Способы и технологические процессы проходки стволов
Проходка шахтных стволов составляет небольшую долю в общем объеме работ при строительстве метрополитенов, однако быстрое и успешное ее проведение сокращает общие сроки строительства, поскольку через шахтные стволы осуществляется разворот основных подземных работ.
Рис. 96. Шахтный ствол:
1 — воротник; 2 — вертикальный ствол; 3 — сопряжение ствола с околоствольными выработками; 4 — зумпф
По назначению различают рабочие шахтные стволы и вентиляционные. Рабочие шахтные стволы служат только для строительных целей. После окончания строительства их забучивают (заполняют кладкой, засыпают грунтом). Вентиляционные стволы являются постоянными сооружениями метрополитенов.
В больших вертикальных выработках на внешние нагрузки лучше работают обделки кругового очертания. Шахтные стволы, используемые при эксплуатации метрополитенов как вентиляционные, находятся в условиях знакопеременных температур, и их обделки требуют особо надежной гидроизоляции. Этим определяется преимущественное применение для шахтных стволов обделок из чугунных тюбингов. Типовой наружный диаметр стволов при строительстве метрополитенов принят равным 6 м.
Шахтный ствол (рис. 96) состоит из верхней части — устья (форшахты) с воротником, основной части — вертикальной протяженной закрепленной выработки, сопряжения ствола с околоствольными выработками и нижней части — зумпфа.
|
|
Воротник представляет собой конструкцию кругового очертания из бетона или железобетона, которая надежно закрепляет верхние кольца ствола в грунте и воспринимает часть веса обделки. В воротнике иногда размещают специальное оборудование, используемое при проходке ствола. Он ограждает устье ствола от стока поверхностных вод.
Сопряжение ствола с околоствольными выработками выполняют в виде бетонного раструба.
Зумпф ствола располагают на 2-3 м ниже уровня подошвы околоствольного двора. Он служит временным водосборником.
Комплекс размещенного в стволе оборудования, необходимого для обслуживания подземных работ в продолжение всего периода строительства, и поддерживающих его устройств называют постоянным армированием ствола. Сечение ствола разделяется на клетьевое, лестничное и лесоспускное отделения, а также отделения для размещения трубопроводов и кабелей (рис. 97).
В состав постоянного армирования ствола входят расстрелы — основные поддерживающие устройства клетьевого подъема и обшивки отделений ствола, проводники — направляющие для клетьевого подъема, оборудование лестничного и лесоспускного отделений, одна или две вентиляционные трубы, трубопроводы для водоотлива, сжатого воздуха и воды, а также постоянные силовые, сигнальные и осветительные электрокабели.
|
|
Расстрелы устанавливают по высоте ствола через каждые 3 м и крепят непосредственно к обделке. Деревянные проводники прикрепляют к расстрелам болтами. Трубопроводы крепят к обделке ствола при помощи хомутов, а электрокабели — посредством специальных кронштейнов и скоб. Ускорить подготовку ствола для ведения дальнейших подземных работ позволяет выполнение возможно большей части работ по его армированию в процессе проходки.
Шахтные стволы пересекают обычно разнородные грунтовые напластования, в том числе слабые неустойчивые и обводненные грунты. Поэтому при проходке стволов используют разные способы и часто применяют специальные способы работ: замораживание грунтов, цементацию и другие виды закрепления грунтов, искусственное водопонижение.
Стволы сооружают с последовательным монтажом колец обделки в призабойной части выработки (подводкой колец снизу) или способом опускной крепи с наращиванием колец сверху.
Способ подводки колец снизу (обычный) применяют при сооружении стволов в природно-устойчивых или искусственно закрепленных грунтах.
|
|
Способ опускной крепи применяют при проходке стволов в слабых неустойчивых грунтах. Одной из разновидностей способа является проходка с задавливанием крепи. В этом случае обделку устья ствола, имеющую несколько больший диаметр, используют в качестве неподвижной опорной части, а опускную крепь собирают в пределах нижнего ее участка. Чтобы не допустить обнажений вертикальных стенок выработки и выпуска грунта в забое, в нижней части опускной крепи делают ножевое кольцо из листовой стали. Крепь погружают, вдаливая гидравлическими домкратами, которые устанавливают на верхние фланцы тюбингов очередного собранного кольца обделки с упором в пакеты из двутавровых балок, раскрепленных в обделку устья ствола.
Рис. 97. Сечение шахтного ствола:
1 — лестничное отделение; 2 — лесоспуск: 3 ooo— клетевое отделение (на две клети); 4 — отделение для трубопроводов и кабелей; 5 — вентиляционная труба
Способ опускной крепи получил дальнейшее развитие в виде способа погружения крепи в тиксотропной оболочке. Сущность его состоит в том, что в процессе погружения зазор между крепью и грунтом заполняют тиксотропным раствором, резко снижающим сопротивление трения. Тиксотропный раствор готовят из специальных видов глин. Он обладает способностью сохранять длительное время свои свойства, т. е. не расслаивается: в нем не выделяется осадок и не отделяется вода. Оказывая давление на стенки выработки, он предотвращает их обрушение или оползание.
|
|
Применение тиксотропной оболочки коренным образом усовершенствовало способ опускной крепи, обеспечило необходимую его надежность, снизило затраты времени на сооружение стволов, уменьшило трудоемкость работ, повысило производительность и улучшило условия труда проходчиков.
Необходимым условием применения опускной крепи является наличие водоупора под толщей проходимых неустойчивых грунтов.
Стволы с наращиванием обделки сверху на полную глубину обычно не проходят: преодолев толщу слабых неустойчивых грунтов, дальнейшую проходку в плотных грунтах ведут обычным способом с монтажом обделки подводкой колец снизу.
Из специальных способов по предварительному закреплению грунтов наибольшее распространение при сооружении стволов получило искусственное замораживание грунтов. Оно эффективно при проходке стволов в водонасыщенных песках, слабых глинистых грунтах и плывунах. Этот способ успешно применяют при ведении проходческих работ вблизи от зданий и сооружений, позволяя обеспечить их сохранность и безопасность работ.
Цементацию и глинизацию применяют при проходке стволов в сильнотрещиноватых скальных грунтах, хорошо проводящих воду, и в крупнообломочных (например, гравелистых) грунтах с большим притоком воды в забой.
Искусственное понижение уровня грунтовых вод для снижения притока воды при проходке стволов ведут при помощи пробуриваемых с поверхности скважин и глубинных насосов.
Способы и технологические процессы проходки стволов
Стволы шахт проходят сверху вниз и снизу вверх. В зависимости от горно-геологических и горнотехнических условий, устойчивости пород и обводненности массива проходку ведут обычным или специальным способами. Обычным способом стволы проходят в устойчивых слабообводненных породах, специальным — в неустойчивых породах со значительным притоком воды, удалить которую из забоя средствами проходческого водоотлива невозможно.
Работы при обычном способе выполняют в следующей последовательности: выбирают технологическую схему проходки и комплекс проходческого оборудования, проектируют технологию работ по процессам, рассчитывают комплексную норму выработки, определяют состав проходческой бригады и продолжительность проходческого цикла. Специальные способы проходки рекомендуется применять в рыхлых и неустойчивых породах.
Технология проходки стволов при обычных способах состоит из следующих процессов: бурения, заряжания и взрывания шпуров, проветривания забоя, водоотлива, уборки породы (погрузка и подъем), установки временной или постоянной крепи.
Бурение.
Шпуры при проходке стволов бурят тяжелыми ручными перфораторами ПР-22, ПР-25М6, ПК-60 и ПК-75 и бурильными установками типа БУКС. Ниже приведены технические характеристики ручных перфораторов и бурильных установок:
Ручные перфораторы | ПК-60 | ПК-75 |
Крутящий момент, Н-м | 160 | 220 |
Частота ударов, с-1 | 41,6—45 | 33,3—41,6 |
Энергия удара, Дж | 90 | 150 |
Осевое усилие подачи, кН | До 7 | 10 |
Рабочее давление сжатого воздуха, МПа | 0,5 | 0,5 |
Масса, кг | 60 | 75 |
Бурильные установки | БУКС-1м | БУКС-1 мц | БУКС-1у2 | БУКС-1у4 |
Диаметр ствола в свету, м | 5,5—9 | 5,5—9 | 4—9 | 4—9 |
Бурильная машина | БГА-1м | БГА-1м | БГА-1м, БУ-1, ПК-60 | БГА-1м, БУ-1, ПК-60 |
Число бурильных машин | 4 | 2 | 2 | 4 |
Длина буримых шпуров, м | 4,25 | 50/2,5 | 5,6 | 5,6 |
Максимальный угол наклона бурильной машины, градус | 10 | 10 | 20 | 20 |
Необходимый диаметр ба- дьевого проема для пропуска машины, мм | 1640 | 1640 | 1330 | 2120 |
Максимальный расход сжатого воздуха, м3/мин | 60 | 60 | 36 | 60 |
Расстояние между шпурами, мм | 800 | 800 | 600—850 | 600—850 |
Расход воды на промывку 100 м шпуров, м3 | 1,0 | — | 1,0 | 1,0 |
Масса, т | 7,5 | 8,5 | 6,54 | 9,4 |
Важными факторами при выборе способа бурения и диаметра стволов являются: поперечное сечение ствола, физико-механические свойства пород, тип ВВ, мощность бурового оборудования и т. д.
Бурят шпуры диаметром 46 и 40 мм. Число перфораторов на забой определяют исходя из объема буровых работ за время цикла, т. е. на один перфоратор приходится 1,5—3 м2 площади сечения ствола.
В стволах с сечением в форме окружности шпуры располагают по окружностям, расстояние между которыми составляет 0,6—1,1 м.
Стволовые бурильные установки позволяют с высокой скоростью бурить шпуры, исключают ручной труд, в 2—3 раза повышают производительность труда проходчиков, улучшают условия их труда.
Заряжание и взрывание.
Заряжание шпуров при проходке стволов — механизированное. Оно осуществляется зарядными машинами типа ЗМК-1. При механизированном заряжании шпуров необходимо строго придерживаться технологии и соблюдать правила безопасности.
Боевики вводят после полного окончания заряжания забоя и переноски зарядного оборудования на безопасное расстояние.
Целесообразная длина шпуров при проходке стволов считается 2,5—3,0 м при диаметре ствола 6,5 м и более и 2,0—2,5 м при меньшем диаметре. Коэффициент использования шпуров (КИШ) при такой глубине достигает 0,85—0,9. При меньшей длине шпуров возрастают потери времени и трудовые затраты на 1 м проходки ствола в общем цикле работ за счет вспомогательных операций.
Диаметр окружности для врубовых шпуров принимают равным 0,25—0,3 диаметра ствола в проходке. Число врубовых шпуров в зависимости от крепости пород и формы вруба принимают равным от 6 до 12. Эффективным врубом является пирамидально-призматический. По окружности вруба бурят комплекс наклонных шпуров, образующих конус или пирамиду, и вертикальные шпуры.
Взрывание короткозамедленное и замедленное с применением электродетонаторов. При групповом соединении электродетонаторов в устье шпуров забивают деревянные колышки, на которые натягивают оголенные провода диаметром 2,5 мм, образующие антенну для подсоединения проводов, которые идут от электродетонаторов.
В качестве ВВ используют прессованный скальный аммонит в патронах диаметром 36 мм, а в качестве забойки — гранулированный шлак, песок или глину. Ниже приведены технико-экономические показатели буровзрывного комплекса при показательных проходках стволов некоторых шахт:
Шахта | 1 | 2 | 3 | 4 |
Диаметр ствола, м: | ||||
в проходке | 7,1 | 7,1 | 7,1 | 7Д |
в свету | 6,5 | 6,5 | 6,5 | 6,5 |
Коэффициент крепости пород | 14—16 | 12—18 | 14—16 | 15—16 |
Число пробуренных шпуров | 76 | 86 | 80 | 80 |
Диаметр шпуров, мм: | ||||
оконтуривающих | 40 | 40 | 40 | 40 |
центральных | 53 | 53 | 40 | 40 |
Расход ВВ, кг: | ||||
на 1 м3 отбитой породы | 1,95 | 2,05 | 2,2 | 2,15 |
на 1 м подвигания забоя | 76,1 | 79,5 | 76,3 | 94,5 |
Подвигание забоя за один цикл, м | 1,8 | 2,1 | 2,7 | 2,2 |
КИШ | 0,9 | 0,9 | 0,9 | 0,94 |
Коэффициент перебора сечения | 1,035 | 1,04 | 1,03 | 1,03 |
Погрузка. Погрузка породы при проходке стволов — наиболее трудоемкий процесс и занимает 35—50 % времени всего проходческого цикла.
Эффективность погрузки зависит от применяемой погрузочной техники, средств подъема и качества дробления взорванной горной массы.
Погрузку взорванной горной массы в стволах осуществляют с помощью грейферных погрузчиков, техническая характеристика которых приведена ниже:
Грейферные погрузчики | КС-2у/40 | КСМ-2у | КС-3 |
Вместимость грейфера, м3 | 0,65 | 0,4; 0,65 | 0,22 |
Продолжительность цикла черпания, с | 25—30 | 25—30 | 25—30 |
Производительность, м3/мин | 1,3—1,6 | 1,3—1,6 | 0,25 |
Управление | Дистанционное | ||
Средний расход сжатого воздуха, м3/мин | 20 | 20 | 8,25 |
При проходке стволов на геологоразведочных предприятиях широко применяют пневматические грузчики КС-3 с ручным вождением и стволовые погрузочные машины, входящие в состав проходческих комплексов. При проходке неглубоких (до 300 м) стволов использование мощных погрузочных машин неэффективно. В неглубоких стволах для погрузки горной массы применяют малогабаритную ковшовую погрузочную машину ППН-2 г. Погрузку породы осуществляют в бадьи вместимостью 3—5 м3.
Проветривание. Стволы проветривают нагнетанием свежего воздуха в забой по вентиляционным трубам. При проходке стволов глубиной до 200 м проветривание осуществляют одним вентилятором типа ВМ-6; при значительной (до 700 м) глубине ствола применяют комбинированные схемы проветривания, при которых вентилятор ВЦО-1,5 работает по всасывающей схеме и одновременно с ним устанавливают на подвесном проходческом полке вентилятор, работающий по нагнетательной схеме через металлические трубы диаметром 1000 мм. Применяют также гибкие трубы, изготовленные из специальной хлопчатобумажной ткани с резиновым покрытием, диаметром 0,5—0,8 м. Трубы наращивают обычно с проходческого полка и крепят к стенкам ствола, а на конец трубопровода крепят насадку, обеспечивающую эффективное проветривание с расстояния 12—15 м. Продолжительность проветривания после взрывания составляет 20—30 мин.
Водоотлив. При небольших притоках воды водоотлив осуществляют забойными насосами в бадью или подвесными насосами непосредственно на поверхность. Применяют следующие проходческие забойные насосы: НПП-1м и «Байкал-2М», приводимые в действие энергией сжатого воздуха. Проходческие насосы НШЛ предназначены для откачки загрязненной воды, а насос ППН-50-12м — для откачки воды при проходке стволов с притоком до 50 м3/ч с подъемом ее на высоту до 250 м.
Перекачные проходческие насосы типа 4НШВМ7х6 предназначены для откачки осветленной воды из водосборника, расположенного в перекачной камере, на поверхность или в расположенную выше перекачную станцию. Эти насосы могут применяться при проходке шахтных стволов глубиной до 350 м без промежуточного перекачивания.
Крепление. Работы по креплению стволов обычно начинают с закрепления верхней части устья монолитной железобетонной крепью на глубину 4—5 м, т. е. устанавливают нулевую раму, которая служит для перекрытия устья ствола, надежного предохранения работающих в стволе людей от падения различных предметов. При проходке ствола стенки его закрепляют кольцами временной крепи из швеллерных балок.
Первое кольцо подвешивают к штанговым подвескам, установленным в верхней части крепи устья, а пространство за кольцами затягивают затяжкой или металлической сеткой, которая впоследствии служит в качестве арматуры.
Для крепления стволов в шахтном строительстве применяют бетоносмесительные установки СБ-84, СБ-91, СБ-10В, СБ-10А:
Бетоносмесители | СБ-84 | СБ-91 | СБ-10В | СБ-10А |
Вместимость смесительного барабана, м3 | 0,5 | 0,75 | 1,2 | 1,5 |
Объем готового замеса, м3 | 0,33 | 0,5 | 0,8 | 1,0 |
Производительность, м3/ч | До Ю | 15 | 18 | 20 |
Мощность электродвигателя, кВт | 3,0 | 4,0 | 13,0 | 13,0 |
Основные размеры, мм: | ||||
длина | 2500 | 1850 | 3725 | 2620 |
ширина | 2000 | 1990 | 2730 | 2700 |
высота | 2735 | 1800 | 2526 | 2150 |
Масса, кг | 1820 | 1275 | 3945 | 3600 |
Бетонную смесь в стволах подают по трубам диаметром 152,4 мм, с толщиной стенки 8 мм, подвешенным с помощью канатов на лебедках или прикрепленных к стенкам ствола.
Для подачи бетона применяют следующий комплекс оборудования: приемный бункер, приемную воронку, став из стальных труб, желоб для разводки бетонной смеси в стволе за опалубку.
Проходчики при креплении направляют бетонную смесь с помощью вращающегося желоба в различные места по периметру ствола, разравнивают и трамбуют ее за опалубкой. Наиболее эффективной считается передвижная призабойная опалубка высотой 4 м.
Дата добавления: 2020-11-29; просмотров: 221; Мы поможем в написании вашей работы! |
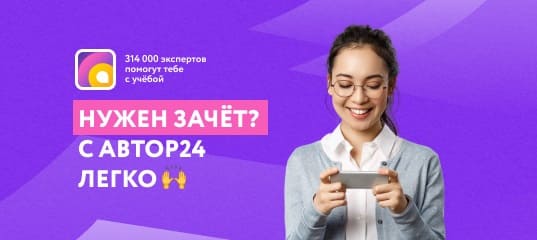
Мы поможем в написании ваших работ!