Восстановление изношенных деталей давлением
Восстановление деталей сваркой и наплавкой
При ремонте оборудования сварку применяют: для получения неразъемных соединений при восстановлении разрушенных и поврежденных деталей, для восстановления размеров изношенных деталей и повышения их износостойкости путем наплавки более стойких металлов.
Автоматизированные процессы сварки и наплавки являются более совершенными и экономически эффективными по сравнению с ручными способами. Наибольшее распространение в ремонтной практике получила автоматическая и полуавтоматическая дуговая сварка и наплавка под слоем флюса. Ручные способы сварки и наплавки менее совершенны, но являются незаменимыми при ремонте деталей машин в неспециализированных ремонтных предприятиях благодаря маневренности, универсальности и простоте процесса.
Газовую сварку применяют для восстановления деталей из серого чугуна. Детали малого размера и веса сваривают без предварительного подогрева, а крупные детали предварительно нагревают.
Электродуговая сварка более экономична и создает более надежное сварное соединение по сравнению с газовой сваркой.
Правильная подготовка детали к сварке обеспечивает высокое качество наплавленного слоя и прочное сцепление его с основным металлом. Перед сваркой детали очищают и разделывают их кромки. Поверхность деталей очищают стальной щеткой, напильником, наждачным полотном, абразивным кругом, пескоструйным аппаратом, затем промывают бензином или керосином, а также подвергают щелочному травлению. Кромки листов свариваемых встык разделывают (скашивают) под углом (60—70°), а края изломов и пробоин выравнивают.
|
|
Наплавка является одним из основных методов восстановления деталей. Она широко применяется в тех случаях, когда трущимся поверхностям необходимо придать большую износоустойчивость. Наплавляют два, три и более слоев часто твердыми сплавами, позволяющими увеличить срок службы деталей в несколько раз. Качество наплавки в значительной степени зависит от состояния восстанавливаемой поверхности. Чугунные и стальные детали из малоуглеродистой стали перед наплавкой обезжиривают с целью удаления масла из пор и трещин. Для этого поверхность детали обжигают газовой горелкой, паяльной лампой или в нагревательных печах. Копоть налет окислов после обжига удаляют с поверхности детали наждачным полотном или ветошью, смоченной керосином или бензином. Участок детали под наплавку обрабатывают стальными щетками или абразивными кругами.
Восстановление деталей металлизацией
Металлизацией называется нанесение расплавленного металла на поверхность детали. Расплавленный металл в специальном приборе — металлизаторе струей воздуха или газа распыляется на мельчайшие частицы и переносится на предварительно подготовленную поверхность детали. Нанесенный слой не является монолитным, а представляет собой пористую массу, состоящую из мельчайших окисленных частиц.
|
|
Способом металлизации восстанавливают размеры посадочных мест для подшипников качения, зубчатых колес, муфт, шеек коленчатых валов и т. п. Чтобы металлизационный слой прочно соединился с поверхностью детали, поверхность очищают от грязи и масла и подвергают пескоструйной обработке.
Твердость металлизационного покрытия определяется качеством наносимого материала.
Гальванические покрытия
Для повышения поверхностной твердости деталей и увеличения их сопротивления механическому износу, а также для восстановления размеров деталей их покрывают слоем хрома (хромируют) толщиной 0,25 и 0,3 мм.
Твердые хромовые покрытия подразделяются на два вида: гладкое и пористое. При гладком хромировании смазка на поверхности детали не удерживается из-за плохой «смачиваемости». При работе деталей возникает сухое трение, на трущихся поверхностях появляются задиры. Для устранения этого недостатка применяют пористое хромирование. В порах и каналах, образующихся на наружной поверхности детали, задерживается смазка, снижающая износ и удлиняющая срок службы деталей. Твердое гладкое хромирование применяют для восстановления размеров деталей, работающих с неподвижными посадками, а пористое — для деталей, работающих при значительных удельных давлениях, повышенных температурах и с большими скоростями скольжения. Поры и каналы в хромовых покрытиях чаще всего образуются электрохимическим способом, при помощи анодного травления.
|
|
Восстановление деталей путем гальванического наращивания слоя стали (осталивание, или железнение) — один из эффективных методов современной технологии ремонта. Осталивание в отличие от хромирования позволяет наносить слой металла значительно большей толщины (2—3 мм и более). Этим способом целесообразно восстанавливать; детали с неподвижными посадками или детали с невысокой поверхностной твердостью; детали, работающие на трение при величине износа более 0,5 мм; детали, работающие одновременно на удары и истира ние.
Твердое никелирование. Повышенная твердость никелевых покрытий достигается за счет применения электролитов специального состава, обеспечивающих получение осадков никеля с фосфором. Никелевые покрытия с содержанием фосфора обычно называют никельфосфорными покрытиями, а процесс их получения — твердым никелированием. Твердое никелирование может осуществляться электрическим и химическим способами. Химическое никелирование является более простым и осуществляется путем выделения никеля из растворов его солей с помощью химических препаратов — восстановителей.
|
|
Восстановление изношенных деталей давлением
Поврежденные и изношенные детали можно восстанавливать давлением. Этот способ основан на использовании пластичности металлов, т. е. их способности под действием внешних сил изменять свою геометрическую форму, не разрушаясь. Детали восстанавливают до номинальных размеров при помощи специальных приспособлений, путем перемещения части металла с нерабочих участков детали к ее изношенным поверхностям. При восстановлении деталей давлением изменяется не только их внешняя форма, но также структура и механические свойства металла. Применяя обработку давлением, можно восстанавливать детали, материал которых обладает пластичностью в холодном или нагретом состоянии. Изменение формы детали и некоторых ее размеров в результате перераспределения металла не должно ухудшать их работоспособность и снижать срока службы. Механическая прочность восстановленной детали должна быть не ниже, чем у новой детали.
К основным видам восстановления различных деталей давлением относятся:
· осадка при восстановлении втулок, пальцев, зубчатых колес;
· раздача при восстановлении пальцев поршней, роликов автоматов и т. п.;
· обжатие при восстановлении вкладышей подшипников и втулок;
· вдавливание при восстановлении зубчатых колес и шлицевых валиков;
· правка для выправления гладких и коленчатых валов и рычагов;
· накатка для увеличения диаметра шеек и цапф валов за счет поднятия гребешков металла при образовании канавок.
Метод пластического деформирования при ремонте деталей применяется не только для восстановления размеров изношенных деталей, но и с целью повышения их прочности и долговечности. Поверхностное упрочнение деталей повышает износостойкость и прочность деталей.
Пластическое деформирование деталей производят также обработкой стальной или чугунной дробью, чеканкой, обкаткой роликами или шариками.
Тема 3 Организация и управление техническим обслуживанием и ремонтом автомобилей
Организация управления производством на СТОА должна обеспечить удовлетворение спроса на услуги, высокое качество и минимальное время ТО и ТР автомобилей при эффективном использовании ресурсов.
Оперативное управление производством на СТОА осуществляет руководитель подразделения по работе с клиентами: начальник производства, начальник или старший мастер участка по работе с клиентами. На СТОА мощностью до шести постов оперативное управление производством осуществляет директор (старший мастер). Руководителю подразделения по работе с клиентами подчинены все структурные подразделения, занятые в управлении производством: группа по работе с клиентами, производственно-диспетчерский отдел, руководители цехов, производственных участков, мастера, бригадиры. В системе управления производством важным элементом является рациональная организация работы участков ТО и ремонта кузовных и окрасочных работ, отделения мелкого и срочного ремонта.
Рабочих, занятых на ТО и ремонте, рекомендуется объединять в комплексные и сквозные бригады с оплатой труда по единому наряду с учетом коэффициента трудового участия. В комплексную бригаду включаются все рабочие всех специальностей, необходимых для выполнения полного объема и комплекса работ по ТО и ремонту автомобилей. В сквозную бригаду входит несколько (как правило, две) однопрофильных бригад, режим работы которых не совпадает. Сквозные бригады создаются для обеспечения непрерывного производственного цикла при выполнении данного вида работ (например, для приемки автомобилей на
СТОА сегодня на завтра). Технический контроль является составной частью производственного процесса обслуживания и ремонта автомобилей на СТОА. Он представляет собой совокупность контрольных операций, проводимых на всех его стадиях, — от приемки автомобиля станцией до выдачи его заказчику после выполнения
необходимого объема работ. В зависимости от места в технологическом процессе технический контроль можно разделить на входной, операционный (текущий) и приемочный (окончательный).
Основная задача входного контроля заключается в определении дефектов, составлении перечня необходимых работ и определении технологически рациональной последовательности их выполнения. Входной контроль организуется на постах приемки автомобилей. Операции контроля выполняются мастером-контролером (приемщиком). Контроль проводят в целях предупреждения возможности появления брака, который так или иначе будет выявлен и устранение которого потребует в дальнейшем значительных неоправданных потерь рабочего времени. Этот вид контроля предусматривает проверку качества жестяницко-сварочных и подготовительных работ, выполняемых перед окраской; шлифовки коленчатого вала перед его установкой в блок двигателя; ремонта заднего моста, коробки передач, амортизатора и телескопической стойки, распределителя и др.
Операционный контроль организуется на производственных участках и в цехах СТОА. Основная задача операционного контроля состоит в проверке и оценке качества выполнения предварительных операций (работ) и определении возможности передачи автомобиля (агрегата) для выполнения последующих работ. На больших и крупных станциях его выполняют мастера ОТК. На средних и малых СТОА функции операционного контроля возлагаются на старших мастеров и мастеров участков, цехов и на бригадиров.
Основная задача приемочного контроля заключается в определении качества и объема выполненных работ. Контроль организуется на производственных участках и постах выдачи.
По отдельным видам работ, таким как проверка и регулировка углов установки управляемых колес, динамическая балансировка колес, мойка автомобилей, противокоррозионная защита кузовов и другим, по которым в ряде случаев заказ-наряд не выписывают, допускается перевод исполнителей на самоконтроль. В этом случае после проведения работ исполнитель ставит в талон контроля качества ТО и ремонта штамп или свою подпись.
Документы, используемые для организации и учета работ СТОА, делят на первичные и сводные. Первичные документы составляют при совершении хозяйственных операций, например при передаче автомобиля заказчиком на СТОА, при получении запасных частей и т.п.
Сводные документы, в основном отчетные, являются сводкой нескольких первичных документов, обобщающей и группирующей их показатели для сокращения числа записей и систематизации учета, например сводный учет расхода запасных частей.
Дата добавления: 2021-03-18; просмотров: 170; Мы поможем в написании вашей работы! |
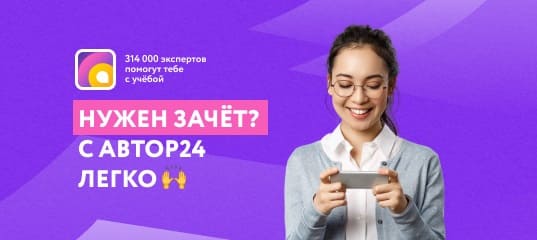
Мы поможем в написании ваших работ!