Литье по выплавляемым моделям
Тема: Способы обработки материалов
Тема урока: «Виды и способы обработки материалов»
Задание
1. Ознакомиться с материалом.
Выписать виды обработки
Составьте краткий конспект.
Теоретический материал
Литье является наиболее распространенным методом формообразования.
Литье в песчано-глинистые формы (литье в землю) – технология получения отливок литьем в «отпечатки», оставленные моделями в формовочной смеси. Способ используют для изготовления изделий, к которым не предъявляются высокие требования по точности размеров и качеству поверхности.
Среди преимуществ методики можно отметить следующие:
· низкая себестоимость продукции;
· практически неограниченные габариты изготовляемых отливок;
· широчайший ассортимент литья, включая изделия сложной формы.
Технология литья в песчано-глинистые формы (рис. 1):
1. Производство изделий литьем в землю включает несколько этапов. Вкратце схема выглядит следующим образом.
2. Изготовление модельного комплекта из дерева, стали и т.д., в зависимости от серийности отливки.
3. Изготовление сухой формовочной смеси из песка (преимущественно кварцевого) и связующего (глины).
4. Изготовление стержней, литниковой системы.
Рис. 1 – Литьё в песчано-глинистые формы
5. Размещение модельного полукомплекта на подмодельных плитах в опоках, засыпка формовочной смеси.
6. Увлажнение смеси в полуформе, уплотнение ручным или механическим способом.
|
|
7. Проставка стержней, установка второй опоки, установка второго полумодельного комплекта, литниковой системы.
8. Засыпка и уплотнение формовочной смеси.
9. Удаление модельного комплекта, сушка и сборка готовых полуформ.
Далее через литник заливают расплавленный металл. После кристаллизации расплава и охлаждения отливки ее освобождают из формы, очищают от нагара и подвергают необходимой механической, термической, химико-термической обработке.
Особенности литья в песчано-глинистую форму:
1. В качестве материала отливок используется серый чугун, обладающий хорошей жидкотекучестью и малой усадкой (1%), малоуглеродистая сталь (< 0,35%С). Редко производятся таким способом отливки из медных и алюминиевых сплавов.
2. Качество отливки по объему весьма низкое, что связано с возможностью попадания в металл разноразмерных неметаллических включений. Из за бурного газообразования при заливки металла во влажную форму в теле изделия образуются газовые пузырки, которые отрицательно сказываются на прочности изделия.
3. Форма отливок может быть весьма сложной, но все же ограничена необходимостью извлечения моделииз формы.
4. Размеры отливки теоретически неограничены. Таким способом получают самые крупные отливки (до сотни тонн). Это станины станков, корпуса турбин и т. д.
|
|
5. Из-за состава формы из отдельных песчинок, качество и точность поверхности низкое – шереховатость 14 квалитета, в связи с чем обработку поверхности изделия проходится производить в несколько этапов. Шероховатость поверхности отливок превышает 0,3мм, на поверхности часто наличествуют раковины и неметаллические включения. Поэтому сопрягаемые поверхности деталей, заготовки которых получают таким методом, всегда обрабатывают резанием.
Литейные сплавы:
1. Чугун является наиболее распространенным материалом для получения фасонных отливок. Чугунные отливки составляют около 80 % всех отливок.
Широкое распространение чугун получил благодаря хорошим технологическим свойствам и относительной дешевизне. Из серого чугуна получают самые дешевые отливки (в 1,5 раза дешевле, чем стальные, в несколько раз – чем из цветных металлов). Область применения чугунов расширяется вследствие непрерывного повышения его прочностных и технологических характеристик. Используют серые, высокопрочные, ковкие и легированные чугуны.
2. Сталь как литейный материал применяют для получения отливок деталей, которые наряду с высокой прочностью должны обладать хорошими пластическими свойствами. Чем ответственнее машина, тем более значительна доля стальных отливок, идущих на ее изготовление. Стальное литье составляет: в тепловозах – 40…50 % от массы машины; в энергетическом и тяжелом машиностроении (колеса гидравлических турбин с массой 85 тонн, иногда несколько сотен тонн) – до 60 %.
|
|
Стальные отливки после соответствующей термической обработки не уступают по механическим свойствам поковкам.
3. Медные сплавы – бронзы и латуни.
Латуни – наиболее распространенные медные сплавы. Для изготовления различной аппаратуры для морских судостроения, работающей при температуре 300 ?С, втулок и сепараторов подшипников, нажимных винтов и гаек прокатных станов, червячных винтов применяют сложнолегированные латуни. Обладают хорошей износостойкостью, антифрикционными свойствами, коррозионной стойкостью.
Из оловянных бронз (БрО3Ц7С5Н1) изготавливают арматуру, шестерни, подшипники, втулки.
Безоловянные бронзы по некоторым свойствам превосходят оловянные. Они обладают более высокими механическими свойствами, антифрикционными свойствами, коррозионной стойкостью. Однако литейные свойства их хуже. Применяют для изготовления гребных винтов крупных судов, тяжело нагруженных шестерен и зубчатых колес, корпусов насосов, деталей химической и пищевой промышленности.
|
|
4. Алюминиевые сплавы.
Отливки из алюминиевых сплавов составляют около 70 % цветного литья. Они обладают высокой удельной прочностью, высокими литейными свойствами, коррозионной стойкостью в атмосферных условиях.
Наиболее высокими литейными свойствами обладают сплавы системы алюминий – кремний (Al-Si) – силумины АЛ2, АЛ9. Они широко применяются в машиностроении, автомобильной и авиационной промышленности, электротехнической промышленности.
Также используются сплавы систем: алюминий – медь, алюминий – медь – кремний, алюминий – магний.
5. Магниевые сплавы обладают высокими механическими свойствами, но их литейный свойства невысоки. Сплавы системы магний – алюминий – цинк – марганец применяют в приборостроении, в авиационной промышленности, в текстильном машиностроении.
2. Литейная технологическая оснастка (формовочные, стержневые и специальные смеси).
Литейную форму (рис. 2) заливают расплавленным металлом через литниковую систему.
Литниковая система – совокупность каналов и резервуаров, по которым расплав поступает из разливочного ковша в полость формы.
Основными элементами являются: литниковая чаша 5, которая служит для приема расплавленного металла и подачи его в форму; стояк 6 – вертикальный или наклонный канал для подачи металла из литниковой чаши в рабочую полость или к другим элементам; шлакоуловитель 12, с помощью которого удерживается шлак и другие неметаллические примеси; питатель 13 – один или несколько, через которые расплавленный металл подводится в полость литейной формы.
Для вывода газов, контроля заполнения формы расплавленным металлом и питания отливки при ее затвердевании служат прибыли или выпор 4. Для вывода газов предназначены и вентиляционные каналы 9.
Рис. 2 - Литейная форма
Разновидности литниковых систем представлены на рис. 3.
Рис. 3 - Разновидности литниковых систем: а – боковая; б – нижняя; в - верхняя
Боковая литниковая система (рис. 3, позиция а). Подвод металла осуществляется в среднюю часть отливки (по разъему формы). Такую систему применяют при получении отливок из различных сплавов, малых и средних по массе деталей, плоскость симметрии которых совпадает с плоскостью разъема формы. Является промежуточной между верхней и нижней, и следовательно сочетает в себе некоторые их достоинства и недостатки.
Нижняя литниковая система (рис 3, позиция б) – широко используется для литья сплавов, легко окисляющихся и насыщающихся газами (алюминий), обеспечивает спокойный подвод расплава к рабочей полости формы и постепенное заполнение ее поступающим снизу, без открытой струи металлом. При этом усложняется конструкция литниковой системы, увеличивается расход металла на нее, создается неблагоприятное распределение температур в залитой форме ввиду сильного разогрева ее нижней части. При такой системе ограничена возможность получения высоких тонкостенных отливок.
Нижний подвод через большое количество питателей часто используется при изготовлении сложных по форме, крупных отливок из чугуна.
Верхняя литниковая система (рис. 3, позиция в). Достоинствами системы являются: малый расход металла; конструкция проста и легко выполнима при изготовлении форм; подача расплава сверху обеспечивает благоприятное распределение температуры в залитой форме (температура увеличивается от нижней части к верхней), а следовательно, и благоприятные условия для направленной кристаллизации и питании отливки. Недостатки: падающая сверху струя может размыть песчаную форму, вызывая засоры; при разбрызгивании расплава возникает опасность его окисления и замешивания воздуха в поток с образованием оксидных включений; затрудняется улавливание шлака.
Верхнюю литниковую систему применяют для невысоких (в положении заливки) отливок, небольшой массы и несложной формы, изготовленных из сплавов не склонных к сильному окислению в расплавленном состоянии (чугуны, углеродистые конструкционные стали, латуни).
В соответствии с условиями технологии литейного процесса, для изготовления таких литейных форм используются специальные смеси для литья, представляющие собой сочетание высокоогнеупорных веществ (асбест, шамот) с песчано-глинистыми составляющими.
Формовочные смеси подразделяют по роду заливаемого металла — на смеси для получения отливок из сталей, чугуна и цветных сплавов; по характеру использования — на единые, облицовочные и наполнительные; по состоянию формы перед заливкой— на смеси для форм, заливаемых во влажном и в сухом состояниях.
Облицовочную смесь, оформляющую рабочую поверхность формы и непосредственно контактирующую с расплавом, тщательно готовят из наиболее доброкачественных исходных формовочных материалов, образуя из нее облицовочный слой толщиной 15—30 мм. Остальной объем опоки заполняют наполнительной смесью, состоящей в основном из оборотной смеси с небольшими добавками свежих исходных материалов.
Наполнительная смесь значительно дешевле и проще в приготовлении, чем облицовочная. К ней предъявляются требования только по газопроницаемости и прочности, которые должны быть не ниже, чем у облицовочной смеси. Использование облицовочных и наполнительных смесей рационально в условиях мелкосерийного и единичного производства, особенно при изготовлении средних и крупных отливок.
Стержни, выполняющие различные полости в отливках, во время заливки расплава и формирования отливки находятся в более тяжелых условиях, чем форма, так как со всех сторон, кроме знаков, они окружены металлом, испытывая его тепловое и силовое воздействие. Кроме того, затруднен отвод из стержней газов, образующихся при выгорании связующих. По этим причинам к стержневым смесям предъявляются более высокие требования по прочности, податливости, газопроницаемости, огнеупорности, выбиваемости.
Стержневые смеси подразделяют на предназначенные для изготовления стержней, упрочняемых нагревом (смеси горячего отверждения), и не требующих тепловой обработки (холоднотвердеющие смеси).
3. Специальные виды литья: по выплавляемым моделям, в оболочковые и металлические формы; литьё под давлением и центробежное.
В современном литейном производстве все более широкое применение получают специальные способы литья: в оболочковые формы, по выплавляемым моделям, кокильное, под давлением, центробежное и другие.
Эти способы позволяют получать отливки повышенной точности, с малой шероховатостью поверхности, минимальными припусками на механическую обработку, а иногда полностью исключают ее, что обеспечивает высокую производительность труда. Каждый специальный способ литья имеет свои особенности, определяющие области применения.
Литье по выплавляемым моделям
Методом литья по выплавляемым моделям изготовляют отливки массой от нескольких граммов до нескольких десятков килограммов (корпуса и детали приборов, лопатки газовых турбин, арматуру, режущий и хирургический инструмент, мелкие автодетали, детали фотоаппаратов, киноаппаратов, швейных и текстильных машин, а также художественное литье). Отливки, полученные этим способом, имеют высокую точность и хорошую чистоту поверхности, позволяющие использовать их без механической обработки.
Дата добавления: 2021-02-10; просмотров: 44; Мы поможем в написании вашей работы! |
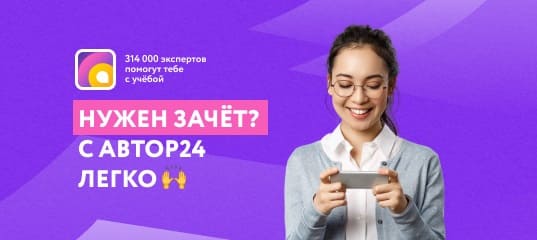
Мы поможем в написании ваших работ!