагрузка, 20 – время выдержки под нагрузкой в секундах.
|
|
ГОСТом установлены нормы для испытаний по Бринеллю
Металлы | Твердость, HB | Толщина образца, мм | Соотношение между нагрузкой и D2 шарика | D шарика, мм | Нагрузка Р, кгс | Выдержка под нагрузкой, сек. |
Черные | 140-150 | 6-3 4-2 >2 | Р=30D2 | 10 5 2,5 | 3000 750 187,5 | 10 |
Черные | ≤140 | >6 6-3 >3 | Р=10D2 | 10 5 2,5 | 3000 250 62,5 | 10 |
Цветные | ≥130 | 6-3 4-2 >2 | Р=30D2 | 10 5 2,5 | 3000 750 187,5 | 30 |
Цветные | 35-130 | 9-3 6-3 2-3 | Р=10D2 | 10 5 2,5 | 1000 250 62,5 | 30 |
Цветные | 8-35 8-35 8-35 | >6 6-3 <3 | Р=2,5D2 | 10 5 2,5 | 250 62,5 15,6 | 60 |
При измерении НВ нет необходимости производить расчет по указанной выше формуле. На практике пользуются заранее составленными таблицами, указывающими число НВ в зависимости от диаметра отпечатка.
Метод НВ не является универсальным, т. к. он не позволяет:
|
|
· Испытывать материалы с твердостью более 450 НВ
· Измерять твердость тонкого поверхностного слоя (толщина должна быть не менее 1-2 мм), т. к. стальной шарик продавливает этот слой и проникает на большую глубину.
Метод Роквелла (ГОСТ 9013)
В качестве индентора используют алмазный конус с углом при вершине 1200 или стальной закаленный шарик диаметром 1,588 мм2. Твердость определяется глубиной проникновения индентора в образец. Испытание проводят на твердомерах – приборах Роквелла типа ТР (рис.3).
Прибор имеет черную (С) и красную (В) шкалы. Шкала «С» используется при испытаниях с помощью алмазного конуса при нагрузке 60 и 150 кгс.
|
Рисунок 3 Схема прибора для измерения Рисунок 4 Схема испытания вдавливанием алмазного конуса
твердости по Роквеллу
Конус или шарик вдавливается при приложении двух последовательных нагрузок: предварительной Р0=10 кгс, и основной Р1, так, что общая нагрузка Р=Р0+Р1 (рис.4).Нагрузка для шарика = 100 кгс.
· Измерение алмазным конусом с нагрузкой 60 кгс (HRA) применяют для очень твердых металлов, твердых сплавов, а также для измерения твердых поверхностных слоев (0,3-0,5мм) или тонких образцов-пластинок.
|
|
· Измерения алмазным конусом с нагрузкой 150 кгс (HRC) проводят:
a). для материалов средней твердости (более НВ 230), как более быстрым способом определения;
b). для закаленной или низкоотпущенной стали;
c). для определения твердости тонких поверхностных слоев (например, цементованный слой).
· Стальным шариком с нагрузкой 100 кгс (HRB) определяется твердость мягкой отожженной стали или отожженных цветных сплавов в деталях или образцах толщиной 0,8-2 мм.
Условия для испытания по методу Роквелла установлены ГОСТом
Примерная твердость по HV | Обозначе- ние шкалы Роквелла | Тип индентора | Нагрузка кгс | Пределы измерения твердости по Роквеллу |
390-900 | А | Алмазный конус | 60 | 70-85 |
60-240 | В | Шарик стальной | 100 | 25-100 |
240-900 | С | Алмазный конус | 150 | 20-67 |
Шкала по измерению твердости HRC изменена в связи с изменением эталона, поэтому в изменяемые значения следует вносить поправку. Твердость в этом случае обозначается: HRC2, она меньше HRC на 1-2 ед.
Метод Виккерса
Метод основан на вдавливании четырехгранной алмазной пирамидки с углом между противоположными гранями, равным 1360. Пирамида вдавливается под действием нагрузки Р (5/120 кгс). Твердость определяется по величине отпечатка (рис.5).
|
|
Твердость HV определяется по формуле:
Рисунок 5 Схема определения твердости
по Виккерсу где Р – нагрузка на пирамиду, d – среднее арифметическое длины обеих диагоналей отпечатка, - угол, равный 1360
Величина диагоналей определяется с помощью специального микроскопа, встроенного в прибор. Число твердости по HV определяют по специальным расчетным таблицам в зависимости от размера диагонали отпечатка и нагрузки. Числа твердости по Виккерсу и Бринеллю для материалов с твердостью до HV 400-450 практически совпадают (НВ= HV).
Измерение твердости HV перед НВ имеет преимущества:
¾ дает более точное значение твердости высокотвердых материалов;
¾ твердость по HV измеряют при значительно меньших нагрузках;
¾ малые нагрузки обеспечивают меньшую глубину отпечатка и позволяют измерять твердость тонких (до 0,3-0,5мм) деталей.
Способ микротвердости
Способ микротвердости – для определения твердости отдельных структурных составляющих и фаз сплава, очень тонких поверхностных слоев (сотые доли миллиметра).
Аналогичен способу Виккерса. Индентор – пирамида меньших размеров. Нагрузки при вдавливании Р составляют 5…500 гс
Метод царапания
Алмазным конусом, пирамидой или шариком наносится царапина, которая является мерой. При нанесении царапин на другие материалы и в сравнении их с мерой судят о твердости материала.
Можно нанести царапину шириной 10 мм под действием определенной нагрузки. Наблюдают за величиной нагрузки, которая дает эту ширину.
Динамический метод (по Шору )
Шарик бросают на поверхность с заданной высоты, он отскакивает на определенную величину. Чем больше величина отскока, тем тверже материал.
Дата добавления: 2021-07-19; просмотров: 176; Мы поможем в написании вашей работы! |
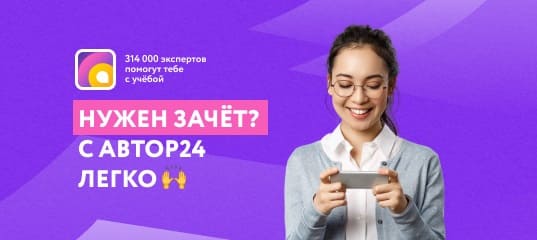
Мы поможем в написании ваших работ!