Требования к деталям, критерии работоспособности и влияющие на них факторы
Раздел 3. Детали машин.
Тема 3.1.
Основные положения. Цели и задачи раздела. Механизм, машина, деталь, сборочная единица. Требования, предъявляемые к машинам, деталям и сборочным единицам.
ДЕТАЛИ МАШИН– научная дисциплина, занимающаяся изучением, проектированием и расчетом деталей машин и узлов общего назначения. Механизмы и машины состоят из деталей. Встречающиеся почти во всех машинах болты, валы, зубчатые колеса, подшипники, муфты называют узлами и деталями общего назначения.
ДЕТАЛЬ – (франц. detail – кусочек) – изделие, изготовленное из однородного по наименованию и марке материала без применения сборочных операций (ГОСТ 2.101-68). Например, валик из одного куска металла; литой корпус; пластина из биметаллического листа и т. д. Детали могут быть простыми (гайка, шпонка и т. п.) или сложными (коленчатый вал, корпус редуктора, станина станка и т. п.).
Среди большого разнообразия деталей и узлов машин выделяют такие, которые применяют почти во всех машинах (болты, валы, муфты, механические передачи и т.п.). Эти детали (узлы) называют деталями общего назначения и изучают в курсе "Детали машин". Все другие детали (поршни, лопатки турбин, гребные винты и т.п.) относятся к деталям специального назначенияи изучаются в специальных курсах. Детали общегоназначенияприменяют в машиностроении в очень больших количествах. Поэтому любое усовершенствование методов расчета и конструцкии этих деталей, позволяющее уменьшить затраты материала, понизить стоимость производства, повысить долговечность,приносит большой экономический эффект.
|
|
СБОРОЧНАЯ ЕДИНИЦА – изделие, составные части которого подлежат соединению на предприятии-изготовителе посредством сборочных операций (свинчиванием, сочленением, пайкой, опрессовкой и т. п.), (ГОСТ 2.101-68).
УЗЕЛ – законченная сборочная единица, состоящая из деталей общего функционального назначения и выполняющая определенную функцию в изделиях одного назначения только совместно с другими составными частями изделия (муфты, подшипники качения и др.). Сложные узлы могут включать несколько простых узлов (подузлов); например, редуктор включает подшипники, валы с насажденными на них зубчатыми колесами и т.п.
КОМПЛЕКТ (ремкомплект) – это набор отдельных деталей, служащее для совершения таких операции как сборка, сверление, фрезерование или для ремонта определенных узлов машин. Например, набор накладных или торцевых ключей, отверток, сверл, фрез или ремкомплект карбюратора, топливного насоса и так далее.
МЕХАНИЗМ – система подвижно соединенных деталей, предназначенная для преобразования движения одного или нескольких тел в целесообразные движения других тел (например, кривошипно-ползунный механизм, механические передачи и т. п.).
|
|
По функциональному назначению механизмы машин обычно делятся на следующие виды:
- передаточные механизмы;
- исполнительные механизмы;
- механизмы управления, контроля и регулирования;
- механизмы подачи, транспортирования и сортирования.
ЗВЕНО – группа деталей, образующая подвижную или неподвижную относительно друг друга механическую систему тел.
Звено, принимаемое за неподвижное, называется стойкой.
Входным звеном называют звено, которому сообщается движение, преобразуемое механизмом в движения других звеньев.
Выходным звеном называют звено, совершающее движение, для выполнения которого предназначен механизм.
Между входным и выходным звеньями могут быть расположены промежуточные звенья.
В каждой паре совместно работающих звеньев в направлении силового потока различают ведущее и ведомое звенья.
В современном машиностроении широкое применение получили механизмы, в состав которых входят упругие (пружины, мембраны и др.) и гибкие (ремни, цепи, канаты и др.) звенья.
Кинематической парой называют соединение двух соприкасающихся звеньев, допускающее их относительное движение. Поверхности, линии, точки звена, по которым оно может соприкасаться с другим звеном, образуя кинематическую пару, называются элементами кинематической пары. По функциональному признаку кинематические пары могут быть вращательными, поступательными, винтовыми и т. д.
|
|
Связанная система звеньев, образующих между собой кинематические пары, называется кинематической цепью. Таким образом, в основе всякого механизма лежит кинематическая цепь.
АППАРАТ – (лат. apparatus – часть) прибор, техническое устройство, приспособление, обычно некая автономно-функциональная часть более сложной системы.
АГРЕГАТ – (лат. aggrego – присоединять) унифицированный функциональный узел, обладающий полной взаимозаменяемостью.
ПРИВОД - устройство, посредством которого осуществляется движение рабочих органов машин. В ТММ применяется адекватный термин – машинный агрегат.
МАШИНА – (греч. "махина" – огромная, грозная) система деталей, совершающая механическое движение для преобразования энергии, материалов или информации с целью облегчения труда. Машина характерна наличием источника энергии и требует присутствия оператора для своего управления. Проницательный немецкий экономист К. Маркс заметил, что всякая машина состоит из двигательного, передаточного и исполнительного механизмов. Категория «машина» в быту чаще употребляется в качестве термина «техника».
|
|
ТЕХНИКА— это созданные человеком материальные средства, используемые им для расширения его функциональных возможностей в различных областях деятельности с целью удовлетворения материальных и духовных потребностей.
По характеру рабочего процесса все многообразие машин можно разделить на классы: энергетические, технологические, транспортирующие и информационные.
ЭНЕРГЕТИЧЕСКИЕ МАШИНЫ - это устройства, предназначенные для преобразования энергии любого вида (электрической, паровой, тепловой и т.п.) в механическую. К ним относятся электрические машины (электродвигатели), электромагнитные преобразователи тока, паровые машины, двигатели внутреннего сгорания, турбины и т.п. К разновидности энергетических машин относятся МАШИНЫ-ПРЕОБРАЗОВАТЕЛИ, служащие для преобразования механической энергии в энергию любого вида. К ним относятся генераторы, компрессоры, гидравлические насосы и т.п.
ТРАНСПОРТИРУЮЩИЕ МАШИНЫ - преобразуют энергию двигателя в энергию перемещения масс (продукции, изделий). К транспортирующим машинам относятся конвейеры, элеваторы, нории, подъемные краны и подъемники.
ИНФОРМАЦИОННЫЕ (ВЫЧИСЛИТЕЛЬНЫЕ) МАШИНЫ - предназначены для получения и преобразования информации.
ТЕХНОЛОГИЧЕСКИЕ МАШИНЫ - предназначены для преобразования обрабатываемого предмета (продукта), состоящего в изменении его размеров, формы, свойства или состояния.
Технологические машины состоят из энергетической машины (двигателя), передаточного и исполнительного механизмов. Важнейшим в машине является ИСПОЛНИТЕЛЬНЫЙ МЕХАНИЗМ,определяющий технологические возможности, степень универсальности и наименование машины. Те части машины, которые вступают в соприкосновение с продуктом и воздействуют на него, называются РАБОЧИМ ОРГАНОМ МАШИНЫ.
В области конструирования машин (машиностроения) широко используется категория ТЕХНИЧЕСКАЯ СИСТЕМА, под которой понимаются искусственно созданные объекты, предназначенные для удовлетворения определенной потребности, которым присущи возможность выполнения не менее одной функции, многоэлементность, иерархичность строения, множественность связей между элементами, многократность изменения и многообразие потребительских качеств. К техническим системам относятся отдельные машины, аппараты, приборы, сооружения, ручные орудия, их элементы в виде узлов, блоков, агрегатов и других сборочных единиц, а также сложные комплексы взаимосвязанных машин, аппаратов, сооружений и т.п.
ПРИВОД - устройство, приводящее в движение машину или механизм.
Привод состоит из:
- источника энергии;
- передаточного механизма;
- аппаратуры управления.
МАШИННЫМ АГРЕГАТОМ называется техническая система, состоящая из одной или нескольких соединенных последовательно или параллельно машин и предназначенная для выполнения каких-либо требуемых функций. Обычно в состав машинного агрегата входят: двигатель, передаточный механизм и рабочая или энергетическая машина. В настоящее время в состав машинного агрегата часто включается контрольно-управляющаяили кибернетическая машина. Передаточный механизм в машинном агрегате необходим для согласования механических характеристик двигателя с механическими характеристиками рабочей или энергетической машины. В зависимости от условий работы машинного агрегата режим управления может осуществляться вручную или автоматически.
КОМПЛЕКС – это тоже сборочная единица отдельных взаимосвязанных машин, автоматов и роботов, управляемые с единого центра для совершения технологических операции в определенной последовательности.Например, РТК – робототехнические комплексы, автоматические линии без участия человека при выполнении технологических операции; поточные линии, где в некоторых операциях участвуют люди, например при удалении оперении птиц.
АВТОМАТ – (греч. "аутомотос" – самодвижущийся) машина, работающая по заданной программе без оператора.
РОБОТ – (чешск. robot – работник) машина, имеющая систему управления, позволяющую ей самостоятельно принимать исполнительские решения в заданном диапазоне.
Устройство, которое выполняет механическое движение, преобразуя энергию, материалы или информацию, называют машиной. В зависимости от назначения машины бывают: энергетические, рабочие, информационные.
Машина состоит из составных частей (агрегатов), сборочных единиц и деталей.
Деталь представляет собой часть машины, изготовленную из единой части металла путем штамповки, ковки, отливки, т. е. без сборочных операций.
Сборочная единица представляет собой совокупность совместно работающих деталей (топливный насос, радиатор и др.).
К составным частям относят наиболее крупные части машины, состоящие из сборочных единиц (двигатель, трансмиссия, ходовая система и др.).
Различают детали машин общего и специального назначения. К деталям машин общего назначения относятся: элементы разъемных и неразъемных соединений; части передач трением и зацеплением; валы и оси, муфты, подшипники; пружины, корпусные детали. К деталям машин специального назначения относятся детали, встречающиеся только в отдельных видах машин. К ним, например, относятся такие детали, как поршень, клапан, шпиндель, лемех и т.п.
Требования к деталям, критерии работоспособности и влияющие на них факторы
Несмотря на большое многообразие современных машин, отличающихся друг от друга назначением, производительностью, скоростью движения рабочих органов и т.д., установлены общие требования, предъявляемые к конструкции самих машин, а также их узлов и деталей.
Машина должна отличаться целесообразностью, легкостью и компактностью конструкции, экономичностью ее изготовления и эксплуатации, прочностью и долговечностью в работе, надежностью и безопасностью действия, привлекательным внешним видом и удобством пользования.
К конструкциям узлов предъявляются требования легкой их сборки и разборки, легкой замены быстроизнашивающихся частей и т.д.
Критериями работоспособности деталей является их прочность, жесткость, износостойкость, виброустойчивость, теплостойкость. Под надежностью деталей и сборочных единиц понимают их свойство сохранять работоспособность в течение заданного срока эксплуатации.
В зависимости от назначения детали ее расчет ведут по одному или нескольким критериям. Например, валы рассчитывают на прочность, жесткость, виброустойчивость, а для резьбовых и сварных соединений главным критерием является их прочность.
Прочность – важнейший критерий работоспособности детали, характеризует ее способность сопротивляться действию нагрузок без разрушения или пластических деформаций. Непрочные детали не могут работать.
Различают поломки деталей при статическом нагружении и при повторно-переменном нагружении, когда рабочие напряжения достигают соответственно предела прочности σв (предела текучести σт) и пределов выносливости σ-1, τ-1.
Жесткость характеризуется изменением размеров и формы детали под нагрузкой. [3] Упругие перемещения деталей не должны превышать допустимых перемещений, устанавливаемых на основании опытов и расчетов. Например, при больших прогибах валов в редукторе резко ухудшается работа зубчатых колес и подшипников.
Износостойкость. В результате изнашивания выходят из строя большинство подвижно соединенных деталей. При этом происходит увеличение зазоров в соединении, что приводит к потере точности работы механизма, возрастанию динамических нагрузок и даже поломке деталей.
Изнашивание увеличивает стоимость эксплуатации, вызывая необходимость проведения дорогих ремонтных работ. Для многих типов машин за период их эксплуатации затраты на ремонты и техническое обслуживание в связи с изнашиванием в несколько раз превышают стоимость новой машины. Этим объясняется большое внимание, которое уделяют в настоящее время трибонике – науке о трении, смазке и изнашивании механизмов. [3]
Повышение износостойкости деталей может быть достигнуто:
- соответствующим выбором материала;
- повышением твердости и чистоты трущихся поверхностей;
- обеспечением условий для жидкостного трения, при котором поверхности деталей разделены тонким масляным слоем. Они непосредственно не соприкасаются, а, следовательно, и не изнашиваются, коэффициент трения становится очень малым (0,005);
- соблюдением рационального режима смазки и предохранения поверхностей от загрязнения.
Виброустойчивость. При высоких скоростях звеньев механизмов могут возникнуть вибрации, которые вызывают дополнительные переменные напряжения и, как правило, приводят к усталостному разрушению деталей. При вибрациях особенно опасно явление резонанса, которое наступает в случае, когда частота собственных колебаний детали совпадает с
частотой изменения периодических сил, вызывающих вибрации, так как при этом резко возрастает амплитуда колебаний и может произойти разрушение детали.
Причинами появления вибрации являются: неуравновешенность движущихся деталей механизма, большие зазоры между сопряженными деталями, неточность изготовления зубьев колес, недостаточная жесткость деталей и корпусов механизмов, периодическое изменение сил и другие причины.
Для предотвращения вибраций необходимо устранить причины, способствующие их возникновению. Часто вибрации можно устранить путем изменения динамических свойств системы, изменения моментов инерции подвижных частей механизма и увеличения жесткости вибрирующих деталей, уравновешивания вращающихся деталей. Для защиты механизма от внешних механических воздействий – толчков, ударов и вибрации – применяются амортизаторы.
Теплостойкость. Тепловые расчеты при проектировании механизмов обычно производятся для решения двух задач:
1) определения температуры нагрева деталей и изыскания способов ограничения ее величины допустимыми пределами;
2) определения величины тепловых деформаций деталей для учета их влияния на точность и надежность механизма.
Пренебрежение к учету влияния тепловых факторов может привести к чрезмерному и неравномерному нагреву деталей механизма и нарушению нормального их взаимодействия.
Чтобы не допустить вредных последствий перегрева на работу машины, если необходимо, вносят соответствующие конструктивные изменения (например, искусственное охлаждение).
Дата добавления: 2021-03-18; просмотров: 118; Мы поможем в написании вашей работы! |
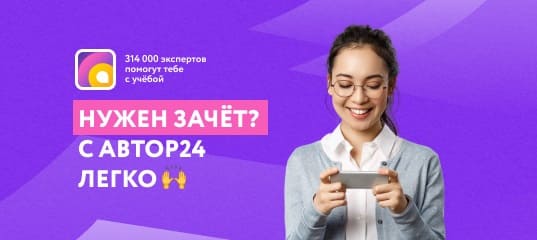
Мы поможем в написании ваших работ!