Влияние состава покрытия на качество шва
Сварочные материалы.
Вспомним кое-что о металлах.
Маркировка сталей:
Например 15 Х1М1ФА
Азот | А* | Кобальт | К | Никель | Н |
Алюминий | Ю | Кремний | С | Ниобий | Б |
Бор | Р | Марганец | Г | Селен | Е |
Ванадий | Ф | Медь | Д | Титан | Т |
Вольфрам | В | Молибден | М | Хром | Х |
*– только в высоколегированных сталях, не в конце.
Основной легирующий элемент – углерод
Сварочные материалы:
- проволока, стержни и пластины
- порошковые проволока и лента
- электроды
- флюсы
- защитные газы
Сварочная проволока выпускается по ГОСТ 2246 диаметром от 0,3 до 12 мм Для механизированных способов сварки используется проволока до 5 мм.
Проволока может иметь чистую или омедненную поверхность. Проволока диаметром 0,3…1,6 мм поставляется, как правило, в кассетах . При транспортировке и хранении проволока упаковывается в водо пыле непроницаемую тару (упаковку). Бухта или касета с проволокой должны иметь бирку с указанием диаметра, марки проволоки , номера партии, и даты выпуска (упаковки).
Например 3 Св-08 А О ГОСТ 2246–70
О – проволока омедненная
Э – проволока предназначена для изготовления электродов
Св-08 – сера и фосфор по 0,04 %
Св-08А – '' – по0,03%
Св-08АА – '' – по0,02 %
Электродные проволоки большого сечения, стержни и пластины используются при электрошлаковой сварке.
|
|
Вольфрамовые электродные стержни (Æ 0,5…10 мм)
Порошковая проволока – это непрерывный электрод, состоящий из металлической оболочки и порошкового наполнителя.
Проволоки бывают шовные и бесшовные.
Коэф. заполнения определяется структурой
Порошковые проволоки разделяются на:
- самозащитные
- для сварки в СО2
- специального назначения (легированные, наплавочные)
Используются в основном диаметры 2…3,2 мм
Проволоки маркируются ПП – марка.
Поскольку основным разработчиком порошковых проволок в СССР являлся Инстиут сварки украинской Академии Наук, то большинство отечественных проволок маркируются ПП – АН [№].
Порошковые проволоки , особенно шовные весьма гидроскопичны и плохо прокаливаются, поэтому требуют особо тщательного хранения.
Сварочные электроды – состоят из стержня и покрытия.
Стержни – сварочная проволока, рихтованная и нарубленная длиной 350 или 450 мм.
Покрытие , шлакообразующие: полевой шпат, кремнезем, каолин, слюда, тальк, ильменитовый и рутиловый концентраты, марганцевая руда, гематит, мрамор, магнезит, плавиковый шпат и др.
Газообразующие – органика: оксициллюлоза, крахмал, древесная мука, дакстрин; карбонаты: мрамор, мел, известняк, доломит, магнезит, сидерит.
|
|
Раскислители – главным образом ферросплавы: ферромарганец, ферросилиций, ферротитан и др.
Легирование как правило через ферросплавы марганца, кремния, вольфрама, молибдена, хрома, никеля, титана, а также ниобием бором и другими элементами.
Для стабилизации горения дуги вводят соединения щелочных и щелочноземельных (калия, натрия, кальция, бария) в виде соединений таких как поташ, кальценированная сода, полевой шпат, мел, мрамор,углекислый барий.
Для повывшения пластичности обмазочной массы в состав вводят пластификаторы – бентонит, каолин, тальк, слюду, целлюлозу идр.
В качастве связующего используется натриевое, калиевое или натрево-калиевое жидкое стекло.
Электроды классифицируются по: назначению; типу покрытия; механическим свойствам; способу нанесения и количеству покрытия.
Электроды для сварки и наплавки сталей в зависимости от назначения в соответствии с ГОСТ 9466 паодразделены на ряд классов: – для сварки углеродимстых и легированных конструкционных сталей; – для сварки легированных теплоустойчивых сталей; – для сварки высоколегированных сталей с особыми свойствами; – для наплавки поверхностных слоев с особыми свойствами.
|
|
Маркировка Паспорт электрода.
Для конструкционных сталей:
1- тип ( Э38…….Э150)
2- марка
3- диаметр стержня (2,0; 4,0)
4- назначение: У – св. углеродистых и низколегированных, Л – легированных конструкционных, Т – теплоустойчивых, В – высоко легир с особыми свойствами, Н – наплавки.
5- Обозначение толщины покрытия: М – тонкое, С – среднее, Д – толстое, Г – особо толстое
6- Группа качества (см Табл) 1,2,3
7- Индексы характеристик наплавленного металла по ГОСТ 9467 – 75, 10051 – 75, 10052 – 75
8- Обозначение вида покрытия: А – кислое, Б – основное, Ц – целлюлозное, Р – рутиловое
9- Пространственное положение: 1 – любое, 2 – кроме верт ¯, 3 – нижнее горизонтальное и , 4 – только нижнее
10- Обозначение рода тока, полярности, напряж хх ИП (см Табл) 0…9
Виды покрытия.
А – кислые содержат в большом количества ферросплавы (в частности ферромарганец) и окислы железа, имеют высокий коэф наплавки и высокую токсичность, дают кислые шлаки не содержащие СаО.
Р – основа – рутиловый концентрат TiO2(45%) , алюмосиликаты(слюда, полевой шпат) карбонаты(мрамор) и органика для газозащиты.
Б – содержит в основном карбонаты (мел, мрамор, магнезит) и плавиковый шпат СаF2 и ферросплавы, хорошо удаляют серу и фосфор
|
|
Пример:
![]() |
Для теплоустойчивых сталей:
1 – Химсостав наплавленного металла
7 – входит предельная рабочая температура, при которой регламентированы показатели длительной прочности наплавленного металла.(0 –ниже 450… 9 – свыше 600 оС).
Влияние состава покрытия на качество шва
Упаковка, хранение, подготовка, контроль.
Прокалка электродов:
Электроды для сварки углеродистых и низколегированных конструкционных сталей:
– с основным покрытием ( УОНИ, ТМУ–21У, ТМЛ–3У и др.)
при Т = 380оС, время 2 часа.
– с рутиловым и рутило-целюлозным покрытием (МР–3, АНО–4, ОЗС–4 и др.) при Т = 170оС . время 1 час.
Электроды для сварки теплоустойчивых сталей:
– с основным покрытием (ОЗЛ–6, ЦЛ–9, ЦТ–26, ЭА–400/10У и др.)
при Т = 220 оС время 1 час.
– с рутиловым покрытием (ВСЦ–4А) при 100оС время 1 час.
Прокалка снижает содержание водорода в наплавленном металле более, чем в 6 раз. Прокаленные электроды хранятся в сушильном шкафу при температуре 60…80оС.
Подача к рабочему месту в количестве не более, чем на одну смену. На рабочем месте хранение в специальном пенале.
Режимы прокалки электродов, порошковой проволоки и флюсов
Марка сварочного материала | Режимы повторной (перед использова нием) прокалки | |||
температура, •С | Продолжи-тельность. ч (допуск +0,5 ч) | |||
номинальная | предельное отклонение | |||
Электроды ТМУ-21У, ЦУ-5, ЦУ-6, ЦУ-7, ЦУ-8, ИТС-4С, УОНИ-13/45, УОНИ-13/55, ТМЛ-1У, ЦЛ-39, ЦЛ-20, ЦЛ-45, ТМЛ-3У, ЦУ-2ХМ, ТМУ-46, ТМУ-50 | 380 | ±20 | 2,0 | |
МР-3, АНО-4, АНО-6М, ОЗС-4, АНО-18, АНО-24 | 170 | ±20 | 1,0 | |
ОЗЛ-6, ЦЛ-9, ЦЛ-25/1, ЦЛ-25/2, ЗИО-8, ЭА-395/9, ЦТ-10, ЦТ-26, ЦТ-26М, ЦТ-15К, ЭА-400/10У, ЭА- 400/10Т, ЦТ-15 | 220 | ±20 | 1,0 | |
ВСЦ-4А | 100 | ±10 | 1,0 | |
Порошковая проволока | ||||
ПП-АН1 | 165 | ±15 | 1,0 | |
ПП-АН3, ПП-АН7 | 240 | ±10 | 2.0 | |
СП-2 | 200 | ±10 | 1.5 | |
ПП-АН8 | 245 | ±5 | 2.0 | |
СП-3 | 200 | ±10 | 1.5 | |
Флюсы | ||||
АН-348А, АН-348АМ, ОСЦ- 45, ОСЦ-45М, АНЦ-1 | 350 | ±50 | 1,0 | |
АН-42, АН-42М, ФЦ-22 | 650 | ±20 | 4.0 | |
ФЦ-11 | 375 | ±20 | 4.0 | |
ФЦ-16 | 620 | ±20 | 4.0 |
Флюсы
Химический состав флюса влияет на состав и свойства наплавленного металла.
Но в некоторых случаях хим. состав флюса может влиять на структуру и не изменяя хим состава металла. Так: при сварке хромоникелевых сталей под высоко кремнистым флюсом ОСЦ–45 получаем крупное зерно, хотя содержание Si увеличивается всего на 0,1 %.
Применение различных флюсов обусловлено и различными требованиями к физическим свойствам шлака, так при сварке кольцевых швов вязкость шлака должна быть примерно в 3…5 раз выше, чем при сварке в нижнем положении.
Для сварки конструкционных углеродистых и низколегированных сталей применяют в основном плавленые высокомарганцовистые флюсы (кислые) с суммарным содержанием (в различном сочетании) SiO2 и MnO примерно 80%, 6…9 % CaF2 , 6% CaO , 3…7 % MgO , 4…5 % Al2O3 и др.(АН–348А, ОСЦ–45, АНЦ–1)
Для сварки легированных теплоустойчивых сталей с целью уменьшения эффекта старения, применяют флюсы с ограничением SiO2 до 20 или даже 10% и MnO до 2…7 % в низко марганцовистых , и до 0,5 % в без марганцовистых флюсах (АН–10, АН–15, АН–42, ФЦ–22, 480Ф–10 и др.) при содержании СаF2 и Аl2О3 примерно по 20…30 % и Сао и МgО примерно по 10%.
При сварке высоколегированных сталей наличие окиси марганца и кремния приводит выгоранию (окислению) легирующих элементов, поэтому их содержание ограничивают до 0,3 и 4 % соответственно.(АН–30, 480Ф–6, 480Ф–7.) , при этом увеличивается содержание СаF2 до 20…60 %, СаО до 10…20 %, Аl2О3 до 20…40 %.
Уменьшение содержания SiO2 менее 3 % приводит интенсивному образованию пор в наплавленном металле. Кроме того уменьшение SiO2 и MnO снижает технологичность флюсов. Такие флюсы – керамические (спеченные гранулы). Такие флюсы при хранении весьма гигроскопичны и требуют прокалки при температуре 650…800 оС в течении 4 часов. В то время как плавленые прокаливаются при 300 оС.
Для электрошлаковой сварки применяют флюсы с большим содержанием ТiО2 для увеличения электропроводности.
Газы и газовые смеси
Газы применяемые при газопламенной обработке:
Кислород – при нормальных условиях имеет плотность 1,33 кг/м3, температура кипения –183оС (90 К), из одного литра жидкого кислорода получается 860 л. при 1кг/см2 Транспортируется в танках в жидком состоянии и в баллонах в газообразном при давлении 150 кг/см2 , объем стандартного баллона 40 литров.(6000л. газа с баллона при нормальном давлении).
Горючие газы:( ацетилен, водород, СО, метан, пропан, пары керосина и бензина)
Ацетилен обеспечивает максимальную температуру пламени 3200 оС, но является взрывоопасным газом. Поэтому баллон емкостью 40 л. на заполнен пористой массой и ацетоном. Ацетилен имеет очень высокую растворимость в ацетоне и при давлении 16 кг/см2 объем газа составляет – 5 м3 . Ацетилен может быть получен и из карбида кальция по реакции:
СаС2 + 2Н2О = С2Н2 + Са(ОН)2
В специальных ацетиленовых генераторах. Ацетилен при этом получается дешевле, но образующаяся известь загрязняет окружающую среду и этот способ в пределах населенных пунктов запрещен.
Защитные газы
Инертные в основном применяются аргон и гелий. Аргон сварочный марки А имеет чистоту > 99,99 % и влажность < 0,03 г/м3 . Инертные газы транспортируются в баллонах в газообразном состоянии при давлении 150 кг/см2. Температура кипения аргона –185,5 оС, а гелия –268,9 оС (4 К). Поэтому аргон может поставляться на предприятия в больших количествах в жидком виде – в танках-газификаторах.
По отношению к меди инертным может считаться азот и он используется в качестве защитного при сварке меди.
Активные в первую очередь СО2 и ее смеси с кислородом или аргоном.
Углекислота имеет температуру кипения (сублемации) –78,9 оС и содержится в 40 литровых баллонах в жидком состоянии. В зависимости от температуры давление в баллоне меняется: –30оС 14,5 ати; –10 26 ати; 0 35,5 ати; +20 58,5 ати.
В баллон заливают 25 кг жидкой углекислоты из которой получают примерно 12,5 м3 газа. ( расход газа на защиту около 10 л/мин или 0,6 м3/час) т е один баллон на 20 часов.
Сварочный углекислый газ при минимальном содержании влаги ( в отличии от пищевого) обеспечивает хорошую защиту нормальные условия для протекания окислительно-восстановительные процессов при наличии повышенного содержания кремния и марганца в проволоке (Св-08Г2С).
Добавление 3…5 % кислорода к СО2 снижает разбрызгивание металла примерно не 30 %.
При наплавке стеллитов используются смеси аргона с 7…12 % водорода. Это обеспечивает раскисление поверхности металла и хорошее растекание присадки.
Дата добавления: 2020-11-23; просмотров: 166; Мы поможем в написании вашей работы! |
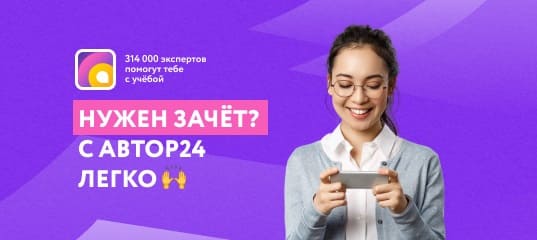
Мы поможем в написании ваших работ!