Основные виды шлифовальных работ
ОБРАБОТКА НА ШЛИФОВАЛЬНЫХ СТАНКАХ
Шлифовальные станки
Шлифованием называется процесс обработки поверхностей деталей при помощи шлифовальных кругов. В большинстве случаев шлифование является отделочной операцией, обеспечивающей высокую точность размеров и хорошее качество обрабатываемой поверхности.
Шлифовать можно плоские, цилиндрические, конические и различные фасонные поверхности деталей, изготовленных как из мягких, так и из самых твердых (в том числе закаленных) металлов и сплавов.
Применяются различные виды шлифования – наружное круглое, внутреннее круглое, плоское, бесцентровое наружное и др. (рис. 69).
Рассмотрим элементы режима резания наиболее распространенного вида обработки поверхностей детали – наружного круглого шлифования в центрах по способу продольной подачи. Этот вид шлифования характеризуется:
1) скоростью резания; 2) подачей; 3) глубиной резания;
4) машинным временем.
Скорость резания V к при наружном круглом шлифовании представляет собой окружную скорость шлифовального круга. Скорость резания выражают в метрах в секунду, выбирают в пределах 30–50 м/с, а в ряде случаев и выше. При наружном круглом шлифовании вращению подвергают также и обрабатываемую деталь; скорость ее вращения составляет 15–50 м/мин.
Подачей S при наружном круглом шлифовании является величина перемещения обрабатываемой детали за один оборот вдоль своей оси (продольная подача); подачу выражают в миллиметрах на оборот детали.
|
|
Глубина резания t (поперечная подача) – это толщина слоя металла, снимаемого шлифовальным кругом за один проход (рис. 69, а).
Машинное время Тм при наружном круглом шлифовании представляет собой время, затрачиваемое непосредственно на процесс резания металла шлифовальным кругом за один проход. Машинное время определяют, исходя из длины продольного хода стола, припуска на сторону диаметра детали, числа оборотов детали, подачи и точности обработки.
При расчете мощности электродвигателя для вращения шлифовального круга и обрабатываемой детали учитывают силу резания, скорость вращения круга и детали.
![]() | ||||||||||||||||||||
Рис. 69. Основные виды шлифования: а – наружное круглое; б – внутренне круглое; в – плоское периферией круга; г – плоское торцом круга; д – бесцентровое наружное; 1 – деталь; 2 – упор; 3 – шлифующий круг; 4 – ведущий круг |
Наружное круглое шлифование в центрах осуществляется путем продольной и поперечной подач, а также глубинным способом.
|
|
При шлифовании способом продольной подачи (рис. 69, а) шлифовальный круг осуществляет главное вращательное движение V к, а обрабатываемая деталь – вращательное движение вокруг своей оси V д и поступательное движение продольной подачи S пр вдоль оси. Глубину шлифования t устанавливают поперечной подачей шлифовального круга.
При шлифовании способом поперечной подачи, или способом врезания, шлифовальный круг получает главное вращательное движение V к вокруг оси и поперечное движение подачи S поп, а обрабатываемая деталь – только вращательное движение V д. Этот способ применяют для шлифования деталей, имеющих небольшую длину обрабатываемой поверхности, полностью перекрываемую шириной шлифовального круга.
Глубинный способ шлифования характерен тем, что шлифовальный круг устанавливается обычно на полную глубину шлифования t и получает главное вращательное движение V к, а обрабатываемая деталь – вращательное вокруг оси V д и продольную подачу S пр вдоль оси детали. Этим способом обычно шлифуют короткие и жесткие валики.
Внутреннее круглое шлифование (рис. 69, б) применяют при обработке сравнительно коротких деталей, закрепляемых в кулачковых патронах. Шлифовальный круг осуществляет главное вращательное движение V к и продольное движение подачи S пр; обрабатываемая заготовка – только вращательное движение вокруг оси V д. Глубину резания t устанавливают поперечной подачей круга.
|
|
Плоское шлифование производят наружной частью (периферией) и торцом шлифовального круга.
При шлифовании периферией круга (рис. 69, в) шлифовальный круг выполняет главное вращательное движение V к и поперечную подачу S поп, а обрабатываемая заготовка, укрепляемая на столе станка, – возвратно-поступательное продольное движение подачи S пр. Глубину резания t устанавливают путем вертикальной подачи круга. Кроме того, стол с деталью может вращаться в горизонтальной плоскости (по принципу карусельных станков), а круг – радиально перемещается относительно стола.
При шлифовании торцом круга (рис. 69, г) обрабатываемая деталь осуществляет то же движение, что и при шлифовании периферией круга, а шлифовальный круг – главное вращательное движение V к вокруг вертикальной оси. Глубину резания устанавливают путем вертикальной подачи вдоль оси круга.
Бесцентровое наружное шлифование (рис. 69, д) состоит в том, что цилиндрическую обрабатываемую деталь 1, поддерживаемую упором 2, пропускают путем продольной подачи между шлифующим 3 и ведущим 4 кругами. Шлифующий круг осуществляет процесс снятия стружки, а ведущий, или подающий, круг, расположенный под некоторым углом a к оси шлифующего круга, обеспечивает вращение детали и ее продольную подачу. В результате поворота оси ведущего круга его окружная скорость V вк раскладывается на две составляющие – скорость вращения детали V д и скорость продольной подачи V вк = m · sin a, где m – коэффициент проскальзывания детали по ведущему кругу (m = 0,94–0,98).
|
|
Угол a обычно принимают в 1–5°; чем больше угол a, тем больше продольная подача, и наоборот.
Для обеспечения лучшего контакта с деталью ведущий круг делают не цилиндрическим, а вогнутым (форма гиперболоида вращения).
Если ось ведущего круга установить параллельно оси шлифующего круга, то Vs = 0 и осевая подача детали будет отсутствовать. Этим пользуются при шлифовании деталей с выступами.
Каждый из рассмотренных видов шлифования имеет свою специфическую форму шлифовального круга и конструкцию станка.
Шлифовальные станки по конструктивным и технологическим признакам (виду выполняемой работы) разделяются на круглошлифовальные, внутришлифовальные, плоскошлифовальные, специализированные, заточные и доводочные.
В подгруппу круглошлифовальных станков входят станки для круглого шлифования в центрах, бесцентровые, полуавтоматы и автоматы; в подгруппу внутришлифовальных – простые, планетарные, бесцентровые, полуавтоматы и автоматы; в подгруппу плоскошлифовальных – продольные и карусельные, работающие периферией и торцом круга, полуавтоматы и автоматы; к специализированным относятся зубошлифовальные, резьбошлифовальные, копировально-шлифовальные, для шлифования шлицевых валиков, шаров и т. д.; к заточным – универсальные для заточки разных инструментов и специальные для заточки инструмента определенного типа. Доводочные станки по применению абразивного инструмента подразделяются на работающие шлифовальным кругом, порошком и полировальными пастами. Имеется несколько моделей каждого типа шлифовальных станков.
На рис. 70 приведен общий вид универсального круглошлифовального станка. Основными деталями и узлами станка являются: станина 7, нижняя часть стола 6, верхняя часть стола 5, бабка шлифовального круга 2, передняя бабка 1, задняя бабка 4.
Верхняя часть стола может быть повернута на некоторый угол к оси шпинделя шлифовального круга для обработки пологих конусов. Заготовки с большим углом конуса шлифуют при повернутой на заданную величину бабке шлифовального круга.
Угловое расположение круга рекомендуется при одновременном шлифовании шейки вала и торца. При такой технологической схеме торец заготовки шлифуется периферией круга, что уменьшает контакт круга с заготовкой, обеспечивая улучшение чистоты обработанной поверхности и исключая возможности прижогов.
![]() |
Рис. 70. Общий вид круглошлифовального станка: 1 – передняя бабка; 2 – шлифовальный круг; 3 – бабка шлифовального круга; 4 – задняя бабка; 5 – верхняя часть стола; 6 – нижняя часть стола; 7 – станина |
На рис. 71 приведена упрощенная кинематическая схема универсального плоскошлифовального станка модели ЗБ722. Станок имеет ряд кинематических цепей, основные из которых – цепь вращения шлифовального круга; цепь ручной и автоматической вертикальной подачи шлифовальной бабки; цепь ручного поперечного перемещения шлифовальной бабки; цепи управления гидрокоробкой стола и гидрокоробкой подач шлифовальной бабки и др.
Наиболее простой является цепь вращения шлифовального круга. Шпиндель круга получает вращение от фланцевого электродвигателя АО62-4 мощностью 10 квт с числом оборотов 1460 в минуту через игольчатую муфту.
Механизмы цепи ручной и автоматической вертикальной подачи шлифовальной бабки осуществляют следующие основные движения:
а) при ручной подаче от маховика А движение передается через шестерни 1 и 2 и кулачковую муфту Б конической паре 3 и 4 и далее на гайку 5, которая связана с ходовым винтом 6; б) при автоматической подаче, осуществляемой от гидропривода, в момент реверса поперечной подачи шлифовальной бабки подается масло в ту или иную полость плунжера механизма подачи, благодаря чему перемещается плунжерная рейка 7. Рейка 7 через шестерню 8 вращает кривошип В, который через шатун Г и систему рычагов поворачивает храповик 9, жестко соединенный с маховиком А. Далее движение передается по описанной выше цепи к винту 6.
![]() |
Рис. 71. Кинематическая схема универсального плоскошлифовального станка модели ЗБ722 |
Для ручного поперечного перемещения шлифовальной бабки вращение от маховика Д через червячную передачу 10 и 11 передается реечной шестерне 12.
Автоматическая поперечная подача шлифовальной бабки гидрокоробкой подач осуществляется рукояткой И, с помощью которой переключается соответствующий плунжер в гидрокоробке подач шлифовальной бабки и производится подача на каждый ход стола.
Инструмент для шлифования
Шлифовальный круг состоит из абразивных зерен и связки. Абразивные зерна непосредственно осуществляют процесс резания при шлифовании, а связка удерживает зерна в теле круга. Между зернами и связкой имеются поры, благодаря которым зерна выполняют роль отдельных резцов; поры служат также местом для выхода стружки.
Шлифовальные круги характеризуются формой и размерами, видом абразивного материала, величиной зерна (зернистостью), типом связки, твердостью и внутренней структурой.
По форме шлифовальные круги бывают:
1) плоские прямого профиля (рис. 72, а) для наружного круглого, внутреннего, бесцентрового и плоского шлифования;
2) плоские конического профиля (рис. 72, б, в) для шлифования резьбы, зубьев шестерен и т. д.;
3) плоские с выточкой (рис. 72, г) для круглого шлифования с подрезкой торца;
4) круги-диски толщиной от 0,5 до 5 мм (рис. 72, д) для отрезных и прорезных работ;
5) круги-кольца и круги-чашки (рис. 72, е, ж, и) для плоского шлифования торцом круга.
![]() | ||||||||||||||||||||||||||||||||
Рис. 72. Формы шлифовальных кругов: а – плоские прямого профиля; б, в – плоские конического профиля; г – плоские с выточкой; д – круги-диски; е, ж, и – круги-кольца и круги-чашки |
Основные размеры шлифовального круга – наружный D и внутренний d диаметры и высота Н. Круги плоские прямого профиля обычно имеют наружный диаметр в пределах от 3 до 1100 мм, высоту (толщину круга) – от 6 до 200 мм.
Режущим инструментом на шлифовальных станках является шлифовальный абразивный круг. Шлифовальные абразивные круги состоят из мелких зерен абразивных материалов, сцементированных между собой связкой. Твердость абразивных материалов значительно выше твердости закаленной стали. Шлифовальные круги изготовляют из абразивных материалов естественного (алмаз, корунд, наждак) и искусственного происхождения (электрокорунд, карборунд, или карбид кремния, и карбид бора).
По ГОСТ 4785–59 шлифовальные круги изготовляют из следующих искусственных абразивных материалов: нормального и белого электрокорунда; черного и зеленого карбида кремния. Электрокорунд – это кристаллическая окись алюминия (AI2O3), получаемая плавкой в электрических печах бокситовой руды. Белый электрокорунд содержит несколько больше окиси алюминия; его режущая способность выше, чем нормального электрокорунда.
Важнейшим параметром, определяющим режущие свойства шлифовального круга, является его зернистость (обозначаемая номером), т. е. размеры зерен (иначе «крупность» зерен) абразивных материалов, из которых состоит круг. Зерна абразивных материалов обладают очень высокой твердостью и теплостойкостью, имеют острые кромки, получающиеся при дроблении кусков, и способны резать весьма твердые металлы (отбеленную корку чугуна, закаленную сталь и т. п.).
Зернистость шлифовального круга оказывает влияние на качество шлифуемой поверхности: чем мельче зерно круга, тем более чистой получается поверхность.
Зернистость шлифовальных кругов обозначают номером, соответствующим числу отверстий на один погонный дюйм сита, через которое просеивают абразивный материал после его измельчения.
Размеры зерен определяются размерами сторон ячеек контрольных сит, применяемых для анализа зернистых абразивных материалов. Так, например, номер зернистости «16» означает, что абразивные зерна этой зернистости проходят через сито с ячейками размером стороны 200 мк и не проходят через сито с ячейками размером стороны 160 мк.
Для изготовления шлифовальных кругов берут абразивные зерна от
№ 10 до № 90; шлифовальные порошки – от № 100 до № 320; микро-порошки марок – от М28 до М5. Крупнозернистые круги (до № 24) применяют для чернового шлифования; среднезернистые (до № 60) – для обычного шлифования и заточки инструмента; мелкозернистые (до № 120) – для чистового шлифования. Круги с очень мелкими зернами (№ 120–320 и микропорошки) используют для шлифования резьб.
Связку, скрепляющую абразивные зерна, изготовляют на неорганической или органической основе – керамической, силикатной, магнезиальной, бакелитовой и вулканитовой. Наибольшее распространение в машиностроении получила керамическая связка, которую приготовляют из огнеупорной глины, полевого шпата и кварца.
Достоинства керамической связки – огне- и водостойкость, большая производительность.
Бакелитовая (органическая) связка – синтетическая смола. Круги на бакелитовой связке прочны и упруги, но плохо переносят воздействие охлаждающей жидкости.
Другой вид органической связки – вулканитовая связка, состоящая из каучука (резины) и серы. Круги на вулканитовой связке прочны и водостойки, позволяют работать с большой окружной скоростью, но сравнительно быстро засаливаются.
Твердость шлифовального круга характеризуется сопротивляемостью связки вырыванию абразивных зерен с поверхности круга под действием внешних сил.
В России приняты семь классов твердости абразивных кругов, причем каждый класс подразделяют по степени твердости. Обозначения кругов различной твердости приведены в табл. 14.
Таблица 14
Название и обозначение класса твердости круга | Обозначения подразделений классов твердости | |
Мягкий Среднемягкий Средний Среднетвердый Твердый Весьма твердый Чрезвычайно твердый | – М – СМ – С – СТ – Т – ВТ – ЧТ | М1; М2; М3 СМ1; СМ2 С1; С2 СТ1; СТ2; СТ3; Т1; Т2 ВТ1; ВТ2 ЧТ1; ЧТ2 |
Правильный выбор твердости круга оказывает существенное влияние на процесс шлифования и прежде всего на самозатачиваемость круга. Самозатачиваемость – это выкрашивание из круга затупленных зерен и обнажение новых зерен с острыми гранями. Если для шлифования данного материала выбран слишком твердый круг, зерна не будут выкрашиваться и, следовательно, самозатачивания не произойдет, что приведет к засаливанию круга и ожогу шлифуемой поверхности; из слишком мягкого круга зерна могут осыпаться, и он потеряет свою форму. Обычно для шлифования мягких материалов выбирают твердые круги, и наоборот.
Шлифовальные круги подвергают правке для восстановления его режущей способности, потерянной в результате засаливания и затупления, для исправления геометрической формы изношенного круга и обеспечения правильного расположения рабочей поверхности круга относительно оси его вращения после установки на шлифовальном станке. Применяют правку шарошками, твердосплавными роликами, абразивными дисками и алмазами.
Под правкой круга понимается процесс удаления с его поверхности слоя изношенных или засалившихся абразивных зерен.
Объемное соотношение абразивных зерен, связки и пор характеризует структуру круга. Структуру круга обозначают номерами от 0 до 12.
С увеличением структуры на один номер объем зерен в круге уменьшается на 2 %, а объем связки увеличивается на 2 % при постоянном общем объеме пор, но изменении их величины.
Круги с мелкими порами (структуры № 0–3) применяют для шлифования твердых и хрупких материалов, когда требуется высокая чистота поверхности; круги с порами среднего размера (структуры № 4–7) – для наружного круглого шлифования, а также для плоского шлифования мягких металлов; круги с открытыми порами (структуры № 8–12) —для скоростного шлифования.
Характеристика шлифовальных кругов находит отражение в их маркировке, в которой указывается также завод-изготовитель; например, марка «3-д Ильича Э46СМ25К ПП500´150´305 35 м/с» обозначает, что круг изготовлен на заводе имени Ильича из электрокорунда, имеет зернистость № 46, твердость СМ2, структуру № 5 на керамической связке, плоскую форму прямого профиля размером 500´150´305 мм, допускаемую скорость вращения 35 м/с. Иногда в маркировке не указывают структуру круга.
Основные виды шлифовальных работ
На шлифовальных станках можно выполнять шлифование наружных и внутренних цилиндрических, конических и фасонных поверхностей, шлифование плоских поверхностей, зубчатых колес, резьбы и другие шлифовальные работы с применением соответствующих кругов и приспособлений [11].
Шлифование наружных цилиндрических поверхностей производят на круглошлифовальных станках, применяя способы продольной и поперечной подачи или глубинный способ. Такие поверхности можно также шлифовать на бесцентровых станках при работе по методу продольной подачи или при шлифовании до упора.
На рис. 73, а, показано шлифование цилиндрической поверхности на бесцентровом станке методом продольной подачи. Цилиндрическая деталь 1 по загрузочным валикам 2 и 3 подается к вращающимся шлифующему 4 и ведущему 5 кругам, захватывается ими и поступает в рабочую зону для шлифования; здесь деталь поддерживается упором (ножом) 6. Отшлифованное изделие из рабочей зоны поступает на выходные направляющие планки 7.
За один проход шлифовальный круг снимает слой металла толщиной 0,02–0,3 мм (на диаметр заготовки).
![]() | ||||||||||||||||||||||||||||||||||
Рис. 73. Основные виды шлифования наружных, внутренних и конических поверхностей: а – шлифование цилиндрической поверхности; б – обработка внутреннего цилиндрического отверстия; в – шлифование отверстий колец; г, д – шлифование наружных конических поверхностей; 1 – деталь; 2, 3 – загрузочные валики; 4 – шлифующий круг; 5 – ведущий круг; 6 – упор; 7 – направляющие планки; 8 – поддерживающий ролик; 9 – прижимной ролик; 10 – ведущий ролик; 11 – корпус; 12 – шпиндель |
Шлифование до упора применяется для обработки ступенчатых деталей.
Внутренние цилиндрические поверхности шлифуют на внутришлифовальных, планетарно-шлифовальных и бесцентровых станках.
Внутреннее шлифование применяют главным образом при обработке точных отверстий в закаленных деталях, а также в случаях, когда по каким-либо причинам невозможно использовать другие, более производительные методы точной обработки отверстий, например алмазное растачивание, хонингование и др.
Существуют две основные разновидности внутреннего шлифования: 1) шлифование отверстия во вращающейся заготовке и 2) шлифование отверстия в неподвижной заготовке.
Первый способ применяют при шлифовании отверстий в небольших по размерам заготовках, преимущественно представляющих собой тела вращения, например, отверстий в зубчатых колесах, в кольцах шарико- и роликоподшипников, а второй – при шлифовании отверстий в заготовках корпусных деталей, которые неудобно или невозможно закрепить в патроне станка.
В обоих случаях осуществляется продольная подача шлифовального круга вдоль оси шлифуемого отверстия; в первом случае – движением шпиндельной головки, во втором – движением стола.
Наиболее существенное отличие внутреннего шлифования от наружного круглого шлифования заключается в том, что обработка производится кругом малого диаметра. Как правило, диаметр круга при внутреннем шлифовании составляет 0,7–0,9 диаметра шлифуемой заготовки.
В обычных конструкциях шпиндельных головок окружная скорость круга при шлифовании отверстий малого диаметра большей частью не превышает 10 м/с и возрастает с увеличением размеров головок в соответствии с увеличением диаметров шлифуемых ими отверстий, доходя до 30 м/с при диаметрах отверстий свыше 30 мм. Относительно малая жесткость шпинделя шлифовального круга ограничивает величину глубины резания (поперечной подачей), составляющей (в зависимости от диаметра шлифуемого отверстия) при предварительном шлифовании стали и чугуна 0,5–0,02 мм и при чистовом шлифовании – 0,002–0,01 мм на один двойной ход. Меньшие значения поперечной подачи применяют при диаметрах отверстий, не превышающих 40 мм, и при больших отношениях длины отверстия к его диаметру. Во всех случаях внутреннее шлифование производят с продольной подачей. Величина продольной подачи составляет, как и при круглом наружном шлифовании, 0,4–0,8 ширины круга – при предварительном шлифовании и 0,25–0,4 ширины круга – при чистовом, причем меньшие значения применяют при отношении длины отверстия к диаметру, равном трем.
Для обработки внутреннего цилиндрического отверстия деталь небольших размеров закрепляют в патроне станка и сообщают ей вращательное движение (рис. 73, б). Шлифовальный круг прямого плоского профиля имеет вращательное движение и две подачи: продольную вдоль оси и поперечную (радиальную) после каждого прохода. Круг должен иметь перебег на своей высоты.
Крупные детали, которые неудобно или невозможно закреплять в патронах, устанавливают на столе планетарно-шлифовального станка, шпиндель круга которого вращается не только вокруг своей оси, но и вокруг оси обрабатываемого отверстия (см. рис. 73, б); кроме того, шлифовальный круг получает продольную подачу вдоль оси.
Отверстия колец (рис. 73, в) шлифуют на бесцентровом станке.
Обрабатываемая деталь 1 вводится в рабочую зону и устанавливается между поддерживающим 8, прижимным 9 и ведущим 10 стальными роликами, находящимися в общем корпусе 11. Ролик 9, вращаясь на оси рычага, с заданным усилием прижимает обрабатываемую деталь к ведущему и поддерживающему роликам. Ведущий ролик, получающий движение от привода, вращает деталь со скоростью 40–60 м/мин. Осевым усилием, возникающим благодаря тому, что ось ведущего ролика повернута примерно на полградуса, деталь торцом прижимается к упору и шлифуется кругом, закрепленным на шпинделе 12. Шлифование обеспечивается благодаря силе трения, возникающей между ведущим роликом и деталью.
Бесцентровое шлифование обеспечивает очень высокую точность обработки.
Шлифование наружных конических поверхностей производят на круглошлифовальных станках путем поворота: 1) стола на угол конусности обрабатываемой детали (рис. 73, г); 2) шлифовальной бабки (рис. 73, д) и
3) передней бабки вместе с закрепленной в кулачковом патроне короткой шлифуемой деталью.
Наружные конические поверхности обрабатывают также заправкой шлифовального круга на конус, при этом улучшение качества шлифования детали достигается продольным колебательным движением круга. Внутренние конические поверхности шлифуют на бесцентровых станках путем поворота корпуса 12 (рис. 73, в) и детали на необходимый угол конусности, а также на внутришлифовальных станках путем поворота на определенный угол передней бабки с закрепленной деталью.
Фасонные поверхности отделывают на кругло- и плоскошлифовальных станках. К фасонному шлифованию относят также обработку направляющих станин сложной формы (рис. 74, а).
![]() | ||||||||||
Рис. 74. Основные виды шлифования фасонных поверхностей, зубчатых колес и резьбы: а – обработка направляющих станин сложной формы; б – шлифование тарельчатыми кругами; в – профильное копирование; г – отделка резьбы; 1 – деталь; 2 – шлифовальный круг |
Шлифование зубчатых колес осуществляют на зубошлифовальных станках методом обкатки или профильным копированием, применяя фасонные шлифовальные круги.
При обкатке зубья шлифуют двумя тарельчатыми кругами (рис. 74, б), которые устанавливают так, чтобы их торцы, обращенные к шпинделям, совпадали с боковыми сторонами зубьев. Боковые профили зубьев обрабатывают при сложных движениях зубчатого колеса и шлифовальных кругов.
При методе профильного копирования (рис. 74, в) зубья шлифуют фасонным кругом, имеющим форму впадины между зубьями. Таким шлифовальным кругом одновременно обрабатывают оба боковых профиля зубьев колеса.
Отделку резьбы производят на резьбошлифовальных станках однониточными или многониточными профильными шлифовальными кругами. Резьбошлифование бывает наружное и внутреннее. При наружном шлифовании резьбы многониточным кругом (рис. 74, г) деталь 1 устанавливают между центрами станка. Шлифовальный круг 2, укрепленный на шпинделе шлифовальной бабки, вращается от отдельного привода и имеет продольное перемещение на один шаг за один оборот детали.
Плоские поверхности шлифуют на плоскошлифовальных станках. Крупные детали закрепляют на столе станка при помощи упоров, планок и других приспособлений, а мелкие детали – при помощи электромагнитных плит.
Плоскости шлифуют периферией или торцом шлифовального круга.
|
![]() | ||||||
Рис. 75. Основные схемы шлифования плоскостей периферией круга: а – при возвратно-поступательном движении стола станка с обрабатываемой заготовкой; б – при закреплении обрабатываемой заготовки на вращающемся столе |
Шлифование периферией круга можно осуществить и при закреплении обрабатываемой заготовки на круглом вращающемся столе (рис. 75, б).
В этом случае шлифовальный круг совершает вращательное и одновременно возвратно-поступательное движение параллельно шлифуемой поверхности. Шлифование плоскостей торцом круга выполняют как при поступательном движении обрабатываемой заготовки, так и при ее вращении.
Контрольные вопросы и задания
1. Перечислите элементы режимов шлифования.
2. Как осуществляется наружное и внутреннее круглое шлифование?
3. Как осуществляется плоское шлифование?
4. Как осуществляется бесцентровое наружное шлифование?
5. Охарактеризуйте шлифовальные станки.
6. Какие инструменты используют для шлифования?
7. Перечислите основные виды шлифовальных работ.
8. Каковы основные виды шлифования фасонных поверхностей, зубчатых колес и резьбы?
Дата добавления: 2020-11-29; просмотров: 424; Мы поможем в написании вашей работы! |
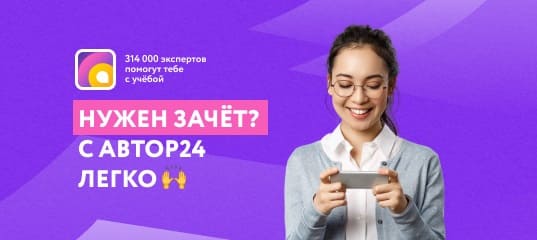
Мы поможем в написании ваших работ!