Обоснование оптимальной геометрии
Геометрические параметры резца влияют на силу резания, износ режущих кромок лезвия и качество обрабатываемой поверхности.
Передний угол – угол в секущей плоскости между передней поверхностью лезвия
и основной плоскостью. Он определяет положение передней поверхности лезвия и влияет на условия образования стружки, силу резания и на прочность лезвия. Угол
назначают в зависимости от физико-механических свойств обрабатываемого материала и конструкции инструмента. По рекомендациям [1, с.6, таблица 1]
Принимаем
.
Главный задний угол – измеряется в главной секущей плоскости между линиями пересечения её с главной задней поверхностью
с плоскостью резания. Задний угол
необходим для возможности перемещения по образованной им поверхности заготовки, для уменьшения контакта задней поверхности лезвия и образованной поверхности заготовки и возникающих между ними сил трения. С увеличением
интенсивность изнашивания лезвия по задней поверхности уменьшается и увеличивается стойкость инструмента. Главный задний угол
выбираем в зависимости от обрабатываемого материала. По рекомендациям [1, с.6, таблица 1]
Принимаем
. Точно так же как и
принимаем
.
Главный угол в плане
– угол, измеряемый в горизонтальной координатной плоскости между проекцией на него вектора скорости подачи и проекцией главной режущей кромки. Он влияет на соотношение составляющих силы резания и на силу, оказывающую воздействие на возможное деформирование заготовки. Главный угол в плане выбирается, в основном, в зависимости от жесткости системы станок – приспособление – инструмент – деталь. Для достаточно жесткой системы СПИД
выбирают в пределах от 45° до 30°, что способствует повышению стойкости резца и увеличению допускаемой скорости резания. По рекомендациям [2, с.304, таблица 8.13] и [2, с.266] выбираем
. Вспомогательный угол в плане
– угол, измеряемый в горизонтальной координатной плоскости между проекцией на неё вспомогательной режущей кромки и линией, на которой лежит вектор скорости подачи. При выборе углов φ и φ1 учитываем, помимо указанных выше факторов, также и конфигурацию обрабатываемой детали, поэтому
|
|
Вспомогательную режущую кромку рекомендуется выполнять под углом , выбираем
, для того, чтобы в дальнейшем выбрать стандартную пластину и избежать дополнительных затрат на переточки.
Угол наклона режущей кромки – угол в плоскости резания между режущей кромкой и основной плоскостью. Он влияет на направление схода стружки и упрочнение лезвия инструмента. Угол
выбирают, в основном, в пределах от 0° до 6°. Так как при увеличении угла
от 0˚ до 6˚ стойкость резца возрастает незначительно, то часто по технологическим соображениям этот угол у составных резцов принимают равным 0˚. Этим достигается снижение трудоемкости изготовления резцов и упрощение настройки заточного станка при заточке резцов.
|
|
Проектирование поверхностей
При проектировании резцов геометрия их рабочей поверхности выбирается, как правило, из условия обеспечения наибольшей стойкости резца, или достижения заданной шероховатости обработанной поверхности, или минимальных сил резания. При этом необходимо также учитывать тип образующейся стружки, вид заготовки и характер припуска. Указанные факторы весьма сильно влияют на надежность выполнения технологической операции. В связи с этим во многих случаях возникает необходимость создания стружколомающих элементов на передней поверхности и упрочнения режущей кромки.
В данном случае нужна криволинейная передняя поверхность с отрицательной фаской для обработки с
МПа. Фаска, как упрочняющий элемент, способствующий повышению надежности работы резца. При чистовом точении сталей и сплавов ширина фаски
выбирается меньше, чем при черновой и получистовой обработке. Наиболее часто
, где а – толщина среза, мм, то Передний угол на фаске
. Принимаем
. На рисунке 1.5 показана режущая часть резца.
|
|
Рисунок 5 – Режущая часть резца.
С увеличением радиуса переходной режущей кромки r повышается прочность вершины резца и его стойкость, а также уменьшается шероховатость обработанной поверхности. Однако, увеличение r вызывает уменьшение фактического угла в плане резца (особенно при малых глубинах резания) и значительный рост силы что может приводить к снижению точности обработки и появлению вибраций в системы станок – приспособление – инструмент – деталь.
При чистовой обработке r выбирают наиболее часто в зависимости от требуемой шероховатости обработанной поверхности и режима резания. По таблицы [1, с.8] принимаем наибольшую подачу при
мм, сталь углеродистая,
мкм. Так как
МПа, то
, Принимаем
Определение толщины среза , мм:
Определение величины фаски , мм:
, принимаем
Фаска по задней поверхности мм
Радиус округления режущей кромки rп выбирают в зависимости от назначения резца: для чистового и получистового точения величину rп обычно выбирают в пределах от 0,01 мм до 0,04 мм, принимаем 0,02= rп
Передний угол на фаске
.
|
|
Задний угол на фаске .
Задний угол на корпусе .
Точно так же как и принимается равной
, так же делают вспомогательную поверхность
, равной
.
Так как принимается равной
, так же делают вспомогательную поверхность
, равной
. Принимаем соответственно:
Вспомогательный задний угол .
Вспомогательный задний угол на фаске .
Вспомогательный задний угол на корпусе .
Компоновка режущей части
Длину режущих кромок определяем графическим методом, для этого изображаем заготовку и резец в четырех положениях.(Рисуно 1.6) Величину режущих кромок определяем в зависимости от максимальной ширины срезаемого слоя. Из построения получаем получаем, что для К максимальное значение- 1.31, поэтому длины режущих кромок будут соответственно К=1,31+5=6,31(6), К>6,31
Рисунок 6- Определение режущей части
8 Выбор напайной твердосплавной пластины
Режущие кромки и примыкающие к ним контактные поверхности на передней и задней поверхностях в совокупности образуют лезвия, соответственно режущим кромкам, называемые главным и вспомогательным. Преодолевая сопротивление, лезвия врезаются в металл заготовки и на всем пути относительно рабочего движения срезают с неё впереди лежащий слой металла, превращая его в стружку. На всех инструментах лезвия в поперечном сечении имеют форму клина, с одной стороны ограниченного передней, а с другой – задней поверхностью. По длине главное лезвие больше вспомогательных.
Положение передней поверхности относительно главной задней поверхности определяет форму клина режущей части и может быть охарактеризовано углом заострения, который измеряется в главной секущей плоскости между линиями пересечения её с передней и главной задней поверхностями. Таким образом, согласно данным выше определениям, , а при заданных
и
угол заострения
:
.
Угол вершины пластины:
Пластина выбирается в зависимости от типа и назначения резца.
В соответствии с рассчитанными параметрами резца выбираем пластину, напаиваемую 07050 ГОСТ 25395-82 из сплава типа Т30К4 ГОСТ 3882-74. Обозначение пластины 61351, с размерами приведенными на рисунке.
На рисунке 1.7 показан вид твердосплавной пластины с размерами.
Рисунок 7 – Пластина твердосплавная
Необходимо уменьшить пластину по длине с 10мм до 8 мм, в целях экономии твердого сплава.
Дата добавления: 2021-01-20; просмотров: 141; Мы поможем в написании вашей работы! |
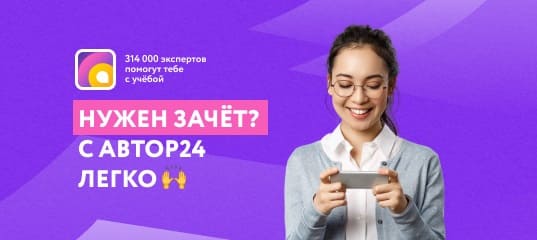
Мы поможем в написании ваших работ!