Измерение и анализ параметров состояния поверхностного слоя
Описание методики проведения работы
Краткие общие и теоретические сведения
Описание методики проведения работы
Выдача индивидуальных образцов изготовленных из деталей, обработанных различными методами
Выбор контролируемых параметров качества поверхностного слоя
Выбор оборудования и измерительных средств для контроля поверхностного слоя образцов
Измерение контролируемых параметров качества поверхностного слоя
Обработка результатов измерения
Вывод по работе
Основное положение
Удовлетворение высоких требований к эксплуатационным свойствам изготовляемых деталей в современном машиностроении обеспечивается достижением в процессе обработки заданных характеристик по отдельным факторам: по точности размеров, погрешности формы, состоянию поверхностного слоя (шероховатость, микротвердость и др.). Эти параметры, значения которых регламентируется в чертеже на деталь и в технических требованиях, могут быть обеспечены различными методами, существенно отличающимися между собой по технико-экономическим показателям. Шероховатость в процессе эксплуатации узла трения претерпевает этап приработки. В этом процессе происходят необратимые изменения в тонком поверхностном слое детали. Изменяются структура, механические свойства и геометрия поверхности на микро- и макроуровне.
В начальный период пластически деформируются и быстро изнашиваются вершины неровностей. В результате возникают новые по форме и размерам микронеровности.
|
|
В конце этапа приработки поверхности трущейся пары приходят к состоянию минимума потенциальной энергии в данных условиях работы. Наступает этап нормального износа, при котором величина шероховатости практически не изменяется. Возникает так называемая «равновесная шероховатость», которая практически не изменяется в процессе нормального износа.
Увеличенная микротвердость после обработки способствует повышению износостойкости деталей, т.к. уменьшается взаимное внедрение микровыступов поверхностей трущихся пар. При нормальном давлении в контактной зоне деформации происходят преимущественно в упругой области, что повышает контактную жесткость.
Оборудование, измерительная аппаратура, приборы, обрабатываемый материал
Операции точения проводятся на универсальном токарном станке модели 16К20
Операции шлифования проводится на круглошлифовальном станке модели 3А110.
Шероховатость обработанных поверхностей измеряется и фиксируется с помощью профилографа- профилометра модели 252 завода “Калибр” или на аналогичном оборудовании.
|
|
Микротвердость поверхностей образцов измеряется прибором ПМТ-3 или на аналогичном оборудовании.
Образцы для обработки изготовляются в виде дисков из стали 45 диаметром 80-150 мм, высотой 50 мм, в состоянии поставки (твердость HB 190…200).
Методика подготовки и проведения экспериментов
Подготовка дисков к экспериментам проводится вне лабораторной работы. Порядок подготовки следующий.
1)Комплект дисков в сборе с оправкой (рис.1.1 а, б) и с закрепленными в дисках образцами-свидетелями проходит предварительную обработку на токарном станке с закреплением в трехкулачковом патроне и поджимом задним центром. Параметр исходной шероховатости цилиндрической поверхности дисков после предварительного точения Ra=2 мкм.
а)
![]() |
б) I
Рис.1.1. Приспособление для проведения опытов
2)Измеряются геометрические параметры режущей части резца. Результат измерений фиксируются в таблице №1
3) Назначается режим резания в соответствии с рекомендациями общемашиностроительных нормативов режимов резания. Рассчитанные параметры фиксируется в таблице №2.
|
|
4) Характеристика шлифовального круга и режимы шлифования назначаются в соответствии с рекомендациями . Характеристики шлифовального круга и режим обработки фиксируются в таблице №3 и №4.
Таблица №1 Геометрические параметры резца, оснащенного
твердосплавной пластиной
Схема обработки | Тип резца | Марка твердого сплава | Геометрические параметры | |||||||
a | g | b | d | j | j’ | e | l | |||
Продольное точение | Проходной упорный | Т15К6 | 12 | 15 | 63 | 75 | 90 | 5 | 85 | 0 |
Таблица №2
Режимы резания резцом, оснащенным твердосплавной пластиной
Обрабатываемый материал; | Вид обработки | Скорость резания V, м/мин | Частота вращения шпинделя n, об/мин | Глубина резания t, мм | Подача Sо, мм/об |
Сталь 45 | Чистовая | 120 | 200 | 0.5 | 0.18 |
|
|
Таблица №3
Характеристика шлифовального круга
Схема обработки | Характеристика шлифовального круга | ||||
Марка абразива | Зернистость | Твердость | Структура | Связка | |
Шлифования | 25А | 40 | M2 | 7 | K |
Таблица №4
Режим резания при шлифовании
Вариант | Обрабатываемый материал; | Вид шлифования | Скорость круга Vк, м/с | Скорость заготовки Vз, м/мин | Глубина резания t, мм | Продоль ная подача S, м/мин |
1 | Сталь 45 | Круглое | 30-35 | 15-55 | 0.005 | 0.2-04 |
Измерение и анализ параметров состояния поверхностного слоя
Поскольку на измерительных приборах трудно или невозможно установить такую крупную деталь, как обрабатываемый диск, исследованию подвергаются так называемые образцы - свидетели – специальные цилиндры, изготовленный из того же материала и прошедшие такую же термическую и механическую обработку, что и исследуемые диски.
Измерение шероховатости производится на профилографе- профилометре модели 252 завода “Калибр”. Действие прибора основано на принципе ощупывания неровностей исследуемой поверхности алмазной иглой датчика и преобразования возникающих при этом колебаний иглы в изменения напряжения индуктивным методом, пропорциональные этим колебаниям.
Электронная часть прибора (рис.1.2) включает в себя электронный блок 7, показывающий 8 или записывающий 9 приборы. Магнитная система датчика состоит из сдвоенного Ш-образного сердечника 2 с двумя катушками 1. Катушка датчика и две половины первичной обмотки дифференциального входного трансформатора 6 образуют балансный мост, который питается от генератора 5. При перемещении датчика относительно исследуемой поверхности алмазная игла 4, ощупывая неровности исследуемой поверхности, совершает колебания, приводя в колебательные движение коромысло 3. При этом меняются зазоры между якорем и сердечником и тем самым вызываются изменения напряжения на выходе дифференциального трансформатора. Они усиливаются в электронном блоке 7, на выходе из которого подключены показывающий 8 или записывающий 9 приборы. Результаты измерений, считанные с цифрового устройства, фиксируются в таблицу №5.
Рис.1.2. Схема измерения
Основные технические характеристики профилографа-профилометра 252
Параметры шероховатости поверхности, определяемые по показывающему устройству | Ra - среднее арифметическое отклонение профиля; Hmax- высота наибольшего выступа профиля; Hmin- высота наибольшей впадины профиля; tp - относительная опорная длина профиля; n – число шагов неровностей в пределах длины трассы ощупывания при из- мерении (по базовой линии). |
Диапазон измерений | профилографа, мкм 0.02…210 профилометра по параметрам Ra, мкм 0.02…100 Hmax, Hmin, мкм 0.1…100 tp, % 0…100 n до 1000 |
Уровни сечения профиля при измерении tp, % | 10, 20, 30, 40, 50, 60, 70, 80, 90. |
Вертикальное увеличение профилографа | 200, 500, 1000, 2000, 5000, 10000, 20000, 50000, 100000. |
Горизонтальное увеличение профилографа | 0,5; 1; 2; 5; 10; 20; 50; 100; 200; 500; 1000; 2000. |
Максимальная длина трассы ощупывания профилографаю. | 50 мм |
Ширина записи | 50 мм |
Скорости трассирования датчика | 0,6; 6; 60 мм/мин |
Значения отсечек шага | 0,08; 0,25; 0,8; 2,5 мм |
Длина трасс ощупывания при измерении (профилометра) | 1,5; 3; 6 мм |
Радиус кривизны вершины щупа | 10±2,5 мкм |
Таблица №5
Измеренный параметр шероховатости
Метод обработки |
Исходная шероховатость Ra, мкм |
Шероховатость после обработки Ra, мкм | |
Измер. | Среднее арифметическое | ||
Точение твердосплавным резцом (диск №1) |
2 | 1.5 |
1.6 |
1.6 | |||
1.6 | |||
Шлифование (диск №2) | 0.8 |
0.8 | |
0.7 | |||
0.8 |
Измерение микротвердости поверхностного слоя после обработки измеряется на приборе ПМТ-3 методом вдавливания индентора (алмазной пирамиды) в выбранный участок исследуемой поверхности. Твердость определяется глубиной внедрения индентора, а значение твердости вычисляется в зависимости от площади отпечатка, которая определятся путем измерения его диагонали d (рис.1.3).
Алмазная пирамида имеет квадратное основание и угол при вершине между противоположными гранями 136о. Для увеличения точности определения твердости измеряют длину d обеих диагоналей отпечатка и в формулу вводят среднее арифметическое значение двух измерений.
Рис.1.3 Схема измерения микротвердости образца-свидетеля
При испытании на микротвердость числовое значение твердости определяется как частное от деления нагрузки P (в Ньютонах) на боковую поверхность F (в квадратных миллиметрах), т.е. в МПа.
H = P = 0,185P .
m F d 2
Для исследования выбирается нагрузка на алмазную пирамиду 0,5 Н, наиболее часто применяемую в практике измерения микротвердости сталей.Результаты измерений микротвердости заносятся в таблицу № 6
Основные технические характеристики ПМТ-3
Испытательные нагрузки | 0,0196~4,9 Н. |
Предел допускаемой погрешности нагрузок в диапазонах основном/дополнительном, не более | +2 % |
Выдержка образца под нагрузкой | 10-15 сек. |
Используемые индентора | Алмазная пирамидка квадратного сечения. |
Расстояние от индентора до опорного столика | 0~70 мм. |
Расстояние от центра отпечатка до станины | 100 мм. |
Габаритные размеры, мм. (ДхШхВ) | 270х290х470 |
Масса | 22 кг. |
Электропитание | ~220V/50Hz. |
Мощность | 0,02 кВт. |
Таблица №6
Измерение микротвердости после обработки
Метод обработки | Размер диагонали отпечатка,мм |
Число твердости, Мпа | |||
1 изм | 2 изм | 3 изм | Среднее арифметич. | ||
Точение твердосплавным резцом | 0.035 | 0.036 | 0.035 | 0.035 | 210 |
Шлифования | 0.023 | 0.023 | 0.024 | 0.023 | 96.5 |
Вывод: В результате проделанной работы установлено, что после обработки поверхности точением шероховатость выше, чем после обработки поверхности шлифованием, микротвердость поверхности после точения выше, чем при шлифовании. После точения образуется наклеп, который увеличивает долговечность металла.
Дата добавления: 2020-11-15; просмотров: 233; Мы поможем в написании вашей работы! |
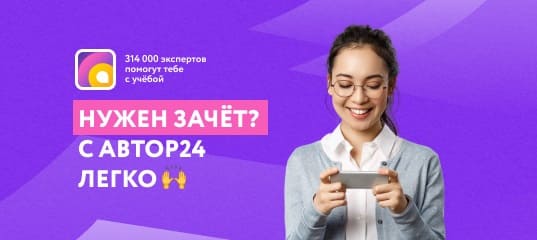
Мы поможем в написании ваших работ!