Графики опытных данных используемых методов контроля
Алгоритм оценки состояния РИ на основе фильтра Калмана
Как видно из схемы сначала фиксируются начальные значения параметров РИ, т. е. значения до начала процесса резания. Затем на основе опытных данных дается предсказание о состоянии РИ в последующие промежутки времени (в процессе резания и после). С помощью пары датчиков методов косвенного контроля получают необходимую информацию о состоянии режущего инструмента. Далее идет объединение полученных данных по необходимым критериям и их корректировка посредством фильтра Калмана. В конечном счете, обновляется первоначальная оценка состояния РИ с учетом зашумленности сигнала.
10
Выбор оптимальных методов контроля
На рисунке представлено измерение мощности привода. Система измерения состоит из следующих звеньев станок 1, электродвигатель 2, к которому подключается датчик тока 3, фиксирующий изменения тока в процессе резания. Так как с изменением силы тока изменяется и нагрузка на электродвигатель 2, а соответственно и на шпиндель станка. Измеренные значения тока датчиком 3 передаются в вычислительную систему ЧПУ 4, где производится их обработка и анализ.
Измерение шероховатости обрабатываемой поверхности детали на станке производится контактным методом датчиками шероховатости (профилометрами – рисунок) в процессе резания для контроля размерной точности детали после выполнения определенной операции обработки.
|
|
Суть работы профилометра заключается в следующем: объект измерения, которым является поверхность детали, шероховатость которой нужно измерить входит в контакт с тонкой алмазной иглой, которая перемещается вдоль поверхности детали перпендикулярно ее плоскости. Колебания иглы означают наличие шероховатой поверхности. С помощью преобразователя (пьезоэлектрического) механические колебания преобразуются в токовый (электрический) сигнал, который поступает на электронный усилитель, где интегрируется и визуализируется.
Износ режущего инструмента 3 (размерный) измеряется при помощи лазерной измерительной системы 1 с универсальным измерительным щупом 2, представленной на рисунке.
Процесс измерения РИ происходит после выполнения им каждой операции. Преимущества щупа – замер и инструмента и детали, используется и для токарных и для фрезерных инструментов, отсутствие влияния охлаждающей жидкости, высокая скорость. В совокупности с лазерной системой, обладающей большей скоростью, точностью и надежностью процесс контроля ресурса инструмента осуществляется на очень высоком уровне.
11
Графики опытных данных используемых методов контроля
|
|
Были построены графики, представленные на рисунке. Как видно из рисунка, с возрастанием количества обрабатываемых деталей постепенно увеличиваются и все исследуемые параметры, а, значит, износ резца по задней поверхности увеличивается.
12
Архитектура
13
Данный интерфейс был разработан с помощью среды разработки программного обеспечения «Visual Studio», на которой был написан код на языке «С#». Консоль программы изображена на рисунке.
14
Для автоматизированной системы был разработан интерфейс работы фильтра Калмана изображенный на рисунке, на котором представлено окошко с параметрами поступающих на вход системы сигналов, подключение источников, т. е. кнопка непосредственной фильтрации данных и окошко предсказания по Калману (итоговое искомое значение). Данные отображаются в виде графиков входных значений и предсказанных откорректированных с помощью фильтра Калмана.
15
Основные итоги выполнения диссертации:
1. Произведен анализ основных методов по контролю над состоянием режущего инструмента, которые разделяются на две основные группы:
- методы прямого (пассивного) контроля режущего инструмента;
|
|
- методы косвенного (активного) контроля режущего инструмента.
2. Изучен принцип работы фильтра Калмана, включающий две основные стадии – предсказание и корректировка, а также алгоритм его работы для повышения точности косвенного контроля РИ.
3. Выявлена оптимальная комбинация методов косвенного контроля: измерение шероховатости поверхности детали, размерного износа режущего инструмента, измерение мощности привода.
4. Разработана архитектура автоматизированной системы контроля состояния режущего инструмента на основе фильтра Калмана.
5. Разработан интерфейс программы для моделирования работы фильтра Калмана в процессе резания.
Дата добавления: 2021-07-19; просмотров: 96; Мы поможем в написании вашей работы! |
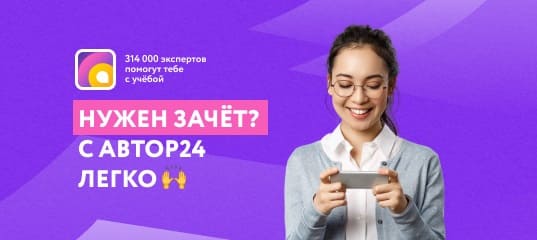
Мы поможем в написании ваших работ!