ДИФФУЗИОННАЯ МЕТАЛЛИЗАЦИЯ (ДИФФУЗИОННОЕ НАСЫЩЕНИЕ МЕТАЛЛАМИ)
Поверхностное насыщение стали алюминием, хромом, бором и другими элементами называют диффузионным насыщением металлами. Изделие, поверхность которого обогащена этими элементами, приобретает ценные свойства, к числу которых относятся высокая жаростойкость, коррозионная стойкость, повышенная износостойкость и твердость.
Поверхностное насыщение стали металлами, а также таким элементом, как кремний, можно осуществлять при 900—1050°С упаковкой изделия в порошкообразную среду (обычно ферросплавы и 0,5—5% NH4C1) погружением в расплавленный металл, если диффундирующий элемент имеет невысокую температуру плавления (например, цинк, алюминий), или насыщением из газовой среды. При газовом методе используют летучие хлориды металлов (А1С13, CrCl2, SiCl4 и т. д.), образующиеся при действии хлора (или хлористого водорода) на металлы или их сплавы с железом при высоких температурах. Между хлоридами и железом протекает обменная реакция, в результате которой образуется диффундирующий элемент в атомарном виде, проникающий в решетку железа. Продолжительность процесса насыщения металлами обычно значительная.
Алитирование. Алитированием называют насыщение поверхности стали алюминием. Чаще применяют алитирование в порошкообразных смесях. Детали упаковывают в ящик, заполненный рабочей смесью, в состав которой входят: алюминиевый порошок (25—50%) или ферроалюминий (50—75%), окись алюминия (25—75%) и хлористый аммоний (--1,0%). Процесс ведут при 900—1050°С в течение 3—12 ч. Нередко применяют алитирование в ваннах с расплавленным алюминием. Алитируемые детали погружают в расплавленный алюминий, содержащий 6—8% Fe (железо добавляют для того, чтобы исключить растворение обрабатываемых деталей в алюминии), процесс ведут при 700—800°С в течение 45—90 мин.
|
|
Хромирование стали — насыщение поверхности стальных изделий храмом. Этот процесс обеспечивает повышенную устойчивость стали против газовой коррозии (окалиностойкость) — до 800°С, высокую коррозионную стойкость в таких средах, как вода, морская вода и азотная кислота. Хромирование сталей, содержащих >0,3—0,4% С, повышает также твердость и износостойкость.
Хромирование чаще ведут в порошкообразных смесях (например, 50% феррохрома, 49% окиси алюминия и 1% хлористого аммония). Некоторое применение нашло газовое хромирование (нагрев в среде, содержащей СгС12) и в вакууме. При хромировании в вакууме изделия засыпают порошком хрома в стальном или керамическом тигле и помещают в вакуумную камеру (давление 10~~2—10~3 мм рт.ст.). При высокой температуре хром испаряется и диффундирует в железо. Хромирование ведут при 1000—1050°С несколько часов.
|
|
Диффузионный слой, получаемый при хромировании технического железа, состоит из твердого раствора хрома в α-железе. Слой, получаемый при хромировании стали, содержащий углерод, состоит из карбидов хрома. Карбидный слой обладает высокой твердостью. Твердость слоя, полученного хромированием железа, составляет HV250—300, а при хромировании стали — НV1200—1300. Глубина хромированного слоя обычно не превышает 0,15—0,20 мм.
В последнее время применяется глубокое хромирование слябов, сутунок, заготовок труб и т.д. на 1,5—8,0.мм в вакууме при высокой температуре (1400—1450°С). При получении хромированных листов, труб и прутков перегрев устраняется в процессе повторного нагрева для обработки давлением.
Хромирование используют для деталей паросилового оборудования, пароводяной арматуры, клапанов, вентилей, патрубков, а также деталей, работающих на износ в агрессивных средах.
Силицирование — насыщение поверхности стали кремнием. Силицирование придает стали высокую коррозионную стойкость в морской воде, в азотной, серной и соляной кислотах и несколько увеличивает устойчивость против износа. Силицирование проводят в порошкообразных смесях (например, 75% ферросилиция +20% шамота +5% Н4С1) или чаще в газовой среде (SiCl4), получаемый пропусканием хлора через реакционное пространство с обрабатываемыми деталями и ферросилицием или карбидом кремния. Процесс ведут при 950— 1000°С.
|
|
Силицированный слой является твердым раствором кремния в α-железе. Силицированный слой отличается повышенной пористостью, глубина его 0,3—1,0 мм. Несмотря на низкую твердость ( HV 200—300), силицированный слой обладает высокой износостойкостью после предварительной пропитки маслом при 170—200°С.
Силицированию подвергают детали, используемые в оборудовании химической, бумажной и нефтяной промышленности (валики насосов, трубопроводы, арматура, гайки, болты и т. д.).
Борирование, т. е. насыщение поверхностного слоя бором, создает очень высокую твердость ( HV 1800—2000), износостойкость и устойчивость против коррозии в различных средах. Борирование стальных изделий чаще выполняют при электролизе расплавленных солей, содержащих бор. Изделие служит катодом в ванне с расплавленной бурой (Na2B207). Температура насыщения 930—950°С при выдержке 2—6 ч.
Хорошие результаты получены при газовом борировании. В этом случае насыщение бором проводят в среде диборана (В2Н6) или треххлористого бора (ВС13) в смеси с водородом при 850—900°С. Глубина борированного слоя достигает 0,1—0,20 мм.
|
|
Борированию подвергают детали, применяемые в оборудовании нефтяной промышленности. Например, втулки грязевых нефтяных насосов для повышения их устойчивости против абразивного износа. Борирование поверхностей контакта штампов для горячей штамповки значительно повышает их стойкость. Борированию можно подвергать любые стали.
Цветные металлы
Из цветных металлов наибольшее применение в строительстве имеет алюминий, обладающий высокой удельной прочностью, пластичностью, коррозионной стойкостью и экономической эффективностью. Серебро, золото, медь, цинк, титан, магний, олово, свинец и другие используются главным образом как легирующие добавки и компоненты сплавов и имеют поэтому специальное и ограниченное применение в строительстве (специальные виды стекла, уникальные объекты - мемориалы на Мамаевом кургане в Волгограде, на Поклонной горе, обелиск в честь покорения космоса в Москве и другие, в которых большое применение нашли титан, медь, и их сплавы; запорно-регулировочная арматура и устройства водопроводно-отопительных, электротехнических систем зданий и сооружений).
В чистом виде цветные металлы, как и железо, вследствие их малой прочности и твердости, применяются редко.
Алюминий- металл серебристо-белого цвета, плотностью 2700 кг/м^ и температурой плавления 658°С. Технический алюминий вследствие малой прочности в строительных конструкциях применяется редко. Повышение прочности достигается легированием Mg, Mn, Си, Si, Al, Zn, а также пластическим деформированием (нагартовкой), закалкой и старением. Все сплавы алюминия делятся на деформируемые и литейные. Деформируемые сплавы в свою очередь подразделяются на термически упрочняемые и неупрочняемые. К термически упрочняемым относятся сплавы Al-Mg-Si, Al-Cu-Mg, Al-Zn-Mg; термически неупрочняемым - технический алюминий и двухкомпонентные сплавы А1-Мп и Al-Mg (магналии). Медь - основная легирующая добавка сплавов - дуралюминов, повышает прочность, но снижает пластичность и антикоррозионные свойства алюминия. Марганец и магний повышают прочность и антикоррозионные свойства; кремний - жидкотекучесть и легкоплавкость, но ухудшает пластичность. Цинк, особенно с магнием, увеличивает прочность, но уменьшает стойкость к коррозии под напряжением. Для улучшения свойств алюминиевых сплавов в них вводят небольшое количество хрома, ванадия, титана, циркония и других элементов. Железо (0,3-0,7%) является нежелательной, но неизбежной примесью. Соотношение компонентов в сплавах подбирается исходя из условий достижения ими после термической обработки и старения высокой прочности, обрабатываемости и коррозионной стойкости. Сплавы обозначаются марками, которые имеют буквенное и цифровое обозначение, характеризующее состав и состояние сплава: М - отожженный (мягкий); Н - нагартованный; Н2 - полунагартованный; Т - закаленный и естественно состаренный; Т1 - закаленный и искусственно состаренный; Т4 - не полностью закаленный и искусственно состаренный. Нагартовка и полунагартовка характерны для термически неупрочняемых сплавов; закалка и старение для термически упрочняемых.
Марки технического алюминия: АД, АД1 (А - алюминий, Д - сплав типа дуралюмина, 1 - характеризует степень чистоты алюминия - 99,3%; в марке АД - 98,8 Al); высокопрочного - В95, В96, ковочного - АК6, АК8 (цифры обозначают суммарное содержание основных и дополнительных легирующих элементов в сплаве (%).
Марки термически неупрочняемых алюминиевых сплавов: АД1М, АМцМ, АМг2М, АМг2Н2 (М - мягкий, Мц - марганец, Мг2 - магний при содержании в сплаве 2%).
Цифровое обозначение марок алюминиевых сплавов: 1915, 1915Т, 1925, 1935Т (первая цифра обозначает основу сплава - алюминий;
вторая - композицию компонентов; 0 - технически чистый алюминий, 1 - Al-Cu-Mg, 3 - Al-Mg-Si, 4 - Al-Mn, 5- Al- Mg, 9 - Al-Mg-Zn; две последние - порядковый номер сплава в своей группе.
Основными видами термической обработки алюминиевых сплавов является отжиг, закалка и старение (отпуск). Отжиг происходит без фазовых превращений и применяется для снятия остаточных напряжений, гомогенизации, рекристаллизации и возврата. В последнем случае происходит восстановление начальных физических и механических свойств сплава, снижение прочности, повышение пластичности и ударной вязкости, необходимые для технологических целей.
Медь в чистом виде имеет небольшую прочность и высокую пластичность. Температура ее плавления 1083°С. Она плохо обрабатывается резанием, но хорошо деформируется в холодном и горячем состояниях. Широко распространены сплавы меди - латуни и бронзы.
Латунь- сплав меди с цинком. Предельная растворимость цинка в меди - 39%. Такой сплав представляет собой твердый раствор цинка в меди. При содержании цинка до 45% возникает вторая фаза. Двухфазные латуни более прочны и тверды, чем однофазные, но малопластичны. Марки латуней обозначают буквой Л и цифрами, указывающими содержание меди в процентах. Механические свойства одно- и двухфазных латуней: (Л96) (томпак), Л80 (полутомпак) (томпак в пер. с фр. - медь). Для улучшения свойств латуни подвергают холодному и горячему деформированию, рекристаллизационному отжигу при 500-700°С и легированию добавками Sn, Si, Mn, Al, Fe, Pb, повышающими прочность, коррозионную стойкость и антифрикционные свойства. Специальные латуни маркируют: ЛА77-2 (латунь, содержащая 77% Си, 2% Al и 21% Zn). ЛАЖ60-1-1 (латунь, содержащая 60% Си, 1% Al, 1% Fe и 38% Zn). Они представляют собой однородные твердые растворы и поэтому весьма пластичны.
Бронзы - это сплавы меди с оловом, алюминием, кремнием, свинцом, бериллием и другими элементами.
Оловянистые бронзы представляют твердый раствор 4-5% олова в меди. При большем содержании олова пластичность и литейные свойства бронзы резко снижаются. Перед обработкой давлением их подвергают рекристаллизационному отжигу при 600-650°С. Для улучшения литейных свойств и повышения прочности в бронзу вводят до 1% фосфора. Алюминиевые и кремнистые бронзы имеют механические свойства, аналогичные оловянистым бронзам, но более дешевые и стойкие в агрессивных средах. В промышленности используют только однофазные бронзы, обладающие высокими пластичными и литейными свойствами.
Бериллиевые бронзы содержат 2-2,5% Be и обладают наилучшими свойствами из всех известных бронз.
Свинцовые бронзы содержат до 30% Pb и не образуют твердых растворов свинца в меди. Они склонны, как и оловянистые бронзы, к ликвации (неоднородность), имеют невысокую прочность, пластичность и хорошие антифрикционные свойства. Маркируют все бронзы аналогично латуням. Например, БрОЦСНЗ-7-5-1 -оловянистая бронза, содержит 3% Sn, 7% Zn, 5% Pb, 1% Ni и 84% Си, БрАЖН 10-4-4 - алюминиевая бронза, содержит 10% А1, 4% Fe, 4% Ni и 82% Си.
Титан- металл серебристо-белого цвета, плавится при 1665±5°С. Существует в двух модификациях: α-титан до 882°С (плотность 4505 кг/м3) кристаллизующийся в гексагональной решетке и β-титан при температуре 900°С и более (плотность 4320 кг/м3), кристаллизующийся в объемно-центрированной кубической. На поверхности титана легко образуется прочная оксидная пленка, защищающая его от коррозии во всех средах и коррозии под напряжением.
Технический титан марок ВТ 1-00, ВТ 1-0 и ВТ 1-1 имеет невысокую прочность, пластичен, хорошо обрабатывается давлением и сваривается. Примеси N, С, О и Н ухудшают антикоррозионные свойства, пластичность и свариваемость титана; охрупчивают (особенно водород) и повышают его прочность и твердость. Для улучшения механических и технологических свойств титана его легируют добавками Аl, Мо, V, Мn, Сг, Sn, Fe, Zn, Si. Различают α-сплавы и α+β-сплавы титана. Они хорошо деформируются в горячем и холодном состоянии, свариваются и противостоят коррозии.
11 Стальные строительные конструкции.
Рациональные марки сталей для строительных конструкций выбирают исходя из их вида, назначения, ответственности, режима и условий работы и эксплуатации. Все виды стальных строительных конструкций разделены на 4 группы.
К первой группе отнесены сварные конструкции, работающие в особо тяжелых условиях динамического нагружения (подкрановые балки, эстакады и др.). Для этих конструкций применяют высокопрочные низколегированные стали типа 18Г2АФпс, 12ГН2МФАЮ, а также ВСтЗГпс5, 09ГС12.
Ко второй группе отнесены сварные конструкции, работающие в условиях статической нагрузки (фермы, ригели, рамы, балки перекрытий и покрытий и др.). Для этих конструкций рекомендуются низкоуглеродистые и низколегированные стали повышенной и высокой прочности - ВСтЗсп5, 09Г2С, 10ХСНД и др.
К третьей группе отнесены сварные конструкции, работающие преимущественно на сжатие (колонны, стойки, опоры под оборудование и др).. Для них могут использоваться наряду с вышеуказанными для второй группы низкоуглеродистые стали - ЗСтЗкп2.
В четвертую группу включены вспомогательные конструкции и элементы (связи, фахверк, лестницы, ограждения и др.). Для них рекомендуются обычные низкоуглеродистые кипящие, полуспокойные и спокойные стали группы Вст3кп (пс, сп) 2(5).
Дата добавления: 2020-12-12; просмотров: 60; Мы поможем в написании вашей работы! |
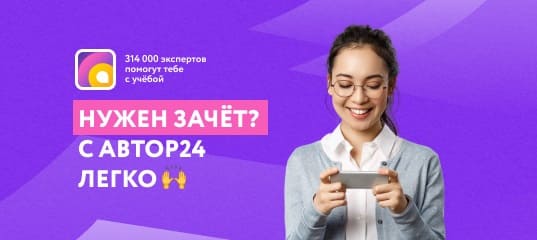
Мы поможем в написании ваших работ!