Рациональный раскрой металла.
План
Виды заготовительных операций, их сущность
Карта раскроя металла.
Рациональный раскрой металла
1. Виды заготовительных операций, их сущность
Заготовительное производство включает следующие операции: складирование; правка исходных заготовок; разметка; резка; подгибка кромок; гибка; очистка под сварку.
Складирование. При организации хранения исходных заготовок необходимо руководствоваться следующими требованиями:
обеспечить защиту металла от атмосферной коррозии, для чего складские помещения должны размещаться в закрытых помещениях, для временного хранения устанавливать навесы для защиты от атмосферных осадков. Особое внимание необходимо уделять сварочным материалам. Они должны храниться в отапливаемом помещении при температуре не ниже 15°С и влажности не выше 50%. Желательно хранить сварочные материалы в герметичных упаковках;
размещать исходные заготовки на хранение с фиксацией точного адреса стеллажа и наименования исходной заготовки;
обеспечить свободный доступ к стеллажам;
оборудовать складские помещения грузоподъемными устройствами.
Правка исходных заготовок. В процессе транспортировки листового и профильногопроката от действия случайных нагрузок возможны искривления формы. Для листового проката:
o волнистость — это искривления листа по всей его ширине;
|
|
o бухтиноватость — местное выпучивание листа;
o серповидность (саблевидность) — искривления листа в плоскости.
Для профильного проката:
o скручивание;
o смалковка;
o размалковка.
Предельные допустимые в соответствии с СП 53-101-98 значения прогибов проката, используемого в металлических конструкциях, приведены в приложении. Исправление дефектов листового и профильного проката предусмотрено операцией правки. Правку проката в зависимости от профиля выполняют на листоправильных или сортоправильных машинах и на прессах в холодном состоянии. Допустима правка стали местным нагревом пламенем газовых горелок, при этом температура зоны нагрева не должна превышать 800 °С для горячекатаных и нормализованных сталей, а для термически улучшенных сталей — 700 °С.
Существующие способы правки предполагают использование схемы нагружения выправляемой заготовки изгибом (рис. 1) либо растяжением (рис. 2).
При правке волнистости листов толщиной от 0,5 до 50 мм изгибом широко используют многовалковые машины с количеством валков от 5 до 21.При прохождении в вальцах лист изгибается в пределах упругости в том случае, если в нем нет искривлений. Если лист имеет искривления, то он, проходя через валки, испытывает пластические деформации. Правка достигается в результате многократного изгиба при пропускании листов между верхним и нижним рядами валков, расположенных в шахматном порядке.
|
|
Чем больше толщина листа, тем меньше количество валков, и чем меньше толщина листа, тем меньше диаметр валка. Качество правки зависит от количества валков, большее количество валков применяют для правки тонких листов и листов из материалов с высоким пределом текучести.
Преимущества правки по схеме растяжения заключаются в более высокой производительности по сравнению с правкой изгибом, в более высоком качестве правки, а также в том, что этот способ позволяет выправлять очень тонкие листы.
Для правки уголков и другого профильного проката используют сортоправильные (углоправильные) машины (рис. 3).
Рис. 3. Схема правки на углоправильных машинах
Правка на углоправильных машинах осуществляется посредством многократных перегибов уголка между двумя рядами роликов, установленных в шахматном порядке так же, как на листоправильных машинах (рис. 3).
Для одновременной правки уголка в обеих плоскостях профиль рабочего ручья ролика выполняют так, чтобы уголок располагался в роликах по диагонали и опирался на каждый правильный ролик двумя полками. Одни и те же ролики можно применить для правки уголков нескольких размеров.
|
|
Правку листового металла толщиной более 50мм, а также профилей круглого сплошного сечения осуществляют под прессом путем локального изгиба искривленных участков (рис. 4).
Рис. 4. Схема правки под прессом 1 — опорные колодки; 2 — искривленная заготовка; 3 — пуансон
Правку, как правило, производят в холодном состоянии, ограничивая относительное остаточное удлинение наиболее деформированных волокон величиной 1% или радиусом изгиба, равным 50δ (δ — толщина листов). Если необходимо создать более значительные деформации, правку сталей производят в нагретом состоянии. Серповидность не поддается исправлению обычными методами.
После правки прокат должен соответствовать следующим требованиям:
Не иметь трещин и расслоений. Допускается наличие местных вмятин по толщине и ширине проката на глубину, не превышающую удвоенной величины минусового допуска для данного вида проката, предусмотренного соответствующим ГОСТ или ТУ, но во всех случаях не более 1 мм по толщине и 3 мм по габаритам сечения.
|
|
Предельные прогибы профильного проката по всей длине элемента не должны превышать 0,001 , но не более 10мм, а про гибы местного искривления — не более 1 мм на длине 1,0м.
Разметка — нанесение контура детали на поверхность исходной заготовки или нанесение линий базирования сопрягаемых деталей при сборке. Выполняется вручную с помошью линейки, циркуля, чертилки, с последующим прокерниванием контурных линий для последующего закрепления изображения. Операция трудоемкая,ограничено поддается механизации и требует высокой квалификации разметчика. Более производительным вариантом разметки является наметка. Выполняется по специально изготовленным шаблонам из тонколистового металла в масштабе 1:1с размерами детали. Усложняет подготовку производства, требует дополнительных затрат на изготовление и хранение шаблонов.
Более производительным методом выполнения разметочных операций являются фотографический и фотопроекиионныи, обеспечивающие проецирование с фотографической пленки контура будущей детали на размечаемую поверхность с последующим закреплением изображения. Методы дорогостоящие, не позволяют получать высокую контрастность изображения, не находят в производстве широкого применения, хотя являются высокопроизводительными и автоматизированными.
Резка. Все существующие приемы резки металлов можно разделить на двегруппы: механическая; термическая.
Достоинством механических способов являются:
высокая производительность;
возможность резки практически любых конструкционных материалов.
К недостаткам следует отнести:
ограничения толщины разрезаемых элементов до 40 мм;
громоздкость и сложность оборудования, высокая стоимость режущего инструмента;
при механической резке происходит исчерпание пластичности в поверхностных слоях зоны реза и, возможно, появление трещин на кромках. В тех случаях, когда после резки предусмотрена операция гибки в направлении поперечном относительно поверхности кромки, необходимо предварительно удалить строжкойнагартованные слои; детали сложной конфигурации с небольшими радиусами закругления механическими способами вырезать можно только с использованием методов штамповки.
Термические способы резки лишены большинства недостатков, характерных для механических способов. Их преимуществами являются:
возможность резки малоуглеродистых сталей практически любой толщины;
возможность вырезки деталей любой конфигурации;
относительная простота и компактность оборудования;
возможность автоматизации.
Недостатками термических способов резки являются:
относительно низкая производительность;
не все материалы одинаково хорошо поддаются резке;
после резки образуются остаточные напряжения;
сравнительно низкое качество поверхности реза.
В производстве сварных конструкций применяют следующие виды ножниц (рис. 5): гильотинные листовые с наклонным ножом (рис. 5, а), двухдисковые с наклонными ножами (рис. 5, г), однодисковые с наклонным ножом, многодисковые(рис. 5, д), ножницы для резки уголка (рис. 5, е), швеллеров и двутавров (рис. 5, ж), пресс-ножницы (рис. 5, б, в) комбинированные сортовые с ручным и механизированным приводом.
Рис. 5. Схемы резки на ножницах различных типов: 1— нижний нож; 2 — разрезаемый материал; 3 — прижим; 4 — верхний нож; 5 — упор
Кромки деталей после механической резки не должны иметь трещин, расслоений, заусенцев и завалов более 1мм.
Применение механической резки допускается без ограничений, если после резки производится механическая обработка кромок на величину не менее 0,2 толщины листового проката.
Термическая резка применяется для листового металла средних и больших толщин и труб большого диаметра. С помощью термической резки может производиться как прямолинейная, так и фигурная резка металла толщиной до 300мм и более.
Основными видами термической резки являются: кислородная (газовая) и плазменно-дуговая (плазменная).
Кислородная резка применяется для малоуглеродистых и низколегированныхсталей толщиной от 5 до 300мм.
Плазменно-дуговая резка применяется для:
♦ малоуглеродистых и низколегированных сталей толщиной 2-28 мм;
♦ коррозионностойких сталей толщиной до 60—80 мм;
♦ алюминиевых сплавов;
♦ меди и ее сплавов.
После термической резки кромки деталей должны быть очищены от грата. Кромки листовых деталей конструкций, остающиеся после сборки и сваркисвободными и работающие на растяжение, должны иметь шероховатость поверхности не более 0,3 мм. Допускается наличие отдельных мест на кромках деталей, не отвечающих указанным требованиям, а также выхватов, не выводящих размер детали за пределы допусков, исправленных плавной зачисткой абразивным кругом или заваркой по специальной технологии с последующей зачисткой мест исправления абразивным кругом, перемещаемым вдоль кромки.
Гибка. Процесс гибки,заключается в пластическом изгибе заготовки,прикотором внутренние слои металла сокращаются, а наружные растягиваются. Гибку следует выполнять при деформациях, исключающих образование трещин. Поэтому в зависимости от свойств материала, толщины, размеров и формы заготовки длякаждого способа гибки и вида оборудования устанавливают предельно допустимые минимальные радиусы. Допускаемые минимальные радиусы гибки основных видов проката из сталей с нормативным пределом текучести до 275 МПа. Если требуется большая кривизна деталей (малый радиус), гибку проводят в горячем состоянии. Температура нагрева должна составлять:
для стали с нормативным пределом текучести до 350 МПа включительно следует нагревать до температуры 900—1000 °С;
для стали, поставляемые в нормализованном состоянии, следует нагревать до температуры 900—950 °С;
при гибки и правке стали всех классов прочности с местным нагревом операции, связанные с пластическим деформированием металла, должны заканчиваться при температуре не ниже 700 °С.
Для предотвращения искажения профильного проката используют гибочные ролики специальной конструкции, а также направляющие и поддерживающие элементы в виде ложементов, вставок или роликов.
Очистка и подготовка поверхности. Приизготовлениисварныхконструкций очистку применяют для удаления с поверхности металла средств консервации, загрязнений, смазочно-охлаждаюших жидкостей, ржавчины, окалины, заусенцев и грата, затрудняющих процесс сварки, вызывающих дефекты сварных швов и препятствующих нанесению защитных покрытий.Для очистки проката, деталей и сварных узлов применяют механические и химические методы.
К механическим методам относятся: дробеструйная обработка, очистка абразивным инструментом, металлическими щетками, шарошками, иглофрезами.
При выборе метода очистки следует придерживаться следующих рекомендаций. Дробеструйная обработка обеспечивает высокую производительность, но требует применения защитных устройств для снижения шума. Ее применяют в серийном и массовом производстве для очистки больших по размеру поверхностей. Очистка абразивным инструментом является наиболее универсальным способом, не требующим громоздкого, сложного оборудования, поэтому данный метод имеет наиболее широкое применение, особенно в монтажных условиях. В качестве абразивного элемента используют абразивные круги сплошного сечения и лепестковые круги, представляюшие собой полоски наждачной бумаги, закрепленные в оправке в радиальном направлении. Последние более плавно огибают обрабатываемую поверхность и обеспечивают более качественную очистку. Очистку кромок и сварных соединений следует выполнять в направлении, перпендикулярном к сварному шву. В противном случае появляющиеся при очистке риски могут послужить инициатором разрушения конструкции при эксплуатации.
Следует обратить внимание, что в процессе абразивной очистки выделяется много пыли. Это необходимо учитывать при обеспечении охраны труда. Кроме того, этот метод неприменим для очистки деталей из алюминиевых сплавов, так как частицы металла быстро налипают на поверхность абразивного инструмента и ухудшают его режущую способность, а также происходит вкрапление частиц абразива в алюминиевые сплавы, что ухудшает его свариваемость. Для очистки деталей из алюминиевых сплавов используют металлические щетки, шарошки или иглофрезы.
Химические методы очистки требуют организации отдельных производственных участков, поэтому используются в основном в массовом производстве, особенно в тех случаях, когда требуется очистка больших поверхностей, например для контактной сварки.Существуют две разновидности химических методов очистки — ванный и струйный. Первый предполагает периодическое погружение очищаемой детали в ванны с различными растворами. Обычно предполагается различный набор растворов для обезжиривания и травления. После каждого раствора производится промывка, а в конце предполагается сушка. Состав растворов зависит от вида и марки материала изделия.
При струйном способе очистки изделие подвергается воздействию тех же химических растворов, но их наносят на изделие струей под давлением. Этот способ очистки повышает производительность и качество, но требует большего расхода материалов.
Химические методы очистки наиболее часто используются при подготовке деталей из алюминиевых сплавов. Назначение пассивирования состоит в том, чтобы на поверхности деталей создать тонкую, плотную пленку, препятствующую дальнейшему окислению поверхности на воздухе, но не вызывающую затруднений при сварке.
Подготовка кромок под сварку. Помимо очистки кромок перед сваркой имтребуется придать определенную форму, обеспечивающую возможность их проплавления и удобство манипулирования электродом. Форма профиля кромки и размеры зависят от выбранного способа сварки, толщины металла, конструкции стыка, его пространственного положения при сварке и возможностей точного направления электрода по стыку. В общем случае при выборе формы профиля кромки следует руководствоваться соответствующими стандартами или отраслевыми нормативными документами. При этом необходимо стремиться к уменьшению объема наплавленного металла и вместе с тем не создавать условия для образования дефектов. При ручной дуговой сварке толстого металла наиболеечасто применяется односторонняя V-образная или двухсторонняя Х-образная разделка кромок (рис. 8). Угол φ выбирают так, чтобы сварщик имел возможность манипулировать электродом и обеспечивать проплавление кромок. Величину притупления кромок с выбирают так, чтобы обеспечивать проплавление корня шва. При такой разделке объем наплавленного металла увеличивается пропорционально квадрату толщины кромок. Применение двусторонней разделки кромок резко сокращает объем наплавленного металла и при правильной последовательности наложения швов уменьшает сварочные деформации, но такая разделка кромок требует кантовки свариваемых деталей, что повышает трудоемкость изготовления и требует доступа к шву с двух сторон. В качестве альтернативы рекомендуют применять несимметричную разделку кромок.
Рис. 8. Форма разделки кромок, применяемая для ручной дуговой сварки
Широкое пространство для манипуляции электродом требуется только в нижней части разделки. В более высоких слоях ширина V-образной разделки становится избыточной, поэтому для больших толщин ГОСТ предусматривает применение фигурных разделок кромок (рис. 9). Для получения такой разделки требуется обработка резанием на кромкострогальных, карусельных или токарных станках, что ведет к увеличению стоимости обработки, но существенно повышает качество подготовки кромок и, следовательно, способствует обеспечению качества сварки.
Рис. 9. Фигурная разделка кромок
Штамповка выполняется в холодном или горячем состоянии для
тонколистового металла холодная штамповка 6-8 мм, а для металла толщиной 8-10 применяют горячую штамповку. Штамповку используют для ускорения изготовления заготовительных операций и уменьшение массы конструкции.Детали двойной кривизны (в двух взаимно перпендикулярных плоскостях) получают вытяжкой, вальцовкой на специальных машинах, обтяжкой, выдавливанием и т.п. Лепестки для крупных шаровых резервуаров делают на многовалковой машине, имеющей форму валков и расположение их осей в соответствие с радиусом обрабатываемой сферической оболочки. Днища эллипсной или сферической формы выполняют из круговой листовой заготовки вытяжкой на прессе с помощью пуансона и матрицы. Детали с переменой кривизной, отличающиеся от тел вращения, получают на растяжно-обтяжных прессах за счет движения профилированного пуансона и дополнительного растягивающего усилия подвижных зажимов. Выдавливание используют для формообразования деталей типа тел вращения. Процесс выдавливания заключается в местном пластическом изгибе круговой вращающейся заготовки давильным инструментом, перемещающимся в плоскости оси вращения профилированной оправки. Под действием инструмента заготовка принимает форму оправки.
Поступающий на предприятие металлопрокат сортируют по видам, толщине, химическому составу и механическим свойствам. После выбора основного металла выполняют заготовительные операции, которые предусматривают изготовления заготовок и готовых деталей для сварных узлов различными способами.
2. Карта раскроя металла.
Раскрой металла — это разделение металла на отдельные заготовки, иногда разные по форме, размерам, но одинаковой толщины — по комплектности на одну единицу изделия, на машинокомплект.
Карта раскроя металла зависит от толщины металла, которую выбирают по чертежу согласно ГОСТ 19903 — 84 для изготовления сварной конструкции выбирают, лист с габаритными размерами Лист рисуют в выбранном масштабе в этом же масштабе на листе металла показывают заготовки деталей для раскроя выбранную деталь с самими большими размерами.
зависимости от размеров деталей различают в основном два типа раскроя:
I. Лист раскраивают с учетом изготовления деталей одного размера - одного
наименования (пример: рис.1).
Лист раскраивают с учетом изготовления деталей разных размеров - разных наименований (пример: рис.2).
Размещение заготовок выполняется с минимальным отходом и максимальным полезным коэффициентом использования. Если детали по своим размерам можно изготовить из полосового проката, то это эффективнее, чем резать листовой прокат. Рациональное использование проката приведет не только к его экономии, но и снижению трудоемкости и повышению производительности, так как сокращаетсячисло резов
Рациональный раскрой металла.
Определяют:
площадь листа Sл = Д*Ш
где Д – длина листа, Ш – ширина листа
площадь одной заготовки Sд1 = д1 * ш1
где д1 – длина одной детали, ш1 – ширина одной детали
Процент отхода металла рассчитывается по формуле:
П от=GЗаг-G1×100% GЗаг.
где G1 - масса детали, кг
GЗаг. — масса заготовки, кг
П | от = | s | л | -sд | * n | ×100 % | |
s д | |||||||
где Sл – площадь листа, мм2
Sд – площадь одной детали, мм2
n - количество деталей на листе, шт
Если % отходов свыше 5% то необходимо из оставшегося металла вырезать более мелкие детали в том же масштабе
П от = | G Заг | - (G1 * n1+G2 | * n2 ) | ||
×100% % отхода должен быть ниже 5% | |||||
G Заг. | |||||
Коэффициент использования определяется по формуле:
КИ=G2
G3
где G2 - масса деталей на листе, кг;
G3 - масса листа, кг.
ПРИМЕР РАСЧЕТА №1
Деталь № 150.03.03, накладка на изделие 2 шт., чистовой вес детали 7,2 кг; 7,2 х 2 = 14,4 кг. Программа 115 изделий.
Выбираем в соответствии с ГОСТ 19903-74 лист размером 6x2500x8000, размешаем деталь. Получаем по 10 шт. в 23 ряда. Всего деталей n = 10 * 23 = 230 шт. Определяем массу деталей в листе
G1 = 7,2 * 230 = 1656 кг
Масса выбранного листа 1972 кг Коэффициент использования
КИ | = | G1 | ||||||||||
G3 | ||||||||||||
Где | G1 - масса деталей на листе, кг | |||||||||||
G2 - масса листа, кг | ||||||||||||
Следовательно, |
| КИ | = | 1656 |
| =,088 | ||||||
| ||||||||||||
1872 | ||||||||||||
Норму расхода на заготовку I детали определяют по формуле: | ||||||||||||
G = | G3 |
| ||||||||||
| ||||||||||||
2 | n | |||||||||||
где | n - число деталей на листе, шт. | |||||||||||
Итак, | G2 | = | 1872 | = 8.13кг | ||||||||
230 | ||||||||||||
Накладка на изделие 2 шт., значит | 8,13 х 2 = 16,26 кг. |
Данные заносим в соответствующие графы карты раскроя металла.
Процент отхода составит (по формуле 4):
8,13 - 7,2
ПОТХ= ×100% = 11,4%
Коэффициент использования металла в машиностроении составил (0,6-0,88), что соответствует нормативным данным.
ПРИМЕР РАСЧЕТА №2
Рассчитываем массу детали по формуле:
V ×
G1 =106
где V— объем детали, м ;
у - плотность стали 7,85 г/см3.
V Д=424×75×6=190800мм3
G = | 190800 × 7.85 | = 1.5кг | |
106 | |||
1 |
2. Количество деталей на листе составляет 80 шт.
3. Масса деталей на листе составляет.
4. Определяем массу листа
G = | V × | = | 8500 × 300 × 6 × 7.85 | = 120.1кг | |
106 | |||||
3 | 106 |
5. Определяем коэффициент использования
К И=120= 0,99 120,1
Коэффициент использования металла в промышленности составляет (0,6-0,88).
Полученный результат соответствует нормативным данным.
6.Определяем массу заготовки
n G Заг= G380
7.Процент отхода составит
П от=G Заг-G1×100%=120.1-120×100%=0.08%
G Заг120.1
Дата добавления: 2021-01-20; просмотров: 551; Мы поможем в написании вашей работы! |
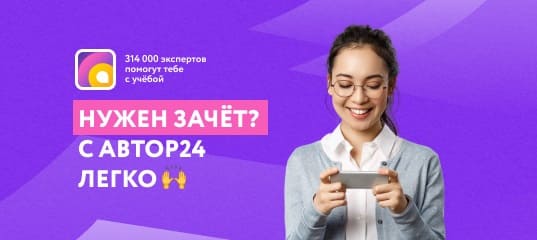
Мы поможем в написании ваших работ!