МЕТАЛЛОКЕРАМИЧЕСКИЕ ТВЁРДЫЕ СПЛАВЫ
Получаемые сплавы при помощи прессования и спекания при температуре 1500°С-2000°С порошка различных тугоплавких карбидов (тантала, титана, вольфрама) и свободного тугоплавкого кобальта имеют название - металлокерамические твёрдые сплавы, в которой в качестве связующего вещества выступает кобальт, а режущая часть - карбиды и их смеси.
Существуют три группы металлокерамических твёрдых сплавов для режущего инструмента на основе карбидов и кобальта:
· Однокарбидные (Вольфрамокобальтовые), которые обозначаются первой буквой основных рабочих компонентов и процентным коэффициентом содержания кобальта: ВК25, ВК20, ВК15, ВК10 (Победит), ВК8, ВК6, ВК4, ВК3, ВК2 - эти сплавы имеют средний показатель теплостойкости из этой группы, которая составляет 800°С - 850°С.
· Двухкарбидные, состоящие из карбида титана и карбида вольфрама в кобальтовой связке, иначе называемые Титановольфрамокобальтовые твёрдые сплавы, обозначаются двумя буквами Т и К, а также цифрами, указывающими на процентное содержание карбида титана и кобальта: Т60К6, Т30К4, Т15К6, Т15К10, Т14К8, Т5К10, Т5К12. Эти сплавы являются самыми термостойкими из этой группы твёрдых сплавов, предназначенных для режущего инструмента - 850°С - 900°С.
· Трёхкарбидные (Танталотитановольфрамокобальтовые) твёрдые сплавы, состоящие из кобальтовой связки трёх карбидов: тантала, титана, вольфрама. Обозначаются как ТТК (не третье транспортное кольцо в Москве), с указанием процентного содержания основных компонентов: ТТ21К9, ТТ20К9, ТТ10К8, ТТ7К15, ТТ8К7, ТТ7К12. Группа этих сплавов имеет наиболее низкую теплостойкость в ≈750°С.
|
|
Эти сплавы могут иметь различную зернистость карбидов и соответствующую маркировку: ОМ - особомелкозернистые (ВК10ОМ), М - мелкозернистые (ВК6М), нормальные - без дополнительного обозначения (ВК8), В, К, КС - крупнозернистые (ВК8В, Т5К10В, ВК15К, ВК20КС).
Твердые сплавы, в отличие от быстрорежущей стали, дороже в несколько раз и изготавливаются в форме пластинок, которыми оснащают составные и сборные инструменты. Инструменты малого размера разрешается выпускать полностью из твердого сплава. Применение твердого сплава в оснастке режущих инструментов позволяет увеличить, в отличие от быстрорежущей стали, скорость рабочей подачи в несколько раз - экономически выгодно только тогда, когда скорость резания может быть увеличена не менее чем в 1,5 раза.
Высокую твердость (до 92 HRA), теплостойкость и износостойкость сплавам обеспечивают карбиды. Чем больше карбидов содержится в сплаве, тем выше ранее рассмотренные показатели, но их прочность ниже. При этом сплавы с карбидами тантала обладают наиболее высокой прочностью, и только затем следуют сплавы на основе карбидов вольфрама. Наименьшую прочность имеют сплавы с содержанием карбида титана. Твердость, теплостойкость, износостойкость изменяют свои показатели обратно пропорционально показателю прочности. Кроме того, чем выше содержание кобальта в сплаве и больше толщина его оболочки (обволакивающие зерна карбидов), тем выше прочность сплава. Именно поэтому крупнозернистые сплавы обладают более высокой и низкой, в случае с мелкозернистыми сплавами, прочностями, чем обыкновенные сплавы фракционного состава, однако, износостойкость крупнозернистых сплавов ниже, а мелкозернистых выше износостойкости подобных аналогов.
|
|
Фракционный состав сплава определяется цифрами в марке после знака химического элемента, например: сплав ВК6 содержит 6% кобальта, остальное – карбиды вольфрама; сплав Т15К6 содержит 6% кобальта, 15% карбидов титана, остальное – карбиды вольфрама и т.п. Вместе с изменениями размера зерен карбида, повышение технико-физических свойств, твердых сплавов, реализуется с помощью покрытия пластинок сплавов ВК тонким слоем (до 6 мкм) карбидов или нитридов титана, которое обеспечивает значительное (в 3-5 раз) увеличение стойкости, при сохранении высокой прочности. Ещё большего значения стойкости можно достигнуть при двухслойном покрытии пластин – 6 мкм карбидов титана и 1 мкм окиси алюминия.
|
|
Более высокими режущими свойствами, в сравнение с традиционными, обладают сплавы группы МС: МС101, МС121, МС146 и т.д.
Твердые сплавы без вольфрама ТМ-1, МНТ-2, МНТА – 2, КТН-16 изготовлены на основе карбидов и карбонитридов титана, тантала, ниобия, и на связки никелевомолибдена. Отсутствие вольфрама, с целью экономии, обеспечивает сплавам в 1,5- 3 раза повышение стойкости, в сравнении со сплавами Т30К4 и Т15К6, при их тонком и чистовом точении.
Подавляющее большинство инструментов оснащают твердыми сплавами, но если брать от общего объема производства металлорежущего инструмента, то их доля не будет превышать 30%. Узконаправленное применение твердых сплавов связано: с их повышенной хрупкостью; предел прочности на изгиб ниже, чем у стали Р18 в 2,5 раза, а ударная вязкость в 1,5-3 раза. Поэтому инструменты из твердых сплавов имеют невысокие технико-физические свойства. Нередко бывают случаи поломок и крошение пластин, когда условия работы обусловлены высокими ударными нагрузками, а так же малой жесткости технологической системы. Учитывая, высокую твердость и малую теплопроводность твердых сплавов, которые затрудняют шлифование и заточку, из-за высоких трудозатрат и возможности образования трещин, можно сделать вывод: твердые сплавы недостаточно пригодны для изготовления мелкоразмерного или мелко профильного инструмента. Для расширения номенклатуры твердосплавных инструментов, их возможности в применении, т.е. достичь реализацию такового же объема как у резцов и фрез, которые состоят из твердых сплавов на 75% и 45% соответственно, необходимо: совершенствование твердых сплавов; применение современных методов изготовления инструментов; широкое применение алмазных кругов для шлифования и заточки.
|
|
МИНЕРАЛОКЕРАМИКА
Изготавливается минералокерамика методом прессования и спекания, в температурном режиме 1720-1760 градусов Цельсия, микроизмельченного порошка корунда, или искусственной окиси алюминия (AL2O3) с окисью магния (MgO) около 1%. Окись магния является связующим компонентом, а покрытие зернами корунда – режущим.
Преимуществом, при выборе материала из минералокерамики является: отсутствие дефицитных компонентов; низкая себестоимость – цена порошка электрокорунда в 125 раз ниже порошка карбида вольфрама; высокая твердость - 93 HRA; высокая теплостойкость – 2000 градусов Цельсия. При этом нужно учитывать: низкую прочность на изгиб – ниже в 3-4 раза относительно твердых сплавов; сниженная ударная вязкость – ниже в 7-10 раз, чем твердых сплавов; особо низкая сопротивляемость периодичному изменению тепловой нагрузки. Поэтому область применения ограничена получистовым точением цветных и черных металлов с высокими скоростями резания в жестких условиях.
Стремление повысить прочность оксидной минеральной керамики привело к образованию керметов, содержащих добавки молибдена, вольфрама титана или сложных карбидов, боридов или силицидов этих элементов, а также окиси алюминия. Такие добавки металлов увеличивают прочность минералокерамики в 1,5 раза, однако стойкость уменьшается в 4-5 раз, а теплостойкость снижают до 1400 градусов Цельсия. Исключение – новые марки В3, ВОК-60, ВОК-63 карбидно-оксидной керамики, но стоимость их в два выше, чем твердого сплава. Например ВРК-20, относительно новая марка нитридной керамики, обладает стойкостью в два раза выше, чем карбидная ВОК-60.
Для увеличения вязкости, керамику легируют ZrO2, а для повышение прочности армируют монокристалами, в виде волокон SiC. Главным промышленным представителем минеральной керамики является микролит ЦМ-332, изготавливаемый в виде пластинок, таких же форм и размеров, что и твердые сплавы.
Дата добавления: 2021-01-20; просмотров: 131; Мы поможем в написании вашей работы! |
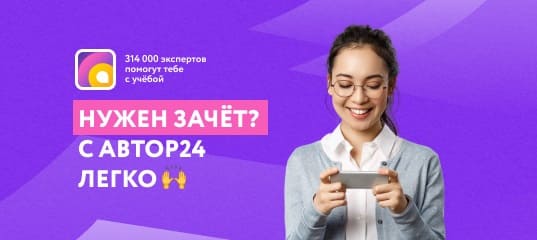
Мы поможем в написании ваших работ!