Очистка и осушка исходного газа
Областное государственное автономное профессиональное образовательное учреждение
«Новгородский химико-индустриальный техникум»
«УТВЕРЖДАЮ»
Заместитель директора по УПР.
____________ А.С. Шаршукова
«_____» ______________ 2016г.
ЗАДАНИЕ
НА ВЫПОЛНЕНИЕ ВЫПУСКНОЙ КВАЛИФИКАЦИОННОЙ РАБОТЫ
Профессия:18.02.03 Химическая технология неорганических веществ Техник-технолог
Группа 3ХТ-2
Студент Черноног Александр Геннадьевич
Тема выпускной квалификационной работы:
«Использование продувочных и танковых газов для захолаживания промывной воды в отделении разделения остаточных газов производства аммиака»
Исходные данные к работе: Технологическая схема производства аммиака, участка разделения остаточных газов
Содержание:
Введение
1.1. Актуальность темы, цель и задачи
2. Основная часть
2.1. Общая характеристика производства
2.2. Физико-химические основы технологического процесса2.3. Характеристика рабочего места
1.3.1. Назначение рабочего места
2.4. Описание технологической схемы
2.5. Характеристика основного оборудования
2.6. Регулирование технологического процесса, сущность компримирования, нарушение режима, причины, меры устранения
2.7. Практическая часть
3. Охрана труда, организация рабочего места
4. Экономическая часть
4.1. Себестоимость продукции
4.2. Классификация затрат
4.3. Пути снижения себестоимости
5. Заключение-анализ производственной деятельности аппаратчика на рабочем месте
|
|
Приложения: Чертёж А1 -2 шт.
Дата выдачи задания 20.02.16 г.
Дата сдачи готовой работы 15.05.16 г.
Руководитель выпускной
квалификационной работы ________________________
(подпись) (расшифровка подписи)
Студент ________________________
(подпись) (расшифровка подписи)
Введение
Атмосфера - газовая оболочка земли, удерживаемая около него гравитацией. Поскольку не существует резкой границы между атмосферой и межпланетным пространством, то обычно атмосферой принято считать область вокруг небесного тела, в которой газовая среда вращается вместе с ним как единое целое. Глубина атмосферы некоторых планет, состоящих в основном из газов (газовые планеты), может быть очень большой.
Атмосфера также является защитным слоем планеты, защищая её обитателей от солнечного ультрафиолетового излучения.
Состав атмосферного воздуха
|
|
Вещество | Обозначение | По объему, % | По массе, % |
Азот Кислород Аргон Углекислый газ Неон Метан Гелий Криптон Водород Ксенон | N2 O2 Ar CO2 Ne CH4 He Kr H2 Xe | 78,084 20,9476 0,934 0,0314 0,001818 0,0002 0,000524 0,000114 0,00005 0,0000087 | 75,5 23,15 1,292 0,046 0,0014 0,000084 0,000073 0,003 0,00008 0,00004 |
Газообразный азот представляет собой одно из самых устойчивых химических веществ. В атмосфере азот находится в свободном состоянии в огромных количествах. Подсчитано, что над поверхностью Земли имеется около 80 тыс. т азота. Важнейшее значение имеет азот для жизни на Земле, являясь одним из элементов, входящих в состав белковых структур, без которых невозможно существование живой клетки.
В жизнедеятельности растений химические соединения. Аммиак является важнейшим соединением азота, участвующим в животных принимает участие не элементарный азот, а связанный, т.е. его азотистом обмене веществ в живой природе.
Основным же неисчерпаемым источником азота служит воздух. Получение аммиака аммиачным методом происходит по обратимой реакции
Н2 + N2 ↔ NН3 + Q
т.е. синтез аммиака осуществляют из азота и водорода.
Технологический процесс получения синтетического аммиака состоит из следующих стадий:
|
|
- сероочистка природного газа;
- паровая конверсия метана, паровоздушная конверсия метана;
- конверсия оксида углерода;
- очистка конвертированного газа от диоксида углерода;
- тонкая очистка конвертированного газа от оксида и диоксида углерода метанированием;
- синтез аммиака.
На стадии синтеза аммиака при снижении давления происходит выделение из жидкого аммиака растворенных в нем газов (так называемых танковых газов). Танковые газы после охлаждения выдаются: часть - на установку разделения остаточных газов - часть на свечу для сжигания.
Продувочные газы, выходящие из сепаратора, отбираются через клапан высокого давления. Далее газ поступает в трубопровод, в котором поддерживается давление не более 4,42 МПа (45 кгс/см2). Давление регулируется клапаном сброса газа в линию продувочных и танковых газов, идущих на сжигание.
Танковые газы из сборников аммиака, пройдя холодильники, собираются в коллектор и подаются в систему топливного газа или на факел. Давление в коллекторе продувочных и танковых газов поддерживается сбросом на факел.
В цех аммиака №3 с установки разделения остаточных газов поступают следующие потоки:
|
|
- азотоводородная смесь с объемным расходом не более 6 200 м3/ч (при н.у.) и давлением не менее 2,53 МПа (25,8 кгс/см2) подается на всас компрессора перед сепаратором; объемная доля компонентов в азото-водородной смеси: Н2 - 91,8 - 93,0 %; N2 - 6,9 - 8,1 %; Ar - не более 0,1 %;
- метановая фракция с объемным расходом не более 1 900 м3/ч (при н.у.) и давлении не менее 0,98 МПа (10 кгс/см2) поступает в линию топливного газа перед сепаратором; объемная доля компонентов в метановой фракции: СН4 - не менее 98,0 %; Ar+N2 - не более 2,0 %.
Газообразный аммиак с давлением не менее 0,17 МПа (1,7 кгс/см2) поступает в расширительный сосуд.
Аммиачная вода поступает в отпарную колонну перед теплообменником. Массовая доля аммиака 4-10 %.
1.1. Актуальность темы, цель и задачи
Технологи ищут пути замены использования жидкого аммиака для захолаживания промывной воды, так как жидкий аммиак на сегодняшний день является дорогим химическим продуктом.
Данной проблеме посвящена моя дипломная работа «Использование продувочных и танковых газов для захолаживания промывной воды в отделении разделения остаточных газов производства аммиака»
Я считаю тему «Использование продувочных и танковых газов для захолаживания промывной воды в отделении разделения остаточных газов производства аммиака» актуальной, т.к. в этом случае производство имеет возможность отказаться от использования чистого аммиака. В результате этого снизится концентрация опасного фактора по аммиаку в воздухе рабочей зоны производства. Кроме того предприятие сможет получить экономию чистого аммиака.
В результате своей работы я должен:
- определить актуальность темы, цель и задачи;
- дать общую характеристику производства;
- рассмотреть физико-химические основы технологического процесса;
- определить назначение рабочего места, охарактеризовать его, определить границы обслуживания;
- сделать описание технологической схемы;
- дать характеристику основного оборудования;
- рассмотреть вопросы регулирования технологического процесса, сущность, нарушение режима, причины, меры устранения, действия технолога в аварийной ситуации
- описание нормы технологического режима
- рассмотреть аналитический контроль
- рассмотреть охрана труда, организацию рабочего места
- определить экономическая часть
- узнать себестоимость продукции
- узнать классификация затрат
- выяснить путь снижения себестоимости
- сделать заключение - анализ производств. деятельности технолога на рабочем месте
1.2. Литературный обзор
Аргон был открыт в 1894 г. двумя английскими учеными Рамзаем и Рэлеем после проведения последним серии работ по точному определению плотности азота. Открытия аргона и других инертных газов (гелия, неона, криптона, ксенона и радона) способствовали разработке основ кинетической теории газов, новой классификации химических элементов в рамках периодического закона Д.И.Менделеева, а в дальнейшем привели к фундаментальным открытиям в теории строения атомов, Обзор истории открытия аргона выполнен Э.Н.Гибертом.
Аргон представляет собой одноатомный элемент периодической системы Менделеева с порядковым номером 18. Атомный вес естественной системы изотопов аргона равен 39,948. Природный аргон, содержащийся преимущественно в атмосфере, является смесью изотопов с массовыми числами 36; 38 и 40, причем относительная концентрация их соответственно составляет 0,337; 0,063 и 99,600 % об.
Появление аргона в атмосфере Земли связано со сложным характером радиоактивного распада К40. В атмосфере Земли накопились десятки миллионов тонн аргона, и в настоящее время его содержание составляет 1,286 % масс. Содержание аргона, растворенного в морской воде, изменяется в пределах от 0,02 до 0,04 % об. Аргон встречается в изверженных породах земной оболочки. Подавляющая часть аргона в космосе состоит из изотопов Ar36 и Ar38. Аргон наблюдается также в атмосфере некоторых звезд и в галактических туманах. Косвенные данные указывают на присутствие аргона и в атмосфере Марса, причем соотношение количеств аргона и азота в атмосфере Марса и Земли одинаково.
Я. И. Френкель и Р. Б. Сегаль рассчитали, исходя из химической теории конденсации, содержание ван-дер-ваальсовских комплексов в паре вблизи от состояния насыщения, Число двойных молекул Аг2, в значительной степени зависящей от близости состояния пара к условиям насыщения и от температуры, достигает наибольших значений вблизи кривой насыщения.
В одном моле аргона число двойных комплексов при Т=90º К составляет1018.5. Эти авторы отмечали возможность образования комплексов из атомов металла и атомов инертных газов (например, HgAr), что в дальнейшем нашло экспериментальное подтверждение. Н. Бернардес и Г. Примаков, используя уравнение Шредингера и потенциал межмолекулярного взаимодействия Морзе, теоретический исследовали возможность образования молекул из двух атомов инертного газа. Путем расчета функций распределения ими установлена концентрация двойных молекул в одноатомных инертных газах: № 2% для, № 3% для Ar, Kr и Xe. Такие количества двойных молекул могут быть обнаружены спектроскопическим методом или методом, основанным на дифракции электронов. Д. Стогрин и Дж. Гиршфельдер, исходя из различных модельных потенциалов, Рассчитали концентрацию двойных молекул в аргоне при Т=120 ÷ 600 ºК.
Известный интерес вызывают также клатратные соединения (или соединения включения) аргона с различными веществами. Первый представитель этого типа соединений был получен Р. Вайяром почти одновременно с открытием аргона. Это был гидрат аргона Ar · 5,75 H2O, представляющей собой соединения включения атома Ar в пространственную секту молекул воды, которые относительно прочно скреплены водородными связями. Склонность к образованию соединений включения обнаруживают также другие вещества, в частности гидрохинон. Клатратное соединение аргон и гидрохинон образуется при кристаллизации гидрохинона под давлением аргона примерно 4,0Мн/м². Способность инертных газов образовывать соединения включения была использована в ряде случаев для промышленного разделения смесей.
Элементные теплообменники. Каждый элемент такого аппарата представляет собой простейший кожухотрубный теплообменник без перегородок. Такие аппараты допускают при этом более высокое давление. Однако такая конструкция получается более громоздкой и тяжёлой, чем кожухотрубный аппарат.
Погруженные теплообменники. В погруженном змеевиковом теплообменнике один теплоноситель движется по змеевику, погруженному в бак с другим жидким теплоносителем. Скорость жидкости в межтрубном пространстве незначительна и следовательно, теплоотдача от жидкости сравнительно невелика. Такие теплообменники находят применение благодаря своей простоте и дешевизне в небольших установках.
Теплообменники типа «труба в трубе». Теплообменный элемент такого аппарата. Отдельные элементы соединены между собой патрубками и калачами, образуя цельный аппарат необходимого размера. Эти теплообменники находят себе применение при небольших расходах теплоносителей и при высоких давлениях.
Оросительные теплообменники. Такой тип теплообменников применяется главным образом в качестве конденсаторов в холодильных установок. Оросительный теплообменник представляет собой змеевик из горизонтальных труб, размещённых в вертикальной плоскости в виде ряда параллельных секций. Над каждым рядом находится жёлоб, из которого струйками стекает охлаждающая вода на теплообменные тубы, омывая их наружную поверхность. При этом часть охлаждающей воды испаряется. Оставшаяся вода возвращается насосом, а потери компенсируются из водопровода. Эти теплообменники устанавливаются на открытом воздухе и ограждаются деревянными решетками, чтобы уменьшить унос воды.
Графитовые теплообменники. Теплообменники для химически агрессивных сред изготовляют из блоков графита, который пропитывают специальными смолами для устранения пористости. Графит отличается хорошей теплопроводностью. Блоки уплотняются между собой прокладками из резины или тефлона и стягиваются крышками со стяжками.
2. Основная часть
2.1. Общая характеристика производства
Установка разделения остаточных газов производства аммиака (участок аргона) предназначена для разделения смеси продувочных и танковых газов (исходный газ) агрегатов аммиака №2 и №3 фирмы ТЕС с выделением жидкого аргона, жидкого азота, азото-водородной смеси и метана.
Установка входит в состав производства аммиака.
Ввод установки в эксплуатацию декабрь 1980 года.
Проектная мощность установки составляет 2,7∙106м³ (при н.у.) газообразного аргона в год.
Достигнутая мощность на 01.01.2002 г. составляет 3,641∙106м³ (при н.у.) газообразного аргона.
Предусмотрена также выдача:
- жидкого азота потребителю до 500 тонн в год;
- азотоводородной смеси на агрегаты аммиака №2 или №3 c объемным расходом 2500-6900 м³/ч (при н.у.). В цеха азотной кислоты и метанола-азотоводородной смеси. На агрегаты аммиака №2 или №3 c объемным расходом 3800-6900 м³/ч (при н.у.)
- метановой фракции на агрегаты аммиака №2 или №3 с объемным расходом 500 - 1500 м³/ч (при н.у.);
- газообразного аргона с избыточным давлением 14,71 МПа (150,0 кгс/см²) на наполнительную рампу для заполнения баллонов;
- газообразного аргона с избыточным давлением 1,57 МПа (16,0 кгс/см²) в сеть объединения с объемным расходом 200 м³/ч (при н.у.);
- аммиачной воды на агрегаты аммиака №2 или №3 или в цех производства аммиачной воды, жидкой углекислоты, наполнения баллонов;
- возврат газообразного аммиака на агрегаты аммиака №2 или №3 после испарения жидкого аммиака.
Установка выполнена в один технологический поток и состоит из следующих стадий:
- деаэрирование деминерализованной воды;
- очистка исходного газа от аммиака;
- осушка исходного газа от влаги;
- низкотемпературное разделение исходного газа;
- компримирование газообразного азота;
- хранение и налив жидких аргона и азота, их испарение и выдача потребителю.
Метод производства - низкотемпературная ректификация исходной смеси.
Технологический процесс разработан фирмой NEACVEB Chemieanlagenbau Erfurt-Rudisleben, Объединенная Германия, по техническому заданию ГИАП, Москва.
Генеральный проектировщик - ГИАП, Москва. Проект во всех частях выполнен ГИАП, Москва.
Строительство установки осуществлено на базе комплектно поставленного из Германии оборудования.
По технико-экономическому уровню установка получения аргона относится к высшей категории.
Реконструкции и расширению установка аргона не подвергалась.
2.2. Физико-химические основы технологического процесса
Процесс разделения продувочных и танковых газов аммиачного производства состоит из следующих стадий:
- деаэрирование деминерализованной воды;
- очистка исходного газа от аммиака;
- осушка исходного газа от влаги;
- низкотемпературное разделение исходного газа;
- компримирование газообразного азота;
- хранение и налив жидкого аргона и азота, их испарение и выдача потребителю.
Процесс получения промывной воды основан на принципе деаэрации (дегазации) воды с целью удаления из нее растворенных газов (кислорода, углекислоты).
Деаэрация воды осуществляется термическим способом, основанным на уменьшении растворимости в воде газов с понижением их парциальных давлений в пространстве над водой, для чего ее доводят до температуры кипения при данном давлении.
Процесс очистки исходного газа от аммиака основан на абсорбционном методе очистки, где в качестве абсорбента - промывной воды используется деминерализованная вода.
По физико-химическим основам процесс относится к химической абсорбции аммиака промывной водой, протекающей по реакции:
H2О + NH3 = NH4OH + Q ккал
с получением аммиачной воды с массовой долей аммиака 2 - 10 %.
Процесс осушки очищенного газа основан на уменьшении влагосодержания газа путем адсорбции влаги силикагелем с последующей периодической десорбцией этой влаги из силикагеля горячим газом.
Разделение многокомпонентной газовой смеси (исходного газа) в конденсаторах и ректификационных колоннах блока разделения с получением аргона, азота, метана, азото-водородной смеси основано на методе глубокого охлаждения многокомпонентной смеси в процессе ректификации.
Ректификация - это физический способ разделения смесей на составляющие вещества, основанный на различии в температурах кипения отдельных компонентов через жидкое состояние.
В ректификационных колоннах разделение смеси на составные части происходит в результате последовательного и многократного испарения жидкости, за счет подведенного тепла и конденсации паров, за счет стекающей сверху флегмы. При этом стекающая вниз по тарелкам жидкость обогащается высококипящим компонентом, а пары, поднимающиеся вверх - низкокипящими компонентами.
Холод, необходимый для получения и поддержания низких температур обеспечивается азотным холодильным циклом.
2.3. Характеристика рабочего места
2.3.1. Назначение рабочего места
Рабочее место технолога газоразделения предназначено для очистки исходного газа от аммиака и влаги, разделения исходного газа на жидкий аргон, жидкий азот, азотоводородной смеси и метановой фракцию методом низкотемпературной ректификации исходного газа (смеси продувочных и танковых газов производства аммиака).
Границы рабочего места.
Рабочим местом технолога газоразделения, являются:
- установка деаэрирования деминерализованной воды ;
- установка очистки и осушки исходного газа (очистка от аммиака и влаги) ;
- центральный пульт управления (ЦПУ) ;
- блок разделения газа ;
- помещение турбодетандера ;
- узел испарения жидкого азота и аргона с выдачей в заводскую сеть ;
- хранилища жидких продуктов (аргона, азота) со всем относящимися к ним оборудованием, арматурой, коммуникациями, электрооборудованием,
средствами КИП и А.
2.4. Описание технологической схемы
2.4.1. Установки пароснабжения и деэарирования
Установки пароснабжения.
Пар с избыточным давлением 882,6-1078,71274,9 кПа (9-13 кгс/см²) и температурой 165-200 °С поступает на установку из сети объединения, или с агрегата №2 производства аммиака и разделяется на два потока. Часть пара используется для подогрева регенерирующего газа в подогревателе поз.
W2003. Остальная часть пара дросселируется до избыточного давления 392,3-588,4 кПа (4-6 кгс/см²) и также разделяется на два потока:
- один поток направляется в цеховой коллектор к паровым подогревателям поз. W1002, W3015, W7071, W7072, ёмкостям аварийного слива поз. B3901 и Е-5, к системе обогрева шкафов КИП, на обогрев арматуры, отборов анализов, бойлера, помещений весовой, сварочной, в испаритель азота (аргона) поз. Т-1;
- другой поток пара дросселируется до избыточного давления 19,61-24,52 кПа (0,2-0,25 кгс/ см²) и поступает в бак деаэратора поз. Е-2 для дегазации и подогрева воды до температуры 102-104 °С.
Предусмотрена также подача пара на обогрев линий аммиачной воды, деминерализованной воды, на обогрев диафрагм газообразного аммиака и пара.
Деаэрирование деминерализованной воды.
Деаэрирование - это удаление из воды растворенных газов (О2, углекислоты), основанном на уменьшении растворимости в воде газов с понижением их парциальных давлений в производстве над водой, для чего ее доводят до кипения при давлении 19,61-24,52 кПа (0,2-0,25 кгс/см²).
Деминерализованная вода с агрегатов аммиака, с объемным расходом 3,2-4,6 м³/ч поступает в колонку К-2 деаэратора Е-2. В колонку К-2 подается также конденсат пара с избыточным давлением:
- 392,3-588,4 кПа (4-6 кгс/см²) от подогревателей поз. W1002, W3015, W7071, W7072 и систем обогрева шкафов КИП и др.
- 882,6-1078,71274,9 кПа (9-113 кгс/см²) после подогревателя поз.W2003.
Для процесса деаэрирования и поддержания температуры 102-104 °С в деаэратор поз. Е-2 подается пар с избыточным давлением 19,61-24,52 кПа (0,2-0,25 кгс/см²).
Выпар после деаэрационной колонки поз. К-2 сбрасывается в атмосферу.
Нормальный уровень воды в деаэраторе поз. Е-2 (60-70 %).. Предусмотрена сигнализация максимального (80%) и минимального (40%) уровня деминерализованной воды в баке деаэратора поз. Е-2.
Деаэрированная вода с температурой 102-104°C и с содержанием кислорода не более 0,3 мг/дм³ на выходе из деаэратора поз. Е-2 проходит теплообменник поз. Т-4, где охлаждается до температуры не более
35-45 ºC охлажденной оборотной водой и поступает на всас насосов промывной воды поз. Р1001/ А,В,С,Д,Е.
2.4.2. Очистка исходного газа от аммиака
Исходный газ от агрегатов №2 и №3 производства аммиака поступает на установку очистки от аммиака. Очистка газа от аммиака необходима, т.к. аммиак, содержащийся в исходном газе, попадая в низкотемпературную часть установки, может вызвать забивку аппаратуры и коррозию деталей, выполненных из цветных металлов.
Очистка производится в колонне абсорбции промывной водой. Исходный газ с объемным расходом 6000-10000 м³/ч (при н.у.) под избыточным давлением 2,942-3,432 МПа (30-35 кгс/см²) с температурой минус 10-35 ºС, с объёмной долей аммиака не более 4% поступает в нижнюю часть промывной колонны К1001. Колонна имеет насадку из металлических колец Рашига.
Для подержания необходимой температуры исходного газа, на входе в колонну поз. К1001 предусмотрен паровой подогреватель поз. W1002.
Вода для промывки поступает из установки деаэрирование с объемным расходом 3,2-6,0 м³/ч на насосы поз. Р1001/А, В, С, Д, Е, после которых с избыточным давлением 3,138-4,119 МПа (32-42 кгс/см²) проходит холодильник промывной воды поз. W1001, охлаждается жидким аммиаком, кипящим при давлении 333,4-411,9 кПа (3,4-4,2 кгс/см²) и с температурой плюс 5-10 °C направляется в верхнюю часть промывной колонны на орошение насадки.
В ходе моих исследований я пришел к выводу, что лучше охлаждать промывную воду в теплообменнике поз. W1001 не жидким аммиаком, а исходным газом, который приходит с агрегата аммиака №2 или №3 с температурой минус 35 ºC. При такой модернизации на участке разделения остаточных газов появляется возможность отказаться от использования дорого продукта - аммиака для захолаживания промывной воды.
Из куба колонны поз. К1001 отбирается аммиачная вода с массовой долей аммиака 2-10 %, которая направляется на отпарную колонну агрегатов аммиака №2 или №3 производства аммиака или в цех производства аммиачной воды.
Влажный исходный газ после промывной колонны с избыточным давлением 2,942-3,432 МПа (30-35 кгс/см²), с температурой 5-30 ºС и с объемной долей аммиака не более 0,0005% (5ppm) поступает на установку осушки в один из осушителей Т2001/ А,В.
2.4.3. Осушка исходного газа от влаги
После очистки от аммиака исходный газ направляется в один из двух переключающихся силикагелевых осушителей - адсорберов поз. Т2001 А, В, где происходит осушка до объемной доли водяных паров не более 0,002% (20 ppm).
При осушке исходный газ направляется снизу вверх.
Адсорберы Т2001 переключаются через каждые 24 часа работы.
Отбросной газ с объемным расходом 500-1500 м³/ч (при н.у.) нагревается в паровом подогревателе W2003 паром с избыточным давлением 882,6-1078,7 кПа (9,0-11 кгс/см²) до температуры 160-185 ºС и направляется в регенерируемый адсорбер поз. Т2001. При регенерации газ подается сверху вниз. Сброс газа осуществляется в атмосферу через автономную свечу.
Процесс десорбции влаги из силикагеля заканчивается, когда температура газа на выходе из адсорбера достигнет 100 °С, после чего проводится охлаждение адсорбера до температуры 15-20 °С отбросным газом или азотом, направляемым мимо парового подогревателя поз. W2003.
После охлаждения происходит переключение, при этом отбросной газ сбрасывается в атмосферу, минуя адсорберы поз. Т2001 А, В.
В подогреватель поз. W2003 подается пар с избыточным давлением 882,6 -1274,9 кПа (9,0-13,0 кгс/см²) с температурой 165-250°C из заводской сети. Конденсат из подогревателя поз. W2003 отводится на установку деаэрирование.
После осушки исходный газ с давлением 2,942-3,432 МПа (30-35 кгс/см²) и с температурой 10-35 °С направляется в низкотемпературный блок разделения газов.
2.4.4. Низкотемпературное разделение исходного газа
Очищенный от аммиака и осушенный от влаги исходный газ поступает в блок разделения газов, проходит последовательно теплообменники витого типа поз. W3011, W3012, W3013, в которых он охлаждается продуктами разделения: азота-водородной смесью, метановой фракцией, отбросанным газом, газообразным азотом из колонны поз. К3030, а также конденсатом из куба поз. W3010 в теплообменнике поз. W3013. Кроме того, после теплообменника поз. W3011 исходный газ дополнительно охлаждается жидким метаном в змеевике испарителя колонны поз. К3020 до температуры минус 125 - минус 105 °С. В теплообменниках поз. W3011, W3012, W3013 происходит охлаждение и частичная конденсация метана (Ткип = минус 164°С). Охлажденная до температуры минус 168 - минус 150 °С, парожидкостная смесь после теплообменников поступает в конденсатор поз. W3010.
1. Конденсатор исходного газа поз. W3010 (водородная колонна)
Конденсатор исходного газа поз. W3010 - колонна с двумя встроенными дефлегматорами, тремя витыми теплообменниками и насадкой из алюминиевой спирали. В теплообменниках витого типа конденсатора поз. W3010 газ охлаждается продуктами разделения: отбросным газом, газообразным азотом, азотоводородной фракцией. В дефлегматорах охлаждение проводится жидким азотом, кипящим под избыточным давлением:
- 470,7-764,9 кПа (4,8-7,8 кгс/см²) - азот среднего избыточного давления (в среднем дефлегматоре);
- 9,8-34,3 кПа (0,10-0,35 кгс/см²) - азот низкого избыточного давления (в верхнем дефлегматоре).
При охлаждении газа до температуры минус 190 - минус 195 °С в конденсаторе поз. W3010 из него конденсируется значительная часть высококипящих компонентов: метана, аргона, азота.
С верхней части конденсатора поз.W3010 отводится водородная фракция (азота - водородная смесь) с объёмной долей:
водорода (Н2) - 91,8 - 93,0 %
азота (N2) - 6,9 - 8,1 %
аргона (Ar) - не более 0,1 %
После рекуперации холода в конденсаторе поз. W3010 и теплообменниках поз. W3013, W3012, W3011 азотоводородная фракция с избыточным давлением 2,942-3,432 МПа (30-35 кгс/см²) и с температурой минус 5 - плюс 20 °С выходит из блока разделения и направляется на агрегаты №2 или №3 производства аммиака. Предусмотрена подача азотоводородной смеси в цеха азотной кислоты, в цех метанола с избыточным давлением 0,883-1,373 МПа (9,0-14,0 кгс/см²).
Образующийся в процессе охлаждения исходного газа конденсат представляет собой смесь жидкого метана, азота и аргона, в котором растворен водород. Конденсат отводится из нижней части конденсатора поз. W3010, дросселируется до избыточного давления 0,883-1,177 МПа (9,0-12,0 кгс/см²) и после частичного испарения в теплообменнике поз. W3013 поступает на разделение в метановую ректификационную колонну поз. K3020. Уровень в кубе конденсатора поз. W3010 (20-50 %).
2. Метановая колонна поз. К3020
Метановая колонна служит для разделения 3-х компонентной смеси с выделением метановой фракции. Колонна имеет 60 ситчатых тарелок, дефлегматор и два медных трубчатых теплообменника.
Необходимое для осуществления процесса ректификации тепло в куб колонны подводится с охлажденным исходным газом и с охлажденным циркуляционным азотом. Флегма образуется в дефлегматоре за счет испарения жидкого азота среднего давления.
Из испарителя метановой колонны отбирается метановая фракция с объёмной долей:
- метана (СН4) - не менее 98,0 %;
- аргона и азота (Ar + N2) - не более 2,0 %.
Далее метановая фракция после рекуперации холода в теплообменнике поз. W3011 выводится из низкотемпературного блока и с давлением 0,883-1,177 МПа (9,0-12,0 кгс/см²) и с температурой минус 5 - плюс 20°С направляется на агрегаты №2 или №3 производства аммиака.
Сопротивление укрепляющей части метановой колонны обеспечивает требуемую чистоту (по метану) азотоаргонной фракции.
Уровень в испарителе метановой колонны поз. К3020 20-40%. Из верхней части колонны поз. К3020 выводится газообразная азотоводородо-аргоновая фракция, которая поступает на разделение в аргонную колонну поз. К3030.
3. Аргонная ректификационная колонна поз. К3030
Аргонная ректификационная колонна служит для выделения чистого аргона из 2-х компонентной смеси. Колонна имеет насадку из 65 ситчатых тарелок, встроенный дефлегматор и встроенный змеевик жидкого азота.
Тепло, необходимое для процесса ректификации, подводится в колонну поз. К3030 с газообразным азотом среднего избыточного давления, который конденсируется в трубках выносного испарителя поз. W3031. Флегма образуется в дефлегматоре, охлаждаемом жидким азотом низкого давления. Стекая вниз по тарелкам, флегма обогащается высококипящим компонентом - аргоном, а пары азота и аргона, поднимаясь вверх, обогащаются низкокипящим компонентом - азотом. В результате ректификации в кубе колонны образуется чистый аргон, а наверху колонны - чистый азот.
Жидкий аргон из нижней части колонны поз. К3030 сливается в выносной испаритель поз. W3031, откуда в качестве товарного продукта поступает в стационарные емкости поз. В5051/А,В.
Образующейся на верхней тарелке колонны поз. К3030 жидкий азот сливается в стационарные емкости поз. В5052/А,В или подаётся в дефлегматоры аргонной и водородной колонн для поддержания уровня жидкого азота в испарителе поз. W3031. Остальная часть после испарения в змеевике колонны поз. К3030 и рекуперации холода в конденсаторе поз. W3010 и теплообменниках поз. W3013 и W3012, W3011 выводится из блока разделения и используется для восполнения потерь азота в азотном холодильном цикле и поддувах кожуха блока разделения.
Отбросная фракция из дефлегматоров колонны поз. К3030, выносного испарителя поз. W3031 и с бокового отвода колонны поз. К3030 с объёмной долей:
водорода (Н2) - 11,0 - 19,0 %
азота (N2) - 75,0 - 85,0 %
аргона (Ar) - 2,0 - 68,0 %
после рекуперации холода в конденсаторе поз. W3010 и теплообменниках поз. W3013, W3012, W3011 с избыточным давлением 63,7 - 156,9 кПа (0,65 -1,60 кгс/см²) и с температурой минус 5 - плюс 20 С° выводится из низкотемпературного блока, используется для регенерации осушителей поз. Т2001 и выбрасывается в атмосферу.
2.4.5. Азотный холодильный цикл
Для покрытия потерь холода и создания флегмы в ректификационных колоннах используется азотный холодильный цикл.
Азот высокого избыточного давления 5,884-9,807 МПа (60-100 кгс/см²) поступает в блок разделения после компрессоров поз. YV4141/А,В, охлаждается последовательно в нижнем змеевике теплообменника поз. W3040 обратным потоком азота и в змеевике испарителя метановой колонны поз. К3020. Затем поток азота высокого избыточного давления делится на две части, одна из которых охлаждается обратным потоком азота низкого избыточного давления 9,8-34,3 кПа (0,1-0,35 кгс/см²) в среднем змеевике поз. W3040, а второй - в детандерном теплообменнике поз.W3043 парами азота среднего избыточного давления 470,7-764,9 кПа (4,8-7,8 кгс/см²). . Охлажденный до температуры минус 135 - минус 145°С азот дросселируется клапанами А 30-061 и А 30-062 с высокого избыточного давления 5,884-9,807 МПа (60-100 кгс/см²) до среднего избыточного давления 470,7-764,9 кПа (4,8-7,8 кгс/см²) и поступает в дефлегматор метановой колонны поз. К3020, откуда часть жидкого азота отбирается в средний дефлегматор конденсатора поз. W3010, а избыток его сливается в выносной испаритель поз. W3031 аргонной колонны.
Жидкий азот из выносного испарителя поз. W3031 после охлаждения в верхней части поз. W3040 дросселируется со среднего избыточного давления 470,7-764,9 кПа (4,8-7,8 кгс/см²) до низкого избыточного давления 9,8-34,3 кПа (0,1-0,35 кгс/см²) и испаряется в дефлегматоре аргонной колонны поз. К3030 и в верхнем дефлегматоре конденсатора поз. W3010.
Пары азота из среднего дефлегматора конденсатора поз. W3010 и дефлегматора метановой колонны поз. К3020 объединяются и вновь делятся на три потока:
- первый поток после подогрева в теплообменнике поз. W3043 до температуры минус 115 - минус 143°С расширяется в турбодетандере поз. V3501 до низкого избыточного давления 9,8-34,3 кПа (0,1-0,35 кгс/см²);
- второй поток конденсируется в выносном испарителе поз. W3031 аргонной колонны поз. К3030;
- третий поток дросселируется клапаном А 30 - 063 со среднего избыточного давления 470,7-764,9 кПа (4,8-7,8 кгс/см²) до низкого избыточного давления 9,8-34,3 кПа (0,1-0,35кгс/см²) и поступает в обратный поток азотного теплообменника поз. W3040 между верхним и средним змеевиками.
Пары азота низкого избыточного давления из верхнего дефлегматора конденсатора поз. W3010 и дефлегматора аргонной колонны поз. К3030 объединяются с потоком азота после турбодетандера в обратный поток, который рекуперирует свой холод в теплообменнике поз. W3040 и поступает на компрессорные установки поз. V4141/А,В, где сжимается до избыточного давления 5,884-9,807 МПа (60-100 кгс/см²) и вновь подается в блок разделения.
Все технологическое оборудование, арматура и трубопроводы низкотемпературного блока разделения исходного газа размещены в двух стальных кожухах, заполненных теплоизоляционным материалом - перлитом. Для предотвращения возможности образования внутри кожухов взрывоопасной смеси в результате утечек из оборудования исходного газа или фракций и попадания воздуха из окружающей атмосферы, в обоих кожухах поддерживается небольшое избыточное давление за счет постоянного поддува, в них азота со сбросом в атмосферу.
Для предотвращения чрезмерного повышения избыточного давления в изоляционных кожухах и их разрушения оба кожуха снабжены специальными дыхательными устройствами поз. F3045 А и В, которые сбрасывают избыток газа из кожуха в атмосферу.
2.4.6. Турбодетандер
Турбодетандер включен в азотно-холодильный цикл, как машина, вырабатывающая холод, в которой механическая энергия, освобождающаяся при расширении газа, превращается во внешнюю работу с одновременным понижением температуры рабочего газа.
Турбодетандер представляет собой радиальную центростремительную реактивную турбину. Рабочее колесо турбины закрепляется на валу, расположенного на двух подшипниках скольжения корпуса турбины. Вал вращается со скоростью 18800 об/мин и связан с планетарным редуктором зубчатой муфтой. Редуктор снижает число оборотов до 3000 об/мин и соединяется с асинхронным генератором эластичной муфтой.
Азот поступает через запорный вентиль А30-122 и быстродействующий клапан А30-650 во входную спираль корпуса турбодетандера. Далее азот протекает по направляющим лопаткам на рабочее колесо турбины.
Регулировка количества газа, поступающего на рабочее колесо турбодетандера, производится посредством изменения ширины направляющего канала. От рабочего колеса азот выходит в осевом направлении, поступает в диффузор и далее по трубопроводу и через выходной вентиль А30-123 направляется в аппарат.
Для быстрого прекращения подачи азота в турбину на входе в нее встроен аварийный клапан. При безаварийной работе клапан находится в открытом положении от действия электромагнита. Клапан автоматически закрывается при любом нарушении работы турбодетандера.
Редуктор одноступенчатый планетарный механизм с вращающимся носителем сателлита состоит из двух внешних колес, которые закреплены в корпусе редуктора при помощи трех демпферов. Демпферы устанавливаются на цапфы, которые прикрепляются на винтах к внешнему колесу. Носитель сателлита имеет с одной стороны полую цапфу. Цапфы находятся на подшипниках скольжения в корпусе редуктора. В носителе спрессованы три цапфы. На цапфе имеется сателлит.
Между сателлитами свободно располагается колесо, на одной стороне которого предусмотрено зубчатое сцепление для передачи крутящего момента. Зубчатка сцепления центрального колеса соединена посредством двойной цепной связи с зубчатым сцеплением соединительной муфты, установленной на одном конце ротора турбины. Нижняя часть корпуса редуктора является коллектором, откуда масло подается вместе со смазкой подшипника турбины в общий сборник.
Смазка подается при помощи винтового маслонасоса, расположенного в торцевой части редуктора. На торце редуктора имеется центробежный регулятор, защищающий турбину от превышения числа оборотов.
В качестве генератора на турбодетандере используется электродвигатель с короткозамкнутым сердечником. При сверхсинхронном числе оборотов ~ 3050 об/мин он работает как асинхронный генератор.
Система смазки: масло всасывается главным насосом через фильтр. Главный насос находится на торце планетарного механизма и всасывает 48 л/мин масла. Для предотвращения увеличения давления масла в системе на трубопроводе имеется предохранительный клапан, через который масло переливается обратно в резервуар.
Перед подачей масла на смазываемые поверхности масло очищают в маслофильтре. На панели управления можно контролировать потерю давления масла в фильтре.
Для пуска и выбега на раме находится вспомогательный маслонасос, который запускается автоматически при минимальном давлении, установленном на контактном манометре. Максимальное давление в маслосистеме не должно превышать 3,5 кгс/см2.
Предусмотрена остановка турбодетандера при достижении блокировочных значений следующих параметров:
- понижение температуры азота на входе в турбодетандер до минус 150 ºC;
- повышение температуры подшипников турбодетандера до 58 °C;
- повышение температуры масла до 60 °C;
- падение давления смазочного масла до или после фильтра до 88,3 кПа (0,9 кгс/см2);
- превышение числа оборотов до 3300 об/мин.
При срабатывании блокировки происходит автоматическое закрытие отсекателя А 30-650 на входе азота в турбодетандер.
Газообразный азот, выходящий из блока разделения, поступает на всас компрессорных установок поз. V-4141/A, В, сжимается до давления 5,884- 9,807 МПа (60-100 кгс/см2) и вновь подается в блок разделения. Для поддержания давления на всасе азотных компрессоров поз. V-4141 А/В предусмотрен автоматический регулятор PIC-4001. Необходимое давление 2,942-7,845 кПа (0,03-0,08 кгс/см2) поддерживается подпиткой азота из коллектора (при недостатке азота в системе) или сбросом части азота в коллектор в атмосферу (при его избытке).
Все технологическое оборудование, арматура и трубопроводы низкотемпературного разделения исходного газа размещены в двух стальных кожухах, заполненных теплоизоляционным материалом-перлитом.
Для предотвращения возможности образования внутри кожуха взрывоопасной смеси в результате утечек из оборудования исходного газа или фракций и попадания воздуха из окружающей атмосферы в обоих кожухах поддерживается небольшое избыточное давление за счет постоянного поддува в них азота со сбросом в атмосферу.
Для предотвращения чрезмерного повышения давления в изоляционных кожухах и их разрушения оба кожуха снабжены специальными дыхательными устройствами поз.F-3045 А и В, которые сбрасывают избыток газа из кожуха в атмосферу.
2.4.7. Хранилище жидкого аргона и азота
Продуктовый жидкий аргон из выносного испарителя поз. W3031 аргонной колонны сливается в одну из двух стационарных емкостей поз. В5051 А,В вместимостью 50 м3 каждая.
Жидкий продуктовый азот из верхней чаши аргонной колонны отводится в аналогичные стационарные емкости жидкого азота поз. В5052
А, В.
Пары аргона образующиеся за счет теплопритока в сливном трубопроводе и емкостях поз. В5051 А,В с избыточным давлением 49,0-127,5 кПа (0,50-1,30 кгс/см²) направляются в конденсатор поз. W5051, в котором сжижаются за счет охлаждения конденсатора поз. W5051 жидким азотом, подаваемым из карманов дефлегматора колонны поз. К3030. Жидкий аргон самотеком сливается обратно в емкости поз. В5051 А,В. Пары азота возвращаются в верхнюю часть аргонной колонны поз. К3030. Избыточное давление испарения азота поддерживается регулятором PICAНL-5001 в пределах не более 196,2-245,2 кПа (2,0 не более 2,5 кгс/см²).
Пары азота из емкостей В5052 А,В также возвращаются в верхнюю часть колонны поз.К3030. Жидкий азот поступает в конденсатор поз. W5051 из верхней чаши аргонной колонны или из емкостей поз. В5052 А,В ( при работе в режиме одного компрессора).
2.5. Характеристика основного оборудования
Очистка и осушка исходного газа
1) Промывная колонна поз. К-1001
Предназначена для проведения процесса абсорбции аммиака из исходного газа промывной водой.
Это вертикальный цилиндрический аппарат, выполненный из углеродистой стали.
Колонна насадочная.
Н = 18000 мм, D = 1200/800 мм, W = 11500 кг, Vаппарата = 8,38 м2
Насадка из стальных колец Рашига
Размер насадки - 25х25х1 мм
Vнасадки = 6,3 м3
Рраб. = 4,315 МПа (44 кгс/см2)
Траб. = 50 °C
Ррасч. = 4,315 МПа (44 кгс/см2)
2) Подогреватель исходного газа, поз W-1002
Предназначен для поддержания необходимой температуры исходного газа на входе в колонну.
Это горизонтальный теплообменник типа “труба в трубе”, выполненный из углеродистой стали.
L = 5400 мм, D = 200 мм
Межтрубное пространство - пар
Рраб. пара = 0,7 МПа (7,14 кгс/см2)
Траб. пара = 300 °C
Трубное пространство - исходный газ
Рраб. = 4,315 МПа (44 кгс/см2)
Траб. = 300 °C
3) Холодильник промывной воды, поз W-1001.
Предназначен для охлаждения промывной воды перед подачей в колонну абсорбции жидким аммиаком.
Это вертикальный кожухотрубный теплообменник из углеродистой стали.
Н = 4595 мм, D = 600 мм, W = 2100 кг
Межтрубное пространство - аммиак
Рраб = 2,059 МПа (21,0 кгс/см2)
Траб. = минус 3°C
Трубное пространство - вода
Рраб. = 4,315 МПа (44,0 кгс/см2)
Траб. = 35°C
Ррасч. = 4,315 МПа (44,0 кгс/см2)
4) Осушители исходного газа, поз Т-2001 А, В. предназначены для проведения процесса адсорбции влаги исходного газа после промывной колонны силикагелем.
Это вертикальный цилиндрический сосуд из углеродистой стали, заполнен силикагелем.
Н = 4600 мм, D = 800 мм, W = 3000 кг
V = 1,84 м3
Вес силикагеля - 750 кг в каждом аппарате
Рабочая среда - исходный газ
Рраб. = 4,315 МПа (44,0 кгс/см2)
Траб. = 175 °C
5) Подогреватель регенерирующего газа, поз W-2003
Предназначен для нагревания отбросной фракции или газообразного азота, поступающих на регенерацию силикагеля в адсорберы.
Это вертикальный кожухотрубный теплообменник из углеродистой стали.
Н = 3000 мм, D = 430 мм, W = 1200 кг
Межтрубное пространство - пар
Рраб. = 1,667 МПа (17,0 кгс/см2)
Траб. = 200°C
Трубное пространство - регенерирующий газ
Рраб. = 0,147 МПа (1,5 кгс/см2)
Траб. = 200°C
Дата добавления: 2020-12-12; просмотров: 48; Мы поможем в написании вашей работы! |
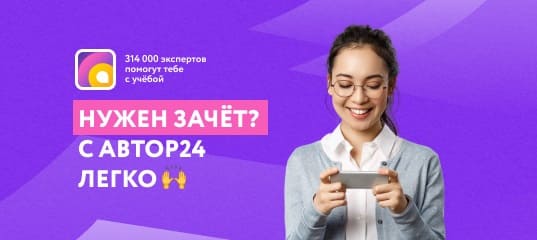
Мы поможем в написании ваших работ!