Единая система допусков и посадок.
Лекция №13. . Тема 4: Соединения деталей машин.
Для выполнения заданных функций машины детали вводят в контакт. Взаимодействующие детали могут быть подвижными одна относительно другой и неподвижными (рисунок 4.1).
Рисунок 4.1.- Классификация соединений
Под неподвижными понимают соединения двух или нескольких деталей, которые в процессе работы не совершают относительного движения. Необходимость применения неподвижных соединений возникает в связи с требованиями расчленения машины на сборочные единицы для удобства обработки, сборки и ремонта.
Необходимость подвижных соединений определяется кинематикой машины, т.к. во время работы детали совершают относительное перемещение, предусмотренное их функциональным назначением.
Взаимная неподвижность деталей обеспечивается с помощью конструктивных и технологических средств, называемых соединениями, которые могут быть разъемными и неразъемными.
Разъемные соединения допускают разборкусоединяемых деталей без повреждений. К ним относятся соединения резьбовые, зубчатые (шлицевые), шпоночные, клемовые и другие.
Неразъемные соединения, к которым относятся сварные, паяные, клеевые, заклепочные и др. при разборке не сохраняют целостность конструкции.
Промежуточное положение между разъемными и неразъемными занимают соединения с гарантированным натягом, в которых сохранность конструкции обеспечивается специальными технологическими приемами.
|
|
Критериями работоспособности соединений деталей является прочность (статическая и циклическая) и износостойкость. Важным критерием работоспособности во многих соединениях является герметичность. В ряде случаях существенным показателем является жесткость соединений.
Сварочные соединения – это соединение частей детали в одно целое за счет местного нагрева соединяемых частей ее до расплавленного или пластического состояния. На рисунке 4.2 представлены различные типы сварных соединений и швов.
Рисунок 4.2. – Классификация сварных соединений и швов
Наиболее рациональным видом сварных соединений является стыковое соединение, получаемое дуговой или контактной сваркой. Для повышения прочности стыковых соединений используют косые швы. Стыковые соединения рассчитывают по номинальным напряжениям, величина которых не должна превышать допускаемое значение, установленное нормативами. При совместном действии нормальных и касательных напряжений расчет проводят по приведенным напряжениям, величина которых устанавливается по третьей теории прочности.
|
|
При действии растягивающей (или сжимающей) силы F напряжение s ш равно
s ш=F/A=F/(hl) £ [ или s ш=F/A=F/(hl) £.
(4.1)
При действии изгибающего момента
s ш=M и / W ш =6 M и //( hl 2 )£ [ , (4.2)
где W ш – момент сопротивления сечения сварного шва.
При действии перерезывающей силы Fп
tш= Fп S ш /(Jш h)£ , (4.3)
где S ш – статический момент относительно нейтральной оси части сечения сварного шва, расположенной выше (ниже) рассматриваемого волокна; Jш – момент инерции сечения сварного шва.
При одновременном действии силы F и момента M и получим
s ш=F/(hl)+ 6 M и //(hl2)£ [ . (4.4)
Допускаемое напряжение для сварочных швов определяют как долю допускаемого напряжения основного металла.
При расчете сварных конструкций на выносливость допускаемое напряжение для основного металла и сварного шва уменьшают по сравнению c допускаемыми напряжениями
и
, которые рекомендованы в расчетах при статическом нагружении:
=
или
. (4.5)
Коэффициент понижения допускаемых напряжений g учитывает: тип соединения, что определяет характер распределения напряжений по сечению; характеристику цикла R; марку стали; эффективные коэффициенты концентрации в сварных швах K s; число циклов нагружения
|
|
g=1/[(aK s ± b) – (aK s b) R] £1. (4.6)
Верхние знаки принимают, если наибольшими по абсолютной величине являются напряжения растяжения, а нижние – если напряжения сжатия. В случае равенства абсолютных напряжений можно принимать как верхние, так и нижние знаки.
Коэффициенты а и b принимают: для углеродистых сталей а=0,58 и b =0,26; для низколегированных сталей а=0,65 и b =0,30.
Заклепочные соединения представляет собой деталь, состоящую из двух и более элементов, соединенных между собой заклепками – стержнями круглого сечения с закладными головками, которые установлены в совмещенные отверстия, с последующим формообразованием замыкающих головок.
В зависимости от назначения заклепочные соединения разделяют на прочные и прочно – плотные (рисунок 4.3).
Рисунок 4.3. – Классификация заклепочных соединений
Клепаные соединения хорошо работают в конструкциях, подверженных резко выраженной вибрационной нагрузке, а также при соединении элементов, не допускающих нагрева при сварке.
|
|
Заклепочные соединения, как правило, загружены силами, действующими в плоскости стыка. Заклепку рассчитывают на срез и на смятие. При этом допускаемые напряжения и
условны, т.к. в таком соединении нагрузка передается, в основном, за счет сил трения. Условие прочности на срез в предположении равномерного распределения нагрузки между заклепками устанавливается по формуле
tс=4F /(pd 2 zi ) £[tс], (4.7)
откуда количество заклепок
z =4F/(p d 2 [tс] ). (4.8)
Условие прочности заклепки на смятие
sсм =F/(dhz) £[sсм], (4.9)
а необходимое количество заклепок
z ³ F/(dh[sсм] ). (4.10)
Из двух найденных расчетом на срез и смятие значений z принимают большее. Длина заклепки выбирается в зависимости от ее диаметра и общей толщины соединения
l = d + ( d / dc)2 hc,
где d – диаметр отверстия; dc – диаметр стержня заклепки; h – наименьшая толщина соединяемых деталей; hc – суммарная толщина соединения; [tс] и [sсм] – допускаемые напряжения, соответственно на срез и смятие заклепки.
В случае, когда на соединение действует переменная нагрузка циклического характера, то допускаемое напряжение, установленное для статических нагрузок понижают с помощью коэффициента g:
для соединений из малоуглеродистых сталей
g=1/(1– 0,3 Fmin / Fmax); (4.11)
для соединений из среднеуглеродистых сталей
g=1/(1,2 – 0,8 Fmin / Fmax). (4.12)
Силы Fmin и Fmax входят каждая со своим знаком.
Помимо расчета заклепки на прочность проверяют также напряжения в соединяемых элементах с учетом ослабления их отверстиями.
При расчете соединений допускаемые напряжения принимают в соответствии с рекомендациями, основанными на опыте эксплуатации. Для заклепок из углеродистых сталей [tс]= 100…140 МПа, [sсм] = 240…320 МПа.
Резьбовые соединения. Резьбовыми являются разъемные соединения, в которых сопряженные детали соединяются с помощью резьбы или резьбовыми крепежными деталями – болты, шпильки, гайки, винты и др.
В зависимости от формы поверхности, на которойобразована резьба различают цилиндрические и конические резьбы. Резьба может быть нанесена на внутренней или внешней поверхности и иметь правое или левое направление. Основные профили резьбы и ее параметры регламентированы государственными стандартами.
В зависимости от формы резьбового контура различают: треугольную цилиндрическую и коническую резьбы, трапецеидальную симметричную и несимметричную – упорную и другие резьбы. В качестве крепежных резьб распространение получили резьбы с треугольным профилем метрические.
В зависимости от числа заходов резьбы бывают одно-двухзаходные и т.д. Расстояние между одноименными точками смежных витков, измеренные вдоль оси называют шагом резьбы. В зависимости от назначения различают резьбовые соединения прочные прочно – плотные
(рисунок 4.4).
Рисунок 4.4. – Классификация резьбовых соединений
По количеству болтов (шпилек, винтов) различают резьбовые соединения с одиночным болтом и группой болтов. Различают соединения с предварительной затяжкой и без предварительной затяжки.
В большинстве случаев резьбовые детали находятся в предварительно затянутом состоянии, что обеспечивает плотность стыка, предотвращает относительное скольжение и раскрытие стыка под действием переменных нагрузок.
Условие прочности для соединений, собираемых без предварительной затяжки и нагруженных растягивающей силой F, направленной по оси болта, имеет вид
sр= 4F/(p [sр]. (4.13)
Из приведенного выражения внутренний диаметр d1 равен
d1= .. (4.14)
Условие прочности для резьбовых деталей, которые предварительно нагружены осевой силой F имеет вид
sэ= £sр, (4.15)
где t = Мк / Wк=[0,5F d2 tg(y+j¢)]/(0,2 ).
Для стандартных болтов можно принимать d2= 1,12 d1; при d<50 мм tg y»0,0194…0,0433 (в среднем tg j¢» 0,2) получим t/sр=0,5 и sэ» 1,3sр. На основании этого с достаточной точностью расчет можно вести только на растяжение, но по увеличенной на 30% расчетной нагрузке:
d1³ . (4.16)
Данные для выбора [sр] приведены в справочниках: для меньших диаметров рекомендуется меньшие значения [sр] из-за возможного перенапряжения от затяжки.
Проверку прочности резьбы на срез под действием осевой нагрузки F производят по формуле
t = [tср], (4.17)
где H – высота гайки; k - коэффициент полноты, зависящий от типа резьбы: для треугольной резьбы k =0,75, трапецеидальной k =0,65, прямоугольной k =0,5; m - коэффициент, учитывающий неравномерность распределения нагрузки по виткам резьбы.
Допускаемое напряжение на срез [tср]=(0,2…0,3sт).
В соединении, подверженном действию циклически изменяющейся нагрузки работоспособность элементов устанавливают с учетом формы и параметров цикла нагружения при пониженных значениях допускаемых статических напряжений.
Единая система допусков и посадок.
Взаимозаменяемость – это принцип конструирования производства деталей, которая обеспечивает возможность правильной сборки ил замены при ремонте независимо изготовленных деталей и узлов без дополнительной их обработки при соблюдении требований качества.
Геометрические параметры деталей количественно оценивают посредством размеров. Размеры, указанные на чертежах, которые называют номинальными, не всегда совпадают с действительными размерами деталей. Функциональные значения деталей и характер их сопряжения можно установить назначением различных сочетаемых предельных размеров, обеспечивающих правильную сборку и нормальную работу узла и механизма.
Предельные отклонения размеров деталей определяются единой системой допусков и посадок.
Разность между наибольшим и наименьшим предельными размерами называют допуском. На рисунке 4.5 показаны цилиндрические отверстия и валы с предельными и номинальными величинами диаметров.
Рисунок 4.5. - Предельные размеры отверстия и вала, определяющие поля допусков.
Положение поля допуска ( IT ) относительно номинального размера определяется верхним и нижним предельными отклонениями. Верхним отклонением ( отверстия ES и вала es) называют алгебраическую разность между наибольшим предельным размером и номинальным, а нижним (отверстия EI и вала ei) – разность наименьшим и номинальным размерами.
При схематическом изображении поля допуска обычно показывают его положение относительно нулевой линии, условно изображающей его номинальный размер.
Расположение поля допуска принято обозначать букой или двумя буквами латинского алфавита – прописной для отверстий и строчной для валов.
Рисунок 4.6. – Схема расположения полей допусков
При сборке двух сопрягаемых деталей различают охватывающую и охватываемую поверхности, которые условно называют отверстием и валом. По разности отверстия и вала устанавливают относительное перемещение деталей. Характер соединения деталей называют посадкой. При сопряжении деталей может возникнуть зазор (положительная разность между размерами отверстия и вала, либо натяг (отрицательная разность между размерами отверстия и вала).
Все посадки подразделяют на три группы: подвижные, характеризуемые наличием зазора; неподвижные (прессовые), обеспечивающие натяг соединения и переходные, при которых возможно получение как натягов, так и зазоров.
Рисунок 4.7. – Схема образования посадок в системах отверстия и вала
Различают две системы образования посадок – система отверстия и система вала. Системой отверстия называют совокупность посадок, в которых предельное отклонения данного отверстий одинаковы для всех посадок, а различные посадки достигаются путем изменения предельных отклонений размеров валов. Такое отверстие называют основным и поле допуска его обозначают буквой Н, которое ставится после номинального размера детали, например:
Системой вала называют совокупность посадок, в которых предельные отклонения валов одинаковы (для данного интервала размеров и квалитетов точности), а различные посадки достигаются путем изменений предельных отклонений отверстий. В системе вала основной деталью является вал, а поле допуска его обозначается буквой h, которая ставится после номинального размера детали, например:
В обозначении посадки входит номинальный размер, общий для обоих соединяемых элементов (отверстия и вала), за которым следует обозначение полей допусков для каждого элемента, например:
Посадки с зазором (рисунок 4.7, поля 1) используют для получения подвижных соединений.
Переходные посадки (рисунок 4.7, поля 2) предназначаются для получения неподвижных соединений, подлежащих периодической разборке и сборке. В соединениях такого типа для предотвращения относительного движения деталей предусматривают фиксирующие устройства: штифты, шпонки и др.
Неподвижные посадки (рисунок 4.7, поля 3) обеспечивают получение неразъемных соединений без применения дополнительных крепежных устройств, только путем натяга.
Соединения с натягом обеспечивают неподвижное скрепление деталей за счет сил трения, возникающих между охватываемой и охватывающей поверхностями при сборке деталей по группе посадок с натягом.
Такой способ соединения применяют для сборки деталей, нагруженных значительными усилиями или подверженных воздействию вибраций и ударов: при соединении зубчатых колес с валами или бандажей червячных колес со ступицами. Сопрягающиеся поверхности при этом оказываются нагруженными давлением р , величина которого ,МПа, может быть посчитана по формуле
, (4.18)
где коэффициенты:
,
; (4.19)
d – номинальный посадочный диаметр сопрягающихся поверхностей, мм; d1 – диаметр отверстия охватываемой детали (для сплошного вала d1=0), мм; d2 – наружный диаметр охватывающей детали, мм; d расчетный натяг, мкм; Е1, ,
,
– модули упругости (МПа) и коэффициенты Пуассона материалов охватывающей и охватываемой деталей.
Расчетный натяг d, мкм, определяют по номинальному табличному натягу dТ с поправками, учитывающими его уменьшение вследствие сглаживания микронеровностей Rz 1 и Rz 2 в месте сопряжения поверхностей, различия рабочих температур t 1 и t 2 деталей и коэффициента линейного расширения a1 и a2 материалов сопрягаемых деталей:
d =dТ – 1,2(Rz 1 Rz 2)
[a2 (t 2
t )
a1 (t 1
t )] d ∙103, (4.20)
где t – температура в сборочном помещении.
Наибольший крутящий момент, которым может быть нагружено соединение
Т£ ; (4.21)
наибольшая осевая сдвигающая сила
Р£pd (4.22)
где f – коэффициент трения.
Шпоночные соединения осуществляется с помощью специальной детали шпонки, закладываемой пазы соединяемых деталей. Оно обеспечивает неподвижное скрепление соединяемых деталей и служит для передачи крутящего момента. На рисунке 8 представлены типы шпонок наиболее употребляемых в машиностроении: а) – клиновая врезная, создает напряженное состояние по широким граням шпонки и передает крутящий момент за счет сил трения на них; б) – призматическая обыкновенная со скругленными торцами, воспринимает давление боковыми узкими гранями; в) – призматическая врезная с креплением на валу, допускает перемещение детали вдоль оси вала; г) – сегментная, работает подобно призматической обыкновенной; д) – круглая цилиндрическая и коническая.
Рисунок 4.8.- Типы шпонок
Призматическая обыкновенная шпонка работает на смятие боковых граней и на срез. Размеры поперечного сечения шпонки (b ´ h) назначают в зависимости от диаметра вала d,мм, а длина ее l, мм, рассчитывается с учетом крутящего момента Т, Н∙м
, (4.23)
а из условия предупреждения среза шпонки
, (4.24)
где и
– допускаемые напряжения на смятие и на срез соответственно.
Дата добавления: 2020-12-22; просмотров: 283; Мы поможем в написании вашей работы! |
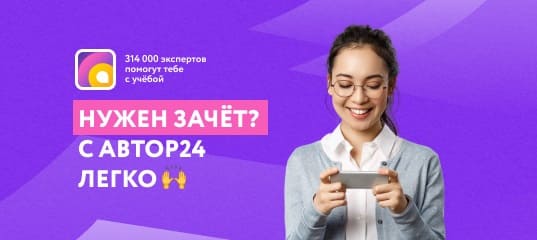
Мы поможем в написании ваших работ!