Тема № 5.4. Основные принципы построения системы допусков и посадок. Единая система допусков и посадок.
Тема 5.2 Основные принципы построения системы допусков и посадок.
Для обеспечения качества продукции, повышения эффективности производства за счет унификации требований к точности, увеличения масштабов выпуска продукции и т. п. используется обязательная система допусков и посадок, охватывающая все размерные параметры. Выпускаются отдельные стандарты на предельные отклонения и посадки различных видов соединений, но все они объединяются едиными принципами построения. Таких принципов можно выделить восемь [21]. 1. Принцип применении рядов предпочтительных чисел заключается в том, что числовые ряды интервалов размеров, градаций точности и других показателей строятся по одному из основных или производных рядов предпочтительных чисел. 2. Принцип масштабных коэффициентов основан на том, что изменение величины допуска в зависимости от размера подчиняется определенной закономерности, описываемой некоторой функцией размера, называемой единицей допуска. 3. Принцип применения коэффициентов точности заключается в том, что числовые значения допусков размеров получаются умножением единицы допуска (значения масштабного коэффициента при среднем в данном интервале значении размера) на определенное число (коэффициент точности). 4. Принцип применения упрощающих способов построения посадок заключается в использовании двух эквивалентных по простоте способов, при которых расположение поля допуска одной, называемой основной деталью, из двух соединяемых деталей оставляют неизменным, необходимую же посадку обеспечивают за счет смешения поля допуска сопрягаемой детали, что обеспечивает требуемый для посадки зазор или натяг. 5. Принцип экономии материала при установлении поля допуска основной детали заключается в расположении последнего "в тело": поле допуска отверстия располагается вверх (в сторону положительных отклонений) при нижнем отклонении Е1 = 0, а вала - вниз (в сторону отрицательных отклонений) при верхнем отклонении е$ = 0. Экономия получается в результате того, что допустимые отклонения действительных размеров уменьшают массу основной детали. 6. Принцип унификации полей допусков предусматривает выделение из общего числа стандартизованных полей допусков полей допусков предпочтительного применения. 7. Принцип физически обоснованного изменения зазора в зависимости от размера соединения заключается в том, что зазоры и натяги изменяются в зависимости от размера соединения по законам, отвечающим физическим условиям применения посадок. 8. Принцип приведения норм точности к определенному температурному режиму указывает на необходимость отнесения стандартизованных предельных отклонений размерных параметров к определенной температуре. Такой температурой является 293,15 К (+20°С) по международной практической температурной шкале. |
|
|
|
|
Тема № 5.3. Система отверстия, система вала
Предусмотрены посадки в системе отверстия и системе вала (рисунок 4.3).
В системе отверстия посадки образуются соединением различных по расположению поля допуска валов с основным отверстием, обозначаемым Н, поле допуска которого располагается одинаковым образом – с нижним отклонением, равным нулю (ЕI = 0), т. е. нижняя граница допуска располагается на нулевой линии.
В системе вала посадки образуются соединением различных по расположению поля допуска отверстий с основным валом, обозначаемым h, поле допуска которого располагается одинаковым образом – с верхним отклонением, равным нулю (es = 0), т. е. верхняя граница поля допуска располагается на нулевой линии.
а б
Рисунок 4.3 – Примеры расположения полей допусков в системе отверстия (а)
|
|
и системе вала (б)
По технологическим и экономическим соображениям главным образом используется система отверстия, так как в этом случае сокращается количество типоразмеров дорогостоящего инструмента для финишной обработки отверстий (зенкеров, разверток, протяжек и т. п.). Валы же вне зависимости от расположения поля допуска обрабатываются одним и тем же резцом или шлифовальным кругом.
Систему вала применяют, как правило, по конструктивным соображениям, например, когда требуется чередовать соединения нескольких отверстий одинакового номинального размера на одном валу, но с различными посадками. В некоторых случаях система вала выгоднее экономически, например, при возможности изготовления деталей типа тяг, осей, валов из точных холоднотянутых прутков без механической обработки их наружных поверхностей.
Тема № 5.4. Основные принципы построения системы допусков и посадок. Единая система допусков и посадок.
Системы допусков и посадок облегчают назначение точностных параметров деталей, ограничивая промышленность минимально необходимыми, но достаточными для реальных целей возможностями выбора.
В настоящее время большинство стран мира применяют системы допусков и посадок ISO (International Organisation for Standarti-sation), которые созданы для возможной унификации национальных систем допусков и посадок.
|
|
В нашей стране переход на единую систему допусков и посадок и основные нормы взаимозаменяемости, которые основаны на стандартах и рекомендациях ISO, начался с 1977 г. Такой переход создает возможности для международной специализации и кооперирования при производстве деталей, сборочных единиц, технологической оснастки, машин и т. п.; обеспечивает повышение конкурентоспособности отечественной продукции на мировом рынке; обеспечивает эффективность научно-технического обмена между различными странами и др.
Для реализации принципа взаимозаменяемости необходимо применение единой системы нормирования точности геометрических параметров изделий машиностроения при их проектировании, изготовлении и эксплуатации.
Системой допусков и посадок называется совокупность рядов числовых значений допусков и посадок, закономерно построенных на основе опыта, теоретических и экспериментальных исследований и оформленных в виде стандартов.
В настоящее время разработаны и действуют системы допусков и посадок для типовых видов сопряжения: гладких, конических, резьбовых, шпоночных, шлицевых, зубчатых передач и др.
В стране с 1980 г. используется единая система допусков и посадок (ЕСДП).
ЕСДП является системой нормирования точности геометрических параметров изделий в машиностроении, она построена на международной (ISO) системе допусков и посадок, применяемой в большинстве стран мира.
Ее действие распространяется на сопрягаемые и несопрягаемые при сборке цилиндрические, плоские и другие гладкие элементы деталей.
В ЕСДП ряды допусков и посадок установлены для диапазонов размеров: менее 1 мм; свыше 1 до 500 мм; свыше 500 до 3150 мм; свыше 3150 мм до 10000 мм.
Величины допусков, размещенных в таблицах ЕСДП, определяются с учетом двух факторов – влияния размера на точность обработки и измерения деталей и требований к точности деталей в зависимости от назначения изделия.
T = ai (1.5), где i – единица допуска связанная зависимостью с размером,
а – число единиц допуска, определяемое номером квалитета.
Под квалитетом понимают совокупность допусков, характеризуемых постоянной относительной точностью, выражаемой в числе единиц допуска. Точность в пределах одного квалитета зависит только от номинального размера.
В ЕСДП для размеров до 500 мм установлено 19 квалитетов: 01, 0, 1, …, 17, для размеров от 500 до 3150 мм – 18 квалитетов. В машиностроении используются квалитеты от 5 до 17, число а единиц допуска для этих квалитетов соответственно: 7, 10, 16, 25, 40, 64, 100, 160 и так далее до 1600. Таким образом, при переходе от одного к другому более грубому квалитету величина допуска увеличивается в 1,6 раза. Через каждые пять квалитетов допуск увеличивается в 10 раз. Допуски системы ИСО обозначаются: IT01, IT0, . . . , IT17.
Для построения рядов допусков каждый из диапазонов размеров разделен на интервалы, например, в диапазоне от 1 до 500 мм установлено 13 интервалов: до 3 мм, св. 3 до 6 мм, св. 6 до 10 мм, …, св. 400 до 500 мм. Для полей допусков, образующих посадки с большими зазорами или натягами введены промежуточные интервалы, что уменьшает колебание зазоров и натягов, делает их более определенными.
Назначать допуск для каждого размера нецелесообразно. В каждом интервале принято одинаковое значение единицы допуска. Оно определяется по значению среднего геометрического крайних размеров интервала
Dср.г= (DmaxDmin)0,5 (1.6)
Допуски и отклонения, установленные стандартами, относятся к деталям, измеренным при нормальной температуре, которая во всех странах принята равной +200С. При этой же температуре выполняется градуировка и аттестация измерительных средств. В случае существенного влияния температурных условий измерения на его точность вводят расчетные поправки, учитывающие линейное расширение материала детали и измерительного средства.
Основное отклонение. Это одно из двух (верхнее или нижнее) отклонений, используемое для определения положения поля допуска относительно нулевой линии, т. е. номинального размера. Таким отклонением является отклонение, ближайшее к нулевой линии (рисунок 4.4).
Рисунок 4.4 – Расположение основных отклонений отверстий и валов в ЕСДП
Предусмотрено 27 вариантов основных отклонений валов и отверстий, что обеспечивает образование посадок с зазором, с натягом и переходных в требуемом для машиностроения ассортименте.
Основные отклонения отверстий обозначают прописными буквами латинского алфавита, валов – строчными буквами. Основное отверстие в системе отверстия обозначается Н, основной вал в системе вала – h.
Основные отклонения A – H (a – h) предназначены для образования полей допусков в посадках с зазорами; отклонения Js – N (js – n) – в переходных посадках; отклонения P – ZC (p – zc) – в посадках с натягом.
Каждая буква обозначает ряд основных отклонений, значение которых зависит от номинального размера. Основные отклонения отверстий приняты симметричными основным отклонениям валов относительно нулевой линии (с небольшим исключением).
Основные отклонения Js и js не имеют числового значения.
Поле допуска образуются сочетанием одного из основных отклонений с допуском по одному из квалитетов. В соответствии с этим правилом поле допуска обозначают буквой (иногда двумя) основного отклонения и номером квалитета, например, для вала h6, d11, ef9; для отверстия H6, D11, CD10.
Поле допуска ограничено с одной стороны горизонтальной линией, определяемой основным, т. е. одним из предельных отклонением (рисунок 1.4). Второе предельное отклонение, ограничивающее поле допуска с другой стороны, образуется по основному отклонению и допуску принятого квалитета.
Если основное отклонение верхнее, то нижнее отклонение для вала определяется зависимостью ei = es – IT, для отверстия EI = ES – IT. Если основное отклонение нижнее, то соответственно: es = ei + IT, ES = EI + IT. Отклонения учитываются со своим знаком.
Во всех трех диапазонах размеров, охватываемых ЕСДП, определены для применения основные ряды полей допусков. В соответствии с рекомендациями ИСО и практикой машиностроения в ЕСДП для диапазона размеров 1 – 500 мм в основных рядах выделены предпочтительные ряды полей допусков, они обеспечивают потребности в 90-95% посадок общего применения. Их применение повышает уровень унификации изделий, сокращает номенклатуру режущих инструментов и калибров, благоприятствует специализации и кооперированию предприятий машиностроения.
В ЕСДП для всех диапазонов размеров установлены для применения рекомендуемые посадки из основных рядов полей допусков отверстий и валов. Для диапазона 1 – 500 мм из них выделены предпочтительные посадки. Унификация посадок облегчает работу конструкторов и удешевляет изготовление деталей.
Дата добавления: 2020-11-23; просмотров: 294; Мы поможем в написании вашей работы! |
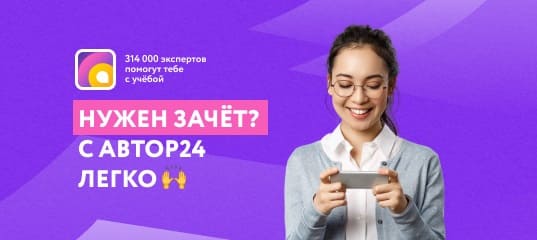
Мы поможем в написании ваших работ!