Современное производство керамических изделий
История развития техники и технологий производства керамики.
КЕРАМИЧЕСКАЯ ПРОМЫШЛЕННОСТЬ (Термин «керамика» происходит от греческого слова «керамос», что означает глина) — подотрасль промышленности строительных материалов, объединяющая предприятия по добыче сырья и производству грубой керамики (кирпича, дренажных и канализационных труб, черепицы); кислотоупорных и огнеупорных изделий; плиток (облицовочных, фасадных, для полов и стен); тонкой керамики (изделий из фарфора и фаянса); керамзита; изделий широкой номенклатуры электротехнической и радиотехнической промышленности и др.
Изготовление изделий из керамики основано на способности глинистых материалов образовывать с водой пластичное тесто, которое может принимать заданную форму и подвергаться обжигу. Процессы керамического производства многообразны, но в общих чертах сводятся к обработке сырья, приготовлению массы, формованию изделий, их сушке и обжигу.
Итак, керамическими называют изделия, изготовленные из глины с различными добавками и обожженные до камнеподобного состояния. Особенности керамической промышленности: повсеместная потребность в керамических материалах и изделиях, большая многотоннажность этой отрасли.
Керамическое производство относится к числу наиболее древних на земле. Наличие легкодоступного материала — глины — обусловило раннее и практически повсеместное развитие керамического ремесла.
|
|
Археологические раскопки, проводимые на территории многих стран Европы, Африки, Азии, Америки подтверждают повсеместное развитие керамического ремесла еще в каменном веке.
Первые изделия из глины были хрупкими и очень боялись влаги, поэтому хранить в них можно было только зерно и другие сухие продукты. Но однажды, удаляя золу погасшего костра, человек заметил, что глинистая земля, которую он всегда брал для изготовления изделий домашнего обихода, под действием тепла стала прочной как камень. С тех пор человек стал обжигать глиняные изделия для придания им прочности. Открытие обжига сделало глиняную посуду древнего человека практичной.
Керамические изделия тогда выполняли способами налепа и спирально-жгутовым — глиняный жгут укладывали один на другой по спирали. (рис.1.2)
рис.1.2 Намотка глиняного жгута и сглаживание поверхности кувшина
Первоначально основным видом керамических изделий были толстостенные сосуды с пористым черепком, круглым или коническим дном (придававшим устойчивость при установке в землю). В глину, чтобы она не трескалась при обжиге, добавлялись толченые раковины и измельченный гранит.
Способы изготовления керамических изделий с течением времени претерпевали существенные изменения. Стремление усовершенствовать труд и улучшить форму изделий привело к появлению гончарного круга.
|
|
1)
2) 3)
4)
Рис.1.3 Ножной (1) , ручной (2), гончарный круг с ременным приводом(3), электрический гончарный круг (4)
Гончарный круг впервые появляется у шумеров (на юге Месопотамии) в конце IV тыс. до н. э. В III- II тыс. до н. э. он распространился по Средней Азии ,Сирии, Египту, Греции, Индии. В других регионах это произошло значительно позже. И только в эпоху раннего Средневековья гончарным кругом стали пользоваться в Германии и России.
Сначала был изобретен ручной гончарный круг (рис.1.3 (2), состоящий из вертикальной оси, укрепленной в опоре; на неё насаживался свободно вращающийся горизонтальный круг.
С изобретением ножного гончарного круга (рис.1.3 (1) вращение круга производилось ногами с помощью большого махового колеса, и обе руки мастера могли формовать изделие. Гончарный круг позволил создавать симметричные, равномерно расширяющиеся или, наоборот, сужающиеся изделия разнообразной формы, значительно повысив производительность труда. Затем появился механический привод для гончарного круга. Позднее был изобретен электрический гончарный круг, используемый и в настоящее время. С его возникновением появилась возможность изменять число оборотов круга и производить более качественные изделия.
|
|
Освоение глиняных богатств, использование их в качестве строительного материала происходило у многих народов почти одновременно. Они независимо один от другого поняли возможности использования глины в качестве сырья для производства стеновых материалов.
Древние строители набивали ящики глиной и высушивали на солнце. Готовые кирпичи-сырцы покрывали смолой и из них возводили стены, а затем постройку облицовывали естественным камнем.
В большинстве стран с освоением техники обжига кирпича отказались от применения кирпича-сырца. Хотя обожженный кирпич и требовал больших затрат на изготовление, но люди на это шли, т.к. надежность и долговечность зданий повышалась во много раз.
Гончаров-кирпичников называли плинфоделателями, а кирпич – плинфот от греческого слова «plinthos», что значит плита. И действительно, форма кирпича того времени плоская плита. Чаще всего квадратная, размером 40х40 и толщиной 2,5 – 3 см., но встречаются плинфы и поменьше.
На Руси кирпичное ремесло возникло в середине 10 в., однако кирпич применялся исключительно для сооружения укреплений и храмов, и только в 18 в. началось строительство жилых домов из кирпича.
|
|
За время существования кирпичного производства кирпич не раз менял свою форму, размеры, а технология во многом оставалась без изменения. Во все времена качество изделий прямо зависело от сырья и его подготовки.
Процесс производства заключался в следующем:
выкопанную глину грузили на подводы и доставляли к кирпичным сараям. Чаще всего так называли гончарные мастерские и заводы по выработке кирпича. Там глина вылеживалась в течение нескольких месяцев. Затем комья глины разбивали кирками или деревянными лопатами и складывали в ямы или специальные ящики. Глину слегка поливали водой и оставляли примерно на сутки для вылеживания, а уже потом начинали мять. Месили или мяли глину чаще всего босыми ногами. По мере надобности добавляли воду, часов через пять глиняное тесто было готово. Эту невероятно изнурительную и монотонную работу со временем пытались облегчить. В середине 19 века начали внедрять глиномешалки, состоящие из ведра с валом, на котором горизонтально крепились ножи – глина загружалась сверху, и ножи, вращаясь, размельчали ее. Такие глиномешалки приводились в движение лошадьми.
Рис.1.4 Конная глиномялка
Так появились конные глиномялки. Готовое глиняное тесто быстро твердеет, поэтому его прикрывали соломой или рогожей, чтобы дольше не высыхала, и использовали по мере надобности для формовки кирпича.
Формовали кирпич в плоть до середины ХIХ века вручную.
Существовало 2 основных способа формовки: подпятный и столовый.
Для подпятного кирпича глину помещали в форму – деревянный ящик и уплотняли его пяткой, так кирпич получался более плотным. Столовый кирпич, как следует из названия, формовали на столе руками. Иногда глину уплотняли деревянным молотком – чекмарем. Стоя за столом, мастер брал форму, обычно это ящик с двумя ручками, внутри имелись перегородки по числу кирпичей. Наиболее удобной считалась форма на 4-6 кирпичей, т.к. при большом количестве ячеек труднее переносить форму и выдавливать из нее кирпичи. Итак, заполнив форму глиной, утрамбовав ее руками или чекмарем, мастер снимал длинным ножом или специальным правилом излишки глины и относил форму на место сушки. Там он выдавливал пальцами сформованные кирпичи на помост или доски. Первое время сушили кирпичи под открытым небом. Позднее стали строить навесы и решетчатые сараи.
Сушильный сарай
Там кирпичи высушивались также естественным путем, но они сохли более равномерно, т.к дождь теперь был не страшен. Это, безусловно, сказалось на качестве кирпича.
На протяжении многих лет постоянно изобретались различные машины для механизации процесса переработки глины и формовки кирпичей. Во второй половине 19 века применялось несколько типов кирпичеделательных машин, которые работали по схожему принципу: по конвейерной ленте непрерывно двигалась глиняная масса, которая разрезалась на кирпичи вращающимся резаком (одновременно до 25 штук).
Далее следовал обжиг высушенного кирпича – сырца.
Кирпичи обжигали во временных печах, которые строили из необожженного кирпича (кирпича-сырца).
Печи состояла из нескольких кирпичных перегородок, стоящих параллельно друг другу, каждая перегородка была шириной примерно в 3 кирпича. На высоте порядка 2 футов (1,2 метра) перегородки соединялись перекладинами и образовывали одну большую стопку кирпичей с маленькими щелями между кирпичами. Кирпичи так укладывались друг на друга, чтобы горячий воздух проходил между ними снизу вверх, обжигая их таким образом. Стопка могла быть высотой до 6 метров.
Печи топили углем или деревом. Топки устанавливали в нижней части стопки, там же делали и дымоходы. После начали топки печи дымоходы закрывали.
Обжиг велся большими партиями сырца. Сначала обжиг вели на слабом огне, постепенно огонь усиливали. Когда сгорала копоть, обжиг считали законченным. После этого еще несколько дней кирпичи остывали в печи.
Время выгрузки определяли следующим образом: если к решетке на которой обжигали кирпич, приложить пучок соломы и она не воспламенится, значит пора выгружать. Общая длительность обжига равнялась двум-трем неделям.
Затем кирпич извлекали из печи и сортировали. Качественным считался кирпич, который имел правильную форму, размеры и при ударе молотком издает чистый звук. Дребезжащий звук (и глухой) свидетельствует о скрытых дефектах.
В дореволюционной России керамическая промышленность характеризовалась крайне низким уровнем техники, массовым применением тяжёлого ручного труда, неравномерным географическим размещением множества мелких предприятий и незначительными масштабами производства. Не было ни одного кирпичного завода круглогодичного действия, кирпич формовали вручную и только на некоторых заводах использовали ленточные прессы с паровым приводом.
Становление керамической промышленности в CCCP началось в годы 1-й пятилетки (1928-1932), когда были коренным образом реконструированы наиболее крупные керамические заводы. Большое количество заводов глиняного кирпича было переведено на круглогодичную работу на базе искусственной сушки сырца. Построены новые заводы по изготовлению плиток для полов, глазурованных плиток, санитарных керамических изделий. Керамические заводы строятся по возможности непосредственно вблизи карьеров глин. Отрасль интенсивно развивалась после Великой Отечественной войны 1941-45. В 50-е гг. построены заводы, оборудованные отечественными высокопроизводительными вакуум-прессами для формовки с тоннельными и камерными сушилками, обжиговыми и тоннельными печами, реконструированы ранее действовавшие предприятия. Освоены поточно-конвейерные механизированные линии, включающие вертикальные прессы и транспортирующие устройства, позволившие устранить тяжёлый ручной труд в производстве труб. В производство керамических плиток впервые в мировой практике внедрена новая технология: массы для всех видов керамических плиток изготовляют шликерным способом путём помола сырьевых материалов в водной суспензии в шаровых мельницах. Разработан, а впоследствии усовершенствован глазуровочный конвейер. С 70-х гг. по абсолютному уровню производства ряда основных материалов керамическая промышленность CCCP занимала 1-е место в мире.
Современное производство керамических изделий
В настоящее время керамические изделия различного назначения получают способами полусухого и сухого прессования из порошков влажностью 5-7%, пластическим формованием из масс влажностью 14-20%, литьем из шликера влажностью 30-45%.
Технология производства керамического кирпича методом пластического формования (как полнотелого, так и пустотелого) состоит из следующих этапов:
1. Добыча сырья;
2. Его подготовка, которая заключается в очистке от посторонних включений, измельчении, смешивании с необходимыми добавками;
Куски глины тщательно измельчаются до размеров 100-150 мм, а затем при помощи специальных конвейеров с набором вальцов происходит последовательное дальнейшее измельчение глиняной массы (до размеров 1 мм) и удаление мелких каменных вкраплений. Затем в смесителе с фильтрующей решеткой глиняная масса увлажняется и тщательно перемешивается. Количество влаги доводится до 18-25%. В смесителе к глине примешиваются необходимые добавки. Чаще всего применяют способ пластического прессования. При этом к измельченному сырью (глине) сначала примешивают различные добавки:
· Чтобы увеличить её пластичность, используют пластифицирующие добавки – поверхностно-активные вещества (ПАВ), бетониты, высокопластичную глину.
· Чтобы понизить излишнюю пластичность исходного сырья и снизить его огневую и воздушную усадку, применяют отощающие добавки – кварцевый песок, шамот, пылевидный кварц, золы теплоэлектростанций.
· Для обеспечения пористости кирпича добавляют древесные опилки, измельченный бурый уголь, торф, отходы угольного производства. Такие добавки называют порообразующими или выгорающими, так как в процессе обжига они полностью сгорают.
· Чтобы снизить температуру спекания керамического черепка, используют флюсы и плавни – полевой шпат, тальк, мел, пегматит, доломит, железную руду.
· Необходимость той или иной добавки и её количества определяется в лабораториях завода опытным путем.
· Затем перемешанную до однородного состояния массу увлажняют до 18-23% и с помощью вакуумного или безвакуумного ленточного пресса формируют из неё кирпич-сырец.
3. Формование кирпича; прессами формуется брус, заготовка будущих кирпичей. отформованный брус разрезается на отдельные изделия, так называемый кирпич сырец.
4. Сушка;
Обжигать сразу кирпич сырец нельзя, так как на данном этапе он имеет очень высокое содержание влаги и при обжиге просто потрескается. Поэтому кирпичи сначала сушат, процесс сушки является обязательным. ГОСТ требует, чтобы на выходе кирпич-сырец имел уровень остаточной влажности 6-8.
В результате испарения воды освобождается место между частицами глины. Происходит уменьшение объема изделий или усадка. Температура сушки и обжига, а также темп роста температуры, играют важную роль в процессе изготовления кирпичей. Влага начинает испаряться при нагреве изделия в диапазоне температур 0-150°C. Когда температура нагрева достигает 70°C, давление водяных паров может достичь критических значений, что в свою очередь приведет к возникновению трещин. Рекомендуемый темп роста температуры 50-80°C в час. При этом скорость испарения влаги с поверхности, не будет опережать скорость парообразования внутри изделия. После завершения сушки кирпичи отправляются на обжиг в специальные печи.
5. Обжиг. Осуществляется в тоннельных и кольцевых печах. Заключительным этапом производства керамического кирпича является его обжиг, который происходит в три этапа: сначала изделия прогреваются (в диапазоне температур 200-800°C), затем непосредственно обжигаются при температуре около 10000С, после чего постепенно охлаждаются, темпы охлаждения достигают значений в 250-300°C в час. Резкая смена температур может привести к появлению трещин, поэтому её снижают постепенно, отбирая из камер горячий воздух и разбавляя его атмосферным. После обжига структура изделия полностью меняется. Теперь это камневидный предмет, водостойкий, прочный, устойчивый к перепадам температур, а также обладающий другими полезными свойствами.
Дата добавления: 2020-11-27; просмотров: 83; Мы поможем в написании вашей работы! |
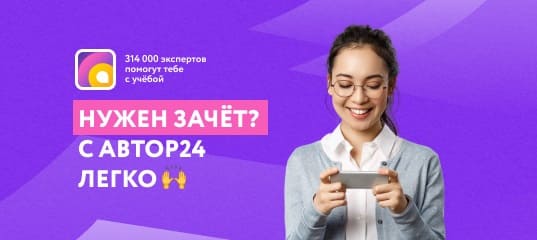
Мы поможем в написании ваших работ!