Контроль качества выполнения технического обслуживания.
ПРАКТИЧЕСКАЯ РАБОТА №47 по ТО
Тема: Технологический процесс ремонта автомобилей
Цель занятия: Изучить технологический процесс капитального ремонта автомобилей
Время выполнения: 2часа
Задание:
1. Описать технологический процесс подготовки автомобиля к капитальному ремонту
2.Составить схему капитального ремонта автомобиля.
3.Вывод.
Ход работы:
1. Технологический процесс капитального ремонта предусматривает три основных этапа:
первый – разборочные, моечно-очистительные процессы, дефектоскопию деталей;
второй – процессы по восстановлению деталей и узлов;
третий – сборочные процессы, включающие приработку агрегатов и испытание автомобилей.
Особенности технологического процесса авторемонта по сравнению с производством следующие: процесс ремонта начинается с разборки автомобиля; процесс производства – с изготовления заготовок деталей. При ремонте обязательной операцией является дефектоскопия деталей, на заводе такой операции нет. При ремонте сборка происходит из деталей ранее работавших в узлах и агрегатах (восстановленные или оказавшиеся годными), но они отличаются от новых из которых собираются автомобили на заводе. Рассмотрим технологическую цепочку капитального ремонта.
|
|
Прием автомобиля в ремонт.
Разборочные работы.
Мойка, обезжиривание деталей и удаление отложений.
Удаление нагара.
Дефектоскопия деталей.
Сортировка деталей.
Восстановление деталей ремонтными размерами.
Восстановление деталей постановкой дополнительных ремонтных деталей.
Прием автомобиля в ремонт.
Автомобили, сдаваемые в капитальный ремонт, должны передвигаться своим ходом. В ремонт автомобили принимаются в соответствии с существующими Едиными техническими условиями на сдачу в капитальный ремонт и выдачу из капитального ремонта автомобилей, агрегатов и узлов. В этих технических условиях указывается, что автомобиль должен быть комплектным, а детали должны иметь только естественный износ. Замена деталей перед отправкой автомобиля или агрегата в ремонт не допускается. При сдаче автомобиля в капремонт необходимо иметь наряд на ремонт, справу о техническом состоянии автомобиля, паспорт для автомобиля и двигателей ранее подвергавшихся капремонту, техпаспорт автомобиля. По результатам приема составляют приемо-сдаточный акт.
Разборочные работы.
Перед разборкой автомобиль моют горячей водой под давлением до 1,5…2,0 МПа. Это обеспечивает надлежащие условия последующих работ по демонтажу агрегатов и узлов. После этого выполняют очистительные операции. Так, разборку агрегатов производят после наружной очистки и обезжиривания с выпариванием острым паром емкостей для масла двигателя, коробки передач и т.д. Подразборка агрегатов производится на тупиковых постах, полная разборка производится как на тупиковых постах, так и на поточных линиях в зависимости от сложности агрегата. Количество повторно используемых деталей при восстановлении автомобилей и производительность рабочих на разборочных операциях в значительной степени определяется технологичностью конструкции автомобиля, т.е. его приспособленностью к разборочным операциям.
|
|
Мойка, обезжиривание деталей и удаление отложений.
На агрегатах и деталях могут быть следующие виды отложений: дорожная промасленная пыль и грязь, жировая пленка, накипь и нагар. Для обезжиривания деталей применяют различные растворы. После обезжиривания детали ополаскивают горячей водой, что предохраняет их от коррозии. Имеются в широком ассортименте синтетические поверхностные моющие средства, которые не вызывают коррозии черных и цветных металлов, не оказывают вредного воздействия на кожу и одежду, поэтому детали после их обезжиривания не нуждаются в ополаскивании. Процесс обезжиривания ведется при невысоких температурах. Для обезжиривания используют такие вещества как сульфонол, керосин и бензин с последующей промывкой жидким маслом (веретенным).
|
|
Для мойки и обезжиривания деталей применяют различные моечные установки и машины. Последние бывают однокамерными, в которых мойка производится только раствором, и многокамерными, в которых детали обмывают раствором, ополаскивают горячей водой, а иногда обдувают воздухом.
Удаление нагара.
Нагар откладывается на ряде деталей двигателя: на стенках камер сгорания, на тарелках клапанов, во впускном и выпускном трубопроводе и др. Нагар образуется вследствие неполного сгорания топлива и масла.
Для удаления нагара применяют щелочные растворы. Детали, имеющие нагар, погружают в ванну с температурой раствора 80 – 90° С на 40 – 60 мин. Часто для очистки деталей от нагара применяют косточковую крошку. Установка, используемая для этой цели, по принципу действия аналогична пескоструйной. Широко также используется ультразвуковая мойка, в результате которой детали как обезжириваются, так и очищаются от нагара. Под влиянием ультразвуковых колебаний в жидкости возникают кавитационные пузырьки, разрушение которых сопровождается мощными гидравлическими ударами. В результате этого молекулярные силы сцепления жировых загрязнений с металлом обрабатываемой детали ослабевают и они отрываются от ее поверхности. Жировые загрязнения превращаются в эмульсию, уносимую моющим раствором.
|
|
Удаление накипи.
В состав накипи могут входить карбонат кальция (СаСО3) и магния (МgCO2), гипс (СаSO4) и силикаты с большим содержанием окиси кремния (SiO2). Количество отлагающейся накипи зависит от жесткости применяемой воды, пробега автомобиля, режима работы двигателя, а также от того, как часто добавляют или заменяют воду. Присутствующие в воде растворенные бикарбонаты кальция и магния при их нагревании превращаются в нерастворимые карбонаты, которые вместе с другими минеральными солями и ржавчиной от коррозии деталей системы охлаждения образует плотный слой накипи, обладающей низкой теплопроводностью. Наблюдается перегрев стенок цилиндра и ухудшается рабочий процесс.
Отложение накипи и образование шлама способствует более интенсивной коррозии металла деталей охлаждения. Для удаления накипи применяют щелочные или кислотные растворы. Для стальных и чугунных деталей применяют растворы соляной кислоты с концентрацией 5…10%, ингибированные техническим уротропином (3…4 г/л) с температурой 60° С.
Для снятия накипи с деталей из алюминиевых сплавов применяют 6-процентный раствор молочной кислоты с температурой 30 – 40° С. Для предохранения деталей от коррозии их промывают в растворе хромпика концентрации 0,5 – 1,0%.
Дефектоскопия деталей.
Дефектоскопия – методика и способы обнаружения дефектов деталей без нарушения их целостности. Дефекты деталей классифицируют в зависимости от причин их появления последующим их признакам: дефекты, вызванные недостатком конструкции детали; дефекты, связанные с нарушением технологии изготовления; дефекты, появляющиеся вследствие недостатков технологического процесса изготовления детали; дефекты в результате естественного изнашивания; дефекты, возникающие из-за нарушений инструкции по эксплуатации автомобиля; дефекты аварийного характера.
Недостатком конструкции могут быть: выбор материала, несоответствующего условиям работы детали, назначение размеров не соответствующих нагрузочным режимам, неправильный выбор сопряжений, термообработки, покрытий, смазки и т.д.
Нарушениями технологии изготовления деталей могут быть: неправильная замена материала, отклонение от предусмотренных посадок сопрягаемых мест, нарушение термообработка и т.д.
Недостатком технологии изготовления является операция старения с целью снятия внутренних напряжений при отливке или штамповки, отсутствие операции старения корпусных деталей и т.д.
Естественный износ сопрягаемых мест деталей является изменение первоначальных размеров сопрягаемых поверхностей. Примерами нарушений инструкции по эксплуатации автомобилей является работа с недопустимыми перегрузками, когда действуют нагрузки, превосходящие расчетные.
Дефекты аварийного характера появляются из-за внутренних пороков или усталости материала детали. Дефектоскопию деталей производят согласно Техническим условиям, разрабатываемым для всех без исключения деталей. ТУ на дефектоскопию содержат эскиз детали с указанием номера, материала и термообработки. В них также указывают перечень дефектов при наличии которых деталь выбраковывают.
В зависимости от конструкции и назначения деталей дефектовка может быть произведена путем внешнего осмотра, испытания на специальных установках, замера геометрических размеров при помощи мерительных инструментов и приборов.
Дефектоскопия внешним осмотром.
Все без исключения детали поступившие на дефектоскопию подвергаются внешнему осмотру при котором определяются трещины, изломы, раковины, вмятины, срыв граней, резьбы и др. Ответственные и сложные детали помимо осмотра проверяют на специальных установках. Так, блоки и головки цилиндров проверяют на герметичность путем опрессовки на гидравлической установке.
Радиаторы и топливные баки проверяют на герметичность, погружая их в воду и нагнетая внутрь воздух под избыточным давлением до 0,5 кг/см2. По появлению пузырьков обнаруживаются дефекты герметичности радиатора. Скрытные трещины могут быть обнаружены различными средствами: рентгеновскими установками, магнитными или ультразвуковыми дефектоскопами, применением флуоресцирующей жидкости и источника ультрафиолетового света. В авторемонтном производстве получил распространение способ магнитной дефектоскопии, как простой, точный и не требующий сложного оборудования.
Если через деталь проникает магнитный поток, то при наличии трещин, раковин, нарушающих магнитную проницаемость металла, направление магнитного потока будет искажаться, причем форма и направление искажения соответствует форме и размерам дефекта (можно с помощью магнитного порошка).
Помимо стационарных, имеются передвижные и переносные дефектоскопы.
Дефектоскопия проверкой геометрических размеров.
Коробление плоскостей проверяют на контрольных плитах при помощи щупов. Изгибы и скручивания стержней балок и валов проверяют шаблонами мерительными инструментами на приспособлениях.
Схема для проверки шатуна на изгиб следующая: чугунная станина, каретка, в верхнюю головку шатуна вставляют палец, в нижнюю – центратор. Устанавливают шатун в приборе так, чтобы он лежал на наклонных призмах зажимов, а оправка центратора – на призмах каретки. Подводя призмы каретки до соприкосновения с оправкой центратора, определяют наличие изгиба и скручивания посредством щупов.
Для контроля размеров и относительного расположения изнашивающихся поверхностей деталей применяют скобы, пробки, шаблоны, штихмасы, штангенциркули, микрометры, индикаторы и др.
В Технических условиях (ТУ) на дефектоскопию приводятся номинальные, предельные и допустимые размеры детали, зазоры и натяги в сопряжениях. По результатам специально поставленных исследований и обобщения опыта эксплуатации, которые обосновывают величины предельных и допустимых износов, выявляют причины повреждений и исследуют рациональные способы восстановления деталей.
Предельным называется такой износ детали, до достижения которого сопряжение, узел, агрегат работают нормально.
Допустимым называется такой износ детали, при котором она без восстановления может прослужить до следующего капитального ремонта автомобиля. Необходимо, чтобы величина этого износа не влияла на показатели работы автомобиля, который должен без повреждений проработать в течение межремонтного цикла. Интенсивность износа трущихся поверхностей деталей не одинакова во времени работы автомобиля.
После того, как сопряженные поверхности приработались, интенсивность износа уменьшается и наступает период работы, в течение которого зазор в сопряжении увеличивается постепенно вследствие нормального износа трущихся поверхностей.
После пробега L3 зазор между деталями становится настолько большим (точки 3 и 31), что появляются дополнительные динамические нагрузки на детали, приводящие в свою очередь, к прогрессирующему возрастанию износа и дальнейшему увеличению зазора между деталями. Зазор cd является предельным, при котором работа сопряжения становится опасной, так как может наступить разрушение детали и отказ автомобиля в работе.
Техническими условиями на дефектоскопию деталей предусматриваются допустимые износы ае и bf (точки 2 и 21), при наличии которых детали признаются годными для дальнейшей эксплуатации в течение следующего межремонтного цикла автомобиля. Последний должен быть меньшим или равным пробегу, равному разности L3- L2 . Следовательно, при определении допустимого износа должны быть известны: межремонтный цикл автомобиля, величина предельного износа и соответствующий этому износу пробег L3, т.е. интенсивность износа.
Сортировка деталей.
В результате дефектоскопии все детали сортируют на три группы: годные, требующие ремонта и непригодные. Каждую группу маркируют краской определенного цвета. Годные детали направляют на комплектацию агрегатов, требующих ремонта, в соответствующие цехи для ремонта, а негодные детали – в утиль.
На все детали, прошедшие контроль, составляют дефектовочную ведомость, в которой указывают общее количество одноименных деталей, а также количество годных, требующих ремонта и негодных деталей.
Анализ дефектовочных ведомостей и получаемых из них коэффициентов сменности и ремонта, а также наблюдение за износом отдельных деталей, изучение характера и причин появления дефектов имеют большое значение для конструкторов автомобилей.
Требованием эксплуатации к конструкции агрегата является примерно равная износостойкость его деталей.
В этом случае после истечения ремонтного цикла все детали данного агрегата будут нуждаться в ремонте одновременно, в период же межремонтного пробега агрегат будет работать надежно.
Детали, подлежащие восстановлению, направляют в соответствующие производственные цехи. В зависимости от сложности детали и характера ее дефекта стоимость восстановления находится в пределах 3…30% стоимости новой детали. При этом, чем сложнее и дороже деталь, тем ниже относительная стоимость ее восстановления. Следовательно, восстановление деталей экономически оправдано.
Дефекты деталей делятся на три основные группы:
- естественные износы, при которых происходят изменения геометрической формы и размеров сопрягаемых поверхностей деталей;
- механические повреждения (деформации, трещины, обломы, выкрашивания, надиры, пробоины);
- повреждения антикоррозионных покрытий и коррозия металла деталей.
Основным назначением восстановления каждой детали является восстановление ее механической прочности, посадок в сопрягаемых поверхностях, износостойкости и антикоррозионной стойкости в целях обеспечения надежной работы в течение всего межремонтного срока службы автомобиля.
Особенности комплектования деталей, сборки узлов и агрегатов.
Особенностью комплектования в авторемонтном производстве является наличие различных по точности групп деталей, поступающих на сборку. На сборку поступают детали, признанные при дефектовке годными, однако имеющие допустимый износ; восстановленные детали; новые детали, поступающие на авторемонтный завод в качестве запасных частей.
Такое многообразие деталей при сборке по методу полной взаимозаменяемости часто приводит к появлению увеличенных зазоров и натягов в сопряжениях, не соответствующих требованиям технических условий на сборку. Объясняется это тем, что восстановленные детали и детали, признанные годными, не укладываются в допуски на геометрические параметры. Поэтому в авторемонтном производстве при сборке наряду с полной взаимозаменяемостью применяют метод регулировки с использованием неподвижных компенсаторов - регулировочных прокладок и шайб, а также метод селективного подбора деталей.
Сборка агрегатов на авторемонтном заводе аналогична сборке на автомобильном заводе, за некоторым исключением. Приработка и испытание агрегатов на авторемонтном заводе аналогична этим операциям на автомобильном заводе.
Обкатка автомобиля.
Новые и поступающие из капитального ремонта автомобили проходят обкатку, согласно инструкции заводов-изготовителей и авторемонтных предприятий. Продолжительность обкатки регламентируется инструкциями заводов-изготовителей.
В течение периода обкатки необходимо:
- не превышать величины полезной нагрузки, установленной заводом-изготовителем;
- избегать движения по тяжелым дорогам;
- не начинать движения с непрогретым двигателем и не давать работать холодному двигателю с большим числом оборотов;
- не заменять в двигателе и агрегатах автомобиля масло и смазки, залитые на заводе;
- следить за температурой тормозных барабанов;
- следить за температурой ступиц колес. При значительном их нагреве ослабить их затяжку подшипников ступиц;
- следить за креплениями автомобиля и соединениями трубопроводов. Ослабленные болты – подтягивать. При обнаружении течи масла, топлива, воды и тормозной жидкости – устранить течь.
По окончании обкатки следует: подтянуть гайки головки цилиндров, выполнить ТО-2, сменить масло в картере двигателя после его промывки, снять ограничительную шайбу или ограничительный винт, установленный на рычаге дроссельной заслонки.
Контроль качества выполнения технического обслуживания.
Контроль осуществляют водитель автомобиля и ОТК АПТ. Качество технического обслуживания и технического ремонта оценивают по результатам проверки автомобиля на КПП, а также непосредственно наблюдением работников ОТК за выполнением работ в зонах ТО или ремонта.
При этом работники ОТК обязаны следить за соблюдением установленных периодичностей и объемов ТО.
Водитель обязательно должен проверить автомобиль перед выездом на линию и следить за его состоянием при работе.
На каждый автомобиль, проходящий КПП заполняют Листок учета технического обслуживания и ремонта автомобиля. В листе записывают вид ТО, дату и время выполнения работ, а при текущем ремонте – содержание заявки водителя, наименование агрегата и неисправности, причину последней. Выполнение работ подтверждается подписью и штампом представителя ответственного за работу.
На каждый автомобиль на АТП заводят “Лицевую карточку автомобиля”. В нее из путевых листов нарастающим итогом записывают ежедневный пробег автомобиля, а условными знаками на основании листов учета ТО отмечают выполнения технического обслуживания (по видам, датам и пробегу), ремонта и замену агрегата
2.
Дата добавления: 2021-07-19; просмотров: 39; Мы поможем в написании вашей работы! |
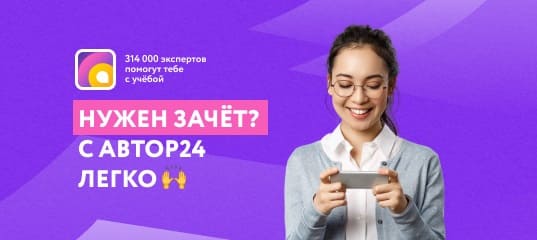
Мы поможем в написании ваших работ!