Особенности развития и размещения отраслей цветной металлургии
Металлургический комплекс – совокупность отраслей, производящих разнообразные металлы и изделия из них.
Металлургический комплекс состоит из двух крупных отраслей — чёрной и цветной металлургии. Чёрная металлургия занимается добычей и производством железа, стали, чугуна. Отличительной особенностью развития данной промышленности является большая материалоёмкость производственного процесса. Основным направлением развития чёрной металлургии является использование всех ценных компонентов сырья, а также промышленных отходов.
С этой целью металлургическое производство включает в себя цеха и заводы других отраслей промышленности, примерами которых могут служить химическое производство, производство стройматериалов. Таким образом, характерной чертой чёрной металлургии становится интеграция производств различных отраслей промышленности. Так, например, крупный металлургический комбинат вначале выплавляет из железной руды чугун, а затем из него производят сталь.
Развитие чёрной металлургии требует значительных объёмов капиталовложений, из которых около тридцати процентов необходимо направлять на экологическую чистоту металлургических производств. В основном металлы чёрной металлургии используют в отрасли машиностроительного производства. Машиностроение, как крупный потребитель металла, имеет очень тесные связи, прежде всего, с чёрной металлургией.
|
|
Цветная металлургия занимается добычей и производством цветных металлов.
По своим физическим свойствам цветные металлы подразделяются на тяжёлые и лёгкие.
К промышленным способам добычи металлов относят следующие способы:
Отличительной особенностью развития цветной металлургии является высокая энергоёмкость сырья производственного процесса. С этой целью производства цветной металлургии размещают в областях, наиболее обеспеченных электроэнергией. Размещение производств цветной металлургии преимущественно ориентировано на энергетический, транспортный и особенно на потребительский факторы.
Таким образом, производство чёрной и цветной металлургии включает в себя:
· Добычу руды чёрных и цветных металлов.
· Изготовление металлов из природного сырья.
· Получение различных сплавов с определёнными свойствами.
· Переработку и отделку металлов.
Чёрная и цветная металлургия имеют ряд общих черт. Во-первых, высокий уровень комбинирования производства. Металлургия включает в себя не только производство металлов, к ней относятся и другие производства, связанные с получением металлов: добыча и подготовка руды, топлива и прочее. Поэтому основная часть чёрных и цветных металлов производится на так называемых комбинатах.
|
|
В чёрной металлургии основа комбинирования — последовательная переработка сырья (руда —> чугун —> сталь —> прокат). В цветной — его комплексное использование, поскольку из руд цветных металлов одновременно можно получить несколько металлов.
Во-вторых, большой расход исходных материалов. Для получения одной тонны стали необходимо затратить семь тонн разнообразного сырья и топлива. В цветной металлургии их потребление ещё больше. Таким образом, металлургия относится к отраслям с высокой материалоёмкостью.
В-третьих, металлургия — крупный загрязнитель окружающей среды. На долю чёрной металлургии приходится одна седьмая, а на долю цветной — одна пятая промышленных выбросов в атмосферу. Ежегодно металлургические предприятия выбрасывают в атмосферу до десяти миллионов тонн вредных веществ. Сброс каждой из отраслей металлургии загрязнённых сточных вод составляет пять процентов. Российские металлургические предприятия, как правило, имеют большую мощность и расположены непосредственно в городах, поэтому они определяют в них экологическую ситуацию и уровень заболеваемости населения.
|
|
Можно ли добывать руду, не нарушая ландшафты? Можно! На помощь приходят геотехнологии. Геотехнология – это наука, изучающая способы и процессы освоения недр. Она создаёт теоретические основы и инженерные решения эффективной, экономически и экологически целесообразной разработки месторождений, строительства и эксплуатации горнодобывающих и других подземных сооружений. При использовании геотехнологий в одну из пробурённых скважин закачивают растворитель руды. По другой скважине полученный под землёй рудный раствор выкачивают на поверхность.
Геотехнологический способ извлечения металлов
Особенности развития и размещения отраслей цветной металлургии
Цветная металлургия является одной из важнейших отраслей тяжелой индустрии, которая специализируется на добыче, обогащении и металлургическом переделе руд цветных, благородных и редких металлов, включая производство сплавов, прокат цветных металлов и переработку вторичного сырья (металлолома). Она влияет на развитие многих отраслей народного хозяйства и способствует ускорению научно-технического прогресса.
Производственные связи цветной металлургии с другими отраслями промышленности необычайно широкие. Цветная металлургия связана с машиностроением, поставляя ему конструкционные материалы: авиа- и моторостроением, станкостроением, электро- и радиотехникой, космической и химической промышленностью, черной металлургией. Цветные металлы применяются в самых разнообразных отраслях промышленности: в электро- и радиопромышленности - медь и алюминий (токонесущие части машин и аппаратов, провода, кабели), вольфрам (электро- и радиолампы), свинец (аккумуляторы, кабели); в машиностроении и приборостроении - почти все цветные металлы; в черной металлургии - легирующие добавки, раскислители; в строительстве - алюминий, медь и их сплавы; в судостроении - никель, алюминий; в фармацевтической промышленности - магний, марганец, серебро, цинк; в производстве красок - хром, цинк, свинец, барий, титан и т.д.
|
|
Развитие атомной техники невозможно без урана, а также таких элементов, как стронций, литий, цирконий, торий, цезий и их сплавов. Чистый цирконий является лучшим конструкционным материалом для атомных котлов, титан играет огромную роль в ракето- и авиастроении. Для радиотехники, электроники и автоматики применяются германий, селен, рубидий и другие полупроводниковые элементы.
Широкое использование большинства цветных металлов объясняется присущими им особыми свойствами: высокой электро- и теплопроводностью, антикоррозийностью, тугоплавкостью, жаропрочностью, небольшим удельным весом и т.д.
По своим физическим свойствам и экономическому назначению цветные металлы подразделяются условно на четыре группы:
1. Основные цветные металлы:
а) тяжелые (медь, свинец, цинк, олово, никель);
б) легкие (алюминий, магний, титан, натрий и др);
в) малые (ртуть, сурьма, висмут, кадмий, кобальт, мышьяк).
II. Легирующие (вольфрам, молибден, ванадий, тантал, ниобий).
III. Редкие металлы и рассеянные элементы (германий, радий, селен, уран, торий, цирконий и др.).
IV. Благородные металлы (золото, серебро, платина с платиноидами).
В связи с разнообразием использования сырья и широким применением цветных металлов в современном народном хозяйстве цветная металлургия характеризуется сложной структурой. В ее состав входят алюминиевая, медная, свинцово-цинковая, никель-кобальтовая, титано-магниевая, оловянная, вольфрамо-молибденовая, благородных металлов, твердых сплавов, редких металлов и другие отрасли.
Цветная металлургия активное влияние оказывает на территориальную организацию производительных сил. Она является отраслью специализации Урала, Восточной Сибири, Дальнего Востока и Севера, способствует формированию территориально-производственных комплексов - Саянского, Братско-Усть-Илимского, Норильского и др. Цветная металлургия выступает в качестве градообразующей отрасли таких промышленных центров, как Норильск, Красноярск, Ревда, Медногорск, Братск, Мончегорск и др.
Особенностью цветной металлургии является объединение большого количества разнохарактерных производств, различающихся по видам металлов и отдельным стадиям технологического процесса. Цветная металлургия рассматривает освоенные процессы производства примерно 90 цветных и редких металлов, редкоземельных и других элементов, т.е. подавляющую часть периодической системы Д.И. Менделеева. Металлургическая переработка руд или концентратов цветных металлов имеет для каждого металла или элемента свою технологию и экономику. В экономической практике нет единой металлургии цветных металлов, а есть металлургия меди, свинца, алюминия, никеля и т.д.
Цветная металлургия отличается от других отраслей самостоятельностью отдельных стадий производственного процесса:
1. Добыча руд и песков или горнорудное производство;
2. Обогащение руд и песков и получение концентрата;
3. Металлургическая переработка концентратов, руд и лома и получение чистого металла;
4. Обработка цветных металлов, придание им определенной формы для лучшего использования в других отраслях промышленности и получение различных сплавов.
Каждая стадия имеет самостоятельную экономику и может быть отдалена во времени и в пространстве.
Второй отличительной особенностью отрасли является низкое содержание полезного вещества в рудах и песках. Так, содержание меди в рудах редко превышает 1-5%, свинцово-цинковые руды имеют в своем составе обычно 1,6 - 5,5% свинца, 4-6% цинка, 0,4-1,0% меди и 0,25% кобальта. Практически для получения одной тонны меди часто требуется свыше 100 т руды, одной тонны никеля - около 200 т, а одной тонны олова - свыше 300 т руды. Расход же сырья на производство редких и рассеянных металлов в сотни и тысячи раз превосходит вес готовой продукции. Содержание меди в концентратах после обогащения возрастает до 8-35%, свинцовых - до 30-78%, цинковых - до 46-62%, оловянных - до 40-60%.
Третьей особенностью цветной металлургии является комплексность руд. Все руды цветных металлов - комплексные, содержащие не один, а несколько металлов, что придает огромное практическое значение комплексному использованию сырья. Так, медные руды Урала содержат до 25, а в некоторых случаях до 50 ценных компонентов. Дополнительные компоненты в рудах являются чрезвычайно дефицитными и в большинстве случаев не образуют самостоятельных месторождений. Поэтому получить их можно только при комплексном использовании руд (например, селен, теллур, индий, галлий и др.).
Кроме того, особенностями отрасли является то, что месторождения цветных металлов имеют небольшие запасы, не позволяющие организовать производство в значительных объемах, а также размещение предприятий в малообжитых районах, в высокогорной местности, в районах с экстремальными природно-климатическими условиями.
К основным факторам, влияющим на развитие и размещение отраслей цветной металлургии, относятся следующие: природный (сырьевой), топливно-энергетический, транспортный, научно-технический прогресс, трудовых ресурсов, потребления, времени.
Горнообогатительные предприятия размещаются под влиянием природного (сырьевого) фактора. К этому фактору можно отнести экономико-географическое положение, горно-геологические условия месторождения, климатические особенности. В медной, свинцово-цинковой и оловянной промышленности обогатительные фабрики расположены вблизи сырья.
Метод селективной флотации позволил использовать руды с весьма низким содержанием металлов, которые раньше считались непромышленными.
Транспортный фактор имеет большое значение при размещении фабрик в медно-никелевой и свинцово-цинковой промышленности.
Размещение металлургических предприятий зависит от топливно-энергетического фактора. Большое значение при размещении цинковых дистилляционных заводов имеет наличие поблизости качественного угля, так как на одну тонну цинка потребляется 4-5 т угля. Никелевые заводы на 1 т никеля расходуют 40-50 т топлива, глиноземные заводы потребляют также значительное количество угля. К энергоемким отраслям, потребляющим большое количество электроэнергии, относятся алюминиевая и магниевая промышленность, производство электролитической меди, цинка, никеля и других металлов. Расход электроэнергии на одну тонну алюминия-сырца составляет 15 тыс. кВтч, а удельный вес электроэнергии в себестоимости продукции заводов достигает 25-50%.
На размещение предприятий цветной металлургии большое влияние оказывает наличие высококвалифицированных кадров, фактор потребления (заводы по обработке цветных металлов размещаются в Москве, Санкт-Петербурге, Туле, Кольчугино).
Цветная металлургия относится к числу наиболее старых отраслей промышленности. Однако в дореволюционный период она отличалась низким технико-экономическим уровнем и Россия производила (не считая благородных металлов) только медь, свинец, цинк, олово и некоторые другие металлы. Лучшие месторождения сырья эксплуатировались иностранными компаниями, на долю которых приходилось свыше 4/5 основного капитала в цветной металлургии. Территориально добыча и переработка руд цветных металлов была сконцентрирована на Урале, в Сибири, Казахстане и Закавказье.
За годы индустриализации народного хозяйства в развитии и размещении цветной металлургии произошли глубокие структурные и территориальные сдвиги. Создана крупная база цветных и редких металлов, возникли алюминиевая, титано-магниевая, никель-кобальтовая и другие отрасли промышленности. СССР вышел на второе место в мире по выплавке большинства цветных металлов. В настоящее время отрасль производит 90 цветных металлов, тогда как в дореволюционный период их выплавлялось лишь 16.
Основными отраслями цветной металлургии являются алюминиевая, медная, свинцово-цинковая, никель-кобальтовая, титано-магниевая, оловянная, вольфрамо-молибденовая и золотодобывающая.
Доля России в мировом производстве шести основных видов цветных металлов (алюминий, никель, медь, цинк, свинец и олово) составляет около 8,5%. На экспорт поставляется около 80% от общего производства основных цветных металлов и 70% редких металлов. Таким образом, российская металлургия функционирует в общей системе мировых хозяйственных связей, и ее состояние в значительной степени зависит от тенденций развития мировой металлургии.
Алюминиевая промышленность занимает первое место в цветной металлургии по объему производства, обогнав традиционные цветные металлы, что обусловлено выдающимися свойствами алюминия. Этот материал используется прежде всего в транспортном машиностроении (алюминиевые сплавы составляют 70% всей массы самолета, вес алюминиевых деталей в легковом автомобиле достигает 100 кг), в строительстве и упаковочной индустрии. Кроме того, алюминий применяется в энергомашиностроении и электротехнике, быту и других отраслях.
На 1 т глинозема в среднем расходуется 2,5 т бокситов или 4-6 т нефтелинов. Переработка нефтелинов, связанная с довольно крупными удельными расходами сырья, а также известняков (15 т на одну тонну глинозема) и топлива, обычно осуществляется на месте. Производство глинозема, относящееся к первой стадии отрасли, приближено к сырью.
Выплавка металлического алюминия (вторая стадия) может производиться вблизи сырьевых районов, т.е. там, где выпускается глинозем, либо территориально разобщена и приурочена к источникам дешевой электроэнергии. Для производства одной тонны алюминия требуется примерно 1900 кг глинозема, 50 кг фтористых солей, 550 кг угольных электродов и 13,5 тыс. кВтч электроэнергии. Важную роль в размещении алюминиевых заводов играют ГЭС, что дает возможность получать дешевый металл.
Основой для организации энергоемкого алюминиевого производства стал план электрификации России - ГОЭЛРО. Первая ГЭС, сооруженная по этому плану в 1926г. на реке Волхов, послужила энергетической базой для первого в стране алюминиевого завода - Волховского (он был построен в течение 1930-1932 гг.). Высококремнистые бокситы для завода добывались на Тихвинском месторождении. В 1931г. в Ленинграде был создан научно-исследовательский институт алюминиевой, магниевой и электродной промышленности.
В 1933г. благодаря строительству крупнейшей в Европе электростанции Днепрогэс сдан в эксплуатацию Днепровский алюминиевый завод в Запорожье. Здесь же был построен и электродный завод. Глинозем поступал из Волховского алюминиевого завода.
В 1938г. начал давать продукцию Тихвинский глиноземный завод, а в 1939г. вступил в эксплуатацию Уральский алюминиевый завод в Каменске-Уральском, сырьевой базой которого явились высококачественные североуральские бокситы.
Во время войны были построены Новокузнецкий и Богословский (в Краснотурьинске) алюминиевые заводы. В послевоенный период наряду с восстановлением предприятий в Волхове, Тихвине и Запорожье началось сооружение новых и расширение действующих заводов.
В 50-е гг. прошлого века введены в строй заводы в Северном (Кандалакшский и Надвоицкий), Закавказском (Канакерский и Сумгаитский) и Поволжском (Волгоградский и Самарский) районах.
Высокими темпами развивалась алюминиевая промышленность в восточных районах на базе дешевой электроэнергии мощных ГЭС, а также тепловых электростанций, работающих на углях открытой добычи. Здесь сооружены крупные алюминиевые заводы - Иркутский, Братский и Красноярский, Ачинский глиноземный комбинат, перерабатывающий нефелиновую руду, открытую в Красноярском крае и Кемеровской области.
В России впервые в мировой практике освоена комплексная переработка нефелинового сырья на глинозем, содопродукты и цемент, что позволило значительно расширить сырьевую базу отрасли. На этом виде сырья работают Волховский и Пикалевский заводы в Ленинградской области и Ачинский глиноземный завод.
Как отмечалось выше, отдельные стадии отрасли могут быть размещены в разных местах. Практически в России первая стадия (производство глинозема) осуществляется частью на месте добычи сырья (Бокситогорский, Каменск-Уральский и Ачинский глиноземный заводы), частью в районах производства металлического алюминия (Волховский алюминиевый завод). Ряд алюминиевых заводов используют глинозем от других предприятий (Новокузнецкий, Красноярский, Братский).
Территориальное размещение алюминиевой промышленности в России нельзя считать рациональным. Большинство заводов расположено в европейской части, которая отличается напряженным энергетическим балансом (ежегодный дефицит топлива здесь составляет 50 млн. т у.т.). В связи с большой энергоемкостью производства заводы Урала превращены в глиноземные. Выплавка алюминия в России переносится в районы, имеющие возможность вырабатывать большие объемы электроэнергии.
Восточная Сибирь является крупнейшим в мире производителем алюминия, на долю которой приходится 1/9 мировой выплавки металла. Братский алюминиевый завод (БрАЗ) имеет производственную мощность в 1,0 млн. (первое место в мире), Красноярский (КрАЗ) мощностью 0,75 млн. (второе место) и Саянский (СаАЗ) мощностью в 0,5 млн. т (третье место), а также Шелеховский заводы используют дешевую электроэнергию Ангаро-Енисейского каскада ГЭС. Использование электроэнергии с низкой себестоимостью позволяет заводам региона экономить на 1 т не менее 100 долл. по сравнению со среднемировыми издержками.
Алюминиевые заводы района получают глинозем с Ачинского (мощность 800 тыс. т) и Богословского (г. Краснотурьинск, мощность 850 тыс. т) глиноземных комбинатов.
В России недостаточное развитие получила заключительная стадия алюминиевой индустрии – это предприятия по глубокой переработке алюминия (производство проката, фольгопрокатные и кабельные). Эти производства в 90-е гг. испытали тяжёлый экономический спад, когда производство алюминиевого проката сократилось в 10 раз. Являясь крупнейшим в мире экспортёром алюминия, Россия в больших объёмах вынуждена импортировать алюминиевую ленту и банки для пивоваренной промышленности, стоимость одной тонны которых в 3-4 раза выше, чем алюминия.
Медная промышленность имеет высокий уровень развития в Восточной Сибири, где функционирует крупнейший в России Норильский горно-металлургический комбинат. Он использует сульфидные медно-никелевые руды Талнахского и Октябрьского месторождений. На комбинате, объединяющем все стадии технологического процесса, производятся медь, никель, кобальт, платина (вместе с платиноидами) и некоторые редкие металлы. Утилизируя отходы производства, здесь получают серную кислоту, соду и другие химические продукты. На долю Норильского горно-металлургического комбината и Надеждинского металлургического завода, а также других предприятий, расположенных в Норильском промышленном районе и Мончегорске (Мурманская обл.), приходится 54% общероссийского производства меди, более 37 % - на долю завода "Уралэлектромедь" в г. Верхняя Пышма (Свердловская обл.). Большие перспективы Восточно-Сибирского региона связаны с освоением Удоканского месторождения медистых песчаников, запасы которого в пересчёте на медь составляют 18 млн. т.
Рафинирование меди (заключительная стадия производства) размещается там, где есть металлургический передел, или комбинируется с выплавкой чернового металла, а также в районах массового потребления готовой продукции (Москва, Санкт-Петербург, Кольчугино и др.). Благоприятной предпосылкой размещения служит наличие дешевой электроэнергии (на одну тонну электролитической меди расходуется 3,5 - 5 тыс. кВтч).
Свинцово-цинковая промышленность характеризуется более сложными структурно-территориальными признаками по сравнению с медной промышленностью. Свинец и цинк, известные с глубокой древности находят широкое применение в народном хозяйстве. Свинец используется в кабельной промышленности, изготовлении рентгенаппаратуры, атомной и шарикоподшипниковой индустрии, оборонной промышленности и т. д. 54% потребляемого в России цинка идёт на цинкование чёрных металлов, 18% - в химическую индустрию, в больших объёмах используется в автомобилестроении, для изготовления гальванических батарей, минеральных красок, латуни и т. д.
Основным видом сырья для отрасли являются полиметаллические руды, содержащие свинец, цинк и очень часто медь, золото, серебро, серу и другие химические элементы.
Особенностями свинцово-цинковой промышленности являются территориальная разобщенность обогащения и металлургического передела, а также то, что не везде свинец и цинк в чистом виде получают одновременно.
Высокая электроемкость цинкового производства (его получают электролитным способом, когда на одну тонну цинка расходуется около 4 тыс. кВтч), а также хорошая транспортабельность цинковых концентратов дает возможность и целесообразность выплавки цинка вдали от сырья, у источников электроэнергии. На Урале электролитным способом цинк выплавляют из цинковых концентратов, получаемых от уральских медеплавильных заводов, а также ввозимых по толлингу из Казахстана.
Дистилляционным способом, при котором используется много топлива (4-5 т кокса на 1 т цинка), и небольшое количество электроэнергии, получат цинк на Беловском цинковом заводе (Кемеровская обл.).
Важной подотраслью цветной металлургии является никель-кобальтовая промышленность. Масштабы производства никеля и его сплавов определяются развитием производства нержавеющей стали, так как 75% выплавленного в мире никеля идёт на её изготовление, 15% никеля используется в выплавке других легированных сталей и сплавов (в основном с медью). Остальные 10% применяются в гальванопокрытиях или в виде порошков в никель-кадмиевых батареях. Кобальт широко используется в производстве твёрдых и специальных сплавов, никель-кобальтовых батарей, магнитов, катализаторов, керамики в лакокрасочной промышленности.
Никель-кобальтовая промышленность наиболее тесно связана с источниками сырья, что обусловлено низким содержанием полупродуктов (штейн и файнштейн), получаемых в процессе переработки исходных руд. При решении проблемы размещения заводов никелевой промышленности необходимо учитывать высокую энергоемкость отрасли, так как при переработке сульфидных руд затрачивается 45 тыс. кВтч электроэнергии, а при получении никеля из окисленных руд пирометаллургическим способом на 1 т никеля - до 50-55 т условного топлива.
Никелевые заводы ввиду высокой материалоемкости созданы на Урале (Верхний Уфалей, Реж и Орск). В Восточной Сибири Норильский район относится к крупнейшим центрам, где комплексно перерабатываются медно-никелевые руды. На Норильском горно-металлургическом комбинате получают никель, кобальт, медь, платину и некоторые другие редкие металлы.
В оловянной промышленности стадии технологического процесса территориально разобщены. Металлургический передел не связан с источниками сырья, так как он ориентируется на районы потребления готовой продукции или расположен на пути следования концентратов (Новосибирск). Это связано с тем, что добыча сырья ведется по мелким месторождениям, а продукты обогащения обладают высокой транспортабельностью.
Титано-магниевая промышленность производит титановую губку, сплавы и различные изделия из титана, магний и его сплавы, которые нашли применение в новейших отраслях машиностроительного комплекса – авиастроении, ракетной и космической технике, военном судостроении и других отраслях. Выплавка титана и магния относится к очень энергоёмким производствам. Затраты электроэнергии на 1 т титана составляют 20-60 тыс. кВтч, на 1 т магния - 20 тыс. кВтч.
По добыче золота, серебра и платины Россия занимает одно из первых мест в мире. В дореволюционные годы эти металлы добывали в Сибири и на Урале.
Особенностью золота является то, что оно выступает в качестве валютного актива, выполняющего ряд функций денег, и в качестве товара со своей себестоимостью производства.
Месторождения платины в виде россыпей давно известны на Урале, где она добывается, в районе Нижнего Тагила и в послевоенные годы около Норильска. Платина и платиноиды (палладий, иридий, осмий и рутений) используются в катализаторах на химических и нефтехимических предприятиях, в электронике, медицине, производстве сотовых телефонов, а также в экологических дожигателях выхлопных газов автомобилей.
Актуальными проблемами развития металлургического комплекса России являются ресурсосбережение, охрана окружающей природной среды и рациональное природопользование. Экологическая обстановка в металлургических регионах продолжает оставаться очень сложной. Индустрия России произвела отходов, содержащих вещества и обладающих токсичностью, объемом 78,5 млн. т, в том числе отходов черной металлургии 32 млн. или 40,8%, и цветной - 19,3 млн. т или 24,6% общего объема отходов.
Открытая или карьерная добыча руд черных и цветных металлов не несет потерь сырья, но приводит к безвозвратной утрате ценных почвенных ресурсов. "Хвосты", образующиеся при обогащении руд, и шлаки металлургического производства в России превышают 300 млн. т.
Дата добавления: 2021-07-19; просмотров: 943; Мы поможем в написании вашей работы! |
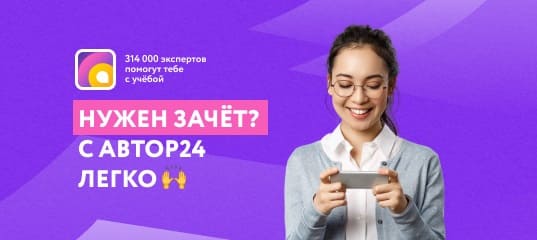
Мы поможем в написании ваших работ!