Получение хлорофилло-каротиновой пасты.
МИНИСТЕРСТВО СЕЛЬСКОГО ХОЗЯЙСТВА РОССИЙСКОЙ ФЕДЕРАЦИИ
федеральное государственное бюджетное образовательное учреждение
высшего образования
«НИЖЕГОРОДСКАЯ ГОСУДАРСТВЕННАЯ СЕЛЬСКОХОЗЯЙСТВЕННАЯ АКАДЕМИЯ»
Заочная форма обучения
Кафедра «Лесная таксация и лесоустройство»
Контрольная работа по дисциплине
Недревесная продукция леса и подсочка
Выполнил студент группы 72
Заочной формы обучения
35.03.01 Лесное дело
Смирнова Ирина Павловна
Проверил:
Мартынова Наталья Валерьевна
Факультет «лесного хозяйства»
Кафедра «Лесная таксация
и лесоустройство»
НИЖНИЙ НОВГОРОД
2020г
Содержание
1. Газификация древесины………………………………………………..3
2. Получение хлорофилло-каротиновой пасты…………………………10
3. Канифольно-экстракционное производство…………………………14
4. Размножение пчел. Практическая работа с пчелами………………..19
5. Требования к сырьевой базе подсочки берёзы………………………23
Список используемой литературы………………………………….......26
1.Газификациядревесины.
Сейчас на промышленных предприятиях отходы древесины и др. биопродукты в лучшем случае сжигаются в печах и топках котлов, которые загружают измельченной щепой или топливными гранулами. Однако, стандартные топки имеют низкий КПД, требуют регулярной очистки и ремонтов, а в атмосферу в виде дыма выбрасываются не сгоревшие сложные и вредные углеводородные соединения и зольная пыль.
|
|
Генераторный газ, как топливо, имеет несомненные преимущества перед прямым сжиганием древесины и др. видов биомассы. Генераторный газ, подобно природному газу, может быть передан на большое расстояние по трубопроводам и в баллонах; его удобно использовать в быту для приготовлении пищи, для отопления и нагревания воды, а также в технологических и силовых установках. Сжигание газа легко автоматизировать; продукты сгорания менее токсичны, чем продукты прямого сжигания древесины и др. видов биомассы.
Генераторный газ используется как сырье для дальнейшей химической переработки и в качестве удобного и эффективного топлива для горелок сушилок, печей, котлоагрегатов, газовых турбин, но чаще, - газопоршневых установок. Таким образом по свойствам он похож на природный газ и может использоваться взамен последнего.
Технология газификации твердых топлив для получения горючего газа не является новой. Пионерами газификации были британцы, немцы и французы (прибл. 1805 - 1815 г.г.). Сначала газ использовался для только для освещения улиц и жилищ при помощи фонарей и ламп, а затем и как топливо. В Москве оборудование для получения искусственного газа появилось на полвека позднее (1865 г.). Тогда английские подрядчики получили монопольное право на освещение города, а также на беспошлинный ввоз оборудования для строительства завода по производству искусственного газа, газопроводов, фонарей, горелок, счетчиков и пр. Уголь для газификации также ввозился из Англии. К 1905 г. Москва располагала 215 верстами газовых сетей, 8735 газовыми фонарями и 3720 частными потребителями газа (историческая справка Мосгаза). Природный газ в Москве появился только в 1946 г. (магистральный газопровод Саратов-Москва). До нач. 60-х годов в СССР газификация твердых топлив была распространена достаточно широко: более 350 газогенераторных установок вырабатывали из разл. типов твердых топлив около 35 млрд. м3/год генераторных газов разного назначения.
|
|
То есть первоначально газовая промышленность занималась изготовлением и распределением генераторного газа и только в середине 20 века стала переходить к газу натуральному.
В 20-50 г.г. прошлого века дровяные газогенераторы устанавливались на автомобили, автобусы, трактора и другую технику, которая изготавливалась серийно (напр. отечественные автомобили ГАЗ-42, ЗИС-21). В лесной промышленности газогенераторными установками оборудовались лесовозные машины и трелёвочные тракторы. На фото показан немецкий мотоцикл, оборудованный весьма компактным газогенератором. После войны транспортные газогенераторы еще долго хранились в мобилизационном резерве.
|
|
Связанная с развитием нефтехимии дешевизна электроэнергии и моторных топлив не стимулировала развития малой и альтернативной электроэнергетики. Сейчас ситуация в нашей стране быстро меняется в пользу применения альтернативных источников энергии т.к. даже простое подключение предприятия или хозяйства к электрической или газовой сети часто становится серьезной проблемой.
Разработкой газификационных установок для древесины и др. твердых топлив сейчас занимаются многие зарубежные и отечественные институты и компании. На отечественном рынке уже есть предложения малогабаритных газификационных установок для фермеров и т.п., но промышленным предприятиям и лесным поселкам нужны более мощные энергетические установки. Газогенераторные установки различаются по мощности: малой – до 100 кВт; средней – от 100 до 1000 кВт; большой мощности – свыше 1000 кВт. Существуют много типов и десятки конструкций газогенераторов, используемых для газификации отходов древесины и др. видов биомассы. Наиболее популярные из них генераторы прямого и обратного горения, а также генераторы с кипящим слоем.
|
|
В газогенераторных установках происходит не только пиролиз; правильнее это процесс называют частичным
(т.е. неполным) окислением углерода (partial oxidation). В газогенераторе сырье проходит четыре этапа преобразования в газ:
Первый этап - быстрое высыхание материала под действием высокой температуры; второй - термическое разложение (пиролиз) биомассы с образованием угля и дегтя, с последующим его испарением и преобразованием в смоляной газ; третий - сгорание органических соединений смоляного газа и части угля; и четвертый, - восстановление на поверхности раскаленного угля двуокиси углерода СО2 до ее моноокиси CO, а воды Н2O - до водорода Н2.
Большая часть реакций происходящих в газогенераторах является экзотермическими, т.е. происходят с выделением энергии. Основными химическими элементами, участвующими в процессе превращения биомассы в газ являются углерод, кислород воздуха и вода. Окислителями являются кислород, двуокись углерода и водяной пар (реакции 1-3). Основными химическими реакциями происходящими при газификации древесины считают:
С + 0,5 О2 → СО2 - 109,4 кДж/моль (1)
С + СО2 → 2СО + 172,5 кДж/моль (2)
С + Н2O → СО + Н2 + 131,2 кДж/моль (3)
С + О2 →2СО2 - 284,3 кДж/моль (4)
СО + H2О ↔СО2+Н2 ± 131,4 кДж/моль (5)
С + 2Н2 → СН4 + 74,8 кДж/моль (6)
СО+ 3Н2→ СН4 + H2О - 206,2 кДж/моль (7)
СО+ Н2→ 0,5СН4 + 0,5 СО2 - 123,8 кДж/моль (8)
Прямой продукт газификации твердых топлив (т. н. сырой газ) всегда содержит некоторые количества углекислого газа СО2, воды H2О, метана СН4 и, кроме того, иногда и высших углеводородов, а при использовании воздуха - еще и NО2. Вследствие наличия в биомассе небольшого количества серы образуется H2S. Скорость газификации твердых топлив существенно зависит от температуры. С повышением давления увеличивается концентрация СН4. Состав получаемого газа зависит от схемы газогенератора и режима процесса.
Выходящий из газогенератора газ имеет высокую температуру и содержит большое количество примесей (золу и смолы), поэтому газогенераторные установки комплектуются специальными системами охлаждения и очистки газа.
Для решения задачи обеспечения автономного энергоснабжения удаленных потребителей с тепловой нагрузкой до нескольких мегаватт и утилизации отходов растительной биомассы наиболее эффективно использование технологии термохимической газификации в аппаратах слоевого типа с воздушным дутьем. Данные установки наиболее просты в конструктивном оформлении и при эксплуатации. Получаемый газ имеет теплоту сгорания 3,5–5,0 мДж/м3 и пригоден для использования в ДВС и топочных устройствах.
В США и странах Евросоюза большое внимание уделяется вопросам утилизации и газификации биомассы, но лидерами в этом направлении становятся Китай и Индия.
В России многие районы недоступны для обеспечения их природным газом, а завоз туда жидкого топлива или угля связан с большими затратами. Оптимальный выход - использование установок по генерированию электроэнергии из биотоплива.
Серийные промышленные электроэнергетические газификационные системы "под ключ" на основе газогенераторов с кипящим слоем для сельскохозяйственных, зерноперерабатывающих, лесных и деревообрабатывающих предприятий производит, например, китайская компания Chongqing Fengyu Electric Equipment.
По предлагаемой компанией технологии измельченные и подсушенные отходы древесины, гидролизный лигнин, солома, рисовая и подсолнечная шелуха, стебли хлопчатника и т.п. из бункера подаются в газификационную колонну. Полученный синтетический газ охлаждается и очищается от пыли и дегтя и поступает в накопитель. Очистка и охлаждение газа осуществляется при помощи циркулирующей в системе оборотной воды. Газификационная установка принципиально проста по конструкции и относительно компактна. Охлаждение воды осуществляется в пруду или бассейне - охладителе. Полученный горючий синтетический газ направляется в газопоршневую установку (газогенератор) или используется на другие цели.
Газификационные установки имеют высокую энергоэффективность. Так на выработку 1 кВт электроэнергии требуется примерно 1,3-1,8 кг рисовой шелухи (соломы) или 1,1 - 1,6 опилок или лигнина. Затраты на комплектное оборудование составляют менее 1000 долларов США на 1 кВт получаемой электрической мощности.
Состав генераторного газа
Состав генераторного газа получаемых из древесных и др. отходов в этих установках приведен в таблице:
компоненты газа | CO | H2 | CH4 | CmHn | H2S | CO2 | O2 | N2 |
количество,% | 17.2 | 4.05 | 6.82 | 1.24 | --- | 15.1 | 0.8 | 54.7 |
Горючими компонентами генераторного газа являются окись углерода (СО), водород ( H2 ), метан (CH4) и другие углеводороды (CmHn). Калорийность получаемого синтетического газа зависит от вида используемого сырья и составляет 1100-1500 ккал/м3 (4.6~6.3 мДж). Например калорийность газа получаемого при переработке рисовой шелухи 1393 ккал/м3 (5.83 мДж/м3);
Содержание смол в полученном газе менее 50мг/Нм3, что соответствует международным нормам, предъявляемым к топливу для двигателей внутреннего сгорания. Синтетический газ не содержит вредных сернистых примесей и соединений.
Газогенерационные установки имеют различную единичную мощность в пределах от 200 до 1200 кВт и проверены во многих странах. В условиях КНР срок окупаемости этих энергоблоков составляет менее 2 лет.
Газификационные установки могут успешно применяться как при организации новых лесных и деревообрабатывающих предприятий, так и для модернизации действующих, в том числе в районах, удаленных от электрических и газовых сетей. Они могут быть интересны также для муниципалитетов, зерноочистительных и сельскохозяйственных предприятий.
Получение хлорофилло-каротиновой пасты.
Из-за ограниченного срока хранения древесную зелень перерабатывают обычно на том предприятии, где ее заготовляют. Она служит сырьем для производства хвойной хлорофилло-каротиновой пасты, эфирных масел и хвойного лечебного экстракта. Извлекают эти продукты экстракцией хвои бензином, паром и водой.
Xлорофилло - каротиновая паста представляет собой густую однородную массу желтовато- или буровато-зеленого цвета с характерным запахом хвои. Паста является поливитаминно-фитонцидным препаратом, ее применяют в медицине и парфюмерной промышленности (ее добавляют в количестве 3—5% в мыло, зубную пасту и кремы). Паста служит сырьем для получения концентратов каротина, витамин Е, хлорофиллина натрия и других ценных препаратов.
Технологический процесс производства включает подготовку древесной зелени, экстракцию смолистых веществ хвои бензином, отгонку бензина и обработку выделенных смолистых веществ. В агрегате древесную зелень подвергают дополнительному измельчению и вальцеванию, чтобы разрушить целостность хвоинок. В естественном состоянии они покрыты тончайшей пленкой, препятствующей процессу экстракции. Подготовленная древесная зелень поступает в промежуточные бункеры, откуда загружается в экстракторы специальной конструкции. Экстрактор состоит из средней цилиндрической части с ложным днищем, верхней откидной крышки с охлаждающим элементом и нижней конусной части с встроенным пароподогревателем. После загрузки сырья в нижнюю часть экстрактора закачивают насосом бензин, который, испаряясь, прогревает хвою. Достигнув верхней крышки, пары бензина конденсируются на поверхности охлаждающего элемента. Стекающие капли бензина проходят через массу хвои и экстрагируют смолистые вещества. Процесс экстракции длится 3,0—3,5 ч. По окончании процесса экстракт сливают в баки, а экстрагированную хвою обрабатывают паром. В холодильнике пары конденсируются. Смесь бензина и воды сливается в флорентину — сосуд, где происходит разделение жидкостей с различной плотностью. Из верхней части флорентины сливается в бак бензин, а из нижней — вода. Полученный экстракт из бака перекачивают в перегонный куб. После отгонки бензина смолистые вещества в виде пасты-сырца сливаются в омылятор. Здесь при перемешивании с раствором натриевой щелочи нейтрализуются свободные кислоты. После нейтрализации влажность продукта доводится до 50%.
В горячем состоянии готовая паста расфасовывается в билоны. Масла добывают из хвои пихты сибирской, сосны, ели и кедра. Пихтовое эфирное масло представляет собой прозрачную жидкость плотностью 900—925 кг/м3 с содержанием борнилацетата не менее 32. Содержание эфирного_масла в пихтовой зелени — до 2,5%..Общим способом получения эфирных масел является отгонка их из хвои водяным паром. Значительную часть пихтового масла получают на стационарных или передвижных установках периодического действия западно-сибирского типа. Установки оборудованы одним или двумя перегонными чанами паровым котлом, баком для воды, холодильником флорентиной и сборником готового продукта. Для получения пара на большинстве установок используют паровые котлы. Древесную зелень предварительно подвергают измельчению и загружают в чан емкостью 7,5 м3. Через массу хвои пропускают пар, который прогревает ее и увлекает с собой эфирное масло. Пары масла и воды направляются в холодильник, где конденсируются и поступают на разделение в флорентину. Годовая выработка пихтового масла на одночанной установке достигает 5 т, на двухчанной — до 8 т.
Для производства масла разработана также установка непрерывного действия типа УНП со шнековым измельчителем древесной зелени. Ее основной частью являются две вертикальные колонны. В первой колонне измельченная масса перемещается вверх при помощи шнека с перфорированными витками и прямотоком обрабатывается паром. Во второй колонне обработка паром ведется противотоком. Производительность такой установки на практике оказалась не выше, чем двухчанной установки периодического действия, а выход и качество масла ниже. Вместе с тем установка обеспечивает полную механизацию процесса загрузки и выгрузки древесной зелени, которая после отгонки масла может быть использована для получения кормов.
Наряду с пихтовым, вырабатывают и другие виды эфирного масла, выход которого из сосновой и еловой хвои примерно в 5—7 раз меньше. Производство масла в этих случаях осуществляется попутно в цехах с комплексной переработкой древесной зелени. Эти эфирные масла как душистые препараты используют для дезодорантов и мыла. После отгонки эфирного масла сосновую или еловую древесную зелень можно подвергать водной экстракции.
Хвойный экстракт, используемый в лечебных целях, получают из сосновой или еловой древесной зелени водной экстракцией сырья. Полученную водную вытяжку упаривают для получения жидкого или твердого хвойного лечебного экстракта. Жидкий экстракт упаривают до плотности 1190 кг/м3, добавляют' к нему поваренную соль и до 1 % эфирного масла. Готовый продукт представляет собой коричнево-черную жидкость с хвойным запахом. Выход экстракта с 50 %-ным содержанием сухого вещества составляет 170—200 кг из 1 т древесной зелени. Твердый брикетированный экстракт получают в виде таблеток по 50 г при более длительном упаривании и с добавкой большего количества соли. Экстракт хорошо растворяется в теплой воде.
Комплексная переработка древесной зелени, которая предусматривает полное использование всех полезных ее компонентов, является наиболее рентабельной и перспективной. Технологическая схема комплексной переработки включает получение эфирного масла, лечебного экстракта и кормовой муки. Древесная зелень дозирующим транспортером загружается в шнековый измельчитель, который подает ее в нижнюю часть первой колонны установки непрерывного действия типа УНП. Здесь ее обрабатывают паром при температуре 115 °С и небольшом избыточном давлении. В перевалочной головке древесная зелень перегружается во вторую колонну, куда также подается пар. Вместе с извлеченным маслом пары воды поступают в холодильник, откуда конденсат стекает в флорентину. Из нее периодически сливаются эфирное масло и конденсат, поступающий в сборник.
Процесс получения лечебного экстракта состоит в следующем. В первой колонне в период прогрева древесной зелени образуется конденсат, который стекает вниз и извлекает из хвои некоторое количество водорастворимых веществ. Дальнейшая их вытяжка осуществляется во второй колонне, куда подаются вода и дистиллят из бака. Образующийся водный экстракт стекает в сборник, затем в горизонтальном и вертикальном испарителях, а так-же с помощью вакуум-насоса, он доводится до 50 %-ной концентрации. В смесителе в него добавляют 0,5 % эфирного масла, после чего готовый продукт разливают в бутылки. Экстрагированная древесная зелень, выходящая из второй колонны, непрерывно отжимается в шнековом прессе. Жидкий продукт отжима направляется в сборник и используется для получения лечебного экстракта, а отжатая зелень поступает на дальнейшую переработку для приготовления корма на участке. Годовой выпуск эфирного масла в цехе комплексной переработки составляет 408 кг, лечебного экстракта 24 т, хвойной кормовой муки 522 т.
Дата добавления: 2021-03-18; просмотров: 124; Мы поможем в написании вашей работы! |
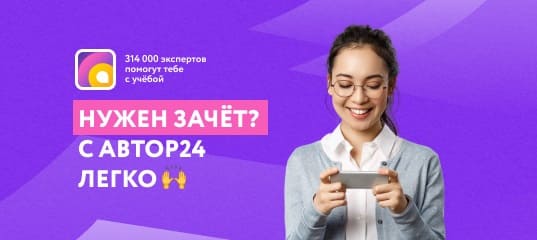
Мы поможем в написании ваших работ!