Характеристики и классификация медных сплавов.
Лекция №5
Цветные металлы и сплавы на основе алюминия, меди, титана. Припои и антифрикционные сплавы. Использование их в автомобиле строении.
Алюминий и его сплавы.
Алюминий — металл серебристо-белого цвета. Он не имеет аллотропных превращений и кристаллизуется в решетке гранецентрированного куба.
Алюминий обладает малой плотностью (при 20°С, 2,7г/см2), хорошей тепло- и электропроводностью, высокой коррозионной стойкостью и пластичностью (ГОСТ 11069-74).
Марка | Сумма примесей, % | Состояние | σв, кгс/см2 | σ0,2, кгс/см2 | δ,% | HB |
А995 | 0,005 | Литой | 5 | - | 45 | 15 |
А5 | 0,50 | Литой | 7,5 | - | 29 | 20 |
АО | 1,0 | Литой | 9 | - | 25 | 25 |
АО | 1,0 | Деформированный и отожженный | 9 | 3 | 30 | 25 |
АО | 1,0 | Деформированный | 14 | 10 | 12 | 32 |
Отжиг алюминия для снятия наклепа проводится при 350—400° С. |
Характеристики и классификация алюминиевых сплавов.
К преимуществам алюминиевых сплавов относятся высокая удельная прочность (σв/γ) и способность сопротивляться инерционным и динамическим нагрузкам. По удельной прочности некоторые алюминиевые сплавы (21) приближаются к высокопрочным сталям (23).
Основные легирующие элементы Си, Mg,Si, Mn, Zn; реже — Li, Ni, Ti, Be, Zr.
Алюминиевые сплавы классифицируют по технологии изготовления, способности к термической обработке и свойствам.
|
|
Деформируемые алюминиевые сплавы не упрочняемые ТО
К этой группе относятся сплавы АМц и АМг. Сплавы отличаются высокой пластичностью, хорошей свариваемостью и высокой коррозионной стойкостью.
Сплавы АМц относятся к сплавам системы Аl—Мn. В отожженном состоянии сплав обладает высокой пластичностью и низкой прочностью.
Сплавы АМг относятся к сплавам системы А1—Mg. Используют в отожженном (мягком — М), реже — в нагартованном (Н — 80% наклепа) и полунагартованном (П — 40% наклепа) состояниях. Применение наклепа ограничено ввиду резкого снижения пластичности.
Сплавы АМг отжигают при температуре 350—420° С. По мере повышения содержания магния предел прочности этих сплавов повышается, но понижается относительное удлинения и увеличивается склонности к коррозии под напряжением.
Сплавы АМц и АМг применяют для изделий, получаемых глубокой вытяжкой, сваркой, от которых требуется высокая коррозионная стойкость (трубопроводы для бензина и масла, сварные баки), а также для заклепок.
Деформируемые алюминиевые сплавы упрочняемые ТО
Сплавы нормальной прочности.
Типичные представители этой группы сплавов дуралюмины относятся к сплавам системы Аl—Сu—Mg. В литом состоянии сплавы имеют пониженную прочность и пластичность сплавов.
|
|
Слитки сплавов проходят гомогенизацию при температуре 480—500° С с последующей горячей пластической деформацией. Отжиг для снятия наклепа проводится при 350—370° С.
Упрочняющая термическая обработка состоит в закалке и естественном старении. В начальный период старения (20—60 мин), проводят такие технологические операции, как клепка, правка, выколотка и другие. Эти сплавы можно подвергнуть обработке на возврат.
Искусственное старение применяется редко, так как у дуралюминов понижается пластичность и чувствительность к концентрации напряжений.
Для защиты от коррозии их подвергают плакированию (листы) или анодной поляризации (трубы и профили).
Дуралюмины выпускают в виде деформированных полуфабрикатов.
Из сплавов Д1, Д16 и Д18 изготавливают клепки которые ставятся в свежезакаленном состоянии и после закалки и естественного старения.
Высокопрочные сплавы
Сплаы отличается высоким пределом прочности (600—700 МПа) и близким к нему по значению пределом текучести. Принадлежат к системе Аl—Zn—Mg—Сu и содержит добавки марганца и хрома.
ТО состоит в закалке и искусственном старении. Естественное старение для сплавов не применяют, так как оно происходит очень медленно и обеспечивает более низкую коррозионную стойкость. Недостатки сплавов системы Al—Zn—Mg—Сu склонность к коррозии и растрескиванию под действием знакопеременных нагрузок, чувствительность к концентрации напряжений и анизотропия свойств. Листовой материал защищают плакированием. Сплав В95 применяют для высоконагруженных деталей конструкций, работающих в основном в условиях напряжения сжатия.
|
|
Высокопрочные алюминиевые сплавы, легированные Сu, Li, Mn и Cd, отличается жаропрочностью, меньшей плотностью и более высоким модулем упругости. Сплавы упрочняются ТО.
По механическим свойствам в отожженном состоянии и коррозионной стойкости этот сплав близок сплаву Д16. Сплав защищают от коррозии плакированием или анодной поляризацией. Пониженная пластичность и чувствительность к концентрации напряжений относятся к недостаткам сплава. Сплав применяется для изготовления высоконагруженных деталей, работающих в условиях сжатия при температурах до 170° С.
Жаропрочные сплавы
Это сплавы, работающие при температурах до 300° С (АК4, АК4-1 и др.). Они легированы элементами (Fe, Ni, Cu),которые при соответствующем их содержании придают им высокую прочность при температурах до 200—300°С. Жаропрочные сплавы применяются после закалки и искусственного старения.
|
|
Предел прочности и относительное удлинение сплавов при повышенных температурах приведены на рисунке.
Сплавы с повышенным содержанием меди обладают более низкой коррозионной стойкостью.
Из жаропрочных сплавов АК4, АК4-1 деформированные в горячем состоянии полуфабрикаты.
Они используются для нагруженных деталей и сварных изделий, работающих при температурах 200—300° С:, поршни двигателей и др.
Ковочные сплавы
Это сплавы, обладающие хорошей при горячей пластической деформации. К этой группе относятся сплавы системы А1—Си—Mg с повышенным содержанием кремния АК6, АК8 и другие. Ковка и штамповка этих сплавов производится при температурах 450—475°С.
Сплавы применяются после закалки и искусственного старения, которые обеспечивают повышение физико-механических свойств.
Изготавливают средненагруженные детали сложной формы: большие и малые крыльчатки, фитинги, качалки, крепежные детали, подмоторные рамы, стыковые узлы.
Литейные сплавы
Литейные сплавы классифицируют по химическому составу А1—Si, A1—Сu, А1—Mg сплавы.
Лучшими литейными свойствами обладают А1—Si сплавы (силумины).
Большинство силуминов имеет небольшую плотность (2,65 г/см3), хорошие коррозионную стойкость и свариваемость. Хорошо обрабатываются резанием только силумины, легированные медью. Механические свойства зависят от состава, технологией изготовления (модифицирование, способ отливки и др.) и ТО. Элементы Mg, Сu, Mn, Ti, повышают прочность и твердость силуминов.
Наиболее широко в промышленности применяют сплавы АК12,АК7ч, АК9ч. Модифицированию подвергаются обычно сплавы, содержащие более 5—6% Si.
Сплав АК9ч имеет хорошее сочетание литейных и механических свойств. ТО этого сплава состоит в закалке и старении. Из него изготавливают: корпусов компрессора, картеров, блоков и др.
Сплав АК7ч лучше сваривается чем сплав АК9ч. Из него изготавливают средненагруженные литые детали.
Высокопрочный сплав АЛ32, предназначен для литья под давлением. Упрочняют отливки путем искусственного старения без предварительной закалки. АЛ32 применяется для нагруженных деталей (блоки цилиндров и головки блоков, корпуса).
Сплавы системы А1—Сu (АМ5) характеризуются невысокими литейными свойствами, низкой герметичностью и пониженной коррозионной стойкостью, но обладают хорошей прочностью и жаропрочностью.
Сплавы системы А1—Mg (АМг10) обладают высокой коррозионной стойкостью, прочностью, вязкостью и хорошей обрабатываемостью резанием. Наилучшие механические свойства сплавы Al—Mg имеют после закалки с 530°С.
Сплавы АМг10 применяют для нагруженных деталей, работающих в условиях высокой влажности.
Антифрикционные сплавы.
Преимуществом алюминиевых сплавов наряду с их хорошими антифрикционными свойствами является малая плотность, высокая теплопроводность, хорошая коррозионная стойкость в масляных средах, достаточно хорошие механические и технологические свойства.
В зависимости от химического состава и структуры алюминиевые антифрикционные сплавы подразделяют на две группы.
1. Сплавы алюминия с медью, сурьмой, никелем и другими элементами в сравнительно мягкой алюминиевой основе. Например АСМ, содержащий 3,5—6,5% Sb и 0,3—0,7% Mg. АСМ заменил бронзу БрС3О в тракторной промышленности при производстве подшипников коленчатых валов.
2. Сплавы алюминия с оловом обладают повышенным пределом выносливости, хорошо работают в условиях сухого или полужидкого трения. Сплавы с 9—10% Sn используются в основном для тяжелонагруженных подшипников дизельных двигателей. Сплавы АО20-1 (17—23% Sn, 0,7—1,2% Си) и АО9-2 (8—10% Sn, 2,0—2,5% Си, 0,8—1,2% Ni, 0,3-0,7% Si) по своим антифрикционным свойствам близки к баббитам. Из них изготавливают вкладыши коленчатого вала двигателей автомобилей.
Медные сплавы.
Медь — металл красновато-розового цвета; кристаллизуется в решетке гранецентрированного куба; аллотропических превращений не имеет.
В зависимости от химического состава различают следующие марки технической меди: М00, М0, M1, М2, М3, М4.
Медь характеризуют высокие тепло- и электропроводность, пластичность и коррозионная стойкость превосходит которые только серебро. Плотность меди 8,94 г/см3.
Медь имеет высокую коррозионную стойкость. Механические свойства меди зависят от ее состояния и в меньшей степени от содержания примесей
Холодная пластическая деформация увеличивает прочность, твердость и упругость меди, но снижает пластичность. Отжиг для снятия наклепа проводится при температуре 550—650°С. Постоянные примеси меди: As, Fe, Si, P, Pb. Кислород находится в меди охрупчивает ее. Висмут и свинец, вызывают красноломкость.
Медь легко деформируется, полируется, хорошо паяется и сваривается. Недостатки меди: высокая плотность, плохая обрабатываемость резанием и низкая жидкотекучесть.
Характеристики и классификация медных сплавов.
Медные сплавы обладают хорошими механическими, технологическими и антифрикционными свойствами.
Для легирования медных сплавов в основном используют элементы, растворимые в меди, Zn, Sn, Al, Be, Si, Mn, Ni. Относительное удлинение некоторых сплавов доходит до 65%.
Наиболее распространена классификация по химическому составу. Медные сплавы подразделяются на две основные группы: латуни и бронзы.
Латунями называются сплавы меди с цинком. Латуни маркируются буквой Л (латунь) и цифрой, показывающей среднее содержание меди в процентах. Л96, Л90, Л80. Легированные латуни кроме цифры, показывающей содержание меди, даются буквы и цифры, обозначающие название и количество в процентах легирующих элементов. ЛАН59-3-2 содержит: 59% Сu, 3% А1, 2% Ni.
Бронзами называются сплавы меди со всеми элементами кроме цинка. Название бронзам дают по основным легирующим элементам. Бронзы бывают на оловянные, алюминиевые, бериллиевые, кремнистые и др. Бронзы маркируются буквами Бр. (бронза), за которыми следуют буквы, а затем цифры, обозначающие название и содержание в процентах легирующих элементов. Например, Бр. ОЦС6-6-3 содержит: 6% Sn, 6% Zn, 3% Pb. Сплавы меди с никелем имеют также и другие названия: мельхиоры, куниали, нейзильберы.
Латуни.
Практическое значение имеют латуни, содержащие до 45% Zn. Сплавы с большим содержанием цинка отличаются высокой хрупкостью.
Двойные латуни по структуре подразделяют на две группы: однофазные со структурой α-твердого раствора; двухфазные со структурой (α+β) фаз.
Лучшей пластичностью обладают однофазные латуни, содержащие около 30% Zn, наиболее высокие прочность и твердость имеет двухфазная латунь с 45% Zn. Рекристаллизационный отжиг однофазных латуней рекомендуется проводить при 600—700° С.
Сплавы, содержащие более 20% Zn, склонны к коррозионному растрескиванию с течением времени. Кратковременный отжиг при 250—300° С, предотвращению коррозионного растрескивания.
Примеси повышают твердость и снижают пластичность латуней. Особенно неблагоприятно действуют свинец и висмут (красноломкость).
Из этих латуней изготавливают холоднокатаных полуфабрикаты.
Двухфазные латуни пластически деформируются в нагретом состоянии. Свинец улучшает обрабатываемость резанием и антифрикционных свойств. Эти латуни получают в виде горячекатаного полуфабриката. Из них изготавливают втулки, гайки, тройники, штуцера и др.
Эти латуни практически не применяются для фасонных отливок, так как имеют довольно большую концентрированную усадочную раковину.
Легированные латуни применяют в виде деформируемых полуфабрикатов и для фасонных отливок. Литейные латуни содержат большее количество цинка и легирующих элементов. К распространенным легирующим элементам латуней относятся: Al, Sn, Si, Ni. Легирующие компоненты повышают технологические свойства, коррозионную стойкость (Al, Sn, Si) и механические свойства (Ni).
Бронзы.
Алюминиевые бронзы.
Отличаются высокими механическими, антикоррозионными и антифрикционными свойствами.
Имеют высокую жидкотекучесть, концентрированную усадку и хорошую герметичность. Из-за большой усадки трудно получить сложную фасонную отливку.
К недостаткам двойных алюминиевых бронз помимо большой усадки относятся склонность к газонасыщению и окисляемости во время плавки, образование крупной столбчатой структуры, трудность пайки. Эти недостатки уменьшаются легированием алюминиевых бронз железом (твердость прочность, антифрик. свойства), никелем (повышает жаропрочность), марганцем.
Из низ изготовляют детали, работающие в тяжелых условиях износа при повышенных температурах (400—500° С): седла клапанов, направляющие втулки выпускных клапанов, части насосов и турбин, шестерни и др.
Бериллиевые бронзы.
Бериллиевые бронзы отличаются чрезвычайно высокими пределами упругости и прочности, твердостью и коррозионной стойкостью в сочетании с повышенным сопротивлением усталости, ползучести и износу.
Основным недостатком бериллиевых бронз является их высокая стоимость. Легирование Mn, Ni, Ti, Co позволяет уменьшить содержание бериллия до 1,7—1,9% без заметного снижения механических свойств (Бр. БИТ 1,7, Бр. БНТ 1,9).
Применяется в качестве упругого элемента в силоизмерителях.
Кремнистые бронзы.
Кремнистые бронзы характеризуются хорошими механическими, пружинящими и антифрикционными свойствами, а также высокой коррозионной стойкостью. Они занимают особое место в машиностроении как заменители дорогостоящих оловянных и бериллиевых бронз.
Из кремнистых бронз изготовляют главным образом ленты, полосы, прутки, проволоку. Для фасонных отливок они применяются редко. Их используют вместо более дорогих оловянных бронз при изготовлении антифрикционных деталей (Бр. КН1-3), (Бр. КМцЗ-1), а также для замены бериллиевых бронз при производстве пружин, мембран.
Свинцовистые бронзы.
Свинцовые бронзы выгодно сочетают в себе хорошие антифрикционные свойства с высокой теплопроводностью. Кроме того, они хорошо воспринимают ударные нагрузки и работают на усталость. В связи с этим их применяют для ответственных высоконагруженных подшипников, работающих при больших скоростях (подшипники дизелей, мощных турбин и др.).
Свинцовые бронзы склонны к ликвации свинца при кристаллизации, что ухудшает их антифрикционные свойства. Этот недостаток устраняется благодаря ускоренной кристаллизации, которая обеспечивает мелкозернистую структуру с равномерным распределением свинца.
Марганцевые бронзы.
Марганцевые бронзы отличаются высокой коррозионной стойкостью и повышенной жаропрочностью. Эти сплавы содержат от 5 до 12% Мп.
Для придания антифрикционных свойств в марганцевые бронзы вводят свинец, для повышения прочности и твердости — никель, улучшения литейных свойств — кремний и алюминий.
Титановые сплавы
Преимуществом титановых сплавов являются высокие прочность, жаропрочность, жаростойкость при достаточно хорошей пластичности, высокой коррозионной стойкости и малой плотности (4,5 г/см3).
По технологии изготовления титановые сплавы подразделяются на деформируемые и литейные, по механическим свойствам — на сплавы нормальной прочности, высокопрочные, жаропрочные, повышенной пластичности. По способности упрочняться с помощью термической обработки титановые сплавы делятся на упрочняемые и неупрочняемые термической обработкой. По структуре титановые сплавы классифицируются на α-, (α + β)- и β-сплавы.
Деформируемые α-сплавы
Сплавы с α-структурой (ВТ5) характеризуются средней прочностью при комнатной температуре, высокими механическими свойствами при криогенных температурах, хорошей жаропрочностью, сопротивлением ползучести и жаростойкостью. Сллавы имеют высокую термическую стабильность и обладают отличной свариваемостью и коррозионной стойкостью. Прочность сварного шва составляет 90% от прочности основного сплава. Обрабатываемость резанием удовлетворительная.
Недостатки этих сплавов: отсутствие способности упрочняться термической обработкой и низкая технологическая пластичность. Сплавы с оловом более технологичны и жаростойки, обладают высоким характеристиками.
Сплав ВТ5 предназначен для изготовления деталей, работающих при температурах до 400° С, сплав ВТ5-1 (2,5% олова) — до 500° С.
Деформируемые α+β-сплавы
Двухфазные сплавы (ВТ3-1, ВТ6, ВТ8, ВТ14 и др.) обладают лучшим сочетанием технологических и механических свойств. Они упрочняются с помощью термической обработки — закалки и старения. В отожженном и закаленном состояниях они имеют хорошую пластичность, а после закалки и старения — высокую прочность при комнатной и повышенных температурах. Особо высокопрочны сплавы ВТ14, ВТ15, ВТ16. Это объясняется высоким содержанием ванадия, молибдена, хрома.
В качестве жаропрочных в основном используются сплавы ВТЗ-1, ВТ8 и ВТ9.
Двухфазные сплавы удовлетворительно обрабатываются резанием и свариваются. После сварки требуется отжиг для повышения пластичности сварного шва. Эти сплавы куются, штампуются и прокатываются. Они поставляются в виде поковок, штамповок, прутков, листов, ленты.
Деформируемые β-сплавы
Однофазные β-сплавы не имеют промышленного применения, так как для получения устойчивой β-структуры сплавы должны быть легированы большим количеством V, Мо, Nb, Та. Компоненты легирования дороги, дефицитны и обладают высокой плотностью. Такие сплавы дорого стоят, имеют пониженную удельную прочность.
Литейные сплавы.
Титановые сплавы имеют хорошие литейные свойства. Небольшой температурный интервал кристаллизации обеспечивает им высокую жидкотекучесть и хорошую плотность отливки. Они обладают малой склонностью к образованию горячих трещин и небольшой линейной усадкой (1%). Объемная усадка составляет около 3%.
Недостатками литейных титановых сплавов являются большая склонность к поглощению газов и высокая активность при взаимодействии со всеми формовочными материалами. Поэтому их плавка и разливка ведется в вакууме или среде нейтральных газов. Для получения крупных фасонных отливок (до 300—500 кг) используют чугунные и стальные формы, мелкие детали отливают в оболочковые формы, изготовленные из специальных смесей.
Антифрикционные сплавы.
Классификация припоев и антифрикционных сплавов приводится в таблице.
Антифрикционные сплавы широко применяются в конструкциях автомобилей в качестве материала трущихся поверхностей вкладышей коленчатых валов двигателей и различных втулок. Применяют оловянистые, свинцовые и кальциевые баббиты, свинцовистые бронзы и антифрикционные сплавы на алюминиевой основе.
Припои различных групп и марок имеют широкое применение в автомобильной промышленности, на авторемонтных и автотранспортных предприятиях. Марки, физико-механические свойства, назначение и химический состав оловянно-свинцовых припоев регламентирует ГОСТ 21930—76.
Медно-цинковые припои регламентирует ГОСТ 23137—78. Серебряные припои по ГОСТ 19738—74. Положительными свойствами серебряных припоев являются высокая механическая прочность, пластичность, электропроводность, коррозионная стойкость.
Дата добавления: 2020-11-29; просмотров: 205; Мы поможем в написании вашей работы! |
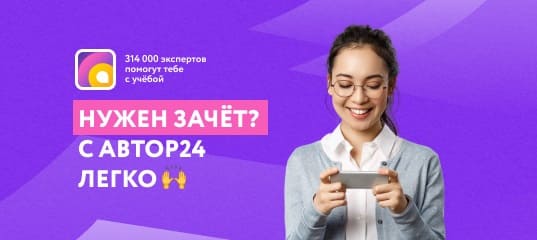
Мы поможем в написании ваших работ!