Назначение и область применения основных методов.
Механическая обработка применяется: как самостоятельный метод восстановления деталей под ремонтный размер и постановку дополнительных ремонтных деталей; для подготовки заготовки к выполнению определенной технологической операции, например металлизации; для окончательной обработки заготовок после пластического деформирования или наращивания слоя металла на изношенные поверхности. Обработкой под ремонтный размер восстанавливают геометрическую форму, требуемую шероховатость и точность изношенных поверхностей деталей, величину зазора в соединении деталей. Дополнительные ремонтные детали применяют с целью компенсации износа рабочих поверхностей деталей, а также при замене изношенной или поврежденной части сложных деталей. При этом за счет материала дополнительной ремонтной детали экономично могут быть обеспечены заданные эксплуатационные требования к изделию в отношении износостойкости, противозадирных свойств, контактной прочности и т.д.
Пластическое деформирование применяют при восстановлении размеров деталей, их формы, усталостной прочности, жесткости, износостойкости и других физико-механических свойств. Сварка и пайка предназначены для восстановления целостности и устранения механических повреждений деталей (трещин, отколов, пробоин и т.п.), а наплавка и напыление —для наращивания слоя материала на изношенные поверхности деталей, как правило, под последующую механическую обработку с целью восстановления их размеров и массы, износостойкости и других свойств.
|
|
Гальванические и химические методы восстановления широко применяются в ремонтном производстве для: — нанесения слоя материала на изношенные поверхности деталей (хромирование, железнение, никелирование) с целью восстановления размеров и эксплуатационных свойств (износостойкости и др.); — защиты деталей от коррозии (цинкование, оксидирование); — защитно-декоративных целей (хромирование, никелирование, цинкование, оксидирование); — придания поверхностям деталей специальных свойств — хорошей прирабатываемости (меднение, лужение), повышенной отражательной способности (хромирование, никелирование) или электрической проводимости (меднение, серебрение) и т.д.; — защиты от науглероживания при цементации (меднение), а также как подслой под другое покрытие (медь, никель) или как грунт под окраску.
Электрофизические и электрохимические методы, предназначенные для удаления слоя металла, применяют в основном при обработке покрытий с высокой твердостью, когда традиционные методы механической обработки невозможны или экономически невыгодны. Электрофизические методы, обеспечивающие нанесение слоя металла, применяются, преимущественно, для упрочнения и повышения износостойкости поверхностного слоя детали (электроискровое упрочнение, лазерное микролегирование, вакуумные конденсационные методы нанесения покрытий и др.).
|
|
Термическая и химико-термическая обработка применяются для восстановления и придания материалу заготовки требуемой структуры и физико-механических свойств, необходимых для обработки заготовки (отжиг) и эксплуатации детали (закалка, легирование поверхностного слоя и т.д.).
Отмеченные способы восстановления деталей обеспечивают требуемый уровень качества, который достигается благодаря правильному выбору способа, а также в результате управления процессами нанесения покрытий и последующей обработки деталей.
Например, повышение износостойкости поверхностного слоя детали может быть обеспечено методами, относящимися ко всем указанным выше группам. По физической сущности эти методы делятся на две основные группы: — методы, основанные на формировании структуры и субструктуры поверхностного слоя металла за счет изменения его химического состава (термическая и химико-термическая обработка, лазерное микролегирование и т.д.); — методы, основанные на создании на восстанавливаемой детали слоя металлического или неметаллического материала (установка дополнительной ремонтной детали, наплавка и напыление материала, электролитическое покрытие, осаждение материала из газовой и паровой фаз, нанесение полимерных материалов, эмалирование и т.д.
|
|
ВОССТАНОВЛЕНИЕ ДЕТАЛЕЙ МЕТОДОМ РЕМОНТНЫХ РАЗМЕРОВ Восстановление сопряжения с применением ремонтных размеров заключается в том, что более дорогую и ответственную деталь обрабатывают по изношенной поверхности под ремонтный размер, а сопряженную деталь заменяют новой, имеющей тот же ремонтный размер, обеспечивая требуемый зазор между деталями. Вместо новой детали может использоваться восстановленная до соответствующего размера изношенная деталь. Следовательно, ремонтный размер — это ближайший к номинальному размер, получаемый обработкой изношенной детали при обеспечении требуемой геометрической формы и шероховатости поверхности. Различают стандартные, регламентированные и свободные ремонтные размеры. Стандартные ремонтные размеры применяют при производстве запасных частей. Восстанавливаемая деталь может иметь несколько ремонтных размеров: 1-й, 2-й и т.д., каждому из которых соответствует определенный размер поверхности. Стандартные ремонтные размеры и допуски на них устанавливает разработчик изделия или завод-изготовитель. Все ремонтные предприятия восстанавливают сопряженные детали в соответствии с ними. Регламентированные ремонтные размеры устанавливаются техническими условиями на ремонт ряда деталей и соединений. Обработку под стандартные и регламентированные ремонтные размеры ведут до тех пор, пока не будет достигнут последний ремонтный размер детали. Преимущество этого способа заключается в том, что он позволяет иметь готовые для замены детали и осуществлять ремонт, соблюдая принцип частичной взаимозаменяемости. Свободные ремонтные размеры предусматривают обработку деталей до получения правильной геометрической формы и требуемой шероховатости рабочих поверхностей. Сопряженная деталь подгоняется к отремонтированной детали до ее размера. Способом ремонтных размеров восстанавливают и резьбовые соединения. В этом случае изношенную резьбу в более дорогой детали резьбовой пары удаляют и заново нарезают резьбу меньшего размера на валу или большего во втулке.
|
|
Дефектация предназначена для оценки технического состояния деталей и их пригодности к дальнейшей эксплуатации путем выявления дефектов деталей и их соединений, а также для изучения и анализа причин их появления. Дефектацию выполняют методами дефектоскопии после очистки, обезжиривания и мойки деталей. Под дефектоскопией понимается совокупность физико-технических и химических методов неразрушающего и разрушающего контроля материалов и изделий на отсутствие в них дефектов. Крупные детали машин обычно дефектуют в разборочном отделении, используя необходимые переносные и передвижные приборы и оборудование. При ремонте узлов на специализированных участках дефектацию деталей выполняют там же. Остальные детали дефектуют в специальном отделении, оснащенном соответствующими инструментами, приборами и стендами. Дефектация деталей проводится в соответствии с техническими условиями на проверку и сортировку деталей, отражающими их возможные дефекты, способы их установления и необходимые для этого технические средства. В технических условиях указываются значения допускаемых износов, размеры деталей, годных к использованию без восстановления и подлежащих восстановлению, и предельные размеры деталей для выбраковки. Технические требования на дефектацию деталей разрабатываются заводами-изготовителями машин и их узлов. Они оформляются в виде карт, в которых по каждой детали приводят общие сведения; перечень возможных ее дефектов; способы выявления дефектов; допустимые без восстановления размеры детали и оптимальные способы устранения дефектов. По результатам дефектации детали делят на 3 группы. Годные детали, износ которых находится в пределах допусков, предусмотренных браковочными картами. На каждой годной детали, прошедшей контроль, ставят условный знак обычно зеленой краской или клеймо контролера.
Годные детали направляют на сборку или на склад годных деталей. Детали, подлежащие восстановлению, износ и повреждения которых могут быть устранены применяемыми на предприятии технологическими методами. Такие детали маркируют условными знаками (цифрами или краской различных цветов в зависимости от способа восстановления) и направляют в производство или на склад заготовок ремонта.
Детали, не пригодные для восстановления по технико-экономическим соображениям. Их маркируют обычно красной краской и направляют на склад как лом с указанием марки металла, из которого изготовлена деталь.
РАЗБОРКА МАШИН Общие положения Разборка это комплекс выполняемых в установленной последовательности операций, предназначенных для разъединения машин и оборудования на сборочные единицы и детали. Степень разборки обусловливается видом ремонта и техническим состоянием объектов разборки. Практикой ремонтного производства выработаны общие правила разборки машин. В первую очередь снимают легкоповреждаемые и защитные части (электрооборудование, топливо- и маслопроводы и т.д.), а затем крупные сборочные единицы (редукторы, двигатели, насосы). Агрегаты гидро- и пневмосистем, автоматики и др. после демонтажа направляют на специализированные участки или рабочие места для определения их технического состояния и при необходимости ремонта. При разборке и последующей дефектации деталей не следует разукомплектовывать сопряженные пары, которые при изготовлении обрабатывают или балансируют в сборе, а также приработанные пары деталей, пригодные для дальнейшей эксплуатации без ремонта. Для разборки прессовых соединений следует использовать стенды, съемники, приспособления, универсальные и специальные инструменты, которые позволяют исключить перекос снимаемой детали за счет равномерного распределения действующей на нее нагрузки. При выпрессовке подшипников, сальников, втулок из ступицы или стакана усилие прикладывают к наружному кольцу, а при снятии с вала — к внутреннему. При снятии деталей без применения указанных средств запрещается наносить удары непосредственно по демонтируемой детали, а следует использовать оправки и выколотки с мягкими наконечниками (медными, из сплавов алюминия). При разборке соединений деталей из хрупких материалов (чугуна, алюминиевых сплавов) во избежание появления в них трещин рекомендуется сначала по определенной схеме ослабить все болты или гайки и только затем разобрать резьбовые соединения полностью. Крепежные детали (гайки, болты, шпильки) при разборке машины складывают в сетчатую тару для более эффективной очистки в моечных установках или возвращают на прежние места. Детали с резьбой повышенной точности запрещается разукомплектовывать. Во избежание попадания посторонних веществ и предметов открытые полости и отверстия для масла в гидроагрегатах после снятия с машины закрывают крышками и пробками. Если метки перед разборкой плохо заметны, необходимо их восстановить. Для подъема и транспортирования деталей и агрегатов массой более 20 кг применяют подъемно-транспортные средства и надежные захватные приспособления. Порядок выполнения разборочных операций и переходов устанавливается в соответствии с требованиями технологической документации. На основании государственных стандартов на предприятии оформляют соответственно маршрутные и операционные карты. Последовательность разборки машины и агрегатов устанавливается картами технологического процесса, которые содержат также рекомендации по использованию универсальных и специальных стендов и оснастки. Последовательность выполнения разборочных операций определяется технологической необходимостью очередности снятия тех агрегатов и сборочных единиц, без демонтажа которых затруднена или невозможна последующая разборка, с обязательным соблюдением условий безопасности труда на рабочем месте. Для повышения производительности труда и обеспечения требований техники безопасности при выполнении разборочных работ рекомендуется применять механизированные устройства. В процессе подготовки машины к ремонту необходимо разбирать подвижные и неподвижные соединения, которые бывают разъемными и неразъемными. Неподвижные разъемные соединения осуществляются при помощи резьбы, шпонок, клиньев, штифтов, шлицев и посадок (с зазором, переходные и с натягом), а неподвижные неразъемные соединения фиксируются с помощью заклепок, сварки, пайки, клеевых композиций, развальцовки и посадок (горячих, прессовых). Для обеспечения сохранности посадочных поверхностей деталей при разборке соединений с натягом (втулок, подшипников качения, шестерен и т.п.) применяют различные съемники (винтовые, гидравлические) и прессы, а также вспомогательные приспособления — оправки, разъемные кольца и др. Не рекомендуется разбирать сопряжения, в которых зазоры, натяги не имеют отклонений от допускаемых значений. Для предупреждения появления возможных повреждений (вмятин, царапин, сколов и т.п.) детали после разборки запрещается укладывать в тару навалом. Также следует соблюдать требования к транспортированию деталей при их перемещении от одного рабочего места до другого.
Дата добавления: 2021-02-10; просмотров: 210; Мы поможем в написании вашей работы! |
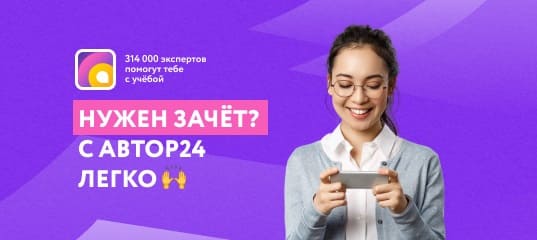
Мы поможем в написании ваших работ!