Структурный синтез при проектировании технологических процессов
Лекция 10. Основные задачи многообъектного технологического проектирования.
Решение задачи сокращения времени на технологическую подготовку производства и выпуска новых изделий, особенно малыми партиями, обеспечивает повышение их конкурентоспособности и дает возможность оперативного реагирования на изменения потребительского спроса. Это, в свою очередь, снижает себестоимость изготовления новой продукции и уменьшает время, которое пройдет от появления новых конструкторских разработок до их внедрения в промышленные образцы.
Для решения этой задачи необходимо определить совокупность необходимых методов и средств образования маршрутов проектирования - последовательностей проектных операций и процедур, ведущих к достижению поставленной цели. При этом методы построения последовательностей проектирования определяются типом проектных задач.
Основой для осуществления многообъектного технологического проектирования являются уже существующие рабочие производственные системы (РПС), ориентированные на выпуск своих производственных заданий (ПЗ) и имеющие фонд свободного времени своего технологического оборудования. Технологическое оборудование, имеющее фонд свободного времени, является ресурсом производственных систем (ПС), необходимым для функционирования виртуальных производственных систем (ВПС). На основе информации о ресурсах ПС оперативно формируется конфигурация (возможно, изменяющаяся во времени), максимально соответствующая требованиям выполняемых ПЗ.
|
|
Особенностью такого подхода является использование элементов интеллектуального управления, позволяющее принимать решения по изменению конфигурации ВПС и формированию управляющей информации в реальном масштабе времени с минимальным участием человека-оператора.
Многообъектное технологическое проектирование с интеллектуальным управлением в РПС включает в себя методики проектирования технологических процессов, методику обеспечения целеустремленной генерации возможных вариантов конфигурации ВПС, методику осуществления верификации сгенерированных вариантов и отбора лучших, а также методику принятия решения, на основе которого осуществляется управление процессом конфигурирования ВПС во времени. В связи с тем, что принятие решения и формирование на его основе управляющего воздействия осуществляется на основе сложных творческих процессов, управление должно строиться как интеллектуальное.
Таким образом, концептуальная идея построения виртуальной производственной системы заключается в мобильной организации временно функционирующих объектно-ориентированных ПС для выполнения текущих технологических процессов на базе РПС. Другими словами, при наличии некоторого ПЗ необходима стратегия выполнения их в РПС, имеющих фонд свободного времени и ориентированных, в свою очередь, на выпуск других, различных по своим параметрам изделий. При этом выполнение спроектированных технологических процессов не должно негативно сказываться на сроках и себестоимости выпуска основной для этих РПС продукции.
|
|
Реализация идеи достигается за счет формирования ВПС рациональной конфигурации, позволяющей выполнять ПЗ в сроки, не превышающие заданные, но близкие к ним, с минимальной себестоимостью. Такой подход обеспечивает отсутствие материальных перестроек при формировании ПС для выполнения ПЗ, минимальные затраты на хранение готовой продукции и минимальные объемы используемых ресурсов оперативных производственных систем (ОПС). Использование свободного технологического оборудования РПС, ориентированных на выполнение своих плановых технологических процессов, обеспечивает существенное снижение времени и трудоемкости технологической подготовки производства.
Данные о предметной области, к которой относится объект, о существующих и разрабатываемых его структурах, известные или прогнозируемые отношения и связи между элементами и свойствами объекта и внешней среды представляют собой порождающую среду. Совокупность информационных потоков, образованных информацией о ПЗ и ОПС, образует порождающую среду, необходимую для генерации вариантов конфигураций ВПС.
|
|
При совместном использовании баз знаний и данных особое значение имеют операции выбора и проекции. По значениям атрибутов, которые рассчитаны на основе информации, полученной из баз знаний, с помощью этих операций проводится отбор необходимой информации из базы данных.
На этапе принятия решения, в соответствии с требованиями и ограничениями более высокого уровня, принимается решение о выполнении некоторого объема ПЗ.
На этапе проектирования производится анализ выбранного ПЗ, разработка технологического процесса в виде набора маршрутов, описаний, выбор оборудования, оснастки и т. д.
На этапе планирования составляется план изготовления изделий по соответствующей технологии на технологическом оборудовании, составляющем ВПС.
На этапе приобретения осуществляется фактическое приобретение сырья, полуфабрикатов, комплектующих, информации, необходимых для производства продукта по соответствующей технологии.
|
|
На этапе производства реализуется план изготовления изделий, в результате которого выполняется ПЗ.
На этапе контроля качества готового продукта осуществляется сравнение продукта с его спецификацией и извещение о несоответствиях, если таковые имеются.
На этапе поставки готовый продукт, прошедший контроль качества, направляется потребителю.
Функции, выполняемые на перечисленных этапах, взаимосвязаны и могут использовать специфичные для той или иной функции данные, разделяемые между несколькими функциями или общие для всех функций.
При решении задачи формирования ВПС необходимо формирование и применение баз данных, которые содержат информацию, полученную на основе основных научных положений технологии проектирования, методов математического моделирования, системно-структурного анализа, теории информации, множеств, математической логики, управления, автоматизированного проектирования и технологии программирования.
Модель системы многообъектного технологического проектирования позволяет не только представить функции и виды деятельности в автоматизированном производстве, но является основой для его системного проектирования. Модель базируется на понятии "управляемое динамическое производство", на котором выполняются следующие последовательные этапы: принятие решения, оценка конструкции, технологическое проектирование, верификация, контроль прохождения ПЗ через ВПС.
Реализация математических моделей функционирования ВПС учитывает, что современное гибкое автоматизированное производство базируется на массовом применении вычислительной техники - начиная от ПС, имеющих, как правило, встроенные микропроцессоры, и кончая автоматизированными рабочими местами конструкторов, технологов, диспетчеров и т. д. В силу физической распределенности этих компонентов объективно возникает задача создания соответствующей распределенной вычислительной системы ЭВМ, охватывающей участки, цеха, заводы, отрасли и т. д.
Эффективность управления реальной ПС зависит от последовательности и значений принимаемых решений, а также от оперативности получаемой информации. Для принятия необходимых решений требуется получение соответствующей информации о ПС в реальном времени, а также о прошлом или возможном будущем. Поскольку время на обработку поступающей информации ограничено, анализ складывающейся производственной ситуации и формирование соответствующей команды управления требуют автоматизации выполнения указанных действий. Это приводит к необходимости использования моделей, имитирующих основные действия оператора при управлении ПС. Такая система должна обладать элементами интеллектуального управления.
На рис. 5.1 представлена структурная модель процесса определения конфигурации ВПС. Генерация вариантов осуществляется на основе эволюционного метода, применяющего генетические алгоритмы.
Для реализации генерации вариантов известен метод комбинирования эвристик. Этот метод позволяет уменьшить требуемую вычислительную мощность всего генетического алгоритма в целом.
По завершении формирования очередных вариантов конфигурации ВПС выполняется процесс их верификации. Целью верификации полученных результатов является оценка вариантов и выбор наилучшего среди них. В случае если на каком-либо этапе генерации сформированный вариант оказывается работоспособным (отвечает условиям целевых функций), такой вариант рассматривается как рабочий, и на его основе формируется команда на практическую реализацию в ПС.
Рис. 5.1. Структура процесса формирования конфигурации ВПС
Верификация является комплексной процедурой, в основе которой лежит имитационное моделирование процессов, протекающих в ВПС. На отдельных этапах имитационного моделирования осуществляется локальная оптимизация с применением таких методов, как линейное программирование, динамическое программирование и т. д. Выбор конкретного метода зависит от типа текущей задачи.
Имитационное моделирование позволяет выделить из общей задачи моделирования отдельные локальные, для решения которых могут быть применены указанные методы. Целью этого этапа является попытка нахождений в рамках сгенерированной текущей конфигурации ВПС наилучшего варианта с точки зрения объемов используемых в ней производственных ресурсов при обеспечении заданных условий.
Если наилучший полученный вариант конфигурации не соответствует заданным условиям, происходит ранжирование сгенерированной популяции. На основе ранжированной популяции осуществляется формирование новой популяции, и далее процесс повторяется до получения рабочего варианта.
После получения массивов данных о технологических операциях, выполнение которых в том или ином составе и последовательности обеспечивает выполнение ПЗ, необходимо формирование окончательных маршрутов их выполнения и последовательности запуска в ВПС.
Эта задача является сложной ввиду высокой вычислительной мощности вследствие высокой размерности. Как показывают исследования, при решении подобных задач следует применять методы эволюционного поиска рационального решения.
Одним из таких методов является метод на основе использования генетических алгоритмов. Согласно методу генетических алгоритмов, возможные решения представляются в виде набора хромосом (популяций). Процесс формирования хромосом может осуществляться двумя способами. При первом способе в качестве генов используются непосредственно проектируемые параметры. Тогда каждому локусу соответствует одна технологическая операция, а генами являются операции из маршрута выполнения ПЗ. Значением i-го гена будет технологическая операция, выполняемая i-й в маршруте обработки.
При втором способе генами являются не параметры технологического процесса (проектируемые параметры), а номера эвристик, используемых для определения последовательности технологического маршрута.
Такой подход получил название метода комбинирования эвристик. Этот метод предполагает поиск последовательности эвристик, обеспечивающий оптимальный вариант технологических маршрутов и их состав. При использовании указанного метода число требующихся генов в хромосоме в два раза меньше, чем при использовании первого способа. Если число применяемых эвристик равно К, то мощность W множества возможных хромосом составляет
![]() | (5.1) |
где - число наименований элементов, составляющих ПЗ.
Для организации алгоритма поиска рабочего варианта распределения ТП в ВПС вводят ограничения целевой функции:
- задействование минимального числа слоев ОПС, т. к. в этом случае сокращается объем транспортных расходов, уменьшается количество договоров и производственных связей;
- выполнение заданных сроков, т. к. срыв сроков недопустим;
- обеспечение минимальной себестоимости.
Для решения поставленной задачи используются следующие эвристики.
Эвристики для выбора очередной технологической операции:
- выбирается ПЗ с наиболее "коротким" сроком;
- выбирается ПЗ с наименьшим временем окончания обслуживания на предыдущей стадии;
- выбирается ПЗ с наименьшей длительностью выполнения очередной операции;
- выбирается ПЗ с наибольшей длительностью выполнения очередной операции;
- выбирается ПЗ с аналогичной выполняемой операцией на данном виде технологического оборудования.
Эвристики для выбора ПС
- выбирается ПС, в которой есть возможность выполнения необходимых специфических технологических операций;
- выбирается ПС, в которой есть возможность осуществления всего необходимого набора технологических операций;
- выбирается ПС, в которой выполнение ПЗ будет иметь минимальную себестоимость;
- выбирается ПС, в которой выполнение очередной операции ПЗ закончится раньше, чем в других;
- выбирается ПС, в которой время выполнения очередной операции минимально.
Полученные две группы эвристик обозначим, соответственно, символами и
. Тогда каждую эвристику первой группы обозначим как
, а каждую эвристику второй группы обозначим как
. Используя разработанные эвристики в их обозначениях, формируют комбинации из 30 возможных вариантов.
Применение метода комбинирования эвристик предусматривает формирование популяции хромосом, состоящей из генов - аналогов каждой из перечисленных в табл. 5.1 комбинаций эвристик. Размер каждой хромосомы определяется числом задействованных единиц технологического оборудования в ВПС. Размер популяции определяется количеством ПЗ. Структура популяции на некотором промежуточном этапе имеет следующий вид (табл. 5.2):
Таблица 5.1. | |||||||||||
| | | ![]() | ![]() | |||||||
| | | ![]() | ![]() | |||||||
| | | ![]() | ![]() | |||||||
| | | ![]() | ![]() | |||||||
| | | ![]() | ![]() | |||||||
| | | ![]() | ![]() | |||||||
Таблица 5.2. | |||||||||||
![]() | ![]() | | ![]() | ![]() | | ||||||
![]() | ![]() | ![]() | | ![]() | ![]() | | |||||
![]() | ![]() | ![]() | | ![]() | ![]() | | |||||
![]() | ![]() | ![]() | | ![]() | ![]() |
| |||||
![]() | ![]() | ![]() | | ![]() | ![]() | | |||||
На основании анализа эволюции хромосом от популяции к популяции производится модификация конфигурации ВПС. Если в результате эволюции формируется рабочий вариант, удовлетворяющий целевой функции, производится попытка исключения из состава ВПС технологического оборудования или даже целой РПС, использованию которой соответствуют эвристики, минимально повторяющиеся в последовательности генов хромосомы.
В случае если в результате эволюционных преобразований не удается получить работоспособный вариант, в состав формируемой ВПС вводят дополнительные единицы технологического оборудования используемых РПС, или элементы других, не используемых до этого частей РПС, которые отвечают эвристикам, максимально часто встречающимся в последовательности генов хромосомы.
Структурный синтез при проектировании технологических процессов
В основе решения задач структурного синтеза различной сложности лежит перебор вариантов счетного множества. При переборе каждая проба включает:
- создание (поиск) очередного варианта;
- принятие решения о замене ранее выбранного варианта новым;
- продолжение или прекращение поиска новых вариантов. Задачи структурного синтеза при автоматизированном технологическом проектировании зависят от уровня сложности.
В наиболее простых задачах синтеза (первого уровня сложности) определяется структура технологического процесса или его элементов (операции, переходы). В этом случае часто используют таблицы применяемости (табличные модели).
Для полного перебора вариантов структуры из конечного множества необходимо задавать перечень всех элементов этого множества (второй уровень сложности структурного синтеза). Такой перечень создается в виде каталога типовых вариантов структуры, например типовых технологических маршрутов. Тогда для данного класса (группы, подгруппы или вида) деталей устанавливается так называемый обобщенный маршрут (обобщенная структура) обработки. Он включает ряд операций обработки, характерный для определенного класса, подкласса или группы деталей. Перечень является упорядоченным и представляет собой множество существующих индивидуальных маршрутов. Маршруты имеют типовую последовательность и содержание, причем они отражают передовой производственный опыт предприятия или отрасли.
При третьем уровне сложности структурного синтеза решаются задачи выбора варианта структуры во множестве с большим, но конечным результатом известных вариантов. Для решения таких задач используют алгоритмы направленного перебора (например, алгоритмы дискретного линейного программирования), алгоритмы последовательные, итерационные и другие, сведение задачи к полному перебору путем ограничения области поиска на стадии формирования исходных данных. Например, оптимизация плана обработки поверхности представляет задачу структурного синтеза, когда выбор варианта плана происходит во множестве с большим, но конечным количеством известных вариантов. Для поиска оптимального варианта применяют алгоритмы дискретного программирования, находят условия, которым должен удовлетворять оптимальный многошаговый процесс принятия решений. Подобный анализ наз ывают динамическим программированием. Оптимальная стратегия обладает тем свойством, что, каков бы ни был путь достижения некоторого состояния (технологического перехода), последующие решения должны принадлежать оптимальной стратегии для части плана, начинающегося с этого состояния (технологического перехода).
К третьему уровню сложности структурного синтеза технологического процесса и его элементов также относятся задачи целочисленного программирования; при этом к требованиям линейности критерия и ограничений добавляется условие целочисленности переменных.
Задачи структурного синтеза четвертого уровня сложности (выбор вариантов во множестве с заранее неизвестным числом элементов или вообще в бесконечном множестве) решаются при активном участии технолога-проектировщика и реализуются в режиме диалога с ЭВМ. Технолог, работающий в режиме диалога с ЭВМ, выбирает такой вариант структуры, который представляет собой оптимальный компромисс между производительностью работы автомата и вероятностью обеспечения заданного качества выполнения операций. ЭВМ помогает технологу принять решение об изменении структуры, рассчитав по программе режимы работы и производительность автомата.
Общую трудоемкость проектирования можно уменьшить с помощью перехода от диалогового режима к пакетному.
Подобные задачи решают путем применения процедур обучения (процедур формирования понятий). В качестве процедур обучения применяют программы распознавания и классификации. При этом происходит перераспределение рутинной и творческой работы при использовании пакетного режима более высокого уровня, технолог занимается подготовкой исходных данных и проверяет окончательный результат.
Пятый, самый сложный уровень структурного синтеза направлен на создание принципиально новых технологических процессов и решается так называемым поисковым конструированием (искусственный интеллект).
Одним из путей поискового конструирования является использование метода эвристических приемов.
- Уяснение или формулирование ТЗ.
- Выбор одного или нескольких аналогов (прототипов) технологического процесса.
- Анализ прототипов, выявление их недостатков и формулирование задачи в виде ответов на вопросы:
- каковы показатели качества в прототипе синтезирующего технологического процесса и насколько желательно их улучшить;
- какие новые параметры качества должен обеспечить создаваемый технологический процесс и какие параметры качества должен утратить рассматриваемый прототип.
- Решение задачи.
Большие трудности, возникающие при поисковом конструировании и эвристическом программировании, привели к появлению экспертных систем. В основе экспертных систем лежит база данных, используемая экспертом (технологом-пользователем) в режиме диалога. Недостатком таких систем явилась зависимость качества проектных технологических решений (в частности, проектирование маршрутной и операционной технологий) от уровня подготовки эксперта. Другой недостаток заключается в ограничении круга решаемых задач и их размерности.
Необходимость повышения уровня интеллектуализации автоматизированного процесса синтеза технологических решений при высоких размерностях решаемых задач потребовала разработки принципиально новых решений, одним из которых явилось создание и использование метода генетических алгоритмов.
Основная философия генетических алгоритмов - оптимизация на основе эволюционных принципов естественных хромосом, т. е. отбор, скрещивание и мутация популяций параметров по принципу "выживания" теории Дарвина. Как первый шаг, вероятность отбора используется для воспроизводства. Пересекающиеся операторы применяются для обмена и повторного комбинирования исходной информации, и, наконец, операторы мутации изменяют полученную информацию для объединения отдельных решений.
Генетические алгоритмы первоначально считали методами исследования, пригодными только для академических целей. Однако вскоре они обеспечили хорошие решения в широком диапазоне производственных проблем, и, что наиболее важно, эти алгоритмы легко корректировались в соответствии с решаемыми задачами и ограничениями. Необходимо лишь постичь искусство кодирования задач оптимизации в генетическую информацию. Генетические алгоритмы обеспечивают большой потенциал, который широко используется для оптимизации производства, планирования и управления предприятиями.
В любой задаче оптимизации на основе генетических алгоритмов есть два главных процесса. Сначала проектируют модуль генетических алгоритмов, а затем моделируют испытания и оценки. Граничные условия определены параметрами исследуемого процесса. Постановка задачи оптимизации для достижения главной цели и возможных альтернатив осуществляется на базе анализа структуры основных массивов производственных данных предприятия. Генетический алгоритм использует некоторый начальный фактический массив этих данных. Если этот предварительный массив адаптируется моделью с ограничениями, происходит возврат к модулю генетических алгоритмов. Если функция соответствия удовлетворена, получаем решение задачи. Во втором поколении модуль генетических алгоритмов обрабатывает первую популяцию параметров и создает новый список параметров, продолжая поиск необходимых мутаций, пока окончательный вариант не удовлетворит функцию соответствия или не закончится заданное пользователем время работы алгоритма. Этот тип системы с применением р азработанных фирмой Siemens инструментов и генетических алгоритмов был внедрен на заводах Megasteel (Малайзия), Zhuijang (Китай), Thyssen Krupp Stahl (Германия) и др.
Применение генетических алгоритмов предполагает отображение возможной структуры технологического процесса в виде хромосомы (фреймов), состоящей из генов (полей). Каждый ген является аналогом операции в технологическом маршруте.
При формировании структуры технологического процесса используется набор эвристических правил, позволяющий эффективно формировать конкретные структуры. Оценка эффективности проводится на основе расчета значений целевой функции и анализа полученных результатов. Реализация такого подхода осуществляется на основе алгоритма, представленного на рис. 5.2.
Рис. 5.2. Генетический алгоритм
Совокупность возможных структур технологического процесса, представленная в виде хромосом, образует популяцию. Процесс решения задачи сводится к формированию новых популяций путем модификации предыдущих. Модификация основана на формировании новых хромосом путем скрещивания лучших (согласно целевой функции) хромосом из предыдущей популяции. Это позволяет достаточно быстро находить работоспособный вариант при решении задач высокой размерности.
Контрольные вопросы
- Дайте пояснения к понятиям РПС, ПЗ, ПС, ВПС.
- Что понимают под интеллектуальным управлением и какие возможности оно дает?
- Что включает в себя многообъектное технологическое проектирование с интеллектуальным управлением в РПС?
- Что дает создание оперативных производственных систем?
- Что входит в понятие "порождающая среда"?
- Что представляет собой метод комбинирования эвристик?
- От чего зависит эффективность управления реальной ПС?
- В чем заключается проведение верификации?
- Поясните суть ранжирования сгенерированной популяции.
- Как используются методы эволюционного поиска рациональных решений?
- Как происходит процесс формирования хромосом?
- Назовите примеры эвристик для выбора очередной технологической операции.
- Назовите эвристики для выбора производственной системы.
- Что лежит в основе экспертных систем?
- Чем объяснить создание и использование метода генетических алгоритмов?
Дата добавления: 2021-03-18; просмотров: 128; Мы поможем в написании вашей работы! |
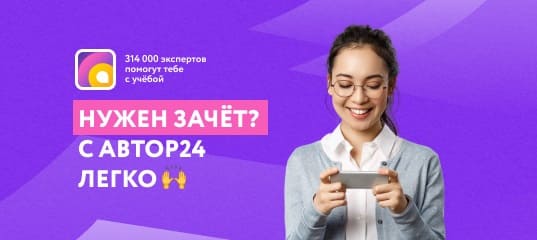
Мы поможем в написании ваших работ!