Тема 4 Противопомпажные клапаны
Лекция: Трубопроводная арматура
Тема 1 Общие сведения о ТПА
Эксплуатационная надежность МГ в значительной степени определяется надежной работой трубопроводной арматуры.
Трубопроводная арматура – техническое устройство, устанавливаемое на трубопроводах и емкостях, предназначенное для управления потоком рабочей среды путем изменения площади проходного сечения.
Вся ТПА классифицируется по назначению:
Запорная арматура – арматура, предназначенная для перекрытия потока рабочей среды.
Регулирующая арматура – арматура, предназначенная для регулирования параметров рабочей среды посредством изменения ее расхода.
Предохранительная арматура – арматура, предназначенная для автоматической защиты оборудования от недопустимого превышения давления посредством сброса избытка рабочей среды.
Обратная арматура – арматура, предназначенная для автоматического предотвращения обратного потока рабочей среды.
Так же ТПА классифицируется по типу присоединения: разборное соединение (фланцевое, муфтовое, цапковое, штуцерное), неразборное соединение (под приварку).
К основным параметрам запорной арматуры относятся: номинальный диаметр, номинальное давление, температура рабочей среды, тип присоединения к трубопроводу, масса.
Номинальный диаметр (DN) – параметр, применяемый для трубопроводных систем в качестве характеристики присоединяемых частей арматуры.
|
|
Номинальное давление (PN) – наибольшее избыточное давление, выраженное в МПа (кгс/см2), при температуре рабочей среды 20 С, при котором обеспечивается заданный срок службы (ресурс) корпусных деталей арматуры, имеющих определенные размеры, обоснованные расчетом на прочность при выбранных материалах и характеристиках прочности их при температуре 20 °С
ТПА маркируется следующим образом:
– конструктивный тип арматуры – краны: пробно-спускной – 10, трубопроводный – 11; запорное устройство указателя уровня – 12; вентиль – 13, 14,15; клапаны: обратный подъемный и приемный с сеткой – 16, предохранительный – 17, обратный поворотный – 27; регулятор давления – 21; задвижка – 30, 31; затвор – 32; конденсатоотводчик – 45;
– материал корпуса арматуры – сталь: углеродистая – с, легированная – лс, коррозионностойкая (нержавеющая) – нж; чугун: серый – ч, ковкий – кч; бронза, латунь – б; алюминий – а; монельметалл – мн; титан – тн;
– тип привода – механический с передачей: червячной – 3, цилиндрической зубчатой – 4; конической – 5; пневматический – 6; гидравлический – 7; электромагнитный – 8; электродвигательный – 9;
– материал деталей уплотнения – бронза, латунь – бр, монельметалл – мн; сталь: коррозионностойкая (нержавеющая) – нж, нитрированная (азотированная) – нт; стеллит 0 ст; сормайт – ср; резина – р; пластмассы (кроме винипласта) – п; винипласт – вн.
|
|
Пример: запорная арматура с обозначением 15кч22еж (15 –вентиль, кч – корпус из ковкого чугуна, 22 – конструкция вентиля (по каталогу), нж – уплотнительные поверхности из нержавеющей стали); 15кч916бр – конструкция вентиля (по каталогу), бр – уплотнительные поверхности из латуни или бронзы); 11с320бк (11 – трубопроводный кран, с – корпус из углеродистой стали, 3 – привод механический с червячной передачей; 20 – конструкция крана (по каталогу), бк – уплотнительные поверхности выполнены непосредственно на корпусе, т.е. без вставных колец).
Требования, предъявляемые к трубопроводной арматуре:
– обеспечение герметичности отключения установок, аппаратов, сосудов, отдельных участков газопровода от технологических линий и сохранение этой герметичности длительное время;
– надежность и долговечность работы;
– пожаровзрывобезопасность;
–обеспечение герметичности рабочей полости по отношению к окружающей среде;
– минимальные размеры и вес.
Тема 2 Запорная арматуры
Наиболее распространенный вид трубопроводной арматуры – запорная арматура. Запорная арматура состоит из трех основных элементов: запорного устройства, привода и системы управления.
|
|
Запорное устройство представляет собой закрытый герметичный корпус, внутри которого размещен затвор. Корпус обычно имеет два (иногда и больше) присоединительных конца, при помощи которых он прочно закрепляется на трубопроводе. Затвор предназначен для герметичного разобщения части трубопровода. Он состоит из седла и запорного тела, которое при герметичном разобщении части трубопровода соприкасаются по поверхности, называемой уплотнительной, и образуют запорную пару.
Привод – это исполнительный механизм, перемещающий запорное тело внутри запорного устройства относительно седла из закрытого положения в открытое и наоборот.
Система управления – служит для подачи дистанционного или местного управляющего сигнала к исполнительному механизму с целью установки затвора в открытое или закрытое положение
Запорная арматура классифицируется по конструктивным типам: кран, клапан (вентиль), задвижка, затвор.
Кран – рисунок 1 запорный или регулирующий орган имеет форму тела вращения или части его, который проворачивается вокруг собственной оси, произвольно расположенной к направлению потока рабочей среды.
|
|
Рисунок 1 – Кран
Клапан (вентиль) – рисунок 2 запорный или регулирующий орган перемещается возвратно-поступательно параллельно оси потока рабочей среды.
Рисунок 2 – Клапан (вентиль)
Задвижка – рисунок 3 запорный или регулирующий орган перемещается возвратно-поступательно перпендикулярно оси потока рабочей среды.
Рисунок 3 – Задвижка
Краном называют запорное устройство, в котором подвижная деталь затвора имеет форму тела вращения с отверстием для пропускания потока и при его перекрытии вращается вокруг своей оси, перпендикулярно к направлению потока. Кран состоит из двух основных деталей: неподвижной – корпуса и вращающейся – пробки.
В зависимости от конструкции затвора краны бывают коническими, цилиндрическими, сферическими или шаровыми;
– от характера движения пробки – с вращение пробки без подъема и с подъемом ее перед поворотом и последующим опусканием (прижимом после поворота);
– по способу присоединения к трубопроводу – фланцевыми, муфтовыми, цапковыми, с концами под приварку и специальными;
– по форме и сечению проходного канала – полнопроходными и с суженным проходом, а также со смазкой и без смазки.
Краны могут иметь ручное управление, гидравлический, пневматический, пневмогидравлический и электрический приводы.
По сравнению с другими видами запорной арматуры краны обладают следующими преимуществами:
– крутящий момент привода (ключа, штурвала и др.) в них передается непосредственно на пробку (в других видах запорной арматуры для обеспечения поступательного перемещения запирающей детали имеется, как правило, резьбовая пара);
– прямоточность движения потока через отверстие в пробке и вследствие этого малое гидравлическое сопротивление;
– компактность (пробка кранов в отличие от подвижных деталей вентилей и задвижек, перемещающихся поступательно, вращается вокруг оси, не перемещаясь в пространстве);
– при работе поверхность пробки не отрывается от корпуса и уплотнительные поверхности остаются замкнутыми, что значительно уменьшает эрозию уплотнительных поверхностей и опасность попадания на поверхность контакта посторонних частиц; возможность использования при малом давлении кранов, имеющих небольшой диаметр условного прохода, для регулирования потока.
Шаровый кран обладает прямоточностью, низким гидравлическим сопротивлением, постоянным контактом уплотнительных поверхностей, малыми габаритными размерами. Корпус и пробка этих кранов имеют сферическую поверхность.
Наиболее трудоемкие операции при изготовлении кранов – механическая обработка и притирка уплотнительных поверхностей корпуса и пробки. Уплотнительные поверхности корпусов шаровых кранов выполняют в виде колец или седел, размеры которых во много раз меньше размеров уплотнительных поверхностей пробок. В шаровых кранах с кольцами, имеющими мягкие уплотнения, необходимость в притирке уплотнительных поверхностей отпадает вообще. Пробку обычно хромируют или полируют.
Дополнительная герметизация шаровых затворов в кранах с большими диаметрами проходных сечений, которые предназначены для установки на газопроводах, рассчитанных на большие условные давления и низкие отрицательные температуры, достигается за счет подачи уплотнительной смазки (пасты, герметик). Шаровой затвор представляет собой узел, состоящий из шара, двух уплотняющих седел и поворотного штока (шпинделя).
По способу установки шара и уплотнительных седел выделяют три основных типа шаровых затворов:
– с плавающим шаром;
– шаром на опорах;
– с плавающим шаром и подпружиненной плавающей втулкой.
Кран с плавающим шаром представлен на рисунке 4.
Рисунок 4 – Кран с плавающим шаром
Принцип работы затвора с плавающим шаром следующий: в корпусе расположены два уплотнительных седла, между которыми штуцерами зажимается стальной или бронзовый шар, имеющий сквозное отверстие, диаметр которого равен внутреннему диаметру трубопровода. С помощью штока шар может поворачиваться в уплотнительных седлах. В открытом положении отверстия шара и трубопровода совпадают, обеспечивая протекание рабочей среды с минимальным гидравлическим сопротивлением. При повороте штока на четверть оборота (на 90°) отверстие шара устанавливается перпендикулярно к проходному отверстию крана. Давлением среды шар прижимается к заднему седлу, чем обеспечивается полная герметичность затвора. Седла уплотняются с корпусом прокладками из резины, а с шаром – тефлоновым кольцом.
Краны с плавающим шаром применяются с диаметром до 100 мм, при давлении до 10 МПа.
Основное преимущество таких затворов – простота и компактность, что определяет высокую надежность в эксплуатации и малую металлоемкость крана.
Необходимые герметичность и надежность работы кранов такого типа обеспечены при выполнении следующих условий:
– удельная нагрузка на поверхность контакта шара и седла должны быть достаточно высокими для уплотнения;
– шар должен быть идеальной сферической формы и высокой чистоты обработки;
– посадка седла должна быть герметичной в канавку (с углом при вершине 60° и глубиной 2–3 мм) на торцевой поверхности гнезда;
– уплотнение седла должно быть выполнено из пластичного и прочного материала (фторопласт, имеющий низкий коэффициент сухого трения, большой диапазон работающих температур, высокую химическую стойкость) и способного выдерживать большие нагрузки.
В нормально работающем затворе с плавающим шаром уплотнение обеспечивается седлом, расположенным за шаром. Седло, расположенное перед шаром, давлением газа может отжиматься от торцовой поверхности и изгибаться. В этом случае рабочая среда может проходить в зазор в полость шарового затвора. Во избежание повреждения седло перед шаром необходимо надежно закреплять в корпусе с помощью пружинного бронзового кольца с внутренними буртами.
Кран с затвором на опорах, показанный на рисунке 5, конструктивно более сложный. Применяют такой кран в основном в шарах с большим диаметром до 1600 мм, которые рассчитаны на давление до 79 МПа. Перенос опорных усилий с уплотнительных седел на полуоси шара позволяет значительно уменьшить момент, необходимый для поворота пробки. Затвор с шаром на опорах может быть выполнен по двум схемам: с уплотняющим седлом перед шаром и за ним.
Рисунок 5 – Кран с затвором на опорах
Принцип работы затвора с уплотнительным седлом следующий: шар, выполненный как одно целое с полуосями, может свободно поворачиваться в двух опорных подшипниках (скольжения или качения). Уплотнительные седла расположены в плавающих втулках, которые уплотняются в корпусе кольцами. Седла затвора предварительно поджимаются комплектом пружин. Седло, со стороны входа, при закрытом затворе прижимается к шару давлением среды, действующим на кольцевую поверхность, которая ограничена окружностями с диаметрами d и 𝐷1. Противоположное седло в уплотнении затвора не участвует.
Конструктивное отличие затвора с уплотняющим седлом за шаром от затвора с уплотняющим седлом перед шаром заключается в том, что он имеет плавающие втулки, у которых диаметр уплотнения 𝐷2 меньше среднего диаметра седла 𝑑ср.
Затвор с шаром на опорах по сравнению с затворами с плавающим шаром имеют следующие преимущества:
– с уплотняющим седлом перед шаром – при закрытом затворе уплотнение шпинделя и большая часть корпуса крана не нагружены внутренним давление;
– с уплотняющим седлом за шаром – значительное снижение нагрузки на опорный подшипник, уменьшение суммарного момента трения в затворе.
Затворы с уплотняющим седлом перед шаром характеризуются значительным крутящим моментом, необходимым для поворота шара, и высокими нагрузками на опорные подшипники в результате увеличения эффективной площади, на которую действует давление.
При эксплуатации магистральных газопроводов используются краны в надземном и подземном исполнении. Кран подземного исполнения включает в себя удлиняющую колону и удлинитель шпинделя. На рисунке 6 представлен кран надземного исполнения, на рисунке 7 представлен кран подземного исполнения.
Рисунок 6 – Кран надземного исполнения
Рисунок 7 – Кран подземного исполнения
Тема 3 Приводы кранов
Поворот затвора в корпусе крана может требовать значительных усилий, поэтому применяют различные типы приводов: ручной (управление осуществляется оператором вручную), электрический (управление арматурой осуществляется с помощью электродвигателя), поршневой (вид привода, в котором присутствует силовой гидроцилиндр и поршень), кривошипный, лопастной (используемые типы приводов встречаются на кранах чехословацкого производства).
Управление кранами может происходить по месту и дистанционно.
В настоящее время самыми используемыми являются поршневые приводы. В качестве источника энергии приводов используется газ, транспортируемый по трубопроводу. Так же для управления этими приводами применяется гидрожидкость – при перестановке затвора крана ручным насосом. Приводы неполноповоротные, с неподвижными или качающимися цилиндрами. Число цилиндров от одного до четырех.
Конструкция поршневого пневмогидропривода крана показана на рисунке 8.
Рисунок 8 – Поршневой пневмогидропривод крана
На рисунке обозначены:1 – крышка; 2 – корпус; 3 – цилиндр; 4 – регулировочный упор; 5 – стопор; 6 – гайка; 7 – поршень; 8 – шток; 9 – направляющая; 10 – плита; 11 – ползушка; 12 – палец; 13 – рычаг.
Работа пневмогидропривода происходит следующим образом: давление управляемой среды подается в соответствующую поршневую полость цилиндра привода, поршень 7 со штоком 8 перемещается, шток через плиту 10, палец 12 и ползушку 11 действует на рычаг 13, заставляет его вращаться в подшипниках, установленных в корпусе и крышке. Гидрожидкость, залитая в подпоршневую полость, выполняет роль демпфера и перетекает из одного цилиндра в другой. Движение прекращается при достижении штоком упора 4
определяется пропускная способность клапана во втором цилиндре 3.
Скорость перетекания гидрожидкости регулируется дросселями, расположенными на крышке насоса.
При отсутствии давления среды поворот рычага осуществляется за счет перекачки гидрожидкости из одного цилиндра в другой с помощью ручного насоса, показанного на рисунке 9.
Рисунок 9 – ручной насос
На рисунке обозначены:1 – корпус; 2 – плунжер; 3 – золотник; 4 – нагнетательный клапан; 5 – крышка; 6 – шпиндель; 7 – рукоятка переключения; 8 – шарик; 9 – всасывающий клапан; 10 – втулка; 11 – скоба; 12 – ручка.
Работа насоса происходит следующим образом: при повороте ручки 12 насоса вверх гидрожидкость всасывается в полость через всасывающий клапан, а при обратном ходе выталкивается через нагнетательный клапан 4 в трубопровод и цилиндр пневмогидропривода. Направление потока гидрожидкости производится рукояткой переключения через золотник 3.
При открытии или закрытии крана рукоятка переключения должна устанавливаться в положения «О» (открытие), «3» (закрытие), «Д» (дистанционное управление).
Дистанционное управление приводом крана осуществляется с помощью импульсного газа и блока соленоидных клапанов. На рисунке 10 показана схема дистанционного управления приводом крана.
Рисунок 10 – Схема дистанционного управления приводом крана
На рисунке обозначены:1 – шаровый кран; 2 – запорный кран; 3 – ручной насос; 4 – обратный клапан; 5 – клеммная коробка; 6 – блок фильтров; 7 – соленоидный клапан; 8 – предохранительный клапан; 9 – отсекающее устройство; 10 – контрольный бак; 11 – конечный выключатель; 12 – привод; 13 – дроссель; 14 – распределительный кран; 15 – бак.
Отбор импульсного газа производится с обеих сторон шарового крана. Газ, пройдя краны 2, обратные клапаны 4 и блок фильтров 6, подается на соленоидный клапан 7. Управление соленоидным клапаном происходит дистанционно, по сигналу с пульта управления или вручную. Газ управления после перестановки соленоидного клапана подается в один из цилиндров привода и, действуя на поршень, производит перестановку шаровой пробки крана.
На рисунке 11 схема расположения гидрожидкости в двух гидроцилиндрах привода крана. Гидроцилиндры разделены на газовую полость и гидрополость. При эксплуатации данного типа привода постепенно происходит износ уплотнений поршней, вследствие чего происходит перетекание гидрожидкости в газовую полость.
Рисунок 11 – Схема расположения гидрожидкости в двух гидроцилиндрах привода
На рисунке 12 схема привода крана с газовым цилиндром и гидроцилиндром, что позволяет исключить перетекание жидкости в газовые полости.
Рисунок 12 – Схема привод с газовым цилиндром и гидроцилиндром
Тема 4 Противопомпажные клапаны
Помпаж возможен для всех центробежных компрессоров (нагнетателей). При помпаже резко ухудшается аэродинамика проточной части, компрессор не может создавать требуемый напор, при этом, давление за ним на некоторое время остаётся высоким. В результате происходит обратный проброс газа. Давление за компрессором уменьшается, он снова развивает напор, но при отсутствии расхода напор резко падает, ситуация повторяется. При помпаже вся конструкция испытывает большие динамические нагрузки, которые могут привести к её разрушению. Помпаж зачастую связан с явлением пневмоудара.
Для защиты от помпажа обычно используется сброс рабочей среды или перепуск с выхода компрессора на его вход в количестве, необходимом для избежания помпажа, для этого в системе антипомпажного регулирования и защиты используются регулирующие или запорно-регулирующие антипомпажные клапаны.
Современные антипомпажные клапаны имеют высокую скорость хода, которая предотвращает длительное воздействие помпажа на компрессор, а также регулируют поток, что требует не только быстрого полного хода, но также и способности реагировать на изменение уставки быстро и точно.
Антипомпажный клапан предназначены для работы с газом и жидкостью и основан на принципе осевого потока. Осевой поток формируется в прямолинейном симметричном проточном контуре между внутренним и наружным корпусами клапана.
На рисунке 13 показан антипомпажный клапан в разрезе.
Рисунок 13 – Антипомпажный клапан
Работа антипомпажного клапана показана на рисунке 14.
|
|
|
|
|
|
Рисунок 14 – Антипомпажный клапан
1– наружный корпус клапана; 2– внутренний корпус; 3– поршень; 4– шток поршня; 5 – шток клапана; 6 – сепаратор
Поршень движется в сепараторе. Дросселирование потока происходит между кромкой поршня и отверстиями сепаратора. Движение поршня изменяет площадь сечения отверстий сепаратора. Поток всегда идет с наружной стороны сепаратора таким образом, что зона, в которой скорость среды максимальна, всегда находится в нем. При закрытии клапана главное уплотнение активируется за счет перепада давления на поршне. Это давление разжимает кольцо уплотнения и таким образом полностью отсекает поток.
Дата добавления: 2020-11-23; просмотров: 197; Мы поможем в написании вашей работы! |
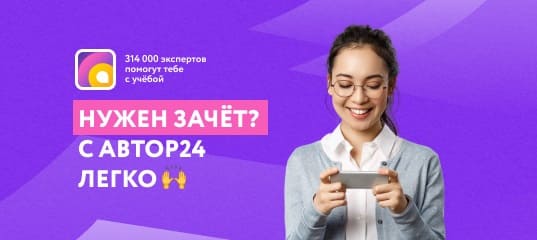
Мы поможем в написании ваших работ!