Подбор механизмов для монтажа сетей газоснабжения
Расчет потребности транспортных средств
Для транспортировки грунта на расстояние свыше 0,5 км в комплекте с экскаватором могут быть использованы автосамосвалы, тракторы с прицепами и полуприцепами.
Необходимая грузоподъемность транспортных средств определяется в зависимости от объема ковша экскаватора, расстояния перевозки и объема разработки грунта.
При этом стремятся, чтобы вместимость кузова выбранного автосамосвала была равна 3-6 ковшам грунта.
Количество автосамосвалов, необходимое для бесперебойной работы экскаватора вычисляется по формуле:
, шт
Пэ – эксплуатационная производительность экскаватора, м3/смен.
, м3/смен
Пт – техническая производительность экскаватора, м3/час.
, м3/час
q – емкость ковша, м3
Кпр-коэффициент первоначаотного разрыхления грунта, зависит от типа грунта и определяется по таблице
Кн- коэффициент наполнения ковша, зависит от грунты: чем рыхлее порода, тем больше 0,9 – мелкодробная порода, 1,2 – песок
n- число циклов (экскаваций) за час работы
tц- продолжительность 1 рабочего цикла для экскаватора с обратной лопатой 0т 21-23с до 50с
Т- продолжительность смены, ч
Кв - коэффициент использования экскаватора по времени с учетом потери времени при передвижке экскаватора, задержке в работе при подачи транспортных средств и пр. Принимается 0,65-0,8.
G – объем грунта, перевозимого автосамосвалом за 1 рейс, м3
|
|
, м3
Т – число часов работы экскаватора в смену,
n - число рейсов в час:
tр- продолжительность рейса, ч
l – расстояние от забоя до места выгрузки, км
vг и vп – скорость соответственно груженого и порожнего автосамосвала, км/час
tп , tраз , tм– время погрузки, разгрузки, маневровых операций автосамосвала, час
nковш. – число разгружаемых на самосвал ковшей, шт.
tразгр. – время разгрузки, для автосамосвалов принимается 1 мин, 1/60 часа.
tм. – время маневровых операций, обычно не превышает 2 мин 1/30 часа.
Кроме того, необходимы транспортные средства для доставки оборудования и материалов на монтажную площадку (железобетонные конструкции колодца, арматура, трубопроводы).
Этот расчет ведем в следующей последовательности:
1. Определяем объем грузоперевозок: Gж/б, Gарм, Gтруб.
2. Задаемся расстоянием перевозок Кп, км.
3. Определяем величину перевозок на заданное расстояние Р=GКп, т х км
4. Находим суточную производительность машины, предварительно выбрав по каталогу автомашину и трубовоз:
Т – число часов работы в смену (8 часов),
v – техническая скорость автомашины по паспорту;
q - паспортная грузоподъемность
- коэффициент использования грузоподъемности
|
|
tпв – время простоя машины под погрузку и разгрузку за одну поездку 0,25 часа
b – количество смен работы, задаемся 1 или 2
- коэффициент использования пробега; если в паспорте нет указаний, то для автомашины,. Перевозящей железобетонные конструкции и арматуру принимается 0, 65, для трубопроводов – 0, 85
Qсутж/б=Qсутарм, т.к. используются одинаковые автомашины
5. Определяем количество автомобилей , шт
- количество дней работы (обусловлено продолжительностью монтажа), сут.
Т.к. для транспортирования железобетонных конструкций (ЖБК) и арматуры принимают одинаковые транспортные средства и Qсут равны, то в этом случае Р=Ржбк+Рарм
Подбор кранов
Подбор крана производят по вылету стрелы и грузоподъемности. Для укладки звеньев труб применяют два крана, для укладки конструкций колодцев – один.
Требуемая грузоподъемность крана:
, кг
Р1- вес 1п.м. трубы, кг
а – длина звена, м
n - количество автокранов, шт
Для определения грузоподъемности крана для укладки конструкций колодцев в числителе будет величина Р1- вес, кг, самого тяжелого из элементов конструкции.
Расчетный вылет стрелы:
, м
В – ширина траншеи (котлована) по верху, м
К1-половина расстояния между осями труб(учитывается только при двухтрубной прокладке газопроводов в траншее), м
|
|
К2 – расстояние от края траншеи до центра трубы, лежащей на бровке (1,7м) /от бровки до края трубы минимально 1-1,5м/, м
К3 – расстояние от трубы, лежащей на бровке траншеи до ближайшей опоры крана (минимально 1,0м принимаем 1, 65м), м
В – расстояние от боковых опор до оси вращения стрелы (по паспортным данным С/2, если не дано, принимаем 1,3-1,65м), м
С – ширина или длина крана по габариту зависит от положения крана, м
Определение опасной зоны работы крана
схема перемещения груза краном
1 – кран
2 – груз
3 – упавший груз
4 – временное ограждение
5 – знак безопасности опасная зона
, м
Rраз –радиус действия стрелы (радиус разгрузки), м
, м
Н – максимальная высота подъема груза, м, 4-5м
L – размер груза, м
Lстр - длина стропа, м
, м
В качестве кранов для укладки труб и элементов колодцев применяют краны на автомобильном ходу (автокраны) и на гусеничном (краны-трубоукладчики).
Автокраны имеют высокую скорость передвижения, а значит весьма мобильны. Их применяют на объектах с небольшими объемами работ и расположенными на больших расстояниях один от другого. Для укладки труб, как правило, используют гидравлические краны с жесткой подвеской рабочего оборудования. Для повышения транспортных свойств крана применяют шасси грузовых автомобилей повышенной проходимости (ЗИЛ, МАЗ, КрАЗ, КаМАЗ) Для увеличения опорного контура крана используют выносные опоры.
|
|
Табл. 3.67, 3.66 + рис. Стр386
Краны-трубоукладчики специально предназначены для подъема и укладки труб в траншею и могут выполнять различные подъемно-транспортные операции. В основном они изготовляются на базе гусеничных тракторов высокой проходимости, оснащены боковой стрелой с противовесом и не имеют поворотной платформы (являются неповоротными). Их можно эксплуатировать при температурах окружающей среды от -400С до +400С.
Табл. Технические характеристики кранов (т.3.67, 3.66)
Краны-трубоукладчики специально предназначены для укладки труб втраншею и могут выполнять различные подъемно-транспортные операции. В основном, все они изготавливаются на базе гусеничных тракторов высокой проходимости, оснащены боковой стрелой с противовесом и не имеют поворотной платформы (т.е., являются неповоротными). Их можно эксплуатировать при в диапазоне температу наружного воздуха -40…+400С.
Табл. Характеристики гусеничных кранов (т. 3.73)
Примечание. Трубоукладчики ТГ61 и ТГ62 не имеют откидного противовеса, что значительно сокращает их рабочий габарит и упрощает управление. ТГ62 оснащен умеренными гусеницами и способен работать на болотистых почвах и грунтах с пониженной несущей способностью.
Грузозахватные приспособления, применяемые при монтаже газопроводов
Легкие трубы (полиэтилен малого диаметра) укладывают с траншею вручную.
Для подвески плетей труб, железобетонных элементов конструкций колодцев к грузовому крюку монтажного крана используют различные грузозахватные приспособления. Они должны обеспечить:
1. необходимую грузоподъемность
2. прочность
3. простую и удобную строповку (надевание) и расстроповку (снятие) элементов
4. надежное закрепление (недопустимо их самопроизвольное раскрытие и отцепление груза
5. неповреждаемость трубы и ее изоляции
кольцевой или универсальный строп.
Он имеет вид кольца из отрезка троса, концы которого сплетены.
Диаметр и длину троса подбирают по диаметру и весу поднимаемых труб. Трос затягивают на трубе петлей. Тросы используют при монтаже труб, не имеющих изоляции и обладающих достаточной прочностью и жесткостью, а также при монтаже не кольцевых строительных конструкций, на одной стороне которых коуш, на другой может быть коуш, крюк или карабин.
Торцевые захваты.
Их защепляют за стенки труб с их торцов и с помощью отверстий в них обычными стропами крепятся к крюку. Их применяют только при погрузке и разгрузке труб.
МЯГКИЕ СТРОПЫ.
Их еще называют полотенца. Используют для монтажа изолированных труб чтобы не повредить изоляцию. Они распределяют усилия подъема на большую поверхность, в результате чего напряжения в изоляционном покрытии под полотенцем не превышают 1-2 кг/см2. Чаще всего используют полотенца из прорезиненной ленты. Оно имеет 4 троса по длине которых крепятся металлические башмаки, к которым приклепывают прорезиненную ленту шириной 60-70 см. и d=10-12 мм. Предназначено такое Полотенце для труб диаметром до 1000 мм.
Строповку трубопроводов производят в двух точках, после чего звено поднимают кранами на 0,7 м. от поверхности земли. Убедившись в надежности строповки и устойчивости механизмов, звено перемещают в проектное положение, изменяя вылет стрелы. Звено опускают плавно без рывков. После выверки положения звена на дне траншеи снимают стропы, передвигают краны и цикл повторяется.
Использование тех или иных строп должно быть обосновано типом груза и расчетами:
1 – звено трубопровода
2 – стропы
3 – канат трубоукладчика
Усилие в стропе: ,
Где Q-вес груза
m-количество строп
a-угол наклона строп (45°)
Разрывное усилие в стропе: ,
Где к- коэффициент запаса (4-6)
По найденным усилиям подбирают диаметр строп.
Техника безопасности при транспортных и погрузочно разгрузочных работах
Каждый автомобиль перед каждым выпуском на работу должен пройти технический осмотр для подтверждения его исправности .
Если грузы перевозят в сопровождении грузчиков, борта необходимо надежно закрепить, а рабочие должны находиться в безопасных местах. Стоять в кузове автомашины или сидеть на ее бортах запрещается.
Перевозимые грузы должны быть надежно закреплены.
Верхняя граница перевозимого груза не должна превышать габаритную высоту проездов ( переходы, мосты, туннели)
Площадки для погрузочных и разгрузочных работ должны быть спланированы и иметь уклон не более 5°. В зимнее время их надлежит регулярно очищать от снега и наледи, а также посыпать песком. Золой или шлаком.
При использовании грузоподъемных средств вес поднимаемого груза не должен превышать из грузоподъемности. Подтаскивать грузы подъемными механизмами запрещается.
Необходимо вести систематический контроль за исправностью и прочностью применяемых погрузочно-разгрузочных механизмов. Т.е. соблюдать сроки их испытаний и своевременно и качественно производить ремонт.
Перевозка грузов автопогрузчиками по строительной площадке разрешается только при ее ровном и плотном покрытии. Рама автопогрузчика должна быть отклонена назад, а высота подъема груза во время перевозки должна быть не более 30-40 см.
ЗАСЫПКА ТРАНШЕЙ И КОТЛОВАНОВ.
При засыпке уложенных в траншею трубопроводов газоснабжения сначала применяют ручной способ , а затем механизированный . Вручную засыпают пазухи между трубопроводами и стенками траншеи и трубопроводы сверху на высоту 20-30 см. Засыпка производится разрыхленным грунтом без примесей камней с его поэтапной утрамбовкой.
Засыпка пазух котлованов выполняется механическим способом.
Дальнейшую засыпку траншей (котлованов) со стенками без укреплений производят бульдозером. При засыпка с укрепленными стенками используют специальные машины – траншеезасыпатели ( для того чтобы полностью не разбирать крепления во избежание обвала стенок. Они могут работать «на себя» или «от себя». При этом грунт для засыпки забирается из отвала.
При засыпке траншей требуется уплотнить грунт так. Чтобы в последующем он не давал осадки. Для этого используют пневматические или электрические трамбовки или вибраторы (виброплиты). Они работают от передвижных компрессоров или передвижных электростанций. При этом глубина уплотнения составляет 0,4-0,75м. Если прокладка трубопроводов происходит в песчаных грунтах, то для его уплотнения требуется обильная поливка.
Расчет вибраторов стр. 182 « Справочник современного проектировщика»
ТЕХНИКА БЕЗОПАСНОСТИ ПРИ ЗЕМЛЯНЫХ РАБОТАХ.
До начала работ должны быть отмечены все подземные сооружения. В зонах подземных коммуникаций работы должны проводиться только с письменного разрешения курирующей их организации
Если на участке обнаружены подземные коммуникации не указанные в проекте, то работы необходимо приостановить до выяснения характера обнаружения.
Участки, разрабатываемые на улицах, проездах во дворах необходимо ограждать. Через траншеи должны быть установлены пешеходные мостики.
Состояние откосов и креплений необходимо проверять ежемесячно. Снимать крепления необходимо в присутствии производителя работ или мастера, снизу вверх по одной доске при слабых грунтах, по 2 и не более 3- при устойчивых грунтах.
При разработке выемок экскаватором запрещается находиться в зоне призмы обрушения и в радиусе действия стрелы плюс 5 м.
Отвалы грунта располагать не ближе 0,5м. от бровки выемки.
При погрузке грунта в автосамосвал не допускается прохождение ковша над кабиной.
В ночное время место работ должно освещаться и иметь предупреждающие фонари с красным светом.
В процессе выполнения работ производят освидетельствование и приемку видов работ, которые будут скрыты последующими видами (уплотнение грунта основания, устройство дренажей и пр.)
Кроме того производят проверку размеров котлована и траншеи , соответствие проекту грунта в основании и степень уплотнения грунта в процессе засыпки.
ПРОИЗВОДСТВО ЗЕМЛЯНЫХ РАБОТ.
Грунт, подлежащий разработке в зимних условиях , должен быть предварительно подготовлен. Подготовка заключается:
1. в предохранении от промерзания
2. в рыхлении мерзлого грунта
3. в оттаивании замерзшего грунта
предохранение грунта от промерзания
Для уменьшения глубины промерзания до наступления морозов выполняют следующие работы:
1. Отвод с участка поверхностных вод
2. Глубокая вспашка поверхностного слоя (30-35см.) с последующим боронованием. Наиболее эффективным является перекрестное рыхлении ев двух взаимно перпендикулярных направлениях на глубину не менее 35 см.Иногда грунт перед вспахиванием подвергают химической обработке, т.е. пропитывают верхний слой веществами понижающими температуру замерзания воды в грунте (до -35°С)
3. Укрытие дешевыми местными утепляющими материалами (опилки, мох, торф, сухие листья, солома, камыш и др.)
4. Установка снегозадерживающих барьеров.
РЫХЛЕНИЕ МЕРЗЛОГО ГРУНТА
Осуществляется (в случае, если своевременно не удалось предохранить грунт от промерзания) взрывным или механическим способом.
Взрывной способ применяется при глубине промерзания более 0,8 м на незастроенных участках, реже- на застроенных участках с использованием укрытий и локализаторов взрыва (тяжелых пригрузочных платформ). При рыхлении на глубину до 1,5 м. используют щелевой метод ( нарезают в грунте щели), при больших глубинах- скважинный. Щели или скважины располагают в шахматном порядке на расстоянии 0,9-1,5м. одна от другой. Затем их заряжают зарядами и сверху забивают песком, взрывают. Участок при этом делят на 3 захватки, размеры которых определяют исходя из сменной производительности экскаваторов. Табл.1
Разработка грунта экскаватором | Работы не ведут по Т.Б. | Бурение, зарядка, взрывание |
I | II | III |
Механический способ применяется при глубине промерзания до 0,8 м. и небольших по площади выемках котлованов и траншей. Для этого используют дизель-молоты (пробивают мерзлый грунт на глудину до 1.3м.) или врубовые машины (они делают прорези шириной 14 см. и глубиной до 2,1 м.), движущиеся в двух взаимно перпендикулярных направлениях. Далее разрыхленный или нарезанный грунт разрабатывают экскаватором.
ОТТАИВАНИЕ МЕРЗЛЫХ ГРУНТОВ.
Применяется при малых объемах работ, в стесненных условиях , в труднодоступных местах и когда нельзя использовать более экономичные и менее энергоемкие способы.
Способы оттаивания различны. Применение того или иного определяют исходя из технических возможностей, экономических соображений и местных условий.
Основной способ оттаивания открытыми кострами малоэффективен и неэкономичен. В городских условиях этот способ применяют в видоизмененном виде: по оси траншеи укладывают короб из металлических полутруб и с одного конца подают горящий факел (газовая горелка), а на другом конце устраивают дымовую трубу.
Оттаивание при помощи паровых игл производят при глубине промерзания грунта более1 м. Паровые иглы устанавливаются на расстоянии 1-2м. друг от друга в шахматном порядке. Паровые иглы устанавливают в заранее пробуренные скважины (h=1-2,5м), которые после закрывают колпаками (во избежание утечек пара через скважины). Паровые иглы применяют при траншей и небольших котлованов. Радиус действия одной иглы 0,5-1,5м. Между собой иглы соединяют гибкими шлангами, каждая игла имеет вентиль для ее выключения. Для питания игл применяются передвижные паровые котлы (р=0,5-0,7 ата). Продолжительность оттаивания в зависимости от типа грунтов составляет 2-6 часов (пески-глинистые грунты), процесс необходимо проводить с перерывами.
Наиболее экономичным является способ оттаивания грунта горячей водой с помощью водяных циркуляционных игл. Горячая вода циркулирует по игле с помощью насоса и возвращается в котел. Продолжительность оттаивания составляет 24 часа.
Оттаивание грунта естественной влажности производят способом электроподогрева переменным током напряжением 110,220 и 380В. При глубине промерзания до 0,7м применяют горизонтальные электроды:
1 – горизонтальные электроды
2 – опилки, смоченные соляным раствором
3 – провода
4 – толь или рубероид (2слоя)
5 – мерзлый грунт
Ток проходит через опилки, прогревает их. Опилки в свою очередь прогревают и оттаивают поверхность грунта. Оттаявший грунт является проводником, нагреваясь под действием тока передает тепло нижним слоям. Опилки теперь служат покрытием для удержания тепла в отогретом грунте.
При глубине промерзания более 0,7 м. применяют вертикальные глубинные электроды. Это стальные стержни диаметром 12-19мм с заостренным концом. Они забиваются на глубину ниже глубины промерзания на 8-10см. В этом случае процесс идет снизу вверх, окончание прогрева- появление проталин в снегу вокруг электродов, размером 5-15 см.
1 – вертикальные глубинные электроды
2 – провода
3 – талый грунт
4 – оттаявший грунт
5 – мерзлый грунт
6 - снег
Работу землеройных машин в зимнее время с подготовленным грунтом организовывают, как правило, круглосуточно во избежание промерзания грунта во время перерывов в работе. Днища траншей и котлованов необходимо предохранять от промерзания путем недобора в них грунта или укрытия из утеплителями. Зачистку основания выемок производят непосредственно перед укладкой трубопроводов или оснований колодцев.
Засыпка производится талым грунтом, чтобы не было последующей осадки. Или делают присыпку (20см) талым грунтом, а далее мерзлым, не содержащим комьев более 10 см.
техника безопасности при рыхлении
и оттаивании мерзлого грунта
При отогревании грунта необходимо принимать меры против ожогов рабочих.
При рыхлении грунта ударными приспособлениями рабочих необходимо снабжать защитными очками с небьющимися стеклами.
Участки производства работ по оттаиванию и рыхлению необходимо ограждать. При электроподогреве расстояние между ограждениями и границами подогреваемого участка должны быть не менее 3м.
Пребывание посторонних лиц на участке запрещается.
Временные линии электропередач прокладывают из изолированных проводов на козелках не менее 0,5м от земли. Исправность электрооборудования и изоляции проводов проверяют ежемесячно.
Разработку грунта на глубину промерзания разрешается вести с вертикальными стенками без креплений. Исключением является сухой песчаный грунт. Его разрабатывают с вертикальными стенками с креплениями или откосами. С наступлением весны особое внимание необходимо обращать на устойчивость откосов, а вертикальные стенки необходимо раскрепить.
СБОРКА И СВАРКА ТРУБ
Стальные трубопроводы в городских условиях прокладывают секциями, состоящими из 2,3,4 и более труб., а в полевых условиях в виде сплошной нити, длина которой может достигать нескольких сотен метров.
Секции труб или звенья соединяют на сварке. Вид сварки зависит от условия работ и диаметра свариваемых труб. На бровке траншеи трубы сваривают поворотным стыком, в траншее- неповоротным.
Сварка стальных труб включает в себя следующие технологические операции:
1. Подготовка труб и кромок их торцов к сборке;
Зачищают изоляцию (на 0,5м по обе стороны), очищают кромки и примыкающие к ним участки труб шириной по 10-15мм с внутренней и наружной стороны от грязи, ржавчины и масел до металлического
блеска. Выравнивают вмятины и неровности торцов, выправляют овальность, чтобы разность диаметров торцов не превышала 1-1,25% номинала. Толщина стенок соединяемых труб не должна иметь отклонения более 12-15% стандартного размера.
2. Раскладка труб на сварочных прокладках;
3. Центровка и стягивание труб до достижения между кромками торцов нужного зазора;
Раскладка труб перед сборкой должна способствовать их беспрепятственной и удобной центровке-совмещению геометрических осей и кромок труб рои строгом соблюдении нормативных зазоров. Для этого применяют специальные зажимы- центраторы. Они бывают наружные и внутренние. Благодаря синхронному действию разжимных кулачков центраторы автоматически обеспечивают калибровку и центровку торцов труб.
4. Скрепление собранного стыка сварочными прихватами;
Наложение коротких (прерывистых) однослойных сварочных швов по длине окружности стыка. Швы делают длиной 50-60мм теми же электродами и при тех же режимах сварки, которые будут применены при сварке стыка. Для труб диаметром 250-300мм делают 3 прихватки на равном расстоянии одна от другой, а для больших диаметров- швы располагают через 30-40 см по длине окружности. Затем швы прихваток очищают от шлака.
5. Сварка стыка
Сварку поворотных и неповоротных стыков труб при толщине стенок до 6 мм выполняют в два слоя, при толщине стенок от 6 до 12 мм- в 3 слоя и при толщине от 12 мм и более- в 4 слоя.
δ – толщина стенки трубы
А - зазор между кромками труб (1,5-3,5 мм, чем меньше δ, тем меньше А)
S - величина притупления кромок (1-2 мм)
α – угол скоса кромок (30-35)
р – допустимое смещение кромок труб (не более 25% от δ на участке не более ¼ длины окружности стыка)
h – величина усиления шва
1,2,3 – слои шва в порядке их наложения (корневой, заполняющий, облицовочный)
Неповоротные стыки начинают сваривать с нижней образующей трубы в 50-ти мм от вертикального диаметра труб. Трубы диаметром до 500 мм сваривают непрерывным швом, а трубы больших диаметров- прерывистым . Неповоротные стыки больших диаметров при необходимости ускорения производства работ сваривают одновременно 2 или 3 сварщика.
Так как ручная сварка неповоротных стыков очень трудоемка и времязатратна, то для этих целей при больших объемах применяют полуавтоматическую и автоматическую сварку с помощью сварочного автомата, состоящего из самоходной тележки, сварочной головки и пульта управления. В процессе сварки головка перемещается вокруг трубы по направляющему поясу и сваривает трубы электродной проволокой.
Для стальных труб чаще всего применяют следующие виды сварки:
1. Автоматическая сварка под слоем флюса. Применяется для соединения поворотных стыков труб диаметра 300 мм и выше. При сварке сварочная дуга окружена жидкой оболочкой расплавленного шлака, изолирующего расплавленный металл от влияния газов атмосферы. Под действием высокой температуры дуги плавятся как присадочный, так и основной металл трубы.
После удаления сварочной дуги шлак всплывает и кристаллизуется. Образуя стекловидную шлаковую корку, а металл образует сварочный шов. Данный вид сварки выполняется по заверенному корневому шву, выполненному ручным способом. При сварке труб толщиной 7-12мм число слоев (без корневого) должно быть не менее двух, а при толщине более 13 мм- не менее трех. При этом h должна быть не более 3 мм и не менее 1мм, В- не более 25 мм.
Электроснабжение сварочных установок как правило обеспечивают от передвижных генераторов с дизельными двигателями.
2. Автоматическая и полуавтоматическая сварка в среде углекислого газа (газоэлектрическая сварка)
Применяется для устройства поворотных и неповоротных стыков труб диаметром 300 мм и выше.
Суть данного вида сварки заключается в том, что электрическая дуга горит между электродной проволокой и свариваемым изделием в струе углекислого газа. Струю газа защищает расплавленный металл от вредного воздействия кислорода и азота воздуха.
Сварку в среде углекислого газа применяют для заварки всех слоев шва.
Электроснабжение установки обеспечивается передвижными генераторами или присоединением к существующим низковольтным электрическим сетям.
3. Стыковая контактная сварка труб.
Применяется для соединения труб диаметром 150-500мм.
Сущность этого вида сварки заключается в том, что свариваемые концы труб нагревают специальным кольцевым трансформатором и затем их прижимают друг к другу, благодаря чему концы труб сращиваются. Для этого используют специальную передвижную контактно-сварочную установку, которую обслуживают 10 человек, ее производительность 5-6 стыков/час.
4. Ручная электродуговая сварка.
Применяется для соединения поворотных и неповоротных стыков труб диаметром от 100 мм, в случаях, когда газоэлектрическая сварка по каким-либо причинам не может быть использована.
5. Ацетиленовая газовая сварка.
Допускается для соединения труб диаметром не более 100мм при толщине стенки не более 5 мм.
Для газовой сварки и резки труб и других металлоконструкций необходим кислород и ацетилен. Их потребность определяется по нормативному расходу.
Расход кислорода при сварке ориентировочно можно принять 800л/час на одного сварщика, а при резке- 20 м³ на 1 тонну металла.
Расход ацетилена при сварке определяется по формуле:
, м³/мин,
Где S-толщина свариваемого металла, мм
Потребность в баллонах кислорода или ацетилена в смену ориентировочно определяется по формулам:
шт;
шт
Кислород поставляется в стальных, окрашенных в голубой цвет баллонах под давлением 15±0,5МПа. На баллоне черной краской наносят надпись «кислород». На каждом баллоне выбивается дата его следующего испытания, которое проводится каждые 3 года.
Транспортировать баллоны надо отдельно от других материалов на специальных подкладках с предохранением от загрязнения маслами и жирами (во избежание взрыва). При замерзании головок кислородных баллонов отогрев можно производить только водой или паром.
Ацетилен поставляют и транспортируют в стальных баллонах с давлением при температуре +20◦С не более 1,9 МПа. Баллон окрашивается в белый цвет с красной надписью «ацетилен».
Хранить баллоны с кислородом и ацетиленом необходимо в вертикальном положении закрепленными и защищенными от прямого действия солнечных лучей.
На трассе хранение подлежит организовывать в переносных запираемых металлических кожухах или шкафах, исключая доступ к ним посторонних лиц.
Полиэтиленовые трубы доставляют на место и раскладывают вдоль траншеи непосредственно перед сваркой и укладкой. Перед сваркой трубы и фасонные части очищают от пыли и других загрязнений. В зимнее время ПЭ трубы разрешается сваривать при температуре воздуха не ниже -15◦С.
Сварка полиэтиленовых труб чаще всего контактная:
-стыковая (осуществляется встык)
-раструбная (в раструб с литыми фасонными частями и в формовочный раструб)
При стыковой сварке максимальное несовпадение кромок не должно превышать 10% толщины стенки. Концы труб при раструбной сварке должны иметь наружную фаску под углом 45◦.
Сварка осуществляется в следующей последовательности:
1. Установка и центрирование труб в зажимном центрирующем приспособлении;
2. Торцовка труб и обезжиривание торцов;
3. Нагрев и оплавление свариваемых поверхностей;
4. Удаление сварочного нагревателя;
5. Соединение разогретых свариваемых торцов труб под давлением (осадка);
6. Охлаждение сварочного шва под осевой нагрузкой.
Для получения прочных и качественных стыков труб необходимо строго соблюдать основные параметры сварки:
- температуру и продолжительность прогрева
- глубину оплавления
-контактное давление при оплавлении и осадке
Укладывать плеть в траншею допускается не ранее чес через 2 часа после сварки последнего стыка.
ИЗОЛЯЦИОННЫЕ РАБОТЫ.
Изоляционные работы сводятся к изоляции стыков стальных газопроводов, так как сами газопроводы на место монтажа поставляются уже с заводской изоляцией.
Данный вид работ выполняют после сварки стыков и предварительного испытания газопроводов. При этом выполняют следующие операции:
1) просушка
2)очистка
3)обезжиривание
4)грунтовка
5)нанесение изоляции
6)оклейка крафт бумагой или нанесение рулонного оберточного материала.
Просушку производят если антикоррозийное покрытие наносят в ненастную погоду.
Очистку выполняют вручную металлическими щетками, обезжиривание- бензином.
Грунтовку производят сразу после обезжиривания, чтобы труба не покрылась ржавчиной вследствие воздушной коррозии и осадков. Её назначение- обеспечить прочное сцепление первого слоя изоляции с трубой.
Далее наносят битумную мастику в горячем виде (170-180◦С), поливая поверхность стыка из шланга от насоса котла и растирая снизу полотенцем.
Рулонным материалом стыки обертывают по горячему битуму с нахлесткой витков 2-3 см.
Операции 5) и 6) повторяются такое количество раз. Какое предусмотрено типом изоляции ( нормальная, усиленная, весьма усиленная)
При изоляции сварных стыков трубопроводов больших диаметров работы производят механизировано. Каждая из установок, последовательно выполняющих изоляционные операции, поддерживается и перемещается от стыка к стыку трубоукладчиком.
Если в качестве изоляции используют липкие ленты, то их накладывают на свежую (не высохшую) грунтовку специальными машинами в два слоя за один подход. Подъем и поддержание трубопровода для изоляции липкими лентами производится также как и при битумной изоляции. Нанесение следует производить при температуре воздуха не ниже -40◦С. При температуре воздуха ниже +10◦С рулоны, ленты и обертки необходимо выдержать не менее 48 часов в теплом помещении при температуре не ниже +15◦С (но не выше +45◦С). При температуре воздуха ниже +3◦С поверхность изолируемого трубопровода надо подогревать до температуры не ниже +15◦С(но не выше +50◦С).
МОНТАЖ АРМАТУРЫ
Перед монтажом арматуры производят ее ревизию. Арматуру устанавливают таким образом, чтобы к ней был обеспечен свободный доступ во время эксплуатации и ремонта. Места установки арматуры на трассе должны полностью предохраняться от восприятия каких-либо изгибающих усилий. На параллельных газопроводах арматуру необходимо смещать относительно друг друга. На вводах в ГРП отключающее устройство необходимо устанавливать не ближе 5м. и не дальше 100м от ГРП.
При последовательной установке задвижек и линзовых (сильфонных) компенсаторов сначала их соединяют в общий блок, скрепляя на фланцах. Затем арматуру устанавливают на место, центруют с трубопроводом. Производят точную инструментальную проверку правильности ее установки и совпадения осей. Далее к арматуре с двух сторон присоединяют патрубки, сболчивая фланцевые соединения с установкой прокладок.
Подтяжку труб и стыковку их с патрубками производят с двух сторон, после чего сваривают последние стыки. При этом фланцы на трубопроводе устанавливают без перекосов и при полном совпадении болтовых отверстий с отверстиями во фланцах задвижек. Болты заворачивают нормальным гаечным ключом, не допуская сильной затяжки.
На трубопроводах при надземной прокладке устанавливают задвижки и П-образные компенсаторы. Компенсаторы на трассу завозят собранными и соединяют с трубопроводом посредством сварки.
На место стыковки компенсатор устанавливают краном на опоры и прихватывают сваркой с обеих сторон, предварительно выверив совпадение осей. Растяжку компенсатора при его установке перед сваркой не производят. Сопряжение компенсатора с трубопроводом должно быть прямолинейным без перекосов.
Компенсатор устанавливают так, чтобы ось его симметрии была сдвинута от рабочего положения на ¼ часть компенсирующей способности в сторону той опоры трубопровода, между которой и компенсатором все стыки уже сварены. Для растяжки компенсатора у другой опоры оставляют не сваренный стык, причем расстояние между кромками стыка берется равным проектной величине растяжки компенсатора.
Все остальные стыки на трубопроводе между опорами должны быть сварены. На оба конца несваренного стыка приваривают фланцы с отверстиями для стяжных болтов. Подтягиванием стяжных болтов сближают кромки труб несваренного стыка до пределов, необходимых для сварки, после чего этот стык сваривают.
Разъемные соединения полиэтиленовых труб, их соединение с металлической арматурой и газопроводами осуществляют с помощью фланцев, устанавливаемых в колодцах. Лучшие характеристики для этих целей имеют фланцевые соединения заклинивающего типа (рис.), при этом технология соединения та же, что и при использовании стальных трубопроводов.
1 – соединяемые трубы
2 – конические фланцы
3 – уплотнительное кольцо
4 – соединительные болты
БЕТОННЫЕ, ЖЕЛЕЗОБЕТОННЫЕ РАБОТЫ
И КИРПИЧНАЯ КЛАДКА
Монолитный бетон или железобетон применяется для устройства оснований и днищ колодцев, а также в фундаментах железобетонных оснований опор при надземной прокладке газопроводов.
Арматура для железобетонных конструкций изготавливается предварительно в арматурном цехе или заготовительных мастерских в виде арматурных сеток, каркасов или укрепленных элементов из стержней, транспортабельных и удобных для сборки на месте.
Опалубка для колодцев и оснований опор должна быть инвентарной. Она изготавливается в виде отдельных съемных щитов и может быть многократно использована. Также изготавливают и поддерживающие конструкции и крепления для опалубки. Для заготовки опалубки применяются строганные пиломатериалы хвойных или лиственных пород с влажностью не более 25%. Возможно бетонирование железобетонных колодцев и оснований опор в опалубке из мелкоячеистой металлической сетки с использованием бетононасосов.
В плотных грунтах днища и стенки колодцев могут бетонироваться без наружной опалубки (враспор с грунтом) при условии соблюдения проектных размеров бетонирующих изделий.
При установке арматуры сборке опалубки следует обратить особое внимание на правильное расположение арматуры и обеспечение защитного слоя бетона арматуры, а также на сохранение устойчивости арматурных каркасов и сетки от смещения их во время укладки бетонной смеси и уплотнения вибраторами.
Бетонирование стен, перекрытий колодцев, оснований опор производится товарной бетонной смесью, получаемой от бетонных заводов. Марка заказываемого бетона принимается не менее проектной.
Бетон перевозится к месту укладки в автобетоновозах и автосамосвалах. Зимой самосвалы должны иметь утепление и обогрев отходящими газами. Разгрузка бетона производится от самосвала в 2-4 бадьи, установленные в один ряд. Бадьи с помощью автокрана подаются к месту укладки бетона.
Укладка бетонной смеси должна производиться без больших перерывов в работе. В жаркую солнечную погоду уложенный бетон должен немедленно укрываться, а в зимнее время утепляться. Во время дождя бетонируемая конструкция должна быть защищена от воды; случайно размытый бетон должен быть удален. При перерывах, превышающих установленные сроки схватывания бетонной смеси, поверхность уложенного бетона должна быть очищена от грязи и цементной пленки с промывкой водой, оставшаяся на поверхности вода должна быть удалена. Немедленно после укладки бетонной смеси она должна быть уплотнена вибраторами: в днищах- поверхностными, в стенах и массивах опор- глубинными. В местах, где расположение арматуры и опалубки не позволяет в достаточной степени уплотнить бетон вибраторами, его следует дополнительно проработать штыкованием. Снятие опалубки с железобетонных конструкций допускается только после достижения бетоном нормируемых показателей прочности.
Выдерживание бетона в зимних условиях производится в тепляках с обогревом его паром, горячими газами, электрообогревом и по методу «горячего термоса»: этот способ основан на укладке бетона в утепленную опалубку, где его температура повышается за счет тепла подогретых составляющих и тепла, выделяемого цементом в процессе его схватывания и твердения. При этом хорошо укрытый бетон остывает настолько медленно, что успевает набрать критическую прочность до замерзания. Кроме того, используют способы бетонирования без подогрева с применением противоморозных добавок. Во всех случаях к моменту остывания бетона ниже температуры замерзания раствора его прочность должна быть не ниже 25% от марочной прочности.
Кроме бетонирования на месте для устройства газовых колодцев используют сборные бетонные и ж/б изделия. До монтажа ж/б конструкций их очищают от грязи, снега, наледи. Плавно, без рывков и раскачивания на высоту 0,3-0,5м от поверхности земли поднимают изделия автокраном , перемещают и опускают в проектное положение. Устанавливают их плавно без толчков и ударов. Стропы снимают после окончания рихтовки и выверки правильности установки. Вертикальные и горизонтальные швы между конструкциями заделывают цементным раствором.
Кирпичная кладка применяется для сооружения стен колодцев, а также для устройства защитного слоя изоляции.
Каменная кладка ниже уровня грунтовых вод, а также во влажных и водонасыщенных грунтах производится на гидравлических растворах. Горизонтальные и поперечные вертикальные швы кирпичной кладки стен должны быть целиком заполнены раствором.
Кирпич на цементном растворе в зимних условиях укладывается замораживанием при последующем естественном оттаивании или применяется раствор с противоморозными добавками, а также прогрев кладки.
В сухую жаркую погоду и при ветре кирпич нужно увлажнять. Кладки подземных сооружений можно предохранять от быстрого охлаждения засыпкой талым грунтом или укрытием теплоизоляционными материалами (минераловатными матами и плитами).
ИСПЫТАНИЕ ГАЗОПРОВОДОВ
Испытание газопроводов проводится дважды:
1. Сразу после монтажа (на прочность) трубопроводов в траншее
2. После засыпки и выдержки его 12 часов (на герметичность)
В обоих случаях испытание проводят пневматическим способом.
Расчет потребности сжатого воздуха для этих целей производится по формуле:
, м3/мин,
Где dв- наибольший внутренний диаметр испытываемых труб, м
Ри- испытательное давление, принимаемое по СНиП, кгс/см2
l- длина трубопроводов, испытываемых в смену, м.
Для предварительных испытаний- на прочность: Табл.2
Рг/пр | Ри, кгс/см2 |
низкое | 1 |
среднее | 4,5 |
высокое | 7,5 |
Для окончательных испытаний- на герметичность: Табл.3
Рг/пр | Ри, кгс/см2 |
низкое | 3.-6. |
среднее | 6.-15. |
высокое | 7,5-12 |
Кроме того, сжатый воздух может потребоваться для технологических процессов, расход на которые (Qпр) определяется по таблице 4:
Расход воздуха пневматическими инструментами. Табл.4
Наименование инструмента | Параметры воздуха | |
давление кгс/см2 | расход, м3/мин | |
отбойный молоток (ОМСП-5) | 4. | 1 |
Щетка для зачиски кромок труб под сварку | 4.-5. | 2,2 |
Шлифовальная машина для зачистки швов (И-44) | 5.-6. | 1 |
Сверлильная машина (И-344) | 5.-6. | 2,2 |
Вибратор глубинный (ВР) | 5. | 1,4 |
Пневмотрамбовка (И-157) | 6. | 1,2 |
В качестве источника сжатого воздуха используются передвижные компрессорные станции, которые подбираются по производительности. (по табл.)
Расчетная производительность компрессорной установки равна:
, м3/мин,
РАСЧЕТ ВРЕМЕННОГО СТРОИТЕЛЬНОГО ХОЗЯЙСТВА
При строительстве сооружений, имеющих линейный характер (магистральных трубопроводов, дорог и пр.), рекомендуется предусматривать временные сооружения (конторы, склады, мастерские, столовые и др.). В целях сокращения затрат на их строительство проектными организациями разработан ряд типовых проектов сборно-разборных, переносимых и передвижных временных сооружений, которые могут быть многократно использованы на разных стройках.
На крупных строительных площадках с длительным сроком строительства обычно применяют инвентарные типовые сборно-разборные временные административно-хозяйственные сооружения различных назначений и размеров.
При строительстве трубопроводов рекомендуется использовать передвижные инвентарные временные сооружения типа вагонов, которые устанавливают на полосе отчуждения трассы трубопровода и передвигают по ходу строительства.
Вагоны устанавливают с противопожарными разрывами между ними и располагают так, чтобы в случае пожара любой вагон можно было откатить от рядом стоящих. На всех вагонах с внешней стороны вешают огнетушители. Внутреннее освещение и отопление вагонов обычно электрическое. При отсутствии постоянной электросети используют временные передвижные электростанции. Если есть возможность использовать сжиженные углеводородные газы (СУГ) в баллонах, то в вагонах устанавливается соответствующие оборудование.
Склады
Площадь склада зависит от вида, способа хранения материалов и их количества.
Площадь склада складывается из полезной площади, занятой непосредственно под хранение материалов, вспомогательной и отпускной площади. Общая площадь склада определяется по формуле:
, м2, где
k- коэффициент, учитывающий проходы, проезды (принимают k=1,5)
Fтр- требуемая площадь склада, м2
, м2, где
Р- запас материалов для хранения (в зависимости от материалов в м2, м3, шт., т.)
Ки- коэффициент использования площади склада, принимается в зависимости от вида склада:
- для закрытых складов 0,5-0,7
- для навесов 0,5-0,6
- для открытых складов 0,6-0,8
q- норма хранения материалов на 1м2 площади склада (табл5.)
Нормы хранения материалов. Табл.5
Наименование материалов | Един. Измерения | Норма складирования на 1м2 | Высота укладки, м | Способ укладки | Способ хранения |
Песок, щебень, гравий | м3 | 1,5-2. | 1,5-2. | штабель | открытый |
Кирпич строительный | тыс.шт. | 0,7 | 1,5 | клетки | открытый |
Ж/б элементы газовых колодцев | м2 | 1,2-1,8 | 2.-3. | штабель | открытый |
Блоки газовых колодцев | м3 | 2.-2,5 | 2,5-3. | штабель | открытый |
Арматура стальная и чугунная | т. | 1,6-1,8 | 2,2 | стеллаж | закрытый |
Трубы стальные крупных диаметров | т. | 0,5-0,8 | 1,2 | штабель | открытый |
Трубы стальныемелких диаметров | т | 1,5-1,7 | 2 | штабель | открытый |
Трубы ПЭ | т | 1.0-1,3 | 1,5-2. | штабель | под навесом, закрытый |
Битум нефтяной | т | 2 | 1,5 | бочки, емкости | под навесом |
Бензин | т | 0,5-0,7 | 1,3 | бочки. | закрытый |
Временные здания и сооружения.
К числу обязательных временных сооружений относятся кладовые, контора прораба, гардеробные, пункты питания, уборные. Определив перечень необходимых зданий и сооружений, производят расчет их площади по максимальному числу рабочих в смену, принимаемое по графику движения рабочих с учетом рабочих, занятых на неосновном производстве (24%), неучтенных работах (10%) и ИТР (1ИТР на 20 раб.). Временные здания и сооружения следует предусматривать в минимальном объеме. (табл. 6)
Нормы площадей временных зданий Табл.6
№п/п | Наименование и назначение помещений | Наименование показателей | ед. измер. | Норма |
1 | Контора прораба | площадь на одного чел. ИТР | м2 | 3.-3,25 |
2 | Материальный склад- предназначен для хранения различного инструмента и штучных материалов, необходимых для производства строительных работ. Имеет 3 помещения: 1- для кладовщика (3,2 м2); 2- для складирования инструмента (7,22 м2); 3- тамбур для приема и выдачи инструментов и материалов (18м2) | Площадь склада | м2 | 28,42 |
3 | Мастерская- предназначена для слесарно-механических и электротехнических работ и имеет следующие помещения: 1- электромастерская (3 м2); 2- инструментальная (3 м2); 3- помещение для станков и верстаков, 4- тамбур (1,3м2). Мастерская оборудована токарно-винторезным станком, слесарным верстаком на 2 рабочих места, верстаком с ручными ножницами , точильным и сверлильным станками. Для выполнения несложных кузнечных работ мастерская имеет наковальню и выносной горн. Оборудование мастерской может быть другим в зависимости от вида работ | Площадь вагона-мастерской | м2 | 19,78 |
4 | Умывальная и гардероб- организуется в вагончике, состоящем из двух отделений: гардеробная со шкафчиками для одежды и умывальная с двумя раковинами | Площадь на 1 рабочего | м2 | 0,4-0,5 |
5 | Помещения для приема пищи ) площадь 1 вагона-столовой составляет 19,78 м2) | Площадь на 1 рабочего | м2 | 1.-1,2 |
6 | Вагон- кухня- используется для подогрева на электропечах пищи, доставляемой в специальных бачках- контейнерах. Устанавливают его рядом с вагоном-столовой. Использование двух вагонов- столовых при одном вагоне- кухне при затрате времени на обед 30 мин позволяет в течение часа обслужить более 100 чел. | Общая 1 вагона | м2 | 19,78 |
7 | Душевые- устанавливаются при наличии вблизи трассы прокладываемого трубопровода существующей сети водопровода и канализации. Как правило используют вагон- душевую на 4 рожка с двумя изолированными отделениями- мужским и женским | Число чел на 1 душ. Площадь одного душа | чел, м2 | 10-20; 3.-3,5 |
8 | Уборные- используют либо вагон- уборную с выпуском сточной воды в люк канализационного колодца (при его наличии), либо биоуборные | Число рабочих на 1 унитаз. Площадь 1 унитаза | чел, м2 | 15-20; 2,6.-3. |
9 | Помещение для сушки одежды- позволяет сушить спецодежду, включая и обувь при производстве работ в сырых условиях | Площадь на 1 рабочего | м2 | 0,2 |
10 | Помещение для обогрева рабочих. Как правило размещают в одном вагоне с конторой прораба | Площадь на 1 рабочего | м2 | 0,1 |
Потребность в электроэнергии
Определяется на основании данных о потреблении энергии машинами и механизмами и необходимой мощности на нужды освещения ( при работе в ночное время).
Общая потребляемая мощность определяется по формуле:
, КВт, где
- мощность силовая, КВт. Принимается по техническим характеристикам механизмов и машин из соответствующих справочников.
- мощность устройств освещения, КВт. Принимается в соответствии с (табл.7)
K1 и K2- коэффициенты одновременности потребления
K1=0,75; K2=1,0
Ориентировочная потребная мощность
для электроосвещения Табл.7
Наименование потребителя | ед. измер. | Средняя освещенность, люкс | Удельная мощность, Вт |
Производство механизированных земляных, бетонных и каменных работ | м2 | 5. | 0,8 |
Монтаж стальных и ж/б конструкций, сварка труб | м2 | 15 | 2,4 |
Освещение проходов и проездов | км | 0,2 | 2500 |
Охранное освещение | км | 0,1 | 2000 |
Внутреннее освещение: механических мастерских административных и бытовых помещений закрытых складов | м2 м2 м2 | 50 50 50 | 18 15 3 |
При суммарном расходе энергии до 20 КВт следует проектировать присоединение к существующим (городским, поселковым) низковольтным электрическим сетям. При большей потребляемой мощности необходимо предусматривать установку трансформатора.
Для ночного освещения места производства работ применяют прожектора, чаще всего ПЗС-45. Прожектора устанавливают на мачтах высотой 25м.
Потребное количество прожекторов:
, шт., где
Р- удельная мощность, принимается 0,25 Вт/м2лк
Е- освещенность, лк (принимается по табл.7)
У- освещаемая поверхность, м2
Рл- мощность лампы (для прожектора ПЗС-45 Рл=1500 Вт)
Потребность в воде
Временный водопровод рассчитывается по максимальному суточному расходу по группам потребителей:
, м3/с, где
- потребность в воде для производственных нужд, м3/с
- потребность в воде на хозяйственно- бытовые нужды, м3/с
- потребность в воде на пожарные нужды, м3/с
, л/с, где
1,2- коэффициент на неучтенные расходы
Qср- средний производственный расход воды в смену, л. Определяется по таблице 8 с учетом количества машин и механизмов, работающих в смену
К1- коэффициент неравномерности потребления воды в смену, принимается равным 2.
, л/с, где
np- наибольшее количество рабочих в смену, чел
n1- норма потребления воды на 1 человека в смену, л. ( определяется по табл.8)
n2- норма потребления воды на прием душа, л. ( определяется по табл.8)
к2- коэффициент неравномерности потребления ( принимается 2,7)
к3- коэффициент, учитывающий отношение рабочих, пользующихся душем к наибольшему количеству работающих в смену ( принимается 0,3)
л/с
, м3/с
По расчетному расходу вычисляется диаметр труб временного водопровода:
, м
Нормы расхода воды.Табл.8
Наименование потребителя | ед. измер. | Расход, л |
Трубовозы, автосамосвалы, грузовые автомобили | маш.-см. | 100. |
Экскаваторы с двигателем внуиреннего сгорания, бульдозеры | маш.-см. | 10-100 |
Автокраны | маш.-см. | 12.-15. |
Трубоукладчики | маш.-см. | 150-300 |
Компрессоры | 1 м3 воздуха | 5.-10. |
Хозяйственно-питьевой расход: а) при наличии канализации б)при отсутствии канализации в) прием душа | на 1 чел в смену на 1 чел в смену на 1 чел в смену | 25 15 30 |
Бестраншейная прокладка трубопроводов.
На пути прокладки трубопроводов как в полевых, так и в городских условиях часто встречаются естественные и искусственные препятствия. Для их преодоления требуются особые устройства, а прокладку производят методами, отличающимися от обычных.
Для преодоления естественных препятствий (оврагов, балок, водоемов) сооружаются воздушные переходы и дюкеры.
Прокладку трубопроводов под искусственными препятствиями (железные и автомобильные дороги, трамвайные пути, проезды с усовершенствованными дорожными покрытиями и др.) производят обычно бестраншейными (закрытыми) способами работ. К ним относятся:
- прокол
-продавливание
-горизонтальное бурение (ГНБ,ННБ)
-вибровакуумная проходка
Если по условиям работ эти способы применить не возможно (диаметр трубопровода более 1200-1400мм), применяют метод щитовой прокладки.
Прокладка трубопровода бестраншейными способами состоит из следующих процессов:
1. устройство горизонтальной скважины
2. прокладка обсадной трубы (футляра)
3. прокладка рабочей трубы (в футляре)
Для футляров применяют изолированные стальные трубы:
бесшовные горячекатаные (только для трубопроводов диаметром до 273мм)
сварные прямо- или спирально-шовные с толщиной стенки на 15-25% более толщины стенки основного трубопровода
Диаметр защитных кожухов (футляров) должен быть больше, чем диаметр прокладываемого трубопровода. Табл.9
Требуемые диаметр и толщина стенок
защитного кожуха (футляра) Табл.9
Наружный диаметр,мм | Толщина стенки защитного кожуха, мм | |||
рабочего трубопровода | Защитного кожуха | Открытом | Бестраншйном | |
Горизонтальное бурение | Продавливание или прокол | |||
159 | 325 | 8 | 8 | 9 |
219 | 377 | 9 | 9 | 10 |
273 | 426 | 9 | 9 | 11 |
325 | 530 | 9 | 9 | 12 |
426 | 630 | 10 | 10 | 12 |
530 | 720 | 10 | 10 | 12 |
630 | 820 | 10 | 10 | 12 |
720 | 920 | 10 | 10 | 12 |
820 | 1020 | 10 | 11 | 14 |
920 | 1220 | 10 | 11 | 14 |
1020 | 1220 | 10 | 11 | 14 |
1220 | 1420 | 11 | 12 | 14 |
1420 | 1720 | 16 | 16 | 16 |
Длина кожуха определяется исходя из ширины дорожного полотна и рекомендуемых нормативных расстояний выхода кожуха за его пределы.
Рабочие трубы диаметром до 300-400 мм, прокладываемые под водоемами, оврагами методом бестраншейного заглубления, можно устраивать без футляров в связных грунтах.
Для устройства перехода бестраншейным способом с обеих его сторон разрывают два котлована: один рабочий (опорный), в котором устанавливают оборудование для производства проходки, а второй- смотровой (улавливающий). Рабочий котлован всегда располагают в нижней точке перехода, и проходку ведут против уклона, т.е. снизу вверх (для облегчения производства работ).
Все указанные бестраншейные способы работ применимы как в грунтах с естественной влажностью, так и в водоносных. Однако при работе в водоносных грунтах открытый водоотлив (откачка протекающей воды непосредственно из котлована) практически невозможно осуществить, и поэтому в них производят искусственное понижение уровня грунтовых вод, что обеспечивает работу в забое «насухо».
искусственное понижение уровня
грунтовых вод
Способ водопонижения и тип применяемого для этого оборудования выбирают в зависимости от глубины разработки котлована, геологических и гидрогеологических условий площадки. ( Табл.10)
Выбор способов водопонижения. Табл. 10
Характеристика грунта | Коэф. фильтрации к, м/сут | Рекомендуемые способы водопонижения при глубине понижения уровня грунтовых вод, м | ||
до 4.-5. | до 18-20 | свыше 20 | ||
глина | - | электроосушение | ||
суглинок | 0,005-0,4 | Одноярусные легкие иглофильтровые установки (ЛИУ) и эжекторные иглофильтры | Многоярусные ЛИУ и эжекторные иглофильтры | - |
супеси | 0,2-0,7 | |||
Песок мелкозернистый мелкий средний крупный гравистый | 1,2-2,0 2,0-10,0 10,5-25,0 25,0-75,0 50-100 | Одноярусные ЛИУ | Многоярусные ЛИУ и эжекторные иглофильтры | Буровые колодцы с артезианскими погружными насосами |
Буровые скважины с центробежными насосами | - | |||
гравий: с песком чистый | 75-150 100-200 | Поверхностный водоотлив | Буровые скважины с погружными насосами |
Иглофильтровый способ предусматривает использование для откачки воды из грунта часто расположенных скважин с трубчатыми водоприемниками малого диаметра- иглофильтрами, соединенных общим всасывающим коллектором с насосами.
Схемы установки иглофильтров
а) одноярусная установка
1 – иглофильтры
2 – всасывающий коллектор
3 – насосы
4 – котлован
1 – нормальный уровень грунтовых вод
2 – гибкий шланг
3 – коллектор
4 – насос
5 – надфильтр
6 – пониженный уровень грунтовых вод
7 – фильтровое звено
б) многоярусная установка
Сначала вводят в действие первый ярус иглофильтров и под его защитой открывают верхний уступ котлована. Затем монтируют второй ярус иглофильтров и открывают второй уступ котлована и т.д.
1 – коллектор 1-го яруса
2 – коллектор 2-го яруса
3 – иглофильтр 1-го яруса
4 – иглофильтр 2-го яруса
5 – нормальный уровень грунтовых вод
6 – пониженный уровень грунтовых вод
Иглофильтры погружают гидравлическим способом:
1 – иглофильтры поднимают краном в вертикальное положение
2 – подают через иглофильтр воду с большой скоростью
3 – вода размывает грунт, образуя скважину
4 – в скважину опускают иглофильтр
Эжекторные иглофильтровые установки откачивают воду из скважин с помощью водоструйных насосов- эжекторов, работающих по принципу передачи энергии одним потоком воды другому.
1 – эжекторный игофильтр
2 – соединительный шланг
3 – распределительный трубопровод
4 – циркуляционный резервуар
5 – высоконапорный насос
6 – сливной лоток
7 – низконапорный насос
Принципиальная схема устройства иглофильтра:
1 – напорна вода
2 – сопло
3 – всасываемая вода
4 – обратный клапан
5 – фильтровая сетка
Погружают такие иглофильтры гидравлическим способом. Расстояние между ними 5-15м.
Электроосушение, заключается в отсасывании воды из грунта действием электроосматических сил, возникающих при пропускании через грунт постоянного электрического тока. Под действием электрического тока вода, содержащаяся в порах грунта перемещается в направлении от анода (-) к катоду (+).
Катодами служат иглофильтры. Их устанавливают по периметру котлована на расстоянии 1,5 м. от его бровки и 1,2 м. друг от друга с погружением из в грунт на глубину не менее 3 м. ниже проектного уровня понижения грунтовых вод.
В качестве анодов служат стальные стержни или старые газовые трубы, которые забивают в грунт тоже по периметру котлована на расстоянии 0,7 м. друг от друга в шахматном порядке по отношению к иглофильтрам. Глубина погружения анодов такая же, что и для иглофильтров, но верхняя их часть должна быть на 0,2-0,4 м выше поверхности земли для соединения их между собой проводами. Иглофильтры тоже соединяют между собой проводами и обе цепи проводовподключают к генератору постоянного тока с напряжением 40-60 В. В результате усиленного движения грунтовых вод в направлении иглофильтров, достигается осушение грунта.
1 – всасывающий коллектор
2 – иглофильтры (катод)
3 – труба диаметром 38 мм (анод)
4 – провод
5 – нормальный УГВ
6 – УГВ после осушения
7 – генератор
8 – насос
9 - водосброс
Электроосушение должно быть начато за 3-5 дней до начала земляных работ. В песчаных грунтах этот способ не дает эффекта. Т.к. песок имеет достаточно высокий коэффициент фильтрации.
Вакуумный способ водопонижения, при котором в зоне иглофильтров создается устойчивый вакуум, применяют для осушения мелкозернистых грунтов (пылевых и глинистых песков, супесей, легких суглинков, илов, лёссов), имеющих малые коэффициенты фильтрации. Для создания во всасывающем коллекторе устойчивого вакуума применяют водовоздушный эжектор, а для откачки воды- водоводяной эжектор. Они питаются рабочей водой, поступающей от центробежного насоса.
Открытые (соединяющиеся с атмосферой) водопонизительные скважины, оборудованные насосами, применяют в случаях:
1) требуются большие глубины понижения УГВ
2) затруднено использование иглофильтров из-за больших притоков
3) осушение больших площадей
4) стесненность территории
Основными конструктивным элементом скважины колодца является фильтровая колонна, внутри которой размещен насос (глубинный погружного типа или артезианский турбинный):
1 – фильтр-отстойник
2 – надфильтровая труба
3 – насосный агрегат
4 – песчано-гравийная подсыпка
5 – местный песчаный грунт
6 – пьезометр для замера
7 – то же в обсыпке
Количество насосов для откачки воды при понижении УГВ определяют в зависимости от притока воды к установке и количества присоединенных к ней иглофильтров. Откачку воды при водопонижении ведут непрерывно в течение всего времени производства работ. Во избежание перерывов в работе насосов и затопления выемок грунтовой водой необходимо иметь аварийные резервные насосы и два ввода электроэнергии от разных источников питания.
Основными требованиями при производстве работ является сохранение плотности грунта в основании сооружения и в самом водоносном слое . Вынос частиц грунта может вызвать в нем осадочные явления, поэтому в откачиваемой воде не должно быть частиц грунта.
После окончания работ иглофильтры и фильтровую колонну извлекают из грунта при помощи крана, тали или других грузоподъемных приспособлений. Демонтаж многоярусных иглофильтровых установок нужно начинать с нижнего яруса, без остановки работы верхних ярусов.
ПРОКЛАДКА ТРУБ СПОСОБОМ ПРОКОЛА
Проколом называют такой способ прокладки, при котором разработку грунта не производят, а отверстие для трубы образуется за счет уплотнения грунта в радиальном направлении.
Прокол лучше применять для прокладки труб малых и средних диаметров (не более 400-500 мм) в глинистых и суглинистых (связных) грунтах. Такие ограничения связаны с тем, что массив грунта прокалывают трубой, оснащенной наконечником, без удаления грунта из скважины. А для этого требуются значительные усилия. В связи с этим и длина прокола труб не превышает 60-80м.
Наконечник служит для уменьшения сопротивлений, возникающих при деформации грунта, и снижения сил трения при вдавливании трубы в грунт.
При небольшой длине прокола трубы прокладывают наконечником с открытым концом.
Тип и количество вдавливающих устройств, способных развивать требуемое усилие, выбирают в соответствии с необходимым расчетным усилием вдавливания. Оно зависит от диаметра и длины прокладываемого трубопровода и от вида грунта. Необходимое нажимное усилие для продвижения трубы в грунте определяется по формуле:
, кН, где
- радиус скважины в грунте
- коэффициент сопротивления грунта
- пористость грунта до прокалывания
- масса 1-го метра футляра
- длина проходки (прокола)
- коэффициент трения стали о грунт
Усилия, требующиеся для прокола труб, колеблются в пределах от 150 до 2000 кН. Определив нажимное усилие, принимают число гидродомкратов для силовой установки и выбирают тип упорной стенки в котловане.
Для прокола труб чаще всего применяют нажимные насосно-домкратные установки, состоящие из одного или двух спаренных гидравлических домкратов с усилием до 170 т каждый, смонтированных на общей раме. Раму с домкратами устанавливают на дне рабочего котлована, из которого ведут прокол. Рядом с котлованом на поверхности размещают гидравлический насос высокого давления.
Трубу вдавливают циклически путем попеременного переключения домкратов на прямой и обратный ход. Давление домкратов на трубу передается нажимными удлинительными патрубками, шомполами или зажимными хомутами. Труба вдавливается на ход штока домкрата, шток возвращается в исходное положение. В образовавшееся пространство вставляется более длинный патрубок или переставляют шпильку шомпола в следующее отверстие.
Общая схема производства работ:
1 – рабочий котлован
2 – приемный котлован
3 – насосная станция
4 – упорная сетка
5 – упорный башмак
6 – гидродомкраты
7 – нажимная заглушка
8 – нажимной патрубок (или шомпол, или зажимные хомуты)
9 – направляющая рама (лежит на шпалах)
10 – приямок (для сварки)
11 – прокалываемая труба
12 – наконечник
После прокола первого звена трубопровода (обычно длиной 6м.) к нему приваривают второе звено и повторяют предыдущую операцию до тех пор, пока не будет завершен прокол на всю длину трубопровода.
Для прокладки труб способом прокола в тяжелоразрабатываемых грунтах (суглинки, глины и др. грунты без крупных включений) используют установки, работающие по принципу «шагающих домкратов» (Упор является подвижным и крепится на направляющей раме, по которой передвигается вместе с домкратами. В этом случае насосная станция является совмещенной с самим домкратом). Применение таких установок позволяет значительно сократить время рабочего цикла.
Гидропроколом прокладывают трубы с помощью энергии струи воды, выходящей под давлением из расположенной впереди трубы специальной конической насадки. Струя воды размывает в грунте отверстие диаметром до 500 мм, в котором прокладывают трубу. Преимущества гидропрокола- простота ведения работ и высокая скорость образования скважины (до 30м/смену). Недостатки- небольшая протяженность проходки (до 20-30м), возможные отклонения от проектной оси и сложные условия работы вследствие загрязненности рабочего котлована.
В несвязных песчаных, супесчаных и плывунных грунтах бестраншейную прокладку трубопровода ускоряют способом вибропрокола. Секция труб последовательно внедряется в грунт под действием ударных импульсов в сочетании со статическим вдавливанием. Способом вибропрокола можно не только прокладывать трубопроводы, но и извлекать их из грунта.
прокладка труб способом продавливания
Продавливанием называют такой способ бестраншейной прокладки труб, при котором в грунт последовательно продавливаются отдельные звенья труб, соединяемые между собой в процессе работ сваркой, с разработкой забоя внутри трубы и удалением грунта через прокладываемую трубу. При этом конец первого звена трубы снабжен ножом.
Этот способ можно применять в любых грунтах для прокладки труб диаметром до 800-1720 мм при длине прокладки до 100м.
Для создания продавливающего усилия можно применять различные устройства типа лебедок, полиспастов. а также тракторов. Однако наибольшее применение для продавливания получили винтовые и гидравлические домкраты, собранные в установку из 2-х, 4-х, 8-ми и более приборов. Количество домкратов в установке зависит от необходимого нажимного усилия Р:
, кН, где
- удельное сопротивление вдавливаемого ножа в грунт, кН
- периметр ножа, м
-коэффициент бокового давления грунта
-масса 1км трубы (футляра), кг
-длина продавливаемой трубы, м
-коэффициент трения трубы о грунт
-вертикальное давление на 1м длины трубы:
, кН, где
-плотность грунта, т/м3
-диаметр кожуха (футляра), м
-коэффициент крепости грунта
Кроме того, необходимое нажимное усилие можно рассчитать приближенно по формуле:
, кН, где
-сила трения грунта о поверхность трубы, принимается 20-25 кН на 1м2 поверхности трубы, кН
-наружный диаметр трубы (футляра), м
-общая длина продавливания трубы, м
Способом продавливания ведут прокладку не только стальных трубопроводов, но и железобетонных колец для газовых колодцев.
При продавливании труб больших диаметров, особенно в твердых грунтах, применяют особо мощные нажимные установки для которых необходимы прочные упорные стенки и специальные нажимные секции или патрубки того же диаметра, что и продавливаемая труба. Все это позволяет разрабатывать грунт внутри трубы небольшими участками в течение всего периода продавливания, т.к. для этого не требуется снимать нажимную секцию.
Разработку грунта внутри трубы в зависимости от условий работ можно производить как механизированным способом, так и вручную.
При продавливании труб диаметром до 700 мм ручную разработку грунта внутри них ведут из рабочего котлована желонками, рукоятки которых наращивают по мере увеличения длины проходки.
При продавливании труб большего диаметра грунт разрабатывает рабочий, находящийся внутри трубы, при помощи лопаты с коротким черенком или пневматическим инструментом. Разработанный грунт нагружают в тележку, которая тросом вытягивается из прокладываемой трубы и поднимается на поверхность грузоподъемными механизмами, грузоподъемностью до 1т.
Применение ручной разработки грунта при продавливании связано со значительными затратами труда рабочих и малой скоростью проходки. Поэтому в настоящее время чаще всего применяют установки с механизированной разработкой и удалением грунта. В этих установках разработка грунта производится режущей головкой, а перемещение его внутри трубы- шнеком.
Для работы в особо прочных грунтах используют виброударную желонку, помещенную внутрь трубы. Труба внедряется в грунт на определенное расстояние (заходку), а затем желонка подается канатом к ее забойному концу, внедряется с помощью вибромолота в грунт, забирает его и с помощью каната перемещает к разгрузочным окнам. Через них грунт высыпается под действием ударов вибромолота в разгрузочные окна кожуха (футляра) на дно траншеи.
Иногда применяют способы с разработкой грунта гидроразмывом и удалением его из забоя в виде пульпы.
прокладка труб способо горизонтального
бурения
Горизонтальным механическим бурением называют такой метод бестраншейной проходки, при котором прокладываемой труде сообщается вращательно-поступательное движение, а грунт удаляют непосредственно через прокладываемую трубу. Этим способом можно забуривать в грунт трубы диаметром до 1720 мм на длину 70-80 м. Однако этот способ недостаточно эффективен в обводненных и сыпучих грунтах. удаляют грунт из трубы способом подмыва.
Процесс бурения и прокладки звеньев трубопроводов в скважину может быть раздельным или совмещенным. При раздельном вначале бурят скважину, а затем, после извлечения из него бурового инструмента, протаскивают трубопровод. При совмещенном методе одновременно с продвижением бурового инструмента прокладывают трубу.
В ходе прокладки непрерывное механическое бурение скважины осуществляется фрезерной головкой, а удаление разжиженного грунта с водой (пульпы) из трубы- по лотку в приямок, откуда его удаляют насосами. Приямок с размерами 160х60 см и глубиной до 60 см организовывают в рабочем котловане.
Метод вибровакуумной проходки
Этот метод основан на принципе вакуума и вибрации и применим для прокладки труб диаметром до 500 мм в связных грунтах. Его принцип заключается в следующем:
1) Сосед цилиндрической формы (в виде стакана) с одним дном открытой стороной прижимают к грунту.
2) Начинают откачивать из сосуда воздух. Из-за разности давлений внутри сосуда и вне его наружный воздух равномерно давит на всю поверхность сосуда.
3) Давление, приходящееся на дно сосуда, заставляет сосуд врезаться в грунт. Давление, приходящееся на цилиндрическую поверхность сосуда, взаимно уравновешивается и не влияет на его движение.
4) Погружение сосуда в грунт облегчается колебательными движениями вибратора, установленного на днище стакана с наружной стороны.
5) Стакан проникает в грунт и наполняется им до тех пор, пока силы трения его стенок о грунт не уравновесятся силами атмосферного давления на дно стакана.
6) Наполненный грунтом стакан извлекают из скважины, опорожняют, устанавливают в скважину вновь.
7) По мере проникновения стакана в грунт к нему прикрепляют элементы разборной штанги, а при извлечении их разбирают.
8) Для продвижения стакана по скважине и его извлечения используют лебедку, трос и систему блоков. (см. рисунок)
9) Когда скважина будет пройдена на всю проектную длину, в нее при помощи лебедки протаскивают трубопровод. После укладки трубопровода зазор между ним и скважиной заполняется песчаной пульпой.
1 – виброваккум-стакан;
2 – штанга
3 – барабан
4 – сборно-разборная рама
5 – вакуум-шланг
6 – вакуум-насос
7 – блоки
8 – трос
9 – лебедка
10 – электродвигатель
ПРОКЛАДКА РАБОЧЕГО ТРУБОПРОВОДА
После того, как одним из рассмотренных способов проложен футляр в него необходимо разместить рабочий трубопровод .Укладку рабочего трубопровода осуществляют способами:
- проталкивания
- протаскивания
Проталкивание применяют для труб диаметром до 1020 мм.
1 – футляр
2 – рабочая труба
3 – оттяжной блок
4 – тяговой канат
Для проталкивания труб используют краны-трубоукладчики грузоподъемностью 12-35т. Перед проталкиванием на дне котлована делают направляющую дорожку из шпал, уголков и рельсов, на которую после смазки солидолом укладывают трубопровод. На торце футляра крепят оттяжной ролик (блок), канат с крюком на конце. Крюк заводят за стенку рабочего трубопровода, а второй конец каната зацепляют за крюк крана-трубоукладчика. В процессе подъема крюка канат натягивается и посредством системы запасовки его через ролик проталкивают рабочий трубопровод в футляр.
Протаскивание рабочего трубопровода применяют при диаметре труб 1220 мм и более. При этом используют тракторы, краны-трубоукладчики или приводные и ручные лебедки грузоподъемностью 3-5т. Перед началом протаскивания трубопровода, как и при проталкивании, устраивают направляющую дорожку и смазывают ее солидолом. Тяговой трос крепят за специальный наконечник или скобу, приваренные к переднему концу трубопровода. Трос проводят в футляре и протягивают через оттяжной блок, закрепленный в котловане со стороны расположения тяговых механизмов, и начинают протаскивание.
ТЕХНИКА БЕЗОПАСНОСТИ ПРИ СООРУЖЕНИИ
ПЕРЕХОДОВ БЕСТРАНШЕЙНЫМИ СПОСОБАМИ
Производство бестраншейных работ значительно опаснее по сравнению с траншейными, так как сама прокладка труб-футляров или устройство горизонтальных скважин скрыты под грунтом, а на пути их прокладки могут встретиться различные искусственные и естественные препятствия в виде подземных сооружений, коммуникаций, валунов и др. Поэтому до начала производства бестраншейных проходок на место работ должны быть вызваны представители организаций 9владельцы подземных сооружений) для указания мест расположения этих сооружений и составления совместного акта о согласовании мероприятий по сохранности сооружений в процессе производства работ по устройству перехода.
При проходке под железнодорожными путями, автомобильными дорогами и городскими проездами любым бестраншейным способом необходимо соблюдать следующие условия:
1) Не допускать просадки сооружения, под которым ведется проходка
2) Точно выдерживать проектный профиль трубопровода или скважины.
3) Обеспечить бесперебойный водоотлив без выноса грунта при наличии на месте проходки грунтовых вод.
При продавливании труб и железобетонных колец с ручной разработкой грунта пребывание рабочих внутри трубопровода допускается если их диаметр не менее 1200мм.
При длине трубопровода более 40 м в проходке должна быть обеспечена искусственная вентиляция. Длительность непрерывного пребывания рабочего внутри трубопровода не должна превышать 1 часа, а интервалы между рабочими циклами должны быть не менее 30 мин.
Разработку грунта внутри трубы допускается вести только при заполнении конца трубы грунтом не менее чем на длину ножа, за пределами его разрабатывать грунт вручную запрещается.
Для сетей освещения и сигнализации в подземных выработках допускается напряжение не более 36 В, а в стесненных условиях не более 12 В.
Во время производства работ по продавливанию грунта запрещается пребывание рабочих в непосредственной близости к нажимным патрубкам.
ДЮКЕРНАЯ ПРОКЛАДКА ТРУБОПРОВОДОВ.
Участок трубопровода, пересекающий овраги, ручьи, реки, озера и подобные им преграды, прокладываемый ниже их дна, называется дюкером. Дюкеры обычно укладываются с заглублением на 1,5-2 м( но не менее 0,5м) для того, чтобы сохранить их от обнажения при размыве дна оврагов и рек и от повреждения якорями проходящих судов.
Трубопроводы, проложенный по дну оврагов и особенно по дну рек, находятся в весьма неблагоприятных условиях, т. к. осмотр их при эксплуатации полностью исключен из-за недоступности, а ремонт крайне затруднителен. Учитывая это, во избежание возможного внезапного выхода из строя трубопровода, дюкеры через водные преграды часто делают двухниточными, то есть прокладывают две параллельные трубы, что позволяет эксплуатировать любую из них при повреждении другой.
На обоих берегах дюкер оканчивается незатопляемыми смотровыми колодцами или камерами, в которых размещают отключающие устройства. В случае надобности в этих же колодцах располагают устройства для опорожнения как самого дюкера, так и прилегающих к нему береговых участков трубопровода при ремонте.
Дюкеры обычно делают из стальных труб, свариваемых в секции и покрываемых противокоррозионным покрытием весьма усиленного или усиленного типа.
УСТРОЙСТВО ДЮКЕРОВ ЧЕРЕЗ СУХИЕ ОВРАГИ И БАЛКИ
Прокладка трубопроводов по дну сухих оврагов осложняется тем, что:
1) Крутые склоны оврагов затрудняют производство земляных работ, доставку труб и секций и их укладку;
2) Возможно внезапное затопление траншей (даже при небольших дождях) в наиболее низких местах оврагов.
В зависимости от крутизны склонов применяют различные методы монтажа труб:
- сверху вниз
-снизу вверх
- комбинированный
Монтаж сверху вниз можно вести на любых склонах, но более целесообразно при крутых. При этом сборку и сварку труб ведут без работающих на склонах машин и механизмов. Первую секцию опускают в траншею одним или двумя кранами-трубоукладчиками (они установлены сверху) и крепят ее тросами к тракторам (один внизу, другой вверху). Нижний трактор протаскивает наращиваемый трубопровод вниз, а верхний удерживает его от самопроизвольного сползания при стыковке каждой последующей секции. После пристыковки вверху очередной секции трубопровод протаскивают вниз на длину этой секции.
Монтаж снизу вверх ведут с доставкой трубных секций на склон кранами-трубоукладчиками, тракторами или лебедками, установленными наверху склона. При уклоне до 20° и хорошем состоянии грунта трубы доставляют к месту монтажа тракторами и наращивают последовательно. Пристыковку производят с помощью одного или двух трубоукладчиков. При монтаже с помощью лебедки длина секций может быть значительной.
Во избежание затопления при дождях самого низкого участка траншеи его разрывают после того, как трубы на этот участок будут полностью подготовлены- сварены, изолированы стыки и испытаны на берме. Опускание труб на таком участке производят тотчас же по разрытии траншеи. После укладки траншею тут же засыпают с тщательным послойным уплотнением грунта (недостаточно уплотненный грунт может быть размыт, а трубопровод может быть обнажен и сдвинут с проектного положения). Засыпку траншеи производят только на том участке, на котором предусматривается пропуск воды по оврагу.
Во избежание повреждения изоляционного покрытия трубопровода (при его прокладке на крутых склонах) поверх изоляции делают футеровку из деревянных реек сечением 20х50 мм.
1 – труба
2 – изоляция
3 – футеровка рейками
4 – стяжной хомут
5 – болт с гайкой
Испытание дюкера, уложенного через сухой овраг можно производить одновременно с соседними участками трубопровода.
УСТРОЙСТВО ДЮКЕРОВ ЧЕРЕЗ ВОДНЫЕ ПРЕГРАДЫ
При устройстве дюкеров через водные преграды выполняют следующие основные процессы работ:
- рытье подводных траншей;
- заготовка и укладка секций труб на дно траншеи;
- засыпка траншеи;
- устройство береговых сооружений;
- испытание дюкера.
Переходы через ручьи и очень малые реки сооружают путем отвода водного потока по новому временному руслу и устройства в месте перехода земляных перемычек или шпунтовых рядов. Земляные, монтажные и все другие работы в этом случае производят так же, как и в обычных условиях, но предусмотрев мероприятия по водоотливу на весь период строительства.
Если ручьи и реки очень малы и скорость течения их невелика, то в этом случае русло перекрывают земляной перемычкой. Ширина и высота которой достаточна для накопления воды перед ней и рытья траншеи, монтажа, испытания и засыпки трубопровода с тщательным уплотнением за ней. Этот способ наиболее дешевый, но не всегда применимый из-за местных условий.
Разработка подводных траншей. Для дюкеров роют подводные траншеи, которые всегда делают с откосами. Ширину подводных траншей определяют в зависимости от диаметра прокладываемого трубопровода и способа балластировки. Если дюкер прокладывают с балластировкой его водой, то ширина траншеи должна быть не менее 1,5 диаметра трубопровода. Если трубопровод балластируют навесными грузами, то ширина траншеи должна быть не менее ширины балластных грузов плюс 1м.
Перед началом разработки подводных траншей в створке перехода на ширине 10м выполняют водолазные работы для выявления затонувших предметов, которые могут помешать работам.
Рытье подводных траншей осуществляют:
- канатно-скреперными установками
- гидромониторами
- экскаваторами
- земснарядами.
Береговые участки обычно разрабатывают драглайнами.
Канатно-скреперная установка применяется для разработки подводных траншей и на прилегающих к дюкеру береговых участках при прокладке дюкеров малых рек шириной до 150 м и больших несудоходных рек шириной до 250м.
Схема канатно-скреперной установки
1 – лебедка
2 – головной блок
3 – бункер (на эстакаде или тракторе)
4 – рабочий трос
5 – холостой трос
6 – скреперный ковш
7 – дно будущей траншеи
8 – блок хвостовой опоры
9 – якорь
При пуске холостого хода лебедки натягивается холостой трос и ковш (его емкость 0,5-2,5 м3) оттаскивается за его тыльную часть к противоположному берегу. Затем лебедка переключается на прямой ход и благодаря натяжению рабочего троса ковш движется по дну реки, набирая грунт (толщина срезаемого слоя до 20 см.). Наполненный ковш втягивается на эстакаду (берег), где разгружается в бункер (вагонетку). Из бункера грунт отвозят на автосамосвалах.
Для ускорения работ используют установки двухстороннего действия (оба хода- рабочие).
На широких реках при использовании канатно-скреперных установок монтируют промежуточные хвостовые опоры, а тяговые устройства размещают на барже. Грунт в этом случае сбрасывают в подводный отвал.
При разработке траншеи гидромониторами отпадает необходимость подъема и транспортирования грунта. Принцип работы такого устройства заключается в размыве грунта струей воды. Этим способом устраивают подводные траншеи шириной до 5 м и глубиной до 1 м через большие реки.
Грунтососные плавучие снаряды предназначены для подводной разработки грунта путем всасывания его и транспортирования пульпы на значительные расстояния. По способу грунтозабора землесосные снаряды различаются на:
- разрабатывающие грунт непосредственным засасыванием
- всасывание грунта с предварительным рыхлением с помощью гидромонитора.
Экскаватором, установленным на барже или понтоне, разрабатывают подводные траншеи при глубине водотоков не более 2-3 м и ширине до 200 м.
При глубине водоемов до 1-1,5 м и ширине до 100 м траншеи разрабатывают экскаваторами со специальных земляных дамб, отсыпаемых от обоих берегов. Посередине водотока оставляют разрыв для пропуска воды. Траншеи в этих местах разрабатывают с помощью канатно-скреперной установки или земснарядами.
Земснарядами подводные траншеи разрабатывают при глубине водоемов более 2 м и шириной более 200 м. Одночерпаковый земснаряд является машиной периодического действия и используется для разработки наиболее тяжелых грунтов 9глубина извлечения грунта до 25 м). Многочерпаковые земснаряды представляют собой машины непрерывного действия и предназначены для разработки грунтов на дне рек и морей (глубина извлечения грунта до 40 м). Разрабатываемый землечерпательными снарядами грунт погружается в шаланды, пришвартованные к земснарядам. Если одним, то работы ведут от одного берега к другому, обеспечивая беспрепятственный проход судов. При использовании двух земснарядов, работы ведут от центра к берегам, при этом оставив между агрегатами проход для судов (минимум 80 м). Оставшийся участок траншеи разрабатывают одним из используемых земснарядов.
УКЛАДКА ТРУБОПРОВОДОВ В ПОДВОДНЫЕ ТРАНШЕИ
Способ укладки дюкера зависит от:
- диаметра трубопровода
- длины подводного перехода
- глубины подводного перехода
При погружении в воду стальных труб диаметром до 300 мм они тонут 9имеют отрицательную плавучесть), а при больших диаметрах- трубы плавают (имеют плавучесть). Поэтому трубы больших диаметров для погружения требуют устройства специальных пригружных конструкций.
Кроме того, диаметр определяет гибкость трубопровода. Эта характеристика используется при укладке дюкеров методом свободного изгиба (максимальный диаметр, при котором метод возможен 250-300 мм).
Независимо от метода укладки дюкера до начала работ выполняют следующие операции:
1) сварка труб в плети
2) испытание
3) изоляция (битумная, весьма усиленная трехслойная)
4) футеровка деревянными рейками (сплошная или с прозорами).
В целом же дюкеры испытывают трижды:
1) после сварки
2) после укладки в траншею
3) после засыпки траншеи.
Основные способы укладки подводных трубопроводов:
1. Опускание всего трубопровода с плавучих или стационарных опор
2. Протаскивание плети трубопровода по дну подводной траншеи
3. Укладка трубопровода с плавучих средств при постепенном наращивании его.
4. Укладка трубопровода со льда.
Для того чтобы труба легла на дно подводной траншеи и могла выполнять функцию дюкера, она должна иметь отрицательную плавучесть как при погружении, так и во время эксплуатации. Это достигается использованием труб с повышенной толщиной стенки, балластировкой отдельными грузами или вспомогательной трубой, заполненной водой. Отдельные грузы представляют собой железобетонные или чугунные блоки седловидной формы (целые или разъемные). Их навешивают на трубопровод на расстоянии друг от друга, определяемом расчетом. Способ утяжеления трубопровода выбирают в зависимости от принятого метода работ.
Опускание трубопровода с плавучих или стационарных опор
Вначале производят подготовительные работы:
1) Строительство спусковых приспособлений и сооружений- стапелей, спусковых дорожек.
2) Устройство фундаментов под механизмы, плавучих или стационарных опор.
Схема заводки трубопровода в створ перехода
1 – стапель
2 – плеть трубопровода
3 – понтоны
4 – створ перехода
I. Утяжеленную на стапеле и снабженную понтонами (для плавучести) трубу опускают на воду.
II-IV. Плеть устанавливают в створе перехода, выверяют, закрепляют от сноса течением и опускают на дно траншеи.
Спуск трубопровода на дно траншеи производят с помощью плавучих или стационарных опор путем снятия понтонов и стравливания тросов с лебедок.
1 – плавучая опора (или стационарная свайная)
2 – лебедка
3 – опускаемая плеть
Освобождение трубопровода от поддерживающих тросов производится только после выверки и испытания дюкера.
Трубопроводы большого диаметра доставляют к месту укладки на плаву (без пригрузов и понтонов). После установки его по оси дюкера к нему крепят пригруз в виде трубы, постепенно заполняемой водой. Под влиянием этого веса труба, поддерживаемая тросами, равномерно опускается на дно траншеи.
Протаскивание трубопровода по дну подводной траншеи.
Этот способ используют для укладки дюкеров любого диаметра при наличии плавного рельефа дна подводной траншеи и береговой полосы значительной длины.
На одном из берегов водоема устраивают строительную площадку, на которой располагают стапель и спусковую дорожку, направление которых перпендикулярно к реке.
Спусковая дорожка- это узколинейный путь (шириной 750 мм), прокладываемый в сторону реки с уклоном 0,001-0,005 на длину, равную ширине реки, то есть на длину прокладываемой плети трубопровода. Если условия работы не позволяют сделать спусковую дорожку длиннее 200 м, то узколинейный путь можно заменить роликовым стендом.
На стапеле производят сварку секций в плеть, изоляцию стыков и испытание. На передний конец плети наваривают конусообразную заглушку, а к ней- кольцо (из круглой стали диаметром 40 мм), за которое цепляют крюк тягового троса. Тяговой трос протаскивают в створе дюкера через весь водоем и выводят на противоположный берег.
1 – узколинейный путь
2 – тележки
3 – газопровод
4 – понтоны
5 – роликовые опоры
6 – место поворота узколинейного пути (по нему будут отъезжать тележки)
7 – буй (контрольный поплавок)
8 – трос
9 – тягач
В процессе протаскивания трубопровода возможны вынужденные остановки, тогда тяговое усилие рассчитывают с учетом повторного трогания:
, кН, где
-сила удельного присоса трубопровода к грунту, т/м2
-площадь опирания трубопровода на грунт, м2.
Тяговое усилие можно создать лебедками, трактором и полиспастом или колонной тракторов.
Когда возникает опасность сдвига и перелома трубопровода в процессе движения его по дну подводной траншеи (значительная скорость течения реки), применяют оттяжки, регулируемые лебедками, которые устанавливают на плавучих средствах или на берегах.
В период движения трубопровода необходимо тщательно наблюдать за ним как на берегу, так и с плавучих средств.
Работа по протаскиванию заканчивается тогда, когда противоположный конец плети будет вытянут из воды на проектную длину.
Укладка трубопроводов способом последовательного наращивания применяется при водоемах очень большой шириной- более 1км. Для укладки трубопровода этим методом необходима достаточная глубина водоема для свободного перехода судна, с которого ведется укладка. Кроме того, этот способ применим лишь тогда, когда скорость течения воды небольшая. Наращивание плети можно производить в надводном и подводном положении.
Сущность надводного метода:
Заготовленные на берегу секции труб длиной 24, 36, 48 м и более баржами доставляют к плывучей базе. Здесь их сваривают наращиванием в нитку, испытывают, изолируют стыки. Плавучая база имеет спусковую роликовую дорожку, по которой непрерывно наращиваемая нитка трубопровода опускается в воду. По мере наращивания плавучая база соответственно перемещается, оставляя за собой на дне подводной траншеи готовую нитку трубопровода.
При укладке трубопровода таким способом используется возможность свободного изгиба трубопровода.
Если работы производят на больших водоемах, где возможен шторм, то в эти периоды работы прекращают: конец трубопровода закрывают временной пробкой и опускают на дно водоема (над концом трубопровода устанавливают буй), плавучую базу отводят в безопасное место.
На участке вывода трубопровода на берег укладку производят при помощи кранов, установленных на берегу.
В подводном положении наращивание осуществляется путем соединения секций, уложенных на дно, водолазами, чаще всего на фланцах.
Укладка трубопровода со льда применяется для любых диаметров труб. но при скорости течения реки не более 2 м/сек.
Для укладки трубопровода со льда с помощью опор или способом свободного погружения дисковыми пилами прорезают сквозную прорубь (майну). Ширина майны должна быть такой, чтобы в нее мог свободно пройти прокладываемый трубопровод. Подготовленный к спуску трубопровод укладывают над майной по оси створа на лежни, проложенные поперек прорези. Над трубопроводом устанавливают козлы с талями, с которых и погружают его так же, как с постоянных или плавучих опор.
Если скорость течения реки превышает 0,5 м/сек, то для предотвращения сноса трубопровода при его спуске применяют оттяжки или направляющие сваи. Сваи забивают в грунт на глубину 2-3 м так, чтобы их верхние концы опирались на лед
1 – лед
2 – майна
3 – блок
4 – лебедка
5 – свая
6 – трубопровод
Если при опускании трубопровода применяют оттяжки, то лебедки устанавливают на расстоянии 25-30 м от майны вверх по течению, а тросы оттяжек пропускают под лед в небольшие проруби. прорубленные во льду перед лебедками.
Производить работы со льда разрешается только тогда, когда толщина льда обеспечивает необходимую несущую способность при размещении на нем трубопровода, механизмов, приспособлений и людей. При недостаточной толщине ледяного покрова ее увеличивают искусственным намораживанием сверху или снизу. В любом случае работы ведут при устойчивой температуре окружающего воздуха ниже -5°С.
Засыпку уложенного на дно подводной траншеи трубопровода можно производить с использованием энергии течения реки, намывом грунта гидромониторами и привозимым грунтом с барж. Эти работы выполняют водолазы.
Кроме того водолазы выполняют следующие работы по прокладке дюкеров:
- проверка выполнения земляных работ при рытье подводных траншей любыми механизмами.
- разработка траншей под водой ручными гидромониторами (планировка дна)
-проверка правильности положения труб при укладке дюкера
- подбивка труб грунтом
- исправление обнаруженных дефектов
- подводная резка и сварка труб (при необходимости)
Дюкеры через водные преграды сооружают в период стояния низких горизонтов воды (летний и зимний). Во избежание заноса грунтом подводных траншей работы , проводимые летом следует заканчивать до ледостава, а проводимые зимой- до весеннего ледохода. Из тех же соображений подводный трубопровод следует укладывать немедленно после отрывки траншей и планировки ее дна, а уложенный трубопровод необходимо не более как в течение суток проверить на правильность положения и плотность прилегания его к грунту на все протяжении перехода и засыпать.
ОСОБЕННОСТЬ ТЕХНОЛОГИИ УСТРОЙСТВА
НАДЗЕМНЫХ ПЕРЕХОДОВ ТРУБОПРОВОДОВ.
Монтаж подвесных трубопроводов.
При надземном переходе через реки, овраги, балки, железнодорожные и другие дороги вначале возводят береговые и русловые опоры (пилоны). Затем на верхних ригелях пилонов устанавливают стреловые краны для укладки рабочих канатов в опорные гнезда- башмаки на пилонах. К рабочим канатам крепят подвески на которых и будет закреплен трубопровод.
Однопролетные строения переходов монтируют на берегу по оси перехода до подъема несущих канатов на пилоны (I-ый способ) или на весу с временных опор после подъема канатов на пилоны (II -ый способ).
В I-ом случае размеченные несущие канаты раскладывают по оси перехода, а их концы закрепляют в анкерных опорах. Далее к этим канатам прикрепляют распорки и узлы подвесок. После этого канаты поднимают на пилоны и закрепляют. Подвески прикрепляют к седлам трубной плети.
II -ой способ применяют для устройства переходов длиной более 100 м. В этом случае на пилонах поднимают только канаты, закрепляя их. Затем, одновременно с двух сторон перехода, на них монтируют подвески трубопровода. Для этого используют телескопические вышки. Закрепив все подвески, приступают к монтажу трубопровода. (см, рисунок)
1 – пилоны
2 – трубопровод
3 - рабочий канат с подвесками
4 – постоянные опоры
5 – якорь
6 – лебедка
7 – отводные блоки
8 – полиспасты
9 – временная опора
Готовые блоки трубопровода из двух плетей (длиной до 40 м) скрепляют между собой жесткими связями и подают в зону монтажа (на баржах и понтонах или, если переход через водоем, укладывают на временные опоры). Монтаж ведут одновременно с правого и левого берегов, равномерно и последовательно загружая несущие канаты. В проектное положение плети поднимают системой полиспастов, прикрепленных к несущим канатам перехода. Береговые плети монтируют методом надвижки с помощью тех же полиспастов. После закрепления плетей трубопроводов в проектном положении и в подвесках их центрируют и сваривают.
После монтажа выверяют прогиб несущих канатов и положение пилонов, окончательно закрепляют все элементы перехода. Затем трубопровод испытывают, окрашивают.
Многопролетные переходы монтируют аналогично по пролетам.
Монтаж висячих трубопроводов.
Вначале устанавливают пилоны и массивные железобетонные якоря с прикрепленными к ним оттяжками. Затем монтируют стояки с компенсационными петлями трубопровода. Далее между пилонами на поплавках или временных опорах выкладывают плеть трубопровода. Монтаж труб на пилоны осуществляют методом подъема или надвижки.
При монтаже методом подъема плеть в проектное положение поднимают синхронно действующими на обоих пилонах полиспастами, после чего ее соединяют с узлами подвесок и магистральным трубопроводом.
При монтаже методом надвижки между пилонами натягивают временный монтажный трос, а к трубопроводу, уложенному у одного из пилонов, крепят тяговой трос и через каждые 14-15 м на жестких стойках –ролики
1 – пилоны
2 – висячий трубопровод
3 – монтажный трос
4 – тяговой трос
5 – постоянные опоры
6 – якорь
7 – трубоукладчики
8 – ролики
9 – тягач
Оба троса перебрасывают через блоки на вершинах пилонов и крепят к тягачу на противоположном берегу. Затем кранами-трубоукладчиками подготовленную плеть трубопровода поднимают и подают так, чтобы она перемещалась к противоположному пилону, опираясь роликами на монтажный трос. Плети придают проектный прогиб, прикрепляют ее к подвескам пилонов и сваривают в одну нить с участками трубопроводов по обе стороны перехода.
МОНТАЖ САМОНЕСУЩИХ ТРУБОПРОВОДОВ.
Самонесущими конструкциями являются балочные и арочные переходы.
Балочные переходы монтируют в два этапа:
1. Устанавливают опоры
2. Монтируют трубопровод способом надвижки или подъема.
Если пролет превышает 50 м, устанавливают промежуточные опоры. При методе надвижки плети трубопровода на катках лебедками (тяговой и тормозной) надвигают на опоры. В многопролетных переходах плети доставляют непосредственно к опорам, а затем кранами укладывают в проектное положение. Простейшие однопролетные балочные переходы через водные преграды монтируют способом протаскивания с последующим подъемом и укладкой кранами на опоры.
Арочные переходы трубопроводов монтируют из укрупненных блоков- полуарок. Начинают монтаж с устройства береговых упоров с оставленными гнездами и забетонированными металлическими опорными рамами. Затем на специальных стендах готовят к подъему монтажные элементы (полуарки). При пересечении железнодорожных путей арочный переход монтируют железнодорожными кранами с использованием передвижной временной монтажной опоры.
Дата добавления: 2020-12-12; просмотров: 160; Мы поможем в написании вашей работы! |
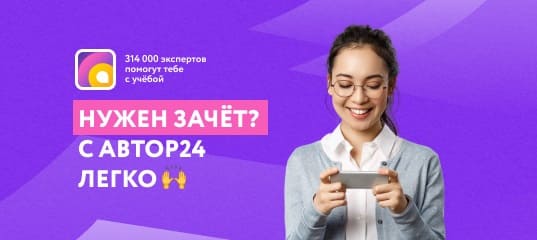
Мы поможем в написании ваших работ!