Определение производительности вращающейся печи. Расчет корпуса вращающейся печи
ОП.07 «Технологическое оборудование»
Ход работы над конспектом:
1) В тетради записать тему и на полях дату занятия.
2) Внимательно прочитать теорию по данной теме и записать в тетрадь.
Ход практической работы:
1) Практические работы № 11-12 «Определение производительности вращающейся печи. Расчет корпуса вращающейся печи» выполняем, пользуясь примерами в методических рекомендациях.
2) Вам нужно внимательно прочитать теорию и пользуясь примерами в методических рекомендациях рассчитать производительность вращающейся печи. На вопросы для самоконтроля ответить устно.
3) Практические работы выполнять на листах формата А4 по установленному образцу. В отчете записать название и цель работы.
4) Практические работы прислать на проверку 04.12.2020 г.
Тема: Холодильники вращающихся печей (барабанный, колосниковый, редукторный). Конвейерный кальцинатор (конструкция, принцип действия).
Практическая работа №11-12 Определение производительности вращающейся печи. Расчет корпуса вращающейся печи
Конвейерный кальцинатор
Конструкция конвейерного кальци натора (рисунок 6), позволяет вынести из корпуса вращающейся печи зоны сушки и подогрева материала.
Конвейерный кальцинатор представляет собой движущуюся со скоростью 0,067—0,137 м/сек бесконечную колосниковую решетку 1, на один конец которой поступает предварительно гранулированное сырье. В процессе грануляции сырье увлажняется до 10—14%.
|
|
Колосниковую решетку монтируют в неподвижном металлическом кожухе 2, отфутерованном огнеупорным кирпичом.
Конвейерный кальцинатор разделен перегородкой 3 на две камеры — сушки 4 и декарбонизации 5. Для создания разрежения в камерах кальцинатор оборудуют Двумя вентиляторами 6, 7, а для очистки газов после прохождения ими камер подогрева — циклонами З. Для разрушения затвердевшей корки сырьевой смеси, находящейся на решетке, в камере декарбонизации смонтирован неподвижный рыхлитель (на рисунке не показан), состоящий из трубы, к которой приварены плоские стальные пластины. Рыхлитель установлен над решеткой таким образом, чтобы пластины были погружены в сырьевую смесь на 50—60% своей длины. Установку рыхлителя в случае необходимости можно изменить по высоте. Для предупреждения перегрева рыхлителя по трубе последнего протекает холодная вода.
Рисунок 7- Конвейерный кальцинатор
При работе кальцинатора из гранулятора 9 гранулы размером 5—20 мм по течке 10 поступают на движущуюся колосниковую решетку 1 кальцинатора, а затем последовательно проходят камеры сушки и декарбонизации. Поток газов из вращающейся печи 11 поступает в верхнюю часть камеры 5, просасывается с помощью вентилятора 6 сквозь слой гранул и направляется на очистку в батарейные циклоны 8. Из циклонов газы направляются в верхнюю часть камеры сушки, а затем при помощи вентилятора 7 просасываются через слой гранул (в камере сушки) и далее уходят в атмосферу или на дополнительную очистку. Материал из кальцинатора поступает по течке 12 во вращающуюся печь 11. Материал, просыпавшийся сквозь щели решетки, попадает на цепной транспортер 13 и далее элеватором 14 подается в печь 11. Температура газов, поступающих из печи в камеру декарбонизации, около 1000° С, а из циклонов в камеру сушки — не выше 300° С. Температура сырьевой смеси, поступающей в печь, 800—1000° .
|
|
Холодильники вращающихся печей
Быстрое охлаждение клинкера, выходящего из печи с температурой 1000—1300 °С, до температуры 50— 150 °С производится в холодильниках различных конструкций: барабанные, колосниковые и рекуператорные..
Барабанный хо лодильник располагается под печью. Он устанавливается под углом 4—6° и наклонен в сторону, противоположную наклону печного барабана. Вследствие вращения и наклонного положения холодильника материал движется к его выгрузочному концу, охлаждаясь поступающим навстречу воздухом, который нагревается при этом до 200—350 °С. Часть холодильника, прилегающая к печи, футеруется шамотным кирпичом остальная часть имеет швеллеры для пересыпания клинкера.
|
|
|
Рисунок 8-Барабанный холодильник
Барабанными холодильниками открытого типа оборудованы короткие печи старых конструкций длиной до 70 м , производительностью 3,3—4,2 кг/сек. Барабанный холодильник (рисунок 8): состоит из цельносварной трубы (барабана) 1, опирающейся двумя бандажами 2 на опорные устройства 3. Длина барабана 15—30 м, диаметр 2,5—5 м, угол наклона 5—6°. Барабан приводится во вращение от электродвигателя 4 через редуктор 5, подвенцовую 6 и венцовую 7 шестерни. Часть барабана со стороны загрузки футеруют огнеупорным материалом, в остальной его части по окружности устанавливают пересыпающие полки. Со стороны выходной части барабана к нему по окружности прикрепляют сито 8. Клинкер из вращающейся печи 9 поступает в холодильник со стороны верхнего конца барабана, воздух с противоположной стороны. Охлажденный мелкий клинкер проваливается через сито, а крупные куски выходят через торцевую часть барабана.
|
|
Рекуператорные холодильники (рисунок 9), представляют собой несколько небольших охладительных барабанов (рекуператоров), расположенных вокруг головки печи и сообщающихся с ней. Рекуператорные холодильники снабжены полками, лопастями или цепями для лучшего пересыпания клинкера. Материал задерживается в холодильнике и тепло его передается проходящему сквозь холодильник воздуху, охлаждающему клинкер и идущему затем в печь. В рекуператорных холодильниках большая часть воздуха, проходящего через холодильники, вступает в непосредственное соприкосновение с охлаждаемым материалом, так что воздух поступает в печь более нагретым, чем в барабанных холодильниках.
Рисунок 9- Рекуператорный холодильник
Рекуператорными холодильниками оборудованы печи до 150 м, для более крупных печей путь клинкера в барабане рекуператора будет недостаточен и клинкер будет выходить с высокой температурой (около 400° С).
Конструкция рекуператорного холодильника, которым оборудована вращающаяся печь 3,6x150 м, представлена на рисунке 9. Холодильник состоит из десяти отдельных барабанов 1, расположенных по окружности выходного конца печи 2. Барабаны крепят к корпусу печи с помощью диафрагм 3, которые соединены между собой при помощи пластин 4, болтов 5 и прокладок 6. Диафрагмы позволяют компенсировать тепловые расширения. В торцовой части барабаны соединяются между собой кольцом 7, составленным из отдельных секций. Соединение отдельных секций между собой осуществляют при помощи компенсаторов, что позволяет компенсировать тепловые расширения.
На боковую поверхность выходного конца барабана крепят решетку 13 для прохода мелкого клинкера. Крупные куски выпадают из барабанов через центральное отверстие колец 7.
Колосниковый холодильник (рисунок 10), представляет собой камеру с горизонтальной колосниковой решеткой.
Материал в колосниковых холодильниках движется с наибольшей скоростью и степень охлаждения клинкера в нем самая высокая. Температура выходящего из этих холодильников клинкера обычно не превышает 50— 60 °С.
|
1 — вентилятор для подачи охлаждающего воздуха; 2—привод; 3 —транспортер для удаления просыпи; 4 — дробилка; 5 — пылеулавливающее устройство; 6 — колосниковая решетка.
Рисунок 10 - Колосниковый холодильник
Продольные стенки камеры на уровне колосниковой решетки футеруются стальными бронеплитами, а выше колосниковой решетки — огнеупорным кирпичом. Клинкер из вращающейся печи через соединительную шахту попадает на неподвижные наклонные колосники и решетки, охлаждается воздухом, подаваемым под эти колосники вентилятором высокого давления напором 10000— 12000 Па (острое дутье). Высокое давление воздуха способствует более равномерному распределению слоя клинкера по ширине решетки, что необходимо для его дальнейшего охлаждения. Далее чередуются ряды подвижных и неподвижных колосников, образуя ступенчатую колосниковую решетку. Перемещение клинкера по решетке в сторону разгрузочного конца происходит в результате возвратно-поступательного движения подвижных колосников. Колосники изготовляют из жароупорной стали, они имеют щели для прохода воздуха. Живое сечение решетки 9,5—10 %. Охлаждают клинкер воздухом, поступающим под решетку от вентилятора общего дутья.
В горячей зоне холодильника воздух нагревается до 550—600 °С и поступает в печь в качестве вторичного, необходимого для горения топлива. Часть менее нагретого воздуха отсасывается дымососом и, после обеспыливания выбрасывается в атмосферу. Мелкие частицы клинкера, перемещаясь по колосниковой решетке, могут просыпаться через щели в подколосниковую камеру, откуда удаляются транспортером. Колосниковые холодильники бывают с одинарным или двойным прососом охлаждающего воздуха. В разгрузочном конце холодильника имеется неподвижная сортировочная решетка. Крупные частицы клинкера, задержанные на решетке, поступают в дробилку для измельчения.
Практическая работа № 11-12
Определение производительности вращающейся печи. Расчет корпуса вращающейся печи
Цель:
Освоить и закрепить практические навыки определения производительности и основных параметров печных агрегатов по заданным условиям, а так же выбора вспомогательного оборудования для данного вида печей
Задание:
Определить длину печей, тепловую мощность и производительность печных агрегатов диаметром 4,5 м (смотри по вариантам) мокрого способа при влажности шлама 38 %, сухого способа с циклонными теплообменниками при удельном расходе тепла qc = 3600 кДж/на 1 кг клинкера, с циклонными теплообменниками и декарбонизатором при qд = 1630 кДж на 1 кг клинкера.
Таблица 1 – Варианты заданий
Варианты | 1 | 2 | 3 | 4 | 5 | 6 | 7 | 8 | 9 | 10 |
D, м | 4,5 | 5,5 | 5 | 6 | 7 | 8 | 4 | 7 | 6,4 | 4,5 |
qд, кДж/кг | 1600 | 1650 | 1700 | 1750 | 1800 | 1900 | 1850 | |||
qс, кДж/кг | 3300 | 3400 | 3500 | 3600 | 3700 | 3800 | 3900 | 3500 | ||
Кw | 38 | 39 | 40 | 28 | 34 | 36 | 32 | 35 |
Методические указания
Рисунок 1 – Вращающаяся печь а – общий вид; б – кинематическая схема |
Вращающаяся печь с теплообменными устройствами внутри корпуса (5х 185 м) состоит из следующих основных узлов (рис. 1, а ): корпуса 1 с надетыми на него бандажами 2, роликовых опор 3, предохранительных упоров и контрольных роликов, установленных на опорах, и привода 4. Корпус представляет собой трубу с внутренним диаметром 5 л и длиной 185 м, уложенную на опоры. Труба сварена из стальных кольцевых обечаек и отфутерована внутри огнеупорным кирпичом. Подбандажные обечайки сваривают из листовой стали толщиной 60 мм , в зоне спекания — 40 мм, в остальных пролетах — 30 мм.
В пролетах между опорами для повышения поперечной жесткости корпуса установлены кольца жесткости 5. Бандажи, имеющие прямоугольную форму, устанавливают на корпусе печи свободно на регулировочных прокладках, меняя которые, получают необходимый, зазор между бандажом и корпусом. Корпус печи опирается на роликоопоры и имеет уклон 3,5%. Каждая опора состоит из двух роликов, монтируемых на станине. Угол между линией, соединяющей центры корпуса печи и ролика, и вертикальной плоскостью равен 30°. Оси опорных роликов установлены в подшипниках скольжения с бронзовыми вкладышами. В последнее время имеется тенденция к установке их на роликоподшипниках. Смазка подшипников жидкая; подают ее черпаками, расположенными на специальном кольце, закрепленном на оси. Подшипники роликоопор имеют водяное охлаждение. В каждом подшипнике установлены термометр и маслоуказатель для визуального контроля за температурой и уровнем масла, а также термосигнализатор, автоматически предупреждающий о перегревах. Для контроля за продольным перемещением печи на одной из опор устанавливают контрольные ролики, а на другой для фиксации — предохранительный упор, который удерживает печь от продольного перемещения в случае среза осей контрольных роликов.
На корпусе печи, на шарнирах (или рессорных подвесках) крепится зубчатый венец 6. Привод печи состоит из главных 7 и вспомогательных 8 электродвигателей и системы редукторов. Главные электродвигатели предназначены для вращения печи во время работы (с шестью скоростями от 0,010 до 0,20 об/сек). Вспомогательный привод предназначен для проворачивания корпуса печи во время ремонтных, футеровочных и аварийных работ. (Угловая скорость печи при работе вспомогательного привода составляет 0,0012 об/сек. Главный привод (рис. 1,) состоит из двух электродвигателей 1, двух редукторов 2, двух подвенцовых шестерен 3 и венцовой шестерни 4. Между редукторами главного привода и вспомогательными электродвигателями 5 устанавливают двухступенчатые редукторы 6. Для контроля угловой скорости печи на приводе имеется тахогенератор 7.
Печь может быть оборудована фильтром-подогревателем 9 (см. рис. 1, а), установленным внутри печи на расстоянии 2 м от холодного конца. Принцип работы фильтра-подогревателя основан на подогреве поступающего в печь шлама теплом отходящих газов. Газы проходят через смоченные шламом цепные полотна; при этом одновременно с подогревом шлама происходит осаждение части содержащейся в - газах пыли. Цепная завеса 10 с гирляндной навеской повышает теплообмен между шламом и отходящими газами. За цепной завесой, внутри корпуса печи, встроено теплообменное устройство ячейкового типа, которое обеспечивает подогрев обжигаемого материала. Теплообменник 11 состоит из литых жаростойких полок, одни концы которых крепят к корпусу печи, а вторые соединяют между собой попарно. Полки обеспечивают подъем материала, который затем свободно ссыпается с них.
Отходящие газы из печи поступают в пылеосадительные устройства (пыльную камеру, циклон, электрофильтр, рукавный фильтр с повышенной теплостойкостью), где происходит очистка газов от пыли.
Печь оборудована устройством для возврата пыли (за цепную завесу), уловленной пылеосадительными устройствами.
Печной агрегат представляет собой комплекс машин, механизмов и устройств, осуществляющих термохимический процесс обжига сырьевых материалов, охлаждение готового продукта— клинкера, обеспыливание отходящих дымовых газов и аспирационного воздуха, а также контроль и управление процессами.
Печные агрегаты разделяют по различным признакам:
- по способу производства — на печи мокрого, сухого и полусухого способов, а также с шахтными печами;
- по типу охладителей клинкера — на печи с рекуператорными (планетарными), колосниковыми, барабанными и другими охладителями;
- в зависимости от размеров вращающейся печи на длинные (80— 230 м) и короткие (до 80 м) печи.
Вращающуюся печь в зависимости от характера процессов, протекающих в обжигаемом материале, условно можно разделить на шесть зон: сушки, подогрева, декарбонизации (кальцинирования) экзотермических реакций, спекания и охлаждения.
Исходное сырье — шлам поступает в первую зону — зону сушки — с начальной влажностью 30— 50%. Часть этой зоны обычно оснащается цепными завесами различной конфигурации для интенсификации процесса сушки. По мере нагревания и испарения влаги происходит загустевание шлама, начинается его гранулирование, и в следующую зону — зону подогрева — материал входит с температурой 100—150 °С, а выходит с температурой 500—600°С.
Начиная с 600°С происходит слабый, а с повышением температуры до 900—1000°С усиливающийся до максимума процесс разложения карбоната кальция с выделением углекислого газа и образованием свободной извести (СаО2). Одновременно в этой зоне — зоне декарбонизации — происходит и образование кристаллов двухкальциевого силиката. Зона декарбонизации является основной теплопотребляющей зоной в печи.
Дальнейшее увеличение температуры материала до 1300°С происходит в зоне экзотермических реакций за счет выделения тепла при реакциях образования двухкальциевого силиката, алюминатов и алюмоферритов кальция. На этой стадии процесса появляется жидкая фаза, часть материала расплавляется и происходит образование трехкальциевого силиката.
Наиболее ответственной частью печи является зона спекания, где при температурах 1350— 1450 °С завершается процесс клинкерообразования. Результат обжига определяется количеством неусвоенной окиси кальция (СаОсв) и кристаллической структурой полученного клинкера. При правильном выборе режима работы зоны спекания и последующей его стабилизации можно снизить расход тепла на обжиг при сохранении заданного качества клинкера.
Пройдя зону спекания, в зоне охлаждения клинкер снижает свою температуру до 1100—1000 °С, а затем окончательно охлаждается в холодильнике. Вторичный воздух, отбирающий тепло от клинкера (200—250 ккал/кг клинкера), входит в печь с температурой 600—800 °С.
При мокром способе производства все эти зоны расположены непосредственно во вращающейся печи, причем более половины длины всей печи (50—60 %) приходится на подготовительные зоны (сушки и подогрева). При сухом способе процессы сушки, подогрева, а также частично декарбонизации, происходят в запечных теплообменниках, а остальные более высокотемпературные процессы — непосредственно в короткой вращающейся печи. В шахтных печах эти зоны не разграничивают, так как процессы обжига происходят без движения материала.
Печные агрегаты являются самым энергоемким оборудованием технологических линий производства цемента, на долю которых приходится около 80 % затрат тепловой и электрической энергии. Поэтому этот вид цементного оборудования подвергают постоянному совершенствованию, направленному на снижение этих затрат. При эксплуатации действующих линий ведут работы по снижению влажности шлама, использованию теплоты корпуса печи и отходящих газов и др.
Дано D = 4,5 м qд = 1630 кДж/кг qс = 3600 кДж/кг Кw= 38 % Найти: Lс = ? Lм= ? Lд= ? Qм= ? Qс= ? Qд= ? |
Длину печей определяем по формулам:
Длина вращающейся печи мокрого способа
LM = 41 · (Dп - 0,5) · Кп , м;
где Dп - внутренний диаметр корпуса печи, м;
Кп - поправочный коэффициент, Кп = 0,97 ÷ 1,03; в большинстве случаев принимают равным 1.
Длина вращающейся печи сухого способа с циклонными теплообменниками
Lс = 17 · (Dп - 0,5) · Кп , м;
Длина вращающейся печи сухого способа с циклонными теплообменниками и декарбонизаторами
LД = 20 · (Dп - 0,5) · Кп , м;
Подставляя значения получаем:
LM = 41 (4,5 — 0,5) 1 = 164 м, принимаем 1М = 170 м;
LC = 17 (4,5 — 0,5) 1 = 68 м, принимаем Lc = 70 м;
LД = 20 (4,5 — 0,5) 1 = 80 м.
Производительность печных агрегатов определяем по формулам:
Производительность печного агрегата мокрого способа (в т/м)
Qм = 3,6 Nтм Кп / qм ,
где
Nтм – тепловая мощность печного агрегата, кВт
q м – Удельный расход теплоты на обжиг 1 кг клинкера, кДж/кг
Удельный расход теплоты определяем по формуле :
qм = 17 · 103 · Кw
где
Кw - коэффициент влажности шлама (0,38)
qм = 17 ·103 ·0,38 = 6460 кДж на 1 кг клинкера
Производительность печного агрегата сухого способа с циклонными теплообменниками
QС = 3,6 Nтс Кп / qс
Производительность печного агрегата способа с циклонными теплообменниками и декарбонизаторами (в т/м)
Qд = 3,6 Nтд Кп / qд
Тепловая мощность печных агрегатов вычисляется по формулам:
Тепловая мощность печного агрегата мокрого способа
Nтм = 29 D2n LМ Kп
Тепловая мощность печного агрегата сухого способа с циклонными теплообменниками (в т/м)
Nтс = 45 D2n Lс Kп
Тепловая мощность печного агрегата сухого способа с циклонными теплообменниками и декарбонизаторами (в т/м)
Nтд = 38 D2n Lд Kп
Подставляя значения в формулы получаем:
Nтм = 29 · 4,52 · 170 · 1= 99832 кВт
Nтс = 45 · 4,52 · 70 · 1= 63788 кВт
Nтд = 38 · 4,52 · 80 · 1= 61560 кВт
Qм = 3,6 · 99832 · 1 / 6460 = 55,6 т/ч
QС = 3,6 · 63788 · 1 / 3600 = 63,8 т/ч
Qд = 3,6 · 61560 · 1 / 1630 = 135,9 т/ч
Вопросы для самоконтроля
1 Для чего предназначены вращающиеся печи?
2 Как классифицируются вращающиеся печи?
3 На какие зоны условно можно разделить вращающиеся печи?
4 Опишите устройство и принцип работы вращающейся печи.
5 Что называется печным агрегатом?
6 Какое вспомогательное оборудование используется при работе вращающихся печей?
7 Чем отличаются вращающиеся печи, работающие при мокром способе производства от таких же печей, работающих при сухом способе производства?
8 Для чего в печи применяются цепные завесы?
9 Для чего вместе с вращающимися печами ставят пылеуловители?
10 Что такое декарбонизаторы и для чего они применяются?
11 Какое оборудование применяется для охлаждения клинкера и как оно классифицируется?
Дата добавления: 2020-12-22; просмотров: 567; Мы поможем в написании вашей работы! |
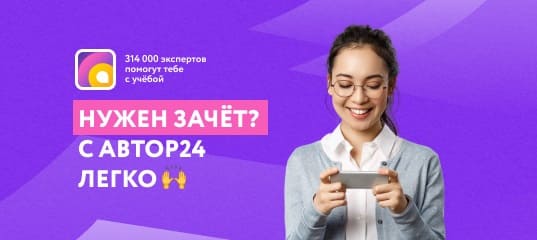
Мы поможем в написании ваших работ!