Основные методы анализа состава и структуры неметаллических включений
Лабораторная работа
АНАЛИЗ СОСТАВА И НЕМЕТАЛЛИЧЕСКИХ ВКЛЮЧЕНИЙ В МАТЕРИАЛАХ
Цель работы: ознакомиться с методами анализа состава и неметаллических включений в материалах.
Задания: 1. Ознакомиться с методами анализа состава и неметаллических включений материалов. 2. Ознакомиться с исследовательским оборудованием. 3. Подготовить отчет по работе.
Общие сведения
Повышение надежности машин и агрегатов требует усиления внимания к проблеме контроля качества продукции металлургического производства. Современное предприятие не может достигнуть требуемого качества продукции, высоких технико-экономических показателей и их непрерывного повышения без четко организованного и постоянно совершенствуемого анализа и контроля продуктов производства. Работа предприятий в условиях рыночной экономики практически невозможна без решения задач повышения качества и конкурентоспособности выпускаемой продукции. В целом это – не только технико-экономическая, но и управленческая проблема.
Литейное и металлургическое производства являются основными поставщиками заготовок и материалов. Доля литых заготовок в различных машинах и конструкциях велика как по номенклатуре, так и по массе, поэтому качество продукции машиностроительного предприятия в значительной степени определяется качеством отливок.
Установленное стандартом, гарантированное качество продукции должно быть обеспечено соответствующим уровнем анализа и контроля ее качественных характеристик. Широкое внедрение и непрерывное совершенствование современных методов анализа и контроля обеспечивает возможность дальнейшего повышения требований к качеству продуктов металлургического производства.
|
|
Высокое качество готовой продукции при минимальных материальных и экономических затратах можно обеспечить эффективной технологией, тщательным ее соблюдением, контролем и регулированием основных параметров технологического процесса с применением современных методов анализа и контроля, включая максимальное использование средств неразрушающего контроля. Необходимо превратить неразрушающий контроль на металлургических и машиностроительных предприятиях из способа сортировки заготовок и готовых изделий в средство активного воздействия на весь производственный процесс, создавать приборы и установки, встроенные в технологический процесс и позволяющие осуществлять контроль качества продукции при полной автоматизации операций контроля с использованием приборов с цифровым отсчетом контролируемых характеристик и применением ЭВМ как для обработки данных, так и для решения логических функциональных задач в процессе измерения.
|
|
Неметаллические включения
Неметаллические включения являются основной плавочной характеристикой стали, в значительной степени определяющей ее свойства. Степень загрязненности включениями, их природа и характер распределения оказывают однозначное влияние на процессы охрупчивания стали при низких температурах. Включения как концентраторы напряжений способствуют зарождению трещин и предопределяют переход стали из вязкого состояния в хрупкое. Повышение общей чистоты стали и получение благоприятной формы включений существенно снижают критическую температуру хладноломкости.
А. А. Байков сформулировал условия, необходимые для получения качественной стали: 1) минимум вредных примесей, 2) отсутствие газовых пузырей и 3) чистота стали по включениям. Если первые два условия на практике выполняются, то третье нарушается наиболее часто. А. А. Байков образно назвал «планктоном» муть мельчайших частиц-включений, находящихся в расплаве во взвешенном состоянии. Они нарушают однородность строения твердой стали и ухудшают ее свойства.
|
|
Неметаллические включения классифицируют по химическому и минералогическому составу, стойкости и происхождению.
По химическому составу неметаллические включения делятся на следующие группы:
1) оксиды: простые – FeO, MnO, Cr2О3, SiО2, А12О, TiО2 и др.; сложные – FeO·Fe2О3, FeO·Al2О3, FeO·Cr2О3, MgO·Al2О3, 2FeO·SiО2, 2MnO·SiО2, 2CaO·SiО2 и др.;
2) сульфиды: простые – FeS, MnS, A12S3, CaS, MgS, Zr2S3, Ce2S3 и др.; сложные (оксисульфиды) – FeS·FeO, MnS·MnO, (Mn,Fe)S·FeO и др.;
3) нитриды: простые – ZrN, TiN, AIN, CeN, NbN, VN и др.; сложные (карбонитриды) – Ti(C,N), Nb(C,N) и др., которые встречаются в легированных сталях, имеющих в своем составе сильные нитридообразующие элементы (титан, алюминий, ниобий, ванадий, церий и др.);
4)фосфиды: Fe3P, Fe2P, Мn5Р2 и др.
По минералогическому составу кислородные включения делятся на следующие основные группы:
1) свободные оксиды – FeO, MnO, Сг2О3, SiО2 (кварц), А12О3 (корунд) и др.;
2) шпинели – сложные оксиды, образованные двух- и трехвалентными металлами типа Ме2+(Ме23+О42-) (ферриты, хромиты, алюминаты, например, FeO · Fe2О3 – магнетит, FeO · Cr203 – хромит, FeO · Al203 – герценит);
3) силикаты, присутствующие в стали в виде стекол, образованных чистым SiО2 или SiО2 с примесями оксидов железа, марганца, хрома, алюминия, вольфрама, а также кристаллических силикатов (ортосиликатов и метасиликатов) типаMe2SiО4 и MeOSiО2 (Fe2SiО4 – файялит, Mn2SiО4 – тефроит (Fe, Mg)2SiО4 – оливин, Ca(Fe, Mg)SiО4 – железистый монтичеллит, MnOSiО2 – родонит и др.).
|
|
По стойкости неметаллические включения разделяют на устойчивые и неустойчивые. К неустойчивым относят включения, которые растворяются в разбавленных кислотах не более 10%-ной концентрации. Неустойчивыми являются сульфиды и оксиды железа и марганца, мелкие включения нитридов алюминия и др. Устойчивые включения – кварц SiО2, корунд Аl2О3, оксиды Cr2O3, ZrO2и др., ряд шпинелей и нитридов, в том числе крупные включения нитрида алюминия, а также некоторые сульфиды и оксисульфиды редкоземельных металлов.
По происхождению в стали неметаллические включения разделяют на эндогенные и экзогенные.
Эндогенные включения образуются в процессе химических реакций, протекающих по ходу плавки, разливки и кристаллизации стали. К ним относятся оксиды, сульфиды, нитриды и фосфиды. Основным источником эндогенных включений в стали являются реакции взаимодействия жидкого металла со шлаком, с газовой фазой, раскислителями и легирующими добавками, а также реакции в процессе кристаллизации стали, имеющие значительное развитие вследствие уменьшения растворимости примесей с понижением температуры металла. В литой стали эти включения находятся в форме кристаллов и глобулей, а в катаной и кованой, в основном, в форме строчек и нитей, ориентированных в направлении деформации.
Экзогенными называют неметаллические включения, механически попадающие в сталь. Обычно это – частицы печного шлака и огнеупоров, с которыми жидкий металл контактирует в процессе плавки, при выпуске из печи в сталеразливочный ковш и во время разливки металла в изложницы. Часть неметаллических включений попадает в металл из шихтовых материалов, но обычно их немного и они сравнительно легко удаляются по ходу плавки. Экзогенные включения присутствуют в стали преимущественно в виде сложных оксидных включений, близких по составу к печным шлакам и огнеупорным материалам.
Эндогенные включения
В процессе металлургического передела кислород, сера и азот, вступая в соединение с элементами шихты и стальной ванны, образуют многочисленные виды неметаллических включений. Выделяемые в ранние периоды плавки (расплавление, окисление) включения успевают удалиться из металла. В зависимости от применяемых раскислителей в большей или меньшей степени удаляются продукты раскисления. Наконец, полностью остаются в металле включения, образующиеся при кристаллизации стали в результате уменьшения растворимости кислорода, серы и азота.
Эндогенные включения в значительной степени характеризуют природу стали и уровень ее свойств. Опытные работы последних лет показали возможность управления природой включений с получением заданных свойств стали. Это направление является основным и наиболее перспективным в электрометаллургии стального литья.
Оксидные включения образуются на всех этапах плавки и разливки стали. Все типы образующихся в стали оксидных включений имеют характерные признаки и могут с достаточной точностью определяться металлографическими методами контроля. Глинозем, корунд (А12O3) встречаются во всех марках стали. На шлифах эти включения имеют вид мелких кристаллов неправильной формы. В литой стали они расположены чаще дезориентированно, реже гроздьями. Включения корунда являются центрами образования оксисульфидных комплексов и в большинстве случаев располагаются внутри включений.
Железная шпинель – герценит FeO · Al2O3 – встречается в сталях, раскисленных малыми добавками алюминия. На шлифах герценитпредставляет собой кристаллы правильной кубической формы, в проходящем свете прозрачен, серо-зеленого цвета.
Силикат марганца – тефроит 2MnO · SiO2 – встречается в сталях, раскисленных без алюминия и содержащих мало кремния. Тефроит аморфен, темного цвета. Чаще встречаемые сложные силикаты железа и марганца nFeO · mMnO · pAl2O3 имеют вид стекол с характерными розетками.
Алюмосиликаты nMnO · mSiO2 · pAl2O3 (легкоплавкие глобулярные включения, дезориентированно расположенные в литой высокомарганцевой стали) – темно-серого цвета, двухфазны вследствие расстекловывания при кристаллизации.
Сульфидные включения. Растворимость серы в твердом технически чистом железе очень мала (<0,003%). Добавки легирующих элементов несколько увеличивают ее растворимость, однако практически можно считать, что сера в твердой стали в основном находится в форме сульфидных включений. Из всех элементов, присутствующих в стали, сера имеет наибольший коэффициент сегрегации, вследствие чего даже при низком ее содержании в крупных отливках и слитках возможна большая загрязненность сульфидами. На участках положительной сегрегации размеры сульфидных включений достигают наибольших величин, а на участках отрицательной сегрегации эти включения более дисперсны.
Образование сульфидных включений происходит не только в жидкой стали, но и в твердой. Имеются доказательства растворимости сульфидов в твердой стали при температуре 900-1300°С. Согласно этим исследованиям, диффузия серы в твердой стали при такой температуре получает значительное развитие и может оказать влияние на характер и форму присутствующих в стали сульфидных включений.
Нитридные включения. В зависимости от плавильного агрегата, методов плавки и марки стали содержание азота изменяется в пределах от 0,003 до 0,03%. Меньше всего азота (до 0,005%) в кислородной конвертерной стали, несколько больше (до 0,007%) – в мартеновской, более всего (0,008-0,012%) в электростали. В углеродистых марках стали содержание азота ближе к нижним пределам. По мере повышения степени легирования такими элементами, как марганец, хром, титан, цирконий, и другими нитридообразующими оно возрастает. В высоколегированных марганцевых, хромистых сплавах содержание азота превышает 0,02%.
Рис. 1 Сетка эвтектических сульфидов по границам зерен
Рис. 2 Типы включений в среднеуглеродистой стали, × 200:
I – глобулярные дезориентированные; II – эвтектические, ориентированные по границам зерен; III – угловатые дезориентированные
Рис. 3 Схема неметаллических включений в комплексно-модифицированной среднеуглеродистой стали, × 1500. Модификаторы присадки, %:
а – 0,1 Al; б – 0,1 Al + 0,15 СК; в - 0,1 Al + 0,15 РЗМ; г – 0,1 Al + 0,2 РЗМ;
д – 0,1 Al + 0,15 СК + 0,15 РЗМ; е - 0,1 Al + 0,5 РЗМ
Экзогенные включения
Как уже отмечалось, экзогенные включения попадают в сталь механически. Это зерна огнеупоров, частицы печного шлака, с которыми металл соприкасается при выпуске из печи и в процессе разливки. В большей степени загрязняются отливки в сырых формах.
При заливке форм жидкая сталь с высокой скоростью передвигается по литниковой системе, оказывая на нее механическое и химическое воздействие. Большая площадь контакта поверхности форм и литников с жидким металлом способствует активной эрозии. Отрыв песчаных зерен и образующихся шлаков с поверхности проводки происходит непрерывно и с увеличением массы отливок возрастает. Например, в отливках массой 2-5 т скорость движения металла в литниках составляет более 1 м/с при удельном расходе стали 10-20 кг/с.
С повышением развеса отливок также возрастает длительность контакта жидкой стали с элементами формы, что усиливает эрозию песчано-глинистых форм. Как показала практика, для получения стали с минимальной загрязненностью экзогенными включениями необходимо соблюдать оптимальный интервал температур заливки форм, так как при увеличении температуры заливки загрязнение стали заметно повышается.
Степень загрязнения стали экзогенными включениями тесно связана с явлениями пригара – внедрения оплавленных песчаных зерен в поверхность тела отливок. Пригар в виде металло-керамической оболочки образуется в результате чрезмерно развитой эрозии поверхности форм и является грубейшим дефектом отливок, в ряде случаев приводящим к массовому браку. Пораженные пригаром отливки требуют зачистки для удаления дефектных зон, теряют товарный вид, выходят за пределы принятых размеров. Естественно, что с увеличением степени пригара соответственно возрастает и глубинное проникновение экзогенных включений.
Образование пригара и других дефектов поверхности отливок в значительной степени вызывается разупрочнением внутренней поверхности формы и стержней при контакте с жидкой сталью. Время, которое необходимо для образования корочки затвердевшего металла, должно быть меньше времени разупрочнения контактной поверхности противопригарного покрытия. Для предупреждения разрушения литниковых каналов при больших скоростях движения жидкой стали (крупные отливки) успешно применяют специальные шамотные трубки.
На эрозию формы оказывают влияние многочисленные факторы: состав стали, интервал ее кристаллизации, степень перегрева, поверхностное натяжение, размеры и конфигурация отливки, скорость движения металла в элементах формы и др. Попытки исследователей изучить воздействие отдельных факторов без их взаимной физико-химической связи приводили к неточным выводам и обобщениям. С этой точки зрения неправильно разделять явления поверхностного пригара на механические и химические.
Многочисленные опыты показали, что металл проникает в поры литейной песчаной формы только тогда, когда на его поверхности образуются оксидные пленки, содержащие закись и окислы железа, закись марганца и другие соединения, которые хорошо смачивают материал формы и поэтому легко просачиваются в поры между зернами песка. Следовательно, одна из существенных причин пригара – окисление поверхностных слоев металла. Окисление железа в контакте с воздухом протекает настолько быстро, что уже в течение первой секунды появляется оксидная пленка из окислов железа толщиной около 1 мкм. Можно предположить, что в процессе заполнения формы жидкой сталью формовочные материалы контактируют преимущественно с тяжелыми окислами. Образующиеся при этом легкоплавкие силикаты становятся цементирующей основой между металлом и зернами песка. Согласно гипотезе А. А. Рыжикова, на поверхности формы последовательно развиваются две реакции:
Feм + Опор. ф. → FеО; FeO + SiO2 → FeO · Si · O2.
Образование окислов на поверхности стали происходит за счет кислорода не только пор формы, но и атмосферы формы.
Для стального литья очень важны качество и состав формовочных материалов. Поэтому литейщики много внимания уделяют разработке новых формовочных составов, обладающих меньшей реакционной способностью к марганцу, железу и их окислам. Например, применение более тугоплавких циркониевых песков в облицовочных и общих смесях улучшает качество поверхности стальных отливок, уменьшает пригар и снижает загрязненность экзогенными включениями.
Можно сделать вывод, что при производстве стального литья основная доля экзогенных включений образуется из материалов формы и их покрытий, причем их состав и огнеупорность имеют первостепенное значение.
Основные методы анализа состава и структуры неметаллических включений
Для определения состава и структуры включений используют различные методы (или комплекс методов). Рассмотрим основные из них.
3.1 Металлографический метод
Металлографический метод исследования включений на шлифах является наиболее простым и удобным. При анализе включений на микроскопе производят наблюдение в светлом и темном полях зрения или в поляризованном свете. Просмотр шлифа с включениями под микроскопом позволяет выявить ряд характеристик этих включений, по которым можно с достаточной степенью точности определить их состав и структуру:
1. Размер включений. Включения находятся в стали в виде частиц определенного размера. Например, включения глинозема чаще всего наблюдаются в виде мелких зерен. В ряде случаев достаточна приблизительная оценка размера включений (очень крупные, крупные, средние, мелкие, очень мелкие).
2. Форма включений. Наблюдаются следующие разновидности форм включений:
1) правильная геометрическая (глобули, прямоугольники, треугольники и др.);
2) неправильная (овалы, многоугольники с искривленными сторонами и др.);
3) вытянутая (в виде нитей и др.);
4) пленочная (по границам зерен или обволакивающая другие включения).
3. Расположение включений. Различают следующее расположение включений в слитке:
1)вверху, в середине, внизу, с краев, в центре дендритной структуры (в осевых и межосевых участках);
2)по сечению шлифа (равномерное по всему шлифу, по краю, по центру);
3)взаимное расположение включений (обособленные частицы, группы, цепочки, одна частица внутри или по краям другой);
4)расположение по отношению к микроструктуре металла (внутри или по границам зерен, с карбидами и т.д.).
4. Строение включений. Включения могут иметь однородное и неоднородное строение. Однородные включения состоят из одной фазы (например, кремнезем, глинозем, твердые растворы), неоднородные из нескольких фаз, достаточно четко различаемых на шлифе.
5. Прозрачность включений. Включения могут быть:
1) прозрачными (кварц и глинозем);
2) полупрозрачными (силикаты с небольшим содержанием оксидов);
3) непрозрачными (силикаты с большим содержанием оксидов);
6. Цвет включений. Различают:
1) собственный цвет, т. е. окраску прозрачных включений при прохождении через них света;
2) отраженный, возникающий вследствие поверхностного отражения.
7. Анизотропность включений. По этому признаку все включения можно разделить на:
1)изотропные;
2)анизотропные.
8. Отражательная способность включений оценивается приблизительно (высокая, низкая, средняя) сравнением силы света, отраженного от включения и окружающего его металла.
9.Пластичность включений определяет их способность к изменению формы в процессе деформации. По пластичности включения могут быть:
1)пластичными;
2)твердыми;
3)хрупкими.
10. Отношение к полировке и твердость включений зависят от состава включений. Хрупкие и твердые включения легко выкрашиваются при полировке, оставляя на шлифе царапины. Замер микротвердости включений осуществляют на специальных приборах (ПТМ-5 и др.) или приставках к микроскопам.
11. Отношение к химическим реактивам также зависит от состава включений. В качестве реактивов используют разбавленные растворы кислот, щелочей, солей и др. При воздействии реактивов поведение включений различных видов неодинаково. Различают три случая воздействия реактива:
1) не действует;
2) изменяет цвет;
3)вытравливает, т. е. растворяет включения.
Совокупность полученных характеристик металлографическим методом достаточно полно характеризует химический состав и структуру включений. При анализе полученных результатов используют классификационные таблицы с характеристиками различных видов неметаллических включений. Если включение имеет своеобразные особенности, не позволяющие отнести его к уже известным, исследование дополняют применением других методов. Металлографический метод имеет следующие недостатки:
1) невозможность определения точного химического состава включений;
2) необходимость использования других методов для качественного определения состава и структуры включений, характеристики которых еще не известны;
3) значительные трудности применения метода для исследования мелких включений.
Исследование включений под микроскопом на шлифе дополняют изучением выделенных включений. Изучение выделенных из металлов включений в проходящем или отраженном свете позволяет определить оптические характеристики включений, т.е. их минералогический состав.
Петрографический метод
Петрографический метод анализа позволяет определить природу и состав оптически прозрачных кристаллических неметаллических включений. Анализ проводят на основании результатов измерения таких оптических свойств (констант) прозрачных кристаллических включений, как показатель преломления света, двупреломление, осность, знак, погасание. Петрографический метод позволяет также определить некоторые характерные признаки включений: размер, форму, прозрачность, окраску, плеохроизм.
Проведение петрографического анализа требует выделения неметаллических включений из металла электролитическим или другими методами. Выделенный осадок обычно не требует измельчения. Отдельные крупные зерна раздавливают между двумя предметными стеклами или истирают в агатовой ступке, предварительно определив их размер под микроскопом. Включения обычно погружают в иммерсионную жидкость с известными физическими свойствами. Приготовленный препарат служит в качестве прозрачного шлифа для изучения включений под поляризационным микроскопом. Определяют форму, прозрачность, окраску и плеохроизм, а также оптические свойства включений.
Микрохимический метод
Химический состав выделенных из металла неметаллических включений можно определить микрохимическим методом, особенность которого заключается в том, что приходится анализировать незначительное количество вещества при условии совместного присутствия его с другими веществами. Поэтому для анализа этим методом используют чувствительные специфические реакции. Для микро- или полумикрохимического анализа включений применяют, в основном, современные физико-химические, а также физические методы, которые в ряде случаев дают удовлетворительные результаты. При этом учитывают, что данный метод анализа включений, выделенных электролитическим методом, дает относительно точные результаты только для стойких включений, которые незначительно разрушаются в процессе обработки осадка и разрушения карбидов.
Микроспектральный метод
Применение микроспектрального метода считается целесообразным в случае необходимости быстрого локального определения состава отдельных крупных включений (>20 мкм) или их скоплений на поверхности шлифа. Существующие установки для определения состава включений прямым или косвенным спектральными способами позволяют определить состав включений на шлифах и в изломах.
Лазерный микрозонд для анализа неметаллических включений в металле включает лазер, микроскоп для работы в отраженном свете, проецирующую оптику и спектрограф. Одна из его конструкций показана на рис. 4.
Рис. 4 Схема лазерного микрозонда: 1 – квантовый генератор; 2 – импульсная лампа накачки (спиральная) для генерации лазерного излучения; 3 – резонатор (рубиновый стержень); 4 – проецирующая оптика; 5 – искровой генератор; 6 – электроды; 7 – анализируемый образец
В данном приборе в качестве лазера используют рубиновый стержень, испускающий мощный световой луч с длиной волны 69,4 нм. Этот когерентный луч проходит через обычный оптический микроскоп и направляется проецирующей оптикой на поверхность шлифа, излома образца или необработанной пробы. Проходя через объектив, лазерный луч фокусируется на площади диаметром 10-40 мкм. Луч лазера, обладающий высокой энергией, испаряет включение с поверхности образца, оставляя след в виде кратера глубиной, равной примерно половине диаметра его луча. Образовавшиеся пары проходят между двумя электродами, находящимися под высоким напряжением, создаваемым генератором. Возникающий искровой разряд возбуждает эти пары, давая спектр, регистрируемый спектрографом. Спектральным анализом пара определяется количество каждого элемента, содержащегося во включениях. При этом отдельные включения или их скопление на шлифе выбирают для анализа лазерным зондом при помощи оптического микроскопа, входящего в состав прибора, при увеличении 400.
Рентгеноструктурный метод
Рентгеноструктурный метод позволяет определить фазовый состав и кристаллическую структуру включений. Для рентгеноструктурного исследования можно использовать металлографические шлифы, осадки включений и крупные единичные включения.
Исследование включений на шлифе обычным рентгеноструктурным методом возможно при условии, если площадь, занятая включениями, составляет не менее 5% площади шлифа; при меньшем количестве включений в металле затрудняется получение четкой рентгенограммы. Однако включения в стали обычно содержатся в значительно меньших количествах, кроме случаев грубых скоплений включений. Поэтому чаще всего осуществляют рентгеноструктурный анализ включений, выделенных электролитическим методом. При этом для получения четкой рентгенограммы необходимо, чтобы фазы, подлежащие определению, содержались в осадке в количестве не менее 20%. Осадок должен быть чистым от карбидов, интерметаллидов и аморфных фаз.
Из осадка изготавливают образец цилиндрической формы диаметром 0,2-0,6 мм. Его получают прессованием с использованием связующих веществ (коллодия, лака) или наклеиванием порошка включений на тонкую стеклянную нить. Осадок включений не подвергают измельчению, чтобы исключить возникновение механических напряжений, приводящих к получению размытых, нечетких линий на рентгенограмме. Съемку рентгенограммы включений проводят в специальных камерах. Для повышения углового разрешения линий на рентгенограмме съемку обычно ведут в фильтрованном хромовом излучении. Сначала снимают рентгенограмму включений без вращения образца, вид линий на которой дает информацию о присутствии во включениях двух или более структурных составляющих. Если линии на рентгенограмме состоят из отдельных рефлексов, и точный замер их затруднен, снимают рентгенограмму с вращением образца. Каждому химическому соединению (фазе), входящему в состав осадка, соответствует своя система линий на рентгенограмме. Расчет рентгенограммы позволяет определить отношение d/n, которое дает возможность по справочным таблицам установить структуру и фазовый состав включений. Наибольшей точности определения структуры включений рентгеноструктурным методом достигают при анализе локально изолированных включений или в прицельной камере со шлифа. Для рентгенографических исследований широко применяют аппараты типа УРС, работающие с крупнофокусными рентгеновскими трубками. Большими возможностями обладают дифрактометры ДРОН-2, ДРОН-ЗМ.
Рентгеновский микроанализ
Особенностью рентгеновского микроанализа при помощи ост-росфокусированного электронного луча является возбуждение характеристического рентгеновского излучения в малом объеме на малой площади. При этом анализируемый участок образца обычно составляет 1-10 мкм, а область возбуждения электронным лучом равна 1-100 мкм3 (от 10-14 до 10-11 г вещества), т. е. в процессе исследования анализируемый образец не разрушается. Микрорентгеноспектральный анализ получил широкое распространение для исследования неметаллических включений без их выделения из металла. Состав включения можно определить, если на это включение направить электронный луч и затем зарегистрировать характеристический рентгеновский спектр атомов элементов, находящихся в возбужденном электронами участке.
Избирательное отражение длин волн характеристического рентгеновского излучения позволяет определить качественный состав включения при сканировании по углам. Количественная оценка состава заключается в сравнении измеренных интенсивностей характеристического рентгеновского излучения определяемого элемента во включении и в чистом эталоне или известном соединении. В первом приближении можно использовать линейное соотношение между относительной интенсивностью и составом:
CA = (I / Is)Cs,
где CA, Cs – соответственно содержание элемента А в образце и в эталоне; I / Is – относительная интенсивность, равная отношению интенсивностей линий элемента А в образце и эталоне.
Наилучшие количественные результаты анализа достигаются при сравнении интенсивности рентгеновского излучения от исследуемого образца и эталона известного химического состава, близкого к исследуемому.
Рентгеновский микроанализатор (микрозонд) включает три основные системы:
1) электроннооптическую, предназначенную для фокусирования пучка электронов на поверхность образца;
2) рентгенооптическую, используемую для анализа возбужденных рентгеновских лучей по длинам волн и интенсивностям и позволяющую проводить качественный и количественный анализ микрообъемов;
3) систему визуального наблюдения, представляющую собой оптический микроскоп, который дает возможность осуществить точный выбор анализируемой фазы.
На рис. 5 представлена принципиальная схема рентгеновского микрозонда.
![]() |
Рис. 5 Принципиальная схема рентгеновского микрозонда: 1 – электронная пушка; 2 – диафрагма; 3 – конденсорная линза (электромагнитная);
4, 5 – диафрагмы; 6 – объективная линза (электромагнитная); 7 – зеркальный
объектив светового микроскопа; 8 – спектрометры рентгеновского излучения
с набором кристаллов-анализаторов; 9 – образец; 10 – источник света
для освещения образца
Источником электронов служит вольфрамовая нить, нагреваемая проходящим током до 2800°С. Между нитью накала, служащей катодом электронной пушки, и анодом подается регулируемое в широких пределах ускоряющее напряжение (5-50 кВ). Ускоренный поток электронов, вылетающих из электронной пушки, фокусируется электромагнитными линзами в зондирующий пучок диаметром до 0,1 мкм, падающий на поверхность полированного образца. Имеющийся световой микроскоп позволяет направить электронный пучок в заданную точку на поверхности анализируемого образца. Под действием электронной бомбардировки из этой точки испускается характеристическое рентгеновское излучение элементов, содержащихся в микрообъеме образца. При помощи рентгеновских спектрометров измеряют длины волн и соответствующие интенсивности излучения, определяя вид и концентрацию элементов в анализируемом микрообъеме. Очень эффективно применение рентгеновского микрозонда для анализа отдельных включений, отчетливо видимых под оптическим микроскопом. Для анализа при помощи рентгеновского микрозонда особое значение имеет качество поверхности шлифа (она не должна иметь выступов и рисок), так как при этом электроны попадают на различные участки поверхности под разными углами, что изменяет угол выхода рентгеновского излучения.
Электронографический метод
Известно, что движущиеся электроны обладают волновыми свойствами и, следовательно, способны к дифракции и интерференции. На этом основано применение электронных лучей для дифракционного изучения структуры включений электронографическим методом и микроскопического исследования при помощи электронного микроскопа (электронно-микроскопическим методом).
Электронографический метод применяют для определения структуры и фазового состава включений в осадке при малом количестве выделенных включений. Осадок включений наносят на пленку-подложку (обычно – из коллодия), которую помещают на металлическую рамку с отверстиями или металлическую сетку с ячейками 0,1-1 мм. Получение четкой электронограммы зависит от чистоты осадка, поэтому при его подготовке очень тщательно удаляют посторонние примеси – карбиды, интерметаллиды и стекла, а также аморфные и кристаллические фазы, образовавшиеся в результате подготовительных операций выделения и обработки осадка. При помощи электронографа, принципиальная оптическая схема которого представлена на рис. 6, получают дифракционную картину (электронограмму), которая в плоскости фотопластинки представляет собой кольцо радиусом r.
Межплоскостное расстояние определяется по формуле:
D = с / r,
где с –- постоянная прибора, с = λ · L, где L – расстояние от образца до фотографической пластинки, мм.
![]() |
Рис. 6 Принципиальная оптическая схема электронографа: А – катод;
Б – фокусирующий электрод; В – анод; а, б – схемы получения дифракционной картины (электронограммы) при фокусировке электронов при помощи одной (а)
и двух (б) электромагнитных линз; в - ход лучей при использовании прибора
в качестве электронного микроскопа; 1 – электронная пушка;
2, 3 – электромагнитные линзы; 4 – кристаллодержатель и анализируемый объект; 5 – дифракционная картина или микроскопическая картина на фотопластинке
Точность определения периодов кристаллической решетки пс электронограмме меньше точности рентгеноструктурного анализа Преимуществом данного метода является то, что в связи с малой длиной волны и сильным взаимодействием электронов с включениями получают четкие электронограммы при меньших размерах кристаллов и меньшем количестве осадка.
4. Выбор методов определения состава и структуры включений
Для определения состава и структуры неметаллических включений, в особенности сложных или их новых видов, используется обычно комплекс методов. Совокупность полученных данных позволяет точно идентифицировать неметаллические включения, выявить источники их возникновения и рекомендовать способы удаления их из металла. В табл. 1 приведены методы и определяемые ими характеристики для различных объектов и размеров определяемых включений, для которых пригодны эти методы.
Таблица 1
Методы определения состава и структуры включений
Метод | Объект анализа включений | Диапазон размеров определяемых включений, мкм | Характеристики, определяемые данным методом |
Металлографический | Шлиф | ≥ 0,5 | Примерный фазовый состав и распределение включений на шлифе |
Петрографический | Осадок Отдельное включение | ≥ 1 ≥ 5 | минералогический состав |
Микрохимический | Осадок Отдельное включение | ≥ 1 ≥ 30 | Химический состав |
Микроспектральный | Шлиф Излом Осадок | ≥ 20 пленки ≥ 1 | Химический состав |
Рентгеноструктурный: микроспектральный локальный общий | Шлиф Отдельное включение Осадок | ≥ 60 ≥ 30 | Структура и фазовый состав |
Микрорентгеноспектральный | Шлиф Излом (реплика) | ≥ 1 ≥ 1 | Состав и распределение элементов по включению |
Электронографический | Шлиф Осадок | ≥ 10 | Структура и фазовый состав |
Электронно-микроскопический | Шлиф, излом Осадок Отдельное включение | ≥ 1 0,005-1 0,005-10 | Структура и фазовый состав |
Контрольные вопросы
1. Классификация неметаллических включений по химическому составу и стойкости.
2. Эндогенные и экзогенные включения.
3. Металлографический метод анализа размера, формы расположения, строения и т.д.
4. Краткая характеристика других методов: петрографический, микрохимический, микроспектральный, ренгеновский, электронографический.
Дата добавления: 2020-12-12; просмотров: 597; Мы поможем в написании вашей работы! |
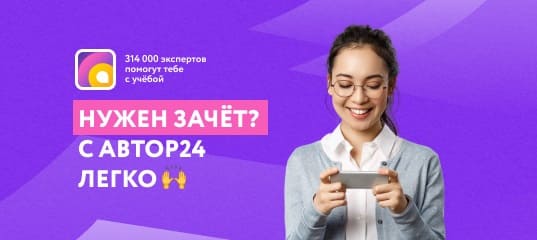
Мы поможем в написании ваших работ!