Висбрекинг-установка с реакционной камерой.
Практическое занятие
Термические процессы нефтепереработки
Цель занятия: закрепление знаний по термическим процессам нефтепереработки.
Пояснения
Под влиянием высоких температур связи между атомами и молекулами углеводородов нефти ослабевают, они могут разрываться, и тогда образуются новые соединения. В каждом гомологическом ряду более легкие, низкокипящие углеводороды расщепляются труднее, чем высококипящие. Наряду с расщеплением и образованием более легких углеводородов происходят и другие превращения, в том числе уплотнение с получением более крупных молекул. Процессы, в которых более тяжелые фракции первичной перегонки нефти подвергаются разложению под влиянием повышенных температур, называются термическими. В нефтеперерабатывающей промышленности применяют следующие термические процессы: термический крекинг, коксование и пиролиз.
Термический крекинг, обычно осуществляемый под давлением до 5 МПа (50 кгс/см2) и при температурах от 420 до 550° С, является процессом качественного изменения сырья с образованием новых соединений, отличающихся от исходных своими физико-химическими свойствами. В зависимости от состава сырья и условий процесса выход бензиновых фракций при крекинге составляет 7—30% от исходного сырья. Наряду с бензиновыми фракциями образуются другие продукты — газообразные, жидкие и твердые (кокс).
|
|
Коксование нефтяных остатков ведут при температурах от 445—460 (при коксовании в кубах) до 485—540° С. В зависимости от качества сырья, типа процесса и технологического режима получают (от исходного сырья) 15—38% товарного кокса, 49—77,5% жидких продуктов (в том числе 7—17% бензиновых фракций) и 5—12% газа до С4 включительно.
Пиролиз дистиллятного сырья, а также легких углеводородов (от этана до бутана) проводят обычно при температурах от 650 до 850° С. Основное назначение пиролиза — получение этилена и пропилена, а раньше — получение ароматических углеводородов.
В 30—50-х гг. термический крекинг сыграл большую роль в увеличении производства бензина, необходимого для карбюраторных двигателей. Однако в дальнейшем качество бензинов, получаемых на установках термического крекинга, перестало удовлетворять возросшим требованиям потребителей. После появления каталитических процессов термический крекинг в основном применяют для получения низковязких мазутов из продуктов, остающихся при первичной переработке нефти, и термогазойлей — сырья для получения сажи. Процессы коксования продолжают развиваться в основном для удовлетворения нужд народного хозяйства в коксе, особенно электродном. Одновременно, а иногда и специально, жидкие продукты коксования используют для увеличения производства светлых нефтепродуктов. Пиролиз развивается быстрыми темпами в связи со все возрастающими потребностями в олефиновом сырье, необходимом для химической и нефтехимической промышленности.
|
|
Установка висбрекинга тяжёлого сырья.
Висбрекинг — процесс однократного термического крекинга тяжелого остаточного сырья, проводимый в мягких условиях. Типичное сырье висбрекинга — мазуты, получаемые при атмосферной перегонке нефтей, или вакуумные гудроны. Восприимчивость гудрона к висбрекингу тем выше, чем ниже температура его размягчения и чем меньше асфальтенов, нерастворимых в н-пентане .
Висбрекинг проводится для производства преимущественно жидкого котельного топлива пониженной по сравнению с сырьем вязкости (вариант I), либо с целью производства в повышенных количествах газойля—сырья для установок гидрокрекинга и каталитического крекинга (вариант II). В обоих вариантах побочными легкими продуктами являются газы и бензиновые фракции, выход которых обычно не превышает 3 и 8 % (масс.) на сырье. Проведение процесса в более жестких условиях, что оценивается по выходу бензина, может приводить к нестабильности топлив, получаемых смешением остаточного продукта висбрекинга с другими компонентами тяжелого жидкого котельного топлива. Нестабильное топливо расслаивается, в нем образуется осадок .
|
|
При проведении висбрекинга по варианту I характерно следующее:
сохранение в составе остаточного продукта (называемого ниже висбрекинг-мазутом) всех жидких фракций, кроме бензиновых;
высокий выход висбрекинг-мазута (90—93 % масс. на сырье);
более низкие по сравнению с сырьем вязкость, температуры начала кипения и застывания висбрекинг-мазута;
простота и гибкость технологической схемы установки, позволяющие перерабатывать остаточное сырье разного качества. В результате висбрекинга гудронов значительно сокращается расход маловязкого дистиллятного разбавителя при приготовлении котельного топлива. Содержание тяжелых бензиновых фракций в остаточном продукте висбрекинга ограничивают, учитывая необходимость получения топлива с достаточно высокой температурой вспышки.
При проведении висбрекинга по варианту II установка дополняется вакуумной секцией, предназначаемой для выделения из висбрекинг-мазута вакуумного газойля. В результате процесса потенциальное содержание вакуумного газойля в сырье повышается на 25—40 % (об.).
|
|
На некоторых заводах часть тяжелого остатка, получаемого по варианту II и являющегося нижним продуктом вакуумной колонны, используется как топливо на самих заводах, а избыток после разбавления маловязким продуктом, например каталитическим газойлем, направляется в резервуар товарного мазута нормированной вязкости. Ниже в качестве примера дана характеристика сырья, используемого для висбрекинга, выходы продуктов и их качество, по данным фирмы Lummus :
Показатели | Остаток атмосферной колонны | Остаток вакуумной колонны |
Характеристика сырья плотность при 15 оС, кг/м3 температура застывания, оС вязкость кинематическая, мм2/с при 50 оС при 99 оС Выходы продуктов, % (масс.) газ нестабильный бензин (кк 175 оС) остаток > 177 оС Характеристика остатка > 177 оС плотность при 15 оС, кг/м3 температура застывания, оС вязкость кинематическая, мм2/с при 99 оС | 948,4 10 175 22 2,5 7,5 90,0 924,8 4,4 10 | 1024,6 49 1900 - 2,5 7,5 90,0 995,8 40,6 380 |
Установка висбрекинга может входить как секция в состав комбинированной установки, например атмосферная перегонка нефти висбрекинг атмосферного мазута вакуумная перегонка висбрекинг-мазута для выделения газойлевых фракций или висбрекинг атмосферного мазута
выделение газойлей (в частности, под вакуумом) термический крекинг смеси газойлей с целью увеличения выхода керосиновой фракции. Возможны также варианты установок висбрекинга: на одних нагретое сырье по выходе из печи направляется в не обогреваемый реактор, где в основном и осуществляется неглубокий термокрекинг; на других — нагретое сырье подвергается висбрекингу в обогреваемом змеевике (сокинг-секция), расположенном во второй топочной камере трубчатой печи.
Для висбрекинга гудронов условия процесса такие: температура 460—500°С; давление 1,4— 3,5 МПа. Длительность пребывания сырья в зоне реакции определяется с помощью уравнения скорости реакции первого порядка . Требуемый объем реакционной зоны, т. е. того участка змеевика, где температура сырья превышает 399 °С, составляет 3,6—4,8 м3 на каждые 1000 м3 перерабатываемого жидкого сырья в сутки.
Процесс висбрекинга протекает с поглощением тепла.
Октановое число бензиновой фракции висбрекинга находится в пределах от 58 до 68 (моторный метод, без присадки). Содержание серы в бензиновых и керосиновых фракциях существенно ниже, чем в сырье; однако эти фракции обычно нуждаются в очистке. Например, подвергая висбрекингу мазут [мол. масса 407, плотность 938,5 кг/м3; содержание серы 1,81 % (масс.), коксуемость 5,0 % ], самотлорской нефти, получали бензин и керосин, содержащие до очистки 0,7 и 1,0 % (масс.) серы.
Рис. 1. Технологическая схема висбрекинг-установки с реакционной камерой: 1, 7, 9, 10, 14 – насосы, 2 – трубчатая печь, 3 – реактор, 4 – редукционный клапан, 5 – холодильник, 6 – теплообменник, 8 – фракционирующая колонна, 11 – аппарат воздушного охлаждения, 12 – водяной холодильник, 13 – сепаратор.
Висбрекинг-установка с реакционной камерой.
Горячий мазут, поступающий с нефтеперегонной установки, подается насосом 1 в змеевик печи 2. По выходе из печи сырье подвергается висбрекингу в реакционной камере 3 (реакторе), работающей при давлении около 1,7 МПа. Полученная смесь продуктов, пройдя редукционный клапан 4, направляется далее в фракционирующую колонну 8. До входа в колонну смесь охлаждается за счет подачи в линию холодного газойля, нагнетаемого насосом 7, через теплообменник 6. Остальная часть охлажденного газойля (рециркулят) возвращается этим же насосом в среднюю зону колонны 8. Балансовое количество газойля отводится с установки через холодильник 5.
Для конденсации бензиновых паров и охлаждения газов, выходящих из колонны 8 сверху, служит аппарат воздушного охлаждения 11. После него смесь проходит водяной холодильник 12. В горизонтальном сепараторе 13 (он же сборник орошения) жирные газы отделяются от нестабильного бензина. Часть бензина подается насосом 14 на верхнюю тарелку колонны в качестве орошения; остальное количество отводится с установки.
Легкая керосиновая фракция отбирается из колонны с промежуточной тарелки и насосом 10 выводится с установки. На некоторых установках эта фракция предварительно продувается водяным паром в выносной отпарной колонне.
Описанная установка является частью комбинированной установки, и с низа колонны 8 остаток — утяжеленный висбрекинг-мазут — направляется насосом 9 в вакуумную ступень.
Термический крекинг. В 1890 г. знаменитый русский ученый В. Г. Шухов спроектировал первую в мире крекинг-установку для получения легких нефтепродуктов из мазута. В дальнейшем, с увеличением потребности в автомобильном бензине, была создана система с реакционными камерами, в которых сырье, нагретое в трубчатом змеевике печи до температуры реакции, задерживалось и крекировалось до образования кокса. Время заполнения реактора коксом определяло продолжительность рабочего цикла установки. Затем вместо реакционной камеры стали создавать реакционный объем в трубах, расположенных в конвекционной камере печи. Во избежание закоксовывания аппаратуры продукты реакции на выходе из печи охлаждали холодным сырьем (так называемый квенч), тем самым прекращая процесс крекинга (по такой схеме работали установки Винклера—Коха). В дальнейшем были введены и другие усовершенствования как за рубежом, так и в Советском Союзе, где термический крекинг был внедрен в 1927—1928 гг.
Как уже говорилось, основной реакцией при термическом крекинге является реакция разложения (расщепления, крекинга). Легче всего подвергаются крекингу парафиновые углеводороды, затем нафтеновые; наиболее устойчивы ароматические углеводороды. В каждом гомологическом ряду легче подвергаются крекингу углеводороды большей молекулярной массы. Таким образом, более тяжелые фракции нефтяных продуктов менее стабильны и крекируются значительно легче, чем более легкие.
Результаты крекинга зависят от фракционного и химического состава сырья и технологического режима, особенно температуры и давления.
Сырье. При прочих равных условиях скорость крекинга зависит от фракционного и химического состава крекируемого сырья.
Скорость образования бензина, так и выход всех образовавшихся фракций увеличиваются с повышением температуры выкипания (утяжелением) сырья. Вместе с тем выход кокса при одинаковом выходе бензина увеличивается при крекировании более тяжелого сырья. В заводских условиях выход кокса допускается не более 0,1% от исходного сырья, при этом условии однократный крекинг мазута дает не более 8% бензина (с температурой конца кипения 200°С), крекинг керосина — не более 40%.
Скорость крекинга зависит также от химического состава сырья. Так, сырье с высоким содержанием ароматических углеводородов плохо поддается крекингу, поэтому скорость его значительно меньше, чем крекинга парафинистого сырья. Как уже говорилось, высокомолекулярные парафиновые углеводороды или парафиновые боковые цепи циклических углеводородов разрушаются легче, чем нафтеновые и особенно ароматические углеводороды с короткими боковыми цепями. Таким образом, скорость крекинга тесно связана с химическим составом и молекулярной массой крекируемого сырья.
Температура — один из основных факторов крекинг-процесса. С повышением температуры скорость реакций крекинга увеличивается. Зависимость температуры и времени крекинга мазута при одинаковом (30%-ном) выходе бензина характеризуется следующими данными:
Температура крекинга, °С . . 400 425 450 475 500
Продолжительность крекинга,
мин 720 120 20 2 0,6
Обычно продолжительность крекинга керосино-дизельных фракций в промышленных условиях составляет 5—7 мин. Для упрощенных расчетов можно принять, что скорость крекинга удваивается при нагреве на каждые 10° С при температуре процесса около 400° С, на каждые 14° С — при 500° С и на каждые 17° С — при 600° С.
Давление заметно не влияет на скорость крекинга и образование бензина при обычных его выходах. Однако крекинг под давлением обеспечивает наиболее желательные условия для распределения тепла и устранения местного перегрева и поэтому дает меньший выход смол и кокса, протекает с максимальным эффектом и минимальным расходом топлива. Повышение давления позволяет увеличить производительность установок.
Первичные реакции не зависят от давления, а вторичные (полимеризации и конденсации) — зависят. Высокие давления благоприятствуют протеканию ряда вторичных реакций, в том числе превращению олефиновых углеводородов в нафтеновые. В результате реакций уплотнения, протекающих быстрее при крекинге под давлением (особенно в паровой фазе), продукты крекинга содержат меньше непредельных углеводородов, чем продукты крекинга, проведенного под низким давлением. Повышение давления способствует протеканию реакции полимеризации, в результате чего содержание в газе непредельных углеводородов, особенно легких олефинов, снижается.
Глубина превращения определяется выходом бензина из исходного сырья. Она является сложной функцией продолжительности и скорости крекинга. Так как скорость крекинга определяется в основном температурой и временем, глубина превращения обычно является функцией времени и температуры. Коксообразование при крекинге крайне нежелательно, так как кокс отлагается в аппаратуре, в трубах печи и трубопроводах, что сокращает межремонтное время и может привести к прогару печных труб и ухудшению качества крекинг-остатка.
Теплота основных реакций термического крекинга. Величиной, необходимой при расчете крекинг-печей, является теплота реакций, которая принимается равной: для легкого крекинга (висбрекинга) гудрона и полугудрона 117—234 кДж/кг (28—56 ккал/кг); для крекинга керосино-дизельных фракций 1256—1465 кДж/кг (300—350 ккал/кг) и для крекинга мазута 1256—1675 кДж/кг (300—400 ккал/кг). Приведенные выше значения теплоты реакций термического крекинга являются разностью между теплотами реакций расщепления, которые проходят с поглощением тепла (эндотермические реакции), и реакций уплотнения, протекающих с выделением тепла (экзотермических). Как видно из приведенных данных, термический крекинг идет с поглощением тепла.
Термический крекинг с рециркуляцией. В результате совместного воздействия рассмотренных выше факторов определяются показатели однократного крекинга. Выход бензина в процессе однократного крекинга ограничивается, с одной стороны, началом его интенсивного разложения (что приводит к увеличению выхода газа) , с другой — усилением коксообразования. Последнее влияет на межремонтное время установки и объем коксоочистительных работ, определяющие длительность ремонта установки. При однократном крекинге получают газ, бензин, промежуточные фракции, крекинг-остаток и иногда — крекинг-керосин. Максимальный выход бензина из легких дистиллятов прямой перегонки нефти при однократном крекинге без заметного коксообразования составляет до 30%, а из тяжелых дистиллятов и остатков (гудрона) — соответственно 20 и 6% исходного сырья.
Более высокие выходы крекинг-бензина с минимальным коксо-образованием могут быть получены в результате многократного повторения крекинга, когда крекируются и дистилляты (промежуточные фракции), получаемые после отделения и удаления остатков, содержащих коксообразующие продукты конденсации. Промежуточную фракцию (крекинг-флегму) можно подвергать крекингу отдельно (так называемый крекинг «гуськом») или в смеси со свежим сырьем (крекинг с рециркуляцией).
В промышленности основным процессом является крекинг с рециркуляцией. Отношение количества крекинг-флегмы к количеству свежего сырья называется коэффициентом рециркуляции, а отношение полной загрузки реакционного аппарата к загрузке его свежим сырьем — коэффициентом загрузки, С увеличением коэффициента рециркуляции растет выход бензина, но снижается производительность установки.
Коксование. Процесс замедленного коксования в необогреваемых камерах предназначен для получения крупнокускового нефтяного кокса как основного целевого продукта, а также легкого и тяжелого газойлей, бензина и газа. Сырьем для коксования служат малосернистые атмосферные и вакуумные нефтяные остатки, сланцевая смола, тяжелые нефти из битуминозных песков, каменноугольный деготь и гильсонит. Эти виды сырья дают губчатый кокс. Для получения высококачественного игольчатого кокса используют более термически стойкое ароматизированное сырье, например смолу пиролиза, крекинг-остатки и каталитические газойли.
Основными показателями качества сырья являются плотность, коксуемость по Конрадсону и содержание серы. Выход кокса определяется коксуемостью сырья и практически линейно изменяется в зависимости от этого показателя. При коксовании в необогреваемых камерах остаточного сырья выход кокса составляет 1,5—1,6 от коксуемости сырья. При коксовании дистиллятного сырья выход кокса не соответствует коксуемости сырья, поэтому составлять материальный баланс расчетным методом для такого сырья нельзя. Главным потребителем кокса является алюминиевая промышленность, где кокс служит восстановителем (анодная масса) при выплавке алюминия из алюминиевых руд. Кроме того, кокс используют в качестве сырья при изготовлении графитированных электродов для сталеплавильных печей, для получения карбидов (кальция, кремния) и сероуглерода.
Основными показателями качества кокса являются истинная плотность, содержание серы, зольность и микроструктура. Для игольчатого кокса истинная плотность должна быть не ниже 2,09 г/см3, для кокса марки КНПС (пиролизного специального), используемого в качестве конструкционного материала, она находится в пределах 2,04—2,08 г/см3 .
Содержание серы в коксе почти всегда больше, чем в остаточном сырье коксования. Из остатков малосернистых нефтей получают малосернистый кокс, содержащий, как правило, до 1,5 % (масс.) серы; кокс из сернистых остатков содержит обычно 2,0— 4,5 % (масс.) серы, а из высокосернистых — более 4,0 % (масс.) .
Содержание золы в коксе в значительной мере зависит от глубины обессоливания нефти перед ее перегонкой.
Пиролиз нефтяного сырья. Назначением процесса пиролиза — наиболее жесткой формы термического крекинга — является получение углеводородного газа с высоким содержанием непредельных, и в первую очередь этилена, поэтому часто установки пиролиза называют этиленовыми установками. Процесс может быть направлен и на максимальный выход пропилена или бутиленов и бутадиена .
Получаемый с помощью пиролиза этилен идет на производство оксида этилена, пластических масс и полимеров. Образующийся в процессе пиролиза пропилен используется в основном для производства полипропилена, акрилопитрила и бутадиена.
Сырьем для процесса пиролиза служат углеводородные газы, легкие бензиновые фракции, газоконденсаты, рафинаты каталитического риформинга, керосиновые и газойлевые фракции; ведутся исследования по пиролизу нефтей и нефтяных остатков. Выбор сырья определяется целью пиролиза, а также доступностью сырья, его количеством, стоимостью, а также экономическими показателями процесса. От качества сырья и технологического режима установки зависят выходы продуктов пиролиза. Наибольший выход этилена получается при пиролизе этана. По мере утяжеления сырья выход этилена снижается с одновременным увеличением выхода пиролизной смолы (углеводородов С6 и выше) и кокса. С повышением температуры процесса и уменьшением времени реакции выход этилена увеличивается. Для повышения выхода непредельных и снижения коксообразования в реакционную смесь подают различные разбавители, например водяной пар, водород, метан или метано-водородную смесь.
Известны различные варианты пиролиза: с твердым теплоносителем, в перегретом водяном паре, в электроразрядных трубках, в вольтовой дуге, в системе с катализатором. Наибольшее же распространение в промышленности получил пиролиз в трубчатых печах.
Основными продуктами современных пиролизных установок являются: этилен чистотой 99,9% (масс.), пропилен чистотой 99,9% (масс.), бутан-бутадиеновая фракция, содержащая 30—40% (масс.) бутадиена, 25—30% (масс.) изобутилена и 15—30% (масс.) н-бутилена, и смола пиролиза. Смола пиролиза разгоняется на фракции по разным вариантам. Например, на установке ЭП-300 выделяют ароматизированную фракцию н.к.—150°С, содержащую 25—30 % (масс.) бензола, 20—25 % (масс.) толуола и 10—15% (масс.) ксилолов для экстракции ароматических углеводородов; фракция 150— 250°С служит дистиллятным топливом, а фракция 250—400СС — компонентом котельного топлива. На одной из зарубежных установок (Германия) смолу разгоняют на бензин до 200°С и остаток. На некоторых заводах страны из смолы получают следующие фракции: н.к.—70°С, являющуюся компонентом бензина; 70—130 °С, используемую для извлечения ароматических углеводородов; 130—160оС, идущую на полимеризацию с получением полимеров стирола; 160—190°С, полимеризуемую в инден-кумароновую смолу; 190—230оС, используемую для извлечения нафталина, и остаток >230°С — пек пиролиза, используемый для получения кокса, пеков или технического углерода.
Задание
1. Заполнить таблицу 1 по основным параметрам термических процессов.
Таблица 1. Параметры термических процессов
№№ п/п | Наименование процесса | Сырьё | Температура, 0 С | Давление, Па |
1. | Термический крекинг | |||
2. | Коксование | |||
3. | Пиролиз | |||
4. | Висбрекинг тяжёлого сырья |
2. Составить таблицу 2, указав наименование процесса и получаемые продукты.
3. Основные факторы термических процессов.
4. Применение продуктов термических процессов нефтепереработки.
5. Почему в газах термических процессов нефтепереработки присутствует большое количество непредельных углеводородов?
Отчет
Дата добавления: 2020-12-22; просмотров: 543; Мы поможем в написании вашей работы! |
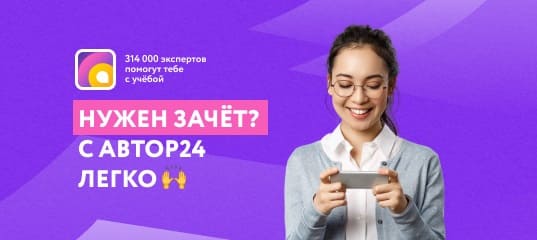
Мы поможем в написании ваших работ!