Эффективность и производительность рукавных фильтров
ЭКЗАМЕНАЦИОННЫЕ ВОПРОСЫ и ОТВЕТЫ (3б раздел)
для группы Эко-18
по дисциплине Теоретические основы и технологии очистки газовых выбросов
Направление подготовки 05.03.06 Экология и природопользование
Профиль Экология
КУРС __3 СЕМЕСТР _____6 ___ 2020/2021 учебный год
№ п/п | ЭКЗАМЕНАЦИОННЫЕ ВОПРОСЫ | ||
11 | 3.11. Тканевые фильтры. Область применения. Конструкции тканевых фильтров. Требования к фильтрующим материалам. Способы регенерации фильтров. Преимущества и недостатки фильтров. | Ниже | |
12 | 3.12. Зернистые фильтры. Область применения. Типы зернистых фильтров. Преимущества и недостатки фильтров. | Ниже |
5.11. Тканевые фильтры. Область применения. Конструкции тканевых фильтров. Требования к фильтрующим материалам. Способы регенерации фильтров. Преимущества и недостатки фильтров
Тканевые фильтры
Рукавный фильтр для систем вентиляции и очистки воздуха представляет собой одно из наиболее эффективных устройств, способных перехватывать загрязняющие частицы и использоваться для очистки газов и газовых смесей. Оборудование может использоваться и как часть системы внутренней вентиляции, возвращающей воздух в помещения, и для удаления пылевых загрязнений из воздуха, направляемого из зданий.
Для тонкой очистки газа чаще всего используются тканевые рукавные фильтры
|
|
Области применения и особенности эксплуатации
Необходимость постоянной очистки воздуха от большого количества мелких частиц материалов и продуктов испытывает большой круг производств. Поэтому системы рукавных фильтров распространены:
– в химической и пищевой промышленности;
– на предприятиях горнорудного и обогатительного производства;
– на литейном производстве, в металлургии, в цехах, где производится доработка чугуна дробометными машинами;
– на мелькомбинатах, элеваторах и других предприятиях, где переработка и хранение сырья остается источником пыли;
– на производственных участках и в окрасочных цехах.
Главным элементом тканевого фильтра является фильтрующий элемент-рукав, изготовленный из фильтровального материала. Фильтровальный материал может быть выполнен как из тканого, так и из нетканого материалов.
В зависимости от требований по чистоте воздуха и особенностей технологических процессов, рукавные фильтры могут оснащаться рукавами из разных материалов — это и натуральные, и синтетические тканые и нетканые полотнища, свернутые в рукава. Эффективность очистки воздуха от определенных типов загрязнений может быть повышена при использовании пористых материалов или тканей с выделяющимися волокнами, байки и ее синтетических аналогов.
|
|
Устройство рукава позволяет крепить его разными способами: на кольцо с подворотом ткани, на пружинные элементы, на хомуты. Как правило, срок службы одного рукава исчисляется несколькими годами. При отсутствии в воздухе агрессивных загрязнений, разрушающих структуру ткани, система регенерации вполне справляется со своей задачи и поддерживает пропускную способность рукавов в течение всего цикла эксплуатации.
Корпус рукавного фильтра, как правило, разделен на несколько камер (секций), в каждой из которых размещено по несколько рукавов. Отдельные секции имеют самостоятельные системы регенерации.
В настоящее время разработано большое число конструкций тканевых фильтров, которые отличаются по следующим признакам:
– форме тканевых фильтровальных элементов (рукавные, плоские, клиновые и др.) и наличию в них опорных устройств (каркасные и бескаркасные);
– месту расположения вентилятора относительно фильтра (всасывающие, работающие под разрежением, и нагнетательные, работающие под давлением);
– методу регенерации ткани (с импульсной продувкой, с встряхиванием, с обратной продувкой и др.);
|
|
– наличию и форме корпуса для размещения ткани (прямоугольные, цилиндрические, открытые (бескамерные));
– числу секций в установке (одно- и многосекционные);
– виду используемой ткани (например, стеклотканевые).
Кроме того, возможна классификация тканевых фильтров по характеру их работы с учетом основной особенности их конструкции:
1) тканевые фильтры периодического действия;
2) тканевые фильтры непрерывного действия:
а) многосекционные рукавные фильтры;
б) рукавные фильтры с обратной струйной продувкой;
в) рукавные и плоские фильтры, регенерируемые импульсами сжатого воздуха;
г) рукавные фильтры, регенерируемые пульсирующим потоком газа;
д) рукавные фильтры, регенерируемые встряхиванием;
е) рукавные фильтры с регенерацией встряхиванием и обратной продувкой.
Наибольшее распространение получили тканевые рукавные фильтры с фильтрующим элементом в виде цилиндрического рукава с регенерацией обратной продувкой или импульсной продувкой сжатым воздухом. Фильтрование газов в фильтрах может идти как снаружи внутрь рукава (обычно имеют каркас), так и изнутри рукава наружу.
Конструкция и устройство
|
|
Конструкция рукавного фильтра рассчитана на пропуск через него большого количества воздуха или газа, который направляется на батареи тканевых рукавов, задерживающих частицы загрязнений. В зависимости от типа установки рукава могут размещаться и горизонтально, чтобы через них проходило максимальное количество воздуха. Пылевые, сажевые и другие частицы забиваются в поры ткани и не проходят дальше, в направлении выходного отверстия для чистого воздуха.
Подавляющее большинство фильтров рукавного типа состоит нескольких блоков:
· корпус с фильтрующими элементами;
· входной (впускной) клапан для газовоздушной смеси;
· батареи рукавов или отдельные рукава на пути потока воздуха;
· выходной клапан с автоматикой для отслеживания давления;
· система регенерации — устройства для быстрой очистки рукавов от накопившейся пыли.
Наиболее распространенным типом тканевого фильтра является рукавный фильтр, схема работы которого дана на рис. 2. Главным элементом такого фильтра является рукав, изготовленный из фильтровальной ткани. Корпус фильтра разделен на несколько герметизированных камер, в каждой из которых размещено по нескольку рукавов. Газ, подлежащий очистке, подводится в нижнюю часть каждой камеры и поступает внутрь рукавов. Фильтруясь через ткань, газ проходит в камеру, откуда через открытый выпускной клапан поступает в газопровод чистого газа (рис. 2, а). Частицы пыли, содержащиеся в неочищенном газе, оседают на внутренней поверхности рукава, в результате чего сопротивление рукава проходу газа постепенно увеличивается. Когда оно достигнет некоторого предельного (по условиям тяги) значения, фильтр переводится на режим регенерации (рис. 2,6), т. е. рукава освобождаются от осевшей на них пыли.
Рис. 2. Схема рукавного фильтра с обратной продувкой и встряхиванием:
а — режим фильтрования; б — режим регенерации.
1 — входной патрубок; 2— корпус фильтра; 3— рукав; 4— продувочный клапан;
5— выпускной клапан; 6— коллектор очищенного газа;
7 — вал механизма встряхивания; 8— пылевыгрузное устройство
Благодаря простоте конструкции и способности эффективно перехватывать пыль, сажу и частично мелкие каплевидные загрязнения, система рукавных фильтров используется на производствах, где технологический процесс связан с постоянной утечкой мелких загрязнений и запылением воздуха.
Эффективность и производительность рукавных фильтров
Общая конструкция и принцип работы рукавной системы очистки воздуха позволяют организовать последовательный процесс. Несколько батарей или рукавов устанавливаются последовательно, перехватывая загрязнения разного типа. Если учесть, что такая система обычно монтируется на этапе механической очистки воздуха, то ее эффективность определяет успешность применения всего комплекса средств очистки воздуха в производственных помещениях.
Требования к фильтрующим материалам
Рукава для фильтров изготавливаются на специализированных предприятиях и являются унифицированными деталями. Их можно подобрать по пропускной способности, степени очистки, размерам фильтрующих пор и волокон, конструкции элемента крепления.
Фильтровальные материалы
По структуре фильтровальные материалы подразделяют на тканые и нетканые.
Тканые материалы представляют собой переплетение нитей диаметром до 300—700 мкм. Продольные нити называют основой, а поперечные утком. Характер переплетения может быть различным. В случае специальной обработки — ворсования на поверхности ткани образуется ворс из спутанных между собойволокон.
К нетканым материалам относятся фильтровальные войлоки и фетры, представляющие собой плотные слои беспорядочно перепутанных волокон, получаемые в основном на специальных иглопробивных машинах. Свойства фетров зависят от свойств волокон, из которых они изготовлены.
В условиях работы фильтров к тканям предъявляют следующие требования:
1) термостойкость, достаточная для работы в условиях температур отходящих газов металлургических агрегатов;
2) химическая стойкость по отношению к агрессивным компонентам, присутствующим в отходящих газах;
3) механическая прочность по отношению к истиранию и многократным изгибам во время регенерации тканей, а также стабильность размеров при рабочих условиях;
4) высокая пылеемкость при фильтрации и способность удерживать при регенерации часть пыли, что обеспечивает достаточно высокую эффективность после регенерации;
5) сохранение максимальной воздухопроницаемости в запыленном состоянии;
6) минимальное влагопоглощение и способность к легкому удалению накопленной влаги (малая гигроскопичность);
7) умеренная стоимость.
Выбор вида ткани определяется в основном температурой, а также влагосодержанием и агрессивными свойствами газового потока, сроками службы ткани в рабочих условиях и стоимостью ткани.
Наряду с тканями из натуральных волокон (хлопок, лен, шерсть) широко применяют ткани из синтетических волокон — капрон, нитрон, лавсан, а также стеклоткани. Используют и нетканые материалы: фетр и войлок.
Свойства широко применяемых для очистки газов фильтровальных материалов приведены в табл. 1.
В настоящее время материалы из натуральных волокон все чаще заменяют синтетическими. Наиболее распространены нитрон и лавсан, обладающие повышенной термостойкостью, достаточной химической стойкостью и механической прочностью наряду с хорошей фильтрующей способностью. Срок службы рукавов из этих тканей 6—12 мес.
Таблица 1. Некоторые свойства фильтровальных материалов
Основное волокно | Термостойкость, оС | Устойчивость к воздействию | Удлинение при разрыве, % | Средний диаметр волокна, мкм | Пористость, % | Горючесть | Влагоемкость, %, при Т=20оС, φ=65% | |
кислот | щелочей | |||||||
Хлопок | 65—80 | ОП | X | 7—8 | 20 | 60 | Да | 7—8,5 |
Шерсть | 80—100 | У | ОП | 30—40 | 27 | 86 | Да | 13—15 |
Нитрон | 130 | X—У | У | 15—17 | 24 | 83 | Да | 0,9-2 |
Лавсан | 130 | X | У—П | 15—25 | 20 | 75 | Да | 0,4 |
Оксалон | 220—250 | X | - | - | - | - | Да | - |
Стекло | 250—300 | X | У—П | 3—4 | 8 | 55 | Нет | 0,3 |
Примечания. 1. Условные обозначения: ОХ — очень хорошая; X — хорошая; У — удовлетворительная; П — плохая; ОП — очень плохая. 2. В таблице приведены ориентировочные значения, которые могут сильно изменяться при применении комбинированных тканей, например, шерсть с капроном и т. п. |
Фильтровальные материалы из стекловолокна характеризуются высокой термостойкостью и достаточной химической стойкостью. Главный недостаток стекловолокон — низкая изгибоустойчивость, вследствие чего рукава быстро выходят из строя. Для улучшения свойств стеклоткани ее обрабатывают кремнийорганическими соединениями. Получены стеклоткани, выдерживающие температуры до 500 °С.
В последнее время начато производство термостойких волокон (оксалан и сульфон) и тканей из них, обладающих той же термостойкостью, что и стеклоткани, но значительно более гибких и эластичных. Испытания этих тканей показали их достаточно хорошие фильтрующие свойства.
Начат выпуск металлотканей и войлоков, выдерживающих температуры до 600 °С и выше.
Материалы сменных фильтроэлементов для рукавных фильтров:
– полиэстер (PE);
– мета-арамид (AR);
– полипропилен (PP);
– полиимид (PI);
– политетрафторэтилен (PTFE) и др.
Способы регенерации фильтров
Очистка рукавного фильтра — регенерация рукавов — может работать с использованием двух принципов воздействия на скопившиеся частицы. В зависимости от того, как поведет себя пыль различного происхождения, возможно ее удаление двумя основными способами:
– интенсивное встряхивание рукава или батареи, при котором частицы осыпаются вниз и направляются в бункер для удаления;
– импульсная продувка рукава или батареи обратным током воздуха или газовоздушной смеси, «выбивающим» частицы из пор ткани.
В отдельных системах фильтрации может использоваться комбинированное воздействие, но это не всегда эффективно, выбор решения зависит от особенностей производства и свойств загрязняющих частиц.
Регенерация рукавов фильтра включается автоматически — по мере накопления пыли на поверхности рукава его пропускная способность снижается, давление воздуха на выходе падает, и датчик-система реагирует активацией обратного продува или механизма встряхивания. Наиболее эффективной является батарейная компоновка — в активной зоне фильтра находится три рукава, один из которых регенерируется, а два продолжают работу в режиме очистки.
Наиболее часто регенерация осуществляется обратной продувкой. Продувочный воздух от специального вентилятора направляют внутрь камеры через открытый продувочный клапан (выпускной клапан закрыт). Фильтруясь через рукав в обратном направлении, воздух разрушает образовавшийся на внутренней поверхности рукава слой пыли, которая падает в бункер, откуда удаляется при помощи шнека, или другого устройства. Отработавший продувочный воздух через подводящий газ патрубок поступает в газопровод неочищенного газа. В целях повышения эффективности регенерации одновременно с обратной продувкой осуществляется встряхивание рукавов, для этого используется специальный встряхивающий механизм, перемещающий вверх и вниз крышку, к которой крепится рукав.
Камеры фильтра переводят на регенерацию по очереди, и, следовательно, фильтр в составе п—1 камера все время находится в работе.
Движение запыленного газового потока через ткань. При прохождении газа через чистую ткань, т. е. в начальный период работы фильтра, частицы пыли осаждаются на волокнах ткани. Захват частиц волокнами происходит за счет действия описанных ранее механизмов касания, инерции, диффузии, гравитации или электростатического взаимодействия. Далее вследствие того, что плотность упаковки у ткани значительно выше, чем у волокнистых фильтров, на лобовой стороне фильтра начинает формироваться сплошной слой из частиц пыли, которые не могут проникнуть в глубь ткани.
Образующийся вторичный лобовой слой (автослой) начинает сам задерживать поступающие частицы, в результате чего толщина его постепенно возрастает, и он становится главной фильтрующей средой. Поскольку поры, образующиеся между частицами лобового слоя, и сами улавливаемые частицы имеют близкие размеры, значительную роль начинает играть ситовый эффект.
Непроницаемость вторичного пылевого слоя для вновь поступающих частиц всех размеров хорошо объясняет обычно очень высокую степень очистки газов (нередко превышающую 99,9%) в тканевых фильтрах в запыленном состоянии. Снижение эффективности фильтра всегда связано с динамическим пробоем этого слоя и проскоком пыли в местах его разрушения, образования трещин, а также с наличием крупных пор в фильтрующем материале, где слой пыли вообще не может образоваться. Возникновение трещин и разрушение пылевого слоя могут происходить непосредственно в ходе процесса фильтрования в результате пульсаций газового потока и микровибрации промышленной установки. Всякое увеличение внешних сил, действующих на систему, в частности рост перепада давления на фильтре, способствует возникновению динамических пробоев слоя.
Практика показала, что оптимальные значения скорости фильтрования в тканевых фильтрах лежат в пределах 0,5— 1,0 м/мин. При больших скоростях фильтрования эффективность тканевых фильтров снижается вследствие выноса пылевых частиц, а гидравлическое сопротивление становится чрезмерно высоким. При меньших скоростях фильтрования необходимо увеличение поверхности фильтра.
С течением времени гидравлическое сопротивление и эффективность фильтра непрерывно увеличиваются.
В процессе регенерации как гидравлическое сопротивление, так и эффективность фильтра снижаются (рис. 3). Поэтому при регенерации следует разрушать и удалять пылевой слой, оставляя проникшую внутрь пыль в порах ткани. Для этого обратную продувку ведут при невысоких скоростях, соизмеримых со скоростями фильтрования.
Рис. 3. Кривые изменения степени очистки и гидравлического сопротивления фильтра
с регенерацией ткани:
tф— время фильтрования; tр — время регенерации
Способы регенерации фильтров
Наиболее распространенными способами регенерации фильтров являются: 1) обратная продувка с встряхиванием; 2) обратная продувка без встряхивания; 3) импульсная продувка; 4) обратная струйная продувка. Иногда применяют регенерацию кручением рукава и вибровстряхиванием.
Обратную посекционную продувку обычно производят воздухом под действием небольшой разности давлений (до 5 кПа) - со средней скоростью проникновения через фильтровальную перегородку 0,6—1,5 м/мин; продолжительность обратной продувки 15—50 с. Для каждого фильтровального материала существует максимальная скорость обратной продувки, дальнейшее увеличение которой не способствует отделению пыли, а лишь вызывает бесполезный рост энергетических затрат. Используя величину пористости ткани εтк, рекомендуется определять скорость обратной продувки по формуле
wобр=k εтк , (1)
где k — коэффициент регенерируемости ткани, равный 1,6—2,0.
Для уменьшения деформации рукавов во время обратной продувки их снабжают распорными кольцами. Обратную продувку осуществляют посекционно с отключением регенерируемой секции от потока очищаемого газа, что следует учитывать при выборе необходимой поверхности фильтра. Отключение и повторное включение секции по окончании регенерации производятся автоматически. Обратную продувку с встряхиванием применяют для изгибоустойчивых тканей (лавсана, нитрона), а без встряхивания — для тканей, плохо сопротивляющихся изгибу (стеклоткани, металлоткани).
Импульсную продувку осуществляют струей сжатого воздуха, которая, выходя из сопла в рукав, увлекает за собой очищенный газ и создает внутри рукава волну повышенного давления (рис. 4, а). Под действием перепада давления рукава, надетые на проволочные каркасы, раздуваются, деформируя пылевой слой, который отделяется от ткани рукава в виде агломератов. При подаче импульсов длительностью 0,1—0,3 с при избыточном давлении 400—800 кПа расход продувочного воздуха не превышает 0,1—0,2 % от количества очищаемого газа. Управление импульсными электромагнитными клапанами сжатого воздуха автоматизировано. Импульсная регенерация осуществляется при работающем фильтре и не требует его отключения. Она позволяет использовать в фильтрах, кроме тканей, тяжелые нетканые материалы.
Увеличение фильтрующей поверхности аппарата может быть достигнуто применением рукавов большей длины. В этом случае сопла импульсной продувки размещают с двух сторон (сверху и снизу).
Струйную продувку применяют при очистке больших объемных расходов газа малой запыленности (до 0,5 г/м3) с достижением выходной запыленности 2—4 мг/м3. Подачу продувочного воздуха осуществляют в плотно охватывающее рукав кольцо, которое медленно движется вдоль рукава вверх и вниз со скоростью 6—15 м/мин (рис. 4,6). Продувка производится струей воздуха, вытекающего через кольцеобразную щель шириной 0,2—2 мм со скоростью 10—60 м/с. Все кольца секции объединены в каретку, приводимую в движение от специального механизма. Пыль отделяется от рукава в результате совместного действия струи продувочного воздуха и деформации рукава движущимся кольцом. Интенсивная регенерация позволяет использовать в качестве фильтровального материала тяжелые нетканые материалы, обеспечивающие высокую эффективность улавливания при высоких скоростях фильтрования (2—б м/мин) без исключения секций на регенерацию. Расход продувочного воздуха составляет 1—6 % объема очищаемого газа. Необходимое давление 60—80 кПа. Существуют и некоторые другие способы регенерации, которые в России широкого распространения не получили.
Рис. 4. Схемы регенерации тканевых фильтров:
а — импульсная продувка; б — струйная продувка.
1— электромагнитный клапан; 2 — ввод сжатого воздуха;
3— сопло; 4— струи сжатого воздуха;
5 — блок автоматического управления регенерацией;
6— рукав; 7 — каркас рукава; 8 — бункер; 9— движущееся кольцо
Типы тканевых фильтров. Основным признаком, в значительной мере определяющим конструкцию фильтра, является способ регенерации ткани. При импульсной продувке и фильтровании газа снаружи внутрь рукава фильтры выполняют каркасными, при обратной и струйной продувке и фильтровании газа из рукава наружу — бескаркасными. В зависимости от конструкции применяют нижний и верхний подвод газа к рукаву. Основные конструкции серийно выпускаемых фильтров общепромышленного назначения характеризуются данными табл. 3—11.
Таблица 3. Фильтры типа ФРО (фильтры рукавные с обратной продувкой)
Характеристика | ФРО-1250-1 | ФРО-1650-1 | ФРО-2500-1 | ФРО-4100-2 | ФРО-5100-2 | ФРО-6000-2 | ФРО-7000-2 | ФРО-8000-2 | ФРО-20000-3 | ФРО-24000-3 |
Фильтрующая поверхность, м2 Количество рукавов Количество секций Высота рукава, м Диаметр рукава, мм Габаритные размеры: (L×В×Н), м Масса, т | 1266 252 6 8 200 5,10× 6,84× 13,77 37,8 | 1688 336 8 8 200 6,60× 6,84× 13,77 50,4 | 2530 504 12 8 200 9,60× 6,84× 13,77 75,6 | 4104 432 8 10 300 12,6× 9,84× 16,20 108.5 | 5130 540 10 10 300 15,6× 9,84× 16,20 136 | 6156 648 12 10 300 18,6× 9,84× 16,20 162,8 | 7182 756 14 10 300 21,6× 9,84× 16,20 190 | 8208 864 16. 10 300 24,6× 9,84× 16,20 217 | 20 520 2160 10 10 300 30,4× 21,0× 22,64 540 | 24 624 2592 12 10 300 36,4× 21,0× 22,64 650 |
Примечание: Ткань — лавсан (130 оС) или стеклоткань (220 °С) |
Таблица 4. Фильтры типа ФРКИ (рукавные, каркасные с импульсной продувкой)
Характеристика | ФРКИ-30 | ФРКИ-60 | ФРКИ-90 | ФРКИ-180 | ФРКИ-360 |
Фильтрующая поверхность, м2 Количество рукавов Количество секций Высота рукава, м Количество электромагнитных клапанов Габаритные размеры (L×В×Н), м Масса, т | 30 36 1 2 6 1,46×2,66×3,62 1,3 | 60 72 2 2 12 2,82×2,06×3,62 2,1 | 90 108 3 2 18 4,14×2,06×3,62 3,0 | 180 144 4 3 24 5,48×2,06×4,62 4,6 | 360 288 8 3 48 5,85×4,37×4,88 9,9 |
Примечание. Диаметр рукава 130 мм; ткань — лавсан (130"С). |
Таблица 5. Фильтры типа ФРКДИ (рукавные каркасные с двусторонней импульсной продувкой)
Характеристика | ФРКДИ-500 | ФРКДИ-720 | ФРКДИ-1100 |
Фильтрующая поверхность, м2 Количество рукавов Количество секций Габаритные размеры (L×В×Н), м Количество электромагнитных клапанов Масса, т | 550 216 6 4,94×4,37×9,21 72 20,5 | 720 288 8 6,28×4,37×9,21 96 28,7 | 1100 432 12 8,95×4,37×9,21 144 33,0 |
Примечание : Диаметр рукава 130 мм, высота 6 м; ткань — лавсан |
Таблица 6. Фильтры типа СМЦ-101А (регенерация обратной продувкой)
Характеристика | Габариты фильтров | ||
I | II | III | |
Фильтрующая поверхность секции, м2 Высота рукава, м Габаритные размеры (L×В×Н), м Масса, т | 55; 50 2,25 3,2×1,7×5,7 2,4; 2,75 | 116; 110 4,5 3.2×1,7×9,2 3,2; 3,6 | 287 9 3,2×1,7×13,9 44 |
Примечания:1. Диаметр рукава 200 мм; количество рукавов 36; ткань — лавсан. 2. Для габарита I собирают не более 4 секций, для габаритов II и III — не более 10 секций. 3. Фильтры I и II габаритов могут быть снабжены механизмами встряхивания |
Таблица 7. Фильтры типа УРФМ (регенерация обратной продувкой с встряхиванием)
Характеристика | УРФМ-ПМ | УРФМ-III |
Фильтрующая поверхность, м2 Количество секций Число рукавов Габаритные размеры (L×В×Н), м Масса, т | 2300 20 840 23×4,8×13,1 109 | 1610 14 488 16,1×4,8×13,1 78,3 |
Примечание. Диаметр рукава 220 мм, высота 4,063 м; ткань — нитрон (130°С) |
Таблица 8. Фильтры типа ФРОС (регенерация обратной продувкой сжатым воздухом при р = 0,15…0,20 МПа)
Характеристика | ФРОС-9 | ФРОС-13,5 | ФРОС-20 | ФРОС-31 | ФРОС-66 |
Фильтрующая поверхность, м2 Количество секций Количество фильтрующих элементов Высота фильтрующих элементов, м Габаритные размеры (L×В×Н), м Масса, т | 9 4 16 2 4,5×2,17×I,8 1,0 | 13,5 4 16 3 5,5×2,17×I,0 1,1 | 20 6 36 2 5,2×2,76×I,6 2,0 | 31 6 36 3 6,2×2,76×I,6 2,3 | 66 8 76 3 6,9×3,36×2,2 3,7 |
Примечание. Ткань — металлическая сетка С120 (500 °С). |
Таблица 9. Фильтры типа РФСП (регенерация поэлементной струйной продувкой)
Характеристика | РФСП-II | РФСП-1580 |
Фильтрующая поверхность, м2 Количество секций Количество рукавов Диаметр рукава, м Габаритные размеры (L×В×Н), м Масса, т | 370 4 88 360 11,5×5,05×13,2 42 | 1580 20 480 220 25,75×7,74×11,77 180 |
Примечание. Высота рукава 5 м; ткань — лавсан (130 оС). |
Таблица 10. Фильтры типа ФРИ (рукавные импульсные)
Характеристика | ФРИ-630 | ФРИ-800 | ФРИ-1250 | ФРИ-1600 |
Фильтрующая поверхность, м2 Максимальная произво-дительность, тыс. м3/ч Габаритные размеры (L×В×Н), м Масса фильтра, т | 606 58,2 4,52×4,22×9,325 15,03 | 808 77,6 5,85×4,22×9.325 18,57 | 1212 116,5 8,54×4,22×9,325 25,52 | 1616 155,2 11,22×4.22×9,325 33,14 |
Таблица 11. Фильтры ФКИ (кассетные импульсные)
Характеристика | ФКИ-28 | ФКИ-84 | ФКИ-168 |
Фильтрующая поверхность, м2 Количество кассет, шт Производительность, тыс. м3/ч Габаритные размеры (L×В×Н), м | 28 1 3,36 2,4×2,45×6,8 | 84 3 11,09 2,65×3,55×7,1 | 168 6 17,10 5,3×3,55×7,1 |
В ПО «Газоочистка» разработаны и подготовлены к серийному выпуску фильтры типов ФРИ (табл. 10) и ФКИ (табл. 11). Фильтры типа ФРИ предназначены для очистки промышленных газов от мелкодисперсной пыли при температуре до 130 °С. Регенерация производится импульсами сжатого воздуха, подаваемого в рукава с двух сторон, сверху и снизу. Пыль, стряхиваемая с рукавов, осыпается в бункер, откуда удаляется с помощью транспортера.
Общими для всех фильтров типа ФРИ являются: начальная концентрация пыли не более 20 г/м3; удельная газовая нагрузка не более 1,6 м3/(м2-мин); гидравлическое сопротивление не более 2 кПа; разрежение внутри аппарата не более 5 кПа; степень очистки газа 98,75 %; материал фильтровальных рукавов — иглопробивное фильтровальное полотно ТУ 17 ЭССР-413—82, артикул 934561.
Фильтры типа ФКИ собираются из кассет с ячейковыми фильтрующими элементами. Фильтровальная кассета имеет металлический каркас, к которому крепятся фильтрующие элементы из иглопробивного фильтровального полотна ТУ 17 ЭССР-413—82, артикул 934561. Высота кассеты не более 2 м. Площадь одного фильтровального элемента 28 м2. Фильтровальный элемент состоит из пяти рядов ячеек с размерами сторон 60×60 мм, в ряду 12 ячеек. Один ряд ячеек заглушён в нижней, а другой в верхней части, вследствие чего происходит полное разделение камер запыленного и очищенного газа. Такой фильтрующий элемент компактен и имеет развитую поверхность фильтрования, вследствие чего габаритные размеры кассетных фильтров значительно меньше, чем рукавных.
Общими для всех фильтров типа ФКИ являются гидравлическое сопротивление не более 2 кПа и запыленность на выходе не более 50 мг/м3.
Фильтры типов ФКИ-28 и ФКИ-84 используют для очистки аспирационного воздуха от технологического оборудования, а фильтры типа ФКИ-168 — для очистки дымовых газов от сушильных барабанов.
Аппараты фильтрующего действия с гибкими перегородками улавливают одинаково хорошо пыли практически всех размеров, вплоть до мелкодисперсных. Однако, не рекомендуется применять их для абразивных и слипающихся пылей, а также при высокой температуре и высокой влажности газа. Основными направлениями развития этих аппаратов являются создание высококачественных фильтровальных материалов и совершенствование конструкций фильтров в целях уменьшения их габаритных размеров (кассетные и патронные фильтры).
Фильтрация аэродисперсных систем через пористые перегородки – это один из наиболее совершенных способов выделения из воздуха взвешенных твёрдых частиц. Этот способ характеризуется следующими особенностями:
- более высокой степенью очистки газов от взвешенных частиц, чем в газоочистных аппаратах других типов (фильтры обеспечивают практически полное улавливание частиц всех размеров, включая субмикронные);
- возможностью улавливания частиц при любом давлении газов;
- высокой степенью очистки при любых концентрациях взвешенных частиц в очищаемых газах;
- возможностью очистки газов, нагретых до высокой температуры использованием химически стойких материалов;
- возможностью полной автоматизации процесса очистки газов;
- стабильностью процесса очистки и меньшей зависимостью от изменения физико-химических свойств улавливаемых частиц и расхода газов, чем при использовании других способов;
- простотой эксплуатации.
Возможности применения газоочистных аппаратов фильтрующего типа значительно расширяются в связи с внедрением новых пористых фильтров из синтетических, стеклянных и металлических волокон, пористых пластических масс, пористой металлокерамики, шлаковаты и других материалов.
Недостатки пористых фильтров - необходимость периодической замены некоторых фильтрующих перегородок; сравнительно высокий расход энергии при использовании отдельных видов пористых фильтров; громоздкость установок с фильтрами (особенно при большом объемном расходе очищаемых газов); относительная сложность эксплуатации. В то же время, как показывают технико-экономические расчеты, стоимость очистки в фильтрах часто ниже, чем в мокрых пылеуловителях.
Преимущества рукавных фильтров:
– эффективность очистки запыляемого воздуха достигает почти 100%;
– возможность возврата теплого очищенного воздуха в помещение, что значительно сокращает затраты на обогрев помещения;
– соответствие современным требованием очистки запыленного воздуха;
– простота монтажа и эксплуатации системы очистки воздуха;
– возможность непрерывной работы в составе системы вентиляции;
– простое обслуживание и минимальные затраты на поддержание работоспособности;
– эффективная очистка воздуха от загрязнений с одновременной и циклической очисткой фильтра от накопленного материала.
Этими преимуществами объясняется распространенность рукавных фильтров в промышленности. Перехватить и удалить из воздуха частицы загрязнений размером от 0,1 до 100 микрометров в режиме циркуляции или вывода — это возможность обеспечить поддержание безопасного режима работы и снижения нагрузки на окружающую среду.
Недостатки рукавных фильтров:
– высокая стоимость по сравнению с циклонными аппаратами;
– сложность устройства, что требует квалифицированного обслуживания персонала;
– работа в условиях ограниченных концентраций пыли в воздушном потоке;
– переменное гидравлическое сопротивление. Но этот недостаток компенсируется эффективными способами регенерации (очистки) фильтрующих элементов.
5.12. Зернистые фильтры. Область применения. Типы зернистых фильтров. Преимущества и недостатки фильтров.
Зернистые фильтры используют в газоочистке при невозможности применения тканевых из-за высокой температуры среды. Зернистые фильтры распространены значительно меньше, чем тканевые фильтры.
В зернистых фильтрах пыль улавливается в слое дисперсного твердого материала. Фильтрующий слой в зернистых фильтрах образован зернами сферической или другой формы.
Зернистый слой в фильтре может быть использован:
- в качестве фильтрующей перегородки для очистки газов от твердых частиц;
- в качестве катализатора или сорбента при каталитической и сорбционной очистке газов.
Зернистые фильтры применяются при обработке запыленных выбросов производства строительных материалов (цементная промышленность и др.), предприятий химической промышленности, при получении редких и драгоценных металлов и в других технологических процессах. Зернистые фильтры используются для одновременного улавливания дисперсных и газообразных примесей газовых выбросов.
Преимуществами многих из зернистых фильтров являются:
- низкая стоимость;
- доступность материалов;
- возможность применения для очистки высокотемпературных газов (до 500÷800 оС);
- возможность работать в условиях агрессивной среды;
- возможность выдерживать большие механические нагрузки и перепады давлений, а также резкие изменения температуры.
- возможность применения для улавливания слипающихся, высокоомных, абразивных пылей, когда затруднено применение аппаратов другого типа;
- возможность возврата в технологический процесс уловленного на фильтре продукта (например: фильтрующий слой состоит из зерен шихты сырья и уловленной пыли).
В зависимости от вида улавливаемой пыли зернистые фильтры могут иметь следующие параметры:
- степень очистки 95-99,5%;
- гидравлическое сопротивление 1300-3000 Па;
- скорость фильтрации 15-35 м/мин.
Различают следующие типы зернистых фильтров:
1) зернистые насадочные (насыпные) фильтры, в которых улавливающие элементы (элементы фильтрующего слоя - гранулы, куски и т.д.) не связаны жестко друг с другом.
К этим фильтрам относятся:
- статические (неподвижные) слоевые фильтры (рис. 1);
- динамические (подвижные) слоевые фильтры с гравитационным перемещением сыпучей среды (зернистого слоя) (рис. 2 и 2 а);
- фильтры с псевдоожиженным слоем насадки.
В насадке насыпных фильтров используют песок, гальку, гравий, шлак, дробленые горные породы, кокс, крошку резины, пластмасс, графита, а также отходы различных производств. Целесообразно насадку зернистого фильтра изготавливать из материала, пыль которого улавливается (например, из асбеста), т. к. в этом случае его вместе с уловленной пылью можно возвращать в производство.
Выбор материала зависит от требуемой термической и химической стойкости, механической прочности и доступности материала.
При накоплении в зернистых фильтрах частиц пыли эффективность пылеочистки возрастает, однако увеличиваются и потери давления на фильтре. При слишком высоких потерях давления возникает необходимость в регенерации фильтра или его замене. Насыпные зернистые фильтры регенерируют ворошением или вибрационным встряхиванием.
Обычно фильтры имеют насадку с размером зерен 0,2–2 мм. Высота неподвижных слоев на сетках находится в пределах 100–150 мм. Начальное сопротивление от 50 до 200 Па. Воздух направляется сверху вниз.
Рис.1. Схемы фильтров с неподвижным зернистым слоем:
а — горизонтальный с периодическим ворошителем; б—с цилиндрическим расположением слоя
и виброрегенерацией; в—горизонтальный с вибровстряхиванием; г—двухходовой на пружинах;
д—плоский двухслойный; е—вертикальный шахтного типа; ж — с вращением кассеты;
з—с секционированным слоем и регенерацией псевдоожижением
Рис. 2 Схемы динамических фильтров с гравитационным перемещением зернистого слоя:
Рис. 2 а. Фильтр с движущимися слоями зернистого материала:
1 - короб для подачи свежего зернистого материала; 2 - питатели; 3 - затворы;
4 - фильтрующие слои; 5 - короб для вывода запыленного материала
2) жесткие пористые фильтры, в которых элементы прочно связаны друг с другом в результате спекания, прессования или склеивания и образуют прочную неподвижную систему. Зернистые жесткие фильтры (пористая керамика, пористые металлы, пористые пластмассы, металлокерамика и др.) обладают значительной устойчивостью к высокой температуре, коррозии, механическим нагрузкам и применяются для фильтрования сжатых газов.
Недостатки таких фильтров: высокая стоимость, высокое гидравлическое сопротивление, трудность регенерации.
Регенерацию можно проводить четырьмя способами:
- продуванием воздухом в обратном направлении;
- пропусканием жидких растворов в обратном направлении;
- пропусканием горячего пара;
- простукиванием или вибрацией трубной решетки с элементами.
Зернистый фильтр может быть единственной ступенью в установке или первой ступенью перед более эффективным фильтром, например с материалами ФП.
В зернистом гравийном фильтре для улавливания пылей с наличием абразивных частиц и агрессивных газов от дробилок, грохотов, сушилок, мельниц, транспортирующих устройств предприятий по производству цемента, извести, гипса, фосфорных удобрений и др. удельная нагрузка на фильтр составляет 17…50 м3/(м2ч), сопротивление фильтра - в пределах 0,5…1,5 кПа. Эффективность очистки - до 99,8 %.
Улавливание частиц пыли в зернистых фильтрах подчиняется тем же закономерностям, что и в волокнистых фильтрах, так как действуют те же механизмы осаждения частиц на препятствии.
При расчете зернистого фильтра сначала определяют характеристики газа при рабочих условиях. Затем степень очистки газа и гидравлическое сопротивление зернистого фильтра заданной толщины.
В настоящее время зернистые фильтры широкого распространения не получили из-за сложности их эксплуатации.
2 вариант:
Зернистые фильтры
Применение зернистых фильтров оказывается целесообразным для очистки газов при температурах, чрезмерно высоких для рукавных фильтров. Кроме того, экономически выгодной является сухая комплексная очистка газов от пыли и газообразных вредных веществ, особенно при условии применения шихтовых материалов в качестве сорбента или катализатора. В ряде случаев зернистые фильтры могут быть с успехом применены для улавливания слипающихся, высокоомных, абразивных пылей или для очистки влажных газов, т. е. в тех случаях, когда применение сухих электрофильтров и рукавных фильтров нецелесообразно Ниже приведены основные области применения зернистых фильтров высокотемпературная очистка газов. Целесообразность применения зернистых фильтров в этом случае обусловлена возможностью очистки уменьшенных объемов газа без нх предварительного охлаждения (в том числе разбавлением воздухом). Кроме того, высокотемпературная очистка газов значительно облегчает утилизацию их тепла.
Сухая комплексная очистка газов от пыли и газообразных вредных веществ с использованием в качестве насыпного слоя соответствующего адсорбента или катализатора. Этот метод позволяет отказаться от дополнительной гидрохимической схемы нейтрализации уловленных продуктов, необходимой при применении абсорбционной схемы улавливания. Этот метод легко осуществляется, когда в качестве адсорбента, катализатора или фильтрующего материала может быть использован материал основного технологического процесса, например шихтовый материал. Поэтому в качестве насадки используют песок, гальку, шлак, дробленые горные породы, древесные опилки, кокс, крошку резины, пластмасс, графита и другие материалы.
Конструкция аппарата зернистого фильтра, предназначенного для очистки газов от мелкодисперсной пылн при высоких температурах, должна обеспечивать: высокую надежность при непрерывной многолетней работе в условиях как обычных, так и агрессивных газовых сред; эффективное улавливание мелкодисперсной пыли; сохранение высокой эффективности улавливания в течение всего периода работы; работу при высоких температурах (400°С и более); заданную эффективность при резком увеличении запыленности, скорости и давления иа входе в случае нарушения технологических параметров установки.
Зернистые фильтры нашли широкое применение при обеспыливании горячих газов в цементной промышленности, при получении редких и драгоценных металлов и др. Кроме фильтрования, гранулы могут выполнять функции теплоносителя и сорбента или катализатора при сочетании процесса фильтрования с адсорбционным нли каталитическим процессом.
Благодаря непрерывному совершенствованию способов регенерации зернистые фильтры находят все более широкое применение в развиты в капиталистических странах (США, Франции, ФРГ, Англии и других) на цементных, известковых, гипсовых заводах, на предприятиях химической промышленности и в новых отраслях промышленности. Конструктивно эти аппараты достаточно просты, имеют низкие эксплуатационные расходы, надежны в работе и обеспечивают достаточно высокую степень очистки газов.
За рубежом разработкой зернистых фильтров в основном заниы ется фирма "Лурги" (ФРГ). Особенностью фильтров этого типа является непрерывное движение рыхлого слоя, который вместе с уловленной пылью проходит через вибрирующий экран. Схема такого устройства показана на рис. 3.32, а. Слой гранул 3, в котором осаждаются частицы пыли, медленно движется вниз. На вибрирующем экране 2 уловленные частицы пыли отсеиваются и попадают в бункер 1. Очищенный фильтрующий материал с помощью механического или пневматического конвейера 9 снова подается наверх в бункер 6. Для непрерывного возобновления движущегося слоя необходима громоздкая и дорогостоящая система циркуляции гранул. Поэтому эти фильтры не получили широкого распространения.
Зернистые фильтры (рис. 3.32, б) обладают тем преимуществом, что позволяют возвращать непосредственно в технологический цикл фильтрующий слой, состоящий из зерен шихты, вместе с уловленной пылью. Подобные установки применяют в асбестовой промышленности для улавливания пыли асбестовой породы из потока газов, выходящих из огневой сушилки. Концентрация пыли на входе в фильтр составляет 14 г/м3, на выходе из фильтра 0,5 г/м3. В качестве фильтровального материала используется кусковая порода размером 12-40 мм.
Зернистые фильтры, регенерируемые импульсной продувкой с периодическим движением вертикального слоя.
На рис. 3.32, в приведена схема такого аппарата, отличительными особенностями которого являются: возможность более длительного работе цикла зернистого слоя без его замены, а при необходимости быстрая смена слоя; способность работать при более высоких температурах; отсутствие вращающихся узлов; возможность использования аппарата при комплексной очистке газов в качестве фильтра-реактора. К недостаткам аппарата относятся неравномерное распределение импульсного потока при регенерации фильтровальной поверхностц и залегание зернистого слоя на жалюзийных решетках тока питания такого аппарата в Запорожском филиале НИИОгаза показали хорошие результаты . Зернистый материал, расположенный на газонепроницаемых перегородках, при выпуске зерен через разгрузочное устройство (см. рис. 3.32, в) остается без движения, удаляется лишь та часть слоя, перед которой нет преграды, расположенная между сеткой 3 и нижними краями наклонных перегородок.
Подача кратковременных импульсов через сопло 5 приводит к неравномерному сбросу зерен с пылью с перегородок, что является недостатком аппарата. Кроме того, при фильтровании через зернистые фильтровальные перегородки происходит значительная потеря энергии импульса.
Рис. 3.32. Схемы зернистых фильтров.
а - с регенерацией продвижением слоя; 1 - бункер для отработанных зерен; 2 - вибросито; 3 - зернистая фильтровальная перегородка; 4,7 - газоходы грязного и чистого газа; 5, 8 - перфорированные экраны; 6 - бункер для свежих зерен; 9 - линия возврата продукта; б - с регенерацией продвижением слоя для сушилок; 1,6 - штуцеры для загрузки свежих и удаления отработанных зерен; 2 - сильфон; а - зернистая фильтровальная перегородка; 4 - решетки; 5, 7 - газоходы чистого и грязного газа; 8 - перфорированный экран; в - с регенерацией импульсной продувкой при периодическом перемещении вертикального слоя; 1 - разгрузочное устройство; 2, 3 - перфорированные экраны (сетки); 4 - зернистая фильтровальная перегородка; 5 - сопло; 6 - загрузочное устройство.
С учетом положительных особенностей аппарата с регенерацией импульсной продувкой в Запорожском филиале НИИОгаза были разработаны принципиально новые конструкции зернистых фильтров типа ФЗВИ для комплексной очистки газов от твердых и газообразных вредных веществ при высоких температурах. При заполнении аппарата инертным фильтровальным материалом он работает как пылеуловитель например при очистке газов сушильных барабанов магнезита в упорной промышленности. При заполнении аппарата катализатиром он используется как фильтр-реактор, например при очистке окиси углерода газов регенерации катализатора каталитического крекинга нефтепродуктов. При заполнении фильтра сорбентом он используется как фильтр адсорбер, например при очистке от фтористых вредных соединений, присутствующих в газах флюсоплавильных у стекловаренных и других печей.
Аппарат ФЗВИ имеет открытую фильтрующую поверхность, и подаче импульса сжатого воздуха вместе с уловленной пылью может быть сброшена часть лобового слоя фильтрующего материала. Инструкция этого аппарата предполагает также возможность постоянного или периодического продвижения фильтрующегося слоя путем сброса его из нижней части кассеты импульсным давлением.
Рис. 3.33. Схема зернистого фильтра с регенерацией импульсной продувкой при периодическом перемещении вертикального слоя.
1 - заслонки; 2, 4 - перфорированные экраны; 3, 7 - газоходы грязного и чистого газа; 5 - зернистая фильтровальная перегородка; 6 - теплообменные трубы.
Рис. 3.34. Схемы зернистых фильтров с регенерацией рыхлением и обратной продувкой.
1 - выхлопная труба циклона; 2 - клапан; 3 - зернистая фильтровальная перегородка; 4 - скребки; 5 - корпус; 6 - привод.
Аппарат этой конструкции предназначен для очистки газов в тех отраслях промышленности и технологических переделах, где в качестве фильтрующего материала может быть использован материал основного технологического производства (например, различные шихтоподготовительные переделы).
Модель фильтра типа ФЗВИ была испытана при производстве сварочных флюсов на Никопольском ферросплавном заводе по очистке газов от пыли и фтористых соединений при температуре до 200 °С, а установке крекинга на Новокуйбышевском нефтеперерабатывающем заводе по дожигу окиси углерода на серийном катализаторе при температуре до 500 °С на Запорожском огнеупорном заводе при очистке газов, отходящих с температурой до 250 °С от барабанчики магнезита шихтовыми материалами.
Зернистым фильтрам этого же типа относятся аппараты, распределения импульсного потока по фильтровальной поверхности можно достичь использованием различных систем и испарительных контуров, вмонтированных внутри.
Зернистые фильтры с регенерацией рыхлением (ворошением) и обратной продувкой (фильтры-циклоны). Различные конструктивные варианты фильтров с регенерацией рыхлением (ворошением) и обратной продувкой (рис. 3.34) находят щирокое применение, особенно за рубежом. Сюда следует отнести аппарат для тонкой очистки газов с температурой выше 500 °С, разработанный фирмами "Сасебо дзюкоге" (Япония) и "Рекс норд" (США). По данным японской фирмы, преимуществами аппарата являются возможность сухой очистки газов с температурой выше 500 °С до остаточной запыленности менее 0,05 г/м3, высокая стойкость фильтрующего слоя против абразивного износа, стабильность процесса очистки, простота обслуживания.
Скорость фильтрации газа в зависимости от типа и размера зерен составляет от 17 до 50 м/мин, газодинамическое сопротивление фильтров находится в пределах от 0,5 до 1,5 кПа. При начальной концентрации пыли более 12 г/м3 перед фильтрами устанавливают циклоны. Остаточное содержание пыли в очищенных газах обычно составляет от 10 до 100 мг/м3, эффективность очистки - от 99 до 99,8%.
К недостаткам фильтров относится накопление пыли в камерах расположенных под фильтрующими слоями гравия, что может привести к забиванию каналов для прохода газа. Кроме того, при вынужденных остановках фильтра возможны конденсация влаги из-за снижения температуры, а также уплотнение фильтровального слоя, что создает сложности ддя его замены В СССР подобные фильтры (типа ФЦГН) разработаны Семибратовским филиалом НИИОгаза.
Зернистые фильтры, с регенерацией удалением лобового слоя скребками. Установлено, что в случае применения в качестве фильтровального слоя фракций 0,5-2 мм достигается высокая степень очистки за счет лобового слоя, непосредственно соприкасающегося с запыленными газами, при этом лишь незначительная часть пыли проникает в глубь слоя. Накопление массы пыли по толщине слоя происходит по экспоненциально убывающему закону. Данное свойство мелкозернистого материала использовано в фильтрах с регенерацией, осуществляемой путем удаления незначительной части лобового слоя скребками (рис. 3.35).
Зернистые фильтры с регенерацией вибровстряхиванием и обратной продувкой. Зернистые фильтры с регенерацией вибровстряхиваиием и обратное продувкой конструкции Научно-исследовательского и проектного института по газоочистным сооружениям, технике безопасности и охране труда в промышленности строительных материалов (НИПИОТстрома) имеют фильтрогальную поверхность одной секции от 1 до 5,4 м2; при групповой компоновке можно достичь производительности по газу от 3 до 150 тыс. м3/ч. В каждой секции расположено три фильтровальных слоя толщиной по 100 мм; в первом слое по ходу газов находятся зерна размером 5 - 10 мм, во втором 3 - 5 мм и в третьем 2,5 - 3 мм (рис. 3.36).
К недостаткам таких фильтров относится наличие значительных вибрирующих масс и гибких эластичных уплотнений, что снижает надежность и механическую прочность узлов и аппарата в условиях высоких температур. Кроме того, вибровстряхивание практически неэффективно без обратной продувки слоев значительным количеством газа (воздуха) с более низкой температурой, что в условиях высокотемпературного фильтрования приводит к резким температурным перепадам конденсации влаги. В последних конструкциях для регенерации ударные волны, которые испытаны на опытно-промышленном образце зернистого фильтра. Использование этого метода реге нерации позволяет упростить эксплуатацию зернистых фильтров и снизить их металлоемкость.
Рис. 3.35. Схема зернистых фильтров с регенерацией удалением лобового слоя скребками.
а - по [29]; б - по [32]; 1,7 - штуцера для загрузки свежих и удаления отработанных зерен; 2 - корпус; 8 - гребенка; 4 - зернистая фильтровальная яерегородка; 5 - перфорированный экран; 6 - люк; 8, 10 - газоходы грязного и чистого газа; 9 - стяжки; 11 - пакет колец; 12 – вал.
Зернистые фильтры, регенерируемые импульсным псевдоожижением фильтровального слоя. В фильтрах фирмы "Дьюкон" (США) в качестве фильтровального слоя использован кварцевый песок с размером частиц 0,8 мм. Этот аппарат опробован для обеспыливания дымовых газов регенератора каталитического крекинга с кипящим слоем на нефтеперерабатывающем заводе.
В СССР разработка конструкций подобных фильтров ведется 3апорожским филиалом НИИОгаза. Отсутствие в этих фильтрах вращающихся и вибрирующих деталей является предпосылкой для их широкого применения при высоких температурах. Кроме того, эти аппараты могут быть автоматизированы по типу рукавных фильтров. Имеется ряд авторских свидетельств на зернистые фильтры, решающих следующие задачи: повышение эффективности очистки; обеспечение компактности конструкции кассеты с увеличенной поверхностью фильтрования повышенной жесткостью каркаса и с минимальной металлоемкостью, способной работать длительное время при высоких температурах без существенных деформаций,улучшение распределения потоков сжатого воздуха при регенерации.
Отличительной чертой зернистых фильтров этого типа является то, что для регенерации зернистого материала используется импульс сжатого воздуха, который псевдоожижает фильтрующий слой, что способствует отделению уловленной пыли от зернистого материала с одновременным ее удалением. Этот принцип был использован при разработке двух разновидностей зернистых фильтров с импульсной регенерацией: с вертикальным фильтрующим слоем (ФЗВИ) и с горизонтальным фильтрующим слоем (ФЗГИ).
Аппарат типа ФЗГИ предназначен для обеспыливания газов с длительным сроком использования (3-5 лет) зернистого материала, т. е. в тех производствах, где отсутствует материал нужной крупности и твердости. В соответствии с этим зернистый материал размещен в отдельных замкнутых ячейках, ограниченных сверху сетками, которые при подаче импульса сжатого воздуха пропускают уловленную пыль, но предотвращают вынос зернистого материала.
Результаты испытаний зернистых фильтров в отраслях промышленности. В 1981 г ВНИИтехуглерод провел испытания зернистого фильтра типа ФНС-50/16 для улавливания сажи, в качестве фильтрующего слоя использовали высокопрочные гранулы технического углерода или пироуглерода. В процессе испытаний были получены следующие результаты:
Рис. 3.36. Схема зернистого фильтра с регенерацией вибровстряхиванием и обратной продувкой.
1 - коллектор; 2, 5 - камеры запыленного и очищенного газа; 3 - пружины; 4 - корпус; 6, 7 - дроссели продувочного воздуха и очищенного газа; 8 - перегородка; 9 - уплотнения; 10 - секция фильтра; 11 - вибратор.
На Московском асфальтобетонном заводе сдан в эксплуатацию зернистый фильтр типа ФЦГН-30 (см. рис. 3.36). При температуре газов, отходящих от барабана, 250 °С, скорости фильтрации 6-20 м/мин и входной запыленности до 15 г/м3 (частицы кварца и клинкера со средним диам. частиц 5-20 мкм) получена степень очистки до 95 %. На Новокуйбышевском нефтеперерабатывающем заводе испытана двухступенчатая схема очистки газов регенерации катализатора в процессе каталитического крекинга.
На первой ступени установки, имеющей производительность до 2000 м3/ч, была предусмотрена очистка газа от пыли в зернистом фильтре с импульсной регенерацией, а на второй ступени - дожигание СО в фильтре реакторе, выполненном по типу аппарата ФЗВИ. Для очистки от пыли был использован слой песка толщиной 150 мм с размером зерен 0,5-1,0 мм. Очищаемый газ имел следующие параметры: содержание СО до 4 % (объемн.), концентрация пыли до 1 г/м3, давление 260-2500 Па, влагосодержание 27-54 г/м3, средний размер частиц 0,5 мкм. Аппарат испытан в диапазоне удельных газовых нагрузок 400-1900 м3/(м5-ч); при этом перепад давления на фильтре состанлял 250-2250 Па, а остаточное содержание пыли не превышало 3 иг/м3. Запыленный зернистый слой регенерировался автоматически через каждые 30 мин подачей двух импульсов сжатого воздуха длительностью 0,8 с. В качестве катализатора применялся катализатор платформинга ДП-56 с частицами цилиндрической формы диаметром 3 и высотой 4 мм. Толщина слоя катализатора около 130 мм.
В течение 360 ч непрерывной работы установки степень очистки от СО в фильтре реакторе составила 99,9 % Перепад давлений к концу испытаний возрос с 2600 до 2900 Па. При последующих испытаниях длительностью 520 ч регенерацию катализатора от пыли осуществляли два раза в сутки подачей двух-трех импульсов сжатого воздуха, при этом перепад давления оставался практически постоянным. В другом случае длительная эксплуатация такого реактора (в течение 1500 ч) при содержании в газах, кроме оксида углерода и пыли (0,5-1,0 г/м3), также углеводородов при продувке слоя катализатора от пыли импульсами сжатого воздуха показала следующие результаты:
После 700 ч эксплуатации катализатора без регенерации полное постановление его активности достигалось тремя сериями импульсов с интервалом в один сутки. Потери катализатора за два года эксплуатации составили 15 л на 100 л загрузки в реактор. Гидравлическое сопротивление слоя катализатора за 400 ч непрерывной эксплуатации без импульсной продувки возрастает от 2600 до 4000 т при одновременном снижении степени очистки. Эти испытания показ ли возможность применения зернистых фильтров для комплексной очистки выбросов, содержащих пыль, оксид углерода и углеводорода.
Испытания двухслойного зернистого фильтра с вертикальными цилиндрическими слоями на очистке фторсодержащих газов при производстве флюсов показали возможность применения подобного аппарата для комплексной очистки выбросов, содержащих мелкодисперсную пыль и фтористые соединения. Температура отходящих газов при испытаниях составляла 325 С. Первый слой по ходу запыленных газов толщиной 0,15 м состоял из дробленого доломита с размером зереи 2-4 мм, второй - из марганцевой руды (толщина слоя 0,1 м, размеры зерен 2 - 4 мм). Общая площадь фильтрации составляла 7,5 м2, удельная газовая нагрузка 1000 м3/(м2ч).
В первом слое в основном улавливалась пыль и частично газообразные соединения. Доулавливание пыли и адсорбция фтористых соединений происходили во втором слое. Отработанные по вертикали слои зерна выводились из аппарата. Продвижение первого слоя осуществлялось при достижении гидравлического сопротивления 1,5 кПа, а второго - при снижении эффективности улавливания фтористых соединений до 95 %. Остаточная запыленность газов не превышала 60 мг/м3 даже при продвижении слоя со средним расходом доломита 100 кг/ч. Период фильтрации запыленных слоев изменялся в зависимости от входной запыленности в диапазоне 10-20 мин. При улавливании фтористых соединений с эффективностью 95-97 % расход марганцевой руды составил 390 кг/ч. Остаточная концентрация фтористых соединений не превышала 33-55 мг/м3. После регенерации (очистки от пыли) дробленый доломит возвращался в аппарат. Отработанная марганцевая руда может быть возвращена во флюсоплавильную печь.
На Челябинском металлургическом комбинате эксплуатируется цилиндрический зернистый фильтр (см. рис. 3.35,6), обеспечивающий очистку дымовых газов 10-т электросталеплавильной печи. Фильтр загружен доломитовой крошкой фракции 2-5 мм. Аппарат рассчитан на 10 тыс. м3/ч газа при газовой нагрузке 0,5-0,6 м3/(м2с). При входной запыленности 5-9 г/м3 остаточная достигает 60-90 мг/м3. Скребковый механизм включается при достижении сопротивления слоя 4 кПа и выключается при снижении сопротивления до 3,4 кПа.
Недостатком фильтров этого типа является большое гидравлическое сопротивление, превышающее обычное почти в два раза. НИПИОТстром разработал зернистые фильтры серии ЗФ с фильтрующей поверхностью одной секции от 1 до 5,4 м2, что при комплектовании в группы обеспечивает пропускную способность их от 3 ДО 150 тыс. м3/ч (табл. 3.21).
В каждой секции имеются трн фильтрующих слоя толщиной до 100 мм; в первом слое по ходу газов находятся зерна размером 5-10 во втором 3-5 и в третьем 2,5-3 мм. Газовая нагрузка (при концентрации на входе в агрегат до 15 г/м3) от 15 до 25 м3/(м2); гидравлическое сопротивление 1200-1500 Па; максимальная температура газа на входе до 400 °С; конечная запыленность 100-120 мг/м3.
Таблица 3.21. Техническая характеристика фильтров.
Фильтры типа ЗФ-4 производительностью около 3 тыс. м2/ч, установленные на силосах цемента в Новороссийске, работают с 1970 г., фильтр ЗФ-6 производительностью около 36 тыс. м3/ч - на фабрике вторичного дробления карьера "Перевал" (г. Слюдянка Иркутской обл.).
В фильтрах ЗЭФ-4 НИПИОТстрома используются материалы с высоким электрическим сопротивлением. В подготовительном нижнем слое находятся гранулы из поликарбоната размером 10-19 мм, а в фильтрующем слое - гранулы полистирола средним размером 3,25 мм. Перед подачей газа насыпной слой приводится в колебательное движение. За счет трения гранулы электрически заряжаются, что позволяет увеличивать степень очистки. При испытании опытного фильтра ЗЭФ-4 для улавливания пыли на цементных силосах степень очистки составляла 99-58 %; концентрация пыли на выходе из аппарата гидравлическое сопротивление 0,7-1 кПа.
При регенерации зернистых фильтров воздействию вибраторов подвергается вся масса фильтра, что в 2-3 раза увеличивает механические нагрузки и износ основных узлов аппарата. Для повышения эффективности регенерации и надежности этих аппаратов НИИцемент разработал конструкцию зернистого фильтра, в котором при регенерации паровоздействию подвергается только фильтрующий слой зерен.
В НИИОгазе разработан фильтр-циклои (рис. 3.37), в котором в качестве первой ступени служит циклон; регенерация насыпного слоя осуществляется ворошением и обратной продувкой.
Запыленный поток, проходя через циклон, подвергается очистке от наиболее крупных частиц пыли, после чего поступает к фильтрующим зернистым слоям 7. Проходя через слой сверху вниз, газ очищается и через переключающий клапан 12 поступает в коллектор очищенного газа 4. По мере осаждения пыли увеличивается гидравлическое сопротивление фильтрующего слоя и подвергается регенерации. Клапан 12 отключает секцию фильтра от коллектора очищенного газа 4 и соединяет ее в раздающим коллектором продувочного воздуха или газа 11. Одновременно включается механизм ворошения 6. Продувочный воздух, проходя через фильтрующий слой снизу вверх, увлекает за собой частицы пыли и уносит их в циклон, где оседают наиболее крупные пылевые частицы. Не уловленная циклонами часть пыли вместе с потоком поступает в другие работающие секции.
При ворошении гранулы, перемещаясь, способствуют отделению пыли, которая неудаляется из насыпного слоя продувочным потоком Регенерация обычно длится 2-3 мин и осуществляется поочередно в каждой секции. На правой стороне рис. 3.37 показана секция аппарата в процессе фильтрования, а на левой стороне - положение переключающего клапана во время регенерации насыпных слоев. Для уменьшения колебаний гидравлического сопротивления установки и ее производительности фильтр-циклон должен иметь не менее четырех секций.
Рис. 3.37. Схема зернистого фильтра-циклона.
1 - циклон; 2 - корпус; 3 - привод ворошителя; 4 - коллектор чистого газа; 5 - вал привода ворошителя; 7 - фильтрующий слой; 8 - камера чистого газа; 9 - пылевыгрузочные устройства; 10 - коллектор грязного газа; 11 - коллектор продувочного воздуха; 12 - переключающий клапан.
Техническая характеристика гравийных фильтров-циклонов.
Условная скорость газа составляет 0,3-0,5 м/с, а при обеспыливании в циклоне - порядка 3-4 м/с. Следовательно, для эффективной работы фильтра-циклона, в котором зернистый слой регенерируют путем перемешивания с обратной продувкой, площадь поперечного сечения фильтра должна быть в 8 -10 раз больше площади сечения циклона. Эти аппараты целесообразно применять при высокой входной концентрации пыли в газе, когда циклон необходим для предварительного обеспыливания.
Дата добавления: 2021-07-19; просмотров: 2516; Мы поможем в написании вашей работы! |
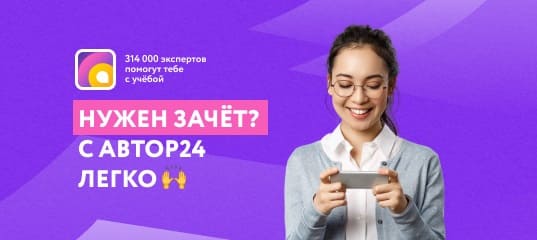
Мы поможем в написании ваших работ!