Оформление лабораторной работы
ИССЛЕДОВАНИЕ ОСНОВНЫХ ПАРАМЕТРОВ
ВАГОННЫХ ДЕТАЛЕЙ И УЗЛОВ
Методические указания к учебно-исследовательским лабораторным работам по курсу дисциплины «Вагоны. Общий курс»
Часть I
САНКТ-ПЕТЕРБУРГ
2012
Указания посвящены лабораторным работам, способствующим более глубокому изучению материала по первой части дисциплины «Вагоны. Общий курс». К каждой работе даются теоретические сведения и исходные данные.
Лабораторные работы выполняются в учебном классе кафедры «Вагоны и вагонное хозяйство» и стендовой аудитории на натурных образцах вагонных деталей и узлов, а также макетов вагонов и необходимым оборудованием, измерительным инструментом и оснасткой. Лабораторные работы проводятся после тематических лекций и контрольных занятий, что дает возможность каждому студенту помимо закрепления теоретического материала получить практические навыки использования лабораторного оборудования, а также познакомиться с элементами исследовательской работы.
Тематика учебно-исследовательских лабораторных работ соответствует учебной программе к вытекает из содержания наиболее важных разделов курса.
Практикум по лабораторным работам построен по следующей схеме: краткие теоретические сведения и исходные данные; цель работы; объекты исследования; стенды и установки, используемые для проведения работы; порядок выполнения работы; требования к оформлению работы.
|
|
Лабораторная работа № 1
ОПРЕДЕЛЕНИЕ ТЕХНИКО-ЭКОНОМИЧЕСКИХ ПАРАМЕТРОВ И ЛИНЕЙНЫХ РАЗМЕРОВ ГРУЗОВЫХ ВАГОНОВ
Технико-экономические параметры являются основной характеристикой эксплуатации грузовых вагонов, определяют эффективность их использования. Основными требованиями, предъявляемыми к грузовым вагонам, являются сохранность грузов и себестоимость перевозок.
Основными параметрами грузового вагона, характеризующими его эффективность, являются: грузоподъемность, тара, количество колесных пар (осность), объем кузова, площадь пола, длина и другие линейные размеры вагона. Для сравнения вагонов между собой пользуются параметрами, представляющими отношения этих величин: удельным объемом кузова, удельной площадью пола, коэффициентами тары, нагрузкой от колесной пары на рельсы, нагрузкой на метр пути. Важными показателями являются средняя статическая и средняя динамическая нагрузки вагона.
Основные условия, которым должны соответствовать вагоны нового поколения, заключаются в максимальном использовании грузоподъемности и вместимости, снижении эксплуатационных расходов на их содержание и ремонт, повышении прочности и долговечности, уменьшении коэффициента тары и обеспечении безопасности движения.
|
|
Исходными данными для проектирования грузовых вагонов являются: габарит, в который должен вписываться вагон, максимальная скорость, грузоподъемность, коэффициент тары, удельный объем кузова, нагрузка от колесной пары нарельсы и нагрузка на погонный метр пути.
В настоящее время, не смотря на то, что подавляющая часть вагонов имеет максимальную осевую нагрузку 23,5 тс/ост, проектируются вагоны с осевой нагрузкой 25, 27 и даже 30 тс/ось, вагоны с осевой нагрузкой 25 тс/ось эксплуатируются на ограниченных полигонах обращения.
Цель работы
Определить основные технико-экономические параметры и линейные размеры грузового вагона, используя его уменьшенный макет, сравнить эти параметры с оптимальными, определить назначение вагона.
Порядок выполнения работы
По заданию преподаватели каждый студент (или подгруппа в количестве 3—4 чел.) определяет основные технико-экономические параметры одного из имеющихся макетов грузового вагона, пользуясь надписями, насенными на кузов и раму вагона, а также комплектом для визуально-измерительного контроля.
|
|
Общий вид макета приведен на рисунке 1.
Рисунок 1. Образец макета вагона-цистерны
Определяются следующие основные размеры модели вагона:
· длина рамы (кузова);
· длина вагона по осям сцепления автосцепок;
· база вагона (расстояние между шкворневыми балками рамы);
· ширина кузова снаружи;
· длина, ширина и высота кузова внутри (для цистерн диаметр и длина котла).
Учитывая масштаб модели (который студентам также предлагается определить ), определяют соответствующие размеры действительного вагона.
Используя формулы, вычисляют основные технико-экономические параметры вагона:
— коэффициент тары (технический) :
(1),
где T— тара вагона, т;
Р — грузоподъемность, т;
— нагрузка от колесной пары на рельсы:
(2),
где n0- количество осей вагона;
— погонная нагрузка, приходящаяся на метр пути:
(3),
где Lавт - длина вагона по осям сцепления автосцепок;
— удельный объем кузова:
(4),
где V- объем кузова внутри;
L,В,Н длина, ширина и высота внутри кузова;
для цистерн (5)
где D - диаметр котла;
для упрощения расчетов 2Vднища не учитываем.
Все исходные величины и вычисленные технико-экономические параметры заносятся и таблицу, после чего сравниваются с допускаемыми и рекомендуемыми величинами для данного типа вагона [1].
|
|
Оформление лабораторной работы
Результаты лабораторной работы оформляются протоколом (отчетом).
Содержание отчета:
Тема лабораторной работы, дата проведения, цель работы, эскиз вагона с указанием всех размеров, масштаб модели вагона.
Таблица размеров, технико-экономических параметров вагона, их допускаемые и рекомендуемые значения.
На основании рассмотренного студент должен привести полную классификационную характеристику вагона, а также указать его узлы, унифицированные с другими типами вагонов. Необходимо установить перечень перевозимых грузов.
Выводы о соответствии технико-экономических параметров модели нагона нормируемым значениям, на основе собственного опыта необходимо отметить основные узлы, требующие модернизации для повышения безопасности движения, а также целесообразности использования вагона.
Лабораторная работа № 2
ОПРЕДЕЛЕНИЕ ОСНОВНЫХ ПАРАМЕТРОВ
КОЛЕСНОЙ ПАРЫ
Колесной парой называется сборочная единица ходовых частей (тележек), состоящая из оси с напрессованными колесами на ее подступичные части. Колесная пара является одной из основных частей, определяющих безопасность движения вагона и его техническую пригодность к выполнению перевозочного процесса [1; 3]. Она направляет движение вагона по рельсовой колее и воспринимает все нагрузки, передающиеся от вагона на рельсы и обратно. Поэтому колесную пару можно рассматривать и как наиболее ответственный узел вагона, составляющие элементы которого — ось и колеса, нагружены наиболее интенсивно, а ось колесной пары, как основной ее элемент, к тому же в эксплуатации испытывает сложный вид нагружения — изгиб с вращением, что дополнительно снижает срок службы осей. Поэтому в соответствии с эпюрой изгибающих моментов наименьший диаметр имеют шейки, а наибольший — подступичные части.
Рисунок 2 - Схема колесной пары:
1 — расстояние между внутренними гранями колес; 2 — диаметр колеса по кругу катания; 3 — диаметр шейки оси; 4— диаметр предподступичной части оси; 5 — диаметр средней части оси; 6 — размеры элементов
Рисунок 3- Элементы колесной пары
На оси выделяются следующие части: шейки, предподступичные части, подступичные части и средняя часть оси. Шейки служат для размещения и закрепления на них буксовых узлов. Для этого на торцах шеек предусматривается резьба или отверстия для болтов. На подступичные части оси под большим давлением напрессовываются колеса. Эти части являются наиболее утолщенными по всей оси. Для смягчения перехода от подступичных частей к шейкам служат предподступичные части. Кроме того, на предподступичной части размещается задний затвор буксы. Переходы от одной части оси к другой выполняются в виде галтелей (плавных переходов) соответствующего радиуса, за исключением перехода к средней части оси. Галтели резко снижают концентрацию напряжений при переходе от одного диаметра оси к другому и тем самым повышают надежность работы оси. Колесо (рисунок 3) имеет обод, диск и ступицу. Ширина обода — 130 мм. Переход от ступицы к ободу выполнен в форме диска, расположенного под некоторым углом к этим частям, что придает колесу упругость и снижает воздействия динамических сил. Диск слегка конусный: у ступицы его толщина больше, чем у обода. Такая форма распределения металла наиболее рациональна, так как обеспечивает равнопрочность колеса относительно поперечных толчков.
У одного края обода колеса, обращенного внутрь колесной пары, имеется гребень, предохраняющий колесную пару от схода с рельсов. Поверхности катания колеса придается коничность для выравнивания неравномерного проката по ширине поверхности катания, а также для облегчения прохождения кривых участков пути (рисунок 4).
Рисунок 4- Профиль поверхности катания колеса
Цель работы
Ознакомление с технологией измерения колесной пары, приобретение навыков самостоятельного пользования измерительным инструментом, определение типа колесной пары.
Объект исследования — лабораторная колесная пара: с одной стороны РУ1, и другой — РУ1Ш.
Инструмент — комплект специального измерительного инструмента, шаблонов и приборов. Инструмент для измерения параметров колесных пар:
Толщиномер – для измерения толщины обода колеса в плоскости круга катания (рис.5,а) Для измерения ножку (1) движка (2) устанавливают по кругу катания так, чтобы риска совпадала с делением 70 на шкале линейки, и закрепляют винтом (3). Лапку (6) подводят до упора под кромку обода, прижимая линейку (5) к его внутренней грани. Движок (4) перемещают по линейке до соприкосновения ножки с поверхностью катания колеса и закрепляют винтом. Против риски движка на шкале линейки определяют толщину обода.
Абсолютный шаблон – для определения проката, ползуна и навара (рис.5,б) Чтобы выявить глубину проката, ножку (4) движка (3) на шаблоне устанавливают на расстоянии 70 мм от внутренней грани обода. Затем вертикальную грань (1) шаблона плотно прижимают к внутренней грани обода колеса, а опорный выступ (2) к гребню и опускают движок до соприкосновения с поверхностью катания. Деление на шкале, оказавшееся против риски на движке (4) укажет величину проката. Размер ползуна и навара определяется разностью двух измерений, а именно в месте наибольшего дефекта и в месте равномерного проката рядом с ним.
При помощи абсолютного шаблона не изменив его установку на колесной паре можно определить и толщину гребня. Только пользоваться в этом случае нужно не горизонтальным, а вертикальным движком, расположенным на противоположной стороне шаблона.
Штихмас (от нем. Stichmab – мерная лента, применяемая в обувном производстве) – предназначен для измерения расстояния между внутренними гранями колес (рис.5,г). При измерении неподвижная ножка (4) штихмаса плотно прижимается к внутренней грани одного из колес, а подвижная ножка (1) подводится к другому колесу и фиксируется стопорным винтом (2). По делениям шкалы измерительной линейки (3) определяется расстояние между внутренними гранями колес.
Скоба ДК – для измерения диаметров катания колес (рис.5,д). Перед измерением ослабляют стопорный винт (1), прижимают скобу (2) опорными поверхностями бабок к внутренней грани обода колеса. Наконечники бабок (3) и (4) подводят до соприкосновения с поверхностью колеса, при этом подвижную бабку фиксируют стопорным винтом (1). Далее производят считывание показаний по шкале по принципу действия штангенприборов.
Скоба рычажная типа СР-150 – для определения диаметра шейки оси колесной пары. Принцип действия аналогичен скобе ДК.
Кронциркуль служит для определения ширины обода колеса. Для измерения ножки кронциркуля раздвигают и плотно прижимают к граням обода колеса. Измеренное расстояние между ножками кронциркуля определяют с помощью масштабной линейки.
Порядок выполнения работы
Каждая подгруппа студентов, используя инструмент, измеряет параметры элементов колеса и оси. Кроме того, по внешнему виду шейки определяется способ крепления деталей буксового узла.
Содержание отчета
Тема лабораторной работы, дата проведения, цель работы, схема наклейки колесной пары с указанием основных размеров, результаты замеров (выполняется в табличной форме), выводы.
Пример результатов замеров приведен в таблице 1
Таблица 1 – Пример оформления результатов замеров.
№п/п | Измеряемые параметры | Наименование инструмента | Допускаемые размеры | Измеренное значение | |
РУ1 | РУ1Ш | ||||
1. | Толщина обода | Толщиномер | |||
2. | Ширина обода | Кронциркуль или прибор для измерения ширины обода | |||
3. | Диаметр средней части | Кронциркуль, измерительная линейка | |||
4. | Диаметр подступичных частей | Кронциркуль, измерительная линейка | |||
5. | Диаметры шеек | Микрометрическая скоба | |||
6. | Диаметры предподступичных частей | Микрометр | |||
7. | Расстояние между внутренними гранями колес | Штихмас | |||
8. | Толщина гребня | Абсолютный шаблон | |||
9. | Диаметры колес по кругу катания | Штангенциркуль |
и прочие размеры.
Лабораторная работа № 3
ИССЛЕДОВАНИЕ РАСПРЕДЕЛЕНИЯ НАГРУЗКИ МЕЖДУ РОЛИКАМИ ПОДШИПНИКА
Роликовые подшипники являются главной составной частью буксового узла, а все остальные элементы предназначены для обеспечения их надежной работы.
Схемы подшипников приведены на рисунках 6-7.
Рисунок 6 – Радиальный подшипник Рисунок 7 – Общий вид деталей
1 — наружное кольцо; подшипника
2 — ролики; 3 — внутреннее кольцо;
4 — сепаратор; 5 — упорное кольцо
Каждый подшипник состоит из внутреннего и наружного колец. Между кольцами помещаются ролики, которые с помощью сепаратора (клетки) удерживают их на одинаковом расстоянии друг от друга.
Внутреннее кольцо подшипника устанавливается на шейку оси колесной пары с натягом (неподвижно), а наружное кольцо свободно входит в корпус буксы. Поворачиваясь вместе с осью, внутреннее кольцо увлекает за собой ролики, каждый из которых вращается вокруг своей оси и перекатывается между наружным и внутренним кольцами по дорожкам качения. Свободное перемещение роликов обеспечивается радиальным и осевым зазорами, а также осевым разбегом.
Для работы роликовых подшипников с минимальным сопротивлением их заправляют (смазывают) консистентной (густой) смазкой
С целью повышения работоспособности буксовых узлов у современных вагонов, в настоящее время происходит постепенный переход к подшипникам кассетного типа полной заводской сборки, что объясняется не только повышением эксплуатационной надежности буксовых узлов, увеличением межремонтных пробегов вагонов, небольшим сроком окупаемости, но и колоссальным снижением работ связанных с полной (ПР) и промежуточной (ПРР) ревизиями Рисунок 8 – Подшипник кассетного
буксовых узлов на протяжении всей типа
эксплуатации. А также снижение влияния человеческого фактора на качество ремонта. Общий вид подшипника кассетного типа приведен на рисунке 8.
Долговечность буксовых роликовых подшипников определяется, главным образом, величиной контактных напряжений в месте соприкосновения роликов и наружных колец подшипников. При проектировании корпусов букс с роликовыми подшипниками обеспечивают рациональное распределение нагрузки между роликами. В буксах грузовых вагонов эта задача решается введением ребер жесткости, расположенных над серединами роликов. В такой буксе радиальная статическая нагрузка воспринимается пятью роликами: на верхний передается 26,2% нагрузки, на соседние с ним — по 24,6% и на крайние из пяти роликов —по 12,3% (рисунок 9).
Рисунок 9 -Распределение нагрузки между роликами подшипника
Цель работы
Экспериментальная проверка распределения нагрузки между роликами буксового подшипника под действием на него вертикальной статической нагрузки и сравнение результатов с теоретическими расчетами.
Порядок выполнения работы
1. Определить распределение нагрузки между роликами теоретически с использованием зависимостей, полученных графическим разложением вертикальной нагрузки на силы, приложенные к роликам подшипников.
2. Включением электродомкрата произвести ступенчатое нагружение стенда (тележки) и по деформации буксового рессорного комплекта определить нагрузку, действующую на буксу и подшипник.
3. При .помощи динамометрического ключа определить нагрузки, действующие на ролики.
4. По результатам эксперимента построить диаграмму распределения нагрузки между роликами и таблицу нагрузок.
5. Экспериментальные результаты сравнить с расчетными.
Содержание отчета
Тема лабораторной работы; дата проведения; цель работы; схема загружения и роликов подшипника; результаты определения нагрузки, на каждый ролик, полученные расчетным и экспериментальным путем (выполняется в табличной форме и в виде эпюры); выводы.
ОПРЕДЕЛЕНИЕ ЖЕСТКОСТИ УПРУГИХ ЭЛЕМЕНТОВ РЕССОРНОГО ПОДВЕШИВАНИЯ
Рессорным подвешиванием (комплектом) называется устройство, состоящее из упругих элементов (например, пружин или других типов), гасителей колебаний (демпферов) и ограничителей перемещений, обеспечивающих необходимую плавность хода вагона (рисунок 10).
Рессорное подвешивание вагонов является одной из главных частей вагона, обеспечивающей при движении по рельсовому пути необходимые ходовые качества. Рессорное подвешивание состоит из упругих элементов, предназначенных для снижения ударов, передаваемых от колесных пар кузову вагона, и гасителей колебаний, ограничивающих амплитуду колебаний и обеспечивающих ходовые качества на необходимом уровне.
В тележке 18-100 рессорное подвешивание состоит из двух комплектов, размещенных в рессорных проемах левой и правой боковых рам. В каждый комплект входит семь двухрядных цилиндрических пружин и два клиновых фрикционных гасителя колебаний.
Рисунок 10 - Общий вид рессорного комплекта тележки 18-100
Каждая двухрядная пружина состоит из наружной и внутренней пружин, имеющих разную навивку — правую и левую соответственно, чтобы пружины не сцеплялись между собой.
Кроме рессорного подвешивания упругие элементы применяются в поглощающих аппаратах автосцепного оборудования, в упругих площадках пассажирских вагонов и в других узлах вагонного оборудования.
При проектировании рессорного подвешивания основным показателем, определяющим его параметры, является жесткость. Жесткость упругого элемента при его конструировании определяется теоретическим путем при помощи зависимостей, учитывающих его геометрические параметры После изготовления опытных образцов упругих элементов их обычно испытывают на специальных стендах с целью установления действительной жесткости.
Экспериментальная проверка определенной расчетным путем жесткости упругих элементов, применяемых в рессорном подвешивании производится на стенде (рисунок 11), представляющем собой гидравлический пресс с регистрирующими органами.
Упругий элемент (цилиндрическая пружина, листовая рессора, резиновый блок) размещается на специальной установке. Установка состоит из станины, в нижней части которой смонтирован гидравлический пресс. Упругий элемент устанавливается на нижнюю платформу 2, которая является частью поршня, верхний упор 3 жестко связан со станнной стенда. Насос 4, подающий жидкость, работает от электросети. Шкала прибора 5 указывает силу, действующую по поршню,а следовательно, и на упругий элемент. На нижней птатформе установлен указатель высоты, на стойке укреплена линейка 6. Таким образом по разности показании устанавливается деформация упругого элемента подвешивания.
Рисунок 11 – Установка для статического испытания элементов рессорного подвешивания
Прежде чем приступить к определению деформации упругого элемента, его сжимают при помощи винта, укрепленного на верхней платформе. Это делается для того, чтобы ликвидировать все зазоры между упругим элементом и упорами стенда.
По шкале определяют начальную высоту упругого элемента, принимая, что в этом случае он не загружен, т. е. Р0 = 0. Затем упругий элемент ступенчато загружают, отмечая на каждой ступени загрузки его высоту. После этого упругий элемент ступенчато разгружают. Этот процесс загрузки — разгрузки повторяют два-три раза, после чего для каждой ступени находят среднее значение деформации упругого элемента. Деформация определяется вычитанием высоты элемента на каждой ступени загружения из первоначальной его высоты.
Если испытанию подвергаются упругие элементы, не имеющие внутреннего трения (например пружины), то значения деформаций при загрузке и разгрузке элемента на соответствующих ступенях должны быть равны. В том случае, когда допытываются упругие элементы, имеющие внутреннее трение (листовые рессоры, резиновые блоки), средние величины прогибов при каждой ступени находят отдельно для загрузки и разгрузки.
Все значения заносятся в таблицу.
Обработка полученных величин ведется по способу наименьших квадратов. Этот способ даст возможность получить аналитическую зависимость исследуемых величин, отражающую экспериментальные данные с наименьшими отклонениями от последних. Для построения зависимости необходимо предварительно задаться ее видом (линейная, квадратичная и т. д.). Если упругий элемент имеет линейную зависимость деформации от усилия, то формула должна иметь следующий вид:
(6),
гдеРо — начальная нагрузка, после которой упругий элемент начинает деформироваться; с — коэффициент жесткости упругого элемента; f—деформация упругого элемента под нагрузкой Р.
Если перед началом опыта к упругому элементу была приложена достаточная «нулевая» нагрузка, которая полностью ликвидировала все зазоры в размерной цепи, то член Р0 будет равен нулю.
Для нахождения величин Р0 и входящих в формулу 6, по способу наименьших квадратов, необходимо решить систему следующих уравнений:
(7)
где n — количество ступеней загружеиия.
После определения коэффициента жесткости упругого элемента его значение сопоставляется с расчетным, которое вычисляется по формулам, известным из рекомендованной литературы.
Кроме того, определяется коэффициент относительного трения, если упругий элемент имеет внутреннее трение.
Погрешность расчетного способа определения жесткости и коэффициента относительного трения определяется по формуле
(8)
где cр и cэ — коэффициенты жесткости упругого элемента, определенные соответственно расчетным и экспериментальным путем.
Лабораторная работа № 4
ИСПЫТАНИЕ ЦИЛИНДРИЧЕСКОЙ ВИТОЙ ПРУЖИНЫ
При действии внешней нагрузки в пружине возникают касательные напряжения от деформации кручения и сдвига и нормальные напряжения от деформации изгиба и растяжения. Доминирующими напряжениями в витке будут касательные, так как угол подъема витка пружин рессорного подвешивания относительно мал. Поэтому при расчете пружин на прочность обычно определяют только касательные напряжения, а нормальными от деформации изгиба и растяжения пренебрегают.
Параметры пружины
hсв- высота пружины в свободном состоянии, мм;
d - диаметр прутка пружины, мм;
D - средний диаметр пружины, мм;
m - индекс пружины;
G - модуль сдвига, Н/м2;
n – полное количество витков;
nр-количество рабочих витков.
Рисунок 12 – цилиндрическая пружина.
Теоретически жесткость пружины определяется по следующей зависимости:
(9),
где G – модуль сдвига материала пружины равен 80*109Н/м2
Практически жесткость упругого элемента –численно равна силе, вызывающей прогиб, равный 1. (10),
где где P – внешняя сила, действующая на рессору, Н; f- прогиб рессоры, м.
Цель работы
Экспериментальное подтверждение зависимости прогиба от действующей нагрузки, экспериментальное определение жесткости пружины.
Порядок выполнения работы
Производится измерение геометрических параметров пружин. На описанном ранее стенде ступенчато нагружают пружину, затем разгружают до 0, при этом регистрируют нагрузки и прогиб под действием этой нагрузки на каждой ступени.
Данные заносятся в таблицу, аналогичную таблице 2 и строится силовая зависимость, аналогичная рисунку 13.
Таблица 2 - Оформление результатов измерений.
№ п/п | Нагружение | n | Разгружение | ||
Сила, кН | Прогиб, мм | Сила, кН | Прогиб, мм | ||
1 | n-1 | ||||
2 | n-2 | ||||
3 | n-3 | ||||
….. | …. | ||||
n | 1 |
Рисунок 13 – Силовая характеристика пружины
Содержание отчета
Тема лабораторной работы, дата проведения, цель работы, схема пружины, результаты замеров, полученных расчетным и экспериментальным путем (выполняется в табличной форме), графическая зависимость. Производится сравнение результатов теоретического и экспериментального расчета, по формуле 8 определяется погрешность результата. На основании анализа делаются выводы.
Лабораторная работа №5
ИСПЫТАНИЕ ЛИСТОВОЙ РЕССОРЫ
В настоящее время в рессорном подвешивании современных вагонов в качестве упругих элементов в основном используются цилиндрические пружины. Но в отличие от листовых рессор, пружина не обладает достаточными силами неупругого , сопротивления, и для обеспечения этих сил в рессорное подвешивание необходимо включать демпфирующие элементы (гасители колебаний).
Листовая рессора Галахова используется в тележках, эксплуатирующихся в рефрижераторных вагонах. Общая конструкция листовой рессоры приведена на рисунке 14.
Рисунок 14– Конструкция и основные параметры листовой рессоры.
1, 5 – Наконечники; 2 – Болты (заклепки); 3 - Выступ для ограничения поперечного сдвига половин рессоры; 4 - Вырез для ограничения поперечного сдвига половин рессоры;
А – длина рессоры; Б- длина хорды рессоры; В – стрела прогиба;
Г – высота рессоры.
h-толщина листа; b- ширина листа
Основными геометрическими параметрами листовой рессоры являются жесткость и коэффициент относительного трения.
(11),
где E – модуль упругости материала листов.
Цель работы
Экспериментально подтвердить теоретические значения жесткости листовой рессоры.
Порядок выполнения работы
Аналогично лабораторной работе №4
Однако, следует обратить внимание, что силовая характеристика листовой рессоры будет отличаться из-за наличиния внутреннего трения.
Силовая характеристика листовой рессоры приведена на рисунке 15
Рисунок 15 – Силовая характеристика листовой рессоры
Замкнутая область, расположенная между линиями нагружения и разгружения, определяет работу сил трения.
Работа силы трения элементов рессорного подвешивания называется амортизацией
Содержание отчета
Аналогично лабораторной работе №4
Список литературы
1. Соколов М.М., Третьяков А.В., Морчилладзе И.Г.. Архитектоника грузовых вагонов. М.: Транспорт, 2006
2. Лукин В.В. и др. Конструирование и расчет вагонов. М.:УМК МПС России, 2000.731 с.
3. Н.А.Чурков, А.А. Эстлинг. Общее устройство вагонов и их взаимодействие с техническими средствами железных дорог. Учебное пособие.-Спб: Петербургский гос. университет путей сообщения, 1997.-120 с.
4. Морчилладзе И.Г., Соколов М.М.,.. Гносеология грузовых вагонов. М.: Транспорт, 2009.-538с.
Дата добавления: 2020-12-12; просмотров: 106; Мы поможем в написании вашей работы! |
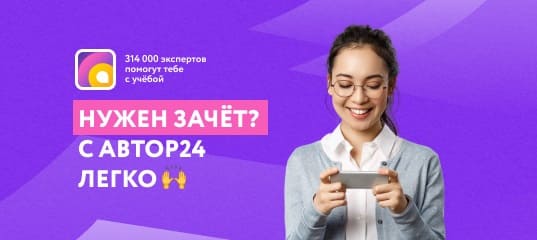
Мы поможем в написании ваших работ!